细纱工艺设计
细纱传动及工艺计算

关,一般Δ为细纱直径d的4倍.根据捻率和捻系数关系式,当纱条单位体积 重量为0.8g/cm时,细纱直径d≈0.04√Tt,于是有
△ = 0.16√Tt 式中:Tt——细纱线密度.
(二)卷绕变换成对齿轮 ZF/ZG (升降变换成对齿轮) 卷绕变换成对齿轮 ZF/ZG 是调整成形凸轮转速或钢领板一次升降时间,
下降快,且快------慢
三. 细纱机自动控制装置
(1)中途关车,自动适位制动停车; (2)中途提前落纱,钢领板自动下降到落纱位置,适位制动停车; (3)满管落纱,钢领板自动下降到落纱位置,适位制动停车; (4)开车前,钢领板制动复位; (5)打开车门时,全机安全自停; (6)满纱后,自动接通36V低压电源,供电动落纱小车落纱; (7)车头面板数字显示牵伸倍数、纺纱线密度、罗拉及锭子速度; (8)纺制直接纬纱时,自动绕取保险纱。
2、形式:圆锥形交叉卷绕形式(又称短动 程升降卷绕)
相邻两卷绕密度不同,向上卷绕密,称为 卷绕层;向下卷绕稀,称为束缚层。这样可 防止内外纱层相嵌。
3、钢领板的运动必须满足的条件: ①短动程升降h,一般上升慢,下降快。
由成形凸轮控制。 ②每次升降后有级升m。 ③管底成形,即绕纱高度和级升从小到
大逐层增加。 即h1﹤h2﹤h3﹤..... ﹤hn = h
式中:当D4=22mm时,ZE=36T;当D4=24mm时,ZE=33T; 当D4=20.2mm时,ZE=39T.
(二)实际捻度 细纱的实际捻度是由捻度试验机测得的。由于机台锭带的滑溜率,
加捻时的捻缩率及加捻效率的影响,使实际捻度与计算捻度往往有差异。 当实测捻度与计算捻度差异大于3%时,应调整捻度变换齿轮。
C19.4tex细纱工艺设计

65 43
38 ZH
33 28
d2 d3
=
65 43
38 ZH
33 28
27 27
=
67.699 ZH
式中:d2——中罗拉直径(27mm); d3——后罗拉直径(27mm); ZH——后牵伸变换齿轮,有 42,43,44,45,47,48,50,52,54,57,59,62,65。
选取后区牵伸选择为
N1
60 Tt
Nt 10
(1 - 捻缩率) 1000 1000
式中:d1——前罗拉直径(mm); N2——前罗拉转速(r/min); N1——锭子转数(r/min); Tt——细纱捻度(捻/10cm); Nt——细纱线密度(tex)。
资料仅供参考
②定额产量 G 定=G 理×时间效率
细纱工序的时间效率一般为 95%~97%,取 96%。 纺 19.4tex 的纱线,则
每台细纱机每天工作 22.5h,则每台细纱机每天定额产量=22.86×22.5=514.35 【Kg/(台·天)】
讨论
资料仅供参考
提高细纱质量的主要技术措施: ① 优选和科学的使用细纱机的专件和器材; ② 合理的细纱生产工艺和工艺措施; ③ 合理的细纱定量和细纱牵伸倍数; ④ 合理的细纱捻系数和细纱后牵伸; ⑤ 适当的细纱隔距快; ⑥ 保证工艺上车要求; ⑦ 创造适宜的温湿度环境; ⑧ 加强设备和工艺管理; ⑨ 设备的周期管理和定期的质量检测; ⑩ 定期对细纱经行质量检测。
资料仅供参考
再见 SEE YOU LATER
粗纱干定量(g/10m) 10 细纱干定量( g/100m)
若细纱线密度为
19.4tex,则
E
实=
542.5 19.4
细纱机钢丝圈型号

细纱机钢丝圈型号篇一:细纱工艺设计方案细纱工艺设计方案1. 分析细纱技术性能选用细纱机型号为FA506型,其主要技术特征见下表2. 配置细纱机主要工艺参数(1)总牵伸与牵伸分配纺18.2tex,考虑总牵伸在30倍;加工针织用纱,后区牵伸一般为1.04~1.20倍,通常情况下偏小为宜,本设计取1.10倍。
(2)罗拉中心距采用三罗拉长短皮圈,握持距的影响因素很多,主要以纤维品质长度而定,一般用经验公式计算。
具体配置如下:(3)罗拉加压皮辊加压(前×中×后)选择150N/双锭×100 N/双锭×140 N/双锭。
(4)皮圈钳口隔距隔距块厚度选择3.0mm。
(5)锭速选择本设计选用FA506型细纱机,所纺纱线为纯棉普梳18.2tex 细特纱,锭速初定为15000r/min。
(6)钢领与钢丝圈的选配钢领与钢丝圈的选配如下:3. FA506型细纱机工艺计算 FA506变换齿轮和皮带轮见下表:(1)速度计算① 主轴转速(r/min)=n×式中:n——主电动机转速(r/min);——主电动机皮带轮节径(mm),有170mm,180mm,190mm,200mm,210mm;——主轴皮带轮节径(mm),有180mm,190mm,200mm,210mm、220mm、230mm、240mm;② 锭子转速(r/min)=×=1460××式中:=16060×——滚盘直径(mm);——锭盘直径(mm);δ——锭带厚度(mm)。
实例:纺18.2tex纱,锭子转速初定为15500r/min,则取170mm,取180mm,则锭子转速修正为15168r/min。
③ 前罗拉转速(r/min)==1460×××××××=8.44××××式中:——捻度变换成对齿轮齿数,有、、、、、、(其中+=120)——捻度变换齿轮(中心牙)齿数,有87、85、80,有77、80、85;为——捻度微调变换齿轮齿数(=20.2mm时,为39;=22mm时,36;=24mm时,为33;)(2)细纱定量及线密度所纺纱线设计线密度为18.2tex,设计细纱标准干定量为==1.68(g/100m)细纱实际回潮率为6.5%,则细纱湿重为=1.68×(1+6.5%)=1.79(g/100m)(3)牵伸计算① 实际牵伸篇二:环锭细纱机钢领环锭细纱机钢领、钢丝圈问题的讨论20xx年7月16日安徽省纺织工程学会钢领、钢丝圈是环锭细纱机及普通环锭捻线机的关键部件,它们与锭子、纱管等配套共同完成纱线的加捻及卷绕,钢领、钢丝圈质量好坏,直接影响纺纱质量、纺纱效率及经济效益,若配套使用不当,不仅影响钢领、钢丝圈使用寿命,而且纺纱张力不稳定,引起纱线毛羽增加、细纱条干恶化、并使细纱断头增加、生产效率下降。
细纱工艺设计

细纱工艺表一、细纱工艺设计的相关知识 1.细纱定量10%)5.81(⨯+=tT G 细纱2.牵伸工艺设计 (1) 总牵伸倍数注:纺精梳纱,牵伸倍数可偏上限选用,固定钳口式牵伸的牵伸倍数偏下限选用表1-2 纺纱条件对总牵伸倍数的影响(2) 后牵伸区工艺表1-3 后牵伸区工艺参数3.捻系数表1-4 影响捻系数的因素%100-(%)⨯=前罗拉输出须条长度加捻成纱长度前罗拉须条输出长度捻缩率表1-6 捻缩率与捻系数的关系比例4.锭速表1-7 不同纺纱特数的参考范围5.卷绕圈距△△是指卷绕层的圈距,一般△为细纱直径的4倍;δtT d 03568.0=当纱条单位体积质量为0.8g/cm 3时,纱线直径为:t T d 04.0≈△ =t T 16.0 6.钢领板级升距)2/sin(1202γρtT m =式中:ρ---管纱卷绕密度,在一般卷绕张力条件下为0.55g/cm 3 2/γ---成形半锥角有关卷绕的其他参数如图所示,参考值见下表: 表1-8 细纱机卷绕部分其他参数7.纲领与钢丝圈(1) 平面纲领与钢丝圈型号的选配表1-9(2) 锥面纲领与钢丝圈型号的选配表1-10(3) 钢丝圈号数的选择表1-11 纯棉纱钢丝圈号数选用范围(4) 钢丝圈轻重的掌握表1-128.罗拉中心距(1)前区罗拉中心距表1-13 前牵伸区罗拉中心距与浮游区长度(2)后区罗拉中心距表1-14后牵伸区罗拉中心距的参考范围9.胶圈钳口隔距表1-15 胶圈钳口隔距参考范围注:在条件许可下,采用较小的上下销钳口隔距,有利于改善成纱质量。
表1-16纺纱条件对胶圈钳口隔距的影响10.罗拉加压表1-17 罗拉加压参考范围11.前区集合器表1-18二、任务实施1.选定粗纱定量、设计细纱定量及牵伸倍数 表1-19 粗纱定量选用参考范围考虑到TJFA458A 型粗纱机的牵伸形式,并结合细纱机的牵伸能力,初步设计粗纱的定量为3.5g/10m 。
根据所纺细纱的线密度JC9.8tex ,公定回潮率为8.5%,实际回潮率为6.3%(在实际生产中,粗纱的回潮率控制在6.0%~6.5%)细纱定量为:)100/(9032.010%)5.81(8.910%)5.81(m g T G t =⨯+=⨯+=细纱)100/96.0%3.619032.0%3.61m g G G ()()(细纱细纱湿=+⨯=+⨯=设FA506型细纱机的牵伸效率为98%(在实际生产中,工厂根据实际牵伸倍数与机械牵伸倍数计算获得,是个统计值,多数情况为94%-98%)。
现代纺纱技术课程教案——细纱

编码:01 制订日期:2007.8项目七细纱模块一细纱概述一、细纱工序的任务1、牵伸2、加捻3、卷绕成形二、细纱机工艺流程模块二细纱机机构一、喂入机构与作用1、喂入部分机构粗纱架、粗纱支持器(托锭式、吊锭式)、导纱杆、横动装置2、喂入作用分析喂入机构的作用:粗纱顺利退绕并均匀地、在一定宽度范围内喂入细纱机牵伸装置。
二、牵伸机构与作用1、牵伸部分的机构与特点(1)组成元件牵伸罗拉、罗拉轴承、皮辊(胶辊)、皮辊轴承、皮圈、皮圈销、集合器、加压机构、吸棉装置等。
2、细纱机牵伸装置的形式(1)三罗拉长短皮圈普通牵伸(2)三罗拉长短皮圈V形牵伸三、加捻卷绕机构与作用(一)细纱的加捻过程须条一端被前罗拉握持,另一端通过钢丝圈的回转而加上捻回,钢丝圈回转一转,加上一个捻回。
(二) 加捻卷绕元件1、锭子:由锭杆、锭盘、锭胆、锭脚和锭钩组成。
实用锭速为12000~18000r/min左右.2、筒管:有经纱管、纬纱管之分。
(1)经纱管长度:根据钢领板升降全程和纺纱线密度决定的,一般比钢领板升降全程大12%左右。
(2)直径:一般为钢领直径的40%~50%;(3)纬纱管用于纺直接纬纱,其长度和直径取决于梭子内腔长度和宽度。
3、钢领:平面钢领和锥面钢领两种①平面钢领PG2(边宽4.0mm) 适纺粗特纱(普通钢领)PG1(边宽3.2mm) 适纺中特纱(高速钢领)PG1/2(边宽2.6mm) 适纺中特纱(高速钢领)规格代号:PG×-×× ××例:PG1-42511-边宽3.2mm;42—内径42mm;51—底外径51mm②锥面钢领:HZ7系列;ZM系列(ZM-6,ZM-20)4、钢丝圈(1)钢丝圈的作用:与钢领、锭子配合完成细纱的加捻、卷绕。
生产上通过调整钢丝圈型号(几何形状)、号数(重量)来控制纺纱张力、稳定气圈形态,达到卷绕成形良好、降低细纱断头的目的。
(2)钢丝圈的工艺要求钢丝圈的几何形状与钢领跑道截面的几何形状要正确配合,钢丝圈的重心要低,使其回转稳定。
细纱工序工艺技术
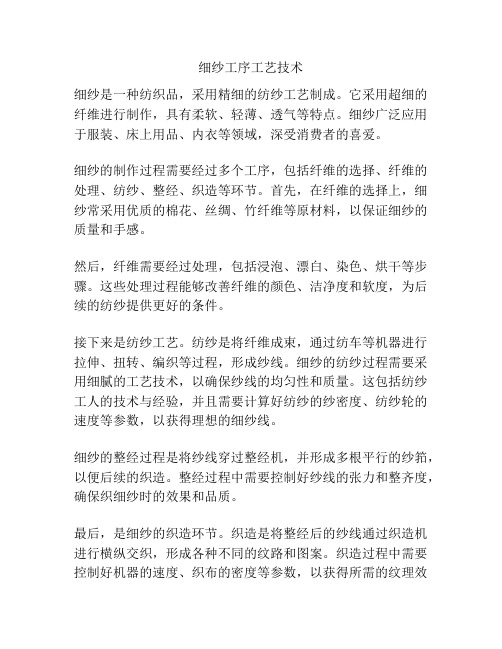
细纱工序工艺技术细纱是一种纺织品,采用精细的纺纱工艺制成。
它采用超细的纤维进行制作,具有柔软、轻薄、透气等特点。
细纱广泛应用于服装、床上用品、内衣等领域,深受消费者的喜爱。
细纱的制作过程需要经过多个工序,包括纤维的选择、纤维的处理、纺纱、整经、织造等环节。
首先,在纤维的选择上,细纱常采用优质的棉花、丝绸、竹纤维等原材料,以保证细纱的质量和手感。
然后,纤维需要经过处理,包括浸泡、漂白、染色、烘干等步骤。
这些处理过程能够改善纤维的颜色、洁净度和软度,为后续的纺纱提供更好的条件。
接下来是纺纱工艺。
纺纱是将纤维成束,通过纺车等机器进行拉伸、扭转、编织等过程,形成纱线。
细纱的纺纱过程需要采用细腻的工艺技术,以确保纱线的均匀性和质量。
这包括纺纱工人的技术与经验,并且需要计算好纺纱的纱密度、纺纱轮的速度等参数,以获得理想的细纱线。
细纱的整经过程是将纱线穿过整经机,并形成多根平行的纱筘,以便后续的织造。
整经过程中需要控制好纱线的张力和整齐度,确保织细纱时的效果和品质。
最后,是细纱的织造环节。
织造是将整经后的纱线通过织造机进行横纵交织,形成各种不同的纹路和图案。
织造过程中需要控制好机器的速度、织布的密度等参数,以获得所需的纹理效果。
总之,细纱工序涉及多个环节,需要细致的工艺技术和丰富的经验。
从纤维的选择到最终的织造,每个环节都需要精心处理,以制作出优质的细纱产品。
只有在这些环节中加入科学的技术和合理的操作,才能生产出细腻、柔软、高质量的细纱,满足消费者的需求。
细纱的制作工艺可以说是纺织行业中最为复杂和繁琐的之一。
从纤维的选择到最终的织造,每个环节都需要精细的处理和丰富的经验。
在下面的内容中,将详细介绍细纱工序的各个环节和其所需的技术细节。
首先,细纱的制作开始于纤维的选择。
优质的纤维是制作高品质细纱的基础,因此工厂通常会选用质地柔软、纤维细长、柔韧且不易起球的原材料。
棉花、丝绸、竹纤维以及一些高科技合成纤维如莱赛尔纤维和模丝纤维等都常用于细纱的制作。
(完整版)细纱工艺
细纱工艺一、细纱工序的任务1. 牵伸:将粗纱牵伸到所要求的特数。
2. 加捻:给牵伸后的纱条加上一定的捻度,使之具有一定的强力、弹性和光泽。
3. 卷绕:卷绕成管纱,便于运输和后加工。
二、细纱工艺设计概要在确定细纱工艺时,应考虑以下一些方面。
(1) 细纱机在向大牵伸方间发展。
为了加大细纱机的牵伸倍数,可采用不同的牵伸机构.改善在牵伸过程中对须条的控制,合理确定牵伸工艺,获得理想的效果。
在加压形式上,目前大多采用弹簧摇架加压和气动加压。
在加大细纱机的牵伸倍数、缩短前纺工序和减少并合数的同时,必须注意改进喂入半制品的质量。
(2) 细纱捻度直接影响成纱的强力、捻缩、伸长、光泽和毛羽、手感,而且捻度对细纱机的产量和用电等经济指标的关系很大,因此,必须全面考虑,合理选择捻系数。
(3) 在加强机械保全保养工作的基础上,保证最大限度地提高车速,选择合适的钢领、钢丝圈、筒管直径和长度等。
(4) 加大细纱管纱卷装可以有效地提高劳动生产率。
在确定管纱卷装时,应考虑最大限度地增加卷绕密度,但必须使络筒时发生的脱圈现象减少到最低限度,否则会降低劳动生产率。
三、细纱牵伸工艺(一) 细纱总牵伸倍数在保证和提高产品质量的前提下,提高细纱机的牵伸倍数,在经济上获得较大的效益。
目前细纱机的牵伸倍数一般在30—50 倍。
总牵伸倍数的能力首先决定于细纱机的机械工艺性能,但总牵伸倍数也因其他因素而变化。
当所纺棉纱线密度较粗时,总牵伸能力较低;当所纺棉纱线密度较细时,总牵伸能力较高;在纺精梳棉纱时,由于粗纱均匀、结构较好、纤维伸直度好、所含短绒率也较低,牵伸倍数一般可高于同线密度非精梳棉纱;纱织物和线织物用纱的牵伸倍数也可有所不同,这是因为单纱经并线加捻后,可弥补若干条干和单强方面的缺陷,但也必须根据产品质量要求而定。
总牵伸倍数过高,产品质量将恶化,棉纱条干不匀率和单强不匀率高,细纱机的断头率也增高。
但总牵伸倍数过小,对产品质量未必有利,反而增加前纺的负担,造成经济上的损失。
细纱工艺计算2
136
15080 12681 12399 11159 10628 10145
4
2. 前罗拉转速(n前)计算
n前n电 D D 1 21 4 9 8Z Z3 4 2 64 3
式中:
Z3 /Z4——捻度成对变换齿轮齿数
5
二、捻度与捻度齿轮的计算
1.选取捻系数 t
根据纱线细度、用途、品质要求和原料特性等选取 捻系数。可从棉纺手册查得。
176
180
200
210
220
19959
19581 18649 16784
19146 18234 16411
17232 16411 14770
15630 14067
15665 14919 13457
176
19516
16046 14442 13754 13129
148 17859
13800 13493 12144 11566 11040
后区牵伸倍数与后牵伸变换齿轮
Z29
23
24 25 26 27 28 29 30 31 32 33 34
后牵伸倍数 1.02 1.06 1.11 1.16 1.20 1.25 1.29 1.33 1.38 1.42 1.47 1.51
9
2、总牵伸倍数与总牵伸变换齿轮
E 总 V V 前 后 d d 前 后 n n 后 前 d d 前 后 n n 前 后 d d 前 后 Z Z 前 后
本机提供的捻度
69.55 71.60 73.77 75.62 76.72 78.91 81.23 83.70 85.49 85.82 88.28 90.87 93.63 96.46 99.30 102.14 102.54 104.73
细纱工艺设计任务与实施.
【工作页—细纱工艺设计】
工作任务
1. 根据分组设计的纱线产品实例,配置该纱线品种的细纱工艺
► 要求:①各小组制定工作计划(时间安排、人员分工、工作程序等) ②提交细纱工艺设计报告(包括参数配置、工艺计算过程等)
③填写细纱工艺设计单 ④上机调试细纱机工艺
⑤制作PPT 电子文档,对你的细纱工艺设计方案进行答辩
2.制作PPT 电子文档,对你的细纱设计方案进行答辩
班级组别学号姓名:日期
纱线品种代号:
主要内容:
►分析所选细纱机技术特点
►配置细纱机主要工艺参数(要说明参数选择的依据,列出详细计算过程)
►完成细纱工艺单设计
►细纱机上机工艺调试(牵伸、捻度)
附表:细纱工艺设计单(表6-11)
表6-11 细纱工艺单
注:细纱机每台420锭。
纺纱工艺设计
一、29tex纯棉普梳纱 此纱主要供29tex 织物的经、纬纱用
29tex、236根/10cm 236根/10cm
(一)细纱机工艺设计 1、细纱干定量(g/100m)Βιβλιοθήκη G G0 W G0 G G0 1W
Gk Ntex 1000 L L 100 Gk
Ntex 2.9 g 10
2.9 2.673 g 1 8.5%
2、细纱机牵伸倍数的设计
FA506型细纱机牵伸倍数10-50倍;
细纱机总牵伸倍数参考范围
纺纱线密度(tex) 摇架加压牵伸倍数
9以下
40-50
9-19
25-50
20-30
20-35
32以上
12-25
选用21倍牵伸
粗纱干定量
G入 E G出 G入 EG出 21 0.267 5.6 g / 10 m
普梳织布用 纱 精梳织布用 纱
11.7~30.7 32.4~194 4.0~5.3 5.3~16 16.2~36.4
细纱的捻系数较低设定为320,可改善布面的丰满度。
Tt
t
Ntex
320 61.9捻 / 10cm 29
4、锭速的选择 锭速的选择与纺纱线密度、纤维特性、钢领直径等有 关; 国产细纱机在14000~17000 r/min,国外可达25000 r/min; 纺制纯棉粗特纱时锭速为10000~14000 r/min,纺棉中特 纱时锭速为14000~16000 r/min,纺棉细特纱时锭速为 14300~16500 r/min; 锭速选用16000 r/min
后区牵伸:机织用纱在1.25~1.5倍;针织用纱在1.02~1.15倍。 后区牵伸选用1.24倍。
- 1、下载文档前请自行甄别文档内容的完整性,平台不提供额外的编辑、内容补充、找答案等附加服务。
- 2、"仅部分预览"的文档,不可在线预览部分如存在完整性等问题,可反馈申请退款(可完整预览的文档不适用该条件!)。
- 3、如文档侵犯您的权益,请联系客服反馈,我们会尽快为您处理(人工客服工作时间:9:00-18:30)。
细纱工艺表一、细纱工艺设计的相关知识 1.细纱定量10%)5.81(⨯+=tT G 细纱2.牵伸工艺设计 (1) 总牵伸倍数注:纺精梳纱,牵伸倍数可偏上限选用,固定钳口式牵伸的牵伸倍数偏下限选用表1-2 纺纱条件对总牵伸倍数的影响(2) 后牵伸区工艺表1-3 后牵伸区工艺参数3.捻系数表1-4 影响捻系数的因素%100-(%)⨯=前罗拉输出须条长度加捻成纱长度前罗拉须条输出长度捻缩率表1-6 捻缩率与捻系数的关系比例4.锭速表1-7 不同纺纱特数的参考范围5.卷绕圈距△△是指卷绕层的圈距,一般△为细纱直径的4倍;δtT d 03568.0=当纱条单位体积质量为0.8g/cm 3时,纱线直径为:t T d 04.0≈△ =t T 16.0 6.钢领板级升距)2/sin(1202γρtT m =式中:ρ---管纱卷绕密度,在一般卷绕张力条件下为0.55g/cm 3 2/γ---成形半锥角有关卷绕的其他参数如图所示,参考值见下表: 表1-8 细纱机卷绕部分其他参数7.纲领与钢丝圈(1) 平面纲领与钢丝圈型号的选配表1-9(2) 锥面纲领与钢丝圈型号的选配表1-10(3) 钢丝圈号数的选择表1-11 纯棉纱钢丝圈号数选用范围(4) 钢丝圈轻重的掌握表1-128.罗拉中心距(1)前区罗拉中心距表1-13 前牵伸区罗拉中心距与浮游区长度(2)后区罗拉中心距表1-14后牵伸区罗拉中心距的参考范围9.胶圈钳口隔距表1-15 胶圈钳口隔距参考范围注:在条件许可下,采用较小的上下销钳口隔距,有利于改善成纱质量。
表1-16纺纱条件对胶圈钳口隔距的影响10.罗拉加压表1-17 罗拉加压参考范围11.前区集合器表1-18二、任务实施1.选定粗纱定量、设计细纱定量及牵伸倍数 表1-19 粗纱定量选用参考范围考虑到TJFA458A 型粗纱机的牵伸形式,并结合细纱机的牵伸能力,初步设计粗纱的定量为3.5g/10m 。
根据所纺细纱的线密度JC9.8tex ,公定回潮率为8.5%,实际回潮率为6.3%(在实际生产中,粗纱的回潮率控制在6.0%~6.5%)细纱定量为:)100/(9032.010%)5.81(8.910%)5.81(m g T G t =⨯+=⨯+=细纱)100/96.0%3.619032.0%3.61m g G G ()()(细纱细纱湿=+⨯=+⨯=设FA506型细纱机的牵伸效率为98%(在实际生产中,工厂根据实际牵伸倍数与机械牵伸倍数计算获得,是个统计值,多数情况为94%-98%)。
第一步:计算实际牵伸倍数 75.389032.0105.310=⨯=⨯=细纱粗纱估实际估G G E 第二步:计算机械牵伸倍数 57.3998.075.38===牵伸效率实际估机械估E E 细纱机的总牵伸倍数是指前罗拉与后罗拉之间的牵伸倍数。
如图所示:由其传动图求其总牵伸倍数。
31310129.927372823271045935d Z Z d Z Z d Z Z d Z Z E N J M K N J M K ⨯⨯⨯⨯⨯=⨯⨯⨯⨯⨯⨯⨯⨯⨯⨯⨯⨯=机械33.392528482569850129.9=⨯⨯⨯⨯⨯=式中:K Z --39、43、48、53、59、66、73、81~89;取85 J Z --39、43、48、53、59、66、73、81~89;取48 M Z --69、59;取69 N Z --28、46;取28 1d --前罗拉直径,mm ,25 3d --后罗拉直径,mm ,25第三步:计算修正后的细纱实际牵伸倍数、粗纱定量及线密度 54.3898.033.39=⨯=⨯=牵伸效率机械实际E E g/10m )48.3109032.054.3810(细纱实际粗纱=⨯=⨯=G E Gtex )58.377100%5.8148.3100%5.81()()(粗纱粗纱=⨯+⨯=⨯+⨯=G T t 第四步:计算后区牵伸倍数中罗拉和后罗拉间的牵伸倍数(结合表1-3)37.12540257826.547826.542336353232~=⨯⨯=⨯⨯=⨯⨯⨯⨯=d Z d d Z de H H 后罗拉中罗拉式中:H Z --36、38、40、42、44、48、50;取40 2d --中罗拉直径,mm ,25 2.设计捻度第一步:初步选取捻系数根据表1-4,参考表1-5,初步设计细纱的捻系数为350. 第二步:计算捻度(1) 计算细纱的捻度: )10/(80.1118.9350cm T T tt t 捻回估估===α(2) 根据传动图,细纱的捻度为: EC A DB EC AD B tex Z Z Z Z Z Z Z Z d Z Z D T ⨯⨯⨯⨯=⨯⨯⨯⨯⨯⨯⨯+⨯⨯⨯⨯⨯⨯+=74.2422253228)(100375971)(3πδδ)10/(16.112368045807574.2422cm 捻回=⨯⨯⨯=式中:3D --滚盘直径,mm ,250mmd--锭盘直径,mm ,24mm 、22mm 、20.5mm ;取22mm δ--锭带厚度,0.8mmB A Z Z /--38/82、45/75、52/68、60/60、68/52、75/45、82/38;取45/75C Z --80、85、87;取80D Z --77、80、85;取80E Z --捻度变换齿轮齿数(与锭盘直径有关),33()24mm φ、)22(36mm φ、)mm 5.2039φ(,取36第三步:计算细纱的捻系数12.3518.916.112=⨯=⨯=t tex t T T α根据表1-6,确定捻缩率为2.26%,为方便操作,捻向设计为Z 向。
3.设计速度 (1) 前罗拉速度%9827375971273228146021⨯⨯⨯⨯⨯⨯⨯⨯⨯⨯⨯⨯⨯⨯=D B E C A Z Z D Z Z Z D n 前罗拉min)/(77.160807520036804518027.827.821r Z Z D Z Z Z D D B E C A =⨯⨯⨯⨯⨯⨯=⨯⨯⨯⨯⨯⨯=式中:1D --电动机带盘节径,mm ,170mm 、180mm 、190mm 、200mm 、210mm ;取180mm2D --主轴带盘节径,mm ,180mm 、190mm 、200mm 、210mm 、220mm 、230mm 、240mm ;取200mm(2) 锭子速度min)/(14165200)8.022(180)8.0250(8.1430%98)()(1460213r D d D D n =⨯+⨯+⨯=⨯⨯+⨯+⨯=δδ锭子4.设计卷绕圈距 第一步:预测卷绕圈距)(5009.08.916.016.0mm T t =⨯=⨯=∆估 第二步:计算卷绕圈距如图所示,钢领板每升降一次,前罗拉输出长度等于同一时间内管纱卷绕长度。
2sin3)(342273720251271042025352201γπππ⨯∆⨯-⨯=⨯∆⨯⨯-=⨯⨯⨯⨯⨯⨯⨯⨯⨯⨯⨯⨯o m m F G d d A d d Z Z d2sin3)(62.4426202γπ⨯∆⨯-⨯=⨯d d Z Z m FG2sin)(0001355.0202γ⨯∆-⨯=d d Z Z m FG2247.10sin 5009.0)1835(0001355.0⨯-⨯=F G Z Z 式中:m d --管纱直径,mm ,35mm o d --管纱直径,mm ,18mm2/γ--成形半锥角,047.10 式中个数据从表1-8中选取。
122=+F G Z Z ,所以52,70==F G Z Z ,则: )(50.07047.10sin 52)1835(0001355.02sin)(0001355.002222mm Z Z d d GFo m =⨯⨯-⨯=⨯⨯-⨯=∆γ5.设计钢领板级升距 第一步:预测钢领板级升距 )(2610.047.10sin 55.01208.9)2/sin(12002mm T m t=⨯⨯==γρ估 式中:ρ--管纱绕纱密度,在一般卷绕张力条件下为0.553/cm g 第二步:计算钢领板级升距由传动图可知,钢领板每升降一次,级升距变换棘轮n Z 撑过n 齿,从而获得级升距2m 。
1301304014014015462⨯⨯⨯⨯⨯⨯=⨯⨯⨯⨯⨯⨯=ππn n Z n D D Z D n m2557.04319556.109556.10=⨯=⨯=n Z n 式中:4D --上分配轴左端轮直径,mm ,130mm 5D --钢领板牵吊轮直径,mm ,130mm 6D --卷绕论直径,mm ,140mmn Z --43、45、48、50、55、60、65、70、72、75、80,取43 6.选取纲领与钢丝圈参考表1-9、表1-10、表1-11、表-12,选择纲领、钢丝圈如下: 纲领:PG1/2,直径38mm 。
钢丝圈型号:2.6Elf。
钢丝圈号数:15/0。
7.设计罗拉中心距根据FA506型细纱机的牵伸形式(长短胶圈牵伸),纤维、粗纱及所纺纱的情况,设计罗拉中心距如下:前区罗拉中心距采用43mm。
后区罗拉中心距采用54mm。
8.设计其他工艺参数(1)罗拉加压(daN/双锭)根据设计的罗拉速度、中心距、定量,选择罗拉的加压为:⨯14前罗拉⨯中罗拉后罗拉:⨯1014⨯(2)胶圈原始钳口隔距由于细纱的线密度为9.8tex,根据表1-15,表1-16,选择胶圈原始钳口隔距为2.4mm。
(3)前区集合器由于细纱的线密度为9.8tex,根据表1-18,选择细纱机的前区集合器开口尺寸为1.6mm。
9.细纱工艺设计表表1-19 细纱工艺设计表。