薄壁轴套的加工
一种薄壁套加工方法
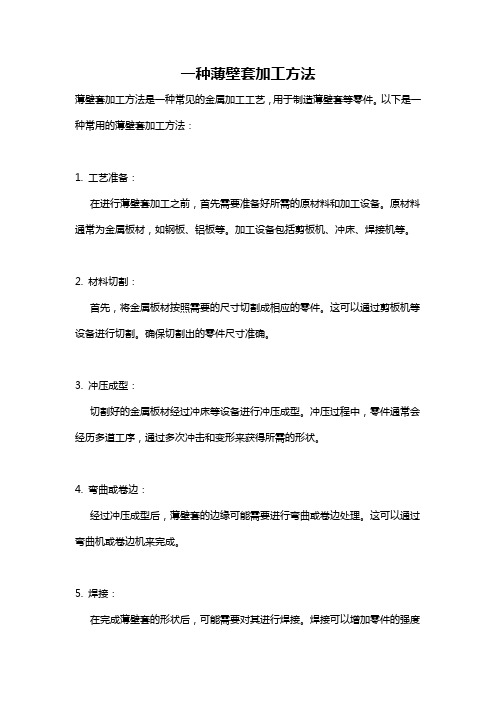
一种薄壁套加工方法薄壁套加工方法是一种常见的金属加工工艺,用于制造薄壁套等零件。
以下是一种常用的薄壁套加工方法:1. 工艺准备:在进行薄壁套加工之前,首先需要准备好所需的原材料和加工设备。
原材料通常为金属板材,如钢板、铝板等。
加工设备包括剪板机、冲床、焊接机等。
2. 材料切割:首先,将金属板材按照需要的尺寸切割成相应的零件。
这可以通过剪板机等设备进行切割。
确保切割出的零件尺寸准确。
3. 冲压成型:切割好的金属板材经过冲床等设备进行冲压成型。
冲压过程中,零件通常会经历多道工序,通过多次冲击和变形来获得所需的形状。
4. 弯曲或卷边:经过冲压成型后,薄壁套的边缘可能需要进行弯曲或卷边处理。
这可以通过弯曲机或卷边机来完成。
5. 焊接:在完成薄壁套的形状后,可能需要对其进行焊接。
焊接可以增加零件的强度和稳定性。
使用适当的焊接设备和焊接材料来完成焊接过程。
6. 表面处理:完成焊接后,对薄壁套进行表面处理。
这可以包括去毛刺、打磨、喷漆等。
表面处理可以提高零件的美观度和耐腐蚀性。
7. 检验和质量控制:在加工过程中,需要进行检验和质量控制,以确保薄壁套的质量符合要求。
这可以通过外观检查、尺寸测量、物理性能测试等方法来进行。
8. 包装和出货:最后,对加工好的薄壁套进行包装,并准备好出货。
根据客户要求,可以选择适当的包装材料和方式,以确保零件在运输过程中不受损坏。
以上是一种常见的薄壁套加工方法。
根据具体需求和加工设备的不同,可能会有一些细微的差异。
在实际应用中,还需根据具体情况灵活调整,以获得最佳的加工效果和质量。
薄壁套优化加工措施

薄壁套优化加工措施薄壁套是一种用于机械传动中的零部件,通常用于连接轴和孔的配合配件。
由于其特殊的结构,薄壁套在加工过程中容易出现变形、偏心和表面质量不佳等问题。
为了解决这些问题,提高薄壁套的加工质量,需要采取一系列的优化加工措施。
一、材料选用在选择薄壁套的材料时,需考虑套的使用环境和工作条件。
常见的材料包括铁、铜、铝等。
铁材质具有良好的机械性能,适用于承受较大载荷时使用,而铜和铝则适用于对降低重量有要求的场合。
根据具体需求,选择适宜的材料可以减少套的变形和表面质量问题。
二、工艺参数调节对于薄壁套的加工过程,合理调节工艺参数十分重要。
首先是切削速度,过高的切削速度容易导致套变形,而过低的切削速度则会使切削阻力增大,影响加工效率。
其次是进给量,进给量不当会导致切削力不均匀,进而引起加工不精确的问题。
通过对这些参数进行合理的调节,可以有效控制套的加工质量。
三、刀具选择选择合适的刀具也是关键。
对于薄壁套的加工,应选择刚性较好的刀具,以减少切削振动和变形的发生。
同时,选择切削边刃角度较小的刀具,可以降低套的切削力,减少套的变形。
此外,刀具的磨损情况也要及时检查并更换,以保证加工的精度和质量。
四、切削润滑在薄壁套的加工中,切削润滑的使用也十分重要。
切削润滑可以减小切削温度,降低切削力,减少切削振动和摩擦,从而提升加工质量。
常见的切削润滑方式有干润滑和湿润滑两种,根据具体情况选择合适的方式来进行切削润滑。
五、切削顺序及夹持方式在薄壁套的加工中,切削顺序和夹持方式也会对加工质量产生一定的影响。
合理的切削顺序可以减少加工过程中的变形和振动现象,提高加工精度。
夹持方式应选择适当,夹持力度要适中,过大的夹持力可能导致套的变形,而过小的夹持力可能导致套的偏心和加工质量不佳。
综上所述,针对薄壁套的特殊加工要求,我们可以通过材料选用、工艺参数调节、刀具选择、切削润滑、切削顺序及夹持方式等措施来优化薄壁套的加工过程。
这些措施旨在减少套的变形和偏心现象,提升套的表面质量和加工精度。
薄壁轴套加工工艺及工装分析

在 掘进 机 机 组 中 需 配 备 电动 机 等 机 械 的 设 计 中, 经常 会 遇 到 一 些 直 径 > 1 0 0 mm, 壁厚< 1 0 ml T l 的薄壁 轴套类 零 件 , 精 度要 求较 高 , 用 简单 的磨 床装 夹定 位 进行 磨削 很 难 达 到加 T 精 度 要求 , 零 件 图如
mm一精 车 内 、 外圆, 均 留余 量 1 mm一 淬 火 处理 , 硬
度达 5 8 ~6 2 HR C 一 上胎磨 内、 外圆。
2 工 装 的设 计 方 案
要加 工 该 零 件 , 首 先 要 解
图 1 薄 壁轴 套
ቤተ መጻሕፍቲ ባይዱ
决 薄壁轴 套磨 削装 卡 时的变 形
( Fu s hun Co a l Mi ni ng M ot o r Ma nu f a c t ur i ng Co., l t d, Fu s hun 1 1 31 22, Chi na )
Ab s t r a c t :S o me m ot o r h ous i n g c a s e wa s e qu i p pe d wi t h b or i ng ma c hi ne u ni t t ha t h as t wo br a c k e t s o n o ne s i d e a nd t he s e br a c ke t s ar e t he c on ne c t i ng pa r t s wi t h bor i ng ma c h i n e u ni t . The r e i s on e s l e e v e i n t he c e nt e r h ol e of br ac ke t whi c h i s t he ma t i ng p ar t o f bo r i ng ma c h i n e a s s e m bl y a nd ne e d s h i g h p r e c i s i o n. The s l e e ve i s ma d e o f 2 0Cr M nTi a l l oy s t r u c t u r a l s t e e l a nd t he s l ee ve be l o ng s t o t hi n wa l l b us hi n gs, w hi c h a r e ve r y di f f i c ul t t o ma c hi ne .Af t e r r e pe a t e d e x pe r i me n t s, i t wa s s u mma r i z e d t h a t a k i n d o f m or e r e a s on a bl e pr oc e s s a nd t o ol i n g pr o gr a m t o s ol ve t hi s p r o bl e m.
大型薄壁轴套的精加工工艺方案

附表薄壁轴套的加工工艺讨论摘要:薄壁类零件一直是车削加工的难点,尤其是大型的薄壁铜套。
本文介绍一种能加工出高精度大型薄壁铜套的加工方法,主要从工件装卡、刀具选择及加工时切削用量的选择三方面来阐述。
关键词: 薄壁轴套、装卡变形、刀具材料及几何角度、切削用量。
薄壁轴套刚性差,机加工工艺性比较差,车削时受切削力和夹紧力的作用,极易产生变形,加工时具有一定难度。
在车削时注意装卡方法、合理选择刀具材料、刀具的几何角度、切削用量及适当地进行冷却润滑,都是加工薄壁类型工件工作时减少变形的关键因素。
下面以我厂生产的毛坯离心铸造大型薄壁铜套作为特例来探讨其机加工方法。
简图(一)铜套的主要外形尺寸如下简图(一)所示。
一、加工要点分析此类零件加工难点主要集中在精加工工序,下面就精加工时的要点进行分析。
1.工件的装卡:工件装卡状态对加工精度的影响非常明显,因此一般应增加工件的支承面和夹压点,使工件受力均匀,并减小夹压应力和接触应力,必要时还应增设辅助支承,以增加工件刚性。
2.刀具的选择:精加工时的刀具刃口一定要锋利,使工件切削过程中受到的切削力以及产生的切削热相应小一些,尽量避免因此而产生的变形量过大。
3.切削用量的选择:切削用量对工件加工时的影响很大,为了减少切削时工件的振动和变形,保证加工精度,选用时应本着使工件所受的切削力和切削热相应小一些,所以一般应采用较高的切削速度,切削深度和进给量不应过大。
二、精加工工艺方法加工中采用立式车床进行车削,粗车至单边留量2+0.2mm后进行精加工。
针对该类零件精加工中存在的问题,具体可以采用以下工艺方法:1.毛坯制作时预留工艺用压卡头,即在长度一端头留法兰式压卡头,卡头尺寸Φ900×50。
粗加工时平法兰两端面,并在切口处车削Φ820宽25应力槽,自然时效后再精车。
精车时应先按简图(二)示进行装卡,精车外圆及卡头两端面。
在孔内用压板压住零件,注意装卡力应均匀,不应过大。
小型薄壁轴承套类零件数控车加工工艺分析

小型薄壁轴承套类零件数控车加工工艺分析冯煜棋(佛山市顺德区陈村职业技术学校,广东佛山528313)摘要:首先简要阐述了小型薄壁轴承套类零件加工的难点,然后分析了小型薄壁轴承套类零件加工的准备内容,包括全面分析零件图样与零件装夹注意事项,最后从刀具选择、量具选择、加工顺序等方面,总结了小型薄壁轴承套类零件加工工艺的技术要点。
关键词:薄壁零件;轴承套类;数控车加工0引言小型薄壁零件在数控车上加工时,粗加工与精细化加工分开进行,在完成粗加工后进行精细化加工。
但粗加工时会出现切削量大、应力大等情况,直接造成后续精细化加工出现变形、尺寸不合理等情况。
因此,需要做好工艺分析工作,改善传统加工工艺的不足,提高小型薄壁轴承套类零件的加工质量。
1小型薄壁轴承套类零件加工的难点分析小型薄壁轴承套类零件选择强度高的硬铝材料,完成加工后需要利用放大镜放大10倍进行检查,确保零件表面不出现划痕。
小型薄壁零件整体尺寸较小,利用夹子难以操作,且夹紧操作时又容易出现形变。
综合分析可以发现,小型薄壁轴承套类零件加工的难点体现在以下方面:(1)零件装夹操作时容易变形,难以控制零件壁的厚度。
结合小型薄壁零件设计图纸与技术要求,加工设计时要重点关注尺寸的精准度、定位的精确性、加工工艺的选择等,结合具体方式选择合适工艺。
(2)小型薄壁零件加工精确度会受到切削热的影响,车削加工时会产生热量,使得金属材料发生变形。
数控车床本身主要用于加工回转类零件,常见的包括轴类或盘类复杂零件,呈现出内外圆锥面或内外圆柱面回转等。
如图1所示,由3个零部件构成典型配件。
整体结构并不复杂,但需要在短时间内保质保量地完成,要求技术人员全面掌握数控车床的性能与操作技巧,制定合适的加工方案。
2小型薄壁轴承套类零件加工的准备2.1全面分析零件图样(1)图形分析要点。
加工轴类零件可以分成两个重要内容,即保证尺寸精确度与表面粗糙度。
如图1所示零件分成三部分,零件图形看似简单,但内部包括几个部分:外端面、锥面、椭圆等,要求技术人员有娴熟的操作技巧,才能顺利完成零部件加工。
薄壁类零件的车削工艺分析

薄壁类零件的车削工艺分析段立波一.引言薄壁类零件指的是零件壁厚与它的径向、轴向尺寸相比较, 相差悬殊, 一般为几十倍甚至上百倍的金属材料的零件,具有节省材料、结构简单等特点。
薄壁类零件已广泛地应用于各类石油机械部件。
但是薄壁类零件的车削加工是比较棘手的,具体的原因是因为薄壁类零件自身刚性差、强度弱,在车削加工中极容易变形,很难保证零件的加工质量。
如何提高薄壁类零件的加工精度是机械加工行业关心的话题。
二.薄壁类零件车削过程中常出现的问题、原因及解决办法我们在车削加工过程中,经常会碰到一些薄壁零件的加工。
如轴套薄壁件(图1),环类薄壁件(图2),盘类薄壁件(图3)。
本文详细分析了薄壁类零件的加工特点、防止变形的装夹方法、车刀材料、切削参数的选择及车刀几何角度。
进行了大量的实验,为以后更好地加工薄壁类零件,保证加工质量,提供了理论依据。
图1轴套薄壁件图2环类薄壁件图3盘类薄壁件1.薄壁类零件的加工特点1.1因零件壁薄,在使用通用夹具装夹时,在夹压力的作用下极易产生变形,而夹紧力不够零件又容易松动,从而影响零件的尺寸精度和形状精度。
如图4所示,当采用三爪卡盘夹紧零件时,在夹紧力的作用下,零件会微微变成三角形,车削后得到的是一个圆柱体。
但松开卡爪,取下零件后,由于零件弹性,又恢复成弧形三角形。
这时若用千分尺测量时,各个方向直径相同,但零件已变形不是圆柱体了,这种变形现象我们称之为等直径变形。
图4三爪卡盘装夹1.2因零件较薄,加工时的切削发热会引起零件变形,从而使零件尺寸难以控制。
对于膨胀系数较大的金属薄壁零件,如在一次安装中连续完成半精车和精车,由切削热引起零件的热变形,会对其尺寸精度产生极大影响,有时甚至会使零件卡死在芯轴类的夹具上。
1.3薄壁类零件加工内孔中,一般采用单刃镗刀加工,此时,当零件较长时,如果刀具参数及切削用量处理不当,将造成排屑困难,影响加工质量,损伤刀具。
1.4由于切削力和夹紧力的影响,零件会产生变形或振动,尺寸精度和表面粗糙度不易控制。
薄壁套件加工工艺分析及应用实例-机械论文

薄壁套件加工工艺分析及应用实例机械论文论文导读::薄壁套件在结构上与刚性套件的区别为“壁薄”,其加工时在各影响因素的作用下,主要技术难点为变形较大,加工精度难以保证。
本文主要分析引起变形的各影响因素,继而探析减小变形的有效工艺措施,并通过生产实例进行工艺验证,取得较好的实际良效,有效地保证了其加工精度要求。
论文关键词:薄壁套件,工艺分析,应用实例俗话说“车工最怕车细长轴、薄壁套”,此话不无道理。
套类零件是用来支承旋转轴及轴上零件或用来导向的,该类零件的主要表面是内孔和外圆,其主要技术要求是内孔及外圆的尺寸以及圆度要求;内外圆之间的同轴度要求;孔轴线与端面的垂直度要求。
薄壁套类零件壁厚很薄,径向刚性很差,在加工过程中受切削力、切削热及夹紧力等诸多因素的影响,极易变形,且变形程度严重,导致以上各项技术要求难以保证。
针对这些问题机械论文,结合本人多年的生产实践经验,本文对薄壁套类零件加工过程中装夹方法、切削用量、刀具几何角度等做了深刻的探讨,以供大家参考、共享。
一、薄壁套件的加工工艺分析1、工件装夹方法薄壁类零件在加工过程中如果采用普通装夹方法,会因为产生很大的变形而无法保证加工精度。
例如用三爪自定心卡盘夹持薄壁套筒镗孔:夹紧后套筒呈三棱形(图1a),虽然镗出的孔成正圆形(图1b),但松开后,套筒的弹性恢复使已镗成圆形的孔变成了三角棱圆形(图1c)。
(a)三爪自定心卡盘装夹(b)镗孔后(c)松开后(d)开口过渡环装夹图1套筒夹紧变形误差故薄壁类零件的装夹,一般应增大工件的支承面和夹压面积,或增加夹压点使之受力均匀,并减小夹压应力和接触应力,必要时可增设辅助支承,以增强工件的刚性。
具体措施如下:(1)采用工艺凸台装夹车削时在坯料上预留一定的夹持长度,在工件完成内孔、外圆及端面的加工后切掉。
这样不但防止了工件产生太大变形,而且保证了内孔、外圆及端面间的位置精度。
但这种方法在应用中局限性而且会造成材料的浪费。
浅谈薄壁套零件的加工

浅谈薄壁套零件的加工薄壁零件的加工问题,一直是较难解决的,通过探讨薄壁类零件在加工中存在的易变形、零件尺寸及表面粗糙度不易保证等技术问题,对加工难点进行分析,给出了工艺路线和加工方案,通过优化、完善装夹方法,从而有效解决此类薄壁类零件的车削加工难题,为以后加工此类薄壁零件提供了经验借鉴。
标签:薄壁零件;变形;夹具薄壁零件应用越来越广范,它具有重量轻,节约材料,结构紧凑等特点,但薄壁零件刚性差,强度弱,装夹基准面小,加工过程中容易变形,不易保证加工质量和精度,因此如何正确的加工薄壁零件也是一个棘手的问题。
1 基本情况介绍该薄壁套零件,材料为45#钢,壁厚最薄2mm,薄壁套最大直径为Ф70mm,内孔粗糙度为0.8,同时内孔精度要求在0.021mm内;外圆要求在0.021mm内,且精度要求较高,零件左端面有端面圆弧,其形状及尺寸如图一所示:2 薄壁零件的工艺分析2.1 工艺难点影响该薄壁零件加工精度的主要因素主要有三方面的问题①易受力变形薄壁零件不易装夹,工件壁薄,在较大的夹紧力下,容易产生夹紧变形。
②易受热变形因工件壁薄,过大的切削热会使工件产生热变形,不易保证工件精度要求。
③易振动变形在高速切削过程中,工件易产生振动,从而影响工件的形位精度和表面粗糙度。
2.2 工艺方案过程零件初始的工艺方案为:①夹持毛坯料,钻孔,内外交叉车削薄壁内外圆和Ф80外圆保证精度。
②对零件切断,为保证总长,长度提前预留1mm 。
③为保证薄壁零件的形位精度,我们采用扇形软爪和开缝套筒对薄壁进行装夹。
④零件调头,切削端面保证总长。
⑤切削端面圆弧。
通过这种方案加工出的工件经过三坐标测量机的检测,零件薄壁外圆和内孔的圆度已经发生变化,为了保证工件的形位公差,我们变径向装夹为轴向装夹。
零件改后的方案为:①对零件薄壁进行粗精车选用Ф24的钻头钻深度为80的孔,用内孔刀粗车内孔留精加工余量,对于Ф30的端面孔可以直接用Ф24钻头钻孔,留余量为轴向装夹定位时使用。
- 1、下载文档前请自行甄别文档内容的完整性,平台不提供额外的编辑、内容补充、找答案等附加服务。
- 2、"仅部分预览"的文档,不可在线预览部分如存在完整性等问题,可反馈申请退款(可完整预览的文档不适用该条件!)。
- 3、如文档侵犯您的权益,请联系客服反馈,我们会尽快为您处理(人工客服工作时间:9:00-18:30)。
薄壁轴套的加工
[摘要] 本文通过对薄壁轴套的论述,总结了其装卡及加工方法以及影响变形因素的一些经验。
[关键词] 薄壁轴套切削变形卡头
薄壁轴套刚性差,在车削过程中受切削力和夹紧力的作用极易产生变形,影响工件尺寸精度和形状精度。
注意装夹方法,合理地选择刀具材料、几何角度、切削用量及适当地进行冷却润滑都是加工薄壁轴套类型工件时减少变形的关键所在。
一、刀具的选择:加工薄壁类工件的刀具刃口一定要锋利,一般采用较大的前角和主偏角
1、前角对工件的影响:前角增大,若后角不变,楔角将减少,则刀具刃口锋利,切削流出的阻力减少,变形系数小,切削变形小。
加工塑性大的材料,增大前角,切削力下降明显,加工脆性材料时,增大前角,切削力下降不显著。
2、主偏角对工件的影响:見表一
注:仅适用于一般钢。
二、切削用量的选择
为减少工件的振动和变形,应使工件上所受的切削力和切削热相应小些,所以薄壁类工件加工时一般采用较高的切削速度,但切削深度和进给量不易过大(見表二)。
如机床精度底、刚性差时,则应适当降低切削速度。
三、工件的装卡及加工
A、下料或多件一料,留a长卡头。
1、若工件为单件,则留a长卡头(参照表三),若工件直径较大,或重量较大,应将卡头适当加长。
2、若工件为多件,则需要视工件长度及外圆大小,考虑多件合下料,留a 长卡头(参照表三),若工件直径较大,或重量较大,应将卡头适当加长。
(适合多件合下料的工件,仅适用于Φ<200mm,多件的长度和<300mm的工件)
B1、Φ≤100mm的工件:
1、夹卡头,按毛坯均匀性找正,粗、精车各部达图。
注1:
如果内孔、外圆精度要求较高,可采用内孔、外圆留磨量,开口弹性卡套装卡轴套,磨内孔达图,然后心轴/锥度心轴装卡,磨外圆达图,若为多件合下料工件,需同磨内孔、外圆达图后再轻卡工件切工件达图。
若两端面公差要求较高(0.05mm以内)或起轴承定位作用的工件,需要两端面单面留0.3+0.1mm留量,并在与外圆、内孔同次装卡中车出的端面刻0.3X0.3V型环线,然后上平面磨床先基准面定位,两面互为基准磨两留量端面达图。
若工件为过盈装配的铜套,考虑到过盈装配时铜套的收缩(铜的收缩率为1:1),为防止装配后将相关件抱死,应该根据装配关系,计算出过盈量,然后在内孔公差的基础上适当加大(在工艺里直接体现出)。
B2、100mm<Φ≤200mm的工件:
1、按毛坯均匀性找正,粗车各部,外圆直径留量2,端面单面留量1,达6.3。
2、在外圆卡头切断处车应力槽(参照表四)。
3、精车各部达图。
注2:
如果内孔、外圆精度要求较高,可采用内孔、外圆留磨量,开口弹性卡套装卡轴套,磨内孔达图,然后心轴/锥度心轴装卡,磨外圆达图,若为多件合下料工件,需同磨内孔、外圆达图后再轻卡工件切工件达图。
若两端面公差要求较高(0.05mm以内)或起轴承定位作用的工件,需要两端面单面留0.3+0.1mm留量,并在与外圆、内孔同次装卡中车出的端面刻0.3X0.3V型环线,然后上平面磨床先基准面定位,两面互为基准磨两留量端面达图。
若工件为过盈装配的铜套,考虑到过盈装配时铜套的收缩(铜的收缩率为1:1),为防止装配后将相关件抱死,应该根据装配关系,计算出过盈量,然后在内孔公差的基础上适当加大(在工艺里直接体现出)。
B3、(200mm<Φ≤400mm)
1、按毛坯均匀性找正,粗车各部,外圆直径留量3,端面单面留量1.5,达6.3。
2、在卡头切断处车内、外应力槽(参照表四)。
3、精车各部达图。
注3:
1、注意内外应力槽必须车在A区域(参照附图一)。
2、精车前用风管冷却,以消除热应力。
3、如果内孔、外圆精度要求较高,可采用内孔抛光、外圆留磨量,心轴/锥度心轴装卡,磨外圆达图。
若两端面公差要求较高(0.05mm以内)或起轴承定位作用的工件,需要两端面单面留0.3+0.1mm留量,并在与外圆、内孔同次装卡中车出的端面刻0.3X0.3V型环线,然后上平面磨床先基准面定位,两面互为基准磨两留量端面达图。
B4、Φ>400mm的工件:
(一)卧车加工按I,立车加工按Ⅱ。
I、按毛坯均匀性找正,粗车各部,外圆直径留量4,端面单面留量2,达
6.3。
保留卡头。
Ⅱ、
1、夹非卡头端,按毛坯均匀性找正,粗车卡头外圆及端面見光。
(便于立车定位、找正装卡)
2、夹卡头端,找正,粗车各部,外圆直径留量4,端面单面留量2,达6.3。
保留卡头。
(二)工件立放,自然时效2~3天。
(三)
1、半精车各部,外圆直径留量2,端面单面留量1,达6.3。
2、在卡头切断处车内、外应力槽(参照表四)。
3、精车各部达图。
注4:
1、对于400mm<Φ≤600mm可用卧车加工,Φ>600mm用立车加工。
2、注意内外应力槽必须车在A区域(参照附图一)。
3、精车前用风管冷却,以消除热应力。
4、时效时及精加工完成后,工件必须立置。
四、卡头尺寸的参照选择
一般零件参照附图二、三及表四车应力槽,特殊零件(外圆较大而壁厚较薄、精度要求较高、A检或出口产品),参照附图四、五及表四车应力槽。
附图一为车内外应力槽时的区域。
(内应力槽不允许车在卡工件长度以内,否则起不到消除应力的作用,参照附图一)
说明:
1、表中各参数具体值根据工件的直径、壁厚、长度及重量由工艺员自行给出。
2、在卡头处车内、外应力槽时,不要伤及工件,内外应力槽左右应错开位置,应力槽深度应保证外应力槽底小于内应槽底直径,应力槽差值圆中径应与工件同一中径。
3、内、外应力槽需在精加工前加工,且精加工时转速不可太快,操作者可根据工件及机床性能自行给出。
五、总结
薄壁轴套的装卡加工,应尽可能的增加工件的支承面和夹紧点,使受力均匀,并减少夹压应力和接触应力。
必要时可增设辅助支承,以增强工件的刚性,对于外径Φ>400mm的工件,粗车工件后,应自然时效2~3天,工件应立放,对于非常薄的工件还应在机床上交检并保证壁厚一致。
参考文献:
[1]《重型机械工艺手册》吕亚臣,哈尔滨出版社,1997年出版.
[2]《典型零件机械加工生产实例》陈宏钧,机械工业出版社,2006年出版.
[3]《实用金属切削加工工艺手册》陈家芳,上海科学技术出版社,2006年出版.。