回流焊工艺流程和自动焊接中炉温测控技术
SMT回流焊工艺温控技术分析
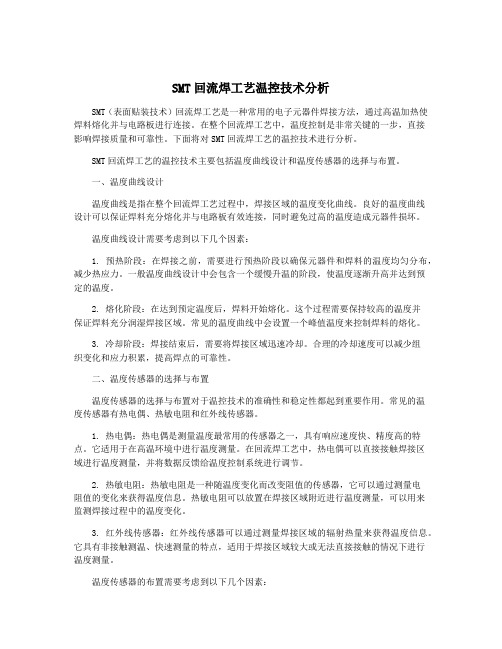
SMT回流焊工艺温控技术分析SMT(表面贴装技术)回流焊工艺是一种常用的电子元器件焊接方法,通过高温加热使焊料熔化并与电路板进行连接。
在整个回流焊工艺中,温度控制是非常关键的一步,直接影响焊接质量和可靠性。
下面将对SMT回流焊工艺的温控技术进行分析。
SMT回流焊工艺的温控技术主要包括温度曲线设计和温度传感器的选择与布置。
一、温度曲线设计温度曲线是指在整个回流焊工艺过程中,焊接区域的温度变化曲线。
良好的温度曲线设计可以保证焊料充分熔化并与电路板有效连接,同时避免过高的温度造成元器件损坏。
温度曲线设计需要考虑到以下几个因素:1. 预热阶段:在焊接之前,需要进行预热阶段以确保元器件和焊料的温度均匀分布,减少热应力。
一般温度曲线设计中会包含一个缓慢升温的阶段,使温度逐渐升高并达到预定的温度。
2. 熔化阶段:在达到预定温度后,焊料开始熔化。
这个过程需要保持较高的温度并保证焊料充分润湿焊接区域。
常见的温度曲线中会设置一个峰值温度来控制焊料的熔化。
3. 冷却阶段:焊接结束后,需要将焊接区域迅速冷却。
合理的冷却速度可以减少组织变化和应力积累,提高焊点的可靠性。
二、温度传感器的选择与布置温度传感器的选择与布置对于温控技术的准确性和稳定性都起到重要作用。
常见的温度传感器有热电偶、热敏电阻和红外线传感器。
1. 热电偶:热电偶是测量温度最常用的传感器之一,具有响应速度快、精度高的特点。
它适用于在高温环境中进行温度测量。
在回流焊工艺中,热电偶可以直接接触焊接区域进行温度测量,并将数据反馈给温度控制系统进行调节。
2. 热敏电阻:热敏电阻是一种随温度变化而改变阻值的传感器,它可以通过测量电阻值的变化来获得温度信息。
热敏电阻可以放置在焊接区域附近进行温度测量,可以用来监测焊接过程中的温度变化。
3. 红外线传感器:红外线传感器可以通过测量焊接区域的辐射热量来获得温度信息。
它具有非接触测温、快速测量的特点,适用于焊接区域较大或无法直接接触的情况下进行温度测量。
回流焊过程
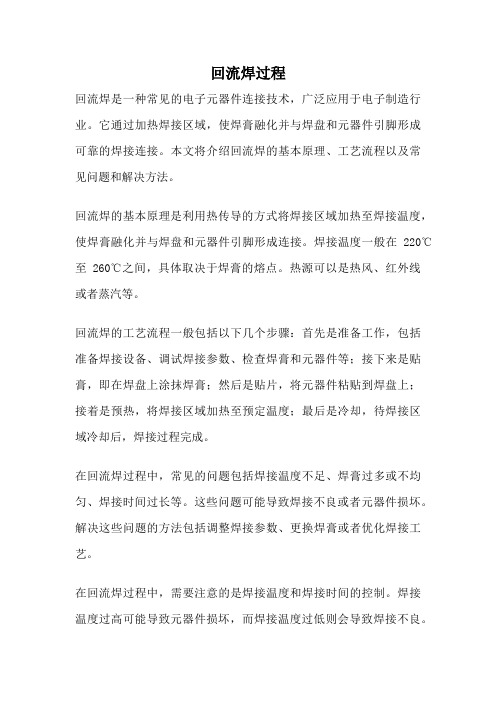
回流焊过程回流焊是一种常见的电子元器件连接技术,广泛应用于电子制造行业。
它通过加热焊接区域,使焊膏融化并与焊盘和元器件引脚形成可靠的焊接连接。
本文将介绍回流焊的基本原理、工艺流程以及常见问题和解决方法。
回流焊的基本原理是利用热传导的方式将焊接区域加热至焊接温度,使焊膏融化并与焊盘和元器件引脚形成连接。
焊接温度一般在220℃至260℃之间,具体取决于焊膏的熔点。
热源可以是热风、红外线或者蒸汽等。
回流焊的工艺流程一般包括以下几个步骤:首先是准备工作,包括准备焊接设备、调试焊接参数、检查焊膏和元器件等;接下来是贴膏,即在焊盘上涂抹焊膏;然后是贴片,将元器件粘贴到焊盘上;接着是预热,将焊接区域加热至预定温度;最后是冷却,待焊接区域冷却后,焊接过程完成。
在回流焊过程中,常见的问题包括焊接温度不足、焊膏过多或不均匀、焊接时间过长等。
这些问题可能导致焊接不良或者元器件损坏。
解决这些问题的方法包括调整焊接参数、更换焊膏或者优化焊接工艺。
在回流焊过程中,需要注意的是焊接温度和焊接时间的控制。
焊接温度过高可能导致元器件损坏,而焊接温度过低则会导致焊接不良。
焊接时间过长可能导致焊盘和元器件引脚受热过多,从而影响焊接质量。
因此,合理设置焊接温度和焊接时间是确保焊接质量的关键。
回流焊作为一种高效、可靠的焊接技术,被广泛应用于电子制造行业。
它不仅可以提高焊接质量和效率,还可以减少人工操作,降低生产成本。
然而,回流焊也存在一些局限性,例如对元器件和焊膏的要求较高,对焊接设备和工艺的控制要求严格等。
因此,在进行回流焊时,需要根据具体情况选择合适的焊接参数和工艺,以确保焊接质量和稳定性。
回流焊是一种重要的电子元器件连接技术,具有广泛的应用前景。
通过合理设置焊接参数和工艺,可以实现高质量、高效率的焊接。
然而,在实际应用中,仍需注意焊接温度和焊接时间的控制,以及解决常见问题和提高工艺稳定性。
只有不断改进和优化回流焊技术,才能更好地满足电子制造行业的需求。
回流焊操作工艺规程
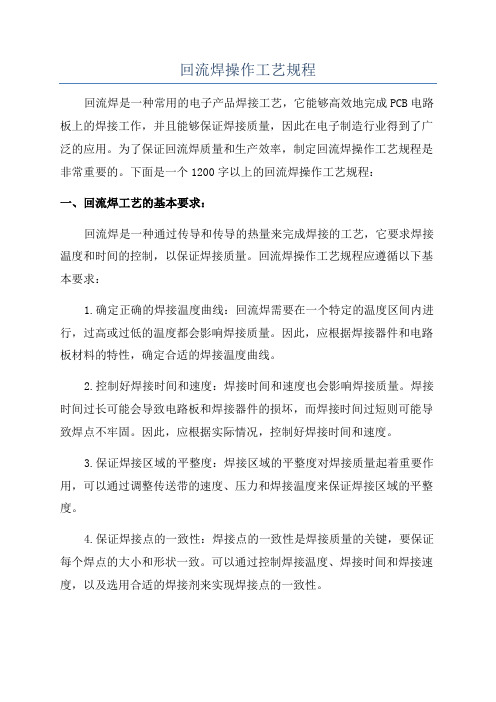
回流焊操作工艺规程回流焊是一种常用的电子产品焊接工艺,它能够高效地完成PCB电路板上的焊接工作,并且能够保证焊接质量,因此在电子制造行业得到了广泛的应用。
为了保证回流焊质量和生产效率,制定回流焊操作工艺规程是非常重要的。
下面是一个1200字以上的回流焊操作工艺规程:一、回流焊工艺的基本要求:回流焊是一种通过传导和传导的热量来完成焊接的工艺,它要求焊接温度和时间的控制,以保证焊接质量。
回流焊操作工艺规程应遵循以下基本要求:1.确定正确的焊接温度曲线:回流焊需要在一个特定的温度区间内进行,过高或过低的温度都会影响焊接质量。
因此,应根据焊接器件和电路板材料的特性,确定合适的焊接温度曲线。
2.控制好焊接时间和速度:焊接时间和速度也会影响焊接质量。
焊接时间过长可能会导致电路板和焊接器件的损坏,而焊接时间过短则可能导致焊点不牢固。
因此,应根据实际情况,控制好焊接时间和速度。
3.保证焊接区域的平整度:焊接区域的平整度对焊接质量起着重要作用,可以通过调整传送带的速度、压力和焊接温度来保证焊接区域的平整度。
4.保证焊接点的一致性:焊接点的一致性是焊接质量的关键,要保证每个焊点的大小和形状一致。
可以通过控制焊接温度、焊接时间和焊接速度,以及选用合适的焊接剂来实现焊接点的一致性。
5.做好焊后检测和维护:焊后检测是确保焊接质量的关键,应定期对焊接点进行可视检查和电性测试,以发现焊接质量问题并及时解决。
同时,要定期对焊接设备进行维护,保持设备的良好状态。
二、回流焊操作工艺规程的制定:为了保证回流焊质量和生产效率,需要制定一套完整的回流焊操作工艺规程。
下面是一套可以参考的回流焊操作工艺规程:1.准备工作a.确定焊接温度曲线:根据焊接器件和电路板材料的特性,确定合适的焊接温度曲线。
b.设置传送带速度:根据焊接区域的大小和焊接时间要求,设置合适的传送带速度。
c.检查回流焊设备:确保焊接设备的工作状态良好,如传送带的运行平稳、加热区域的加热元件正常工作等。
回流焊接工艺[1]
![回流焊接工艺[1]](https://img.taocdn.com/s3/m/e5c53c8dee06eff9aef807b8.png)
预防对策
1 减薄模板厚度或缩小开口尺寸或改 变开口形状 ; 2 调整模板与印制板表面之间距离, 使接触并平行。
严格来料检验制度,把问题反映给 PCB设计人员及PCB加工厂;对已经 加工好PCB的焊盘上如有丝网、字符 可用小刀轻轻刮掉;如印制板受潮或 污染,贴装前应清洗并烘干。
PPT文档演模板
回流焊接工艺[1]
调整温度曲线,提高峰值温度或 延长回流时间。
15. 焊锡裂纹
焊锡裂纹原因分析
峰值温度过高,焊点突然冷却, 由 于击冷造成热应力过大。 在 焊料与焊盘或元件焊端交接处容 易产生裂纹。
①加工合格模板。
②调整模板与印制板表面之间距离, 使接触并平行。
f 刮刀压力过大、造 成焊膏图 形粘 严格控制印刷工艺,保证印刷质量。 连;模板底面污染,粘污焊盘以外的 地方,
g 贴片压力过大,焊膏挤出量过多, 提高贴片头Z轴高度,减小贴片压力。 使图形粘连。
PPT文档演模板
回流焊接工艺[1]
7. 气孔
PPT文档演模板
回流焊接工艺[1]
8. 焊点高度接触或超过元件体
焊点过高原因分析
a. 焊锡量过多:可能由于模板厚度与开 口尺寸不恰当;模板与印制板表面不平 行或有间隙。
b. PCB加工质量问题或焊盘氧化、污染 (有丝网、字符、阻焊膜或氧化等),或 PCB受潮。焊料熔融时由于PCB焊盘润湿 不良,在表面 张力的作用下,使焊料向 元件焊端或引脚上 吸附(又称吸料现 象)。另一种解释,由于引脚温度比焊 盘处温度高,熔融焊料容易向高温处流 动。
e 印刷工艺——两个焊盘上的焊膏量不一 清除模板漏孔中的焊膏,印刷时经常 擦洗
致
模板底面。如开口过小,应扩大开口尺寸。
f 传送带震动会造成元器件位置移动。 g 风量过大 。
回流焊工作流程
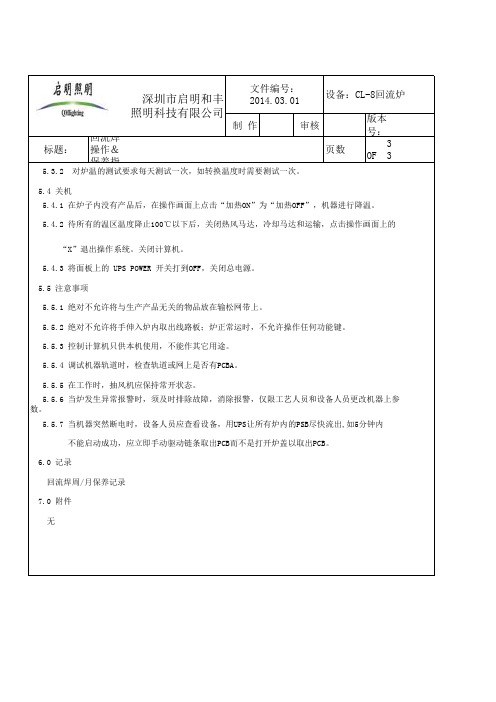
制 作 审核版本号:标题:回流焊操作&保养指示页数 3 OF 3
深圳市启明和丰照明科技有限公司
文件编号:2014.03.01设备:CL-8回流炉
5.5.6 当炉发生异常报警时,须及时排除故障,消除报警,仅限工艺人员和设备人员更改机器上参数。
5.3.2 对炉温的测试要求每天测试一次,如转换温度时需要测试一次。
5.4 关机
5.4.1 在炉子内没有产品后,在操作画面上点击“加热ON”为“加热OFF”,机器进行降温。
5.4.2 待所有的温区温度降止100℃以下后,关闭热风马达,冷却马达和运输,点击操作画面上的 5.4.3 将面板上的 UPS POWER 开关打到OFF,关闭总电源。
“X”退出操作系统。
关闭计算机。
不能启动成功,应立即手动驱动链条取出PCB而不是打开炉盖以取出PCB。
6.0 记录
回流焊周/月保养记录
7.0 附件
无 5.5.7 当机器突然断电时,设备人员应查看设备,用UPS让所有炉内的PSB尽快流出,如5分钟内 5.5 注意事项
5.5.1 绝对不允许将与生产产品无关的物品放在输松网带上。
5.5.2 绝对不允许将手伸入炉内取出线路板;炉正常运时,不允许操作任何功能键。
5.5.3 控制计算机只供本机使用,不能作其它用途。
5.5.4 调试机器轨道时,检查轨道或网上是否有PCBA。
5.5.5 在工作时,抽风机应保持常开状态。
回流焊接技术的工艺要点参考炉温曲线调整13页
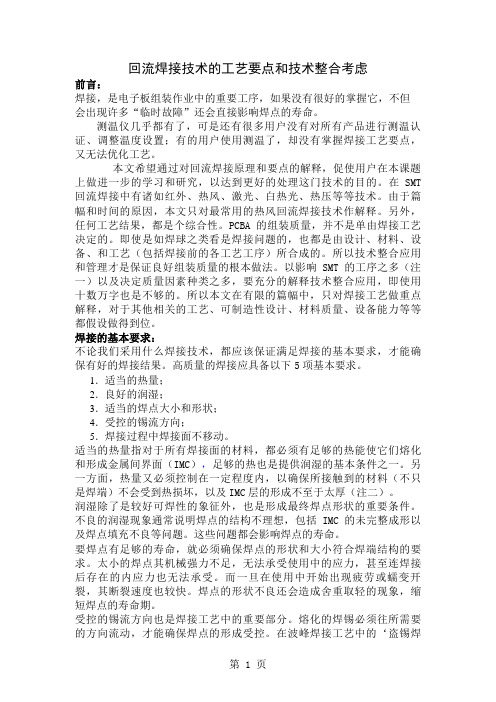
回流焊接技术的工艺要点和技术整合考虑前言:焊接,是电子板组装作业中的重要工序,如果没有很好的掌握它,不但会出现许多“临时故障”还会直接影响焊点的寿命。
测温仪几乎都有了,可是还有很多用户没有对所有产品进行测温认证、调整温度设置;有的用户使用测温了,却没有掌握焊接工艺要点,又无法优化工艺。
本文希望通过对回流焊接原理和要点的解释,促使用户在本课题上做进一步的学习和研究,以达到更好的处理这门技术的目的。
在SMT 回流焊接中有诸如红外、热风、激光、白热光、热压等等技术。
由于篇幅和时间的原因,本文只对最常用的热风回流焊接技术作解释。
另外,任何工艺结果,都是个综合性。
PCBA的组装质量,并不是单由焊接工艺决定的。
即使是如焊球之类看是焊接问题的,也都是由设计、材料、设备、和工艺(包括焊接前的各工艺工序)所合成的。
所以技术整合应用和管理才是保证良好组装质量的根本做法。
以影响SMT的工序之多(注一)以及决定质量因素种类之多,要充分的解释技术整合应用,即使用十数万字也是不够的。
所以本文在有限的篇幅中,只对焊接工艺做重点解释,对于其他相关的工艺、可制造性设计、材料质量、设备能力等等都假设做得到位。
焊接的基本要求:不论我们采用什么焊接技术,都应该保证满足焊接的基本要求,才能确保有好的焊接结果。
高质量的焊接应具备以下5项基本要求。
1.适当的热量;2.良好的润湿;3.适当的焊点大小和形状;4.受控的锡流方向;5.焊接过程中焊接面不移动。
适当的热量指对于所有焊接面的材料,都必须有足够的热能使它们熔化和形成金属间界面(IMC),足够的热也是提供润湿的基本条件之一。
另一方面,热量又必须控制在一定程度内,以确保所接触到的材料(不只是焊端)不会受到热损坏,以及IMC层的形成不至于太厚(注二)。
润湿除了是较好可焊性的象征外,也是形成最终焊点形状的重要条件。
不良的润湿现象通常说明焊点的结构不理想,包括IMC的未完整成形以及焊点填充不良等问题。
回流焊工艺流程和自动焊接中炉温测控技术
结
束
1,交习题, 交实验报 告。
2,准备专题 实验并提 交报告。
3,留下对本 课程的意 见。
● 其它工艺的影响:如PCB板上焊盘和绿色绝缘油漆交 界面内容易腐蚀变窄问题。
●为了节省能源,为了节约占地空间,在生产规模不大的 场合,一种小型回流焊炉出现了。
●被焊接板子在炉内不动,让炉子具有温控曲线的变化规 律,利用时间换取大型炉内走一次的焊接经过。
●具有适时的温度检测和曲线描绘能力,具有数据存储记 录和分析功能,使产品量产中的质量控制和事故追踪变 成可能。
炉内温升机构(动画请双击图标)
可靠焊接的炉温曲线
理想焊接温度曲线是所便用焊膏厂所推荐的。
传统的炉温测量与调控
• 带尾巴的监测系统 选一块PCB板,并在板上焊接位置安放热电偶,
通过专用导线引到炉外的测量电路,测量电路 在炉外与计算机相连。
PCB板及板上热电偶从炉子这头进,那头出, 一旦板子从炉中出来,还要迅速从原路退回去, 防止拉断线缆。板子经过各温区的实测温度都 会被采集记录出来。
回流焊接工艺流程中的数控技术 的应用(动画请双击图标)
锡膏印刷机动作/贴片机动作/回流焊炉
印刷机将焊膏准确印到各要焊接 的焊盘上
• 焊锡丝变成焊膏,PCB基板上对应的焊盘 上要均匀涂印上一层焊膏,是通过专门 镂空的薄膜板向印刷电路板上的对应焊 盘刮印上焊膏的。
• 它要求定位精度要高 (X-Y两个方向), 速度要快。
13、He who seize the right moment, is the right man.谁把握机遇,谁就心想事成。21.6.1221.6.1 215:41:1215:41 :12Jun e 12, 2021
回流焊炉温测试通用工艺
《回流焊炉温测试通用工艺》焊接:A类设置:包括单面回流焊产品,双面回流焊第一面、双面(一面焊膏、另一面胶水)的焊膏面(带BGA产品不在此类);B类设置:包括普通双面回流焊的第二面;C类设置:包括所有带BGA的产品;手机设置:289、389、802手机主板。
回流焊的温度曲线分为以下几段:预热、保温干燥、焊接。
预热是为了使元器件在焊接时所受的热冲击最小。
元器件一般能忍受的温度变化速率为4℃/SEC 以下,因此预热阶段升温速率一般控制在1℃/SEC~3℃/SEC,同时温升太快会造成焊料溅出。
保温干燥是为了保证焊料助焊剂完全干燥,同时助焊剂对焊接面的氧化物去除,起活化作用。
回流焊接区,锡膏开始融化并呈流动状态,一般要超过熔点温度20℃才能保证焊接质量。
为了保证呈流动状态的焊料可润湿整个焊盘以及元器件的引出端,要求焊料呈熔融状态的时间为40~90秒,这也是决定是否产生虚焊和假焊的重要因素。
胶水固化:对于对于LOCTITE3513红胶的温度曲线要求(Underfill):回流焊是SMT最后一个关键工序,是一个实时过程控制,其过程变化比较复杂,涉及许多工艺参数,其中温度曲线的设置最为重要,直接决定回流焊接质量。
公司生产线均采用强迫对流热风回流炉(Hot-air reflow oven),其热特性改变相对较小,同时采用免清洗焊膏Qualitek delta(sn/pb比例63/37),能必较完美完成公司现有PCB低密度产品回流焊接,高密度PCB板则须特别控制。
现在我们对回流炉管制的具体操作是检查回流炉各温区温度,定期测量温度曲线,以检验回流炉是否被控制在正常壮态,是否达到焊膏及胶水推荐温度曲线,同时检查温度的均匀性。
但是,公司PCB组装上大量使用BGA、PLCC、FINE PITCH 等元件,加上PCB材料、尺寸、元件布置、可焊性的不同,其传热程度、温度曲线和回流炉温度设置必然有差别。
必须对不同类型PCB作温度曲线测量。
回流焊工艺流程
回流焊工艺流程一、引言回流焊是现代电子制造中常用的一种焊接工艺,该工艺能够高效、可靠地连接电子器件和电路板。
本文将详细介绍回流焊工艺流程,包括焊接设备的准备、焊接参数的设定、焊接过程的控制等内容。
二、焊接设备准备在进行回流焊之前,需要准备以下设备: 1. 回流焊机:选择合适的回流焊机,确保其具备稳定的温度控制和精准的时间控制能力。
2. 焊接台:准备一个稳定的工作台,以便安装和固定电路板。
3. 胶水:使用胶水将电路板固定在焊接台上,以防在焊接过程中移动或晃动。
三、焊接参数设定在进行回流焊之前,需要对焊接参数进行设定,以确保焊接质量和稳定性。
常见的焊接参数包括: 1. 温度曲线:根据焊接材料和组件的要求,设计适当的温度曲线。
温度曲线通常包括预热阶段、温升阶段、保温阶段和冷却阶段。
2. 焊接时间:根据焊接材料和组件的要求,确定适当的焊接时间。
过短的焊接时间可能导致焊点与电路板之间的接触不良,而过长的焊接时间可能导致焊点过热或焊接材料溶解。
3. 焊接速度:根据焊接材料和组件的要求,确定适当的焊接速度。
过快的焊接速度可能导致焊接不充分,而过慢的焊接速度可能导致焊点过热或焊接材料溶解。
4. 回流区域控制:确保回流焊区域的温度均匀分布,避免焊点温度过高或过低。
四、回流焊工艺流程回流焊的工艺流程通常包括以下几个步骤: 1. 装配准备:将需要焊接的电子器件和电路板准备好,确保其表面没有杂物和氧化物。
2. 固定电路板:使用胶水将电路板固定在焊接台上,以防在焊接过程中移动或晃动。
3. 调整焊接参数:根据焊接要求和焊接材料,设定合适的焊接温度、焊接时间和焊接速度。
4. 开始焊接:将固定好的电路板放入回流焊机中,启动焊接过程。
焊接过程中,回流焊机将根据设定的温度曲线控制加热和冷却过程,实现焊接的同时不损坏电子器件。
5. 焊接检测:焊接完成后,对焊接质量进行检测。
常见的检测方法包括目视检查、X射线检测和拉力测试等。
回流焊工艺流程
回流焊工艺流程
《回流焊工艺流程》
回流焊是一种常用的电子元器件焊接工艺,通过将PCB板上
的元器件和焊膏预先装配在一起,然后通过回流焊炉进行加热并使焊膏熔化,从而实现元器件与PCB板的连接。
回流焊工
艺流程是一个复杂的过程,需要严格的操作规范和技术要求。
首先,在回流焊工艺流程中,需要对焊接材料进行选择和准备。
焊料的选择需要考虑到元器件的种类和PCB板的特性,以确
保焊接效果和质量。
在准备焊料时,需要注意控制焊料的温度和稳定性,以免影响焊接效果。
其次,回流焊工艺流程中需要进行元器件的贴装和预热。
在贴装过程中,需要根据元器件的尺寸和特性进行合理的排布和定位,以确保元器件能够正确地连接到PCB板上。
而在预热过
程中,则需要控制加热温度和时间,以确保元器件和焊料能够充分融合。
接下来,回流焊工艺流程中的关键步骤是回流焊。
在回流焊过程中,需要控制好加热温度和速度,以确保焊料能够均匀熔化并与元器件和PCB板完全连接。
此外,还需要注意避免过高
的温度和过长的加热时间,以免影响元器件和PCB板的性能。
最后,在回流焊工艺流程中,需要对焊接后的元器件和PCB
板进行冷却和检验。
冷却过程中,需要保持环境温度的稳定,以确保焊料的结构和性能。
而在检验过程中,则需要对焊接点
和焊料进行检查,以确保焊接效果和质量。
总之,回流焊工艺流程是一个十分重要且复杂的工艺过程,需要严格按照操作规范和技术要求进行操作。
只有这样,才能够确保焊接效果和质量,同时提高生产效率和产品性能。
- 1、下载文档前请自行甄别文档内容的完整性,平台不提供额外的编辑、内容补充、找答案等附加服务。
- 2、"仅部分预览"的文档,不可在线预览部分如存在完整性等问题,可反馈申请退款(可完整预览的文档不适用该条件!)。
- 3、如文档侵犯您的权益,请联系客服反馈,我们会尽快为您处理(人工客服工作时间:9:00-18:30)。
铅锡合金在焊接过程中的优缺点。
• Sn63-Pb37的锡铅形成的共晶合金具有优 良的浸润性和低的熔点,可焊性极好。
• 从早先进行铜铁制品的焊接,汽车发动 机冷却水箱的修理,到电子线路的安装 焊接,其应用有些年头了。
• 铅有毒性,电器报废废弃后会污染环境。 随着清洁生产和绿色制造技术的开展, 有关法现的制定与强制执行,无铅焊接 技术得到提倡。
2,有一电路输人电路隔直电容坏了,但发现它是10微法16V的, 现在手中能找到的替换电容都在47微法以上50V以上,甚至耐 压100V,能不能替换来修好仪器呢?有什么问题?请分析并讲 出理由。
自动焊接焊炉炉温控制技术的进 步对测控系统的要求
• 一般自动焊的回流焊炉有五至七米长,内部分 好几个温区,贴好器件的PCB板进入炉体后, 先后进入升温区、保温区和焊接区,最后降温 并出炉,完成焊接。
• 板子的大小,板上器件的多少和大小,板子进 入炉内的速度都关系着焊点焊膏是否完全熔化 而焊牢。温度太高,PCB基板会翘曲,温度过 低,焊膏尚没有熔化,温度不均匀又会造成部 分焊上,另一部分没焊上。
练习题
1,用电涡流位移传感器构成测量振动仪器,传感器输出有-12V间 隙电压,再加上振动波形是叠加在其上的。有一用户购入这样 的监测系统后在实验室中进行验收。他先用一稳压电源提供仪 器输入端一负电压模拟输入,仪表有相应间隙电压显示;接着 用一信号发生器正弦输出取代刚才电源注入,仪器也有振动指 示;最后他把这两个模拟输入并在一起注入仪器,仪器输出只 有间隙电压而没有了振动值。为什么?他错在那?正确的办法 是什么?
带隔热层的采样记录装置随PCB板子一同 经过各温区进行测量。 (动画请双击图标)
具有无线发射接受装的定时测量装置
• 这种开始炉温调整多为制造厂中进行,不能保 证今后所焊接各种尺寸板子都样样合适。
• 这种定期走一趟,用来检查焊炉控温结果是否 仍保持理想状态?要不要重新调整?容易造成 成批废品损失!
国内现状与国际技术水平
● 大量的已购炉子只适用于传统铅锡焊料。
● 生产炉具的工厂都声称新生产的炉子具有无铅焊料 焊接能力。 实际上用无铅焊料,例如锡银铜焊料焊是能焊上, 其可靠性大打折扣!十几个小时或是几十个小时还 是几百个小时后会出现脱焊,重要设备是绝不允许 的!需要做深人实验研究和技术改进。
● 先进国家已经解决问题,从而对我们实现绿色壁垒。 KIC公司提供实时监测系统和技术支持并和大厂商捆 缚,提供解决方案。
● 其它工艺的影响:如PCB板上焊盘和绿色绝缘油漆交 界面内容易腐蚀变窄问题。
●为了节省能源,为了节约占地空间,在生产规模不大的 场合,一种小型回流焊炉出现了。
●被焊接板子在炉内不动,让炉子具有温控曲线的变化规 律,利用时间换取大型炉内走一次的焊接经过。
●具有适时的温度检测和曲线描绘能力,具有数据存储记 录和分析功能,使产品量产中的质量控制和事故追踪变 成可能。
贴片机要自动准确将相应元器 件安放到相应焊盘上
• 贴片机要从元件库中将相关元器件和芯 片取出,并准确安放到PCB板上焊接位置。
• 要求: 定位准确。 动作迅速。
• 无论是印刷机,还是贴片机,其传送带 运动的启停与自动夹紧装置的动作都要 控制,特别是自动定位与对准,元器的 快速获取和安放,所有机构的动作明明 白白是数控技术的应用,只是这里不是 做数控加工机床,其负载力不大,而要 更快捷地完成程序指定的动作。考虑到 定位方案,空间运功的形成,没有机械 制造的基础,不把机、光、电结合,没 有测控技术的参与,是绝对达不到如此 完美、和谐的统一的!
• 或者应用热场测量与分析,神经网络、 模糊数学,建模与仿真,给出优化方案。
• 炉温曲线必需符合所选择焊膏厂推荐的 曲线。
无铅焊接技术对焊炉温控水平 的要求
• 可焊接温区的变窄,考验回流焊炉 温度控制能力和精度!
• PCB基板受热翘曲妨碍焊接质量!
• 各国对绿色制造技术的要求,ROSH 法规的强制执行,向生产厂商,科 技工作者,动态测试技术提出了挑 战!
• 只有实时监控炉温才是最可靠方案!
(在炉内最贴近焊板的传送带两边上方安排几十只热电 偶,随时测量所在炉堂位置处的实际温度,测温传感 器不用随PCB板跑,测量电路也置于炉外。)
•实时多点炉温监测系统(动画请双击图标)
炉温曲线的监控
• 必需对过往的大量焊接实践进行必要数 据收集、统计分析,建立应对策略。
炉内温升机构(动画请双击图标)
可靠焊接的炉温曲线
理想焊接温度曲线是所便用焊膏厂所推荐的。
传统的炉温测量与调控
• 带尾巴的监测系统 选一块PCB板,并在板上焊接位置安放热电偶,
通过专用导线引到炉外的测量电路,测量电路 在炉外与计算机相连。
PCB板及板上热电偶从炉子这头进,那头出, 一旦板子从炉中出来,还要迅速从原路退回去, 防止拉断线缆。板子经过各温区的实测温度都 会被采集记录出来。
• 焊锡丝用烙铁手工一个一个焊点分步焊接。 • 当生产批量较大,使用插好元器件的电路板在
传送带带动下通过带有高温镕化后的铅锡合金 锡锅的波峰焊机一次焊接。
• 当元器件越来越小,引脚越来越多,从四面出 腿到采用整个底面都出引脚的BGA封装芯片, 只能采用表面贴装技术,批量高速生产采用回 流流焊工艺。
• 此时,焊锡丝变成焊锡膏,预先印在焊盘上。 • 通过加热炉使焊膏溶化将元器件焊到焊点上。
回流焊接工艺流程中的数控技术 的应用(动画请双击图标)
锡膏印刷机动作/贴片机动作/回流焊炉
印刷机将焊膏准确印到各要焊接 的焊盘上
• 焊锡丝变成焊膏,PCB基板上对应的焊盘 上要均匀涂印上一层焊膏,是通过专门 镂空的薄膜板向印刷电路板上的对应焊 盘刮印上焊膏的。
• 它要求定位精度要高 (X-Y两个方向), 速度要快。
案例四,回流焊接工艺与炉温控制 中的制造与测试技术
电子产品生产制造过程中焊接技术的发展与演变。
铅锡合金在焊接过程中的优缺点。
回流焊接工艺流程中数控技术的应用。
自动焊接焊炉炉温控制技术的进步对测控系统的要求。
无铅焊料焊接的要求与强制执行对现有生产设备性能 的挑战。
电子产品生产制造过程中焊接技 术的发展与演变