船舶舵系镗孔工艺规范
油轮舵叶镗孔工艺

73400 DWT 油轮舵叶镗孔工艺一.舵叶镗孔前具备的条件。
1.舵叶的所有的焊接工作全部结束,并经船东船检认可,冲沙并涂一度防锈底漆后才可以进行镗孔。
二.舵叶的划线与找平。
1.划出舵叶两端面的等分线,两等分线的连线构成的平面即为舵叶的纵中剖面,打上洋冲点,提交船检认可。
2.将舵叶置于胎架上,采用临时支撑固定,在舵叶下部布置四只千斤顶用以调节舵叶的水平位置,提交船检认可(如图一所示)。
3.按图一所示安装激光仪两只,将两只激光仪2在同样适当的高度调节水平,利用千斤顶调节舵叶的水平位置,使得舵叶相应上下端面与舵叶的纵中面的交点分别与相应激光经纬仪2的光点重合,则舵叶水平。
将舵叶焊于胎架平台上,防止移动,且提交船检认可。
4.按图一所示安装激光经纬仪3,调节其高度及左右位置,使得激光经纬仪3与舵叶纵中剖面等高且使激光经纬仪的光点在上下端面上距边缘的距离分别为560mm和2000mm,则激光经纬仪3的光线为舵叶所要加工的中心线,误差不超过0.2mm。
5.划出加工圆及检验圆,并打上洋冲点(如图二所示)。
三.舵叶的镗孔。
1.采用专用镗排进行镗孔,将镗排调整与加工圆同轴即可进行。
2.根据图纸要求分别镗孔,对于上铸钢件的下端面先镗至φ476mm,对于下铸钢件的下端面先镗至φ442.8mm(即下舵销孔)。
拂配余量施工人员自己控制。
3.锥孔镗削前首先镗出阶梯孔,加工尺寸如图三所示。
4.利用镗杆的靠模装置分别将上下锥孔镗至如图四所示尺寸(见“舵结构”(F131-100)和“上铸钢体”(M131-100)、“下铸钢体”(M131-100)。
5.铸钢体加工出油槽和油孔(见“上铸钢体”(M131-100)和“下铸钢体”(M131-100)提交船东及船检认可。
6.制作完成后,内部清除铁屑杂质等并涂防锈油一度。
备注:该工艺已经考虑压入量,拂配余量根据现场加工确定。
测量时应由金加工车间检验员与质管部检验员分别测量,相互比较直到测量尺寸误差不超过0.02mm,然后把尺寸抱船研所计算舵销加工尺寸。
镗孔加工工艺介绍

镗孔
镗孔是对锻出,铸出或钻出孔的进一步加工,镗孔可扩大孔径,提高精度,减小表面粗糙度,还可以较好地纠正原来孔轴线的偏斜。
镗孔可以分为粗镗、半精镗和精镗。
精镗孔的尺寸精度可达IT8~IT7,表面粗糙度Ra值1.6~0.8μm。
镗孔分为一般镗孔和深孔镗孔,一般镗孔在普通车床就可以,把镗刀固定在车床尾座或者固定在小刀架上都可以。
深孔镗孔需要专用的深孔钻镗床,镗刀要加上镗秆,还要加上液压泵站利用冷却液把铁屑排除。
一、常用镗刀
1.通孔镗刀镗通孔用的普通镗刀,为减小径向切削分力,以减小刀杆弯曲变形,一般主偏角为45°~75°,常取60°~70°.
2.不通孔镗刀镗台阶孔和不通孔用的镗刀,其主偏角大于90°,一般取95~100°,刀头处宽度应小于孔的半径。
二、镗刀的安装
1.刀杆伸出刀架处的长度应尽可能短,以增加刚性,避免因刀杆弯曲变形,而使孔产生锥形误差。
2.刀尖应略高于工件旋转中心,以减小振动和扎刀现象,防止镗刀下部碰坏孔壁,影响加工精度。
3.刀杆要装正,不能歪斜,以防止刀杆碰坏已加工表面。
船舶舵系镗孔工艺

船舶舵系镗孔工艺简介船舶舵系镗孔工艺是指在船舶制造中,对船舶舵桨的支撑座进行镗孔加工的工艺。
舵桨是船舶的重要部件,起到控制船舶航向的作用,而舵桨的支撑座则是用于支撑和固定舵桨的装置。
舵桨的安装质量和舵桨支撑座的加工质量,直接影响船舶的操纵性和航行安全性。
因此,船舶舵系镗孔工艺的设计和执行非常重要。
工艺流程船舶舵系镗孔工艺的主要流程如下:1.准备工作:在正式进行舵系镗孔前,需要进行相关的准备工作。
首先,要对舵桨支撑座进行检查,确保没有损坏或缺陷。
其次,要准备好所需的工具和设备,包括镗孔工具、测量工具等。
2.确定镗孔位置:根据船舶设计图纸和相关规范,确定舵桨支撑座的镗孔位置。
这需要考虑船舶的结构特点和使用要求,确保舵桨能够正常运行并承受相应的力。
3.加工设备调试:在进行实际的镗孔加工前,需要对加工设备进行调试,确保设备能够正常运行,并进行必要的校准工作。
4.加工操作:根据确定的镗孔位置,使用镗孔工具进行加工操作。
在进行镗孔时,要注意操作的准确性和稳定性,确保镗孔的精度和质量。
5.清洗和检查:在镗孔完成后,需对舵桨支撑座进行清洗,清除加工过程中产生的切屑和污物。
然后,对镗孔进行检查,确保镗孔的尺寸和表面质量符合要求。
6.装配和固定:在镗孔通过检查后,将舵桨安装到舵桨支撑座上,并进行固定,确保舵桨在船舶运行中不会出现松动或脱落的情况。
7.质量检验:完成装配和固定后,需要对舵桨支撑座进行质量检验。
主要检查舵桨的安装偏差、固定牢固度等指标,确保舵桨能够正常运行。
工艺要求船舶舵系镗孔工艺的执行需要满足以下要求:1.精确性:镗孔的位置、尺寸和形状需要严格按照设计要求进行加工,确保舵桨的安装和使用性能。
2.稳定性:加工操作需要稳定可靠,避免产生振动或误差,影响镗孔质量。
3.安全性:在进行镗孔工艺时,需要采取必要的安全措施,防止意外事故的发生。
4.可追溯性:对每一道工序和加工参数进行记录和追溯,确保加工过程的可控性和可追溯性。
舵系安装原则工艺

舵系安装原则工艺一、概况本船为双桨双舵船舶,舵系中心线位于FR0肋位,左、右舵系分别距舯±3100mm,舵系中心线与轴系中心线空间垂直。
舵叶为悬挂舵,舵叶最大迴转角度±35º,舵机舱内设160kn.m电动拨叉式液压双推舵舵机,上舵承为A200平磨水密式,下舵承为申龙高分子包钢套组合,下舵承与舵颈间浇注环氧,下舵承为开式海水润滑。
舵系安装主要参考图纸:FF5005-230-01 舵系布臵图FF5005-231-01 舵叶FF5005-231-03 舵系零件图FF5005-231-04 舵杆`二、舵叶的制造1) 舵叶铸钢件在与舵叶结构装焊前,应先进行划线后粗加工。
厚度应留约10mm余量(单边)。
粗加工后应划出中心的十字线及铸钢件的中心线,以便舵叶结构安装时定位。
2) 舵叶按照FF5005-231-01 在胎架上装焊,注意铸件与舵叶钢板焊接前应预热至100℃至150℃才能施焊,装焊完毕后进行火工校正,外形尺寸要求可以参考CB/T4000-2005 标准,高度尺寸误差±4mm(极限±6mm),宽度方向±4mm(极限±6mm)。
舵叶完工后进行气密试验,试验压力为:0.02~0.03MPa。
试压时,通知船东、船检到场。
3) 舵叶经检验合格后再对其进行划线确定舵叶的中心线,并对舵叶铸钢件精加工,精加工后其表面粗糙度要达到3.2,平面度要求:当与舵杆法兰结合时,0.05塞尺不能插入15mm。
在舵杆上下端及舵叶的上下端面划出中心线、舵角零位,并做好洋冲标记。
4) 舵叶制作完成后,内腔搪涂环氧沥青漆。
搪涂前,船东要求复检。
三、舵叶法兰螺栓孔的铰(镗)1) 舵叶法兰的螺栓孔,建议在舵叶制造工序完工,并检验合格;法兰平面精加工后,与舵杆法兰组合钻镗。
钻孔前须检查两法兰的接触情况,当两法兰夹紧后,用0.05塞尺不能塞入15mm。
船东要求报验,请协作机械厂到时通知船东。
项目-船舶轴系安装,镗孔
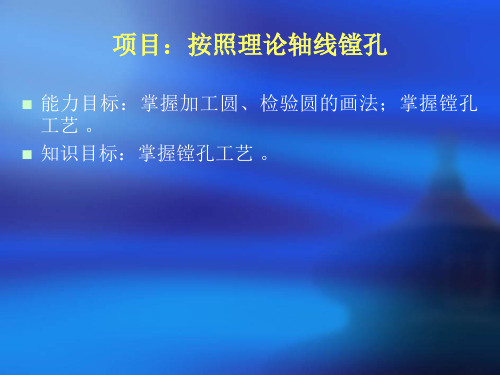
㈡镗孔技术要求
⑴镗削后,孔与检验圆线中心的偏差≯ 0.10mm; ⑵尾柱(或人字架)轴毂孔和尾隔舱孔的同轴度误差≯
0.10mm;舵系各舵承孔同轴度误差≯ 0.20mm; ⑶孔端面与孔轴中心线的垂直度误差≯0.15mm/m;
镗排装置示意图
1-进给箱 ;2-传动机构;3-止推轴承;4- 轴承;5,6-支架; 7-蜗轮、蜗杆;8-刀架;9-镗杆;10-尾隔舱壁;11-电动机; 12-皮带轮
⒉镗排在船上的安装、校中镗杆
镗排在船上的安装,主要工作是校中镗杆。 镗杆的校中就是使镗杆的轴线与轴系理论中 心线相重合。将轴承与镗杆在镗杆轴承架上 安装好后,可以通过调整镗杆轴承的位置, 使镗杆对中。校中镗杆的方法有以下几种:
⑷孔的圆度与圆柱度误差不得超过下表的规定;
表3—1轴系各孔的圆度、圆柱度允差(位:mm)毂孔直径 <80
80~ 120
120~ 180
180~ 260
260~ 360
360~ 500
500~ 700
规定值 0.04 0.05 0.06 0.07 0.08 0.09 0.10
⑸加工后的内孔配合面处以及端面的粗糙度RA值分别不得 超过3.2µm和12.5µm;
⑵用加工圆线和检验圆线校中镗杆
根据轴毂端面的加工圆线和检验圆线,用独脚卡钳或者划针 盘校中调整镗杆的位置,使其找正。
图3—3依据加工圆线和检验圆线使用划针盘或独脚卡钳校中镗杆 1-划针盘;2-镗杆;3-检验圆线
加工圆线和检验圆线的划法
加工圆线和检验圆线同心,加工圆是为了镗孔时确 定其加工线,以便于达到所规定的尺寸要求。检验 圆线比加工圆直径稍大,它是作为镗孔和船帕大修 检验轴系理论中线用。加工圆线和检验圆线的划法 如下:
船舶舵系镗孔工艺探究
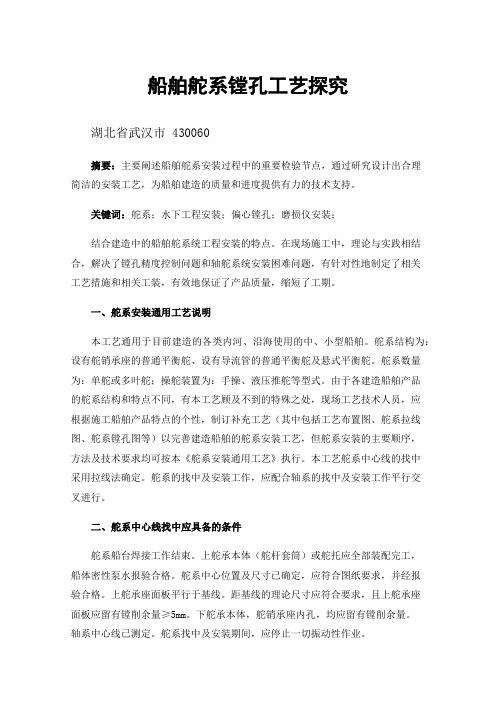
船舶舵系镗孔工艺探究湖北省武汉市 430060摘要:主要阐述船舶舵系安装过程中的重要检验节点,通过研究设计出合理简洁的安装工艺,为船舶建造的质量和进度提供有力的技术支持。
关键词:舵系;水下工程安装;偏心镗孔;磨损仪安装;结合建造中的船舶舵系统工程安装的特点。
在现场施工中,理论与实践相结合,解决了镗孔精度控制问题和轴舵系统安装困难问题,有针对性地制定了相关工艺措施和相关工装,有效地保证了产品质量,缩短了工期。
一、舵系安装通用工艺说明本工艺通用于目前建造的各类内河、沿海使用的中、小型船舶。
舵系结构为:设有舵销承座的普通平衡舵、设有导流管的普通平衡舵及悬式平衡舵。
舵系数量为:单舵或多叶舵;操舵装置为:手操、液压推舵等型式。
由于各建造船舶产品的舵系结构和特点不同,有本工艺顾及不到的特殊之处,现场工艺技术人员,应根据施工船舶产品特点的个性,制订补充工艺(其中包括工艺布置图、舵系拉线图、舵系镗孔图等)以完善建造船舶的舵系安装工艺,但舵系安装的主要顺序,方法及技术要求均可按本《舵系安装通用工艺》执行。
本工艺舵系中心线的找中采用拉线法确定。
舵系的找中及安装工作,应配合轴系的找中及安装工作平行交叉进行。
二、舵系中心线找中应具备的条件舵系船台焊接工作结束。
上舵承本体(舵杆套筒)或舵托应全部装配完工,船体密性泵水报验合格。
舵系中心位置及尺寸已确定,应符合图纸要求,并经报验合格。
上舵承座面板平行于基线。
距基线的理论尺寸应符合要求,且上舵承座面板应留有镗削余量≥5mm。
下舵承本体,舵销承座内孔,均应留有镗削余量。
轴系中心线已测定。
舵系找中及安装期间,应停止一切振动性作业。
三、安装的主要问题1.镗孔精度的控制。
(1)镗杆挠度的消除。
要保证轴系工程的安装精度首先要严格控制轴系镗孔的精度.而镗杆本身又存在挠度。
为了消除镗杆本身的挠度,考虑在镗杆上增加一个中间轴承。
在轴系拉线、照光前先对所使用的镗杆进行挠度测量,根据所用镗杆的长度和轴承的位置,先在车间布置并进行测量,然后将测量的数据进行统计分析,再根据挠度公式计算钢线的挠度,经综合考虑计算后得到镗杆中间轴承部位的实际挠度.船上装镗杆时按该值调整。
船舶舵系镗孔工艺
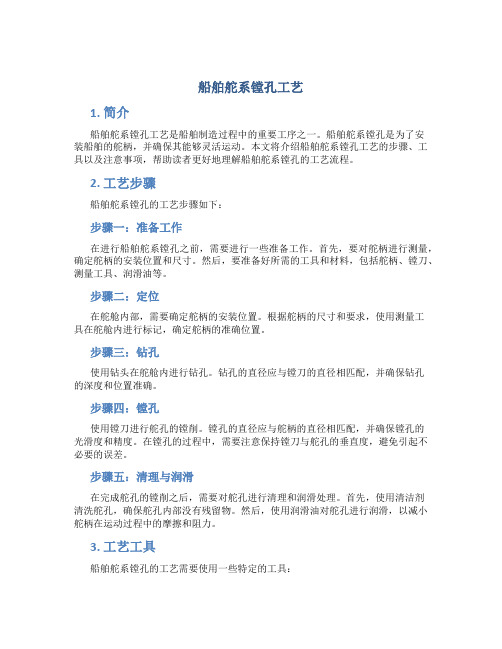
船舶舵系镗孔工艺1. 简介船舶舵系镗孔工艺是船舶制造过程中的重要工序之一。
船舶舵系镗孔是为了安装船舶的舵柄,并确保其能够灵活运动。
本文将介绍船舶舵系镗孔工艺的步骤、工具以及注意事项,帮助读者更好地理解船舶舵系镗孔的工艺流程。
2. 工艺步骤船舶舵系镗孔的工艺步骤如下:步骤一:准备工作在进行船舶舵系镗孔之前,需要进行一些准备工作。
首先,要对舵柄进行测量,确定舵柄的安装位置和尺寸。
然后,要准备好所需的工具和材料,包括舵柄、镗刀、测量工具、润滑油等。
步骤二:定位在舵舱内部,需要确定舵柄的安装位置。
根据舵柄的尺寸和要求,使用测量工具在舵舱内进行标记,确定舵柄的准确位置。
步骤三:钻孔使用钻头在舵舱内进行钻孔。
钻孔的直径应与镗刀的直径相匹配,并确保钻孔的深度和位置准确。
步骤四:镗孔使用镗刀进行舵孔的镗削。
镗孔的直径应与舵柄的直径相匹配,并确保镗孔的光滑度和精度。
在镗孔的过程中,需要注意保持镗刀与舵孔的垂直度,避免引起不必要的误差。
步骤五:清理与润滑在完成舵孔的镗削之后,需要对舵孔进行清理和润滑处理。
首先,使用清洁剂清洗舵孔,确保舵孔内部没有残留物。
然后,使用润滑油对舵孔进行润滑,以减小舵柄在运动过程中的摩擦和阻力。
3. 工艺工具船舶舵系镗孔的工艺需要使用一些特定的工具:•钻头:用于进行舵孔的预钻。
•镗刀:用于进行舵孔的镗削。
•测量工具:用于确定舵柄的安装位置和尺寸。
•清洁剂:用于清洗舵孔。
•润滑油:用于对舵孔进行润滑处理。
使用正确的工具并保持其良好状态对于保证工艺的质量和效率至关重要。
4. 注意事项在进行船舶舵系镗孔工艺时,需要注意以下事项:•安全第一:工艺操作过程中,要保证操作人员的安全。
合理使用个人防护装备,避免发生意外伤害。
•精度要求:船舶舵系工艺对镗孔的直径精度和位置精度要求较高。
在操作过程中要确保工艺达到要求的精度。
•润滑处理:舵孔的润滑处理是保证舵柄灵活运动的重要环节。
在润滑处理过程中,要使用适量的润滑油,并确保润滑油能够充分覆盖整个舵孔表面。
船舶建造中轴系镗孔工艺改进

置 由电机 、开式蜗轮蜗杆传动装置组成 。镗杆安装调正后 ,将蜗 通过分析 ,造成质量问题 的主要原 因有 :
轮套装在镗杆上 。其与镗杆采用丝杆滑动键配合方式 ,便于镗 a.设备结构不合理 ,配合部件磨损快 ,精度低 。原有镗孔设备
杆能在蜗轮孔 内前后移动 ;蜗杆部分制成独立件 ,安装在支架 中,镗杆两端支点使用铸铁衬套 ,衬套与镗杆之 间有一定的间 上 ,根据镗杆调正后 的位置 ,调整蜗杆 与蜗轮配合至转动灵活 隙 ,非 封 闭式结 构 ,需 要 手动 加 人润 滑 油 ,这 种结 构 在 长期 使用
状态 ,固定住蜗杆部件。
之后 ,会 导 致 铁屑 、泥 沙 、水 等 杂 物 进 入 镗杆 与衬 套 之 间 ,加速
其工作原理为镗杆安装前 ,先采用测微准直望远镜照光仪 铸铁衬套的磨损 ,使其间隙进一步增大 ,施工运转时设备振动
器找 出轴系中心线 ,根据轴系中心线在艉轴架及艉轴管前后端 变大 ,导致工件表面粗糙 ,工件尺寸 、圆度 、圆柱度不可控 ,质量
面划 出艉轴承孑L的加工线及检验线 。然后 ,将镗杆安装到艉轴 不稳 定 。
架及艉轴管 内,镗杆两端用铸铁衬套支撑 ,衬套 固定在支架上 , 原有镗孔设备加工舱 内轴承孔时 ,动力输出只能采用蜗轮
支架焊接在各艉轴架及艉轴管本体上。再根据艉轴承孔的加工 蜗杆传动 ,现场定位 ,蜗轮蜗杆开放式布置 ,加工过程 中有铁
关键 词 :镗 孔 设备 ;空 心镗杆 ;自动进 给 装置
近些年工厂承担 的船舶建造任务 ,多为长轴系船舶 ,其艉轴 到规定尺寸 。原轴系镗孔设备结构示意图见图 1。
承孔需在坞内搭载合拢后进行现场镗孔。坞 内施工周期紧,且
新型船舶轴 系镗孔精度要求越来越高 。而工厂原有 的镗孔设
- 1、下载文档前请自行甄别文档内容的完整性,平台不提供额外的编辑、内容补充、找答案等附加服务。
- 2、"仅部分预览"的文档,不可在线预览部分如存在完整性等问题,可反馈申请退款(可完整预览的文档不适用该条件!)。
- 3、如文档侵犯您的权益,请联系客服反馈,我们会尽快为您处理(人工客服工作时间:9:00-18:30)。
船舶舵系镗孔工艺规范
船舶舵系镗孔工艺图片
前言
本规范以CSQS中国造船质量标准(1998)为依据,并参考兄弟船厂之相关工艺文件,结合本公司的实际情况编制而成。
本规范由上海外高桥造船有限公司提出;
本规范由设计部归口;
本规范主要起草(编制):舒继宏。
标检:周德兴。
审核:杜剑锋。
本规范由总工程师南大庆批准。
1 范围
本规范规定了船舶舵系镗孔工艺的工艺准备、人员、工艺要求、工艺过程及检验。
本规范适用于万吨级以上钢质船舶的舵系镗孔。
其他钢质船舶亦可参照使用。
2 规范性引用文件
CSQS 中国造船质量标准(1998)
3 工艺准备
3.1图样及相关工艺技术文件。
3.2镗孔工具
a)a)镗孔专用设备;
b)b)校中用划针盘及弹性接头;
c)c)月牙扳手;
d)d)刀具。
3.3检查镗孔工装设备完好性。
3.4 依照上舵承座和上下舵销座,制作镗孔架。
3.5 确认上舵承座、工艺法兰及上下舵销座上下端面镗孔所需的校圆线,镗削圆线及提高校中精度的工艺基准螺丝钉。
4 人员
4.1 操作人员和检验人员应具备专业知识,并经过相关专业培训、考试或考核取得合格证书,方可上岗操作。
4.2 操作人员和检验人员应熟悉本规范要求,并严格遵守工艺纪律和现场安全操作规程。
5 工艺要求
5.1 镗孔的圆度、圆柱度公差符合CSQS中国造船质量标准(1998),见表1。
表1 镗孔圆度、圆柱度公差值
单位为毫米
5.2
5.3
5.4
5.5 镗削后平面与舵中心线的垂直度误差不大于0.10mm/m。
6 工艺过程
6.1镗杆安装时,应按上舵承座及工艺法兰、上舵销座上端面与下舵销座下端面上的校圆线和工艺基准螺钉为校中依据,用内径千分尺调整镗杆与工艺基准间的距离,使镗杆与舵系中心重合,误差不大于0.02mm。
镗杆与舵系中心重合见图1
6.2 舵系镗排安装
a) 舵系上、下舵钮镗排安装示意图,见图2;
图2 舵系上下舵钮镗排安装示意图b) 舵系上舵承基座镗排安装示意图,见图3。
图3 舵系上舵承基座镗排安装示意图
镗杆调整后应进行无负荷动车,加注润滑油脂,检查支架各连接点螺栓松紧情况。
6.4 粗镗加工
6.4.1 依据施工图样,将各孔直径尺寸、长度尺寸等全部加工到半精镗前状态,各阶梯孔留有1~1.5mm加工余量。
6.4.2 切削深度不大于4mm、进给量0.60mm/r、镗杆转速10r/min,要求粗糙
度不小于。
6.4.3 工作中如发现较大面积砂眼、裂缝等铸件缺陷应及时反馈。
6.5 半精镗加工
6.5.1 提高同轴度精度,各档孔径应留有0.5mm加工余量。
6.5.2 切削深度不大于0.80mm、进给量0.30mm/r、镗杆转速10r/min,要求粗
糙度不小于。
6.5.3工作中应在孔径表面喷注由植物油70%和煤油30%组成的混合冷却油。
6.6 精镗加工
6.6.1应在夜间或阴雨天进行,且应停止船上影响精镗加工的振动性作业。
6.6.2切削深度不大于0.15mm、进给量0.15mm/r、镗杆转速10r/min、要求粗
糙度不小
于。
6.6.3 各档孔径每一次镗出,中途不允许停止镗削。
6.6.4工作中应在孔径表面喷注混合冷却油。
6.6.5内孔镗削合格后才允许切削端部平面,其外形按施工图纸,所镗平面必
须垂直于
中心线,垂直度公差应不大于0.1mm/m。
6.6.6各端面镗削尺寸按图样,并以端面镗削线为准,长度误差之和为±2㎜。
6.7镗杆拆除前,认真检查各加工表面的加工质量,应符合本规范规定的工艺
要求。
6.8镗杆拆除后,消除孔径边缘毛刺,测量各挡孔径尺寸并作记录。
测量记录表格见表2。
表2 测量记录表格
单位为毫米
7 检验
镗孔后检查下列内容:
a)a)镗削加工面的粗糙度;
b)b)舵承各挡加工尺寸及孔径尺寸;
c)c)镗孔圆度和圆柱度;
d)d)镗孔同轴度;
e)e)各镗孔处的圆角或倒角的准确性及镗削平面直径的准确性。