si-al复合材料文献总结
Al-Si研究现状

1.4 Al-Si合金的研究现状铝的比重小,塑性好,具有优良的导电性和导热性,表面有致密的氧化膜保护,抗腐蚀性好,而且回收成本低,是一种可持续发展的有色金属。
在纯铝中,加入其它金属或非金属元素,能配制成各种可供压力加工或铸造用的铝合金。
由于铝的密度小,其比强度(拉伸强度/比重)远比灰铸铁、铜合金和球墨铸铁的高,仅次于镁合金、钦合金和高合金钢[80]。
铝及其合金的上述优点决定了它在工业上越来越重要的地位和突飞猛进的发展。
铝的消费己从最初的军工、航空航天、电力、机械等传统领域扩展到交通运输、建筑等领域,其中交通、建筑及包装三个领域的消费比例约占消费总量的70%,而汽车工业的发展也为铝材消费提供了巨大的市场空间。
铝合金最早于1903年试用于内燃机活塞,其成分为Al-10%Zn-3.5%Cu,然而其耐热性不能满足要求,不久就被放弃,但对活塞材料的发展是个突破。
随后欧美研制出Al-8%Cu合金,改进了活塞的耐热性,基本上满足了当时活塞的使用要求,因而该合金曾盛行了一个时期。
1921年“Y合金”(Al-4%cu-1.5%Mg-2.0%Ni)问世,合金中加入Cu和Mg起到弥散强化作用,加Ni 生成NiA13金属间化合物,提高了合金的抗高温蠕变性能。
这样,“Y合金”以其高耐热性、较好的铸造和锻造性能而作为典型的活塞用铝合金而广泛使用。
我国研制成功RR合金(Al-2%cu-l%si-1%Fe-1.5%Mg-1%Ni),通过加入Ni、Fe等合金元素提高了耐热性81】。
1920年PacZ发现Na对Al-si二元共晶合金具有变质作用[82],能改变合金的显微组织,显著提高合金的力学性能,Al-si共晶合金开始应用于活塞生产。
1924年德国KS公司研制成功膨胀系数低于“Y合金”的A1-Si系活塞合金—KS245合金(Al-14%Si-4.5%Cu- 1.5%Ni-0.7%Mg)。
1926年KS公司研制成功过共晶Al-Si合金KS280,达到进一步降低合金热膨胀系数的目的。
Al-Si系铸造铝合金材料的研究

sr n t e n cin a d Cu pa sa mp r n l n sr n h n n te gh niga t n ly n i ot tr e i te g e i g A1一Sis re a tn s. o a o t eis c si g
Ke wo d y r s:Al— S e e ; au n m ly;c sig isr s i lmiu a o l at n
强 度 铸 造 A —S 合 金 不 可 忽 视 C l i u元 素 的 添加 。 关 键 词 : 1 i ; 合 金 ; 造 A 一S 系 铝 铸 中 图 分 类 号 : G 1 T I5 文 献 标 识 码 : A
Re e r h o — S e is a u i u a tng m a e i l s a c f AI — is re l m n m c s i t r as
0 前 言
铝 合金作 为传 统 的金属 材料 , 因其密度 小 , 比强 度 高等 特点 , 已广 泛应用 于 航空 、 天 、 车 、 械等 航 汽 机 行 业 。在机 车车辆 上采 用铝 合金 材料 替代传 统 的钢 铁 材料 可 以很 好 的减 轻 列 车 自重 , 因此 开 发适 合 轨
SiC/Al复合材料界面反应的热力学分析

化 学反 应 方 程 式
3 i() A ():A C () S() SC S +4 l1 h 3S +3 is 3i S +4 l1 =2 1 3S +3 is S () A () A2 () S() O O SO () Mg1 =2 s s +S() i 2s +2 () M o() is 2 i2s +Mg1 +2 l1 =Mg h ds +2 is S0 () () A () A O ) S() Mg s +A O () o() h 3s =Mg b 4s A 0 () 3 g 1 +4 1 3s =3 : b 4s +2 l1 M () A2 () Mg 0 () A () 0 A
于不同的 SC i 预处理工艺、 不同型号的铝合金基体、
不 同的制 备工 艺均对 应着 不 同的界面反 应 ,且界 面 反应对两 相之 间的浸 润性有 很大 的影 响 引 . 本 文通过 分析 复合材 料界 面可能 发生反 应 的热 力学 条 件及 生 成物 A C 和 Mg 1 热力 学 稳定 h, A 的 0
相 关 , 两材料本 身 的结构 、 态及物 理 、 学等性 与 形 化 质密切相 关 】 .在 SC A 复合 材料 制备 过程 中 , i/ 1 由
2 o () A ()+ SO () M A24s +3is Ms s +4 l1 3 i2s =2 g 1 () S() 0 3 () h 3s =3 o ()+2 () Mg1 +A O () Ms s Al1
1 界面反应 的热力学分析
1 1 界面 可能发 生 的化学反 应 .
函数关 系式 , 即
过程中, 可能存 在 的反应如表 1 示 【 ". 所 2 】 .
表 1 SC / 复 合 材 料 制备 中可 能 的化 学反 应 i,
《SiCp-Al复合材料微观断面磨抛与两相三维重构试验研究》范文
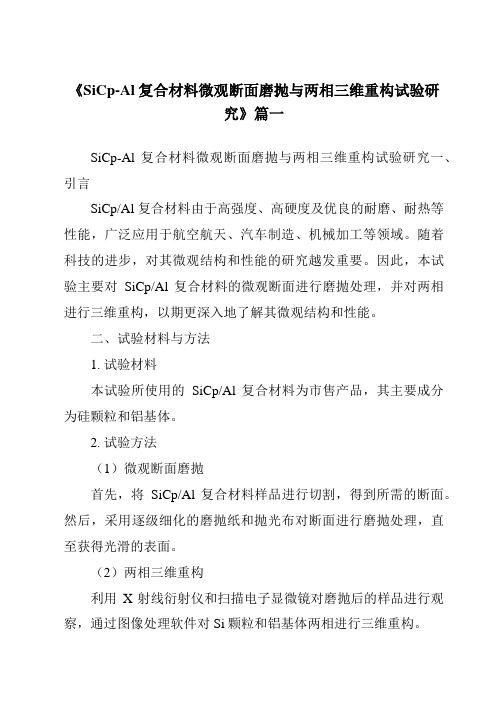
《SiCp-Al复合材料微观断面磨抛与两相三维重构试验研究》篇一SiCp-Al复合材料微观断面磨抛与两相三维重构试验研究一、引言SiCp/Al复合材料由于高强度、高硬度及优良的耐磨、耐热等性能,广泛应用于航空航天、汽车制造、机械加工等领域。
随着科技的进步,对其微观结构和性能的研究越发重要。
因此,本试验主要对SiCp/Al复合材料的微观断面进行磨抛处理,并对两相进行三维重构,以期更深入地了解其微观结构和性能。
二、试验材料与方法1. 试验材料本试验所使用的SiCp/Al复合材料为市售产品,其主要成分为硅颗粒和铝基体。
2. 试验方法(1)微观断面磨抛首先,将SiCp/Al复合材料样品进行切割,得到所需的断面。
然后,采用逐级细化的磨抛纸和抛光布对断面进行磨抛处理,直至获得光滑的表面。
(2)两相三维重构利用X射线衍射仪和扫描电子显微镜对磨抛后的样品进行观察,通过图像处理软件对Si颗粒和铝基体两相进行三维重构。
三、试验结果与分析1. 微观断面磨抛结果经过逐级磨抛处理后,SiCp/Al复合材料的微观断面呈现出光滑的表面,颗粒分布均匀,无明显缺陷。
这为后续的两相三维重构提供了良好的基础。
2. 两相三维重构结果通过X射线衍射仪和扫描电子显微镜的观察,得到了Si颗粒和铝基体的二维图像。
利用图像处理软件对二维图像进行处理,得到了两相的三维模型。
从三维模型中可以看出,Si颗粒在铝基体中分布均匀,两相之间的界面清晰可见。
四、讨论通过对SiCp/Al复合材料微观断面的磨抛处理和两相三维重构,我们可以更深入地了解其微观结构和性能。
首先,光滑的表面和均匀的颗粒分布有利于提高材料的力学性能和耐磨性能。
其次,两相三维模型清晰地展示了Si颗粒和铝基体的分布情况,为进一步研究其性能提供了有力的工具。
此外,本试验方法为其他复合材料的微观结构和性能研究提供了参考。
五、结论本试验通过对SiCp/Al复合材料微观断面的磨抛处理和两相三维重构,得到了其光滑的表面和清晰的两相分布情况。
Al-Si复合材料化学镀Ni-P合金研究
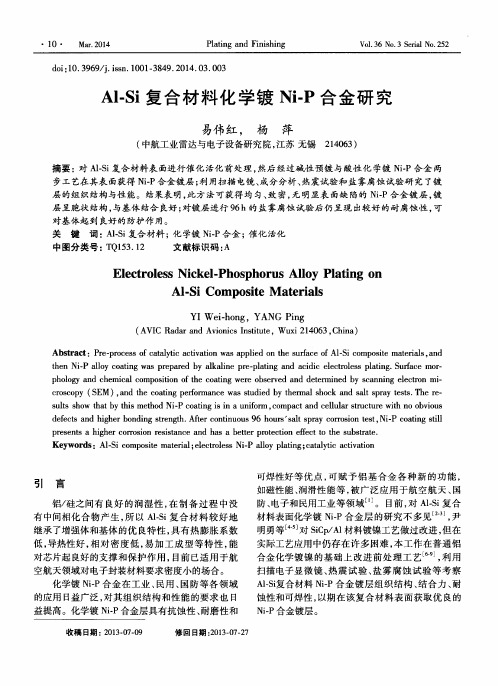
引 言
A l — S i 复 合材 料化 学镀 N i — P合 金 研 究
易伟 红 , 杨 萍
( 中航工业雷达与电子设备研究院, 江苏 无锡 2 1 4 0 6 3 )
摘 要 :对 A 1 - s i 复合 材料 表 面进 行催 化 活化前 处理 , 然后 经过 碱 性预 镀 与 酸 性化 学镀 N i — P合 金 两 步工 艺在 其表 面获得 N i — P合 金镀 层 ; 利 用扫描 电镜 、 成分 分析 、 热震试 验 和盐 雾腐 蚀 试验研 究 了镀 层的组织结构与性能。结果表 明, 此方法可获得均 匀、 致密, 无明显表 面缺 陷的 N i . P合金镀层, 镀 层 呈胞状 结构 , 与基 体 结合 良好 ; 对镀层 进行 9 6 h的盐 雾腐蚀 试 验后 仍 呈现 出较好 的耐腐 蚀 性 , 可
・
1 0・
Ma r . 2 0 1 4
பைடு நூலகம்
P l a t i n g a n d Fi n i s hi ng
Vo 1 . 3 6 N o . 3 S e r i a l No . 2 5 2
d o i : 1 0 . 3 9 6 9 / j . i s s n . 1 0 0 1 — 3 8 4 9 . 2 0 1 4 . 0 3 . 0 0 3
t h e n Ni — P ll a o y c o a t i n g wa s p r e p a r e d b y a l k a l i n e p r e- p l a t i n g a n d a c i d i c e l e c t r o l e s s p l a t i n g . Su fa r c e no r - p h o l o g y a n d c h e mi c l a c o mp o s i t i o n o f t h e c o a t i n g we r e o bs e r v e d a n d d e t e r mi n e d b y s c a n n i n g e l e c t r o n mi -
SiCP_Al基复合材料的研究与进展

SiCP/Al基复合材料的研究与进展罗洪峰 林 茂 陈致水 廖宇兰(海南大学机电工程学院 海南 570228)摘 要: 综述了SiCP/Al基复合材料的国内外研究现状,从材料的选择、制备技术和性能等方面,分析了该材料发展过程中存在的一些问题,并且展望了该材料今后的发展。
关键词:铝基复合材料 碳化硅颗粒 研究进展1、前言SiC P/Al基复合材料具有较高的比强度、比刚度、弹性模量、耐磨性和低的热膨胀系数等优良的物理性能,且制造成本低,可用传统的金属加工工艺进行加工,引起了材料研究者们的极大兴趣,在航空航天、军事领域及汽车、电子仪表等行业中显示出巨大的应用潜力。
从80年代初开始,国外投入了大量财力致力于颗粒增强铝基复合材料的研究,并已在航空航天、体育、电子等领域取得应用。
如DWA公司生产的25V ol%SiC P/6061Al基复合材料仪表支架已用于Lockheed飞机的电子设备。
美国海军飞行动力试验室研制成SiC P/Al基复合材料薄板并应用于新型舰载战斗机。
俄罗斯航空、航天部门将SiC P/Al基复合材料应用于卫星的惯导平台和支承构件。
国内从80年代中期开始在863计划的支持下,经过十几年的努力,SiC P/Al基复合材料的研究方面有了很大提高,在材料组织性能、复合材料界面等方面的研究工作己接近国际先进水平。
2、SiC P/Al基复合材料的制备工艺目前用于生产颗粒增强铝基复合材料的工艺方法大体可分为四类:液态工艺(搅拌铸造、液态金属浸渗、挤压铸造等)、固态法(粉末冶金等)、双相(固液)法(喷射共沉积、半固态加工等)、原位复合法。
2.1、搅拌铸造法搅拌铸造法是通过机械搅拌装置使增强体颗粒与固态或半固态的合金相互混合,然后浇注成锭子的技术。
与其它制备技术相比,该方法工艺设备简单、制造成本低廉,可以进行大批量工业生产,而且可制造各种形状复杂的零件,因此是目前最受重视、用得最多的制备铝基复合材料的实用方法。
al在si扩散系数

al在si扩散系数引言在材料科学领域,研究材料的扩散性质对于了解材料的性能和应用具有重要意义。
其中,铝(Al)在硅(Si)中的扩散系数是一个关键参数,它决定了Al在Si晶体中的扩散速率和扩散深度。
本文将探讨Al在Si中的扩散机制、影响因素以及测量方法。
扩散机制在固体中,扩散是指原子、离子或分子从高浓度区域向低浓度区域的自发性运动。
对于Al在Si中的扩散,主要有以下两种机制:1.空位扩散:在Si晶体中,空位是指晶格中原子缺失的位置。
Al原子可以通过占据空位的方式从一个位置跳到另一个位置,从而实现扩散。
2.替代扩散:Al原子可以取代Si晶体中的某些位置上的Si原子,从而实现扩散。
这种扩散机制通常发生在高温下,当温度升高时,Al原子更容易替代Si原子。
影响因素Al在Si中的扩散系数受多种因素的影响,下面列举了一些重要的因素:1.温度:温度是影响扩散速率的最主要因素。
一般来说,随着温度的升高,扩散系数也会增加。
这是因为高温下原子具有更大的热运动能量,更容易克服位垒从而实现扩散。
2.晶格缺陷:晶格缺陷包括空位、间隙原子和位错等。
这些缺陷会影响Al原子在Si晶体中的扩散行为。
例如,空位的存在可以提供Al原子扩散所需的跳跃位置。
3.掺杂:杂质原子的存在可以显著影响Al在Si中的扩散。
掺杂原子可以改变晶格结构和扩散路径,从而影响扩散速率。
4.应力:应力是指晶体内部的力学应力。
应力可以改变晶格的形貌,从而影响Al原子的扩散行为。
测量方法测量Al在Si中的扩散系数是材料科学研究中的一个重要课题。
以下是几种常用的测量方法:1.掺杂法:通过在Si晶体中掺入一定浓度的Al原子,并在高温条件下进行退火,观察Al原子在Si晶体中的扩散行为,从而得到扩散系数。
2.同位素标记法:利用同位素标记技术,将Al原子与Si晶体中的Si原子进行同位素替代,然后通过测量同位素的扩散行为来确定扩散系数。
3.电子显微镜法:利用电子显微镜观察Al原子在Si晶体中的扩散行为,结合图像处理和分析技术,计算出扩散系数。
金刚石/铝复合材料制备与性能研究

金刚石/铝复合材料制备与性能研究铝基复合材料由于具有高导热、低密度和热膨胀系数的性能,是目前应用较为广泛的电子封装材料,金刚石是自然界中已知最硬的材料,它具有很高的热导率,金刚石/铝复合材料以其优异的性能有着较好的发展前景,但其制备过程仍存在缺陷,本文研究了金刚石/铝复合材料制备方法,并对性能进行分析。
标签:金刚石/铝复合材料;制备过程;性能研究1 金刚石/铝复合材料铝基复合材料由于具有高导热、低密度和热膨胀系数的性能,是目前应用较为广泛的电子封装材料,尤其对于航空航天电子设备和移动电子设备,有着巨大的吸引力。
铝基复合材料已经成功地应用于微波管的载体、密封式微波热沉材料、MCM 组件的热沉、印刷电路板(PCB)用热沉。
金刚石是自然界中已知最硬的材料,具有很高的热导率(天然的金刚石为2200~2600 W/(m·K),人工的金刚石为1200~2000 W/(m·K))、弹性模量(1050GPa)以及低的热膨胀系数(1.3×10?6 K?1),且在室温下是绝缘体。
利用它与常用金属(A1、Cu等)性能的巨大差异性,将其作为增强相与金属或合金复合,制备出的复合材料可以显著改善热导率、热膨胀系数、强度等性能,是理想的第四代金属基电子封装材料。
2 金刚石/铝复合材料制备方法目前,国内外学者已经成功制备金刚石增强金属基复合材料,并已小批量生产应用于电子封装领域。
BEFFORT 等采用液压浸渗后挤压成形的方法成功制备出金刚石/Al 复合材料。
但基体与增强相润湿性差及不同传质方式导致的界面结合问题,极大地削弱金刚石在复合材料中的作用。
需要对金刚石进行表面改性或对基体进行合金化处理。
MIZUUCHI 等将复合粉末采用放电等离子烧结的方式成功制备了致密度高达99%以上、热导率为552W/(m·K)的金刚石/Al 复合材料。
采用Al与体积分数60%以上的金刚石颗粒复合制备金刚石/Al复合材料,其热导率的理论值应在800 W/(m·K)以上。
- 1、下载文档前请自行甄别文档内容的完整性,平台不提供额外的编辑、内容补充、找答案等附加服务。
- 2、"仅部分预览"的文档,不可在线预览部分如存在完整性等问题,可反馈申请退款(可完整预览的文档不适用该条件!)。
- 3、如文档侵犯您的权益,请联系客服反馈,我们会尽快为您处理(人工客服工作时间:9:00-18:30)。
热导率的影响情况
①粉末冶金液相烧结制备过程中压制压力对材料热导率的 影响
720MPa附 近出现峰值
热导率的影响情况
结果分析:
700℃低温烧结:
材料内部空隙率随着压制压力的增大而降低,增强了热导率。
1000℃高温烧结:
孔隙率变化不大,但Si-Al界面结合状态改善,大的压制压力下形 成适当的冶金结合形态。
热处理对导热性能的影响
复合材料经挤压铸造法制备, 制备过程中由于Si和Al的热膨胀系数 不匹配, 在冷却过程中会在Si一Al 界面处引入大量的热错配应力。 这种热应力会使得基体合金的晶格发生畸变, 从而导致品格产生非谐 振, 降低热传导性能。 退火的主要目的就是使这种热错配应力降低。因此, 复合材料经过 退火处理后热导率会上升。
弯曲强度的影响情况
影响弯曲强度的主要因素为
复合材料通过控制制备工艺参数,相 含量以及后续热处理方式可以有效的改 善材料的各性能。
作为电子封装材料,Si/Al复合材料主要考虑的 性能有:
密度
热导性
热膨胀 系数
• 较低的密度 • 较高的导热系数 • 较小的热膨胀系数,与芯片匹配
弯曲强度
• 一定的弯曲强度起到支撑保护的作用
影
复合材料中Si的含量
响
因
制备工艺参数
素
后续热处理工艺
密度的影响情况
① 杨培勇等人利用粉末冶金液相烧结技术制备Si/Al复合材料, 130 μm Si粉与13 μm的Al粉按质量1:1混合
Si含量对复合材料导热性能的影响
随着Si含量的增加热导率逐渐下降,主要是由于Si的热导率比Al要低的 多。单晶Si的导热系数为148W/(m· K),而Al的导热系数为237W/(m· K) 不管是基体还是增强体,增加Si的含量,都是添加了附加相,都会引 入Si-Al界面,降低热导。
热导率的影响情况
新型网状结构Sip/Al复合材料的 制备及组织性能研究
文献总结
主要内容:
英文文献翻译 Effect of Si content on microstructure and properties of Si/Al composites(Si含量对Si/Al复合材料组织和性能的影响) 中文文献阅读 Si/Al 电子封装材料粉末冶金制备工艺研究 Sip/Al 复合材料中的界面和硅相形貌的演变 界面及 Si元素含量对 Si-Al复合材料导热性能的影响
论 文 简 述
Effect of Si content on microstructure and properties of Si/Al composites(Si含量对Si/Al复合 材料组织和性能的影响): 利用放电等离子体烧结技术制备Si/Al复合材料,研究 不同Si含量对复合材料各性能的影响。 Si-Al 电子封装材料粉末冶金制备工艺研究: 杨培勇等人利用粉末冶金液相烧结技术制备所需复合材 料,研究了压制压力、烧结工艺对材料微观组织及性能的 影响
压制压力对烧结体密度的影响
密度的影响情况
700℃低温烧 结 • 压制压力增 加,烧结体 密度呈上升 趋势
1000℃高温烧 结 • 压制压力增 加,烧结体 密度较大, 但变化不明 显
压坯 • 压制压力增 加,密度呈 上升趋势
密度的影响情况
结果分析:
700℃低温烧结: Al液粘度较大,与Si的润湿性差,液相的流动对孔隙的填充作用 有限,材料空隙率较大。 1000℃高温烧结: Al流动性较好,与Si的润湿性好,材料内部气孔减少,材料密度 较大,且随压制压力变化不大。 压坯: 本身孔隙率较大。
论 文 简 述
Sip/Al 复合材料中的界面和硅相形貌的演变 王小峰等人利用挤压铸造法制备Sip/Al 复合材料,研 究不同高温真空热处理工艺条件下,高体积分数Sip/Al 复合材料(φ(Si)=65%)中硅铝界面特征与硅相形貌的演变 过程。 界面及 Si元素含量对 Si-Al复合材料导热性能的影响 修子扬等人采用压力浸渗专利技术制备了,体积分数为 65 % 的高体积分数环保型Sip/Al复合材料.研究了基体与 增强体中Si含量对m的Al粉和44μm的Si粉混合制备Si的体积分数分别是 50%,55%,60%,65%,70%的Si/Al复合材料。
Si含量对复合材料密度的影响
Si含量↑ 密度↓
随着Si含量的增加,复合材料气孔率增加(毛细作用影响),导致 密度下降
密度的影响情况
影响密度的主要因素为材料内部 的大小
的流动和Si 颗粒的重排过程的进行, 减少材料内部大量存在的孔洞。 2)提高烧结温度和延长烧结时间有利于溶解-析出过程的充分进行 ,细小Si 颗粒大部分消失, 颗粒形状发生钝化。材料内部的界面总数大大减少, 界面 对自由电子和声子的散射降低, 导致材料的热导率升高 3)通过提高烧结温度和适当延长烧结时间改善体系的润湿性和促进溶解析出 过程的进行有利于材料内部高热导Al 基体形成连通网络结构。这对于材料内 部热量有效地传递。
4) 1000℃x2h时,材料的热导率最高若继续升高烧结温度或延长烧结时间Si 颗粒发生比较严重的团聚和偏析, 阻断Al 的连通网络结构。
热导率的影响情况
• ③修子扬等人采用压力浸渗专利技术制备了体积分数为65 % Sip/Al复 合材料.平均粒径10 μm高纯Si颗粒,以LG5,LD11,Al-Si20为基体。
压制压力超过720MPa,脆性相Si内部出现微裂纹,缺陷甚至颗粒已 经发生解理、破碎。1000℃高温烧结缺陷也无法完全恢复。新的解理 面对声子和自由电子的散射相当严重,导致界面热阻增加。
热导率的影响情况
②粉末冶金液相烧结制备过程中烧结温度和时间对热导率的影响
1)提高烧结温度可以促进氧化铝膜的破裂,改善体系的润湿性。促进液态Al
热导率的影响情况
影响热导率的主要因素
热膨胀系数的影响情况
放电等离子体烧结制备复合材料
Si含量对热膨胀系数的影响
Si的热膨胀系数 (4.1x10-6K-1) 比Al的热膨胀系数 (23.6x10-6K-1)小很 多。 实验值最低可达到 9.2x10-6K-1 Si含量为60%时复合材 料热膨胀系数为 9.8x10-6K-1 与半导体 热膨胀系数相似
热膨胀系数的影响情况
影响热膨胀系数的因素
弯曲强度的影响情况
放电等离子体烧结技术制备Si/Al复合材料 Si含量对弯曲强度的影响
Si相为脆性相Si/Al 复合材料的断裂方式主 要有: Si相的解理断裂 Al相的韧性撕裂 Si相与Al相的界面分离。 Si含量的增加使Si相的 解理断裂几率增加,弯 曲强度降低