焊缝焊接探伤工艺
二级探伤焊缝焊接技巧

二级探伤焊缝焊接技巧如下:
1、垂直或倾斜位置开坡口的接头必须从下向上焊接,对不开坡口的薄板对接和立角焊可采用向下焊接;平、横、仰对接接头可采用左向焊接法。
2、有坡口的板缝,尤其是厚板的多道焊缝,焊丝摆动时在坡口两侧应稍作停留,锯齿形运条每层厚度不大于4mm,以使焊缝熔合良好。
3、根据焊丝直径正确选择焊丝导电咀,焊丝伸出长度一般应控制在10倍焊丝直径范围以内。
4、导电咀磨损后孔径增大,引起焊接不能稳定,需重新更换导电咀。
5、接缝长度超过1米以上,应采用分中对称焊法或逐步退焊法。
焊缝X射线探伤技术操作规定

焊缝X射线探伤技术操作规定一、为使国家有关标准在我公司X射线无损检测工作中的正确实施,确保产品质量,特制定了本规定,RT人员必须遵照执行。
二、探伤室根据委托单上的探伤要求,对工件进行RT检测。
作业班由2-3人组成,带班者必须有RT-Ⅱ资格证,并对本班工件质量及人身、设备安全负责。
三、根据工件的具体情况选用X光机,严格按使用X光机操作规程进行工作。
带班人要贯彻执行《X射线操作工艺》。
四、当被检工件、结构、材质、形状及焊接材料、工艺重大变化时,应作射线照相检验工艺评定,直到结果满足有关标准、技术文件的要求。
五、确保拍片质量的规定:⑴.底片上的定位标记和全部识别标记,应按规定摆放正确、齐全、一般不得用手写的方法,事后任意涂改或添补。
底片编号,铅皮尺不允许压焊缝。
底片编号见《焊接操作工艺》。
⑵.象质计必须放在射线源侧,被检区长度1/4处,钢丝应横跨焊缝并与焊缝方向垂直,细丝置外。
当射线源一侧无法放置象质计时,也可放在胶片一侧的表面上。
⑶.操作时,要注意调整机头,使射线束应指向被检部位中心,并在该点与被检区平面或曲面的切面垂直。
暗室处理严格按照操作规程进行,若黑度达不到应找原因。
⑷.所得射线底片不应有机械的、化学的或其它工艺性的雾迹、花纹、水迹、化学色素、划痕、指纹、邹折、污物等。
射线照相质量标准按JB4730-2005标准。
六、射线探伤原始记录及探伤报告规定。
射线探伤记录及拍片部位图是产品质量档案的重要资料之一,是填写产品出公司质保书、合格证的重要依据,要求会制部位图字体要工整、标记号码清晰。
部位图上应有符号说明及方位批示,缺陷返修情况。
底片及经有关人员签字的原始记录和检验报告必须妥善存七年以上,以备随时查核。
焊缝的超声波探伤及缺陷评定
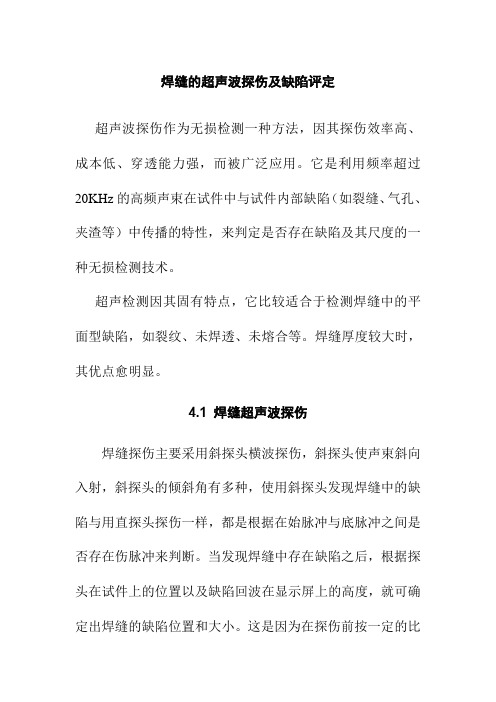
焊缝的超声波探伤及缺陷评定超声波探伤作为无损检测一种方法,因其探伤效率高、成本低、穿透能力强,而被广泛应用。
它是利用频率超过20KHz的高频声束在试件中与试件内部缺陷(如裂缝、气孔、夹渣等)中传播的特性,来判定是否存在缺陷及其尺度的一种无损检测技术。
超声检测因其固有特点,它比较适合于检测焊缝中的平面型缺陷,如裂纹、未焊透、未熔合等。
焊缝厚度较大时,其优点愈明显。
4.1 焊缝超声波探伤焊缝探伤主要采用斜探头横波探伤,斜探头使声束斜向入射,斜探头的倾斜角有多种,使用斜探头发现焊缝中的缺陷与用直探头探伤一样,都是根据在始脉冲与底脉冲之间是否存在伤脉冲来判断。
当发现焊缝中存在缺陷之后,根据探头在试件上的位置以及缺陷回波在显示屏上的高度,就可确定出焊缝的缺陷位置和大小。
这是因为在探伤前按一定的比例在超声仪荧光屏上作有距离—波幅曲线。
下面详细介绍。
(1)检测条件的选择由于焊缝中的危险缺陷常与入射声束轴线呈一定夹角,基于缺陷反射波指向性的考虑,频率不宜过高,一般工作频率采用2.0-5.0MHz:板厚较大,衰减明显的焊缝,应选用更低一些的频率。
探头折射角的选择应使声束能扫查到焊缝的整个截面,能使声束中心线尽可能与主要危险性缺陷面垂直。
常用的探头斜率为K1.5~K2.5。
常用耦合剂有机油、甘油、浆糊、润滑脂和水等,从耦合剂效果看,浆糊与机油差别不大,但浆糊粘度大,并具有较好的水洗性,所以,常用于倾斜面或直立面的检测。
(2) 检测前的准备(3)探测面的修整探测面上的焊接飞溅、氧化皮、锈蚀和油垢等应清除掉,探头移动区的深坑应补焊后用砂轮打磨。
探测面的修整宽度B应根据板厚t和探头的斜率K计算确定,一般不应小于2.5Kt。
(4)斜探头入射点和斜率的测定1) 斜探头的入射点测定。
斜探头声束轴线与探头楔块底面的交点称为斜探头的入射点,商品斜探头都在外壳侧面标志入射点,由于制造偏差和磨损等原因,实际入射点往往与标志位置存在偏差,因此需经常测定。
焊缝超声波探伤
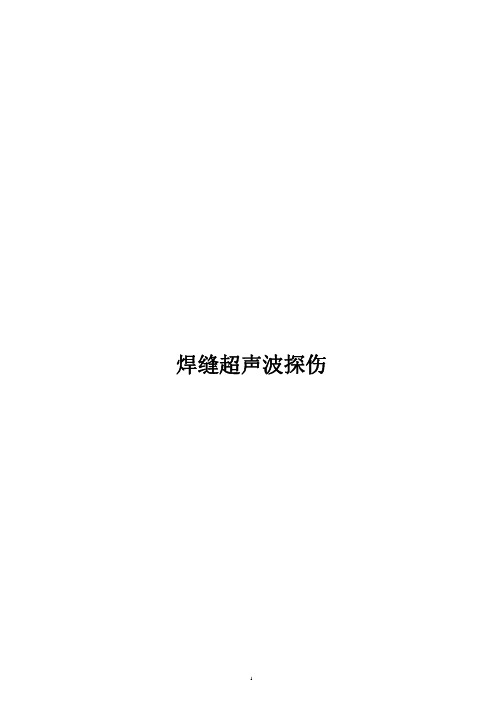
焊缝超声波探伤锅炉压力容器和各种钢结构主要是采用焊接的方法制造。
为了保证焊缝质量,超声波探伤是重要的检查手段之一。
在焊缝探伤中。
不但要求探伤人员具备熟练的超声波探伤技术。
而且还要求探伤人员了解有关的焊接基本知识,如焊接接头型式,焊接坡口型式、焊接方法和焊接缺陷等。
只有这样,探伤人员才能针对各种不同的焊缝,采用适当的探测方法,从而获得比较正确的探测结果。
第一节 焊接加工及常见缺陷锅炉压力容器及一些钢结构件主要是采用焊接加工成形的。
焊缝内部质量一般利用射线和超声波来检测。
对于焊缝中的裂纹、未熔合等危险性缺陷,超声波探伤比射线更容易发现。
一、焊接加工l.焊接过程常用的焊接方法有手工电弧焊、埋弧自动焊、气体保护焊和电渣焊等。
焊接过程实际上是一个冶炼和铸造过程,首先利用电能或其他形式的能产生高温使金属熔化,形成熔池,熔融金属在熔池中经过冶金反应后冷却,将两母材牢固地结合在一起。
为了防止空气中的氧、氮进入熔融金属,在焊接过程中通常有一定的保护措施。
手工电弧焊是利用焊条外层药皮高温时分解产生的中性或还原性气体作保护层。
埋焊和电渣焊是利用液体焊剂作保护层。
气体保护焊是利用氩气或二氧化碳等保护气体作保护层。
2.接头形式焊接接头形式主要有对接、角接、搭接和T型接头等几种:如图7.1所示。
在锅炉压力容器中,最常见的是对接,其次是角接和T型接头,搭接少见。
3.坡口形式为保证两母材施焊后能完全熔合,焊前应把接合处的母材加工成一定的形状,这种加工后的形状称为坡西,坡口各部分的名称如图7.2所示。
根据板厚、焊接方法、接头形式和要求不同,可采用不同的坡口形式。
常见对接和角接接头的坡口形式如图7.3所示。
二、焊缝中常见缺陷焊缝中常见缺陷有气孔、夹渣、未焊透、未熔合和裂纹等,如图7.4所示。
1.气 孔气孔是在焊接过程中焊接熔池高温时吸收了过量的气体或冶金反应产生的气体,在冷却凝固之前来不及逸出而残留在焊缝金属内所形成的空穴。
产生气孔的主要原因是焊条或焊剂在焊前未烘干,焊件表面污物清理不净等。
焊缝超声波探伤作业指导书

有限责任公司钢结构焊缝超声波探伤作业指导书编号:HHR/ZD-02编制:现场检测室审批:年月日钢结构焊缝超声波探伤指导书1、适用范围本指导书适用于一般工业与钢结构焊缝超声波探伤的检测。
2、依据标准GB/T11345—1989《钢焊缝手工超声波探伤方法和探伤结果分级》。
GB/T50621—2010《钢结构现场检测技术标准》。
JG/T203—2007《钢结构超声波探伤及质量分级法》。
GB 50205—2001《钢结构工程施工质量验收规范》。
3、仪器设备和人员的要求3。
1 钢结构检测所用的仪器、设备和量具应有产品合格证、计量检定机构出具的有效期内的检定(校准)证书,仪器设备的精度应满足检测项目的要求。
检测所用检测试剂应标明生产日期和有效期,并应具有产品合格证和使用说明书。
3.2 检测人员应经过培训取得上岗资格;从事钢结构无损检测的人员应按现行国家标准《无损检测人员资格鉴定与认证》GB/T 9445进行相应级别的培训、考核,并持有相应考核机构颁发的资格证书。
3.3 从事焊缝探伤的检验人员必须掌握超声波探伤的基本技术,具有足够的焊缝超声波探伤经验,并掌握一定的材料、焊接基础知识。
3。
4 焊缝超声检测人员应按有关规程或技术条件的规定经严格的培训和考核,并持有相应考试组织颁发的等级资格证书,从事相对考核项目的检验工作。
注:一般焊接检验专业考核项目分为板对接焊缝;管件对接焊缝;管座角焊缝;节点焊缝等四种。
3.5 取得不同无损检测方法的各技术等级人员不得从事于该方法和技术等级以外的无损检测工作。
3.6 现场检测工作应由两名或两名以上检测人员承担.3。
7 超声检验人员的视力应每年检查一次,校正视力不得低于1。
0。
4、检测钢结构焊缝超声波探伤时,基本要求4.1 现场调查宜包括下列工作内容:1 收集被检测钢结构的设计图纸、设计文件、设计变更、施工记录、施工验收和工程地质勘察报告等资料;2 调查被检测钢结构现状,环境条件,使用期间是否已进行过检测或维修加固情况以及用途与荷载等变更情况;3 向有关人员进行调查;4 进一步明确委托的检测目的和具体要求;4.2 检测项目应根据现场调查情况确定,并应制定相应的检测方案.检测方案宜包括下列主要内容:1 概况,主要包括设计依据、结构形式、建筑面积、总层数,设计、施工及监理单位,建造年代等;2 检测目的或委托方的检测要求;3 检测依据,主要包括检测所依据的标准及有关的技术资料等;4 检测项目和选用的检测方法以及检测数量;5 检测人员和仪器设备情况;6 检测工作进度计划;7 所需要委托方与检测单位的配合工作;8 检测中的安全措施;9 检测中的环境措施。
焊缝探伤报告
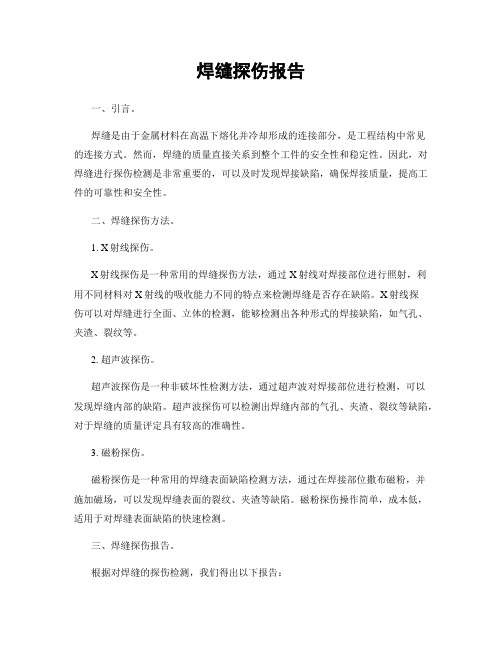
焊缝探伤报告一、引言。
焊缝是由于金属材料在高温下熔化并冷却形成的连接部分,是工程结构中常见的连接方式。
然而,焊缝的质量直接关系到整个工件的安全性和稳定性。
因此,对焊缝进行探伤检测是非常重要的,可以及时发现焊接缺陷,确保焊接质量,提高工件的可靠性和安全性。
二、焊缝探伤方法。
1. X射线探伤。
X射线探伤是一种常用的焊缝探伤方法,通过X射线对焊接部位进行照射,利用不同材料对X射线的吸收能力不同的特点来检测焊缝是否存在缺陷。
X射线探伤可以对焊缝进行全面、立体的检测,能够检测出各种形式的焊接缺陷,如气孔、夹渣、裂纹等。
2. 超声波探伤。
超声波探伤是一种非破坏性检测方法,通过超声波对焊接部位进行检测,可以发现焊缝内部的缺陷。
超声波探伤可以检测出焊缝内部的气孔、夹渣、裂纹等缺陷,对于焊缝的质量评定具有较高的准确性。
3. 磁粉探伤。
磁粉探伤是一种常用的焊缝表面缺陷检测方法,通过在焊接部位撒布磁粉,并施加磁场,可以发现焊缝表面的裂纹、夹渣等缺陷。
磁粉探伤操作简单,成本低,适用于对焊缝表面缺陷的快速检测。
三、焊缝探伤报告。
根据对焊缝的探伤检测,我们得出以下报告:1. 焊缝内部存在气孔和夹渣,对焊接质量造成一定影响,需重新进行焊接处理。
2. 焊缝表面存在裂纹,需要进行修补处理,确保焊缝的完整性和稳定性。
3. 焊缝连接部位存在局部变形,需要重新进行焊接处理,确保焊接部位的稳固性。
四、结论。
焊缝探伤是确保焊接质量的重要手段,通过对焊缝的全面检测,可以及时发现焊接缺陷,保证焊接质量,提高工件的可靠性和安全性。
在进行焊接工艺时,需要严格按照工艺要求进行操作,确保焊接质量,减少焊接缺陷的产生。
五、致谢。
感谢对本次焊缝探伤工作给予支持和帮助的各位专家和同事,在他们的指导和帮助下,我们完成了本次焊缝探伤工作,并得出了相应的报告。
六、参考文献。
[1] 焊接工程手册。
[2] 焊接质量检测技术。
[3] 焊接工艺规程。
以上就是本次焊缝探伤报告的全部内容,希望能对大家有所帮助。
焊缝超声波探伤检验规程

焊缝超声波探伤检验规程1 目的指导本公司无损探伤人员工作,规范无损探伤的检验过程。
2 范围本程序适用于公司钢结构产品制造(包括外包外协件)中的无损检验工作。
3 职责3.1品保部探伤员Ⅰ、Ⅱ、Ⅲ级人员负责探伤工作的实施。
3.2品保部探伤员Ⅱ、Ⅲ级人员负责检验规程的编制、现场检测技术指导。
3.3品保部负责无损探伤的质量控制工作,对无损探伤中有争议的问题做出裁决。
3.4品保部负责自检报告的签发。
4 检验规程4.1探伤准备工作a) 距离一波幅曲线:利用RB-1或RB-2试块测试距离一波幅曲线,评定线、定量线和判废线满足GB11345-89标准中9.2.1的B级要求。
b) 探伤灵敏度:不低于评定线,扫查灵敏度在基准敏度上提高6dB。
c) 探伤时机:碳素结构钢应在焊缝冷却到环境温度,低合金结构钢应在完成焊接24小时后进行探伤;另外,探测要经过打磨,外观检验合格后进行探伤。
d) 探伤方式和扫查方式:探伤方式见:扫查方式有锯齿形扫查、前后、左右、环绕、转角扫查等几种方式。
e) 检查部位:检查部位根据GB50205-2001《钢结构工程施工质量验收规范》及设计文件、工艺文件。
f) 抽检率:当设计和合同未对抽检率做出规定时,按GB50205-2001《钢结构工程施工质量验收规范》表5.2.4,当设计和合同对抽检率做出规定时,按设计和合同执行。
4.2探伤方法4.2.1平板对接焊缝a) 探头选择探头的K值选择如表1。
表1 探头的K值根据厚度不同按下表选择图1 平板对接焊缝的超声波探伤4.3.2 T型接头焊接的检验按T型焊缝的特点及GB11345-89标准要求,选择以下三种探伤方式组合实施检验。
4.3.2.1焊缝内部缺陷检测a) 探头选择见(表2)b) 根据不同检验等级要求选择探伤面,探伤面如图1所示。
表2 探头的K值根据腹板厚度不同按下表选择b) 探测位置c) 对所有反射波幅超过定量线的缺陷,均应确定其位置,最大反射波幅所在区域和缺陷指示长度。
焊缝探伤检测方法

焊缝探伤检测方法焊接是制造业中常见的连接工艺,而焊缝的质量直接影响着焊接件的性能和安全性。
因此,对焊缝进行探伤检测是非常重要的。
本文将介绍几种常见的焊缝探伤检测方法,以供参考。
首先,常见的焊缝探伤检测方法之一是磁粉探伤。
这种方法利用磁粉在外加磁场下的磁性特性,通过磁粉在缺陷处的聚集来发现焊缝中的裂纹、夹杂等缺陷。
这种方法简单易行,对表面缺陷的检测效果较好,但对于深层缺陷的检测能力有限。
其次,超声波探伤是另一种常用的焊缝探伤方法。
超声波探伤利用超声波在材料中的传播和反射特性来检测焊缝中的缺陷。
这种方法可以对焊缝进行全面、非破坏性的检测,对于各种形式的缺陷都有较好的检测能力。
但是,超声波探伤对操作人员的技术要求较高,且对焊缝的几何形状和材料性质有一定的限制。
另外,涡流探伤也是一种常见的焊缝探伤方法。
涡流探伤利用交变磁场在导电材料中产生涡流的原理,通过检测涡流的变化来发现焊缝中的缺陷。
这种方法对于表面和近表面的缺陷有较好的检测能力,对于导电性好的材料也有较好的适用性。
但是,对于非导电材料和厚度较大的材料,涡流探伤的效果就会大打折扣。
最后,X射线探伤也是一种常用的焊缝探伤方法。
X射线探伤利用X射线在材料中的透射和吸收特性来检测焊缝中的缺陷。
这种方法可以对焊缝进行全面、深层的检测,对于各种形式的缺陷都有较好的检测能力。
但是,X射线探伤设备价格昂贵,操作复杂,对操作人员的技术要求也很高。
综上所述,不同的焊缝探伤方法各有优劣。
在实际应用中,需要根据具体的焊接工艺、焊缝形式和材料性质选择合适的探伤方法。
同时,对于复杂的焊缝结构,也可以采用多种探伤方法相结合的方式,以提高检测的准确性和全面性。
希望本文介绍的焊缝探伤检测方法能对相关人员有所帮助。
- 1、下载文档前请自行甄别文档内容的完整性,平台不提供额外的编辑、内容补充、找答案等附加服务。
- 2、"仅部分预览"的文档,不可在线预览部分如存在完整性等问题,可反馈申请退款(可完整预览的文档不适用该条件!)。
- 3、如文档侵犯您的权益,请联系客服反馈,我们会尽快为您处理(人工客服工作时间:9:00-18:30)。
焊缝超声波检测工艺焊缝超声波检测工艺锅炉、压力容器主要是采用焊接加工形成的。
焊缝内部质量主要利用射线和超声波来检测。
但对于焊缝中的裂纹、未焊透等危险性缺陷,超声波检测出射线更容易发现。
为了有效地检出焊缝中的缺陷,检测人员除了具备超声波检测的测试技术外,还应对焊接过程、焊接接头和坡口形式以及焊缝中常见缺陷有所了解。
,o"[9F)_$p.V'N,E(W,y#N1.对接焊缝超声波检测方法-B7{*R1|:P/L(1)检测频率、探头、仪器要求"G;f&P7U4Y对接焊缝超声波检测时通常采用2.5MHZ横波斜探头检测。
在某些特殊场合下也可采用5MHZ或1.25MHZ的探头。
在检测时探头工作频率应符合所选用的检测频率,其误差不得超过4%-5%(缺陷定量精度要求为±1dB)。
JB4730-1994标准《锅炉和钢制压力容器对接焊缝超声波探伤》规定:横波斜探头K值选择应符合下表规定。
在检测条件许可的情况下,应尽量采和K值较大的斜探头检测以提高面积形缺陷(如裂缝)的检测能力。
带有曲率工件的超声波检测时,探头与工件表面接触面积的尺寸将直接影响超声耦合,致使耦合损耗增加,为此在带有曲率工件的焊缝超声波检测时,应尽可能采用接触面尺寸(探头与工件表面接触的底面尺寸)较小的探头检测。
为了保证缺陷测定数据的正确性及可靠性,对接焊缝超声波检测时,仪器与探头组合后的基本性能要求见下表。
$a8x+J5~7y+B6k4J.l9d$P0I斜探头K值选择(JB4730-1994)仪器与探头组合后的基本性能要求:(2)控测方向和检测面选择6F)K6v4B8~;W!d探测方向和检测面应按被检测焊缝中可能产生的裂纹、未熔合的方向选择,尽可能采用K值较大的探头(减小声波入射缺陷的角度)进行超声波检测。
JB4730-1994标准规定:$|r)x'J,Q(H+J&f①母材厚度为8-46mm的对接焊缝,在焊缝单面两侧用一种K 值的横波斜探头,在一次波和二次波的位置上探测。
探头移动范围为:$hB3n(g-v$@!O|S1≥2δK+50(mm)4H(H,L+e-B;R.n式中-b#n5i7R.Q;iS1—探头移动范围长度,mm;:w3z.^9]8S#Iδ—工件材料厚度,mm;1P"y5e7S!vK—斜探头K值(\'M*M'x3i②母材厚度为46-120mm的对接焊缝,在焊缝两面侧用两种K值斜探头,在一次波位置上探测。
探头移动范围为:!Y6e$~8{:F#j1pS2≥δK+50(mm)!S6i)F%x*{式中7G:E!|'W-S%N8]/`S2—探头移动范围长度,mm;,^5C6Z*a$e*O"[(Cδ—工件材料厚度,mm;/Y8K#f,x5{8]6\$k(|2^K—斜探头K值4X,TT2b+p2}$N1j!c检测焊缝中横向缺陷时,基本上有下列三种情况:8G8V2i9?&~①在已磨平焊缝加强层及热影响区域表面上以一种(或两种)K值的斜探头,用一次波在焊缝区域两面作正反两个方向的探测。
#X+F*Y1z3~$M$G②当焊缝加强层因受限于某些条件不能磨平时可用一种(或两种)K值的斜探头,用一次波在焊缝两面两侧进行斜平行扫查、扫查时探头声束中心轴线与焊缝中心线夹角小于100。
:p9@5o!{1[③电渣焊缝中经常产生呈八字形分布的裂纹,可用一种(或两种)K值的斜探头在声束轴线与焊缝中心线夹角为450的方向上,在焊缝两面两侧进行斜平行扫查。
-d2t,p']0d$Z(3)探头扫查方式4kf%e8W!CY"o(t焊缝超声波检测探头基本扫查方式主要有:前后扫查;左右扫查;围绕扫查;转动扫查。
在焊缝超声波检测时,探头在探测面上的移动范围长度按式要求计算。
探头在扫查过程中,扫查速度不超过150mm/s,且每相邻两次扫查有10%-20%的覆盖区域。
+l-[&u7~4@5C%p^+y(4)检测灵敏度较准1k,_7d2o&i9]5T+m焊缝超声波检测时按JB4730-1994标准规定:检测灵敏度应在CSK-ⅡA型长横孔试块或CSK-ⅢA型短横孔试块上根据距离一波幅曲线图的灵敏度进行较准。
在实际超声检测操作中,应考虑试块及被探工件材质和表面粗糙度不同引起的材质衰减以及表面耦合差异补偿。
利用JB4730-1994标准规定的DAC曲线图校准检测灵敏度如下表15所示。
8w*R,`x.a,x.R'V4|距离—波幅曲线的灵敏度(JB4730-1994)表15!P6o5g)T7|2P4O0R&r②在SG-Ⅱ试块上选择合适深度的横孔作为参考基准点(如深度为20mm的¢2mm横孔)。
4j&I1m:a+e(v1@③DAC曲线图的评定查阅参考基准点A的dB值及A点至评定线的dB值。
2`$R*['r%l!|-]7y④在DAC曲线图的评事实上线上查阅与最大声程对应的工件材料厚度(或水平跨距)处的dB(c)值(C)。
'C9_+S-[)f)u1S*K7`⑤确定工件与试块表面的耦合损耗补偿修正量(dB2)。
.`(~"TG%Z;O,a)H/H:E⑥计算工件与试块材料超声波衰减补偿修正量(dB3)。
,K4P8M;A!g5?.m7y%g⑦仪器衰减器上读数调节为:6n+n2@&V;F8W)G9~6{∑dB=dB(C)+dB2+dB35Q7Y/J%X:`⑧探测SG-Ⅱ试块上深度为20mm的¢2mm横孔,调节仪器增益旋钮,使其反射回波高度为示波屏满幅度的80%(或50%)。
,{3?7p'i;g#v:^8p)j4W⑨调节衰减器指示值为dB(C)即达到标准要求的检测灵敏度。
4E*]:s3d,A;M%K(5)缺陷指示长度测定9Z2x.~,O(~*[5l按JB4730-1994标准规定缺陷指示长度测定方法为:当缺陷反射回波只有一个峰值时,用半波高度法(6dB法);当缺陷反射回波有多个峰值时,端点反射回波幅度超过定量线时用缺陷端点法测定。
&?;M+O(F%B5F6_①半波高度法(6dB法)由于波高降低原来的一半正好为6dB,因此半波高度法又称为6dB法。
半波高度法具体做法是:移动探头找到最大反射波(不能达到饱和),然后沿缺陷方向左右移动探头,当缺陷波高降低一半时,探头中心线之间距离就是缺陷的指示长度。
6dB法的具体做法是:移动探头找到缺陷的最大反射波后,调节衰减器,使缺陷波高降至基准波高。
然后用衰减器将仪器灵敏度提高6dB,沿缺陷方向移动探头,当缺陷波高降至基准波高时,探头中心线之间距离就是缺陷的指示长度。
$L*l3k,x:[*@#s)t,d!Q②端点半波高度法(端点6dB法)当缺陷各部分反射波有多个高点时,测长采用端点半波高度法。
端点半波高度法测长具体做法是:当发现缺陷后,探头沿着缺陷方向左右移动,找到缺陷两端的最大反射波,分别以这两个端点反射波高为基准,继续向左、向右移动探头,当端点反射波高降低一半时(6dB时),探头中心线之间的距离即为缺陷的指示长度。
)T't5Y2C(j%Y3V"u8?9s1c2.大口径管座角焊缝超声波检测6z"j3e6w!Y-Z2i,w 超声波检测中,大口径管一般是指明外径大于100mm的管材。
在锅炉、压力容器等产品中,大口径管座焊缝结构形式及危害性缺陷(裂缝)焊缝中常见的裂缝主要是工件(或管座)材料的层间撕裂以及焊缝内部裂缝。
)`2C'Y2k9x/i(1)检测工艺7q*m%T:\7H2H管座角焊缝超声波检测时,通常采用2.5MHz频率进行检测,通常采用化学糨糊或机油作为耦合剂。
按JB3144-1982《锅炉大口径管座角焊缝超声波探伤》标准规定,在检测中可采用软保护膜单晶片直探头或双晶片直探头,为了获得良好的声耦合,标准推荐使用专用的晶片尺寸为8mm*9mm,与工件接触面尺寸为10mm*16mm的软保护膜单晶片纵波直探头。
若需要使用斜探头(横波)作辅助检测时,斜探头与工件接触面尺寸应符合下式的要求:"c4[5s-j!A0La(或b)≤R/2)c%Q"t,_!t5V式中*q-_2H&iOz8R#wa—斜探头底面长度,mm;#L(g'c;A/c)_Mb—斜探头底面宽度,mm;8o._'d7F-V1^.f"\(^R—检测面曲率半径,mm。
1h'^'R+i%D'\4G-Y按JB3144-1982标准规定,大口径管座角焊缝超声波检测时,以直探头(纵波)检测为主,在直探头不可探测区域(由产品几何尺寸及声束特性限制)以斜探头(横波)作辅助检测。
若产品技术条件中规定要求探测管座角焊缝中的横向缺陷时,应将筒体内壁焊缝加强层,磨平后用斜探头(横波)在焊缝表面上作正、反两个方向的探测。
直探头纵波检测时可采用工件或试块底面(包括工件圆柱曲底面)反射回波进行时基线校准。
斜探头横波检测时时基线校准则按JB4730-1994标准规定执行。
直探头纵波检测时,使用工件圆柱形曲底面作为参考反射体,并使用计算法校准仪器检测灵敏度。
也可采用带有工件曲率半径相同的平底孔试块,以平底孔作为参考反射体结合计算进行灵敏度较准。
实际检测中具体要求的检测灵敏度为:6f&W)Av(X7V0w7P评定灵敏度:平底孔¢2mm-6dB5o$?D!X,x+Q'c定量灵敏度:平底孔¢3mm5`$M0E3n2h;L&V+F判废灵敏度:平底孔¢6mm%l"K'd/s&R;h!l(t*Y斜探头横波检测时,按JB4730-1994标准中有关条文规定进行检测灵敏度校准。
无论直探头检测还是斜探头检测,其探测灵敏度不得低于评定灵敏度。
缺陷指示长度测定方法主要按JB4730-1994标准规定。
但可以允许使用可行的其他测试方法及手段进行测定。
对于相同深度的两个相邻缺陷间距小于其中较长者,则可作为一个缺陷处理,并以缺陷累计指示长度作为该缺陷指示长度;如大于较长者,则以两个缺陷处理,分别测试其指示长度。
*K;d#y2s1[(2)焊缝质量评定;u;n.I:^9K9?!P按JB3144-1982标准规定的焊缝质量评定:1Y.Q-]-`%f2m3i1)缺陷判废区3@#uG'k8R-z;|在焊缝两熔合线(返修后复探时为返修焊补的熔合线)以外5mm内的区域均作为焊接缺陷的判废区域。
在焊接缺陷的判废区中不允许存在下列缺陷:-^%\/|/M(])y/u)d(J:~①纵向缺陷5D5}'e$z8P*Ia.缺陷反射回波当量达到超过判废区灵敏度者。
b.缺陷反射回波当量达到或超过定量灵敏度,但低于判废灵敏度而指示长度L ≥δ/3,且最小可为10mm,最大不超过30mm者(δ为焊缝截面中心线的高度,包括焊缝加强层高度)。