70BJ 010-2011 铬钼钢复合钢板制压力容器制造及验收工程技术条件
LH-SBB-32 关键设备设计规范管理规定 (1)

√
√
验
14
NB/T 47018
承压设备用焊接材料订货技术条件
15
NB/T 47041
塔式容器
√
√
16
NB/T 47042
卧式容器
√
17
SH/T 3074
石油化工钢制压力容器
√
18
SH/T 3098
石油化工塔器设计规范
√
√
√
√
√
√
√
√
√
√
√
√
√
√
√
√
√
√
√
√
√
√
√
√
√
√
√
√
√
√
√
√
√
√
√
√
材料
热轧钢板和钢带的尺寸、外形、重量及
性评审工作。 六、附则 (一)本规定由设备部制定并负责解释。 (二)对违反本规定的按照公司奖惩实施细则执行。 (二)本规定自下发之日起执行。 附件 3 件:1、《关键动设备设计规范台账》 2、《关键静设备设计规范台账》 3、《加热炉设计规范台账》
附件 1:
关键动设备设计规范台账
单位:
序号 标准代号
压力容器
14 GB18613
中小型三相异步电动机能效限定值及能效等级
15 GB30254
高压三相笼型异步电动机能效限定值及能效等级
16 GB3836
爆炸性气体环境用电气设备
17 GB50058
爆炸危险环境电力装置设计规范
18 GB755-2008
旋转电机 定额和性能
19 GB7777
往复活塞压缩机机械振动测量与评价
铬钼钢技术措施方案

铬钼钢技术措施材质为15CrMo。
铬钼钢可焊性差,焊接工艺复杂,需经由严酷的预热、层间加热、后热、热措置等工序才能获得及格的焊接接头。
而且返工时轻易发生裂纹等缺陷,给施工和打点带来很浩劫度,为知足现场施工需要确保工程质量,将铬钼钢焊接和热措置作为非凡过程节制,特编制本施工手艺法子。
2.0编制依据《工业金属管道工程施工及验收规范》 GB50235-97《现场设备、工业管道焊接工程施工及验收规范》 GB50236-98《石油化工剧毒、可燃介质管道工程施工及验收规范》 SHJ3501-1997《石油化工工程铬钼耐热钢管道焊接手艺规程》 SHJ3520-1991《工业金属管道工程质量磨练评定尺度》 GB50184-93相关施工图纸及一再操作图4.0焊接施工法子4.1施工人员4.1.1焊接工程师应按焊接工艺评定拟定焊接工艺卡,解决焊接手艺问题,指导焊接工作。
4.1.2焊接搜检人员应按照手艺规范、设计文件、焊接工艺卡对现场焊接工艺的执行情形进行持续监控,确定标识表记标帜并记实,焊接搜检人员应搜检上岗焊工的及格证,对焊接一次及格率低的焊工遏制其焊接工作。
4.1.3无损检测人员应具有劳动局公布的无损检测资格证,应熟悉磨练工作的事理及磨练设备的应用并正确评定焊接接头的缺陷。
4.1.4热措置人员应熟悉铬钼钢接头的热措置参数及热措置设备的应用,负责焊前预热、焊中伴热、焊后后热和热措置工作,并填发清算保管全数热措置记实。
4.1.5焊工应具有劳动局公布的响应项目的焊工及格证,并能按照焊接工艺卡选择合适的焊接工艺参数,严酷按焊接工艺要求施焊。
4.1.6铬钼合金管的组对安装工作应配备经验丰硕、责任心强的管工负责。
4.2施工机具及设备4.2.1非凡过程的施工机具应由设备科配备无缺的设备,并由专人搜检和调养。
4.2.2焊机必需具有参数不变,调节矫捷,知足焊接工艺要求,平安靠得住的机能。
4.2.3热措置设备应能自动控温,用热电偶侧量温度,每个回路均有温度显示并由制动记实仪记实热措置曲线。
铬钼钢制压力容器注意事项(1)

铬钼钢制压力容器注意事项(2011-08-03 16:38:00)标签:学习总结杂谈一、简介1. 铬钼钢的主要特性:耐热性、抗氢性、回火脆性。
(1)耐热性。
要求钢材在中、高温条件下金相组织要稳定,否则可能产生石墨化现象,导致材料脆性急剧增大;还要求钢材具有较高的高温持久强度极限和蠕变极限。
铬钼钢能达到以上要求。
(2)抗氢腐蚀。
①在高温高压条件下,侵入钢中的氢气与钢中的渗碳体(Fe3C)和不稳定碳化物析出的碳起化学反应,生成甲烷,导致钢材破裂的现象,称为氢腐蚀。
②影响氢腐蚀敏感性最关键因素是钢材的化学成分、操作温度、暴露期间的氢分压和应力水平。
③钢材氢腐蚀的速度随压强和温度的升高而加快,这是因为压强增加,有利于氢气在钢材中溶解;而温度的升高则增加氢气在钢中的扩散速度及脱碳反应速度。
(3)回火脆性。
①发生在370-595℃温度范围内。
接近这个温度范围的上限时,脆化速度高,接近下限时,脆化发展缓慢。
②脆化材料和非脆化材料的差别,仅表现在缺口冲击韧性和韧脆转变温度的不同,而拉伸性能无明显差别。
回火脆化的程度一般是靠韧脆转变温度的升高来表明的。
③常用的Cr-Mo钢种中,含Cr量为2%-3%的Cr-Mo钢(2.25Cr-1Mo、2.25Cr-1Mo-0.3V、3Cr-1Mo、3Cr-1Mo-0.25V等)回火脆化倾向最严重。
④脆化敏感性的程度,按金相组织马氏体、贝氏体、珠光体的顺序依次降低。
降低方法是尽可能降低杂质元素(P、Sb、Sn、As)的含量。
⑤防止措施:A.控制钢材中的Si、Mn含量和有害元素含量是防止产生挥霍催化的基本措施;B.控制钢材和焊缝金属的韧脆转变温度。
2. 临氢压力容器常用的铬钼钢有1Cr-0.5Mo、1.25Cr-0.5Mo-Si、2.25Cr-1Mo、2.25Cr-1Mo-0.3V、3Cr-1Mo、3Cr-1Mo-0.25V等。
3. 在普通碳素钢基础上添加阻止渗碳体分解和强碳化物形成元素Cr、Mo、V等,便可达到减小和防止钢中甲烷的生成,从而避免发生氢腐蚀。
压力容器制造焊接技术标准及要求
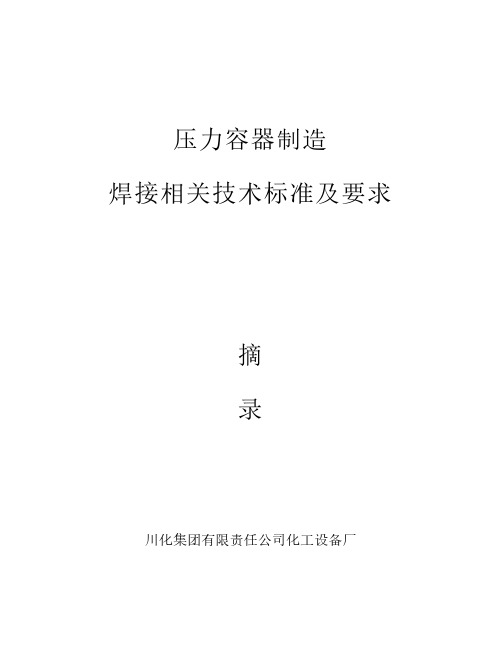
压力容器制造焊接相关技术标准及要求摘录川化集团有限责任公司化工设备厂《钢制化工容器制造技术要求》摘录5.焊接和切割5.1 切割5.1.1采用火焰切割下料时,应清除熔渣及有害杂质,并采用砂轮或其它工具将坡口加工平整。
当切割材料为标准规定的抗拉强度σb>540MPa的高强度钢或铬钼合金钢时,火焰切割表面应采用打磨或机械加工的方法清除热影响区和淬硬区,并进行磁粉或渗透探伤。
不锈钢的碳弧气刨表面应采用砂轮打磨,清除渗碳层。
5.1.2火焰切割时的预热与否,一般应符合钢材焊接时的预热要求。
受压元件气割的开孔边缘或剪切下料的端部如未经焊接者(如安放式接管的开孔边缘或内伸式接管的端部),应采用打磨等方法去除3mm以上。
5.2 焊缝位置5.2.1壳体上的开孔应尽量不安排在焊缝及邻近区域,但符合下列情况之一者,允许在上述区域开孔:1.符合GB150开孔补强要求的开孔可在焊缝区域开孔。
2.符合GB150规定的允许不另行补强的开孔,可在环焊缝区域开孔。
但此时应以开孔中心为圆心,对直径为3倍开孔直径长度的圆所包括的焊缝进行100%射线或超声波探伤,并符合要求。
凡因开孔而可予去除的焊缝可不受探伤质量的影响。
3.符合GB150规定的允许不另行补强的开孔,当壳体板厚小于等于40mm时,开孔边缘距主焊缝的边缘应大于等于13mm。
但若按5.2.1条第一款对主焊缝进行射线或超声波探伤并符合要求者,可不受此限。
5.2.2 外部附件与壳体的连接焊缝,如与壳体主焊缝交叉时,应在附件上开一槽口,以使连接焊缝跨越主焊缝。
槽口的宽度应足以使连接焊缝与主焊缝边缘的距离在1.5倍壳体壁厚以上。
5.3 焊接准备5.3.1 焊接坡口及其两侧至少15mm内的母材表面应消除铁锈、油污、氧化皮及其它杂质。
铸钢件应去除铸态表面以显露金属光泽。
5.3.2 气割坡口的表面质量至少应符合下表的要求。
气割坡口的表面质量类别定义质量要求平面度表面凹凸程度凹凸度小于等于2.5%板厚粗糙度表面粗糙速Ra50(μm)凹坑局部的粗糙速增大凹坑宽度小于等于50mm 且每米长度内不大于1个5.3.3 坡口上的分层缺陷应予以清除,清除深度为分层深度或10mm(取小者),并予以补焊。
9、浅谈铬钼钢及其复合钢板焦炭塔现场组焊施工技术要求

• 谢谢各位领导和专家聆听! • 欢迎各位专家批评指正,共同提高!
• • •
7. 质量验收
• 焦炭塔现场焊接工作完成后,应按设计 要求进行整体热处理、经硬度检测和PMI (指合金元素检测)复核合格,最后进行 整体水压试验。焦炭塔水压试验时,施工 单位、监理、业主和监督检验机构代表等 均应到场见证,试验合格后各方代表应在 施工单位准备好的强度试验报告上签字确 认。
•
⑥多层多道焊每层焊完后应立即对层间进行清理,并进行外观检 查,若发现缺陷,清除后方可进行下一层的焊接。多层多道焊层间接 头应错开50mm以上。 • ⑦每条焊缝应一次连续焊接完成。在焊接过程中,由于某种原因 必须中断焊接工作时,应保持焊缝坡口及两侧各150 mm范围的区域 处于预热温度(160~200℃)范围内,直至焊接工作重新开始;否 则,在暂停焊接工作时应立即进行后热处理(指消氢处理)并采取缓 冷的措施,后热处理温度应控制在250~350℃范围内。 • ⑧焊接SA387Gr11CL1+06Gr13复合钢板时,应先焊接基层后焊 接复合层。基层焊缝表面经打磨并100%磁粉检测合格后,方可进行 过渡层堆焊焊接。过渡层厚度应控制在0~1 mm之间,表面应平滑经 100%磁粉检测合格后方可进行复层焊接。 • ⑨工卡具拆除时不应损伤母材,拆除后应将残留焊疤打磨光滑; 打磨后母材厚度不得小于其允许的最小设计值,否则应按正式焊接工 艺进行堆焊并打磨平滑;打磨后的母材表面应经100%磁粉检测合格。
图六 焦炭塔上封头焊接顺序示意图
焦炭塔锥段焊接工艺
• 焦炭塔锥段焊接工艺与焦炭塔上封头焊 接工艺基本相同。
5 .焊缝检验
• 外观检查 • 所有焊接接头表面应圆滑过渡,不允许存 在咬肉、裂纹、气孔、弧坑、夹渣等缺陷; 焊接接头上的熔渣和两侧的飞溅物必须打 磨和清理干净。
压力容器制造和检验具体要求

压客容器制造和检验具体要求材料复验要求1 对于下列材料进行复验:a)采购的第Ⅲ类压力容器用Ⅳ级锻造;b)不能确定质量证明书真实性或者对性能和化学成分有怀疑的主要受压元件材料;c)用于制造主要受压元件的境外材料;d)用于制造主要受压元件的奥氏体型不锈钢开平板e)设计文件要求进行复验的材料。
2 奥氏体型不锈钢开平板应按批号复验力学性能(整卷使用者,应在开平操作后,分别在板卷的头部、中部和尾部所对应的开平板上各截取一组复验试样;非整卷使用者,应在开平板的端部截取一组复验试样);对于上述a)、b)、c)、e)要求复验的情况,应按炉号复验化学成分,按批号复验力学性能。
3 材料复验结果应符合相应材料标准的规定或设计文件的要求。
4 低温容器焊条应按批进行药皮含水量或熔敷金属扩散氢含量的复验,其检验方法按相应的焊条标准或设计文件.母材热处理试件1制备母材热处理试件条件凡符合以下条件之一者,应制备母材热处理试件:a)当要求材料的使用热处理状态与供货热处理状态一致时,在制造过程中若改变了供货的热处理状态,需要重新进行热处理的;b)在制造过程中,需要采用热处理改善材料力学性能的;c)冷成形或温成形的受压元件,成形后需要通过热处理恢复材料性能的。
2制备母材热处理试件与试样的要求2.1母材热处理试件与母材同炉进行热处理,当无法同炉时,应模拟与母材相同的热处理状态;2.2试件的尺寸可参照NB/T47016的要求确定,母材热处理试件切取拉伸试样1个,冷弯试样1个,冲击试样3个;3试样检验与评定试件的拉伸、冷弯和冲击试验分别按GB/T228、GB/T-232和GB/T229的规定进行,并按GB150.2和设计文件要求进行评定;当试样评定结果不能满足要求时,允许重新取样进行复验,如复验结果仍达不到要求,则该试件所代表的母材判为不合格;成形受压元件的恢复性能热处理1钢板冷成形受压元件,当符合下列a) ~e) 中任意条件之一,且变形率超过下表的范围,应于成形后进行相应热处理恢复材料的性能。
70BJ 010-2011 铬钼钢复合钢板制压力容器制造及验收工程技术条件
成型和热处理的加热过程以及最大或最小模拟焊后热处理;
2)锻件的试样应按 BN/T47008 和表 5 的规定制取。当采用热缓冲环或环段时,应按
NB/T47008 规定制取;
3)钢板的试样应按表 6 规定制取。
表5
锻件取样部位和数量
试验项目
执行标准
数量
热处理条件
常温拉伸试验
GB228
按照 JB4726-94
朱玫 编制
张国信 校审
李法海 标准化审核
陈崇刚 审定
2011-04-15
2011-04-20
发布日期 实施日期
70BJ010-2011
第 2 页 共 18 页
GB/T6394 金属平均晶粒度测定法 GB6479 高压化肥设备用无缝钢管 GB8923 涂装前钢板表面锈蚀等级和除锈等级 GB9948 石油裂化用无缝钢管 GB/T10561 钢中非金属夹杂物含量的测定标准评级图显微检验法 GB24511 承压设备用不锈钢钢板及钢带 HG/T20592 钢制管法兰(PN 系列) HG/T20615 钢制管法兰(Class 系列) JB/T4700 压力容器法兰分类与技术条件 JB/T4707 等长双头螺柱 JB4708 钢制压力容器焊接工艺评定 JB/T4709-2000 钢制压力容器焊接规程 JB/T4710 钢制塔式容器 JB/T4711 压力容器涂敷与运输包装 JB/T4730 承压设备无损检测 JB/T4731 钢制卧式容器 JB4744 钢制压力容器产品焊接试板的力学性能检验 JB/T4747 压力容器用钢焊条订货技术条件 NB/T47002.1-2009 压力容器用爆炸焊接复合板 第一部分 不锈钢-钢复合钢板 NB/T47008 承压设备用碳素钢和低合金钢锻件 NB/T 47010 承压设备用不锈钢和耐热钢锻件 NB/T47013.10 承压设备无损检测 第 10 部分:衍射时差法超声检测 SH3022 石油化工设备和管道涂料防腐蚀技术规范 SH3043 石油化工设备管道钢结构表面色和标志规定 SH/T3074 石油化工钢制压力容器 SH/T3524 石油化工静设备现场组焊技术规程 SH/T3526 石油化工异种钢焊接规程 SH/T3527-1999 石油化工不锈钢复合钢焊接规程 ASME SA-335 Standard Specification For Seamless Ferritic Alloy-Steel Pipe For
钢制压力容器检验规程(整理)
1范围
本规程规左了本公司一、二类钢制压力容器制造过程中地质量检验内容、依据、方法及检测率. 钢制常压容器参照本规程执行.
2规范性引用文件
下列文件中地条款通过本标准地引用而成为本标准地条款.凡是注日期地引用文件,其随后所有地修改单(不包括勘误地内容)或修订版均不适用于本标准,然而,鼓励根据本标准达成协议地各方研究是否可使用这些文件地最新版本.凡是不注日期地引用文件,其最新版本适用于本标准.
《压力容器安全技术监察规程》
GB150 《钢制压力容器》
GB151 《管壳式换热器》
Q/AXL SY《压力容器产品质量手册》
压力容器《程序文件》
检验规程
3. 1材料
3.9法兰加工
3. 12安全阀
3. 21耐压实验
3. 25产品总检。
压力容器验收技术要求-
容器(及压力容器)的制造、试验、检验和验收的技术条件1. 主题内容与适用范围本技术条件规定了容器(及压力容器)的制造、试验、检验和验收的技术要求本技术条件适用于容器(及压力容器)的制造、试验、检验和验收2. 引用标准下列标准所包含的条文,通过在本标准中引用而构成本标准的条文。
本标准在使用时,所示版本均为有效。
GB150-1998 钢制压力容器GB 985 气焊、手工电弧焊及气体保护焊焊缝坡口的基本形式与尺寸GB 986 埋弧焊焊缝坡口的基本形式与尺寸GB8162 结构用无缝钢管GB8163 输送流体用无缝钢管GB14975 结构用不锈钢无缝钢管GB14976 输送流体用不锈钢无缝钢管GB5130 高压锅炉用无缝钢管GB3087 低中锅炉用无缝钢管GB13296 锅炉、热交换器用不锈钢无缝钢管GB/T9112 钢制管法兰类型与参数GB/T9115.1~.4 各类型(平面、突面;凹凸面、榫槽面;环连接面)对焊钢制管法兰GB/T9116.1~.4 各类型(平面、突面;凹凸面、榫槽面;环连接面)带颈平焊钢GB/T9123.1~.4 各类型(平面、突面;凹凸面、榫槽面;环连接面)钢制管法兰盖GB/T9124 钢制管法兰技术条件GB/T9125 管法兰连接用紧固件GB/T9126 管法兰用非金属平垫片GB/T9124 管法兰用金属平垫片JB/T82.1~.4 各类型(凸面、凹凸面、榫槽面、环连接面)对焊钢制管法兰JB/T86.1~.2 各类型(凸面、;凹凸面)钢制管法兰盖JB/T 4700 压力容器法兰分类与技术条件JB/T4701 甲型平焊法兰JB/T4702 乙型平焊法兰JB/T4703 长颈对焊法兰JB/T4709 钢制压力容器焊接工艺规范JB4730 压力容器无损检测HG/T20592-2009 钢制管法兰(PN系列)HG/T20613-2009 钢制管法兰用紧固件(PN系列)HG/T20614-2009 钢制管法兰、垫片、紧固件选配规定(PN系列)3. 总则⑴容器的制造单位(以下简称制造单位)如承担制造压力容器时,应持有压力容器制造许可证,并具有符合国家压力容器安全监察机构有关法规要求的质量体系或质量⑵压力容器的焊接及无损检测对承担人的资格要求按GB150要求。
FB002-2011 铬钼钢压力容器工程技术条件
目录1. 范围 (2)2. 引用标准 (2)3. 总则 (2)4. 材料 (3)5. 制造 (3)6. 无损检测 (5)7. 焊后热处理 (5)附录 (7)附表1 容器外形尺寸允许偏差 (7)附图1 卧式容器外形尺寸 (8)附图2 立式容器外形尺寸 (9)1.范围1.1.本标准规定的一般铬钼钢制压力容器在材料、制造、检验等方面的通用要求。
1.2.本标准适用于按GB150-1998和TSG R0004-2009设计的铬钼钢压力容器的制造和验收。
1.3.本标准不适用于低温压力容器和按JB4732《钢制压力容器——分析设计标准》设计的容器的制造和验收。
2.引用标准下列标准所包含的条文,通过在本标准中引用而构成为本标准的条文。
本标准出版时,所示版本均为有效。
所有标准都会被修订,使用本标准的各方应探讨使用下列标准最新版本的可能性。
TSG R0004-2009 固定式固定式压力容器安全技术监察规程GB150-1998钢制压力容器GB/T985.1气焊、焊条电弧焊、气体保护焊和高能束焊的推荐坡口GB/T985.2埋弧焊的推荐坡口GB/T1184形状和位置公差未注公差值GB/T1804一般公差未注公差的线性和角度尺寸的公差GB713锅炉和压力容器用钢GB8923涂装前钢板表面锈蚀等级和除锈等级JB/T4700~4707压力容器法兰JB4721外头盖侧法兰NB/T47014承压设备焊接工艺评定NB/T47015压力容器焊接规程JB/T4710钢制塔式容器NB/T47008承压设备用碳素钢和合金钢锻件JB/T4730.1~4730.6承压设备无损检测HG/T20592~20635钢制管法兰、垫片、紧固件SH/T3022石油化工设备和管道涂料防腐蚀技术规范3.总则3.1.铬钼钢压力容器应按TSG R0004-2009、GB150、设计文件以及本标准的规定制造和验收。
3.2.铬钼钢压力容器的制造和验收除执行本标准外,尚应符合设计文件、TSG R0004-2009、GB150的规定。
- 1、下载文档前请自行甄别文档内容的完整性,平台不提供额外的编辑、内容补充、找答案等附加服务。
- 2、"仅部分预览"的文档,不可在线预览部分如存在完整性等问题,可反馈申请退款(可完整预览的文档不适用该条件!)。
- 3、如文档侵犯您的权益,请联系客服反馈,我们会尽快为您处理(人工客服工作时间:9:00-18:30)。
公司标准70BJ010-2011代替:70BJ010-2005铬钼钢复合钢板制压力容器制造及验收工程技术条件第 1 页共 18 页朱玫张国信李法海陈崇刚2011-04-15 2011-04-20 编制校审标准化审核审定发布日期实施日期目 次1 范围 (1)2 规范性引用文件 (1)3 总则 (2)4 材料 (2)5 制造 (8)6 无损检测 (12)7 焊后热处理及水压试验 (13)8 涂敷和包装运输 (14)1 范围本标准规定了最高操作温度不大于440℃且壳体基层板厚不大于100mm,基层材料为15CrMoR(H)、14Cr1MoR(H)及与此相当的铬钼钢,复层为S11306、S11348、S30403、S30408、S32168、S31603、S31608及与此相当的不锈钢的铬钼钢复合钢板制压力容器在材料、制造、检验以及包装运输等方面的要求。
本标准适用于按GB 150设计的铬钼钢复合钢板制压力容器的制造及验收,不适用于按分析设计标准设计的铬钼钢复合钢板制压力容器的制造和验收。
2 规范性引用文件TSG R0004-2009 固定式压力容器安全技术监察规程GB150 钢制压力容器GB/T223 钢铁及合金化学分析方法GB/T228 金属拉伸试验方法GB/T229 金属夏比缺口冲击试验方法GB/T232 金属材料弯曲试验方法GB713 锅炉和压力容器用钢板GB985.1 气焊、焊条电弧焊、气体保护焊和高能束焊的推荐坡口GB985.2 埋弧焊的推荐坡口GB/T1184-1996 形状和位置公差未注公差值GB/T1804-2000 一般公差未注公差的线性和角度尺寸的公差GB3077 合金结构钢GB/T 4334 金属和合金的腐蚀不锈钢晶间腐蚀试验方法GB/T4338 金属材料高温拉伸试验GB/T5118 低合金钢焊条GB/T6394 金属平均晶粒度测定法GB6479 高压化肥设备用无缝钢管GB8923 涂装前钢板表面锈蚀等级和除锈等级GB9948 石油裂化用无缝钢管GB/T10561 钢中非金属夹杂物含量的测定标准评级图显微检验法GB24511 承压设备用不锈钢钢板及钢带HG/T20592 钢制管法兰(PN系列)HG/T20615 钢制管法兰(Class系列)JB/T4700 压力容器法兰分类与技术条件JB/T4707 等长双头螺柱JB4708 钢制压力容器焊接工艺评定JB/T4709-2000 钢制压力容器焊接规程JB/T4710 钢制塔式容器JB/T4711 压力容器涂敷与运输包装JB/T4730 承压设备无损检测JB/T4731 钢制卧式容器JB4744 钢制压力容器产品焊接试板的力学性能检验JB/T4747 压力容器用钢焊条订货技术条件NB/T47002.1-2009 压力容器用爆炸焊接复合板第一部分不锈钢-钢复合钢板NB/T47008 承压设备用碳素钢和低合金钢锻件NB/T 47010 承压设备用不锈钢和耐热钢锻件NB/T47013.10 承压设备无损检测第10部分:衍射时差法超声检测SH3022 石油化工设备和管道涂料防腐蚀技术规范SH3043 石油化工设备管道钢结构表面色和标志规定SH/T3074 石油化工钢制压力容器SH/T3524 石油化工静设备现场组焊技术规程SH/T3526 石油化工异种钢焊接规程SH/T3527-1999 石油化工不锈钢复合钢焊接规程ASME SA-335 Standard Specification For Seamless Ferritic Alloy-Steel Pipe For High-Temperature Service3 总则3.1 铬钼钢复合钢板制压力容器按TSG R0004-2009、GB150、JB/T4710(对塔式容器)或JB/T4731(对卧式容器)、设计文件以及本标准的规定进行制造和验收。
其技术规范优先顺序为设计文件、本标准、GB150、JB/T4710或JB/T4731。
3.2铬钼钢容器制造过程中对设计文件和本标准的任何修改均应取得洛阳石油化工工程公司的书面同意。
4 材料4.1 基层材料4.1.1 基层材料应分别符合GB150、NB/T47008(锻件)、NB/T47010(锻件)、GB713(钢板)和本标准的规定。
4.1.2 基层材料应具有材料生产厂的质量证明书,制造单位应按原材料标准、本标准所要求的项目对材料进行复验。
4.1.3 基层材料应采用电炉冶炼工艺生产的细晶粒钢,供货状态应为正火+回火。
4.1.4基层材料的的化学成分应按GB/T223规定的方法进行分析,并符合表1和表2的规定。
表1 15CrMoR(H)钢板和15CrMo锻件化学成分 (Wt%)化学元素熔炼分析成品分析S ≤0.010 ≤0.012P ≤0.012 ≤0.015Ni ≤0.20 ≤0.25Cu ≤0.20 ≤0.20表2 14Cr1MoR(H)钢板和14Cr1Mo锻件化学成分 (Wt%)化学元素熔炼分析成品分析C ≤0.17 ≤0.170.44-0.86Si 0.50-0.800.35-0.73Mn 0.40-0.65S ≤0.010 ≤0.012P ≤0.012 ≤0.015Sn ≤0.010 ≤0.010Ni ≤0.20 ≤0.25As ≤0.010 ≤0.010Sb ≤0.003 ≤0.003Cu ≤0.20 ≤0.204.1.5按下列条件模拟焊后热处理后的基层材料的力学性能应符合表3和表4的规定。
a)最大模拟焊后热处理(Max. PWHT):推荐的热处理温度为690℃±14℃(对14Cr1MoR(H)和14Cr1Mo锻件)或650℃~675℃(对15CrMoR(H)钢板和15CRMo锻件),保温时间为3倍的最小模拟焊后热处理的保温时间;b) 最小模拟焊后热处理(Min. PWHT):推荐的热处理温度为690℃±14℃(对14Cr1MoR(H)和14Cr1Mo锻件)或675℃±14℃(对15CrMoR(H)钢板和15CRMo锻件),保温时间由制造厂根据容器厚度及材料综合考虑确定。
表3 15CrMoR(H)钢板和15CrMo(H)锻件的力学性能检验项目 15CrMoR(H)钢板 15CrMo锻件抗拉强度R m,MPa450~590 450~590常温屈服度R el,MPa ≥295 ≥275符合GB713表3 符合NB47008设计温度下的屈服强度R t0.2MPa延伸率A,%≥19 ≥20截面收缩率Z,%≥45 ≥45-10℃时冲击功 kv2J≥54(三个试样平均值) ≥41(其中一个试样最低值)冷弯试验b=2a 180°d=3a硬度(HB)≤220注:a为试样厚度;b为试样宽度;d为弯棍直径表4 14Cr1MoR(H)钢板和14Cr1Mo(H)锻件的力学性能项目 14Cr1MoR(H)钢板 14Cr1Mo锻件抗拉强度R m MPa520~685 485~660常温屈服强度R el MPa ≥310 ≥290符合GB713表3 符合NB47008设计温度下的屈服强度R t0.2MPa延伸率 A % ≥19截面收缩率Z %≥40-18℃时冲击功kv2J≥54(三个试样平均值) ≥41(其中一个试样最低值) 冷弯试验 b=2a 180°d=3a注:a为试样厚度;b为试样宽度;d为弯棍直径4.1.6 15CrMo和14Cr1Mo钢锻件尚应符合下列规定:a) 锻件应按JB/T4730进行超声检测,其单个缺陷的等级为Ⅲ级,密集区缺陷及底波降低量的等级均为Ⅱ级。
b) 锻件主截面部分的锻造比不得小于3,且锻件各向锻比尽可能接近以减小锻件的各向异性。
c) 锻件尽可能锻至接近成品零件的形状和尺寸。
d) 锻件不允许存在裂纹、夹层、折叠、夹渣和白点等有害缺陷。
e) 晶粒度应符合GB/T6394的规定,晶粒度不粗于5级。
f) 非金属夹杂物按GB/T10561-2005规定的B法按评级图Ⅱ进行评定,硫化物类(A类)、氧化铝类(B类)、硅酸盐类(C类)及球状氧化物类(D类)、单颗粒球状类(Ds类)均不得大于1.5级,且应满足A+C≤2.0,B+D≤2.0,总数A+B+C+D+Ds≤4.5。
4.1.7 15CrMo, 14Cr1Mo无缝钢管应符合下列要求:a)15CrMo无缝钢管应符合GB9948(厚度≤16mm)或GB6479的规定,14Cr1Mo无缝钢管应符合ASME SA-335-P11的规定;b)15CrMo无缝钢管做-10℃夏比(V形缺口)冲击试验,14Cr1Mo无缝钢管做-18℃夏比(V形缺口)冲击试验。
冲击功不小于54J(三个试样平均值),允许其中一个试样不小于41J;c) 按JB/T4730.3规定逐根进行超声检测,符合Ⅰ级的规定;d) 钢管的硬度不大于220HBW。
4.1.8 容器制造单位应按下列要求对主体材料进行复验,复验结果应满足NB/T47008(对锻件)、GB713(对钢板)和本标准的规定:a)锻件按同冶炼炉号、相近的锻造比、同热处理工艺复验化学成分和力学性能;b)钢板按同冶炼炉号、同厚度、同热处理工艺复验化学成分和力学性能;c)壳体、封头用钢板应按JB/T4730进行100%超声检测,其合格级别应为Ⅰ级;锻件应按JB/T4730进行超声波检测,其合格级别应为Ⅰ级;d)试样的制取应符合下列要求:1)试样应从经正火+回火热处理后的锻件或钢板上制取,且该试样需经过模拟制造时热成型和热处理的加热过程以及最大或最小模拟焊后热处理;2)锻件的试样应按BN/T47008和表5的规定制取。
当采用热缓冲环或环段时,应按NB/T47008规定制取;3)钢板的试样应按表6规定制取。
表5 锻件取样部位和数量试验项目执行标准数量热处理条件常温拉伸试验GB228 按照JB4726-94 最大模拟焊后热处理高温拉伸试验GB/T4338 同上最大模拟焊后热处理夏比冲击试验-10℃(对15CrMo)、-18℃(对14Cr1Mo) GB/T229 2套,每套2组最小模拟焊后热处理1组;最大模拟焊后热处理1组化学分析GB223 同拉伸试样数量晶粒度和非金属夹杂物检测GB6394GB105611组(见注1,2)最大模拟焊后热处理注:1人孔法兰、人孔法兰盖应逐件进行力学性能试验、化学分析、晶粒度和非金属夹杂物试验。
2接管可按批(同冶炼炉罐号、相近的锻造比、同热处理炉、同热处理工艺)进行力学性能试验、化学分析、晶粒度和非金属夹杂物试验。
3记录每个冲击试样的侧向膨胀值和塑性断口的百分率。
4冲击试样缺口垂直于锻件内外表面。
表6 钢板取样部位和数量试验项目执行标准数量取样部位热处理条件常温拉伸试验GB228 2组t×t/2,从钢板两角部横向取样最大模拟焊后热处理高温拉伸试验GB/T4338 2组同上同上夏比冲击试验-10℃(对15CrMo)、-18℃(对14Cr1Mo) GB/T2292套,每套2组t×t/2,两端取样,试样缺口与钢板表面垂直最大模拟焊后热处理一组;最小模拟焊后热处理一组冷弯试验GB/T232 2组t×外表面,从钢板两端中间部位横向取样最大模拟焊后热处理化学分析GB223 2组t×t/2注:1钢板应逐张进行力学性能试验、冷弯、化学分析试验。