FMEA讲义修订版
FMEA工程应用培训讲义

FMEA工程应用培训讲义FMEA (Failure Mode and Effects Analysis)是一种常用的风险管理工具,广泛应用于工程设计和制造过程中,旨在提前识别和消除潜在的故障和缺陷。
FMEA可以帮助工程师在设计和制造过程中确定风险,并制定相应的措施来降低潜在故障和缺陷的发生概率。
一、FMEA的基本原理1.1 FMEA的概念FMEA是一种通过系统化的方法,对产品、设计或工作过程中的潜在故障模式进行分析和评估的方法。
通过找出故障模式的潜在原因和效应,可以采取相应的预防措施来减少故障的发生。
1.2 FMEA的目的FMEA的主要目的是通过提前识别和消除潜在的故障和缺陷,提高产品和流程的可靠性和质量。
它能够帮助工程师在设计和制造的过程中识别可能导致产品故障的因素,并制定相应的改进措施。
二、FMEA的应用步骤2.1 选择要分析的过程或产品首先确定要进行FMEA分析的具体产品或过程。
这可以是一个正在开发的新产品,也可以是一个现有产品的改进过程。
2.2 组织FMEA团队确定一个专门的团队来进行FMEA分析。
该团队应由各个领域的专家组成,包括设计工程师、制造工程师和质量控制专家。
2.3 确定潜在故障模式分析可能导致产品故障的各个环节,包括设计、制造、运输、安装和使用过程。
对每个环节,确定可能发生的故障模式。
2.4 评估故障模式的严重性对每个故障模式,评估其可能对产品或过程的影响程度,包括安全性、可靠性和成本等方面。
2.5 确定故障模式的原因对每个故障模式,找出可能导致其发生的潜在原因。
这些原因可以是设计缺陷、制造误差、操作错误等。
2.6 评估故障模式的概率对每个故障模式,评估其发生的概率。
这可以通过历史数据、专家访谈等方式进行评估。
2.7 评估故障模式的可探测性对每个故障模式,评估其是否可以通过检测手段及时发现。
如果不能及时发现,应考虑改进措施。
2.8 制定改进措施根据故障模式的严重性、原因、概率和可探测性,制定相应的改进措施。
FMEA我的讲义

FMEA的实施 FMA:Failure Mode Analysis
FMA(失效模式分析) FMEA(潜在失效模式及后果分析)
失效已经产生
失效还未产生,可能发生,但不是一 定要发生
核心:纠正
核心:预防
诊断已知的失效
评估风险和潜在失效模式的影响
开始于产品设计和工艺开发活动之前
指引开发和生产
指引贯穿整个产品周期
• 4、1985年由国际电工委员会(IEC)出版的FMECA 国际标准(IEC812),即参考MIL-STD-1629A加以部分 修改而成。
13
FMEA 之適用範圍
• 1、ISO9004 8.5節FMEA作為設計審核的要項,另 FTA(失效樹分析)風險分析亦是。
• 2、CE標志,以FMEA作為安全分析方法。
E: Effect 後果
Effect談三種: 1.對本身的立即影響
2.對同一水平的影響, 也可能對下一工序的影響 3.對產品使用者的影響
6
FMEA定義
後果的通常表現形式:
人身安全 不舒服的氣味 不穩定 作業中斷 無法繫緊 無法安裝 損壞裝備
手感不良
作業過多
無法操作
操作不良
車控不良
顧客不滿意
滲漏
外觀不良
12
FMEA 之沿革
• 1、FMEA的前身為FMECA,是在1950由格魯曼飛機 提出,用在飛機主控系統的失效分析
• 2、波音與馬丁公司在1957年正式編訂FMECA的作业 程序,列在其工程手冊中
• 3、60年代初期,美太空总署将FMECA成功的应用于 太空计划。美军同时也开始应用FMECA技术,并于 1974年出版MIL-STD-1629 FMECA作业程序。
DFMEA培训讲义

三种FMEA的差异
设计FMEA 用来在产品交付生产前分析产品 分析重点 由设计缺陷引起的潜在产品失效模式 过程FMEA 用来分析制造与装配过程 分析重点 由制造或装配过程缺陷引起的潜在产品失效模式
三种FMEA的差异
系统FMEA 用来早期构思系统阶段,分析系统与子系统 分析重点 由系统缺陷引起的与系统功能相联系的 潜在失效模式分析 一个系统与其他系统间的相互作用 系统单元间的相互作用
克莱斯勒召回46.4万辆“PT漫步者”
PT漫步者是2001年才投入量产的新 车型,甫一上市即大受欢迎,两年间共生产 464315辆,其中已售出42.5万辆, 今年上半年PT漫步者的销量比去年同期增 长5%,已成为克莱斯勒最畅销的车型。 (杨钧)
气囊系统不合格——通用招回72万辆 问题车
【新华网 】北京2002年8月20日专电 据法新社19日报道,美国通用汽车公司当日宣布,已经开始召回72万辆气囊 系统存在问题的汽车。 通用公司在声明中说,这72万辆车中有57万辆在发生事故时气囊可能无法展 开,原因是感应和判断系统存在问题,对气囊的展开信号的顺序产生干扰。另15万 辆车气囊系统的焊接有问题,气囊展开时焊缝可能会断裂,并产生飞散的碎片,并且 气囊也可能无法充分展开。
必须有整体性的规划,并且 循序渐进地逐步改善企业的 研发环境
FMEA的产生
FMEA是一种实用的解决问题的方法,
可适用于许多工程领域(核电厂、水库、卫
星、飞机、十大召回事件… … ),目前世界
许多汽车生产商和电子制造服务商(EMS)都
已经采用这种模式进行设计和生产过程的管
理和监控。
因发动机问题日产公司召回30多万辆汽车
日本尼桑公司将召回百万辆有故障汽车
DFMEA讲义
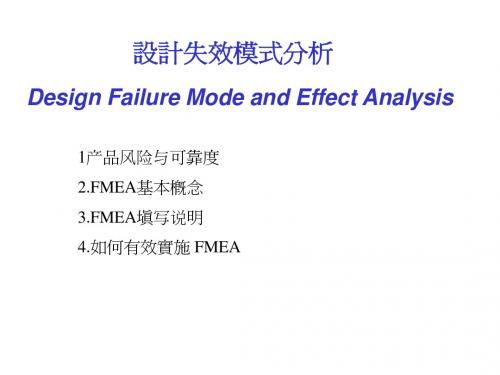
QS 9000 品質系統要求
ISO 9000 品質系統
客戶要求 QS 9000 + IASG 生產零件核准程序(PPAP) 客戶指定要求
客戶參考手冊
APQP&CP
品質手冊 程序 作業指導書 其他文件
FMEA
MSA SPC
三、設計 FMEA 填寫說明
(19) 建議措施: 當失效模式依RPN數排列其風險順序時,針對最高級的影響和關鍵項目提出 矯正措施。 任何建議措施的目的是要減少任何發生度、嚴重度和難檢度。增加設計驗證 或確認措施的結果,只可降低難檢度的等級。 透過設計變更去除或管制某一或多個影響失效模式的原因或方法,只能降低 發生度的等級。 只有設計變更能降低嚴重度等級。可以考慮下列的採行措施,但並不限於此: 實驗設計 修改設計 修改測試計畫 修改原物料規格 RPN結果:將矯正措施實施後,經鑑定、評估和記錄嚴重度、發生度、和難 檢度的等級結果填入,進一步的措施只要重覆(19) ~ (22)之步驟 即可。
物品直接表現失效的形式如下: 1. 實體破壞:硬式失效 2. 操作功能中止 3. 功能退化 4. 功能不穩定
軟式失效
2 ~ 4 項物品機能因老化 ( Aging )、退化( Degradation ) 或不穩定 (Unstable)而不能滿足原設定的要求標準, 所以失效現象及研判準則 必頇量化。
FMEA的基本概念:
無法操作以及短暫失去功能 不符合的項目的裝配表面處理及異音,不良資訊來自一般客戶 不符合的項目的裝配表面處理及異音,不良資訊來自特定客戶
5
4 3 2
無
無影響
1
三、設計 FMEA 填寫說明 2 發生率劃分標準:
DFMEA技术讲义

北京运通恒达科技有限公司
直面风险
11
只要存在,就一定会发生 我们不可能消除所有的风险 我们的目的是在有限的资源下最大可能地减少风险损失
北京运通恒达科技有限公司
风险举例
6
北京运通恒达科技有限公司
第二部分 FMEA的分析思想
7
风险从何而来?
如何描述风险? 如何控制风险?
FMEA的思路
FMEA的效益
北京运通恒达科技有限公司
风险从何而来?
潜在的安 全危险
差的管理计划和 标准作业程序 差的工 程能力
8
未明确的 顾客期望
累计的风险
模糊的作 业标准 原材料散布
差的规格限 设备的故障 测量散布 (生产线上和 QC)
北京运通恒达科技有限公司
采用什么类型的FMEA ?
风险来源
31
设计上的缺陷
过程中的不足
“不正确”的使用
服务相关
设计FMEA d-FMEA 系 功 产 统 能 品 FMEA FMEA FMEA
过 程 FMEA (p-FMEA)
应 用 FMEA (a-FMEA)
服 务 FMEA (s-FMEA)
北京运通恒达科技有限公司
北京运通恒达科技有限公司
FMEA的其它几种叫法
PFMEA
Potential Failure Mode and Effects Analysis
5
PMEA
Problem Mode and Effects Analysis
FMECA
Failure Mode Effects & Criticality Analysis
2024版FMEA培训资料最新版(ppt14)

验证预防措施有效性
在实施预防措施后,需要对措施的有 效性进行验证,确保措施能够真正降 低风险。
制定预防措施
根据潜在风险,制定相应的预防措施, 如改进设计、优化工艺、提高材料质 量等,以降低风险发生的概率。
纠正措施选择依据探讨
进行FMEA分析
对关键工序进行详细的故障模 式分析,找出潜在的故障模式、 原因及影响。
组建FMEA团队
包括生产、技术、质量等相关 部门人员,共同进行FMEA分 析。
收集数据
收集历史故障数据、生产数据、 设备维护数据等,为FMEA分 析提供基础。
制定预防措施
针对潜在的故障模式,制定相 应的预防措施,如设备维护计 划、操作规范等。
FMEA培训资料最 新版(ppt14)
contents
目录
• FMEA概述与基本原理 • FMEA实施流程与步骤 • 失效模式与影响分析(FM) • 风险控制措施制定与实施 • FMEA在产品设计阶段应用案例 • FMEA在生产过程监控中应用案例 • 总结回顾与展望未来发展趋势
01
FMEA概述与基本原 理
经济性影响
评估失效对经济方面的 影响程度,如可能导致 生产停顿、维修费用增
加等。
运行性影响
评估失效对设备运行的 影响程度,如可能导致 设备性能下降、运行不
稳定等。
环境性影响
评估失效对环境方面的 影响程度,如可能导致 环境污染、资源浪费等。
04
风险控制措施制定与 实施
预防措施设计思路分享
识别潜在风险
通过因果图的方式,将问题与其原因进行关联,有助于直观地发现问题的根本原因。
FMEA授课讲义6934

设计FMEA 小组成员
❖ 在筹备样件期间开始 ❖ 设计工程师—通常的小组领导 ❖ 检验工程师 ❖ 可靠性工程师 ❖ 制造工程师 ❖ 最终服务工程师 ❖ 项目经理 ❖ 质量工程师 ❖ 顾客联系人 ❖ 其他,包括:销售、开发、过程、QA/QC等
permission.
FMEAs的关联
失效模式
后果
原因
SFMEA
问题的分支
问题
问题产生的原因
DFMEA 问题产生的原因来自 准确的后果定义 设计失效模式产
SFMEA
来自SFMEA
生的原因
PFMEA 问题产生的原因来自 和DFMEA相同 详细的过程失效
DFMEA
的后果
模式产生的原因
prepared by kingie, Not copy without permission.
FMEA 的益处
❖ 预防计划 ❖ 识别改变需求 ❖ 降低成本 ❖ 减少浪费 ❖ 降低保证成本 ❖ 降低无增值操作
prepared by kingie, Not copy without permission.
FMEA 的前提条件
❖ 选择适当的小组和有效的组织成员 ❖ 为每个产品/服务、过程/系统选择小组 ❖ 建立团队体系 ❖ 定义顾客和顾客需求/期望 ❖ 涉及/过程需求 ❖ 开发过程流程图**
❖在最初的DFMEA 中, 希望负责设计的工程师 能夠直接地、主动地联 系所有相关部门的代表。
❖ FMEA应成为促进不同部 门之间充份交換意見的 催化剂,从而提高整高 集体的工作水平。
prepared by kingie, Not copy without permission.
新版FMEA 勘误修订版培训资料
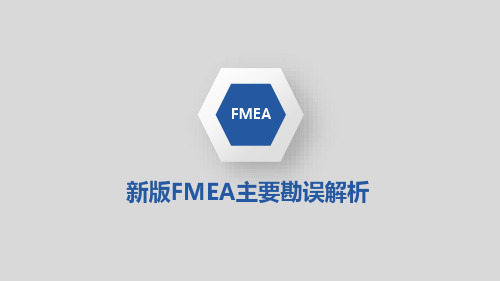
更正版本: StructureAnalysis: Process Structure 4M Elements Man (Operator) Machine (Greasing Device) Material (Grease) EnvironMent(Cleanliness) Operator Press Machine Sintered Bearing Cleanliness
功能树/网或功能分析表格和参数图(P图)
更正版本: Functiontree/net or function analysis form sheet and/or parameter diagram (P-diagram), as applicable功能树/ 网或功能分析表格 ,或参数图(P图) 若适用。
更正版本: Note: Occurrence can drop based on product validation activities 注:发生度可根据产品验证活动而降低( 去掉了10,9,8,7)
解读:在DFMEA发生度评分标准中,有测试或类似运 行条件下的现场经验后,会降低发生度。不仅仅只是降 低7分及以上的发生度。
新版FMEA主要勘误解析
章节2.5.9Table D3 DFMEA 探测度 D 原文:Detection Maturity Method for D=7: Proven test method for verification of functionality or validation of performance, quality, reliability and durability; planned timing is later in the product development cycle such that test failures may result in production delays for re-design and/or retooling
- 1、下载文档前请自行甄别文档内容的完整性,平台不提供额外的编辑、内容补充、找答案等附加服务。
- 2、"仅部分预览"的文档,不可在线预览部分如存在完整性等问题,可反馈申请退款(可完整预览的文档不适用该条件!)。
- 3、如文档侵犯您的权益,请联系客服反馈,我们会尽快为您处理(人工客服工作时间:9:00-18:30)。
– 设计 – 操作者 / 领班 – 质量 – 工程 – 采购 – 试验 – 供应商
PFMEA之具备事项
FMEA是早期预防失效及错误发生的最重要且最有效的 方法之一。
一个良好的FMEA必须具备:
第二:使用统计推论、模拟分析、同步工程及可靠度工程等以确认 及定义失效。
如果正确及适当地使用,FMEA方法会使评价行动更准确及更有效 率
FMEA之效益
◆指出设计上可靠性的弱点,提出对策 ◆针对要求规格、环境条件等,利用“纸上沙盘”演 练,
对不适当的设计,即时加以改善,节省无谓的损 失 ◆有效的实施FMEA,可缩短开发期限及开发费用 ◆FMEA发展之初期,以设计技术为考量,但后来的 发展,除设计阶段使用外,制造工程及检查工程亦 可适用
振动:不适用 湿度:0—100%
D-FMEA的准备——D-FMEA方块示意图
字母=零件 =接口,不相连
数字=连接方法
=附着的/相连的 =不属于此FMEA
零件 (功能) 零件编号
4
平板 E
5
+
开关 开/关
C
2
灯罩 A
1
电池 B
FMEA的步骤
子系统 潜在 潜在 失效 失效 模式 后果
功能 要求
后果是 什么?
模式和影响都得了考虑。
·确定过程缺陷,提出进一步的控制来解决问
题,通过… √消除或降低生产不可接受产品的频率。 √增强对不可接受产品的可探测度。
·确定关键特性和重要特性,以便编制完整的
制造控制计划。
·建立过程改进的优先顺序。 ·提供自动的过程设计文件,今后开发制造和
组装过程提供指导。
FMEA Team
D-FMEA的跟踪
• 对设计、图样进行评审,以确保建议的措 施得到实施,
• 确认更改已纳入到设计/装配/制造文件中, • 对设计FMEA、FMEA的特殊应用以及控
制计划进行评审。
过程失效模式和后果分析-PFMEA
• 目标 PFMEA的主要目的是减少制造风险,通过…
·帮助分析新的制造和装配过程。 ·确保存在的和潜在的制造和/或装配过程失效
1974出版Mil-STD-1629 FMECA
1985出版IEC812FMEA 1980出版Mil-STD-1629A
FMECA
FMEA类型
类别比较 时机
系统FMEA
设计FMEA
过程FMEA
早期概念及设计 产品于生产前制 生产/过程
阶段
造
分析
系统及子系统 产品
生产或过程
评估
系统间的功能及 交互影响
FMEA
潜在的失效模式及后果分析
What is FMEA?
FMEA是一种工程技术,用以定义、确认及消除在 系统上设计、过程及服务还没有到达顾客前已 知的或潜在的失效、问题等。
潜在的失效模式,是指过程可能发生的不满足过程要求和
/或设计意图的形式,是对某具体工序不符合要求的描述。
潜在的失效后果,就是失效模式对顾客的影响。 确定过程缺陷,提出进一步的控制来解决问题,预防缺陷
的发生。
FMEA的沿革
Grumman Aircraft Company
1950FMEA飞机主 操纵系统失效分析
Chrysler, Ford GM, ASQ, AIAG
1993出版FMEA手册 1995出版FMEA手册
Boeing & Martin Marietta Aerospace Company
ENVIRONMENT (HUMIDITY)
RAW MATERIAL
MIXER SPEED
Cause and Effects Matrix
INPUTS Heavies in Produc t Lights in Produc t Moisture in Produc t Acidity in Produc t Low Capacity From Unit Excessive Downtim e Material Losses Corrosion of Equipment Poor Reactor Performanc e
• 当既有的系统、设计、产品、过程或服务被考虑要改善时
• 当既有的系统、设计、产品、过程或服务的条件有新的应 用时。
PFMEA 实施流程
Process Map过程流程图
PAPERWORK
TURN STEAM ON TO DICY TANK
LOAD DMF
BILL OF MATERIALS ISO PROCEDURES REWORK
9
设计控制只有极少的机会能找出潜在的起因/机理及后续的失 效模式
8
设计控制有很少的机会能找出潜在的起因/机理及后续的失效 模式
7
设计控制有较少的的机会能找出潜在的起因/机理及后续的失 效模式
6
设计控制有中等的机会能找出潜在的起因/机理及后续的失效 模式
5
设计控制有中上多的机会能找出潜在的起因/机理及后续的失 效模式
频度
10 9 8 7 6 5 4 3 2 1
探测度 绝对不肯定 很极少 极少 很少 少 中等 中上 多 很多 几乎肯定
准则:设计控制可能探测出来的可能性
探测度定级
设计控制将不能和/或不可能找出潜在的起因/机理及后续的 失效模式,或根本没有设计控制
10
设计控制只有很极少的机会能找出潜在的起因/机理及后续的 失效模式
配合和外观/尖响和卡嗒响等项目不舒服。大多数顾客 (75%以上)能感觉到有缺陷。
配合和外观/尖响和卡嗒响等项目不舒服。50%的顾客能感 觉到有缺陷。
配合和外观/尖响和卡嗒响等项目不舒服。有辨识能力的顾 客(25%以下)能感觉到有缺陷。
无可辨别的后果。
严重度
10 9 8 7 6 5 4 3 2 1
失效发生的可能性
这是一种非常严重的失效形式,是在具有失效预兆的前提 下所发生的,影响到行车安全和/或不符合政府的法规。
车辆/项目不能运行(丧失基本功能)
车辆/项目可运行,但性能下降,顾客非常不满意
车辆/项目可运行,但舒适性/方便性项目的性能下降,顾客 不满意。
车辆/项目可运行,但舒适性/方便性项目的性能下降,顾客 有些不满意。
FMEA展开时机
• 依照FMEA定义,它是一种方法,消除或减少已知或潜在 问题,以强化顾客满意至最大极限。因此,为了要达成此 目的,展开FMEA的时机必须越早越好!
• 经由质量功能展开(QFD)已知某些资料时,就应立刻展 开FMEA
• 当设计新的系统、新设计、新产品、新过程、新服务时。
• 当现有的系统、设计、产品、过程或服务等不管是何种理 由,将要变更时
4
设计控制有较多的机会能找出潜在的起因/机理及后续的失效 模式
3
设计控制有很多的机会能找出潜在的起因/机理及后续的失效 模式
2
设计控制几乎肯定能找出潜在的起因/机理及后续的失效模式
1
风险顺序数(RPN)
风险顺序数是严重度(S)、频度(O)和探 测度(D)的乘积。即:
RPN=(S)×(O)×(D)
在某一特定的DFMEA范围内,RPN值(11000)可用于设计中可能出现的高见险事 项的排序。
Process Step Process Inputs
1 2 3 4 5 6 7 8 9 10 11
OUTPUTS
Total
139 Day Tanks Analysis
10 10 9 9
9
Reactor Cat./HF Ratio
7
Reactor Rxr Temperature
73 Lights RemovaC重与评价
消除故障模式
于构想设计时就预测可 能发生的故障,只要有 一丝丝的可能性的故障, 就全部列出。
针对故障模式排列优先 顺序,采重点指向,排 定重要故障模式优先处 理
以固有技术针对不希望看到 的重要故障模式,检讨处置 方式与提出建议,确认由试 验得到的实证及发生条件
D-FMEA的时间跨度 在一个设计概念最终形成之时
或之前开始
在产品开发的各个阶段中,当
设计有变化或获得信息增加时, 及时、不断地修改
在最终产品加工图样完成之前
全部结束
概念提出 /批准
项目 批准
样件
试生产
投产
策 划 D-FMEA开始的时机
策划
产品设计和开发
过程设计和开发
产品与过程确认 生产
反 馈、评 定 和 纠 正 措 施
Nation Aeronautics and Space Administration ( NASA)
1957工程手册中正式 列出FMEA程序
1960FMEA成功地 应用于航空计划
Defense Department
International Electrical Commission ( IEC )
指南的更改
-无功能 -部分功能/功能 过强/功能降级 -功能间歇 -非预期功能
怎样能 得到预 防和探 测?
该方法在探测 时有多好?
后果 无警告的严
重危害 有警告的严
重危害 很高 高 中等
低
很低
轻微
很轻微 无
评定准则:后果的严重度
这是一种非常严重的失效形式,它是在没有任何失效预兆 的情况下影响到行车安全或不符合政府的法规。
严 级 潜在失 频 现行控制
重 别 效起因/ 度
度 机理 S
O预 探 防测
探 R 建议 测 P 措施 度N D
责任及 目标完 成日期
措施结果
采取 S O D R