APQP_(福特)_elements-updated
APQP报告程序

填写要评审的零件的名称。
(如适用)10. Part Number填写被评审的零件的零件编号。
(如适用)11. Notice Level填写被评审零件的被关注等级(如适用)。
12. User Plant填写车辆将要被制造的工厂。
填写状态报告表格 (续)13. G/Y/R Status填写23个要素的状态14. Element / Activity填写问题报告的要素的编号和问题的活动报告。
15. Issue(s) for Red/Yellow Elements总结这里涉及到的和引发的风险。
16. Corrective Action / Resolution Plan填写提及问题的纠正活动的总结和纠正问题的解决计划(8D可跟踪这里可能提及问题)。
17. Timing填写问题公开日起,和何时解决,填写关闭日期。
18. Responsibility填写福特汽车公司和/或供方负责问题后续工作人员的姓名。
质量事件检查表附录B中,列出一个完整的质量事件检查表的示例,和包括23个要素检查表的Excel 文件的网站站点。
这些检查表覆盖了成功实施这些要素的基本要求,但是可能不包括。
这些检查表是用来指导如何评估你的状态。
这些检查表的要素期望是根据FPDS过程的里程碑报告分组。
阴影部分应填写适当的里程碑。
针对下一个里程碑的要求,根据需要更新以前阴影部分的里程碑。
为了便于报告,APQP状态报告表格与检查表和信息工作表相联系。
风险评估在形成小组后,每一APQP小组应尽快进行一次风险评估。
风险评估的目的是决定在APQP过程中供方、组织或项目小组必须完成那一要素。
风险评估 (续)要在风险评估中评估的要素包括:1) 质量历史l 在用的模式或代替产品有高的保修机录或运行状况不良。
l 在接受工厂(总装和冲压厂、供方工厂等等)发生频繁的质量拒收和/或冲突。
l 相似的部件或系统导致一次召回活动。
2) 供方大纲l新供方或新制造场所l 对于供方制造场所,产品或制造技术是全新的l 历史上的供方生产的业绩为差l 由于大量的新业务,供方资源变得紧张l 供方场所不是Q-1或低于Q-1证明3) 工程大纲l 新设计l 制造技术是新的工业技术l 相似的产品是导致大量设计变更而威胁项目事件进度原因l 高的产品或过程的复杂性l 由于高的可见度或功能性,产品处于战略重要地位4). 与目标相对的绩效l 设计目标(重量、材料、功能性能,等等)将难以完成l 可靠性目标将难以完成l 质量目标(保修、TGWs、废料率、返工率,等等)将难以完成l 项目时间进度被压缩l 成本目标过高5). 调整如果提出任何以上列出的关心的列表,顾客可以要求所有的 APQP 要素被完成并报告。
APQP 第三版 中文
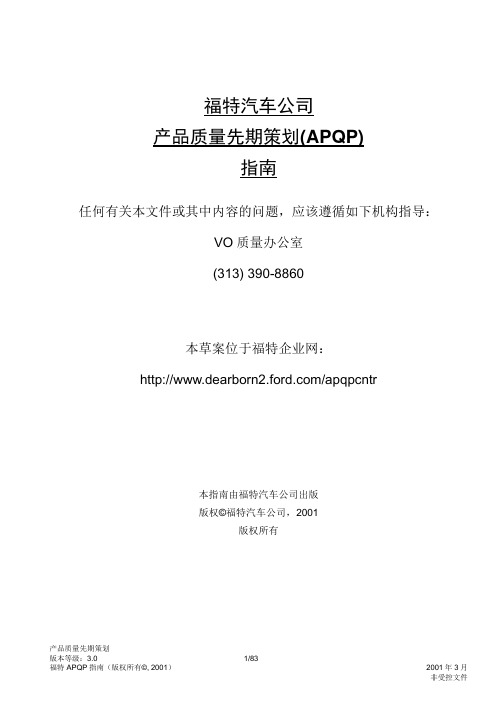
APQP 报告程序……………………………………………………………………………………10
APQP 状态报告流程图…………………………………………………………………………………11 APQP 状态报告…………………………………………………………………………………………12 APQP 状态报告表格……………………………………………………………………………………13 填写状态报告表格………………………………………………………………………………………14 质量事件检查表…………………………………………………………………………………………15 风险评估…………………………………………………………………………………………………15
产品质量先期策划
版本等级:3.0
8/83
福特 APQP 指南(版权所有©, 2001)
2001 年 3 月 非受控文件
要素(续)
最后级别的一个附加更改是两个要素的结合,“生产件批准(PSW)”和“MRD 的 PSW 零 件交付”合并为一个要素:
生产件批准程序(PPAP)/零件提交保证书(PSW)
产品质量先期策划
版本等级:3.0
3/83
福特 APQP 指南(版权所有©, 2001)
2001 年 3 月 非受控文件
目录(续)
附录部分…………………………………………………………………………………………52
APQP介绍

• Define roles and responsibilities 定義權責
• Identify external customer needs, expectations and requirements 鑑別外部客戶需求
teams plan and execute activities support common goals 確保其他小組計劃並執行支援活動
Customer Requirements 客戶要求
• Ways to Determine Customer Requirements 來源
• Print 圖面 • Purchase Request or Request for Quotation 採
展開時間及順序
• Product complexity 產品複雜性 Stamping 沖壓 Sub-assembly 組立
• New 新產品 • Modification 設變
Progressive Fundamentals 成功的基礎
• KEY** Organize a Cross-Functional TEAM 組成 跨功能小組
實驗計劃法
Specific Production Staff, Quality & Engineering, QA manager, product engineer
*Your APQP Team should attend as many classes as time will allow
Customer and Supplier Involvement 客戶及廠商的參與
目標
Continuous improvement持續改善
福特汽车-品质系统介绍(中英文)
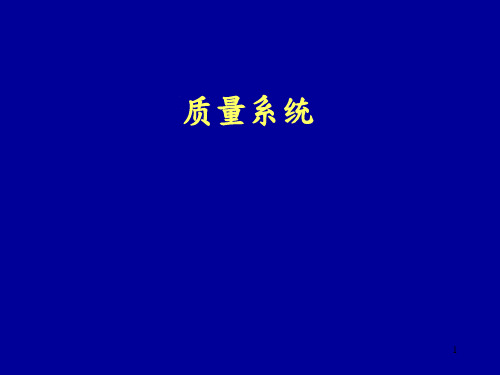
Ford Total Quality Excellence
• Sustained quality excellence requirescontinuous process improvement. This means, regardless of how good present performance may be, it can become even better. 维持卓越的质量必须持续作流程的改善
• 建置QIS(Quality Information System)系统,在生产在线 直接反应质量问题并于第一时间实时改善。
• 1994年导入顾客导向式车辆评价系统 Nova-C (New Overall Vehicle Assessment- Customer)。
• 1996年起导入QOS质量运行系统。
Achievement • 1994年获得Q1再次验证肯定。 • 1996年成为国内首家汽车业者通过ISO-9001国际标准
验证,得到世界质量系统标准的肯定。
• Quality excellence can best be achieved bypreventing problems rather than by detecting and correcting them after they occur.达成卓越的质量必须注重在问题的预防
• All work that is done by Company employees, suppliers, and dealers is part of a process that creates a product or service for a customer.Each person can influence some part of that process and, therefore,affect the quality of its output and theultimate customers’ satisfaction with our products and services. 每个公司员工对质量及最终的顾客满意都有贡献
apqp 产品质量先期策划
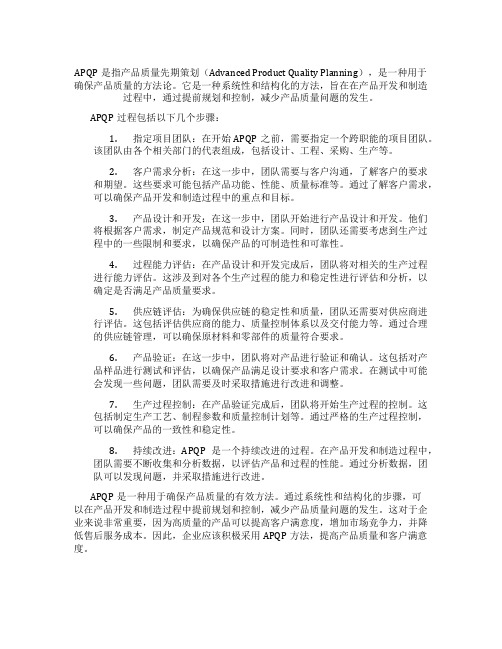
APQP是指产品质量先期策划(Advanced Product Quality Planning),是一种用于确保产品质量的方法论。
它是一种系统性和结构化的方法,旨在在产品开发和制造过程中,通过提前规划和控制,减少产品质量问题的发生。
APQP过程包括以下几个步骤:1.指定项目团队:在开始APQP之前,需要指定一个跨职能的项目团队。
该团队由各个相关部门的代表组成,包括设计、工程、采购、生产等。
2.客户需求分析:在这一步中,团队需要与客户沟通,了解客户的要求和期望。
这些要求可能包括产品功能、性能、质量标准等。
通过了解客户需求,可以确保产品开发和制造过程中的重点和目标。
3.产品设计和开发:在这一步中,团队开始进行产品设计和开发。
他们将根据客户需求,制定产品规范和设计方案。
同时,团队还需要考虑到生产过程中的一些限制和要求,以确保产品的可制造性和可靠性。
4.过程能力评估:在产品设计和开发完成后,团队将对相关的生产过程进行能力评估。
这涉及到对各个生产过程的能力和稳定性进行评估和分析,以确定是否满足产品质量要求。
5.供应链评估:为确保供应链的稳定性和质量,团队还需要对供应商进行评估。
这包括评估供应商的能力、质量控制体系以及交付能力等。
通过合理的供应链管理,可以确保原材料和零部件的质量符合要求。
6.产品验证:在这一步中,团队将对产品进行验证和确认。
这包括对产品样品进行测试和评估,以确保产品满足设计要求和客户需求。
在测试中可能会发现一些问题,团队需要及时采取措施进行改进和调整。
7.生产过程控制:在产品验证完成后,团队将开始生产过程的控制。
这包括制定生产工艺、制程参数和质量控制计划等。
通过严格的生产过程控制,可以确保产品的一致性和稳定性。
8.持续改进:APQP是一个持续改进的过程。
在产品开发和制造过程中,团队需要不断收集和分析数据,以评估产品和过程的性能。
通过分析数据,团队可以发现问题,并采取措施进行改进。
APQP是一种用于确保产品质量的有效方法。
TS16949五大工具:APQP

确定范围 产品项目的最早阶段,重要的是识别顾客的需要、期望和要 求。
选一个项目经理,负责监督策划过程。 确定每一代表方的角色和职责 确定内部和外部顾客 确定顾客的要求(适用时,使用试验设计QFD) 确定小组职能,选择加入小组的人员(包括供方) 理解顾客的期望,如设计、试验次数 对所提出的设计、性能要求和制造过程进行可行性评定 确定成本、进度和应考虑的限制条件 明确所需的来自顾客的帮助 确定文件化的过程和方法
试生产
投产
策划
产品设计和开发
策划
过程设计开发
产品与过程确认 生产
反馈、评定和纠正措施
计划和确 定项目
产品设计和 开发验证
过程设计和 开发验证
产品和过 程确认
反馈、评定 和纠正措施
19
10.APQP与防错
整个APQP的过程是采取防错措施,降低产品/服务交付到顾 客时产生问题的风险,这是APQP的核心。
3
一. 概 述
3.APQP的实施要求
ISO/TS16949要求使用多阶段策划过程,然而,它不是要 求一成不变的执行APQP方法
APQP手册应该作为一个参考。它只是一个建议的格式或 建议的途径
4.实施APQP的时机
新产品 更改的产品
4
一. 概 述
5. 产品质量策划循环
是著名的戴明PDCA质量循环概念在产品质量策划中的应用; 持续改进是PDCA循环的要点; APQP是ISO/TS16949系统中不 可或缺的重要子系统; APQP子系统中还包含其他许 多系统,如FMEA、控制计划。
福特汽车公司PPAP

美国三大汽车公司(克莱斯勒、福特、通用)从1993年2月起就为向它们提供装车生产件以及售后服务件的供方们提出了强制性的《生产件批准程序 Production Part Approval Process》要求,英文缩写PPAP。
至今《生产件批准程序》(PPAP)已是第四版。
由于存在着不同和差异,三大汽车公司在《生产件批准程序》的通用要求基础之上,还有着各自的特殊要求。
下面的简略译文是福特汽车公司生产件批准的一些特殊要求和具体做法。
福特汽车公司对生产件批准程序(PPAP)第四版的特殊要求(一)(2013年6月20日修改发布)范围生产件批准程序(PPAP )第四版适用于世界各地区福特汽车公司和合资企业。
本文件中提到的“福特”,指福特汽车公司以及合资的企业。
美国汽车工业行动集团参考文件• APQP表格磁盘• CQI-9《特殊过程:热处理系统评估》• CQI-19《AIAG 分供方管理过程指南》• 国际汽车特别工作组 ISO/TS16949《质量管理体系汽车生产件和服务件组织应用ISO9001的特别要求》•《先期产品质量策划和控制计划》参考手册•《测量系统分析》参考手册•《生产件批准程序》(PPAP).•《统计过程控制》(SPC) 参考手册福特汽车公司参考文件• 福特工程CAD和制图标准(FECDS)• 福特汽车对 CQI-9 《特殊过程:热处理系统评估》提出的特殊要求• 福特汽车FMEA手册• 福特汽车阶段PPAP手册• 特殊过程评估和要求• 福特汽车ISO/TS16949顾客特殊要求ISO国际标准化组织参考文件• ISO/IEC17025 检测和校准实验室能力的通用要求1适用性“经授权的顾客代表”是由整车厂和动力部件厂派到组织现场的供应商技术助理现场工程师(STA)。
PPAP第四版中提及的组织指的是向福特汽车公司提供生产件和服务件的外部供应商现场。
分供方则是指提供产品给组织,支持组织按照合同向福特汽车公司提供产品的供应商。
APQP_和PPAP过程专业术语

APQP_和PPAP过程专业术语第一篇:APQP_和PPAP过程专业术语APQP 和PPAP过程专业术语(红色—重点注释;艳红色—评估中;蓝色—新增)DELPHI:在流程图的检验栏有以下四种注释:A = Automatic, or machine inspected(i.e.leak tester)A代表自动检测或仪器检测(比如耐压、通断、针高等);M = Manually inspected by the operator(i.e.hand gage)M代表操作工手动检测(比如工人用检测板进行针位检测);V = Visually inspected by the operator V代表操作工目视检测(比如外观检测); Q = Quality Audit, control plan check Q代表品质监控(比如IQC、OQC、IPQC、SPC控制等)Appearance Approval Report 外观批准报告AAR ADV ADV-DV Analysis/Development/Validation 分析/开发/验证 ADV Design Validation A D V 设计验证Analysis/Development/Validation Plan and Report, This from is used to summarizeA/D/V P&R the plan and results for validation testing.Additional information Can be found in the GP-11procedure.分析/开发/验证计划和报告Additional Engineering Changes 附加工程更改AEC ADV-PV ADV product Validation A D V产品验证Automotive Industries Action Group, an organization formed by General Motors,AIAG AP APO APQP AQE ASQE ANOVA ASDE BOM BOP CCAR Ford and Daimler Chrysler to develop common standards and expectations for automotive suppliers.汽车工业行动集团 Advanced Purchasing 先期采购(General Motors)Asian Pacific Operations(通用)亚太分部Advanced Product Quality Planning 产品质量先期策划 Advanced Quality Engineer 先期质量工程师Advanced Supplier Quality Engineer 先期供应商质量工程师Analysis of Variance方差分析法Advanced Supplier Development Engineer 高级供应商开发工程师 Bill of Materials 材料清单 Bill of Process 过程清单Concerned and Corrective Action Report 相关整改报告Corrective Action Request 整改需求 Cross function Team 多方论证小组Coordinate Measuring Machine三坐标测试仪Weekly Production Volume 周产能Capability Index for a Stabile process 过程能力指数 Customer Requirements 客户要求 Commodity Manager 产品经理Corporate Commodity Manager 公司产品经理Customer Satisfaction 客户满意度Level 1/2 Controlled Shipping 1/2级受控发运Component Technical Specifications 零件技术规范Dimension Control Plan(Dynamic Control Plan)尺寸控制计划(动态控制计划)Design of Experiment试验设计Daily Production Volume 日产量CAR CFT CMM CPV CPK CR CM CCM CS CS 1/2 CTS DCP DOE DPV DFM/DFA Design for Manufacturability/Design for Assembly 可制造性/可装配性设计DVP&R DV DRE DFMEA EWO EDI FE1,2,3 ES EPC FAI FCR FE FTA FTC FTQ Design Validation Plan and Report 设计验证计划和报告 Design Validation 设计验证Design Release Engineer设计发放工程师Design Failure Mode and Effects Analysis设计失效模式及后果分析Engineering Work Order 工程更改指令Electronic Data Interchange 电子数据交换 Functional Evaluations1,2,and 3 功能评估 Engineering Specification工程规范Early Production Containment 早期生产遏制First Article Inspection 首件检验 Field Call of Rate Function Evaluation 功能评估 Failure Tree Analysis 故障树状分析 First Time Capability 试生产能力 First Time Quality 直通率(一次合格率)Gage Repeatability and Reproducibility 量具的重复性与再现性Geometric Dimensioning & Tolerancing 几何尺寸&公差General Motors 通用汽车公司General Motors Europe 通用汽车欧洲部分 General Procedure 总体步骤Global Product Description System 全球产品描述系统 Global Purchasing System 全球采购系统Global Quality Tracking System 全球质量跟踪系统Global Vehicle Development Process 全球车辆开发过程initial Sample Inspection Report 首次样品检验报告Incidents per Thousand Vehicles 每千辆车缺陷数 Interim Approval Authorization 临时批准授权Integral Corrective Action List 整体整改列表ICRInterface Change Request Lower Control Limit 控制下限Lower Specification Limit工程规范下限Key Control Characteristic 关键控制特性Key Characteristics Designation System 关键特性指示系统(GM)Key Product Characteristic关键产品特性(General Motors)Latin American Operations(通用)拉丁美洲分部 Lean Capacity Rate, It is the GM daily capacity requirement 最低生产能力Maximum Capacity Rate, It is the GM maximum capacity requirement 最大生产能力 Modified Production Part(Nissan Form)改良生产零件 Make or Purchase 制造/采购Manufacturing / Materials Resource Planning 加工/物料资源计划Material Reject Report 物料拒收报告Material Production Control 物料生产控制Material Production Control Europe 欧洲物料生产控制Material Review Board物料评审 Material Required Date 物料需求日期GR&R GD&T GM GME GP GPDS GPS GQTS GVDP ISIR IPTV IAA ICAL LCL LSL KCC KCDS KPC LAO LCR MCR MPP MOP MRP MRR MPC MPCE MRB MRD MSA NAO NCC NBH NDA/O N.O.D OEE OEM OTS PPAP PAD PC&L PSW PDT PFMEA PPM PSA PPK PFC PQC PFD PTC PTRPVP&R PR/R PV PRR QSA QSA QSR QTC QFD QOS QRR@R RASIC RFQ RPN RCM SCIF SC SCR Measurement Systems Analysis 测量系统分析(General Motors)North American Operations(通用)北美分部Non Conformity Cost不良品成本New Business Hold 停止新业务Non Disclosure Agreement/Obligation保密协议/和约Notice of Decision 决议通知Operating Equipment Effectiveness 操作装置效率Original Equipment Manufacturer原始设备制造商(整车厂)Off Tooling Sample 正式工装/模具生产样品Production Part Approval Process 生产件批准程序Production Assembly Documents 生产装配文件Production Control & Logistics 生产控制&物流Part Submission Warrant 零件提交保证书Product Development Team 项目开发组Process Failure Modes and Effects Analysis 过程失效模式及后果分析Parts per Million 每百万PPEIPlatform to Powertrain Electrical Interface Potential Supplier Assessment 潜在供应商评审Performance index for a stable process 初试过程能力指数Process Flow Chart 过程流程图Product Quality Characteristic 产品质量特性Process Flow Diagram 过程流程图Pass Through Characteristic 过程特性Production Trial Run 生产试行Production Validation Plan and Report 产品验证计划与报告Problem Reporting & Resolution 问题报告及决策Production Validation 生产产品验证Problem Resolution Report 问题决策报告Quality System Assessment 质量系统评审Quality System Base 质量体系基础Quality System Requirement质量体系要求Quotes Tool Capacity 工装报价能力Quality Function Deployment质量功能展开Quality Operating System 质量运行体系Quality Reject/Report 质量拒收/报告Run at Rate 产能审核(产能审核指的是按照正常的生产状态进行审核,其中包括人员,设备,工装,材料和工艺。
- 1、下载文档前请自行甄别文档内容的完整性,平台不提供额外的编辑、内容补充、找答案等附加服务。
- 2、"仅部分预览"的文档,不可在线预览部分如存在完整性等问题,可反馈申请退款(可完整预览的文档不适用该条件!)。
- 3、如文档侵犯您的权益,请联系客服反馈,我们会尽快为您处理(人工客服工作时间:9:00-18:30)。
APQP Status Repo rting Pro cess
Module Introduction 组成部分介绍
Introduction to the APQP Process APQP过程介绍
APQP Status Repo rting Pro cess
18 包装规范
19 产品试生产 20 生产控制计划 21 初始过程能力研究 22 生产确认试验 23 生产件批准 (PSW)
APQP Status Repo rting Pro cess
福特四项特殊要素
1. Sourcing Decision 选点决定 ; 2. Customer Input Requirements 顾客输入要求 ; 3. Craftsmanship 精致工艺; 4. Subcontractor APQP Status 分承包方APQP状态 ;
Course Introduction
APQP Status Reporting Process APQP 状态报告程序
APQP Status Repo rting Pro cess
Participant Introductions
Write your name and division on a name tent card with the markers provided. 在纸上写下你的姓名部门. Prepare to introduce yourself to the class by sharing: 向课堂上的所有人介绍: Your name 你的名字 Your title 你的职称 Why you are interested in the APQP course 你为什对APQP课程感兴趣 Your interest 你的日常兴趣爱好
APQP Status Repo rting Pro cess
16
Plan & Define 计划与定义
Product Design & Development 产品设计和开发
Prototype Build 样件制造
Process Design & Development 过程设计和开发
Product & Process Validation 产品与过程确认
Vehicle Scaleability
S1 - Modifications to trim, e.g., new seat sew style modifications only for seats or insert material changes for interior appliqués.
APQP Status Repo rting Pro cess
APQP Benefits
APQP aids the program team by: APQP帮助项目小组:
Adding discipline 增加纪律 Facilitating early identification of required changes 早期确定可能的更改 Avoiding late changes 避免晚期更改 Providing a quality product on time, at acceptable cost, to satisfy customers 用可接受的价格,准时提供优质的产品,满足客户 Facilitating continuous improvement 使持续改进更方便
APQP Status Repo rting Pro cess
1-4
Module Introduction
FPDS Timing Relationship and Responsibilities FPDS 时间进度
关系和职责
APQP Status Repo rting Pro cess
Scaleability
APQP Status Repo rting Pro cess
APQP Benefits (Cont’d)
Elements 要素
Teamwork 小组工作 Communication 沟通 Timing/Planning 时间/计划 Identify Activities 定义行动
Roles 角色
1-1
Ford Initiatives
APQP Status Repo rting Pro cess
Definition APQP (Advanced Product Quality Planning) is a structured method for defining and executing the actions necessary to ensure that a product satisfies the customer. APQP是一种结构化的方法,用来确定 和制定确保某产品使顾客满意所需的 步骤
S2 - Minor freshening, e.g., new seat pads, lamp decoration with carryover tooling, optics.
Manufacturing Scaleability
M1 - Carry-over engine/transmission with minor calibration revisions to, i.e., no machining changes, very minor assembly revisions, and no plant facilities/infrastructure revisions.
APQP 23个要素
1 选点决定 2 顾客输入要求 12 小组可行性承诺
13 制造过程流程图 14 过程失效模式后果分析 15 测量系统评价 16 试生产控制计划 17 操作工过程指导书
3 精致工艺技术
4 设计失效模式后果分析 5 设计评审 6 设计验证计划 7 分承包方 APQP 状态 8 设施、工具和量具 9 样件制造计划 10 样件制造 11 图纸和规范
APQP Status Repo rting Pro cess
FPDS
Months before Job 1 for S1 to S6 programs S1-S6项目在Job 1之前的时间节点
APQP Status Repo rting Pro cess
FPDS Online Resources
Feedback Assessment & Corrective Action 反馈、评估和纠正措施
APQP Status Repo rting Pro cess
1-2
APQP 指南目的
Includes best practice APQP evaluation process, process metrics, and status reporting Links the APQP process to Product Development and manufacturing processes 把APQP过程与产品开发和制造过程相联系。 Defines roles and responsibilities for the APQP process 定义APQP过程的角色和职责 Develops a common APQP process for both internal and external manufacturing and assembly suppliers 为内部制造和外部供应商提供一个通用的开发过程
APQP Status Repo rting Pro cess
Accessing the APQP Guidelines 访问 APQP 指南
Both the Guideline and the forms are available. 指南和表格均可由此获得。
/apqp
APQP Status Repo rting Pro cess
检查清单中的重要要素
Design FMEA 设计FMEA Design Verification Plan & Report 设计验证计划和报告 Prototype Build Control Plan 样件制造控制计划 Manufacturing Process Flowchart 制造过程流程图 Process FMEA 过程FMEA Pre-Launch Control Plan 试生产控制计划 Operator Process Instructions 作业指导书 Production Control Plan 生产控制计划
APQP Status Repo rting Pro cess
Goal
The goal of the APQP process is to facilitate communication between all persons and activities involved in a program and ensure that all required steps are completed on time, with a high quality-of-event, at acceptable cost and quality levels. APQP的目的是使所有参加该项目的人员和 行为便于沟通,确保所有开发阶段按时,以 可接受的成本和质量水准完成.
APQP Status Repo rting Pro cess
APQP Purpose
The purpose if the APQP process is to establish: APQP的目的是建立:
Common expectations for internal and external suppliers 对内外部供应商共同的要求 Common process metrics 通用的过程表格 A common program status reporting format 共同的状态报告格式 Roles and responsibilities for the APQP elements APQP各要素的职责和角色 A better understanding of how the APQP elements relate to FPDS 更好理解APQP各要素和 FPDS的联系