FMEA 技术的应用
质量管理五大核心工具之FMEA
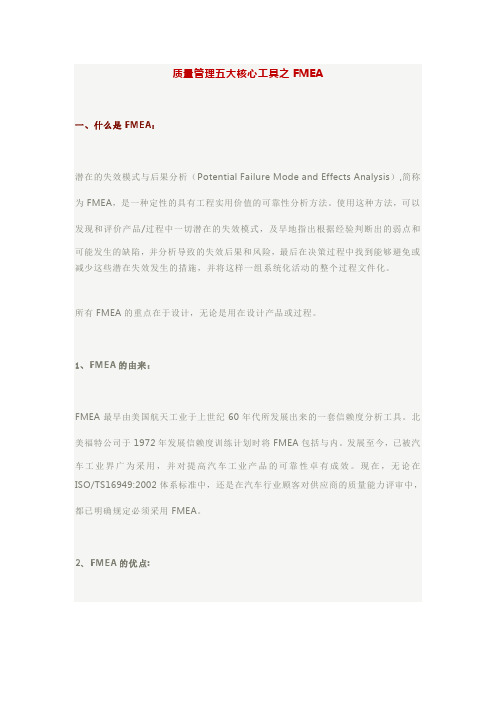
质量管理五大核心工具之FMEA一、什么是FMEA:潜在的失效模式与后果分析(Potential Failure Mode and Effects Analysis),简称为FMEA,是一种定性的具有工程实用价值的可靠性分析方法。
使用这种方法,可以发现和评价产品/过程中一切潜在的失效模式,及早地指出根据经验判断出的弱点和可能发生的缺陷,并分析导致的失效后果和风险,最后在决策过程中找到能够避免或减少这些潜在失效发生的措施,并将这样一组系统化活动的整个过程文件化。
所有FMEA的重点在于设计,无论是用在设计产品或过程。
1、FMEA的由来:FMEA最早由美国航天工业于上世纪60年代所发展出来的一套信赖度分析工具。
北美福特公司于1972年发展信赖度训练计划时将FMEA包括与内。
发展至今,已被汽车工业界广为采用,并对提高汽车工业产品的可靠性卓有成效。
现在,无论在ISO/TS16949:2002体系标准中,还是在汽车行业顾客对供应商的质量能力评审中,都已明确规定必须采用FMEA。
2、FMEA的优点:由于FMEA是一种定性的分析方法,因此与定量的分析方法相比,FMEA就显得简便易懂,且较直观,易于被人们掌握并运用。
尤其是在一些不能用定量的可靠性数字说明问题的工程关键阶段,FMEA就更为适用。
3、FMEA的实施●∙∙减少减少潜在的隐忧——使用FMEA作为专门的技术应用、以识别并减少潜在的隐患;——全面实施FMEA能够避免许多车辆抱怨事件的发生。
●∙∙适时性是成功实施FMEA的最重要因素之一——是”事发前”的行为,要求FMEA必须在设计或过程失效模式被无意纳入产品或过程之前进行;——事先花时间完成FMEA分析,能更容易并低成本地对产品/过程进行修改,从而减轻事后修改的危机;.—— FMEA能够减少或消除因进行预防/纠正而带来更大损失的机会。
●∙∙FMEA适用场合——新设计、新技术或新过程。
该FMEA的领域是完成设计、技术或过程。
fmea分析
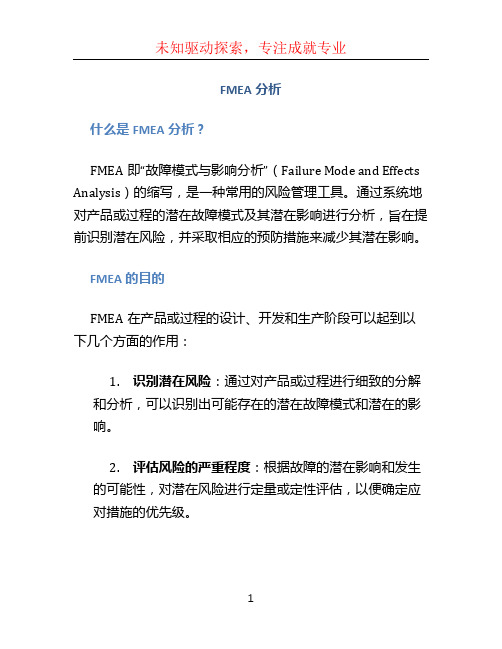
FMEA分析什么是FMEA分析?FMEA即“故障模式与影响分析”(Failure Mode and Effects Analysis)的缩写,是一种常用的风险管理工具。
通过系统地对产品或过程的潜在故障模式及其潜在影响进行分析,旨在提前识别潜在风险,并采取相应的预防措施来减少其潜在影响。
FMEA的目的FMEA在产品或过程的设计、开发和生产阶段可以起到以下几个方面的作用:1.识别潜在风险:通过对产品或过程进行细致的分解和分析,可以识别出可能存在的潜在故障模式和潜在的影响。
2.评估风险的严重程度:根据故障的潜在影响和发生的可能性,对潜在风险进行定量或定性评估,以便确定应对措施的优先级。
3.确定风险控制措施:基于评估的风险严重程度,制定相应的风险控制计划,包括预防措施、检测措施和修正措施,以减少故障发生的可能性和减轻其影响。
4.提高产品和过程可靠性:通过对潜在故障模式和影响的深入分析,可以发现设计或工艺上的问题,并提出相应的改进措施,以提高产品和过程的可靠性。
FMEA的应用步骤FMEA分析一般由以下步骤组成:1.确定FMEA的范围和对象:明确FMEA的应用范围,确定要分析的产品或过程,以及需要参与FMEA分析的团队成员和相关专家。
2.创建FMEA分析表:根据产品或过程的特征和结构,创建FMEA分析表,包括列出可能出现的故障模式、故障后果、故障发生的可能性、目前的控制措施等信息。
3.评估故障的潜在影响和可能性:对每个故障模式进行评估,确定故障的潜在影响和发生的可能性,并进行定量或定性的风险评估。
4.制定风险控制措施:根据风险评估的结果,确定相应的风险控制措施,包括预防措施、检测措施和修正措施,以减少故障的潜在影响和发生的可能性。
5.实施风险控制措施:根据制定的措施,执行相应的行动计划,包括改进设计、制定工艺规范、加强检测和监控等。
6.监控和更新FMEA分析:定期监控和评估已实施的风险控制措施的效果,及时更新FMEA分析表,以反馈和改进措施。
PFMEA管理规定

4.5.6严重度(S):严重度是指与评估的过程步骤中针对给定的失效模式最严重影响相关的评级等分,他是在一个FMEA范围内的相对评级,评定时无需考虑频度或探测度。
4.5.7频度:频度(O)描述了失效起因在过程中的发生频率,同时考虑了相关的当前的预防控制。
当措施完成时,频度和探测度值将被重新评估,一个新的措施优先级可能要被确定。重新评估应当基于采取的预防和探测措施的有效性,并且新的值基于过程FMEA频度和探测度评级表中的定义。
4.6.6持续改进:
PFMEA是过程的历史记录。初始严重度、频度和探测度(S、O、D)数值需显示可见,或至少可作为历史记录的一部分使用和访问。分析完成后将形成一个储存库,能够记录过程决策和设计改进的进展。
建立日期
版次
文件编号
修订日期
2019.12.23
四、过程FMEA的执行:
4.1过程FMEA步骤一:策划与准备
4.4.1该过程考虑工厂内所有过程均可通过PFMEA进行分析或重新分析。准备阶段的总体优势是将资源集中在优先级最高的过程上。
4.1.2过程策划与准备步骤的主要目标:
①项目识别
②项目计划:目的、时间安排、团队、任务、工具(5T)
4.4.6失效起因:失效起因是指失效模式出现的原因,失效模式是失效起因的结果。
4.4.7失效分析:根据过程步骤,导出失效并从功能分析中创建失效链。
4.4.8失效分析文件化:结构分析、功能分析和失效分析完成后,结构树或电子表格制成多种视图。
批准
审核
作成
第3页共13页
****************公司
3.3生产部职责:
生产部负责提出对生产过程中的生产流程等不合理现象,必要时参与FMEA小组;
FMEA详解及其案例分析

FMEA定义: 是通过对可能发生的(和/或已经发生的)失效模式进行分
析并判断其可能造成的(和/或已经产生的)后果而产生的 风险程度的一种量化的定性分析计算方法;
根据风险的大小,采取有针对性的改善措施,从而了解 产品(和/或制造过程)设计能力,达成一种事先预防并实 施改善措施进行改善的方法工具。
运,接收,材料运输,储存,传送或标签。
FMEA 的三种情形
1
•新设计,新技术或新过程.FMEA的范围是全部设计,技术或过程.
•对现有设计或过程的修改( FMEA应该着重于设计和过程的更改,由更
2
改而可能引起的相互作用以及从市场上所获得的历史信息。它可包括 法律法规的变更。)
•在新的环境,场所,应用和使用形式下(包括:工作循环,法律和
风险举例说明 钣金冲压工厂 特点:长期、猛烈的冲击振动
频繁的振动
连接处松动
泄漏
油滴到地面上
地面积油 人员摔伤 上告、索赔
根源模式 中间模式 最终模式
风险的描述:
•风险的后果(危害)有多严重?
•风险发生的可能性有多大?
•是否能提前发现风险?
风险的控制:
•风险的后果(危害)有多严重?
降低后果(危害)的影响程度:提高自身“健状度”,增强风 险承受能力。
能做些什么?
-- 设计更改 -- 过程更改 -- 特别控制(SPC,全检) -- 标准、程序或指南的更改 -- 导入防呆措施 -- 加强设备保养 -- 加强参数控制 -- 加强工作技能
如何 探测?
探测 难易度?
再评价, 风险是否 降低?
变化
项目/ 潜在失 潜在 严 级 潜在 发 现行控制
过程
效模式 失效 后果
失效模式和效果分析FMEA在制药行业的应用教材

失效模式和效果分析FMEA在制药行业的应用教材失效模式与效应分析(Failure Mode and Effects Analysis, FMEA)是一种常用的质量管理工具,它可以帮助制药行业发现潜在的问题,预防和减少产品质量问题的发生,从而提高产品质量和安全性。
本文将探讨FMEA在制药行业的应用,并分析其效果。
FMEA的基本原理是通过识别潜在的失效模式,并分析这些失效模式可能引起的效应,进而制定合适的预防和纠正措施。
在制药行业,FMEA通常用于产品开发、生产过程和设备维护等环节。
下面将详细介绍FMEA在这些环节的应用。
首先,FMEA在制药产品开发阶段起到了重要的作用。
制药产品的设计失效可能导致产品质量问题和安全隐患。
通过应用FMEA,可以对设计过程中潜在的失效模式进行识别和评估,并制定相应的改进方案。
例如,通过对产品配方进行FMEA分析,可以找出可能导致配方不稳定的因素,如不合适的原材料、配方比例不当等。
这样可以在产品设计阶段及时进行调整,避免质量问题的发生。
其次,FMEA在制药生产过程中的应用也十分重要。
生产过程中的失效可能导致产品质量不稳定和生产效率降低。
通过应用FMEA,可以识别和评估生产过程中的潜在失效模式,并设计相应的控制措施。
例如,在制药生产过程中,可能存在温度控制失效、搅拌不均匀等问题。
通过应用FMEA,可以定位这些问题的发生原因,并制定相应的控制措施,比如使用更精确的温度控制设备、改进搅拌工艺等。
此外,FMEA还可以应用于制药设备的维护管理。
设备故障可能导致生产中断和质量问题。
通过应用FMEA,可以识别设备故障的潜在失效模式,并制定相应的预防和纠正措施。
例如,对于关键设备,可以制定定期保养计划,定期更换易损件,增加备件库存等。
通过这些措施,可以降低设备故障的概率,保证生产的稳定性和质量。
FMEA作为一种质量管理工具,在制药行业的应用具有一定的优势和效果。
首先,通过FMEA可以对潜在的失效模式进行全面、系统的分析。
风险评估技术-失效模式和效应分析(FMEA)及失效模式、效应和危害度分析(FMECA)

失效模式和效应分析(FMEA及失效模式、效应和危害度分析(FMECA)1 概述失效模式和效应分析(Failure Mode and Effect Analysis ,简称FMEA)是用来识别组件或系统未能达到其设计意图的方法。
FMEA 用于识别:•系统各部分所有潜在的失效模式(失效模式是被观察到的是失误或操作不当);•这些故障对系统的影响;• 故障原因;• 如何避免故障及 /或减弱故障对系统的影响。
失效模式、效应和危害度分析(Failure Mode and Effect and Criticality Analysis ,简称 FMECA)拓展了 FMEA 的使用范围。
根据其重要性和危害程度,FMECA 可对每种被识别的失效模式进行排序。
这种分析通常是定性或半定量的,但是使用实际故障率也可以定量化。
2 用途FMEA 有几种应用:用于部件和产品的设计(或产品) FM EA ;用于系统的系统FMEA ;用于制造和组装过程的过程 FMEA ;服务FMEA和软件FMEA。
FMEA/ FMECA 可以在系统的设计、制造或运行过程中使用。
然而,为了提高可靠性,改进在设计阶段更容易实施。
FMEA/ FMECA 也适用于过程和程序。
例如,它被用来识别潜在医疗保健系统中的错误和维修程序中的失败。
FMEA/FMECA 可用来:•协助挑选具有高可靠性的替代性设计方案;•确保所有的失效模式及其对运行成功的影响得到分析;•列出潜在的故障并识别其影响的严重性;•为测试及维修工作的规划提供依据;• 为定量的可靠性及可用性分析提供依据。
它大多用于实体系统中的组件故障,但是也可以用来识别人为失效模式及影响。
FMEA 及 FMECA 可以为其他分析技术,例如定性及定量的故障树分析提供输入数据。
3 输入数据FMEA 及 FMECA 需要有关系统组件足够详细的信息,以便对各组件出现故障的方式进行有意义的分析。
信息可能包括:• 正在分析的系统及系统组件的图形,或者过程步骤的流程图;• 了解过程中每一步或系统组成部分的功能;• 可能影响运行的过程及环境参数的详细信息;• 对特定故障结果的了解;• 有关故障的历史信息,包括现有的故障率数据。
FMEA技术在军事装备维修中的应用
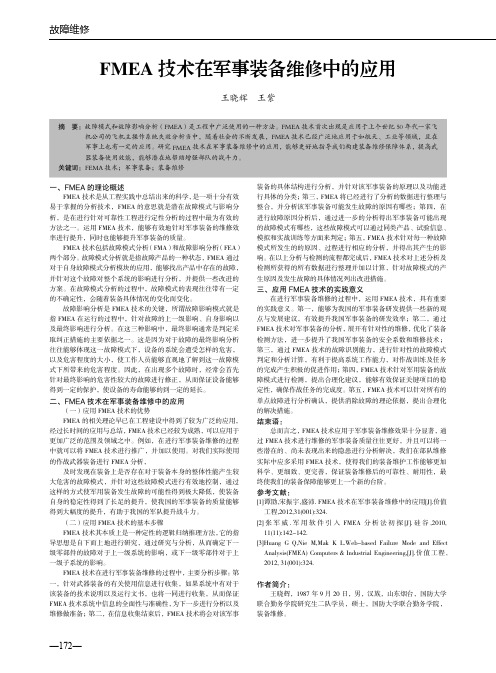
故障维修—172—FMEA技术在军事装备维修中的应用王晓辉王紫摘要:故障模式和故障影响分析(FMEA)是工程中广泛使用的一种方法。
FMEA技术首次出现是应用于上个世纪50年代一家飞机公司的飞机主操作系统失效分析当中,随着社会的不断发展,FMEA技术已经广泛地应用于如航天、工业等领域,且在军事上也有一定的应用。
研究FMEA技术在军事装备维修中的应用,能够更好地指导我们构建装备维修保障体系,提高武器装备使用效能,能够潜在地帮助增强部队的战斗力。
关键词:FEMA技术;军事装备;装备维修一、FMEA的理论概述FMEA技术是从工程实践中总结出来的科学,是一项十分有效易于掌握的分析技术,FMEA的意思就是潜在故障模式与影响分析,是在进行针对可靠性工程进行定性分析的过程中最为有效的方法之一。
运用FMEA技术,能够有效地针对军事装备的维修效率进行提升,同时也能够提升军事装备的质量。
FMEA技术包括故障模式分析(FMA)和故障影响分析(FEA)两个部分。
故障模式分析就是指故障产品的一种状态,FMEA通过对于自身故障模式分析模块的应用,能够找出产品中存在的故障,并针对这个故障对整个系统的影响进行分析,并提供一些改进的方案。
在故障模式分析的过程中,故障模式的表现往往带有一定的不确定性,会随着装备具体情况的变化而变化。
故障影响分析是FMEA技术的关键,所谓故障影响模式就是指FMEA在运行的过程中,针对故障的上一级影响、自身影响以及最终影响进行分析。
在这三种影响中,最终影响通常是判定采取纠正措施的主要依据之一。
这是因为对于故障的最终影响分析往往能够体现这一故障模式下,设备的系统会遭受怎样的危害,以及危害程度的大小,使工作人员能够直观地了解到这一故障模式下所带来的危害程度。
因此,在出现多个故障时,经常会首先针对最终影响的危害性较大的故障进行修正,从而保证设备能够得到一定的保护,使设备的寿命能够的到一定的延长。
二、FMEA技术在军事装备维修中的应用(一)应用FMEA技术的优势FMEA的相关理论早已在工程建设中得到了较为广泛的应用,经过长时间的应用与总结,FMEA技术已经较为成熟,可以应用于更加广泛的范围及领域之中。
fmea案例
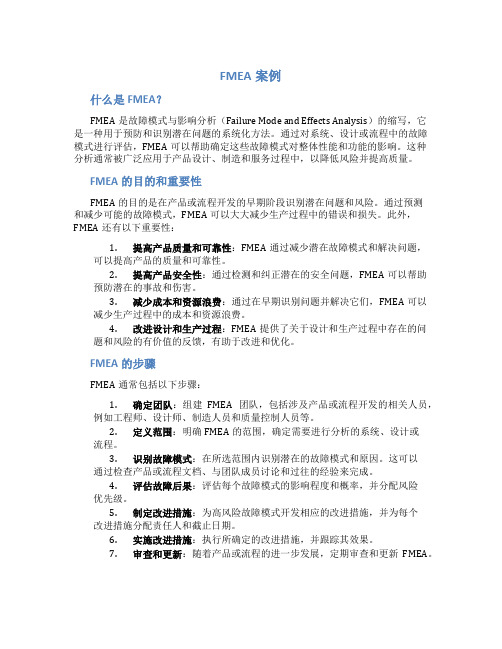
FMEA案例什么是FMEA?FMEA是故障模式与影响分析(Failure Mode and Effects Analysis)的缩写,它是一种用于预防和识别潜在问题的系统化方法。
通过对系统、设计或流程中的故障模式进行评估,FMEA可以帮助确定这些故障模式对整体性能和功能的影响。
这种分析通常被广泛应用于产品设计、制造和服务过程中,以降低风险并提高质量。
FMEA的目的和重要性FMEA的目的是在产品或流程开发的早期阶段识别潜在问题和风险。
通过预测和减少可能的故障模式,FMEA可以大大减少生产过程中的错误和损失。
此外,FMEA还有以下重要性:1.提高产品质量和可靠性:FMEA通过减少潜在故障模式和解决问题,可以提高产品的质量和可靠性。
2.提高产品安全性:通过检测和纠正潜在的安全问题,FMEA可以帮助预防潜在的事故和伤害。
3.减少成本和资源浪费:通过在早期识别问题并解决它们,FMEA可以减少生产过程中的成本和资源浪费。
4.改进设计和生产过程:FMEA提供了关于设计和生产过程中存在的问题和风险的有价值的反馈,有助于改进和优化。
FMEA的步骤FMEA通常包括以下步骤:1.确定团队:组建FMEA团队,包括涉及产品或流程开发的相关人员,例如工程师、设计师、制造人员和质量控制人员等。
2.定义范围:明确FMEA的范围,确定需要进行分析的系统、设计或流程。
3.识别故障模式:在所选范围内识别潜在的故障模式和原因。
这可以通过检查产品或流程文档、与团队成员讨论和过往的经验来完成。
4.评估故障后果:评估每个故障模式的影响程度和概率,并分配风险优先级。
5.制定改进措施:为高风险故障模式开发相应的改进措施,并为每个改进措施分配责任人和截止日期。
6.实施改进措施:执行所确定的改进措施,并跟踪其效果。
7.审查和更新:随着产品或流程的进一步发展,定期审查和更新FMEA。
FMEA案例研究下面是一个关于工业自动化机器系统的FMEA案例研究:1. 范围定义本次FMEA案例研究针对工业自动化机器系统的设计和制造过程。
- 1、下载文档前请自行甄别文档内容的完整性,平台不提供额外的编辑、内容补充、找答案等附加服务。
- 2、"仅部分预览"的文档,不可在线预览部分如存在完整性等问题,可反馈申请退款(可完整预览的文档不适用该条件!)。
- 3、如文档侵犯您的权益,请联系客服反馈,我们会尽快为您处理(人工客服工作时间:9:00-18:30)。
• 嚴重度------S • 發生率------O • 難檢度------D • 風險優先數------RPN=S*O*D
七.嚴重性:
• 衡量失效的影響程度. • 對外觀、結構、功能、性能穩定性、可靠性之影響. • 對下一制程、使用者、設備之影響. • 對最終客戶、政府法規、安全、環保的違及.
6.精密量測:通過高度規、三次元、二次元、投影儀等獲取
所需的數據.
五.主流程
分析制程特性 定義製造流程 分析產品特性
分析失效模式 分析失效原因 分析發生率 分析現行控制方法 分析難檢度 計算風險優先數 決定優先改善之失效模式 建議改善措施 改善實施 分析失效效應 分析嚴重度
六.幾個重要的分析指標:
二.FMEA的必要性
• 提升工程師工程分析能力. •列出所有可能的原因,按優先順序予以解決,提 出所有對應措施改善,避免遺漏,避免抓不到重 點,避免作不必要的責任追查.
• 提升制程品質可靠度.
• 下一次工程分析之參考.
三.兩類FMEA
• a.設計FMEA: 工標主導.
配合. 各處QE 、工程及模具設計單位 工標、工程、製造單位配合.
難檢度(D)劃分標準
等級/評分
1~2
劃分標準 描述
幾乎可以肯定地檢測出 來
可偵度
≧99.99%
3~5
6~8 9 10
有良好的手段可以檢測
可能檢測出來 很有可能檢測不出 很可能檢測不出來
≧99.80%
≧98.00% ≧90.00% ≦90.00%
十.制程FMEA範例及案例分析:
見附表.
制程FMEA範例
• b.制程FMEA: QE主導.
衝壓品管課所作FMEA為制程FMEA,它作為一種新的品管 技術,由QCE(衝壓制程品質工程師)負責推動和應用. 1.后工程抱怨. 2.制程之重大異常. 應用時機 3.重復發生的異常. 4.客戶投訴.
衝壓制程失效模式分析
制程名稱 及功能 預估失 效模式 預估失效原因 控制措施 實施日 責任人 效果 確認
4-6.(Moderate)
7-8.(High)
可能造成客戶很不滿意,並導致客戶重大抱怨, 但不會導致安全事故或違及政府法規.
9-10.(Very High) 導致客戶停線或對產品有致命性的功能性影 響,或可能導致安全事故,或違及政府法規.
八.發生率:
• 某一原因導致失效發生的機率. • 測定方式:CPK 、主觀判定、統計資料. (舉例說明“攻牙無限位”).
FMEA 技 術 的 應 用
報告人:彭衛安
單位:DT(V)品保部衝壓品管課
制作時間:2000年9月6日
FMEA 技 術 的 應 用
•
一.起源:
FMEA:失效模式、效應與關鍵性分析是一種系統化工程設
計
輔助工具,利用表格方式協助工程師進行工程分析,使 其發現潛在缺陷及影響程度,以避免失效發生或降低 其發生時產生之影響.
Cpk
≧1.67
≧1.50
≧1.33 ≧1.17 ≧1.00 ≧0.83 ≧0.67 ≧0.51 ≧0.33 <0.33
6(Moderate) 7(High) 經常發生 8(High) 9(Very High) 幾乎不可避免 10(Very High)
九.難檢度:
• 在現行的控制措施下,檢測失效發生的能力. • 測定方式:主觀判定 、 統計資料 (舉例說明“分隔板之散熱孔”)
制 程 名 稱/ 目 的 預估 失效 模式 預估 失效 影響 嚴 重 度 S 預 估 失 效 原 因 發 生 率 O 現行 難 控制 檢 措施 度 D R P N 建 議 控 制 措 施 責 完 狀 任 成 態 人 日 期 已採 S O D R 取之 P 措施 N
裝 上 蓋
卡鉤 卡不 到位
影響 外觀 和功 能
發生率(O)劃分標準
等級/評分
1(Remote) 2(Very Low)
3(Low) 4(Moderate) 5(Moderate) 偶爾發生,但不 佔有大的比例
描述
幾乎不可能發生 有輕度發生的可 能 有可能發生
劃分標準 發生率
1/1500K 1/150K
1/15K 1/2K 1/400 1/80 1/20 1/8 1/3 1/2
四.作制程FMEA須具備的方法和工具:
1.品管七大手法:運用柏拉圖、分層法、直方圖等方法進
行數據匯總分析.
2.腦力激蕩法:挖掘可能的原因. 3.對比分析法:進行等級界定與優先順序劃分. 4.愚巧法:利用輔助方法去“防呆”也是措施之一. 5.樹圖、KJ法等:由各因素之間的關係、關聯,來確定采取
的控制措施.
嚴重度(S)劃分標準
等級/評分(Rank) 1.(Minor) 劃分標準(Criteria) 幾乎不會對產品有任何影響,即使有影響,客 戶亦不會注意.
2-3.(Low)
客戶可能會注意,可能會對客戶造成裝配和使 用上的輕微不便,可能會使下道工站輕微的重 工.
會造成客戶的不滿意,造成客戶抱怨,甚至會 導致重工動作發生.
6
人 工 操 作
3
無
6
108
使 用 夾 具
--
--
OK
使用 6 2 2 夾具 和增 加檢 驗工 站 使用 8 2 1 夾具 和增 加檢 驗工 站
24
裝 FD D
FDD FDD 錯位 磁片 彈不 出
8
人 工 操 作
3
無
8
192
使 用 夾 具
--
--
OK
16