涤纶筒子染色常见问题分析
影响涤纶DTY染色均匀性的问题分析

影响涤纶DTY染色均匀性的问题分析涤纶DTY是一种化学纤维,具有强度高、耐磨损、耐化学腐蚀等优点。
在纺织行业中得到了广泛应用,尤其是在纺织品染色中。
然而,涤纶DTY染色的过程中,容易出现染色不均匀的问题。
这个问题对于生产和加工而言是非常棘手的,因为它会降低染色品质、裸露出白点和色差,影响产品的美观度。
本文将会探讨影响涤纶DTY染色均匀性的问题的原因和解决方法。
原因分析1.染料选择不当染色剂是染色过程中最关键的部分之一,选择不当可能会导致染色不均匀。
染色剂的颜色浓度、温度和染液的PH值等都会影响染色剂的效果。
若染色剂不配合涤纶DTY的物理特性,如硬度和垂度的差异等,就很容易引起染色不均匀的问题。
2.预处理不当涤纶DTY染色前,需要对其进行预处理,包括脱油、漂白、Mercerizing等处理。
如果预处理的时间不够、浓度不够导致残留等情况,都有可能影响涤纶DTY染色的均匀性。
3.工艺参数不精确染色工艺是非常复杂的,染色温度、染液比例、染色机器的转速等都会影响涤纶DTY的染色效果。
如果工艺参数不精确,就可能导致染色不均匀。
4.设备问题涤纶DTY的染色需要使用染色机器,如果机器性能有问题,比如旋转不稳定,或染色流程出现问题等都有可能导致涤纶DTY染色的不均匀性。
解决方法1.染料选择合适在选择染料时,需要考虑到其颜色浓度、温度,以及和涤纶DTY物理特性的配合。
在选取染料剂之前,建议通过试验检测,选择一种性能稳定的染料。
2.加强预处理在涤纶DTY染色之前,要对其进行足够充分的预处理,确保清洁度、柔软度、可染性等,防止残留导致染色不均匀。
3.精确控制工艺参数在染色过程中,需要精确控制染色温度、染液比例、染色机器转速等参数,防止其偏差导致染色不均匀。
4.设备维护对涤纶DTY染色过程中的设备进行维护和保养,比如清理机器、保持相对湿度等可以有效防止设备偏差影响染色均匀性。
结语涤纶DTY染色不均匀对于纺织企业生产和加工都是非常不利的,因此需要重视该问题的解决。
涤纶化学工艺常见问题分析

涤纶化学工艺常见问题分析摘要随着科技的发展,染色设备的不断提高,涤纶筒子纱的染色,如高温高压染色,它工艺简单,操作方便。
涤纶筒子纱高温高压染色中往往会出现诸如大样与原样有很大的差异,如走样(色相不对),色光的偏差等问题。
解决涤纶染色工艺中的诸多问题,对于提高企业的利润,赢得市场是至关重要的。
关键词涤纶;色差;工艺1碱处理涤纶主要化学成份聚对苯二甲酸乙二醇酯,一般在红外光谱图中无大量羟基峰存在。
在碱处理后如果涤纶分子链断裂水解羟成对苯二甲酸钠和乙二醇,红外光谱中的羟基峰将有所增加。
对比涤纶纤维碱处理前后的红外吸收光谱,-OH基的特征吸收峰在3350厘米-1附近无明显的变化,表示碱处理后羟基无明显增加,涤纶分子链无明显断裂现象,化学作用仅在表面进行,未深入到分子内层。
表1为涤纶线样品,经不同碱处理时间后分子量变化表,根据表1数据分忻,在碱处埋过程中,各阶段的分子量,包括重均分子量、数均分子量、粘均分子量以及分子量分布等都变化不大,表明碱处现对涤纶分子量影响不大,碱液对涤纶无明显的降解作用。
从数据分析,处理15分钟以后,低分子物含量略有下降,可能由于涤纶中原有少量低聚物先行溶解,以后经30、60、120和240分钟处理后,低聚物由于热与碱的作用,又逐步略育增加,但因总的低聚物含量很低,在碱处理过程中含量的变化,还不足以单独说明质量的变化。
2pH值中酸性染色和碱性染色工艺的比较1)中酸性染色。
碱减量→水洗→中和→酸性pH值染色→水洗→还原净洗→水洗→中和→烘干→增深(浸轧DEEPART BL或BUILDER RN)→烘干→整理(浸轧柔软剂、抗静电剂)→热处理。
2)碱性染色。
碱减量→水洗→碱性pH值染色→水洗→烘干→增深(浸轧BUILDER RN-1)→烘干→整理(浸轧柔软剂、抗静电剂)→热处理。
3)工艺比较。
碱性染色法工序简短,加工成本低,但是易引起“头梢色差”等染色问题。
而且用碱性染色法染色的布留有较多的碱成分,增深加工浸轧液的pH值易转化成碱性。
阳离子可染涤纶染色不匀的成因及控制
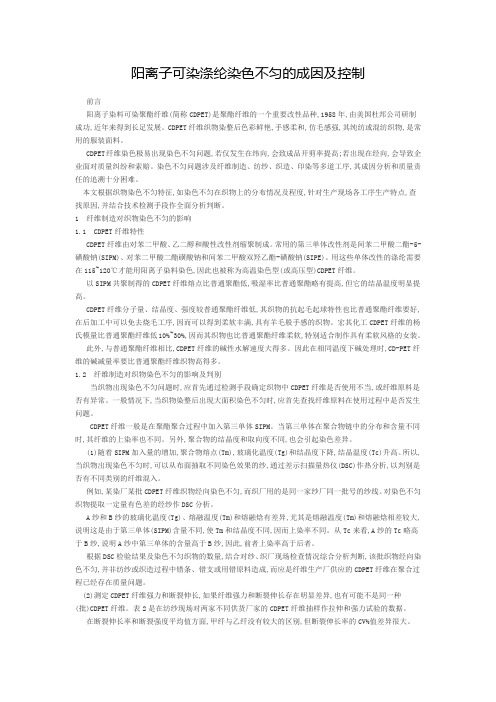
阳离子可染涤纶染色不匀的成因及控制前言阳离子染料可染聚酯纤维(简称CDPET)是聚酯纤维的一个重要改性品种,1958年,由美国杜邦公司研制成功,近年来得到长足发展。
CDPET纤维织物染整后色彩鲜艳,手感柔和,仿毛感强,其纯纺或混纺织物,是常用的服装面料。
CDPET纤维染色极易出现染色不匀问题,若仅发生在纬向,会致成品开剪率提高;若出现在经向,会导致企业面对质量纠纷和索赔。
染色不匀问题涉及纤维制造、纺纱、织造、印染等多道工序,其成因分析和质量责任的追溯十分困难。
本文根据织物染色不匀特征,如染色不匀在织物上的分布情况及程度,针对生产现场各工序生产特点,查找原因,并结合技术检测手段作全面分析判断。
1 纤维制造对织物染色不匀的影响1.1 CDPET纤维特性CDPET纤维由对苯二甲酸、乙二醇和酸性改性剂缩聚制成。
常用的第三单体改性剂是间苯二甲酸二酯-5-磺酸钠(SIPM)、对苯二甲酸二酯磺酸钠和间苯二甲酸双羟乙酯-磺酸钠(SIPE)。
用这些单体改性的涤纶需要在115~120℃才能用阳离子染料染色,因此也被称为高温染色型(或高压型)CDPET纤维。
以SIPM共聚制得的CDPET纤维熔点比普通聚酯低,吸湿率比普通聚酯略有提高,但它的结晶温度明显提高。
CDPET纤维分子量、结晶度、强度较普通聚酯纤维低,其织物的抗起毛起球特性也比普通聚酯纤维要好,在后加工中可以免去烧毛工序,因而可以得到柔软丰满,具有羊毛般手感的织物。
宏其化工CDPET纤维的杨氏模量比普通聚酯纤维低10%~30%,因而其织物也比普通聚酯纤维柔软,特别适合制作具有柔软风格的女装。
此外,与普通聚酯纤维相比,CDPET纤维的碱性水解速度大得多。
因此在相同温度下碱处理时,CD-PET纤维的碱减量率要比普通聚酯纤维织物高得多。
1.2 纤维制造对织物染色不匀的影响及判别当织物出现染色不匀问题时,应首先通过检测手段确定织物中CDPET纤维是否使用不当,或纤维原料是否有异常。
涤纶筒子染色常见问题分析

涤纶筒子染色常见问题分析----江苏旷达实验室张凤涤纶织物由于强度高,回弹性好,耐磨性优良,尺寸稳固性好,抗皱性好,而被普遍应用于各类纺织品及服装面料。
涤纶筒子纱线染色是采纳高温高压染色法在高温高压筒子纱染色机上进行的。
由于聚酯纤维结构超级紧密,分散染料在低温条件下几乎是不上染。
涤纶筒子纱染色是在必然的温度下,利用染色机主泵的压力作用使染液穿透卷绕在具有多孔不锈钢筒管上的纱线层,使分散染料的分子与纤维不断接触,染料第一是被纤维外层吸附,继而再向纤维内部扩散而达到上染得目的。
我公司主若是ATY、DTY,现就这几年我公司常见染色问题论述以下两点:一、阻碍筒子纱匀染性的因素及预防方法较高的染液循环频率和较低的染料吸收速度是筒子纱匀染的重要条件。
染料的吸收速度除受纤维及染料本身特性的阻碍外,它还受助剂、染液温度、PH值等因素的阻碍。
在实际生产中阻碍筒子纱匀染的因素是相当复杂的,那个地址以筒子纱染色时大体的操作因素为主,来论述它们对筒子染色进程中匀染情形的阻碍。
这些因素是筒子纱的染液流速或染液循环频率、染色时染液的升温速度、筒子纱卷绕密度等。
一、阻碍筒子纱匀染性的因素A、每循环上染率对匀染的阻碍由于纤维对染料的吸收作用,染液内染料浓度在染液流向方向上慢慢减少,引发染液流向下方纤维时染料的吸收量下降,即染料的吸尽作用。
反映染料吸尽作用最直接的指标是染液每循环一次纤维吸收染料的百分率,即每循环上染率。
每循环上染率越大,吸尽作用越强烈,所得的筒子纱匀染性越差。
B、流速对匀染程度的阻碍通过筒子纱的染液流速或筒子纱染色时染液的循环频率,是决定筒子纱染色质量的重要参数。
同一纤维品种用一样的染化料在相同条件下染色时,染料的最终平稳上染率是不变的,而达到匀染所需要的时刻随染液流速的增加而减小。
也确实是说,在相同的染色时刻内,流速越高,筒子纱的匀染程度就越好;流速越低,筒子纱的匀染程度就越差;但流速过大易显现毛羽等疵病,因此,操纵好流速也是超级重要的,一样是要操纵在25~30 L·(min.kg)。
筒子纱染色如何避免染色上色不匀、白节白点、色渍色斑
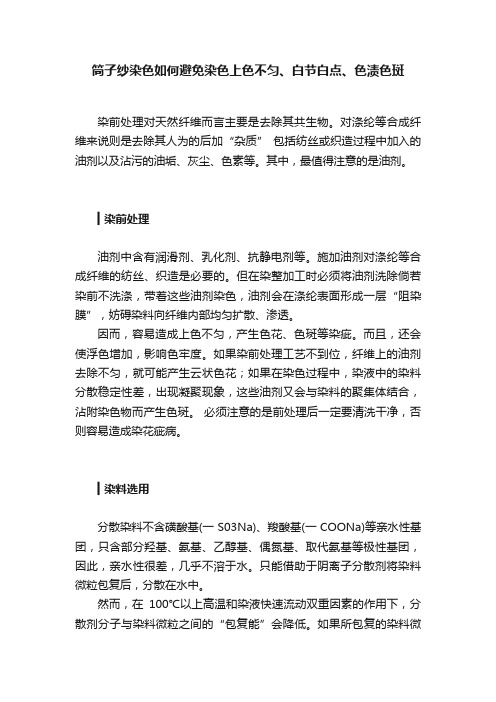
筒子纱染色如何避免染色上色不匀、白节白点、色渍色斑染前处理对天然纤维而言主要是去除其共生物。
对涤纶等合成纤维来说则是去除其人为的后加“杂质” 包括纺丝或织造过程中加入的油剂以及沾污的油垢、灰尘、色素等。
其中,最值得注意的是油剂。
▎染前处理油剂中含有润滑剂、乳化剂、抗静电剂等。
施加油剂对涤纶等合成纤维的纺丝、织造是必要的。
但在染整加工时必须将油剂洗除倘若染前不洗涤,带着这些油剂染色,油剂会在涤纶表面形成一层“阻染膜”,妨碍染料向纤维内部均匀扩散、渗透。
因而,容易造成上色不匀,产生色花、色斑等染疵。
而且,还会使浮色增加,影响色牢度。
如果染前处理工艺不到位,纤维上的油剂去除不匀,就可能产生云状色花;如果在染色过程中,染液中的染料分散稳定性差,出现凝聚现象,这些油剂又会与染料的聚集体结合,沾附染色物而产生色斑。
必须注意的是前处理后一定要清洗干净,否则容易造成染花疵病。
▎染料选用分散染料不含磺酸基(一S03Na)、羧酸基(一COONa)等亲水性基团,只含部分羟基、氨基、乙醇基、偶氮基、取代氨基等极性基团,因此,亲水性很差,几乎不溶于水。
只能借助于阴离子分散剂将染料微粒包复后,分散在水中。
然而,在100℃以上高温和染液快速流动双重因素的作用下,分散剂分子与染料微粒之间的“包复能”会降低。
如果所包复的染料微粒游离出来,就会重新聚集成更大的染料颗粒。
这种现象即为分散染料的“高温凝聚性”不同结构的分散染料,其热凝聚现象不同。
大体可分三种:一为不易发生热凝聚。
这类染料不会因升温、降温或相互碰撞而凝聚。
使用这样的染料染色一般不会造成染色不匀或色斑色渍。
二为容易发生热凝聚但随着染料分子向纤维内部扩散,染料的聚集体会再度解聚,只要染料在纤维表面吸附均匀,一般就不会造成色花、色渍。
三为容易发生热凝聚,而且在染色过程中,又难以解聚。
使用这类染料染色时,特别是当使用的分散剂或匀染剂高温分散能力较差时,就很容易由于染料的热凝聚而造成色泽不匀。
涤纶筒子纱染色出现内外层差如何解决?

涤纶筒子纱染色出现内外层差如何解决?
筒子纱染色很容易出现内外层色差,杭州绿典化工认为,这主要是受到染料的性能、染色设备和匀染剂的效果这三方面的影响。
首先染料的分散性差,导致染料很容易凝聚,不能很好的分散在水中,就很容易导致色花和内外层差;
其次染色的设备主要是保持染浴能循环均匀,保证染料能均匀被纱线吸附;
最后匀染剂主要是解决染料的分散性、缓染性、移染性问题,可以促进染料均匀的分散、减缓染料的上染速率、即时色花也能把染料重新均匀的分散在纱线上。
前两个问题可能是很难改变,因为染料本身性能决定、设备不能轻易更换,那么确保使用性能良好的匀染剂是最有效、成本最低的一种减少色花的方法。
高温匀染剂LD-LP.Conc 缓染性能优秀、分散性极好、移染性超强,可以确保染料上染速率放缓、染料能均匀分散并且即时有色花也能通过助剂修正过来,如此一来,涤纶筒子纱染色就不容易出现内外层差。
涤纶筒子纱染色低聚物的减少和去除
涤纶筒子纱染色低聚物的减少和去除1.1 涤纶高温高压染色经常会遇到低聚物的问题,在筒子纱染色时被同行们称之为“白粉”。
虽然所有的化学纤维都存在低聚物,但是只有涤纶纤维的低聚物,对纺织印染加工有着较大的影响。
所以,讨论涤纶染色的低聚物问题,具有重要的意义。
1.2 早在1960年代初,H.Zahn先生就已经指出了涤纶低聚物对纺织印染加工的危害。
此后,国外一些生产纺织印染助剂的公司曾针对性地推出了相应的助剂, 但经珠江三角洲深圳、顺德、东莞的一些染厂在使用后,普遍认为:作用不大。
尤其是对于涤纶染色时,低聚物最难以去除的筒子纱染色(主要是染宝蓝色、黑色等深色),和汽流纺生产的筒子纱作用不大。
1.3 我们在助剂开发研制和印染加工生产的工、商一体化配合协作下,经历了两年多的反复研究、实践,全部采用国产原料,成本低于进口助剂,在内外销筒子纱的染色上使用,取得了明显的效果。
2 低聚物的产生2.1 事实上,涤纶纤维在化纤生产的合成喷丝时,低聚物已经作为副产品产生了。
其化学结构呈线状和环状,在经过很高的染色温度作用下,低聚物就会分离出来。
2.2随着人们生活对化学纤维需求量的不断扩大,国内大小化纤厂的数量也比改革开放前,明显增加了很多。
再加上现实市场价格、成本的竟争白热化,使得化纤产品的质量也参差不齐。
另外,国内涤纶染色所需的分散染料经过几次类似现在的“彩电大战”,价位大都已低至十几、二十几元,迫使染料厂在分散染料中所用的分散添加剂,也无奈随之调换品种。
而且,采用滤饼中间体来加工染料的小染料厂,也如雨后春笋般地冒出来了很多。
这样一来,更使得涤纶染色低聚物的问题越发突出。
2.3在涤纶的染色过程中,低聚物的产生是不可避免的。
倘若我们的染厂把希望寄托在涤纶纤维生产厂,提供无低聚物的涤纶纤维上面,或依想单靠某种染料来彻底解决这个问题,那看来只能是一个梦想。
即便是现在尚未普及和完善的涤纶碱性染料染色,也不可能做得更好,且又成本偏高而色谱不太齐全。
提高涤纶染色牢度的措施
提高涤纶染色牢度的措施提高涤纶染色牢度的措施涤纶是一种常用的合成纤维,具有优异的强度、耐磨性和耐光性等特点,因此广泛应用于纺织、服装、家居等领域。
但是,涤纶在染色过程中容易出现脱色、退色等问题,影响产品的质量和美观度。
为了提高涤纶染色牢度,需要采取一系列措施。
一、优化染色工艺1.选用合适的染料涤纶具有较强的亲水性和静电性,在染色过程中容易吸附空气中的灰尘和杂质,导致颜色不均匀。
因此,在选择染料时应考虑其分散性和亲水性,以确保颜色均匀且牢固。
2.调整染料浴比例在进行涤纶染色时,应根据不同的面料类型和颜色深浅调整染料浴比例。
通常情况下,深色面料需要使用较高浴比才能达到理想效果。
3.控制温度和时间涤纶对温度和时间敏感,在染色过程中需要控制好温度和时间。
一般来说,涤纶染色温度应在120℃以下,时间不宜过长,以避免纤维熔化或变形。
4.添加助剂在涤纶染色过程中,可以添加一些助剂来提高染料的分散性和亲水性,如分散剂、乳化剂、增白剂等。
这些助剂可以有效地提高涤纶染色牢度。
二、改善后处理工艺1.漂白处理在进行涤纶染色前,可以进行漂白处理来去除面料中的杂质和污渍,并使面料更加均匀。
漂白处理可以采用氧化漂白、还原漂白等方法。
2.定型处理定型是指将面料加热至一定温度并保持一定时间,使其保持所需形状和尺寸的过程。
定型可以使面料更加牢固和耐用,并提高其抗皱性和耐洗性。
3.后整理处理后整理是指对已经染色的面料进行整理加工,以改善其手感、光泽度和外观效果。
常见的后整理方法包括压光、起毛、烫平等。
三、加强管理和监控1.加强员工培训在染色生产过程中,操作人员应具备一定的染色知识和技能,能够正确地进行染色操作。
因此,企业应加强员工培训,提高其染色技能和意识。
2.建立严格的质量控制体系企业应建立完善的质量控制体系,从原材料采购、生产过程监控、产品检验等方面进行全方位的质量监控和管理。
如发现问题及时进行处理,并采取有效措施避免再次出现。
涤纶筒子纱染色、产生色花的原因及处理方法
涤纶筒子纱染色、产生色花的原因及如何处理方法:涤纶筒子纱染色是在一定的温度下,利用染色机主泵的压力作用使染液穿透卷绕在具有多孔不锈钢筒管上的纱线层,使分散染料的分子与纤维不断接触,染料首先被纤维外层吸附,继而再向纤维内部扩散而达到上染目的。
涤纶筒子纱染色,产生色花的原因是多方面的,现将容易造成色花的因素及其控制方法分述如下:①松式络筒松式络筒对染色质量起关键性作用,络筒好坏对获得匀染十分重要。
不锈钢筒管一般有弹簧筒管和多孔筒管,弹簧筒管可自由压缩,染液穿透面积大,有利于匀染。
简纱卷绕密度以0.33g/cm3~0.398g/cm3为宜。
筒纱卷绕密度过紧,染液穿透困难,局部因接触染料太少而得色偏浅,极易造成色花或色圈等染疵,卷绕密度过松,筒纱容易变形脱落,造成乱纱,难以上机。
络筒后倒角要均匀,运输及装锅时要小心,防止碰坏筒纱,络筒纱层不宜过厚,每只筒纱重量要均匀,如不注意都有可能影响匀染。
②筒纱前处理筒纱前处理目的是去除涤纶纱在纺纱沾污油剂及络筒工序沾污油污。
通常可采用净洗剂加纯碱于80℃下处理30min,前处理后一定要充分清洗,否则容易造成染花疵病。
③染料的选择分散染料在高温高压筒纱染色时一定要选择好染料,特别是拼色可选用相容性好的低温型三原色,如分散红E-4B、分散黄E-4RL、分散蓝E-4R 或高温型三原色,如分散红S-5BL、分散橙S-4RL、分散蓝S-3BG等可拼成大部分常见的色谱。
同时还要考虑分散染料的高温凝聚性,必要时应做试验,否则可能形成染料聚集,造成染斑。
④助剂的选择筒子染色对水质要求很高,可选用螯合分散剂,如螯合分散剂R-DL对水中的Ca2+,Mg2+具有很强的螯合能力,一般用量为0.5~1g/L,既可降低水的硬度又可增加染料的分散能力,防止染料聚集产生染斑。
高温匀染剂在筒纱染色中有极为重要作用。
选用时要求匀染性好,高温分散性好,移染性好,不影响上染率。
选用时最好先做试验。
⑤严格控制染浴pH值及升温速率,分散染料高温高压染色时,染浴最适宜pH 值为4.5~5,有些分散染料对pH值有敏感性,在pH值小于4或大于5以上时会引起色变,上染率下降。
简子纱染色需要注意几个问题
简子纱染色需要注意的几个问题近年来,由于越来越多的客户认识到筒子纱线染色损耗小、质量高、交货快、效益好,因此,筒子纱线染色订单快速增长。
然而涤纶筒子纱线染色工艺复杂,要求很高,且影响因素较多难于控制,稍有疏忽,容易造成色花。
一、染色原理涤纶筒子纱线染色是采用高温高压染色法在高温高压筒子纱染色机上进行的。
由于聚酯纤维结构紧密,分散染料在低温条件下几乎不上染。
只有将温度提高至90℃以上,染料的上染才逐渐增加。
达到110℃以上时,涤纶纤维中无定型区高分子链段的运动加剧,增加了微隙,降低了染料分子扩散进入纤维内部的阻力,提高了染料分子扩散速度,使分散染料的上染速率迅速加大。
至130℃才能获得满意的染色效果,染料利用率达到90%以上,得色丰满,各种染色牢度优良。
涤纶筒子纱线染色就是在一定的温度下,利用染色机上主泵的压力作用使染液穿透卷绕在具多孔筒管上的纱线层,使染料分子与纤维分子接触,溶解了的染料首先被纤维外层吸附,接着再向纤维内部扩散,从而达到上染目的。
二、染色易色花应注意以下问题:2.1松筒涤纶筒子纱线染色前需先松筒。
松简首选不锈钢弹簧管,其优点是有效穿透面积特别大,对获得匀染非常有利。
可自由压缩,对不同数量批号的订单有极强的适应能力。
筒纱的卷绕密度大小是很重要的,考虑到染色机械的泵的扬程高度,涤纶筒纱的卷绕密度以0.33-0.39g/立方厘米为宜。
卷绕太紧,染液难以穿透很厚的纱层,局部因接触染料太少而得色偏浅造成色花或色圈等染疵,卷绕太松,筒纱容易变形脱落,造成乱纱,难于上机。
2.2前处理前处理的目的是去除涤纶纱线在纺纱和松筒等人缸染色前工序中沾污在纱线上的油剂,通常采用除油灵,加碳酸纳2g/L于80℃条件下处理20min。
必须注意的是前处理后一定要清洗干净,否则容易造成染花疵病。
2.3染料的选择高温高压染色应尽量选用分子量小、分散性优良的染料,国产分散红E-4B、分散黄E-3RL、分散蓝E-4R是一组很匹配的低温型染料组合。
- 1、下载文档前请自行甄别文档内容的完整性,平台不提供额外的编辑、内容补充、找答案等附加服务。
- 2、"仅部分预览"的文档,不可在线预览部分如存在完整性等问题,可反馈申请退款(可完整预览的文档不适用该条件!)。
- 3、如文档侵犯您的权益,请联系客服反馈,我们会尽快为您处理(人工客服工作时间:9:00-18:30)。
涤纶筒子染色常见问题分析----江苏旷达实验室张凤涤纶织物由于强度高,回弹性好,耐磨性优良,尺寸稳定性好,抗皱性好,而被广泛应用于各种纺织品及服装面料。
涤纶筒子纱线染色是采用高温高压染色法在高温高压筒子纱染色机上进行的。
由于聚酯纤维结构非常紧密,分散染料在低温条件下几乎是不上染。
涤纶筒子纱染色是在一定的温度下,利用染色机主泵的压力作用使染液穿透卷绕在具有多孔不锈钢筒管上的纱线层,使分散染料的分子与纤维不断接触,染料首先是被纤维外层吸附,继而再向纤维内部扩散而达到上染得目的。
我公司主要是ATY、DTY,现就这几年我公司常见染色问题阐述以下两点:一、影响筒子纱匀染性的因素及预防措施较高的染液循环频率和较低的染料吸收速度是筒子纱匀染的重要条件。
染料的吸收速度除了受纤维及染料本身特性的影响外,它还受助剂、染液温度、PH值等因素的影响。
在实际生产中影响筒子纱匀染的因素是相当复杂的,这里以筒子纱染色时基本的操作因素为主,来阐述它们对筒子染色过程中匀染情况的影响。
这些因素是筒子纱的染液流速或染液循环频率、染色时染液的升温速度、筒子纱卷绕密度等。
1、影响筒子纱匀染性的因素A、每循环上染率对匀染的影响由于纤维对染料的吸收作用,染液内染料浓度在染液流向方向上逐渐减少,引起染液流向下方纤维时染料的吸收量下降,即染料的吸尽作用。
反映染料吸尽作用最直接的指标是染液每循环一次纤维吸收染料的百分率,即每循环上染率。
每循环上染率越大,吸尽作用越强烈,所得的筒子纱匀染性越差。
B、流速对匀染程度的影响经过筒子纱的染液流速或筒子纱染色时染液的循环频率,是决定筒子纱染色质量的重要参数。
同一纤维品种用同样的染化料在相同条件下染色时,染料的最终平衡上染率是不变的,而达到匀染所需要的时间随染液流速的增加而减小。
也就是说,在相同的染色时间内,流速越高,筒子纱的匀染程度就越好;流速越低,筒子纱的匀染程度就越差;但流速过大易出现毛羽等疵病,因此,控制好流速也是非常重要的,一般是要控制在25~30 L·(min.kg)。
C、升温速度对匀染程度的影响筒子染色时的升温速度直接影响到筒子染色时间的长短,还会影响筒子染色机的产量、能耗。
为此,确定合理的升温速度是筒子染色工艺中的一个重要内容。
从染液吸尽作用的原理出发,避免升温速度过快引起每循环上染率增加过大导致筒子纱不匀染,对确保筒子纱的染色质量是十分重要的。
染色过程中升温速度增加时,每循环上染率也随之加大,这将导致筒子纱不匀染程度的增加。
根据小样实验,当循环速度在2.85~3.25次/min情况下,即使升温速度为0,筒子纱仍由0.68单位的得色率平均偏差值存在。
因此现在许多工厂采用恒温染色法来保证匀染。
D、筒子纱卷密度对不匀染程度的影响筒子纱卷绕密度不同,染色后的匀染程度也有所不同。
在不同筒子纱卷绕密度的条件下,每循环上染率的变化及用目测和分光光度评定的筒子纱不匀染程度结是不同相同的。
为了得到良好的染色结果,筒子纱的卷绕密度应尽量低些。
但如果筒子纱的卷绕密度过低,则极易引起筒子纱型的崩垮,而且还会过多地减少筒子染色的装料量,因此筒子染色时,筒子纱卷绕密度应控制在0.3~0.45g/cm3左右(一般ATY密度小,DTY密度大)。
2、解决匀染性的措施A、把开始时染料的迅速吸收阶段的吸收速率调节得十分缓慢,随后控制染料的上染速率,使染液的平衡吸收率平稳、平缓地增加。
这种方法在实际生产中已得到普遍使用。
我们染涤纶纱一般是加入助剂,染料,在缸体内运行一段时间再升温,以控制整个染色过程中平衡吸收率的变化。
也可以用控制染色升温的办法来控制染液的平衡吸收率。
B、使用快速扩散的染料。
这是一个十分理想的办法,但在实际使用中,由于快速扩散染料水洗牢度很差,在涤纶纤维上它的光牢度也很差,因而要从牢度要求的角度来选用染料。
C、采用增加流速或减小浴洗比的方法,即提高染液的循环频率。
D、减小筒子纱的厚度,使染液在流线方向穿过筒子纱的距离变小。
但生产小筒子纱会带来经济上的问题。
E、采用延长染色时间的方法,既增加染液的循环次数。
以上的各种方法可以单独使用,也可以几种方法同时使用,以保证筒子纱的染色质量。
目前,快速筒子纱染色主要使通过提高染液循环频率的方法来实现。
二、对筒子纱内、中、外色差的影响因素及预防措施人们对筒子染色疑问最大的,也是最常见的质量问题,就是内-中-外色差。
这里姑且不论由于纤维品质的原因而造成内-中-外色差,就工艺和设备而言造成内-中-外色差最重要的原因是染液流量不足。
可从下面10个方向进行讲解。
1、主泵流量不足从筒子染色理论分析可知,筒子染色有个明显的特征,即染液在筒子纱线中的循环运动过程中,染料浓度会沿程下降(dc/dx,沿程浓度差)只有当染液循环速度大到足以补充染料被吸附变稀,使内—中—外各处纱线接触到的染液浓度一致,才不会出现沿程色差。
也就时说,要防止内—中—外色差,主泵必须提供足够的染液流动速度——流量。
理论和实践证明:只要流量足够,即使只打正循环,也可以匀染,使内—中—外达到无色差的满意效果(实际情况中由于染液在内—中—外圈的流线密度不同,还会出现内—中—外色差)。
2、有效流量不足主泵流量不等于实际上真正穿透筒子纱层的流量(有效流量),两者之比为有效流量率(有效流量率=有效流量/主实际流量)。
造成两种流量不等的原因是部分流量泄漏了,如筒管之间的密封不良。
如前所述,不同筒管的有效流量率,从60%~90%不等,以间隔片密封的不锈钢锥形管主泵有将近一半的流量是无效流量。
另外由于某些原因造成的“露眼”或“破肚”,导致染液“短路”,也会显著降低有效流量率。
3、卷绕密度过大,筒子纱层过厚众所周知,筒子染色需准备松式筒子,不仅密度匀,而且比常规筒子松、密度小。
不论染色筒子卷绕密度如何,在筒子染色时,都会产生“过滤阻力”。
密度大,阻力大,反之阻力小。
筒管上卷绕的纱层太厚(纱太多),过滤阻力也会增大,一般认为纱层厚度不超过50mm 为宜。
4、正、反循环安排染色筒子从内层到外层,半径逐渐增大,各层容纱量也随之增大,但是主泵的有效流量,在各层上并没有增大。
也就时说,不同半径处的纱层面上通过的染液流量是同样的。
当染液作由内向外的正循环时,沿程层纱的面积逐渐增加,单位面积上通过的染液随半径的增加而减少(及流线密度下降)。
尽管流体的速度已大到足以弥补沿程浓度降低,然而由于(染)料少纱多,同样会发生内深外浅的问题。
当染液作反循环时(从外向内),流向沿程染液流线密度越来越大,情况变成(染)料多纱少,沿程染料浓度减少,就有利于减少内—中—外色差。
因而,对主泵能力不足的染色机应考虑一定的反循环时间。
以致出现有人设计反循环时间比正循环还长的情况。
5、进料时染料液主循环的方向一般染色机进料时由主料泵把配好的料打到主泵进口,再由主泵混合同主缸中其它染液通过出口进入纱线强制循环系统,循环方向由正反之分。
正循环时,泵出口染液直接通向各筒子内层,此时该部分染浴物料浓度比全浴浓度大,而纱线量又最少。
反循环时,泵出口染浴首先进入染缸缸体与全浴混合后,从筒子的外表面被压入(或吸入)到筒子的内侧。
反循环时,一方面由于染液被稀释,浓差没有正循环开始时大,而另一方面纱线量又是从大变小,因而造成的沿程浓差要小得多,这对筒子内层沉积物的减少也是有益的。
因而建议注料时,主循环应取反循环,有利于减少内—中—外色差。
6、筒子密度变化造成内—中—外色差纱线染色过程中不同纤维其溶胀程度不一致。
如在水中,涤纶直径增大10%,棉纤维的直径增大20%,羊毛直径增大15%,粘胶纤维直径增大35%以上,Tencel直径增大更多。
由于络松筒时是干纱,在水中直径增大造成纱变粗,而长度增加很小(1%-2%),使卷绕密度变大。
在碱溶液中溶胀更是严重。
合成纤维在热水中其长度会收缩,也会使筒子密度变大。
一些弹性纱(如氨纶包芯纱、包缠纱)在湿热状态下也会剧烈收缩,所有这些都会破坏原来卷绕均匀的筒子,一方面密度变大,另一方面变得不均匀。
如上所述,筒子密度变大就会使过滤阻力增大,导致染液流量变小,而加剧内—中—外色差。
7、染化料性质及染色工艺的影响不论什么时候染化料本身的性质还是染色工艺参数的设定,都会影响上染速率(尤其是染料的初染率)和移染率,当上染率太快,移染率又低时会造成不匀染,即内—中—外色差。
8、染后柔软剂使用不当的的影响一般染色后纱线会发涩、发毛,致使后道工序进行困难,深色尤为严重。
为此不少厂家增加了“上油”工序,一般是用平滑性表面活性剂处理,有的用有机硅处理。
但是有机硅由于折光度低会产生“增深”效应,如果“上油”不匀,即增深不匀,也会造成内—中—外色差。
9、水质影响筒子染色时,筒子上的纱线如同滤材。
染色全过程中,前处理、染色、皂洗、清洗液数千次的穿透过滤。
当水质不良、含杂过高,管道设备中铁锈污垢存在,或在前处理中,纤维共生物在前处理液中,因分散不匀,有些杂质沉积在纱线上,造成内层发黄(也有黄褐色)。
因而筒染应使用软水,设备管道一定要冲洗干净。
10、筒子卷绕密度不匀筒子卷绕时,径向密度分布不均匀,内层太松,以致染液轴相流量增加,造成内深外浅,也会造成内—中—外色差。
每个公司不尽相同,有待我们仔细去发现,去遏制。
以上仅是根据我公司染色丝出现的问题作出的详细分析,总结了各个因素对筒子纱匀染性、筒子中外层产生的影响。
通过对各个影响因素的了解,来解决生产中出现的类似问题,从而提高公司产品质量,最终满足客户的需求!。