注塑模具设计图纸检查项目表
注塑模具十大标准评分表
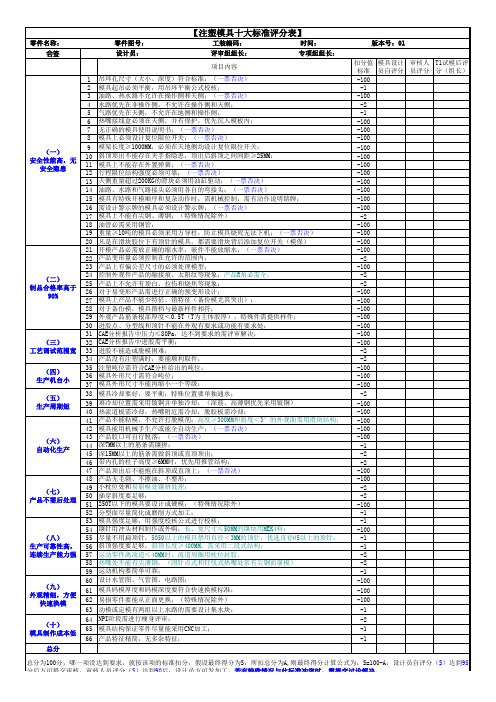
(一) 安全性能高,无 安全隐患
(二) 制品合格率高于 90%
(三) 工艺调试范围宽 (四) 生产机台小 (五) 生产周期短
(六) 自动化生产
(七) 产品不需后处理
(八) 生产可靠性高, 连续生产能力强
(九) 外观精细,方便 快速换模 (十) 模具制作成本低 总分
总分为100分,哪一项没达到要求,就按该项的标准扣分,假设最终得分为S,所扣总分为A,则最终得分计算公式为:S=100-A;设计员自评分(S)达到 95分后方可提交审核,审核人员评分(S)达到90后,设计员方可发加工。若有特殊情况与此标准冲突时,需提交讨论解决。
设计员自评分s达到95分后方可提交审核审核人员评分s达到90后设计员方可发加工若有特殊情况与此标准冲突时需提交讨论解决四生产机台小九外观精细方便快速换模十模具制作成本低三工艺调试范围宽二制品合格率高于90分后方可提交审核审核人员评分s达到90后设计员方可发加工
【注塑模具十大标准评分表】
零件名称: 会签 零件图号: 设计员: 工装编码: 评审组组长: 项目内容 1 2 3 4 5 6 7 8 9 10 11 12 13 14 15 16 17 18 19 20 21 22 23 24 25 26 27 28 29 30 31 32 33 34 35 36 37 38 39 40 41 42 43 44 45 46 47 48 49 50 51 52 53 54 55 56 57 58 59 60 61 62 63 64 65 66 吊环孔尺寸(大小、深度)符合标准;(一票否决) 模具起吊必须平衡,用吊环平衡公式校核; 油路、热水路不允许在操作侧和天侧;(一票否决) 水路优先在非操作侧,不允许在操作侧和天侧; 气路优先在天侧,不允许在地侧和操作侧; 热嘴接线盒必须在天侧,并有保护,优先沉入模板内
注塑模具设计制作规范与验收标准表

模具名称:模穴数:型腔表面处理:产品材料:otting per attached sketch/按下图所示的配合关系检查sembly lifter/装斜顶时的检查项目查项目品合格率:85%以上,附品管检查报告。
预验收须满足模具验收标准表合格项85%以上。
2.终管检查报告。
终验收须满足模具验收标准表合格项95%以上。
签名:年月日浇口及模胚制作参考标准常见浇口尺寸基本设计原则推荐如下:1. 点浇口:2. 扇形浇口:3. 潜伏式浇口:L= W=w=宽度 [mm]A= 型腔表面积 [ mm 2 ] n= 材料常数 for PE, PS30An L = ~ mmd = 浇口直径( mm )t = 零件壁厚( mm )A = 型腔表面积 ( mm 2 )dL t4At 0.206n d ⨯=4. 边缘浇口:5. 凸耳浇口:L = ~ mmh = n tWt L h30AnW=W=w= 浇口宽度 [mm]A= 型腔表面积 [ mm2 ]n= 材料常数for PE, PS30An30? ~15o ~W = 浇口宽度 ( mm )A = 型腔表面积 ( mm2 )n = 材料常数 material constantfor PE, PS6. 重叠式浇口:模架尺寸选择参考标准一、 注塑类模具镶块式模具的模架与镶件大小的选择,可参考下面的数据: 图4-146 模架尺寸的确定“A ”—表示镶件侧边到模板侧边的距离; “B ”—表示定模镶件底部到定模板底面的距离; “C ”—表示动模镶件底部到动模板底面的距离; “D ”—表示产品到镶件侧边的距离;30An L= ~ W=w= 浇口宽度 [mm] A= 型腔表面积 [ mm 2 ] n= 材料常数30An W= w= 浇口宽度 [mm] A= 型腔表面积[ mm 2 ] n= 材料常数for PE, PS“E”—表示产品最高点到镶件底部的距离;“H”—表示动模支承板的厚度(当模架为A型时)“X”—表示产品高度。
注塑模具设计评审表
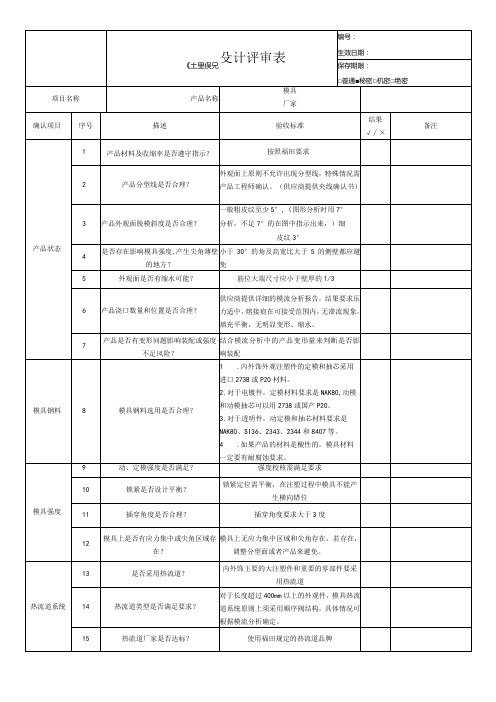
评审结论,
模具供应商,
零部件供应商,
采购本部,模具工程师、SQE
记录部门:
记录人:模具工程拜
记录日期:
一般粗皮纹至少5°,(图形分析时用7°
分析,不足7°的在图中指示出来,)细
皮纹3°
4
是否存在影响模具强度,产生尖角薄壁的地方?
小于30°的角及高宽比大于5的侧壁都应避免
5
外观面是否有缩水可能?
筋位大端尺寸应小于壁厚的1/3
6
产品浇口数量和位置是否合理?
供应商提供详细的模流分析报告,结果要求压力适中,熔接痕在可接受范围内,无滞流现象,填充平衡,无明显变形、缩水。
21
油缸顶出的模具是否设计行程开关?
油缸顶出的模具箱设计复位行程开关,防止撞模。
22
油路设计是否平衡?
油路设计要求平衡,使油同时到达每个油缸,保障顶出平衡。
模具工艺
23
模具加工工艺是否合理?
要求模具加工工艺简洁,效率高,非胶位部分减少电火花加工的部位,尽量全部采用NC加工
24
模具精度和表面质量要求是否达标?
17
较大滑块、斜顶、镶块、顶块是否设计水路?
较大的滑块、镶块和顶块需要设计水路:水路直径要大于6mm。
18
热流道喷嘴周围是否设计单独的冷却水路?
热流道喷嘴周围要设计单独的冷却水路。
顶出系统
19
模具顶出是否合理?
筋位、侧壁附近均应有顶出,要求布置均匀,顶出平衡
20
大型模具是否采用油缸顶出?
大型模具采用油缸顶出
热流道系统
13
塑胶模具设计检验清单
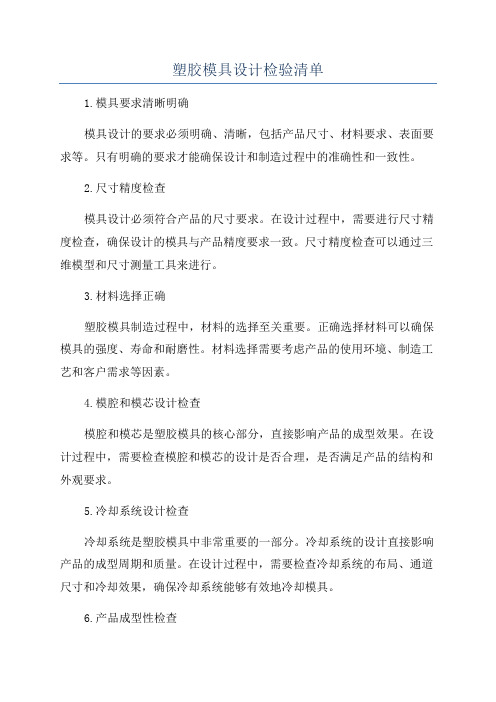
塑胶模具设计检验清单1.模具要求清晰明确模具设计的要求必须明确、清晰,包括产品尺寸、材料要求、表面要求等。
只有明确的要求才能确保设计和制造过程中的准确性和一致性。
2.尺寸精度检查模具设计必须符合产品的尺寸要求。
在设计过程中,需要进行尺寸精度检查,确保设计的模具与产品精度要求一致。
尺寸精度检查可以通过三维模型和尺寸测量工具来进行。
3.材料选择正确塑胶模具制造过程中,材料的选择至关重要。
正确选择材料可以确保模具的强度、寿命和耐磨性。
材料选择需要考虑产品的使用环境、制造工艺和客户需求等因素。
4.模腔和模芯设计检查模腔和模芯是塑胶模具的核心部分,直接影响产品的成型效果。
在设计过程中,需要检查模腔和模芯的设计是否合理,是否满足产品的结构和外观要求。
5.冷却系统设计检查冷却系统是塑胶模具中非常重要的一部分。
冷却系统的设计直接影响产品的成型周期和质量。
在设计过程中,需要检查冷却系统的布局、通道尺寸和冷却效果,确保冷却系统能够有效地冷却模具。
6.产品成型性检查在模具设计过程中,需要对产品的成型性进行检查。
成型性的检查包括产品的结构设计、脱模方向以及壁厚等方面。
通过成型性检查,可以确保产品能够顺利成型,并且产品质量符合要求。
7.模具寿命评估模具的寿命是塑胶模具设计的重要考虑因素。
在设计过程中,需要评估模具的寿命,确定模具材料和结构的合理性。
模具寿命评估可以通过模具使用经验和模拟软件进行。
8.模具维护方案制定模具在使用过程中需要进行维护和保养,以确保其良好的工作状态和延长寿命。
在设计过程中,需要制定模具的维护方案,包括清洁、润滑和定期检查等内容。
9.模具制造工艺评估模具的制造工艺评估是塑胶模具设计的重要环节之一、通过工艺评估,可以确定模具的制造难度、工艺流程和制造时间等。
工艺评估需要考虑模具的结构和材料等因素。
10.工装夹具设计检查在塑胶模具设计过程中,还需要对工装夹具进行设计检查。
工装夹具的设计应与模具设计相匹配,以保证工装夹具能够正确、稳定地夹持模具,确保成型质量和安全性。
注塑模具设计制作规范方案和验收标准表

模具名称:模穴数:型腔表面处理:产品材料:签名:年月日浇口及模胚制作参考标准常见浇口尺寸基本设计原则推荐如下:1. 点浇口:2. 扇形浇口:3. 潜伏式浇口:4. 边缘浇口:5. 凸耳浇口:W = 浇口宽度( mm )A = 型腔表面积( mm2 )n = 材料常数material constant 0.6 for PE, PS0.7 for POM, PC, PP0.8 for CA, PMMA, PA0.9 for PVCh = 浇口厚度t = 零件壁厚6. 重叠式浇口:W=w= 浇口宽度 [mm]A= 型腔表面积[ mm2 ]n= 材料常数0.6 for PE, PS0.7 for POM, PC, PP0.8 for CA, PMMA, PA0.9 for PVC浇口厚度= nt浇口长度L1 = 0.5~0.75 L2 = h+( w/2 )t= 零件壁厚模架尺寸选择参考标准一、注塑类模具镶块式模具的模架与镶件大小的选择,可参考下面的数据:图4-146 模架尺寸的确定“A”—表示镶件侧边到模板侧边的距离;“B”—表示定模镶件底部到定模板底面的距离;“C”—表示动模镶件底部到动模板底面的距离;“D”—表示产品到镶件侧边的距离;“E”—表示产品最高点到镶件底部的距离;“H”—表示动模支承板的厚度(当模架为A型时)“X”—表示产品高度。
以上数据,仅作为一般性结构塑件摸架参考,对于特珠的塑件应注意以下几点:①当产品高度过高时(产品高度X≥D),应适当加大“D”,加大值ΔD=(X-D)/2;②有时为了冷却水道的需要对镶件的尺寸做以调整,以达到较好冷却效果;③结构复杂需做特殊分型或顶出机构,或有侧向分型结构需做滑块时,应根据不同情况适当调整镶件和模架的大小以及各摸板厚度,以保证模架的强度。
④垫块高度的确定:垫块的高度应保证足够的顶出行程,然后留出一定的余量(5-10mm),以保证完全顶出时,⑤模架整体结构的确定:在基本选定模架之后,应对模架整体结构进行校核,看所确定的模架是否合适所选定或客户给定的注塑机,包括模架外形的大小、厚度、最大开模行程、顶出方式和顶出行程等,最后模架的整体尺寸以5mm为单位(例如计算所得模架尺寸为:232mm*253mm*186mm,那么实际应该取:235mm*255mm*190mm)。
模具拆解检表

承压片
耐磨片
弹簧
氮气弹簧
弹簧力度 斜顶杆、直顶与滑座固定螺 丝;耐磨片螺丝; 滑块压条、限位螺丝; 以及其他受力部位螺丝;
检查是否漏气失效
螺丝
是否有松动、松脱现象
油缸 行程/复 位开关
抽芯、滑动部件是否有拉伤; 油缸油压检查 检查是否按要求连接、损坏
拆解后检查滑块摩擦面状态
拆解后检查限位块固定螺钉变 放在水平玻璃板上滚动,有变形及时更换 形 拆解后检查斜导杆变形 放在水平玻璃板上滚动,有变形商讨对策
拆解后检查所有导槽和导杆磨 表面受损严重要拍照留档,商讨对策 损
注塑模具拆解检查表(三)
日期:
项目名称 内容 滑 块 机 构 顶针 复位杆 导杆导套 序号 模具名称 检查内容 要 求 拆解后检查滑块有弹簧(特大 用手直接推动(戴好防护手套),有松动 滑块除外)和无弹簧状态的运 要拍照留档,做后续重点检查,有弹簧状 动顺畅情况; 态手推不动,要检查限位块固定螺钉尺寸 是否匹配 拆解后检查所有顶针变形 拆解后检查所有复位杆变形 放在水平玻璃板上滚动,有变形商讨对策 放在水平玻璃板上滚动,有变形商讨对策 模具编号 检查记录 备注
1
模 具 外 观
2 3
1
型芯 热流道
型芯整体放在水平平整地面,顶针板用行 拆解前检查所有直顶块能否完 车吊起35mm以上,放入30mm左右圆 全嵌入直顶块穴 棒,用人工拔出圆棒,顶针板自由落体复 位 拆解前检查直顶块与导杆之间 用手直接检查(戴好防护手套),有松动 是否松动或可旋转,导杆与顶 或可旋转要拍照留档,商讨对策 针板之间是否松动 拆解后检查直顶块摩擦面状态 表面受损严重要拍照留档,商讨对策
2 3
直 顶 机 构
4
拆解后检查直顶块导杆是否变 放在水平玻璃板上滚动,检查导杆是否弯 形 曲 拆解后检查所有直顶块能否完 型芯整体侧转90°,连上导杆的直顶块手 全嵌入直顶块穴 推入直顶块穴 拆解后检查所有直顶块与直顶 碰红丹检查底部避让面以外要求全接触, 块穴有效接触面情况 口部全周有5mm宽接触面 直顶与直顶座配合处检查; 检查直顶座根部是否有裂纹; 直顶座上是否有凹痕(直顶长度);
最新模具设计检查表说明
XXX模具设计检查表说明2018年8月1 模具结构1.1 浇口套浇口直径与注塑机喷嘴直径是否匹配,通常为ø3.51.2 按WORKSHEET要求的机台吨位检查模具外形尺寸是否超差。
1.3 需要的开模距离注塑机是否可以满足。
1.4 定位圈的直径按WORKSHEET大小设计。
1.5 码模槽大小根据机台吨位设计。
1.6 检查水路接头是否和注塑机部件干涉。
1.7 面板和底板都要设计隔热板,厚度按HASCO规范。
通常做8.5mm。
1.8 所有模板覆盖隔热板。
按WORKSHEET要求。
1.9 隔热板固定螺丝用HASCO Z32/6X10 。
1.10 浇口套与定位圈是否密封,防止注塑机喷嘴溢料时漏到模具内。
1.11 检查浇口套SR40 和ø 36。
1.12 浇口套SR处距离面板最大为35mm。
1.13 每块板之间加撬模槽,30*25 深度5mm。
1.14 锁模扣大小按要求设计。
1.15 吊环要有定位杆,吊环大小按要求。
30-50-80-110Tn Z721/12/18X0.7 M12 1400KG150Tn Z721/16/20X1.4 M16 2800KG吊环定位杆HASCO Z021.16 母模侧,公模侧,整套模具,三个重心位置。
其它模板吊环孔。
1.17 模具站脚。
通常地侧滑块有水路时需要。
出口模具需要。
1.18 导柱、导套安装方式是否正确,中心销是否正确。
1.19 主要导柱需比滑块斜导柱进入滑块前先插入导套。
1.20 基准角导柱直径小一号。
HASCO标准。
1.21 支撑柱。
1.22 锁模脚螺丝。
1.24 模仁用V型锁块。
1.25 精定位是否正确。
1.26 面板上安装某某公司。
XXX标准。
1.27 面板天侧加工某某公司放置槽。
1.28 油缸、气缸放在模具天侧。
1.29 开模顺序的检查。
特别是由母模抽芯、公模抽芯、滑块套滑块等机构的动作顺序。
1.30 顶针板强制拉回机构低于底板1mm。
1.31 母模有顶针板时复位杆不能与公模顶针板复位杆重叠。
模具评审记录
E. 油缸动模抽芯2顶出
模 G. 油缸顶板2级顶复位
作 M. 合模 分 析 O .油缸定模抽芯1复位
Q. 油缸动模抽芯1复位
F. 油缸顶板1级顶出 H. 设备顶针顶出 J. 设备顶针退回 L. 油缸顶板1级复位 N. 油缸定模抽芯2复位 P. 油缸动模抽芯2复位 R. 塑料注射
33 是否有顶杆布置在不平整产品面,顶杆是否设计止转,头部斜面是否防滑
34 是否有粘上模可能、顶出行程是否足够、是否需先复位、是否需二次顶出
35
是否设计微动开关、开关座和计数器,开关座是否设置在非操作侧模脚中间位置(注意注塑机 压板位置)
36 是否适合机械手取件,嵌件模导柱是否在非嵌件侧
37 用拉攀做先复位是否与注塑机模板相符,最多横向中心用上下两个拉攀
43 整个零件的支撑柱是否均匀分布,特别是注射中心区域,尽量不要与顶出孔干涉
44 上下模仁厚度是否足够,上下模板厚度是否足够,滑块锁紧块强度是否足够
45 模仁定位是否需要用锲紧块定位或两直边和两斜边,模仁及镶件厚度尾数是否为3或8
46 所有镶件和斜顶沿周是否做圆角以增加模具强度
冷却
47 水路可持续流动,水路是否均匀分布;一般不在塑件熔接的地方设置水路﹐避免影响制品强度
28
斜顶配合斜面的角度是否大于斜顶运动角度(即斜顶杆角度)2-3度,保证运动复位时不会有 碰伤
29 与斜顶座的配合是否有足够强度、耐用
30 顶针规格是否合适(尽量用大顶针和较少规格),是否兼作排气作用
31 检查模具设计的顶出,确保不会有干涉。3D模具数模的运动分析是必须的
32 是否均匀顶出(会引起脱模困难、及外观问题),官位长度为顶针直径3到5倍
电镀类零件
58 零件应尽量在非外观面上多设置几个装挂位置,以保证零件镀层的均匀
模具设计评审检查表
零件号数模版本号零件类别材料信息材料牌号公司模具材料牌号类似零件收缩率验证结果OKNOKN/A成型部件斜顶(或顶杆)运动到底,要保证3mm 间隙要保证运动结束时与产品有3mm 间隙运动干涉分析斜顶热处理不应放在容易与对手件干涉或产生异响的区域分型线不可分在零件R 角处或是否获得SGM QD/Design/外观工程师/SQE 批准模具结构不可有“薄铁”、“尖角”斜顶行程斜顶杆直径斜顶座是否是顺序阀分型线抛光斜顶杆衬套斜顶杆需要做淬火处理斜顶杆最大角度模具强度型芯或型腔面皮纹面浇口位置动模采用镶件的方式,抛光时,将镶件安装到定模,镶件与定模的产品面一起抛光(外观面)开模方向都至少有3°脱模斜度门板以上大模具〉=20mm流道的流长电镀级ABS+PC≤200mm电镀级ABS≤250mm分型线处模具配合阶差在SGM的认可清单中选取材料供应商收缩率范围分型线不可在A 面或外分是否获得SGM QD/Design/外观工程师/SQE 批准外分 内分一膜一腔 一膜多腔外饰件 内饰件 电镀件 皮纹件 油漆件 高光件 匹配件模具等级IP 、DP <=15° ,其余<=12°流道脱模斜度浇注系统冷流道满足Moldflow 填充分析的各项指标要求皮纹每增加0.015mm 深度,沿开模方向上在原有脱模斜度上至少增加1°采用标准件浇口类型冷流道长度需控制在80mm 以内后续浇口容易切除,不可对外观面产生损伤Moldflow 填充分析分型线位置模具插穿角度冷料井建议双衬套导向热流道每个冷流道的转角,都须有冷料井分型线处最小插穿角度为7°浇口分型线GM材料标准模具收缩率分析结果确认零件名称模具设计评审资质模具供应商检验项目姓名是否自动脱浇口顺序阀须采用圣万提(Synventive )热流道基本要求能否满足GMW15424(2013版)模具设计评审检查表Mold Design Checklist零件基本信息模具设计工程师模具类型模具钢材信息。
注塑模具试模验收点检表A0
合格
可 接收
不可 接收
其他 38 注塑工艺验证是否与之前工艺吻合,无较大偏差(各阶段产品认可的注塑工艺)
具体不良事项描述
备注
注塑模具试模验收点检表
项目名称
产品名称
点检项目
1 试模准备原材料是否跟试制单一致
2 试模材料干燥温度、时间、干燥方式是否遵循原材料供应商推荐标准 注 塑 3 水/油路连接方法是否符合模具上标示,并循环通畅 准 4 所有应该连接的行程开关是否已正确连接(顶出行程开关、油缸行程开关) 备
5 模温是否达到设定条件才开始进行试模
设 25 模温机运行正常(数显、温度、流量无异常) 备
26 热流道温控正常(数显、实际温度设定温度基本一致)
27 注塑机台型号与模具式样书要求一致
28 产品分型面、排气槽部位、滑块衔接部位是否有飞边
29 产品滑块连接部位段差是否明显
30 镶件、镶块、模仁皮纹是否一致,皮纹是否有损伤
31 表面无多料、料花、油污、水印 产 品 32 出模顺畅无拉伤、变形、拉白
状 33 熔接痕是否明显(目测不明显、手感无凹凸痕) 态
34 表面状态良好(无烧焦,气雾,缩形,顶白,缺料等)
35 产品模腔编号/零件号/LOGO/时间钟/材料信息标记清晰准确
36 产品表面光洁、无划伤、划痕(高光零件、电镀件)
37 模具能连续稳定生产1000模或者5个小时以上
产品尺寸是否符合标准
模具编号
具 13 模具冷、热流道嘴尖(胶口)无拉丝、余料无残留,针阀系统大小不一致、热流道射胶不稳定)热流道浇口套无漏胶
问 15 开/关模计数器功能正常
题 16 滑块与斜导柱配合功能正常(闭合部位无碰撞、缝隙均匀)
17 模具信息铭牌符合标准(模具编号、车型、制造商、制造日期等)
- 1、下载文档前请自行甄别文档内容的完整性,平台不提供额外的编辑、内容补充、找答案等附加服务。
- 2、"仅部分预览"的文档,不可在线预览部分如存在完整性等问题,可反馈申请退款(可完整预览的文档不适用该条件!)。
- 3、如文档侵犯您的权益,请联系客服反馈,我们会尽快为您处理(人工客服工作时间:9:00-18:30)。
注 塑 模 具 设 计 图 纸 检 查 项 目 表
模号: 序号 1 2 3 4 5 6 7 8 9 零件名称: 内 设计者: 容 日期: 自检 复检
设计所用2D、3D、产品图档是否为客户提供最新图档? 3D图中产品有无放缩水?有无出模角度?有无倒扣?修改过的3D是否与原始的3D核对过? 模具是否按《模具设计技术要求》和《模具设计标准集》设计? 主流道是否尽量短,进胶是否平衡? 进胶点的尺寸是否完整?流道及进胶点大小是否合理?进胶点位置是否在厚胶部位? 镶件、行位、斜顶、PL线是否符合产品要求?是否照设计资料? 精度高或易损坏或难加工或困气的部位是否尽量镶出? 镶件是否考虑有利于加工?(有没有碰数基准位、装夹位等) 斜顶、行位的行程是否计算清楚,是否易于装配,且不会与其他部位干涉?是否有倒扣?
10 制品是否会粘前模、粘行位、粘斜顶? 11 顶出力是否足够 ?顶针布置是否符合“顶出平衡和最大着力点”原则?顶针是否尽量大些? 12 顶针、镶针、夹线是否与产品特殊要求面冲突? 13 设计上是否考虑模具加工应尽量使用磨、线切割、电脑锣而不用火花加工? 14 内模、模胚尺寸是否与订料尺寸一致?硬模内模实际高度是否比订料高度数低0.5mm? 15 3D、2D装配图和零件图中是否有基准角符号及C角?是否已将零件编号打在正确位置? 16 司筒壁厚是否太薄(小于0.65mm是否用双托)?订料尺寸是否按标准填写? 17 材料单有无漏零件?订料有没有放余量及考虑装夹长度? 18 细微结构处是否放大处理? 19 尺寸标注是否足够,画面是否清晰?规定有公差尺寸是否有标注? 20 运水是否充分,且水孔直径尽量在8以上? 21 撑头是否足够,且安排在模具中间位置? 22 直径2.0以下顶针是否尽量选用托针? 23 顶针、螺丝、镶件是否撞运水? 24 弹弓长度是否计算准确?一般40%压缩比,弹弓预压长度为10-15mm? 25 偏心模具定位圈中心是否与顶辊孔中心一致? 26 行位下有顶针的模具,是否有先复位装置或顶针板中行程开关控制? 27 斜顶与顶针、司筒是否在根部有干涉? 28 设计OK的图档(2D、3D)是否按照规范放置于网络上? 记录管制编号:QD07-01-30