摩擦液柱成形过程的二维CFD数值模拟
成形磨削过程中气液两相流VOF模拟与分析

成形磨削过程中气液两相流VOF模拟与分析叶久贞;季田;张利萍;庞桂兵【摘要】在成形磨削过程中,磨削液在磨削区域的流动和分布情况是影响磨削精度的重要因素.通过对磨削区气体进行气流场模拟分析得出,砂轮表面附近存在气障层,工件表面附近存在返回流,并且气障层和返回流会对磨削液的有效供给产生阻碍作用.运用气液两相流VOF理论,通过对磨削区磨削液流场中的气液两相流模拟分析得出,不同喷射位置和喷射速度产生不同磨削效果,并提出了磨削液的最佳喷射位置和喷射速度,对提高成形磨削的质量和效率,防止磨削过程中工件的烧伤提供了重要的参考依据,同时对实现绿色制造具有重要的工程实际意义.%The grinding fluid flow and distribution were important factors affecting grinding accuracy in the process of shaping grinding.The air flow field simulation showed that the air barrier layer was existed near the surface of the grinding wheel, while the return flow was existed near the surface of the work piece, and the air barrier layer and return flow would hinder the effective supply of grinding fluid.The air-liquid two-phase flow field simulation in the grinding zone was obtained based on the theory of air-liquid two-phase flow-VOF showed that different jet positions and velocities had different grinding effects, and the best jet locations and velocities of grinding fluid were proposed, which would provide important foundation to improve the quality and efficiency to prevent burns from the work piece in the shaping grinding, while the realization of green manufacturing would have important engineering practical significance.【期刊名称】《大连工业大学学报》【年(卷),期】2017(036)003【总页数】5页(P218-222)【关键词】气流场;气液两相流流场;气障层;返回流;喷射位置;喷射速度【作者】叶久贞;季田;张利萍;庞桂兵【作者单位】大连工业大学机械工程与自动化学院, 辽宁大连 116034;大连工业大学机械工程与自动化学院, 辽宁大连 116034;大连工业大学机械工程与自动化学院, 辽宁大连 116034;大连工业大学机械工程与自动化学院, 辽宁大连 116034【正文语种】中文【中图分类】TH115成形磨削是机械加工中应用最广泛的精密加工方法之一,在机械加工中占有非常重要的地位[1]。
金属液流动与凝固过程数值模拟分析方法研究

金属液流动与凝固过程数值模拟分析方法研究金属液流动和凝固过程数值模拟分析方法研究概述金属液流动和凝固过程是金属材料加工中的重要环节,对于金属制品的质量和性能有着重要影响。
因此,研究金属液流动和凝固过程的数值模拟分析方法具有重要的理论价值和实际应用价值。
本文将针对金属液流动和凝固过程的数值模拟分析方法进行研究,探讨其原理、步骤和应用。
一、数值模拟方法原理数值模拟方法是通过将物理系统离散化为有限的控制体积或网格,建立物理方程组,并使用数值计算方法求解,从而获得系统的增量或离散化解。
在金属液流动和凝固过程的数值模拟中,通常采用的是计算流体力学方法(CFD)或有限元方法(FEM)。
计算流体力学方法以连续介质力学为基础,通过对连续介质流动进行方程建模和求解,获得流动场的信息,进而研究流动的性质和变化规律。
在金属液流动和凝固过程的数值模拟中,流动方程通常采用Navier-Stokes方程,并结合运动边界条件、控制方程和物理方程对金属液流动过程进行数值模拟。
有限元方法是通过将物理系统划分为有限个单元,通过使用多项式近似解的方法,得到局部解之后,通过求解单元间的关系得到整体解。
在金属液流动和凝固过程的数值模拟中,有限元方法通常采用二维或三维的网格划分方法,将金属液的流动与凝固过程离散化为有限个单元,然后针对每个单元进行方程建模和求解,最终获得整体的解。
二、数值模拟方法步骤1. 建立几何模型:首先需要建立金属液流动和凝固过程的几何模型,通过CAD软件或者网格生成软件能够实现。
2. 网格划分:将几何模型离散为有限个单元或控制体积,进行网格划分。
在金属液流动和凝固过程的数值模拟中,网格划分需要根据流场的特点和凝固过程的要求进行合理的选择。
3. 建立物理模型:在金属液流动和凝固过程的数值模拟中,需要对流动方程、凝固方程和物理方程进行建模。
根据流动的性质和过程的要求,可以选择不同的物理模型。
4. 边界条件和初始条件:通过观察实验或实际生产中的数据,确定流场和凝固过程的初始条件和边界条件,以供数值模拟求解时使用。
自由流场二维圆柱阻力系数数值模拟
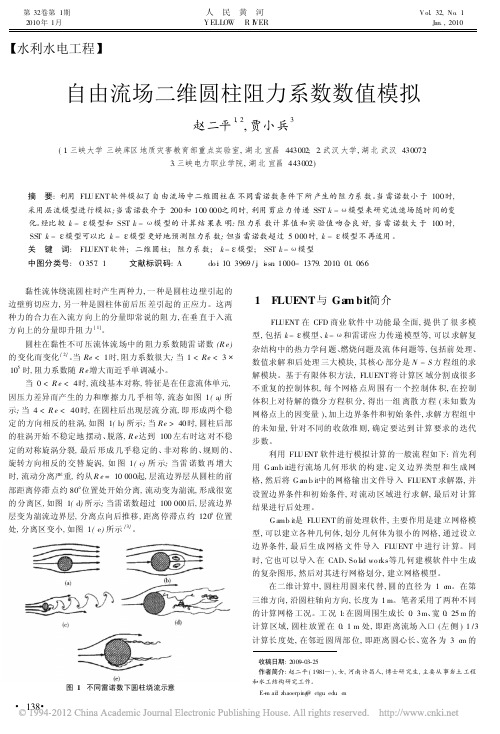
黏性流体绕流圆 柱时产生两种力, 一 种是圆柱边 壁引起的 边壁剪切应力, 另一种是圆柱体前后压 差引起的 正应力。这两 种力的合力在入流方 向上的分量即常说的阻 力, 在垂 直于入流 方向上的分量即升阻 力 [ 1]。
圆柱在黏性不可 压流体流 场中的 阻力系 数随雷 诺数 (R e) 的 变化而变化 [ 2] 。当 Re < 1时, 阻力系数很大; 当 1 < Re < 3 @ 105 时, 阻力系数随 R e增大而近乎单调减小。
当 0 < R e < 4时, 流线基本对称, 特征是在任意流体单元, 因压力差异而产生的 力和摩 擦力几 乎相 等, 流态 如图 1( a) 所 示; 当 4 < R e < 40时, 在圆柱后出现层流 分流, 即 形成两个稳 定 的方向相反的驻涡, 如图 1( b) 所示; 当 Re > 40时, 圆柱后部 的驻涡开始 不稳定地 摆动、脱落, R e达到 100 左右时这 对不稳 定的对称旋涡分裂, 最后 形成 几乎稳 定的、非对称 的、规则 的、 旋转方向相反的 交替 旋涡, 如 图 1( c) 所 示; 当雷 诺数 再 增大 时, 流动分离严重, 约从 R e = 10 000起, 层流边界层从圆柱的前 部距离停滞 点约 80b位置处开始分离, 流动变为湍流, 形成很宽 的 分离区, 如图 1( d) 所示; 当雷诺数超过 100 000后, 层流边界 层变为湍流边界层, 分离点向后推移 , 距离 停滞点 约 120b 位置 处, 分离区变小, 如图 1( e) 所示 [3] 。
CFD数值模拟过程
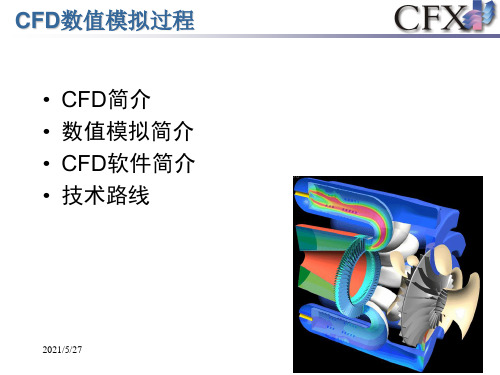
2021/5/27
5
CFD数值模拟过程
CFD简介 数值模拟简介 CFD软件介绍 技术路线
深刻地理解问题产生机理,指 导实验,节省所需人力、物力 和时间,并有助于整理实验结 果、总结规律。
2021/5/27
6
基本原理是数值求解控制流体流动的源自分方程,得出流场 在连续区域上的离散分布,从而近似模拟流体流动情况。
tui xj uiuj x P i xijjSui
2021/5/27
2
CFD数值模拟过程
CFD简介 数值模拟简介 CFD软件介绍 技术路线
Computational Fluid Dynamics(计算流体动力学) 计算机技术 + 数值计算技术 流体实验 计算机虚拟实验
技术路线
➢ 建立数学物理模型
➢ 数值算法求解
➢ 结果可视化
2021/5/27
4
CFD数值模拟过程
CFD简介 数值模拟简介 CFD软件介绍 技术路线
进行流场分析、计算、预测的专业软件。通过CFD软件,可以 分析并显示发生在流场中的现象,在比较短的时间内,能预测 性能,并通过改变各种参数,达到最佳设计效果。
基本原理是数值求解控制流体流动的微分方程,得出流场 在连续区域上的离散分布,从而近似模拟流体流动情况。
tui xj uiuj x P i xijjSui
2021/5/27
3
CFD数值模拟过程
CFD简介 数值模拟简介 CFD软件介绍
利用计算机求解各种守恒控制偏微分方程组的技术。
涉及流体力学(湍流力学)、数值方法乃至计算机图形学等多 学科。且因问题的不同,模型方程与数值方法也会有所差别, 如可压缩气体的亚音速流动、不可压缩气体的低速流动等。
(整理)微观表面形貌流体动压润滑效果的二维CFD有限元分析
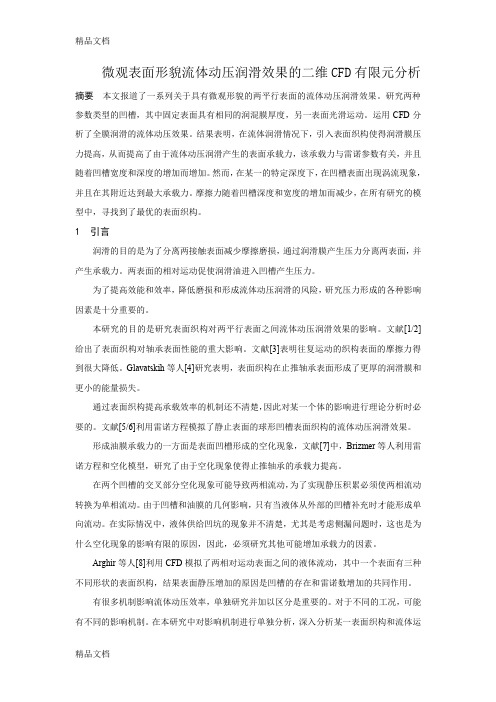
微观表面形貌流体动压润滑效果的二维CFD有限元分析摘要本文报道了一系列关于具有微观形貌的两平行表面的流体动压润滑效果。
研究两种参数类型的凹槽,其中固定表面具有相同的润混膜厚度,另一表面光滑运动。
运用CFD分析了全膜润滑的流体动压效果。
结果表明,在流体润滑情况下,引入表面织构使得润滑膜压力提高,从而提高了由于流体动压润滑产生的表面承载力,该承载力与雷诺参数有关,并且随着凹槽宽度和深度的增加而增加。
然而,在某一的特定深度下,在凹槽表面出现涡流现象,并且在其附近达到最大承载力。
摩擦力随着凹槽深度和宽度的增加而减少,在所有研究的模型中,寻找到了最优的表面织构。
1 引言润滑的目的是为了分离两接触表面减少摩擦磨损,通过润滑膜产生压力分离两表面,并产生承载力。
两表面的相对运动促使润滑油进入凹槽产生压力。
为了提高效能和效率,降低磨损和形成流体动压润滑的风险,研究压力形成的各种影响因素是十分重要的。
本研究的目的是研究表面织构对两平行表面之间流体动压润滑效果的影响。
文献[1/2]给出了表面织构对轴承表面性能的重大影响。
文献[3]表明往复运动的织构表面的摩擦力得到很大降低。
Glavatskih等人[4]研究表明,表面织构在止推轴承表面形成了更厚的润滑膜和更小的能量损失。
通过表面织构提高承载效率的机制还不清楚,因此对某一个体的影响进行理论分析时必要的。
文献[5/6]利用雷诺方程模拟了静止表面的球形凹槽表面织构的流体动压润滑效果。
形成油膜承载力的一方面是表面凹槽形成的空化现象,文献[7]中,Brizmer等人利用雷诺方程和空化模型,研究了由于空化现象使得止推轴承的承载力提高。
在两个凹槽的交叉部分空化现象可能导致两相流动,为了实现静压积累必须使两相流动转换为单相流动。
由于凹槽和油膜的几何影响,只有当液体从外部的凹槽补充时才能形成单向流动。
在实际情况中,液体供给凹坑的现象并不清楚,尤其是考虑侧漏问题时,这也是为什么空化现象的影响有限的原因,因此,必须研究其他可能增加承载力的因素。
基于材料变粘度模型的摩擦液柱成形CFD数值模拟

基于材料变粘度模型的摩擦液柱成形CFD数值模拟陈忠海;谢美芬;陈家庆;吴春诚;白若琦;程城远;邱晓华【摘要】采用Gambit软件建立了摩擦液柱成形过程流场二维轴对称变粘度模型,运用商业计算流体动力学(CFD)软件Fluent对单元成形过程中稳态阶段塑性金属的流动情况进行了数值模拟.通过改变模拟过程中的进给速度或旋转速度,保持其他参数不变的情况下分析了塑性金属速度场、压力场的变化情况,对比了理想等粘流体模型和实际变粘流体模型的差异.结果表明,金属棒的进给速度对流体压力场的影响显著;随着旋转速度的增加,金属棒壁面以及底部的流体速度显著增加,该区域是单元成形过程中的主要产热区.【期刊名称】《电焊机》【年(卷),期】2015(045)007【总页数】8页(P132-139)【关键词】摩擦液柱成形;变粘度;摩擦叠焊;计算流体动力学;数值模拟【作者】陈忠海;谢美芬;陈家庆;吴春诚;白若琦;程城远;邱晓华【作者单位】温州科技职业学院,浙江温州325006;温州科技职业学院,浙江温州325006;北京石油化工学院,北京102617;温州科技职业学院,浙江温州325006;温州科技职业学院,浙江温州325006;温州科技职业学院,浙江温州325006;温州科技职业学院,浙江温州325006【正文语种】中文【中图分类】TG453+.9摩擦叠焊是由英国焊接研究所(TWI)于1991年前后发明的一种新型固相连接技术,在材料的成形加工尤其是钢结构裂纹的水下维修方面具有巨大的应用潜力[1]。
摩擦叠焊的基本单元成形过程为摩擦液柱成形(Friction Hydro Pillar Processing,FHPP),一系列沿着预定轨迹相互搭接的FHPP便构成了摩擦叠焊。
因此,围绕FHPP单元过程中塑性金属的流动、受力、产热等问题进行理论或实验研究,对揭示摩擦叠焊的成形机理和连接特性具有重要意义。
本研究在理想模型的基础上,采用变粘度模型进行数值模拟,以期得到更多对实验研究具有参考和指导意义的结论,为后续开展热力耦合的数值模拟奠定坚实基础。
基于FLUENT的齿轮成形磨削气液两相流仿真分析

机械与动力工程河南科技Henan Science and Technology总第874期第3期2024年2月基于FLUENT 的齿轮成形磨削气液两相流仿真分析尹铭禹 杨佳兆 杜征征 邢 波 杨思源 杨 敏(南京工程学院工业中心,江苏 南京 211167)摘 要:【目的】针对齿轮磨削加工中冷却效果不佳,表面液流量少的问题进行研究。
【方法】设定不同的砂轮转速对磨削气流场进行仿真分析。
在液流场中使用VOF 气液两相流模型对不同喷嘴位置进行仿真模拟。
【结果】结果表明:砂轮旋转带动周围气体形成返回流,阻碍射流进入磨削加工区域;砂轮转速30 m/s 流体速度比砂轮转速20 m/s 时高50%,能够满足磨削加工需求且返回流强度适中;距离齿轮表面垂直距离40 mm 的喷嘴位置,能更好地将磨削液喷射至磨削区域,冷却效果最优。
【结论】经过上述仿真分析可得出最佳的砂轮转速和喷嘴位置,对实际加工中节能降耗有一定的指导意义。
关键词:齿轮;气流场;气液两相流;仿真模拟中图分类号:TP391.9 文献标志码:A 文章编号:1003-5168(2024)03-0018-04DOI :10.19968/ki.hnkj.1003-5168.2024.03.004Simulation Analysis of Gas-liquid Two-phase Flow in Gear Forming Grinding Based on FLUENTYIN Mingyu YANG Jiazhao DU Zhengzheng XING Bo YANG Siyuan YANG Min(Industrial Center ,Nanjing Institute of Technology ,Nanjing 211167,China )Abstract: [Purposes ] This paper conducts the research on the problem of poor cooling effect and low sur⁃face liquid flow in gear grinding. [Methods ] The grinding flow field was simulated by setting different grinding wheel speed. The VOF gas-liquid two-phase flow model is used to simulate different nozzle po⁃sitions in the liquid flow field. [Findings ] The results showed that the rotation of the grinding wheel drove the surrounding gas to form a return flow, which prevented the jet from entering the grinding pro⁃cessing area. The fluid speed of the 30 m/s grinding wheel is 50% higher than that of the 20 m/s grinding wheel, which can meet the requirements of grinding processing and the return flow strength is moderate.The nozzle position of 40 mm vertical distance from the gear surface can better spray the grinding fluid to the grinding area, and the cooling effect is optimal. [Conclusions ] The optimal grinding wheel speed and nozzle position can provide certain guiding significance for the energy saving and consumption reduction in the actual processing.Keywords: gear; flow field; gas-liquid two-phase flow; simulation0 引言在齿轮磨削加工中,砂轮与齿轮经过滑擦、耕犁、切削三个阶段会产生大量的热,可能会引发齿轮表面烧伤、裂纹、应力集中等损伤[1-2]。
车用液力变矩器混合流道CFD仿真方法

989
中国机械工程第 27 卷第 7 期 2016 年 4 月上半月
问题,将传统变矩 器 流 道 模 型 和 导 轮 无 叶 片 模 型
有机结合,并根据 仿 真 和 实 验 数 据 制 定 模 型 选 择
方法,建立变矩器 混 合 流 道 模 型 进 行 多 工 况 动 态
交叉扩散项;
Sk 、
片流道模型(图1b)进行仿真,以变矩器变矩比 K
开始变为 1、导 轮 扭 矩 接 近 于 0 时 的 速 比 作 为 导
轮开始空转的速 比 点,并 与 从 液 力 变 矩 器 试 验 数
据中确定的偶合 器 工 况 转 换 点 进 行 对 比 验 证,如
图 2 所示.
∂u
∂p
2
V ∇ )
u= -
+ (
Sω 为用户自定义的源项.
2 偶合工况转换点
由于变 矩 器 的 通 用 特 性,变 矩 器 导 轮 开 始 空
过程仿真,并进行试验验证.
转的速比(偶合工况转换点)
io 随泵轮转速的变化
1 基本原理
动态工况变矩器内部液体流动是非稳态湍流
运动,可用非稳态的连 续 性 方 程 和 Nav
i
e
r
S
t
oke
t
i
on mode
lo
fhyd
r
odynami
c
t
o
r
r
t
e
rwa
se
s
t
ab
l
i
shed.Th
i
smode
lmi
tau
t
oma
t
i
c
a
l
- 1、下载文档前请自行甄别文档内容的完整性,平台不提供额外的编辑、内容补充、找答案等附加服务。
- 2、"仅部分预览"的文档,不可在线预览部分如存在完整性等问题,可反馈申请退款(可完整预览的文档不适用该条件!)。
- 3、如文档侵犯您的权益,请联系客服反馈,我们会尽快为您处理(人工客服工作时间:9:00-18:30)。
第23卷 第1期 石油化工高等学校学报 V ol.23 No.1 2010年3月 JO U RN AL O F P ET ROCH EM ICAL U N IV ERSIT IES M ar.2010文章编号:1006-396X(2010)01-0055-05摩擦液柱成形过程的二维CFD数值模拟陈忠海, 陈家庆*, 焦向东, 周灿丰, 关 佩, 高 辉(北京石油化工学院海洋工程连接技术研究中心,北京102617)摘 要: 采用G ambit软件建立了摩擦液柱成形(FH PP)过程流场的二维轴对称模型,运用商业计算流体动力学软件Fluent对FH PP稳态阶段塑性金属的流动情况进行了数值模拟。
通过改变模拟过程中的单一关键参数而保持其他参数不变,分别讨论了金属棒和孔洞之间径向间隙、材料粘度、金属棒转速、金属棒进给速度以及基材孔底形状等对理想金属塑性流体流动成形过程中速度场和压力场分布变化的影响。
结果发现,塑性金属材料的压力分布主要受进给速度(即轴向力)和材料粘度的影响,与金属棒的旋转速度和径向间隙关系不大;而速度分布受进给速度以及径向间隙的影响不明显,但与金属棒的旋转速度关系密切,尤其是靠近速度入口面以及金属棒附近的材料受旋转作用影响显著;通过改变基材孔洞底部的形状,可以改善塑性金属材料的流动情况,同时也揭示了实验过程中孔洞底部存在缺陷的原因。
关键词: 摩擦液柱成形; 摩擦叠焊; 计算流体动力学; 数值模拟中图分类号: T G404 文献标识码:A doi:10.3696/j.issn.1006-396X.2010.01.014T wo-Dimensional N um erical Sim ulation of Friction H ydro PillarProcessing by Com putational Fluid DynamicsCH EN Zhong-hai,CH EN Jia-qing*,JIAO Xiang-dong,ZH OU Can-feng,GUAN Pei,GAO H ui (Resear ch Centr e of Of f shore Engineer ing J oining T echnology,B eij ing I nstituteof P etr ochemical T echnology,Beij ing102617,P.R.China)Received22N ovember2008;r evised19S ep tember2009;accep ted9December2009Abstract: A t wo-dimensional ax isymmetr ic mo del o f fr ictio n hydro pillar processing(F HP P)w as established base on G ambit so ftwa re.U sing the co mmercial co mputational fluid dynamics soft war e Fluent,the numer ical simulation of plastic metal flow patter n w as car ried out in steady phase o f F HP P.W hile keeping the other parameter s constant ly during the process o f numerical simulation,the v elocity f ield and st atic pressur e field dist ributio n change of ideal metal plastic fluid during the form ing pro cess wer e analyzed by changing only one critica l parameter r espectiv ely,such as the radial clearance betw een metal stud and the base hole,the mat erial viscosity,the rota ry speed of metal stud,the feed rate of metal stud and the bott om shape of the base hole.T he result show that the static pressur e distributio n of plastic met al is affected remar kably by the feed rate(i.e.the axial fo rce)and the mater ial v iscosity of metal stud,and has little to do with the r otar y speed and the r adial clea rance. Although the feed r ate and the radial clear ance hav e little influence on the v elo city dist ribution of plast ic metal,the effect o f rot ary speed is relat ively remar kable,especially fo r the mater ial neig hbo ring to the w all o f the v elocit y inlet and nearby the met al stud.T he flo w conditio n o f the plast ic metal material can be impr oved by chang ing t he bo ttom shape of the base ho le, which can also rev eal the reason w hy there ex ist some defects at the bott om o f the hole.T he above-ment ioned research can pr ov ide some g uidance t o the future exper imental st udy adopting appr opriate par amet ric combination,and can also lay solid foundatio n fo r the futur e numerical simulation by thermo-mechanical coupling.Key words: F r iction hydro pillar pr ocessing(FH PP);F rict ion stitch welding;Co mputatio nal fluid dynamics;N umerical simulatio n*Co rr esponding author.T el.:+86-10-81292134;fax:+86-10-81292144;e-mail:Jiaqing@收稿日期:2008-11-22作者简介:陈忠海(1980-),男,浙江永嘉县,硕士,现在温州科技职业学院工作。
基金项目:国家自然科学基金项目(50675022);国家863计划海洋技术领域2006年度专题课题(2006A A09Z329);北京市属高等学校人才强教计划资助项目(N o.PH R200906214)。
*通讯联系人。
摩擦叠焊是由英国焊接研究所(TWI)发明的一种新型固相连接技术,在材料的成形加工尤其是钢结构的水下维修方面具有巨大的应用潜力[1]。
由于摩擦叠焊的基本成形单元为摩擦液柱成形(Fr ictio n H ydro Pillar Pro cessing,FH PP),一系列沿着预定轨迹相互搭接的FH PP便构成了摩擦叠焊,因此,就FH PP过程中塑性金属的流动、受力、产热等问题进行理论或实验研究,对于揭示摩擦叠焊的成形机理和连接特性具有重要意义。
本文首次通过商业计算流体动力学(CFD)软件对FH PP过程进行数值模拟,以期得到一些对实验研究具有参考和指导意义的结论,并为后续开展热力耦合的数值模拟奠定基础。
1 相关历史文献回顾采用商业CFD分析手段对摩擦焊接类固相连接过程中塑性金属的流动情况进行数值模拟是最近几年方兴起的研究工作,迄今主要结合搅拌摩擦焊(Fr ictio n Stir Welding,FSW)来开展。
2003年,美国南卡大学Rey no lds A P及Seidel T U等[2]基于流体力学理论,采用商业CFD软件建立了二维FSW成形过程模型,并通过改变材料特性和焊接参数预测了焊缝塑性金属的流动趋势。
研究表明,粘度在较高的温度和应变率情况下仍然非常大,可达10000Pa s,甚至更高;同时指出塑性金属的雷诺数很小(0.0001左右),以此来判定流动状态为层流而非紊流。
2004年前后,英国剑桥大学的Colegro ve P A 等[3-5]采用商业CFD软件建立了二维、三维FSW 成形过程模型。
二维数值模拟发现,利用滑动模型和粘性模型所得到的材料流动性差别比较大,在滑动模型中,搅拌头后方出现流线图膨胀现象,而前进侧出现材料的拖拽现象。
三维模型包括球状热源和搅拌头附近的局部热源两部分,模拟时采用的网格较为粗糙,搅拌头附近区域的一些重要细节均未考虑。
2006年,Colegr ove P A等[6]再次采用商业CFD软件对7449厚铝合金板的FSW成形过程进行了数值模拟。
对比了不同搅拌头横截面、转速所产生的影响,分析了不同搅拌头产生的压力分布与所引起的变形区域大小,以及如何减小搅拌头在焊接方向所受的压力,得出了合适的数值模拟模型和合理转速,并指出焊接过程中的产热量与搅拌头形状没有明显联系,与材料的塑性化有一定关系,而与轴肩接触面积的关系最为密切。
2006年,美国南卡大学的Long T等[7]对FSW 成形过程进行了二维数值模拟,主要研究了材料特性以及转速、焊接速度等参数变化对成形过程的影响。
模拟过程中的热量主要由流体粘性耗散产生,并将该模型看作是一系列粘弹流体通过一个旋转的锥形搅拌头。
结果发现,靠近搅拌头附近的流体温度远远高于其他位置。
同时在不同的焊接速度和旋转速度情况下,得到了3种比较典型的流线图,并在保持其他参数不变的情况下,分别分析了粘度、热耗散、轴向力产生的影响。