第四章模具工作部分尺寸计算
止动片说明书
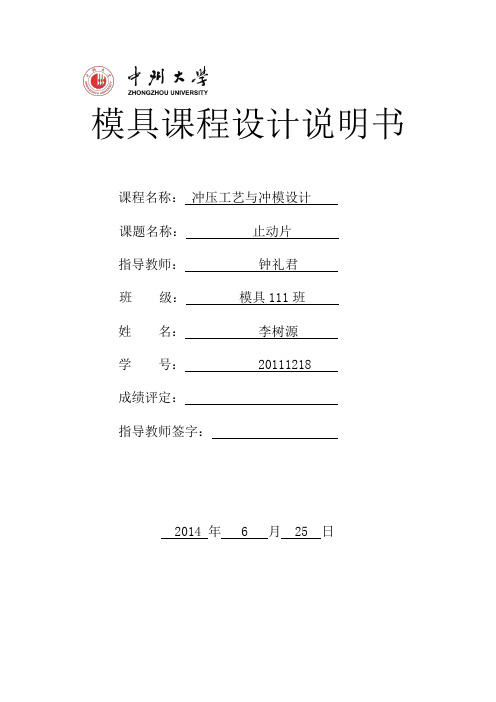
模具课程设计说明书课程名称:冲压工艺与冲模设计课题名称:止动片指导教师:钟礼君班级:模具111班姓名:李树源学号: 20111218成绩评定:指导教师签字:2014 年 6 月 25 日摘要本设计为一止动件的冲压模具设计,根据零件的尺寸、材料、批量生产等要求,首先分析零件的材料、结构工艺和尺寸精度,确定冲裁工艺方案,然后通过工艺设计计算,确定排样和板料规格,计算冲裁力和压力中心,初选压力机,计算凸、凹模刃口尺寸和公差,最后设计选用零、部件,对压力机进行校核,绘制模具总装草图,以及对模具主要零件的加工工艺规程进行编制。
其中在结构设计中,主要对凸模、凹模、凸凹模、定位零件、卸料与出件装置、模架、冲压设备等进行了设计,对于部分零部件选用的是标准件最终才完成这篇课程设计。
关键词:冲压模具凸模凹模凹凸模目录摘要 (1)引言 (3)第一章设计任务1.1零件设计任务 (4)第二章工艺分析和方案选择2.1冲压件工艺分析 (5)2.2分析比较和确定工艺方案 (5)2.2.1加工方案的分析 (5)2.2.2模具结构型式的选择 (6)第三章计算冲裁压力、压力中心和选用压力机3.1排样方式的确定及材料利用率计算 (7). 3.1.1排样方式的确定 (7)3.1.2材料利用率计算 (8)3.2计算冲裁力、卸料力 (9)3.3压力机的选择 (9)3.4 确定模具压力中心 (10)第四章模具工作部分尺寸及公差4.1工作零件刃口尺寸计算 (10)4.2工作零件结构尺寸 (11)4.2.1 凹模外形尺寸确定 (11)4.2.2 凸模的长度 (11)4.2.3凸凹模的长度 (11)4.2.4其他主要零件结构 (12)第五章零件 (13)第六章装配 (23)设计心得 (25)参考文献 (26)引言冲压是利用安装在冲压设备(主要是压力机)上的模具对材料施加压力,使其产生分离或塑性变形,从而获得所需零件(俗称冲压或冲压件)的一种压力加工方法。
拉伸模具工作尺寸计算公式

拉伸模具工作尺寸计算公式在拉伸模具设计中,工作尺寸的计算是非常重要的一部分。
工作尺寸的准确计算可以保证拉伸模具的制作和使用过程中的精准度和稳定性。
本文将介绍拉伸模具工作尺寸计算公式的相关知识和方法。
拉伸模具工作尺寸计算公式是根据拉伸模具的结构和工作原理来确定的。
在进行拉伸模具设计时,首先需要明确拉伸模具的结构和工作原理,然后根据这些信息来确定工作尺寸的计算公式。
下面将介绍一些常见的拉伸模具工作尺寸计算公式。
1. 模具尺寸计算公式。
在进行拉伸模具设计时,首先需要确定模具的尺寸。
模具的尺寸包括模具的长度、宽度和高度。
模具的尺寸计算公式一般为:模具长度 = 产品长度 + 2 冲头直径。
模具宽度 = 产品宽度 + 2 冲头直径。
模具高度 = 产品高度 + 2 冲头直径。
其中,冲头直径是指用于冲压成型的冲头的直径。
通过这些公式可以计算出模具的尺寸,从而确定拉伸模具的工作尺寸。
2. 模具材料计算公式。
拉伸模具的材料是决定模具寿命和稳定性的重要因素。
在进行拉伸模具设计时,需要根据模具的工作原理和使用条件来选择合适的模具材料。
模具材料的计算公式一般为:模具材料量 = 模具长度模具宽度模具高度模具密度。
其中,模具密度是指模具材料的密度。
通过这个公式可以计算出模具所需的材料量,从而确定拉伸模具的材料。
3. 模具强度计算公式。
拉伸模具在工作过程中需要承受较大的拉伸力和压力,因此模具的强度是设计中需要重点考虑的问题。
模具强度的计算公式一般为:模具强度 = 模具材料强度模具材料量。
其中,模具材料强度是指模具材料的抗拉强度或抗压强度。
通过这个公式可以计算出模具的强度,从而确定拉伸模具的稳定性和耐用性。
4. 模具成本计算公式。
在进行拉伸模具设计时,需要考虑模具的成本。
模具的成本包括材料成本、加工成本和人工成本等。
模具成本的计算公式一般为:模具成本 = 模具材料成本 + 模具加工成本 + 模具人工成本。
其中,模具材料成本是指模具材料的采购成本,模具加工成本是指模具的加工和制作成本,模具人工成本是指模具制作过程中的人工费用。
冲压工艺与模具设计第4章 拉深
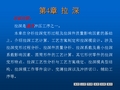
2.筒壁的拉裂
主要取决于:
一方面是筒壁传力区中的拉应力; 另一方面是筒壁传力区的抗拉强度。 当筒壁拉应力超过筒壁材料的抗拉强度时,拉深件就会在 底部圆角与筒壁相切处——“危险断面”产生破裂。
防止拉裂:
一方面要通过改善材料的力学性能,提高筒壁抗拉强度;
另一方面通过正确制定拉深工艺和设计模具,降低筒壁所 受拉应力。
1.等重量法 :已有拉深件样品时,使用等重量法来求毛 坯直径会非常方便。 2.等体积法 :适用于变薄拉深件。
3.等面积法:不变薄拉深工序用来计算毛坯尺寸的依据。
4.3.2 修边余量
修边余量:拉深件口部或凸缘周边不整齐;特别是经过多 次拉深后的制件,口部或凸缘不整齐的现象更为显著;因 此必须增加制件的高度或凸缘的直径,拉深后修齐增加 的部分即为修边余量。
4.凸模圆角部分 5.筒底部分 坯料各区的应力与应变是很不均匀的。
拉深过程中零件应力与应变状态
4.2.3 拉深变形过程中凸缘变形区的应力分布
圆筒件拉深时凸缘
变形区应力分布图
4.2.4 拉深件主要质量问题
拉深过程中的质量问题:Fra bibliotek主要是凸缘变形区的起皱和筒壁传力区的拉裂。
凸缘区起皱: 由于切向压应力引起板料失去稳定而产生弯曲; 传力区拉裂: 由于拉应力超过抗拉强度引起板料断裂。
毛坯尺寸的计算必须将加上了修边余量后的制件尺寸作 为计算的依据。 表4-5为无凸缘圆筒件的修边余量; 表4-6为带凸缘圆筒件的修边余量。
4.3.3 简单旋转体拉深件毛坯尺寸计算
1.将拉深件划分为若干个简单的几何体; 2.分别求出各简单几何体的表面积; 3.把各简单几何体面积相加即为零件总面积; 4.根据表面积相等原则,求出坯料直径。
冲压工艺与模具设计课程教案
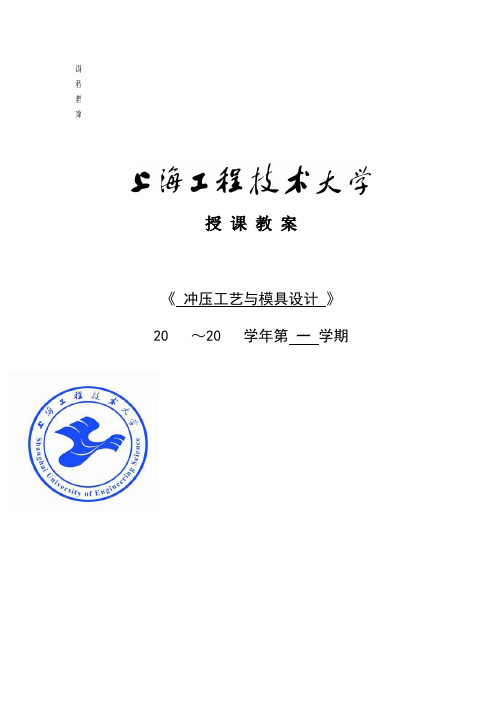
课程教案授课教案《冲压工艺与模具设计》20~20学年第一学期学院(部)材料工程学院系(室)材料工程系课程代码总学时64课程类别必修();核心();公选();选修(√)授课专业材料成型及控制工程授课班级任课教师赵中华职称副教授教案(章节备课)学时:2章节第一章绪论教学目的了解冲压工艺的基本概念,熟悉本专业的历史、现状和发展方向。
了解本课程学习的任务、主要内容以及主要的参考文献资料。
重点难点重点:冲压工艺的特点、冲压工艺的基本工序。
教学内容教学方法教学手段学时分配教学内容:1.介绍冲压工艺的定义、用途及加工范围。
2.介绍冲压工艺的特点。
3.讲解冲压工艺的两大基本工序。
4.讲解冲压工艺的材料种类及选用材料的基本依据。
教学方法:在绪论这一章,讲授时主要采用师生互动的教学方法,通过国民经济的发展现状、发展趋势及平时的日常生活中的典型事例,介绍本课程的一些基本概念。
教学手段:课堂讲授学时分配:2学时章思考题1.冲压工艺有什么的优缺点?2.冲压常用材料有哪几种?3.选用冲压材料的基本依据是什么?主要参考资料1.肖景容主编. 冲压工艺学[M]. 北京:机械工业出版社,19932. 王孝培主编.冲压手册[M]. 北京:机械工业出版社, 19913. S.A.Elenev.PRESSWORKING[M].MOSCOW: MIR PUBLISHERS,1983备注教案(章节备课)学时:18章节第二章冲裁工艺教学目的使学生了解冲裁变形过程;掌握冲裁断面存在四个区域及特点;掌握冲裁间隙是冲压重要工艺参数及刃口尺寸的计算原则;了解计算各种力的方法;掌握减小冲裁力的三种方法,了解掌排样和搭边的定义、排样的类型、搭边的作用,掌握模具压力中心计算的方法;了解提高冲裁件精度方法。
重点难点重点:冲裁断面存在四个区域及特点;冲裁间隙是冲压重要工艺参数;刃口尺寸的计算原则。
难点:冲裁间隙是冲压重要工艺参数;刃口尺寸的计算原则。
教学内容教学方法教学手段学时分配教学内容:1.冲裁变形过程及冲裁断面分析2.冲裁间隙对冲压工艺的影响,冲裁间隙值的确定,冲裁刃口尺寸计算原则及方法3.冲裁力、卸料力、推件力、顶件力的定义及计算方法4.减小冲裁力方法、排样和搭边、冲裁件的工艺性5.模具压力中心计算6.精密冲裁工艺教学方法:结合理论教学,在讲授完每一节内容后安排部分时间进行师生互动,主要是冲裁间隙是冲压重要工艺参数;刃口尺寸的计算原则。
冲压模复习题
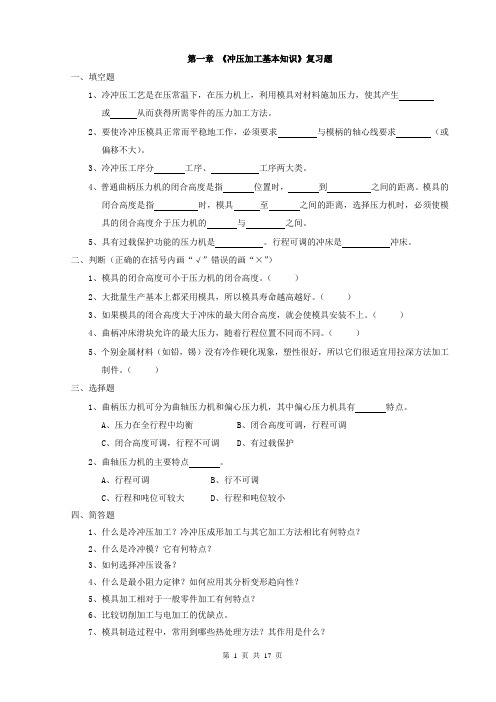
一、填空题1、冷冲压工艺是在压常温下,在压力机上,利用模具对材料施加压力,使其产生或从而获得所需零件的压力加工方法。
2、要使冷冲压模具正常而平稳地工作,必须要求与模柄的轴心线要求(或偏移不大)。
3、冷冲压工序分工序、工序两大类。
4、普通曲柄压力机的闭合高度是指位置时,到之间的距离。
模具的闭合高度是指时,模具至之间的距离,选择压力机时,必须使模具的闭合高度介于压力机的与之间。
5、具有过载保护功能的压力机是。
行程可调的冲床是冲床。
二、判断(正确的在括号内画“√”错误的画“×”)1、模具的闭合高度可小于压力机的闭合高度。
()2、大批量生产基本上都采用模具,所以模具寿命越高越好。
()3、如果模具的闭合高度大于冲床的最大闭合高度,就会使模具安装不上。
()4、曲柄冲床滑块允许的最大压力,随着行程位置不同而不同。
()5、个别金属材料(如铅,锡)没有冷作硬化现象,塑性很好,所以它们很适宜用拉深方法加工制件。
()三、选择题1、曲柄压力机可分为曲轴压力机和偏心压力机,其中偏心压力机具有特点。
A、压力在全行程中均衡B、闭合高度可调,行程可调C、闭合高度可调,行程不可调D、有过载保护2、曲轴压力机的主要特点。
A、行程可调B、行不可调C、行程和吨位可较大D、行程和吨位较小四、简答题1、什么是冷冲压加工?冷冲压成形加工与其它加工方法相比有何特点?2、什么是冷冲模?它有何特点?3、如何选择冲压设备?4、什么是最小阻力定律?如何应用其分析变形趋向性?5、模具加工相对于一般零件加工有何特点?6、比较切削加工与电加工的优缺点。
7、模具制造过程中,常用到哪些热处理方法?其作用是什么?一、填空题1、普通冲裁件断面具有、、和四个明显区域。
2、落料凹模在下半模称为复合模,结构上有套打料除件装置。
3、落料凹模在上模的叫复合模,而落料凹模在下模的叫复合模,其中复合模多一套打料装置。
4、要使冷冲压模具正常而平稳地工作,必须使与模柄的轴心线(或偏移不大)。
课程设计带凸缘筒形件首次拉深的拉深模设计
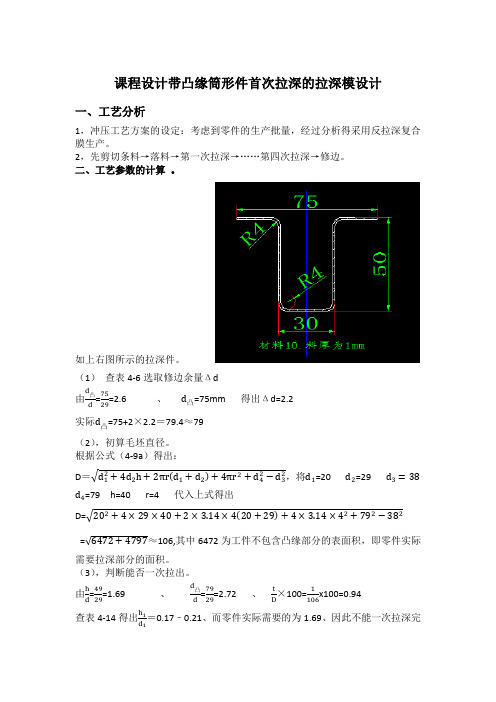
课程设计带凸缘筒形件首次拉深的拉深模设计一、工艺分析1,冲压工艺方案的设定:考虑到零件的生产批量,经过分析得采用反拉深复合膜生产。
2,先剪切条料→落料→第一次拉深→……第四次拉深→修边。
二、工艺参数的计算 。
如上右图所示的拉深件。
(1) 查表4-6选取修边余量Δd 由d 凸d=7529=2.6 、 d 凸=75mm 得出Δd=2.2实际d 凸=75+2×2.2=79.4≈79 (2),初算毛坯直径。
根据公式(4-9a )得出:D =√d 12+4d 2h +2πr (d 1+d 2)+4πr 2+d 42−d 32,将d 1=20 d 2=29 d 3=38d 4=79 h=40 r=4 代入上式得出D=√202+4×29×40+2×3.14×4(20+29)+4×3.14×42+792−382 =√6472+4797≈106,其中6472为工件不包含凸缘部分的表面积,即零件实际需要拉深部分的面积。
(3),判断能否一次拉出。
由h d =4929=1.69 、d 凸d=7929=2.72 、 t D ×100=1106x100=0.94查表4-14得出h1d 1=0.17﹣0.21、而零件实际需要的为1.69、因此不能一次拉深完成。
(4),计算拉深次数及各工序的拉深直径。
,因此需要用试凑法计算利用表4-14来进行计算,但由于有两个未知数m和d td1拉深直径。
下面用逼近法来确定第一的拉深直径。
的值为由于实际拉深系数应该比极限拉伸系数稍大,才符合要求,所以上表中d td11.5、1.6、1.7的不合适。
因为当d t的值取1.4的时候,实际拉深系数与极限拉深系数接近。
故初定第一次d1拉深直径d1=56.因以后各次拉深,按表4-8选取。
故查表4-8选取以后各次的拉深系数为当m2=0.77时d2=d1×m2=56×0.77=43mm当m2=0.79时d3=d2×m3=43×0.79=34mm当m3=0.81时d4=d3×m4=34×0.81=27mm<29mm因此以上各次拉程度分配不合理,需要进行如下调整。
第4章 拉深

学习目的与要求
1.了解拉深变形规律及拉深件质量影响因素; 2.掌握拉深工艺计算方法; 3.掌握拉深工艺性分析与工艺设计方法; 4.认识拉深模典型结构及特点,掌握拉深模工 作零件设计方法; 5.掌握拉深工艺与拉深模设计的方法和步骤。
概述
拉深又称拉延,是利用拉深模在压 力机的压力作用下,将平板坯料或空心 工序件制成开口空心零件的加工方法。 它是冲压基本工序之一。可以加工旋转 体零件,还可加工盒形零件及其它形状 复杂的薄壁零件。
和ζ
3max
的变化规律
3)筒壁部分受力分析
筒形件的拉深系数与拉深次数
在拉深工艺设计时,必须判断制件是否能一次拉 深成形,或需要几道工序才能拉成。正确解决这个问 题直接关系到拉深生产的经济性和拉深件的质量。
1.拉深系数
每次拉深后的筒形件直径与拉深前坯料(或工序 件/半成品)的直径之比。
m1 d1 D m2 d 2 d1 .......... ... mn 1 d n 1 d n 2
拉深变形过程
拉深过程中金属的流动(网格分析)
凸缘产生内应力:径向拉应力σ1;切向压应力σ3 凸缘塑性变形:径向伸长,切向压缩,形成筒壁 直径为d高度为H的圆筒形件(H>(D-d)/2)
通过拉深网格分析我们发现,工件底部的 网格变化很小,而侧壁上的网格变化则很大, 以前的等距同心圆,变成了与工件底部平行的 不等距的水平线,并且愈是靠近工件口部,水 平线之间的距离愈大,同时以前夹角相等的半 径线在拉深后在侧壁上变成了间距相等的平行 垂线,以前的扇形毛坯网格变成了拉深后的矩 形网格。
(1)不用压边圈时
Z=(1.0~1.1)tmax (2)用压边圈时 2次拉深: 第1次 第2次 3次拉深: 第1次 第2次 第3次 1.1t (1.0~1.05)t 1.2t 1.1t (1.0~1.05)t
弯曲模工作部分的设计计算

3 活动式弯曲模
几个简单的弯曲工序复合在一套模具中。
利用凹模(或凸模)的摆动、转动或滑动,实现 毛坯的弯曲加工。
4 级进弯曲模
将冲裁、弯曲、切断等工序布置在同一模具上, 实现级进工艺成形。
Bd=Bp+2C
式中 B—弯曲件基本尺寸 △—弯曲件制造公差; δp 、δd——凸、凹模制造公差
二、弯曲模的典型结构
1 敞开式弯曲模
结构简单,制造方便,通用性强; 但毛坯弯曲时容易窜动,不易保证零件精度。
2 有压料装置的弯曲模
工作时凸模和下顶板压紧毛坯,防止其产生移 动。
毛坯上加工孔,辅之定位销,效果更好。
弯曲模工作部分的设计计算
一、弯曲模作部分的尺寸计算
弯曲模工作部分的尺寸: 指凸模、凹模的圆角半径和凹模的深度; U形件的弯曲模还有凸、凹模之间的间隙及模 具宽度尺寸等。
1 凸凹模的圆角半径
凸模的圆角半径rp等于弯曲件内侧的圆角半径r, 但不能小于材料允许的最小弯曲半径rmin。
如果r<rmin,弯曲时应取rp≥rmin。随后增加一 道校正工序,校正模的rp=r;
否则,凹模深度可小于零件高度。
3 凸、凹模间隙
弯曲V形件时,凸、凹模之间的间隙靠调整压 力机的闭合高度来控制。
U形件弯曲,必须合理选择凸、凹模间隙。 间隙过大,则回弹大不易保证工件精度。
间隙过小,会使零件边部壁厚减薄,降低模具 寿命,且弯曲力大。
4 模具宽度尺寸
弯曲件宽度尺寸标注在工件外侧时,以凹模为基 准,先确定凹模尺寸。考虑到模具磨损和弯曲件 的回弹,凹模宽度尺寸为:
当弯曲件内侧的圆角半径较大时(r/t>10),必 须考虑回弹,修正凸模圆角半径。
凹模的圆角半径rd根据板材的厚度t选取: t≥2mm, rd=(3~6)t
- 1、下载文档前请自行甄别文档内容的完整性,平台不提供额外的编辑、内容补充、找答案等附加服务。
- 2、"仅部分预览"的文档,不可在线预览部分如存在完整性等问题,可反馈申请退款(可完整预览的文档不适用该条件!)。
- 3、如文档侵犯您的权益,请联系客服反馈,我们会尽快为您处理(人工客服工作时间:9:00-18:30)。
第4章模具工作部分尺寸的计算
4.1凸、凹模圆角半径的确定
凸、凹模的圆角半径对拉伸制件影响很大。
毛坯经凹模圆角进入凹模时,受到弯曲和摩擦作用。
凹模半径r d过小,因径向拉力较大,易使拉伸件表面划伤或产生断裂;r d过大,由于悬空面积增大,使压边面积减小,易起内皱。
因此,合理选择凹模圆角半径是极为重要的。
一般情况下,只要拉伸变形区不起皱,凹模圆角半径应尽量取大值,这不但有利于减少拉伸力,而且还可以延长凹模寿命。
查【1】p194得表4-1:
表4-1首次拉伸凹模的圆角半径r d1
该件为有凸缘拉伸件r d=10t
式中t—坯料的厚度,㎜
所以,r d=10×0.6=6㎜
凸模圆角半径r p的大小,对拉伸也有影响。
若r p过小,r p处弯曲变形程度大,危险断面所受拉力大,制件易产生局部变薄,降低变形程度;若过大,凸模与毛坯接触面小,易产生底部变薄和内皱。
查【1】p194式7-40得:
r p1 = (0.7~1.0 )r d1
r p=r d=6㎜
最后一次拉伸凸模圆角半径应等于制件的圆角半径,但不得小于(2~3)t。
如果制件的圆角半径要求小于(2~3)t时,则凸模圆角半径仍取(2~3)t,最后用一次整形工序来得到制件要求的圆角半径。
在实际生产中,应根据现场试模情况对上面所列数值作必要的修正。
一般在实际设计中先选取较小的数值,而在试模调整时再逐渐增大,直到冲到合格制件时为止。
4.2凸、凹模间隙的确定
拉伸模间隙是指单边间隙,即凹模和凸模直径之差的一半。
拉伸时凸、凹模之间的间隙对拉伸力、制件质量、模具寿命等都有影响。
拉伸模凸、凹间隙过小,使拉伸力增大,从而使板料内应力增大;同时摩擦加剧,导致制件变薄严重,甚至拉裂。
间隙过大,对板料的校直作用小,拉伸成的制件侧壁不直,并且在壁部容易起皱,或者制件有锥度,精度差。
因此,正确地确定凸模和凹模之间的间隙非常重要。
拉伸模在确定其凸、凹模间隙的方向时,主要应正确选定最后一次拉伸的间隙方向,在中间拉伸工序中,间隙的方向是任意的。
而最后一次拉伸的间隙方向应按下列原则确定:
当拉伸件要求外形尺寸正确时,间隙应由缩小凸模尺寸取得;当拉伸件要求内形尺寸正确时,间隙应由缩小凹模尺寸取得。
查【1】p194得表4-2:
表4-2带压边圈拉伸时的单边间隙值
因该件属于一次拉伸件,故取单边间隙Z=t=0.6㎜。
4.3凸、凹模工作部分的尺寸与公差
凸、凹模工作部分尺寸的确定,主要考虑模具的磨损和拉伸件的回弹。
工件的尺寸公差在最后一道工序考虑,最后一道工序的凸、凹模尺寸由拉伸件的尺寸标注方法决定。
如图 3—1(a)所示,制件尺寸标注在外形时,要求以凹模尺寸为基准,通过减小凸模尺寸保证间隙,其相应凸、凹模尺寸的计算公式为
max 0(0.75)d d D D
max (0.752)p P D D Z
如图3—1 (b)所示,制件尺寸标注在内形时,要求以凸模尺寸为基准,通过加大凹模内形尺寸保证间隙,其相应凸、凹模尺寸的计算公式为
0min (0.4)p P
d d min 0(0.42)d d d d Z
图 4—1工件尺寸与模具尺寸
式中:D d 、d d ——凹模的基本尺寸,mm ;
D p 、d p ——凸模的基本尺寸,mm ;
D max ——拉伸件外径的最大极限尺寸,mm ;
d min ——拉伸件内径的最小极限尺寸,mm ;
Δ——工件公差;
δd 、 δp ——凹模和凸模制造公差,见表4—3;
Ζ——拉伸模单边间隙,mm 。
表4—3 凸模与凹模的制造公差
由零件图知道,要保证外形尺寸:查表4—3 δd =0.08 mm 、δp =0.05mm ,Δ=0.02㎜ D max =550.7㎜、Z=0.6㎜
凹模尺寸max 0(0.75)d d
D D =0.080.0800(550.70.750.02)550.685㎜ 凸模尺寸0max (0.752)p
P
D D Z =0.050.0500(550.70.750.0220.6)549.485㎜ 4.4拉深凸模的通气孔
通常,在拉深凸模上要求加工通气孔。
其目的是保证拉深件能顺利地从凸模上脱出。
否则会在拉深件与拉深凸模之间形成真空而难以脱模,或使拉深件底部出现不平整。
常见的凸模气孔开设如图3—2所示
图3—2凸模通气孔
表4—3 通气孔的设计尺寸查【1】p190得表4—3,取凸模直径12㎜。