4-1附录一:物料平衡计算书
物料平衡计算公式
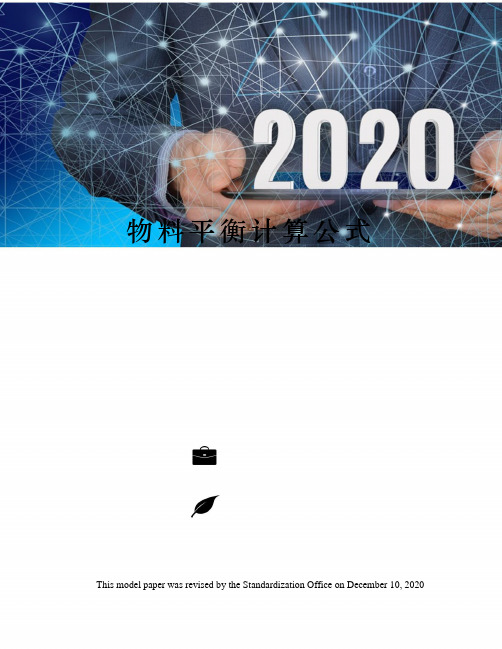
物料平衡计算公式This model paper was revised by the Standardization Office on December 10, 2020物料平衡计算公式:每片主药含量理论片重=测得颗粒主药百分含量1.原辅料粉碎、过筛的物料平衡物料平衡范围: %~100 %物料平衡= %100⨯+ac b a-粉筛前重量(kg) b-粉筛后重量(kg) c-不可利用物料量(kg)2.制粒工序的物料平衡物料平衡范围: %~ %制粒工序的物料平衡=a d cb ++×100% 制粒工序的收率=ab ×100% a-制粒前所有原辅料总重(kg) b-干颗粒总重(kg)c-尾料总重(kg) d-取样量(kg)3.压片工序的物料平衡范围: %~ %压片工序的物料平衡=ad c b ++×100% 压片工序的收率=ab ×100%a-接收颗粒重量(kg) b-片子重量(kg)c-取样重量(kg) d-尾料重量(kg)4.包衣工序的物料平衡包衣工序的物料平衡范围: %~ %包衣工序的物料平衡 = b a ed c +++包衣工序的收率 = b a c+a-素片重量(kg) b-包衣剂重量(kg) c-糖衣片重量(kg) d-尾料重量(kg) e-取样量(kg)5.内包装工序物料平衡内包装工序物料平衡范围: %~ %包材物料平衡=%100⨯++++A a dc b Ba- PTP 领用量(kg) b- PTP 剩余量(kg) A- PVC领用量(kg) B- PVC 剩余量(kg) c-使用量(kg) d-废料量(kg)片剂物料平衡=%100⨯++a dc ba :领用量(Kg)b :产出量(Kg)c :取样量(Kg)d :废料量(Kg)6.外包装工序的物料平衡包装材料的物料平衡范围:100%包装材料物料平衡=%100⨯+++ea d cb e-上批结存 a-领用量 b-使用量 c-剩余量 d-残损量7.生产成品率成品率范围:90%~102%片剂收率= %100⨯++a dc ba-计划产量 b-入库量 c-留样量 d-取样量 1.粉碎过筛和称配岗位物料平衡检查:配料量╳100% 粉碎过筛后原辅料总重(物料平衡范围应控制在~%)2.制粒干燥、整粒总混岗位物料平衡检查:总混后重量+不良品╳100%干颗粒净重+润滑剂+崩解剂(物料平衡范围应控制在~%)3.充填抛光岗位物料平衡检查:胶囊总重+细粉+不良品+废胶囊壳重量╳100%颗粒总重+胶囊壳重量(物料平衡范围应控制在~%)4.铝塑内包岗位物料平衡检查:(成品板总重/平均每板重量+不良品)×规格(粒/板)╳100%胶囊领用量/平均胶囊重(物料平衡范围应控制在~%)5.总物料平衡检查:成品产量╳100%理论产量(物料平衡范围应控制在97~100%)。
(完整版)物料平衡计算公式:
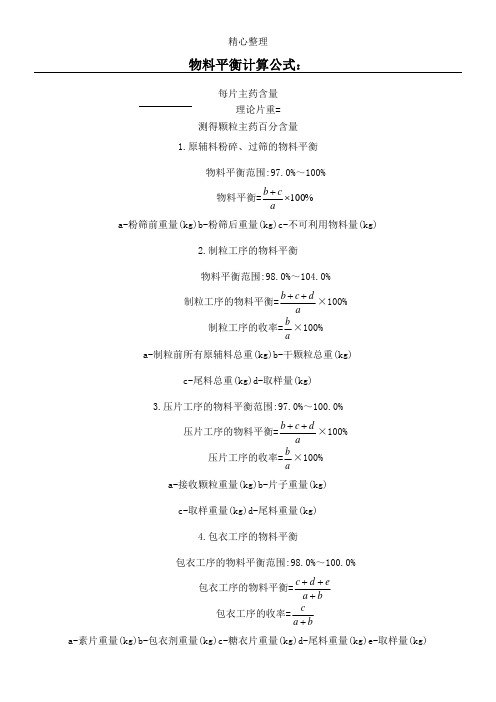
物料平衡计算公式:
每片主药含量
理论片重=
测得颗粒主药百分含量
1.原辅料粉碎、过筛的物料平衡
物料平衡范围:97.0%~100% +c b
c-取样重量(kg)d-尾料重量(kg)
4.包衣工序的物料平衡
包衣工序的物料平衡范围:98.0%~100.0%
包衣工序的物料平衡=b
a e d c +++ 包衣工序的收率=b
a c + a-素片重量(kg)b-包衣剂重量(kg)c-糖衣片重量(kg)d-尾料重量(kg)e-取样量(kg)
5.内包装工序物料平衡
内包装工序物料平衡范围:99.5%~100.0%
包材物料平衡=%100⨯++++A
a d c
b B a-PTP 领用量(kg)b-PTP 剩余量(kg)A-PVC 领用量(kg)
B-PVC 剩余量(kg)c-使用量(kg)d-废料量(kg)
片剂物料平衡=%100⨯++d c b
粉碎过筛后原辅料总重
(物料平衡范围应控制在99.8~100.2%)
2.制粒干燥、整粒总混岗位物料平衡检查:
总混后重量+不良品
╳100%
干颗粒净重+润滑剂+崩解剂
(物料平衡范围应控制在99.0~100.0%)
3.充填抛光岗位物料平衡检查:
胶囊总重+细粉+不良品+废胶囊壳重量
╳100%
颗粒总重+胶囊壳重量
(物料平衡范围应控制在96.0~101.0%)
4.铝塑内包岗位物料平衡检查:
(成品板总重/平均每板重量+不良品)×规格(粒/板)
╳100%。
lxl 衡算 (2)

附录一.物料衡算1.计算基准日产33.3333吨(100%)氧化钙,83.3333吨(100%)碳酸钙。
300天工作日(年工作时间7200小时)。
各生产工序的收率为:(1)石灰石煅烧工序考虑石灰石过烧和生烧等因素,取石灰石转化率为95%,石灰石中碳酸钙含量按97%估算,筛选过程中生石灰石随灰渣、煤渣筛去,损耗为3%,故该工序总收率为:η1=97%×95%×(1-3%)=89.39%(2)石灰消化工序收率为η2=93%,损耗在消化机和旋风分离器中,消化机中石灰乳随同大块渣石一起排除,旋风分离器中石灰乳则随一定粒度的僵石灰或尚未化好的粒子由旋液分离器底部排除。
(3)碳化工序收率为η3=99.9%。
(4) 后处理工序离心脱水,随滤过液带去约1%~2%的碳酸钙,但这部分可返回消化机中,回收使用,考虑该部分收率为99%,回转窑干燥收率为99.8%。
筛分、包装等操作收率为99.8%。
后处理收率为η4=99%×99.8%×99.8%=98.6%故氧化钙的生产总收率为:ηA=η1=89.39%碳酸钙生产总收率为:ηB=η1×η2×η3×η4=89.39%×93%×99.9%×98.6%=81.89%按每天生产33.3333吨氧化钙,也即生产595.2375Kmol/d或N1=24.8016Kmol/h 氧化钙所需原料石灰石量,根据氧化钙总收率应为:G1=N1/ηA=24.8016÷89.39%=27.7453Kmol/h按每天生产83.3333吨碳酸钙计,也即生产832.5837Kmol/d或N2=34.6910Kmol/h 碳酸钙所需原料石灰石量,根据碳酸钙总收率应为:G2=N2/ηB=34.6910÷81.89%=42.3645 Kmol/h共计需原料石灰石量:G=G1+G2=27.7453+42.3645=70.1098 Kmol/h以下的所有物料衡算均根据以上的基准进行的。
物料衡算.pdf
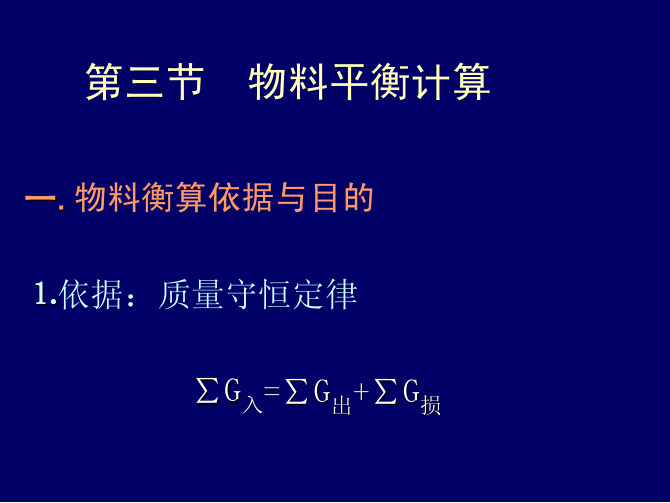
6)每吨原料乳标准化后应提取稀奶油量
=1000× [(3.5-8.1×0.38)/(30-5.87×0.38)]=15.2kg 或0.38=R=(1000 ×3.5-c ×30)/(1000 ×8.1-c ×5.87)
7)分离出30%的稀奶油15.2公斤,应需原料乳量
=1000×15.2/115=132kg
=(7.62×1000)/250=30.5≈30(瓶/分)
10) 工艺总损失5%(下厂调查) 11) 实际每分钟生产瓶数
=31/(100-5)%=32.6≈33瓶/min —设备生产能力 —瓶子数(周转7
12) 实际班产瓶数
=33×60×7小时=13860瓶/班 天)
13) 每班生产箱数 算基准
=13860/24=577.5≈578箱/班
面 粉 875kg 水 315kg 面 粉 350kg
酵 母 25kgkg 接种面团 1372.5kg
水 472.5kg 盐 25kg 油 50kg 切块损 失 52.2kg
可通过工厂实际数 据或实验得来。 注:部分原料工艺 损耗率及原料折用 率见书
糖 62.5kg
二次调粉后面团 2175kg 拌干粉 量 25kg 搓圆后面团 2127.8kg 湿面包坯 2147.8g 成品 1933.02k
=12228×(21.7%/74%)=3584kg
21)浓缩设备蒸发水量
=12228—3584=8644kg
22)乳糖品种添加量为0.025%取值 23)乳糖品种添加量
=3584×0.025%×1.1=1kg
24)浓缩过程中损失量1% 25)最终成品量
=(3584+1)×99%=3549kg
26)成品率=3549/10000=35.5%=成品/原料 27)采用962#罐397g 28)成品罐数=3549/0.397=8940罐 29)每箱48罐可装 =8940/48=186.3/48=186.3箱=187箱
物料平衡计算公式:教学文案
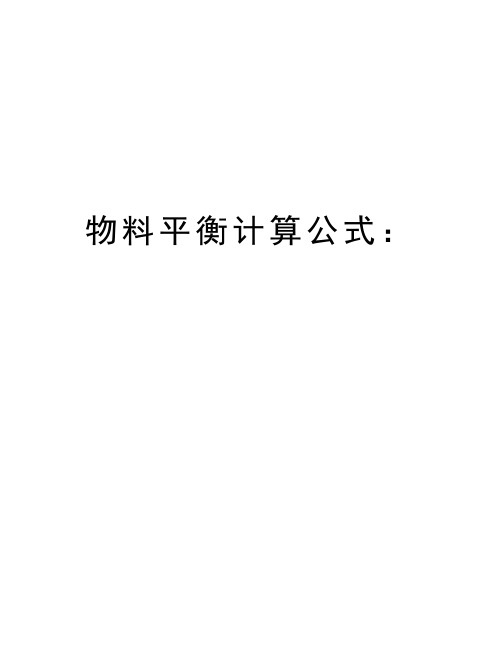
物料平衡计算公式:物料平衡计算公式:每片主药含量理论片重=测得颗粒主药百分含量1.原辅料粉碎、过筛的物料平衡物料平衡范围:97.0 %~100 %物料平衡= %100⨯+ac b a-粉筛前重量(kg) b-粉筛后重量(kg) c-不可利用物料量(kg)2.制粒工序的物料平衡物料平衡范围:98.0 %~104.0 %制粒工序的物料平衡=a d cb ++×100% 制粒工序的收率=ab ×100% a-制粒前所有原辅料总重(kg) b-干颗粒总重(kg)c-尾料总重(kg) d-取样量(kg)3.压片工序的物料平衡范围:97.0 %~100.0 %压片工序的物料平衡=a d cb ++×100% 压片工序的收率=ab ×100% a-接收颗粒重量(kg) b-片子重量(kg)c-取样重量(kg) d-尾料重量(kg)4.包衣工序的物料平衡包衣工序的物料平衡范围:98.0 %~100.0 %包衣工序的物料平衡 =ba e d c +++ 包衣工序的收率 =b ac +a-素片重量(kg) b-包衣剂重量(kg) c-糖衣片重量(kg) d-尾料重量(kg) e-取样量(kg)5.内包装工序物料平衡内包装工序物料平衡范围:99.5 %~100.0 %包材物料平衡=%100⨯++++Aa d cb B a- PTP 领用量(kg) b- PTP 剩余量(kg) A- PVC 领用量(kg)B- PVC 剩余量(kg) c-使用量(kg) d-废料量(kg)片剂物料平衡=%100⨯++ad c b a :领用量(Kg) b :产出量(Kg)c :取样量(Kg)d :废料量(Kg)6.外包装工序的物料平衡包装材料的物料平衡范围:100%包装材料物料平衡=%100⨯+++ea d cb e-上批结存 a-领用量 b-使用量 c-剩余量 d-残损量7.生产成品率成品率范围:90%~102%片剂收率= %100⨯++ad c b a-计划产量 b-入库量 c-留样量 d-取样量1.粉碎过筛和称配岗位物料平衡检查:配料量╳100%粉碎过筛后原辅料总重(物料平衡范围应控制在99.8~100.2%)2.制粒干燥、整粒总混岗位物料平衡检查:总混后重量+不良品╳100%干颗粒净重+润滑剂+崩解剂(物料平衡范围应控制在99.0~100.0%)3.充填抛光岗位物料平衡检查:胶囊总重+细粉+不良品+废胶囊壳重量╳100%颗粒总重+胶囊壳重量(物料平衡范围应控制在96.0~101.0%)4.铝塑内包岗位物料平衡检查:(成品板总重/平均每板重量+不良品)×规格(粒/板)╳100%胶囊领用量/平均胶囊重(物料平衡范围应控制在98.0~101.0%)5.总物料平衡检查:成品产量╳100%理论产量(物料平衡范围应控制在97~100%)。
物料平衡计算的技巧和步骤
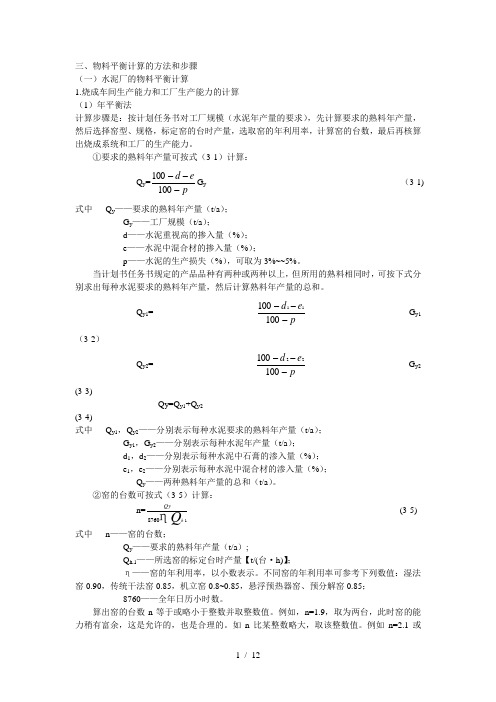
三、物料平衡计算的方法和步骤 (一)水泥厂的物料平衡计算1.烧成车间生产能力和工厂生产能力的计算 (1)年平衡法计算步骤是:按计划任务书对工厂规模(水泥年产量的要求),先计算要求的熟料年产量,然后选择窑型、规格,标定窑的台时产量,选取窑的年利用率,计算窑的台数,最后再核算出烧成系统和工厂的生产能力。
①要求的熟料年产量可按式(3-1)计算: Q y =ped ---100100G y (3-1)式中 Q y ——要求的熟料年产量(t/a );G y ——工厂规模(t/a );d ——水泥重视高的掺入量(%);e ——水泥中混合材的掺入量(%); p ——水泥的生产损失(%),可取为3%~~5%。
当计划书任务书规定的产品品种有两种或两种以上,但所用的熟料相同时,可按下式分别求出每种水泥要求的熟料年产量,然后计算熟料年产量的总和。
Q y1=pe d ---10010011G y1(3-2)Q y2=pe d ---10010022G y2(3-3)Qy=Q y1+Q y2(3-4)式中 Q y1,Q y2——分别表示每种水泥要求的熟料年产量(t/a );G y1,G y2——分别表示每种水泥年产量(t/a ); d 1,d 2——分别表示每种水泥中石膏的渗入量(%); e 1,e 2——分别表示每种水泥中混合材的渗入量(%); Q y ——两种熟料年产量的总和(t/a )。
②窑的台数可按式(3-5)计算:n=1.8760h QQyη (3-5)式中 n ——窑的台数;Q y ——要求的熟料年产量(t/a );Q h.1——所选窑的标定台时产量【t/(台·h)】;η——窑的年利用率,以小数表示。
不同窑的年利用率可参考下列数值:湿法窑0.90,传统干法窑0.85,机立窑0.8~0.85,悬浮预热器窑、预分解窑0.85;8760——全年日历小时数。
算出窑的台数n 等于或略小于整数并取整数值。
例如,n=1.9,取为两台,此时窑的能力稍有富余,这是允许的,也是合理的。
物料平衡计算公式
物料平衡计算公式 Document serial number【KK89K-LLS98YT-SS8CB-SSUT-SST108】物料平衡计算公式:每片主药含量理论片重=测得颗粒主药百分含量1.原辅料粉碎、过筛的物料平衡物料平衡范围:97.0%~100%物料平衡=%100⨯+ac b a-粉筛前重量(kg)b-粉筛后重量(kg)c-不可利用物料量(kg)2.制粒工序的物料平衡物料平衡范围:98.0%~104.0%制粒工序的物料平衡=a d cb ++×100% 制粒工序的收率=ab ×100% a-制粒前所有原辅料总重(kg)b-干颗粒总重(kg)c-尾料总重(kg)d-取样量(kg)3.压片工序的物料平衡范围:97.0%~100.0%压片工序的物料平衡=a d cb ++×100% 压片工序的收率=ab ×100% a-接收颗粒重量(kg)b-片子重量(kg)c-取样重量(kg)d-尾料重量(kg)4.包衣工序的物料平衡包衣工序的物料平衡范围:98.0%~100.0%包衣工序的物料平衡=b a e dc +++ 包衣工序的收率=ba c + a-素片重量(kg)b-包衣剂重量(kg)c-糖衣片重量(kg)d-尾料重量(kg)e-取样量(kg)5.内包装工序物料平衡内包装工序物料平衡范围:99.5%~100.0%包材物料平衡=%100⨯++++Aa d cb B a-PTP 领用量(kg)b-PTP 剩余量(kg)A-PVC 领用量(kg) B-PVC 剩余量(kg)c-使用量(kg)d-废料量(kg)片剂物料平衡=%100⨯++ad c b a :领用量(Kg)b :产出量(Kg)c :取样量(Kg)d :废料量(Kg)6.外包装工序的物料平衡包装材料的物料平衡范围:100%包装材料物料平衡=%100⨯+++ea d cb e-上批结存a-领用量b-使用量c-剩余量d-残损量7.生产成品率成品率范围:90%~102%片剂收率=%100⨯++ad c b a-计划产量b-入库量c-留样量d-取样量1.粉碎过筛和称配岗位物料平衡检查:配料量╳100%粉碎过筛后原辅料总重(物料平衡范围应控制在99.8~100.2%)2.制粒干燥、整粒总混岗位物料平衡检查:总混后重量+不良品╳100%干颗粒净重+润滑剂+崩解剂(物料平衡范围应控制在99.0~100.0%)3.充填抛光岗位物料平衡检查:胶囊总重+细粉+不良品+废胶囊壳重量╳100%颗粒总重+胶囊壳重量(物料平衡范围应控制在96.0~101.0%)4.铝塑内包岗位物料平衡检查:(成品板总重/平均每板重量+不良品)×规格(粒/板)╳100%胶囊领用量/平均胶囊重(物料平衡范围应控制在98.0~101.0%)5.总物料平衡检查:成品产量╳100%理论产量(物料平衡范围应控制在97~100%)。
物料平衡计算
物料平衡计算
7.物料平衡计算方法:
7.1 物料平衡计算:
配料平衡= 实际配料量(kg)
×100% 批理论配料量(kg)
物料平衡范围:99.5~100.5%
压片平衡= 【成品片重量(kg)+可回收量(kg)+不合格品量(kg)
+废弃量(kg)】×100%
领取颗粒重量(kg)
物料平衡范围:98%--100%
内包装平衡= 【实际产量(板)+取样量(板)+不合格品量(板)+废弃量
(板)】×100%
理论产量(板)
物料平衡范围:99.5%~100.5%
包装平衡= 【成品箱数(箱)×1板×10盒×20包+零头(包)×
1板×10盒+取样量(盒)×1板+不合格品量(板)】
×100%
半成品数量(板)
物料平衡范围:98%~102%
成品物料平衡= 成品入库数量+留样数量+不合格数量
×100% 理论产量(粒)
标签和类标签的包材物料平衡达100% 7.2技术经济指标:
7.2.1成品率:(理论收率)
成品率= 成品入库数量+留样量
×100% 理论产量
7.2.2成本:
成本=
车间成本(元)
成品与入库数量(片)7.2.3一次合格率:一次合格率= 一次合格品数
×100% 成品数。
物料平衡计算公式
精心整理
物料平衡计算公式:
每片主药含量
理论片重=
测得颗粒主药百分含量
1.原辅料粉碎、过筛的物料平衡
物料平衡范围:97.0%~100%
a-2.a-c-3.a-c-取样重量(kg)d-尾料重量(kg)
4.包衣工序的物料平衡
包衣工序的物料平衡范围:98.0%~100.0%
包衣工序的物料平衡=
b a e d
c +++ 包衣工序的收率=b
a c +
a-素片重量(kg)b-包衣剂重量(kg)c-糖衣片重量(kg)d-尾料重量(kg)e-取样量(kg)
5.内包装工序物料平衡
内包装工序物料平衡范围:99.5%~100.0%
包材物料平衡=%100⨯++++A
a d c
b B a-PTP 领用量(kg)b-PTP 剩余量(kg)A-PVC 领用量(kg)
B-PVC 剩余量(kg)c-使用量(kg)d-废料量(kg)
a c 6.e-7.a-1.配料量
╳100%
粉碎过筛后原辅料总重
(物料平衡范围应控制在99.8~100.2%)
2.制粒干燥、整粒总混岗位物料平衡检查:
总混后重量+不良品
╳100%
干颗粒净重+润滑剂+崩解剂
(物料平衡范围应控制在99.0~100.0%) 3.充填抛光岗位物料平衡检查:
胶囊总重+细粉+不良品+废胶囊壳重量
╳100%
颗粒总重+胶囊壳重量
(物料平衡范围应控制在96.0~101.0%) 4.
5.。
物料平衡计算公式
物料平衡计算公式在化工、制造业以及环境保护等领域,物料平衡计算是一项重要的工作。
通过物料平衡计算,可以确保生产过程中物料的流动和转化得到准确控制,从而提高生产效率和产品质量。
物料平衡计算利用物质守恒定律,根据输入和输出物质的质量来推导系统内部物质的转化和流动情况。
在进行物料平衡计算时,通常需要采用一些计算公式来求解各个参数和变量。
下面将介绍几个常用的物料平衡计算公式。
1. 总质量平衡计算公式总质量平衡计算是最基本的物料平衡计算。
它根据输入和输出物质的总质量来推导系统内部物质的转化和流动情况。
总质量平衡计算公式可以表示为:输入物质的总质量 = 输出物质的总质量 + 系统内部物质的总质量变化这个公式意味着,系统内部物质的总质量随着时间的推移可能会发生变化,可能会增加或减少。
2. 组件质量平衡计算公式除了总质量平衡计算,组件质量平衡计算也是非常重要的。
它根据输入和输出物质的组件质量来推导系统内部物质的组件转化和流动情况。
组件质量平衡计算公式可以表示为:输入物质中某组件的质量 = 输出物质中某组件的质量 + 系统内部物质中某组件的质量变化这个公式可以根据具体情况来进行求解,比如针对某个特定的化学反应,可以将反应物的组件质量与生成物的组件质量进行比较,从而推导出系统内部物质的组件转化情况。
3. 能量平衡计算公式除了物质平衡计算,能量平衡计算也是非常重要的。
它根据输入和输出物质的能量来推导系统内部物质的能量转化和流动情况。
能量平衡计算公式可以表示为:输入物质的总能量 = 输出物质的总能量 + 系统内部物质的总能量变化 + 系统对外界的能量传递这个公式包含了系统内部物质能量的变化以及系统与外界交换能量的情况。
在能量平衡计算中,通常需要考虑物质的热容和热传导等因素。
4. 浓度平衡计算公式在某些情况下,需要根据输入和输出物质的浓度来推导系统内部物质的浓度转化和流动情况。
浓度平衡计算公式可以表示为:输入物质中某组件的浓度× 输入物质的总流量 = 输出物质中某组件的浓度× 输出物质的总流量 + 系统内部物质中某组件的浓度变化× 系统内部物质的总流量这个公式可以根据具体情况来进行求解,比如针对某个溶解过程,可以将溶质的浓度与溶液的总流量进行比较,从而推导出系统内部物质的浓度转化情况。
- 1、下载文档前请自行甄别文档内容的完整性,平台不提供额外的编辑、内容补充、找答案等附加服务。
- 2、"仅部分预览"的文档,不可在线预览部分如存在完整性等问题,可反馈申请退款(可完整预览的文档不适用该条件!)。
- 3、如文档侵犯您的权益,请联系客服反馈,我们会尽快为您处理(人工客服工作时间:9:00-18:30)。
物料平衡计算书年产8万吨醋酸乙烯项目
设计团队:ET-5队
小组成员:张钊田燕苟晓桃卢锁霞李雪梅
设计单位:西北师范大学
设计时间:2019年7月
目录
第1章总论 (1)
第2章物料衡算的意义 (2)
第3章物料衡算遵循的原则 (3)
第4章物料衡算 (4)
4.1 物料衡算任务 (4)
4.1.1 醋酸乙烯合成工段物料衡算 (4)
4.1.2 醋酸乙烯粗分工段物料衡算 (1)
4.1.3 二氧化碳气体吸收工段物料衡算 (1)
4.1.4 醋酸乙烯精制工段物料衡算 (12)
4.1.5 全流程衡算 (1)
第1章总论
本项目利用总厂乙烯和醋酸及空气置换的氧气使用经典的USI方法生产工业级的醋酸乙烯产品,每年生产量为 8 万吨。
在已确定化学生产工艺和流程后,由定性阶段转向定量阶段,通过对整个生产系统、生产车间,以及部分重要的生产单元进行物料衡算计算出主、副产品的产量,原材料的消耗定额、“三废”排放量及组成,以及产品收率等各项经济技术指标,从而定量地评述初步设计所选择的工艺路线、生产方法及工艺流程在经济上是否合理。
第2章物料衡算的意义
在化学工程中,设计或改造工艺流程和设备,了解和控制生产操作过程,核算生产过程的经济效益,确定原材料消耗定额,确定生产过程的损耗量,对现有的工艺过程进行分析,选择最有效的工艺路线,对设备进行最佳设计以及确定最佳操作条件等都要进行物料衡算。
而且,化学工程的开发与放大都以物料衡算为基础的。
物料衡算是质量守恒定律的一种表现形式。
凡引入某一设备的物料成分、质量或体积比等于操作后所得产物的成分、质量或体积加上物料损失。
第3章物料衡算遵循的原则
1)对一般的体系而言,物料分布均可表示为:
∑(物料的累积率)=∑(物料进入率)-∑(物料流出率)+∑(反应生成率)-∑(反应消耗率)
2)当系统没有化学反应时,则可简化为:
∑(物料的累积率)=∑(物料进入率)-∑(物料流出率)
3)在稳定状态下有:
∑(物料进入率)=∑(物料流出率)
4)物料衡算包括总质量衡算、组分衡算和元素衡算。
各种衡算方法的适用情况
如表 3-1 所示:
第4章物料衡算
4.1物料衡算任务
从原料到产品输出,其工艺路线可分为如下3个步骤:
醋酸乙烯合成工段、甲基丙烯酸甲酯合成工段、甲基丙烯酸甲酯精制工段。
对于本厂,工艺采取年开工300天(7200小时)的连续操作,其中一年内的四~五周(约30天)用于固定的停车设备检修及紧急情况处理。
物料衡算的主要任务在于:
(1)确定醋酸乙烯酯的实际产量以及质量指标;
(2)确定氯仿、乙烯、乙酸、氧气的循环量以及损失率等指标;
(3)确定工艺中的“三废”排放量等公共经济指标;
(4)各主要单元过程的物料衡算,并指导工艺设备的尺寸确定;
(5)汇总全流程物料衡算,数据用于完成物料流程图等后续设计任务
4.1.1
醋酸乙烯合成工段物料衡算
图4-1醋酸乙烯合成工段流程图
由工艺流程图可知,反应工段有反应器、混合罐、换热器单元过程,需要对它们进行物料衡算。
醋酸乙烯粗分工段物料衡算
4.1.2
图4-2醋酸乙烯粗分工段流程图
由工艺流程图可知,醋酸乙烯粗分工段有气液分离罐、混合器,换热器,吸收塔,需要对它们进行物料衡算,因为E0202,E0203(换热器)单股进料出料,流股组成未发生变化,不对其进行物料衡算。
4.1.3
二氧化碳气体吸收工段物料衡算
图4-3二氧化碳气体吸收流程图
程图可知,醋酸乙烯气体吸收工段工段有混合罐、闪蒸罐和吸收塔重要单元过程,需要对它们进行物料衡算。
4.1.4
醋酸乙烯精制工段物料衡算
图4-4醋酸乙烯酯精制流程图
由工艺流程图可知,醋酸乙烯精制工段工段有萃取塔、混合罐、吸收塔和精馏塔等重要单元过程,需要对它们进行物料衡算。
因为泵与换热器只有一股进料,所以不需要做物料平衡计算。
全流程衡算
4.1.5
全流程中,对所有进口流股的物料和所有出口流股的物料进行物料衡算,核算总进口质量与出口质量之差
年产8万吨醋酸乙烯酯项目表21全流程物流结果表(二)
年产8万吨醋酸乙烯酯项目
进物料总质量流量: 11221.5+12859.998+30000+9367.9+477161+2327.8+11871.9=542938.2
进物料总质量流量:3899.56+178034.1+1321.12+4448.4+5367.8+312362.1+34197.7+10291.77=542938.1
误差:出料质量-进料质量=542938.1-542938.2=-0.1
由上述结果,所有表格可以看出,单元进、出物料的总体质量保持平衡。
2
年产8万吨醋酸乙烯酯项目
1。