危害发生可能性L判定
安全标准化风险评价准则
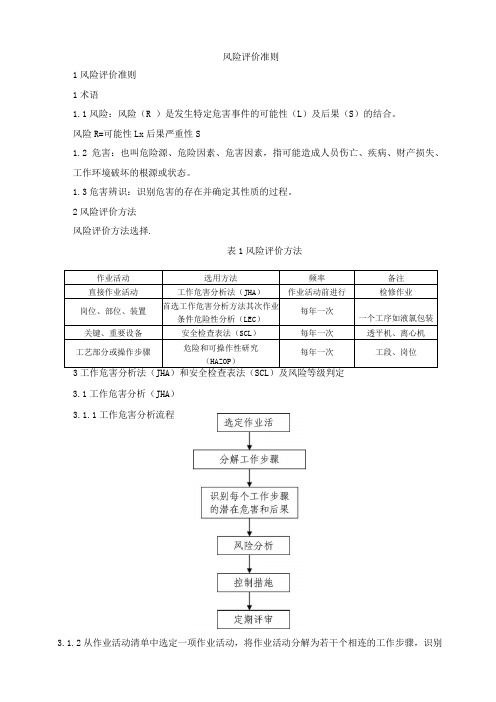
风险评价准则1风险评价准则1术语1.1风险:风险(R )是发生特定危害事件的可能性(L)及后果(S)的结合。
风险R=可能性Lx后果严重性S1.2危害:也叫危险源、危险因素、危害因素,指可能造成人员伤亡、疾病、财产损失、工作环境破坏的根源或状态。
1.3危害辨识:识别危害的存在并确定其性质的过程。
2风险评价方法风险评价方法选择.表1风险评价方法作业活动选用方法频率备注直接作业活动工作危害分析法(JHA)作业活动前进行检修作业岗位、部位、装置首选工作危害分析方法其次作业条件危险性分析(LEC)每年一次一个工序如液氯包装关键、重要设备安全检查表法(SCL)每年一次透平机、离心机工艺部分或操作步骤危险和可操作性研究(HAZOP)每年一次工段、岗位3工作危害分析法(JHA)和安全检查表法(SCL)及风险等级判定3.1工作危害分析(JHA)3.1.2从作业活动清单中选定一项作业活动,将作业活动分解为若干个相连的工作步骤,识别3.1.1工作危害分析流程每个工作步骤的潜在危害因素,然后通过风险评价,判定风险等级,制订控制措施。
作业步骤应按实际作业步骤划分,佩戴防护用品、办理作业票等不必作为作业步骤分析。
可以将佩戴防护用品和办理作业票等活动列入控制措施。
作业步骤只需说明做什么,而不必描述如何做。
作业步骤的划分应建立在对工作观察的基础上,并应与操作者一起讨论研究,运用自己对这一项工作的知识进行分析.3.1.5识别每一步骤可能发生的危害,对危害导致的事故发生后可能出现的结果及严重性也应识别。
识别现有安全措施,进行风险评估,如果这些控制措施不足以控制此项风险,应提出建议的控制措施。
如果作业流程长,作业步骤很多,可以按流程将作业活动分为几大块。
每一块为一个大步骤,可以再将大步骤分为几个小步骤。
3.1.7对采用工作危害分析的评价单元,其每一步骤均需判定风险等级,控制措施首先针对风险等级最高的步骤加以控制。
3.1.8频繁进行的类似作业,可事先制定标准的工作危害分析记录表。
风险矩阵法(LS)
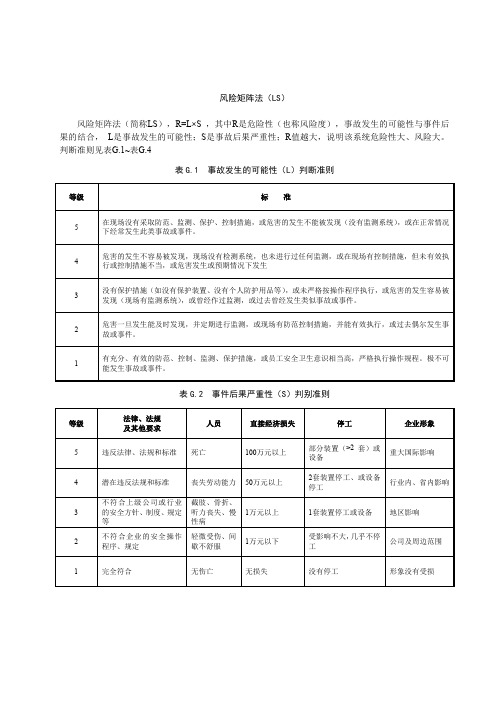
风险矩阵法(LS)风险矩阵法(简称LS),R=L×S,其中R是危险性(也称风险度),事故发生的可能性与事件后果的结合,L是事故发生的可能性;S是事故后果严重性;R值越大,说明该系统危险性大、风险大。
判断准则见表G.1~表G.4表G.1事故发生的可能性(L)判断准则等级标准5在现场没有采取防范、监测、保护、控制措施,或危害的发生不能被发现(没有监测系统),或在正常情况下经常发生此类事故或事件。
4危害的发生不容易被发现,现场没有检测系统,也未进行过任何监测,或在现场有控制措施,但未有效执行或控制措施不当,或危害发生或预期情况下发生3没有保护措施(如没有保护装置、没有个人防护用品等),或未严格按操作程序执行,或危害的发生容易被发现(现场有监测系统),或曾经作过监测,或过去曾经发生类似事故或事件。
2危害一旦发生能及时发现,并定期进行监测,或现场有防范控制措施,并能有效执行,或过去偶尔发生事故或事件。
1有充分、有效的防范、控制、监测、保护措施,或员工安全卫生意识相当高,严格执行操作规程。
极不可能发生事故或事件。
表G.2事件后果严重性(S)判别准则等级法律、法规及其他要求人员直接经济损失停工企业形象5违反法律、法规和标准死亡100万元以上部分装置(>2套)或设备重大国际影响4潜在违反法规和标准丧失劳动能力50万元以上2套装置停工、或设备停工行业内、省内影响3不符合上级公司或行业的安全方针、制度、规定等截肢、骨折、听力丧失、慢性病1万元以上1套装置停工或设备地区影响2不符合企业的安全操作程序、规定轻微受伤、间歇不舒服1万元以下受影响不大,几乎不停工公司及周边范围1完全符合无伤亡无损失没有停工形象没有受损表G.3安全风险等级判定准则(R 值)及控制措施表G.4风险矩阵表后果等级54321(表中人员伤亡、直接经济损失情况仅供参考,不具有确定性,可根据各企业风险可接受程度进行相应调整。
)。
风险评价准则
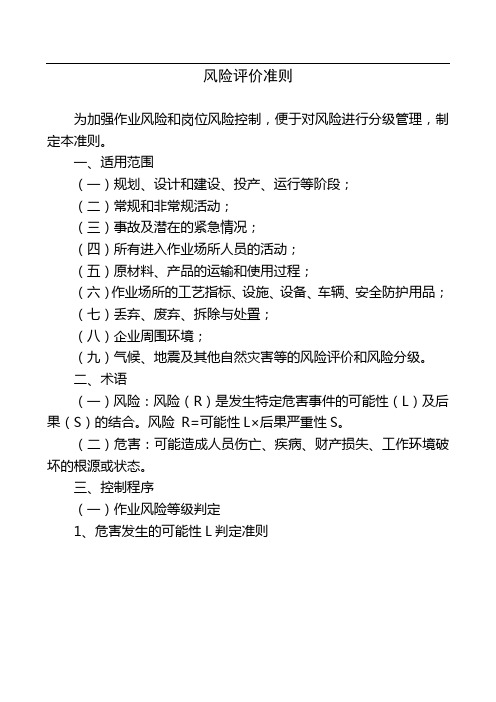
风险评价准则为加强作业风险和岗位风险控制,便于对风险进行分级管理,制定本准则。
一、适用范围(一)规划、设计和建设、投产、运行等阶段;(二)常规和非常规活动;(三)事故及潜在的紧急情况;(四)所有进入作业场所人员的活动;(五)原材料、产品的运输和使用过程;(六)作业场所的工艺指标、设施、设备、车辆、安全防护用品;(七)丢弃、废弃、拆除与处置;(八)企业周围环境;(九)气候、地震及其他自然灾害等的风险评价和风险分级。
二、术语(一)风险:风险(R)是发生特定危害事件的可能性(L)及后果(S)的结合。
风险R=可能性L×后果严重性S。
(二)危害:可能造成人员伤亡、疾病、财产损失、工作环境破坏的根源或状态。
三、控制程序(一)作业风险等级判定1、危害发生的可能性L判定准则2、危害后果严重性S判定准则3、风险等级R判定(表3)(二)工作危害分析(JHA)1、定义:从作业活动清单中选定一项作业活动,将作业活动分解为若干个相连的工作步骤,识别每个工作步骤的潜在危害,然后通过风险评价,判定风险等级,制定控制措施。
2、作业步骤应按实际作业步骤划分,佩戴防护用品、办理作业票等不必作为作业步骤分析。
可以将佩戴防护用品和办理作业票等活动列入控制措施。
3、作业步骤只需说明做什么,而不必描述如何做。
作业步骤的划分应建立在对工作观察的基础上,并应与操作者一起讨论研究,运用自己对这一项工作的知识进行分析。
4、识别每一步骤可能发生的危害,对危害导致的事件发生后可能出现的结果及严重性也应识别。
识别现有安全措施,进行风险评估,如果这些控制措施不足以控制此项风险,应提出建议的控制措施。
5、如果作业流程长,作业步骤很多,可以按流程将作业活动分为几大块。
每一块为一个大步骤。
可以再将大步骤分为几个小步骤。
6、对采用工作危害分析的评价单元,其每一步骤均需判定风险等级,控制措施首先针对风险等级最高的步骤加以控制。
7、频繁进行的类似作业,可事先制定标准的工作危害分析记录表(见附表一)。
设备设施风险等级判定方法RLS

设备设施风险等级判定方法R=L×S
第一条危害发生的可能性L判定准则
L值防范措施经验其它
5 现场没有采取防范、保护、控
制措施
正常情况下曾重复发生
危害
危害发生时不能被发现
4 现场没有采取保护措施或保
护措施不当
正常情况下发生过危害
危害发生时不易被发现
未严格遵守操作规程
3 现场没有采取防范措施或控
制措施不当
异常情况下发生过危害危害发生时容易被发现
2 现场没有采取防范措施或防
范措施不当
未发生过危害危害发生时能及时发现
1 现场有防范、保护、控制措施极不可能发生危害严格执行操作规程
第二条危害后果严重性S判定准则
S值人员财产损失(万元)停车其它
5 造成人员伤亡﹥50 公司停车重大环境污染
4
造成人员重伤﹥25 部分关键装置停车公司形象受到重大负面影响
3 造成轻伤﹥10 降低生产负荷造成环境污染
2
造成人员轻微伤﹤10 影响不大,几乎不
停车
造成轻微环境污染
1 无人员伤亡无损失无停车无污染,无影响
第三条安全风险等级R判定
风险等级风险(R=L×S)控制措施
巨大风险20-25 在采取措施降低危害前,不能继续作业,对改进措施进行评估
重大风险15-16 采取紧急措施降低风险,建立运行控制程序,定期检查、测量及评估
中等风险9-12 建立目标、建立操作规程、加强培训及交流可接受风险4-8 建立操作规程,作业指导书等,定期检查可忽略风险﹤4 无需采取控制措施,保存记录。
事件发生的可能性L判断准则
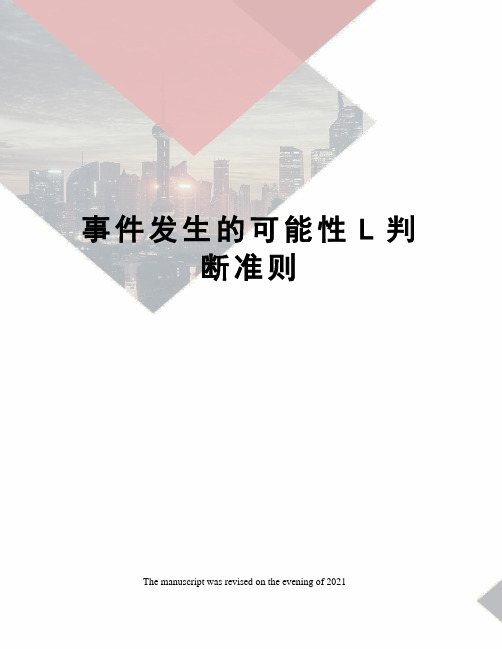
没有保护措施(如没有保护装置、没有个人防护用品等),或未 严格按操作程序执行,或危害的发生容易被发现(现场有监测系统),或曾经作监测,或过去曾经发生类似事故或事件,或在异常情况下发生过类似事故或事件。
2
危害一旦发生能及时发现,并定期进行监测,或现场有防范控制措施,并能有效执行,或过去偶尔发生危险事故或事件。
1
有充分、有效的防范、控制、监测、保护措施,或员工安全卫生意识相当高,严格执行操作规程,极不可能发生事故或事件。
事件后果严重性S判别准则
等级
法律、法规及其他要求
人
财产损失/万元
停工
公司形象
5
违反法律、法规和标准
死亡
>50
部分装置(>2套)或设备停工
重大国际国内影响
4
潜在违反法规和标准
丧失劳动能力
>25
2套装置停工或设备停工
行业内、省内影响
3
不符合上级公司或行业的安全方针、制度规定等
截肢、折、听力丧失、慢性病
>10
1套装置停工或设备停工
地区影响
2
不符合公司的安全操作规程、规定
轻微受伤、间歇不舒服
<10
受影响不大,几乎不停工
公司及周边范围
1
完全符合
无伤亡
无损失
没有停工
形象没有
受损
风险等级判定准则及控制措施
有条件、有经费时治理
<4
轻微或可忽略的风险
无需采用控制措施,但需保存记录
工作危害分析(JHA)记录表
风险度
等 级
应采取的行动/控制措施
实施期限
20~25
巨大风险
在采取措施降低危害前,不能继续作业,对改进措施进行评估
安全风险评价判定准则

4
人员伤亡
造成轻伤3人以上。
15
设备损坏
造成设备或财产损失在10万元到50万元之间。
生产中断
造成设备一类障碍。
环境污染
对周边居民及环境有些影响,引起居民抱怨、投诉。
职业健康损害
造成1~2例可治愈的职业病;
造成3~9例与职业有关的疾病。
5
人员伤亡
造成轻伤1~2人。
5
设备损坏
暴露期低于正常允许水平
0.5
表3 后果(C)基准值
序号
事故可能造成后果的严重程度
分值
1
人员伤亡
造成死亡≥3人;或重伤≥10人。
100
设备损坏
造成设备或财产损失≥1000万元。
生产中断
造成较大以上电力安全事故。
环境污染
造成大范围环境破坏;
造成人员死亡、环境恢复困难;
严重违反国家环境保护法律法规。
职业健康损害
造成设备或财产损失在2万元到10万元之间。
生产中断
造成设备二类障碍。
环境污染
轻度影响到周边居民及小范围(现场)生态环境。
职业健康损害
造成1~2例与职业有关的疾病;
造成3~9例有影响健康的事件。
6
人员伤亡
可能造成人员轻微的伤害(小的割伤、擦伤、撞伤)。
1
设备损坏
可能造成设备或财产损失在2万元以下。
生产中断
造成3~9例无法复原的严重职业病;
造成9例以上很难治愈的职业病。
2
人员伤亡
造成1~2人死亡;或重伤3~9人。
50
设备损坏
造成设备或财产损失在100万元到1000万元之间。
风险评价方法(SCL、JHA、LEC)说明与举例
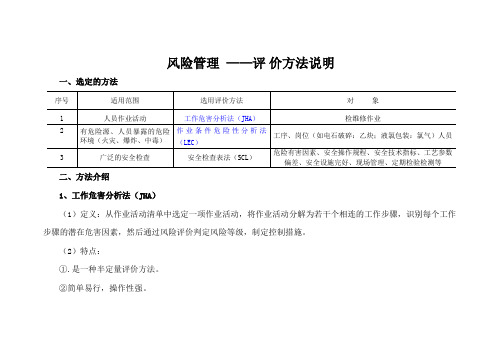
风险管理——评价方法说明一、选定的方法二、方法介绍1、工作危害分析法(JHA)(1)定义:从作业活动清单中选定一项作业活动,将作业活动分解为若干个相连的工作步骤,识别每个工作步骤的潜在危害因素,然后通过风险评价判定风险等级,制定控制措施。
(2)特点:①.是一种半定量评价方法。
②简单易行,操作性强。
③分解作业步骤,比较清晰。
④有别于掌握每一步骤的危险情况,不仅能分析作业人员不规范的危害,而且能分析作业现场存在的潜在危害(客观条件)。
2、作业条件危险性分析法(LEC)(1)定义:作业条件危险性评价法是一种简便易行的衡量人们在某种具有潜在危险的环境中作业的危险性的半定量评价方法。
该方法以与系统风险有关的三种因素指标值之积来评价系统风险的大小,并将所得作业条件危险性数值与规定的作业条件危险性等级相比较,从而确定作业条件的危险程度。
作业条件危险性评价法(LEC法)是以所评价的环境与某些作为参考环境的对比为基础,将作业条件的危险性作因变量(D),事故或危险事件发生的可能性(L)、暴露于危险环境的频率(E)及危险严重程度(C)为自变量,确定了它们之间的函数式,根据实际经验,给出了3个自变量的各种不同情况的分数值,采取对所评价的对象根据情况进行“打分”的办法,然后根据公式计算出其危险性分数值,再在按经验将危险性分数值划分的危险程度等级表查出其危险程度的一种评价方法。
(2)特点:①是一种半定量评价方法。
②简单易行,操作性强,危险程度的级别划分比较清楚、醒目。
③有利于掌握企业内部危险点的危险情况,有利于促进改措施的实施。
④缺点:由于它主要是根据经验来确定3个因素的分数值及划定危险程度等级,因此具有一定的局限性,只能作为作业的局部评价,不能普遍适用。
3、安全检查表方法(SCL)(1)定义:安全检查表分析法是利用检查条款按照相关的标准规范等对已知的危险类别、设计缺陷和与一般工艺设备、操作、管理相关的潜在危险性和有害性进行判别检查。
安全风险评价风险矩阵法(L·S)、LEC法

欢迎共阅
风险矩阵法(L·S)
英国石油化工行业最先采用,即辨识出每个作业单元可能存在的危害,并判定这种危害可能产生的后果及产生这种后果的可能性,二者相乘,得出所确定危害的风险。
然后进行风险分级,根据不同级别的风险,采取相应的风险控制措施。
风险的数学表达式为:R=L×S。
其中:
R—代表风险值;
L—代表发生伤害的可能性;
S—代表发生伤害后果的严重程度。
欢迎共阅
从人员伤亡情况、财产损失、法律法规符合性、环境破坏和对企业声誉损坏五个方面对
R
R
R
R
作业条件风险程度评价(LEC)
基本原理是根据风险点辨识确定的危害及影响程度与危害及影响事件发生的可能性乘积确定风险的大小。
定量计算每一种危险源所带来的风险可采用如下方法:
D=LEC。
式中:
D—风险值;
L—发生事故的可能性大小;
E—暴露于危险环境的频繁程度;
C—发生事故产生的后果。
当用概率来表示事故发生的可能性大小(L)时,绝对不可能发生的事故概率为
续改进的思想。
下表可作为确定风险级别界限值的参考。
- 1、下载文档前请自行甄别文档内容的完整性,平台不提供额外的编辑、内容补充、找答案等附加服务。
- 2、"仅部分预览"的文档,不可在线预览部分如存在完整性等问题,可反馈申请退款(可完整预览的文档不适用该条件!)。
- 3、如文档侵犯您的权益,请联系客服反馈,我们会尽快为您处理(人工客服工作时间:9:00-18:30)。
受影响不大,几乎不停工
企业及
周边范围
1
完全符合
无伤亡
无损失
没有停工
形象
未受损
风险等级R判定及控制措施
风险度
等级
应采取的行动/控制措施
实施期限
20~25
红色
(重大风险)
在采取措施降低危害前,不能继续作业,对改进措施进行评估
立刻
15~16
橙色
(较大风险)
采取紧急措施降低风险,建立运行控制程序,定期检查、测量及评估
危害发生可能性L判定
等级
标 准
5
在现场没有采取防范、监测、保护、控制措施,或危害的发生不能被发现(没有监测系统),或在正常情况下经常发生此类事故或事件。
4
危害的发生不容易被发现,现场没有检测系统,也未发生过任何监测,或在现场有控制措施,但未有效执行或控制措施不当,或危害常发生或在预期情况下发生。
3
没有保护措施(如没有保护装置、没有个人防护用品等),或未严格按操作程序执行,或危害的发生容易被发现(现场有监测系统),或曾经作过监测,或过去曾经发生类似事故或事件,或在异常情况下类似事故或事件。部分装置(>2套)或设备停工
重大国际国内影响
4
潜在违反
法规和标准
丧失劳动能力
>25
2套装置停工、或设备停工
行业内、省内影响
3
不符合上级企业或行业的安全方针、制度、规定等
截肢、骨折、听力丧失、慢性病
>10
1套装置停工或设备
地区影响
2
不符合企业的安全操作程序、规定
轻微受伤、间歇不舒服
2
危害一旦发生能及时发现,并定期进行监测,或现场有防范控制措施,并能有效执行,或过去偶尔发生事故或事件。
1
有充分、有效的防范、控制、监测、保护措施,或员工安全卫生意识相当高,严格执行操作规程。极不可能发生事故或事件。
危害后果严重性S判定
等级
法律、法规及
其他要求
人 员
财产损失
/万元
停 工
企业形象
5
违反法律、
立即
或近期整改
6~12
黄色
(一般风险)
可考虑建立目标、建立操作规程,加强培训及沟通
2年内治理
1~5
蓝色
(低风险)
可考虑建立操作规程、作业指导书但需定期检查或无需采用控制措施,但需保存记录
有条件、有经费时治理
风险矩阵表
严
重
性
(S)
5
低
中
高
很高
很高
4
低
中
中
高
很高
3
较低
中
中
中
高
2
较低
低
中
中
中
1
较低
较低
较低
低
低
风险度(R)
1
2
3
4
5
可能性(L)