浅谈坯用干混色料性能对生产应用的影响
色料的生产控制对产品质量的影响
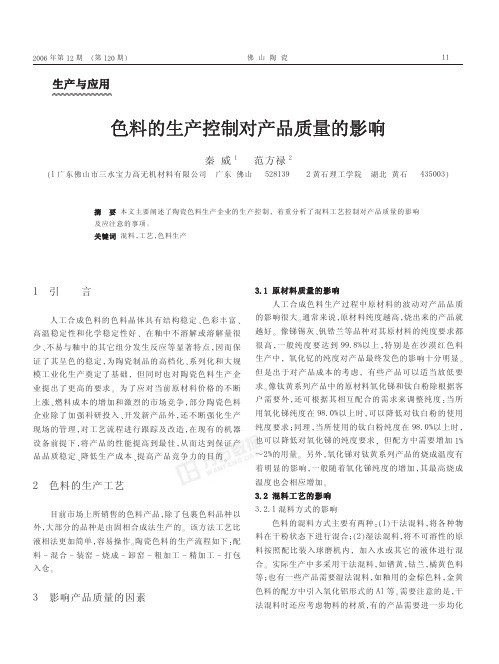
+ 混料 $ 工艺 $ 色料生产
&’’引
言
人工合成色料生产过程中原材料的波动对产品品质 的影响很大 % 通常来说 $原材料纯度越高 $ 烧出来的产品就 越好 % 像锑锡灰 #钒锆兰等品种对其原材料的纯度要求都 很高 $ 一 般 纯 度 要 达 到 --,./ 以 上 $ 特 别 是 在 沙 漠 红 色 料 生产中 $ 氧化钇的纯度对产品最终发色的影响十分明显 % 但是出于对产品成本的考虑 $ 有些产品可以适当放低要 求 % 像钛黄系列产品中的原材料氧化锑和钛白粉除根据客 户需要外 $ 还可根据其相互配合的需求来调整纯度 & 当所 用氧化锑纯度在 -.,%0 以上时 $ 可以降低对钛白粉的使用 纯度要求 ’ 同理 $ 当所使用的钛白粉纯度在 -.,%0 以上时 $ 也可以降低对氧化锑的纯度要求 $ 但配方中需要增加 $0
!’’工业固体废弃物
目前 # 在陶瓷行业中应用的工业固体废弃物主要有各
!!!!!!!!!!!!!!!!!!!!!!!!!!!!!!!!!!!!!!!!!!!!!!!!
或同一批次的产品没有色差 # 从而保证产品质量的稳定 $ 质的稳定和性能提高的作用更加重要 $
&’’结
语
(’ 素木洋一 ) 日 *+ 釉及色料 ),*+ 中国建筑工业出版社 #(-.!’ 俞康泰 + 现代装饰色釉料与装饰技术手册 ),*+ 武汉理工大学出
版社 #$---
陶瓷色料生产过程中对产品质量有影响的因素主要 集中在原材料 %混料 %烧成和加工等工艺 #各个工序都对产 品质量起着关键作用 $ 原材料的合理搭配可以在保证质量 的前提下 # 有效降低成本 & 合理的烧成制度可以保证产品 的性能达到最佳 &色料煅烧之前的混料工艺对产品最终品
干法混合生产工艺
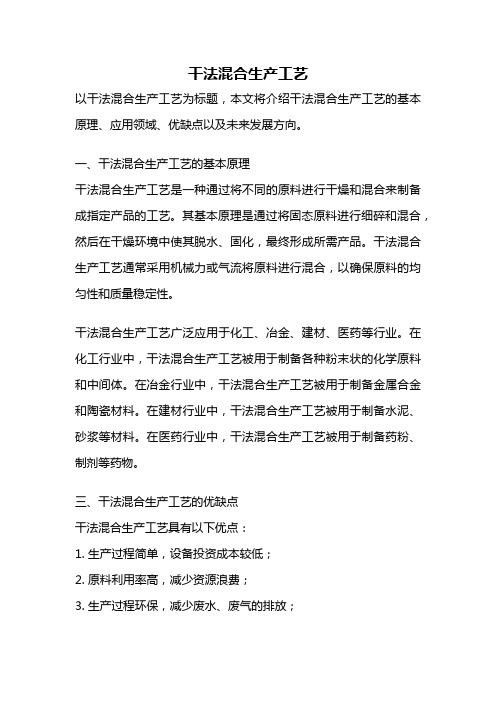
干法混合生产工艺以干法混合生产工艺为标题,本文将介绍干法混合生产工艺的基本原理、应用领域、优缺点以及未来发展方向。
一、干法混合生产工艺的基本原理干法混合生产工艺是一种通过将不同的原料进行干燥和混合来制备成指定产品的工艺。
其基本原理是通过将固态原料进行细碎和混合,然后在干燥环境中使其脱水、固化,最终形成所需产品。
干法混合生产工艺通常采用机械力或气流将原料进行混合,以确保原料的均匀性和质量稳定性。
干法混合生产工艺广泛应用于化工、冶金、建材、医药等行业。
在化工行业中,干法混合生产工艺被用于制备各种粉末状的化学原料和中间体。
在冶金行业中,干法混合生产工艺被用于制备金属合金和陶瓷材料。
在建材行业中,干法混合生产工艺被用于制备水泥、砂浆等材料。
在医药行业中,干法混合生产工艺被用于制备药粉、制剂等药物。
三、干法混合生产工艺的优缺点干法混合生产工艺具有以下优点:1. 生产过程简单,设备投资成本较低;2. 原料利用率高,减少资源浪费;3. 生产过程环保,减少废水、废气的排放;4. 生产效率高,生产周期短。
然而,干法混合生产工艺也存在一些缺点:1. 对原料的要求较高,需要选择适合干法混合的原料;2. 在干燥和固化过程中,可能会产生粉尘污染;3. 由于混合过程中无法调控温湿度等参数,可能导致产品的质量不稳定。
四、干法混合生产工艺的未来发展方向为了进一步提高干法混合生产工艺的效率和质量稳定性,未来的发展方向主要包括以下几个方面:1. 引入先进的机械力和气流混合设备,提高混合效果;2. 开发新型的干燥和固化技术,提高产品的质量和稳定性;3. 结合智能化技术,实现生产过程的自动控制和监测;4. 探索新的原料组合和配方,拓宽干法混合生产工艺的应用范围;5. 加强环境保护意识,减少粉尘污染和废水、废气的排放。
干法混合生产工艺是一种重要的制备工艺,广泛应用于化工、冶金、建材、医药等行业。
虽然该工艺存在一些缺点,但通过不断的技术创新和发展,可以进一步提高其效率和质量稳定性,实现更广泛的应用。
浅谈干法施釉和湿法施釉工艺
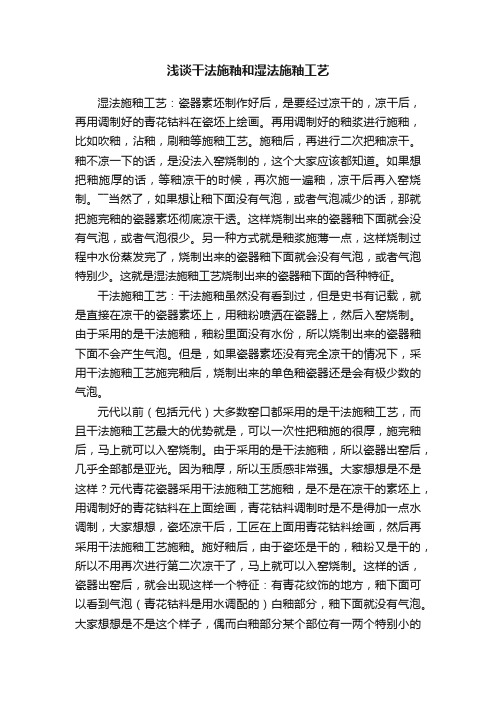
浅谈干法施釉和湿法施釉工艺湿法施釉工艺:瓷器素坯制作好后,是要经过凉干的,凉干后,再用调制好的青花钴料在瓷坯上绘画。
再用调制好的釉浆进行施釉,比如吹釉,沾釉,刷釉等施釉工艺。
施釉后,再进行二次把釉凉干。
釉不凉一下的话,是没法入窑烧制的,这个大家应该都知道。
如果想把釉施厚的话,等釉凉干的时候,再次施一遍釉,凉干后再入窑烧制。
――当然了,如果想让釉下面没有气泡,或者气泡减少的话,那就把施完釉的瓷器素坯彻底凉干透。
这样烧制出来的瓷器釉下面就会没有气泡,或者气泡很少。
另一种方式就是釉浆施薄一点,这样烧制过程中水份蒸发完了,烧制出来的瓷器釉下面就会没有气泡,或者气泡特别少。
这就是湿法施釉工艺烧制出来的瓷器釉下面的各种特征。
干法施釉工艺:干法施釉虽然没有看到过,但是史书有记载,就是直接在凉干的瓷器素坯上,用釉粉喷洒在瓷器上,然后入窑烧制。
由于采用的是干法施釉,釉粉里面没有水份,所以烧制出来的瓷器釉下面不会产生气泡。
但是,如果瓷器素坯没有完全凉干的情况下,采用干法施釉工艺施完釉后,烧制出来的单色釉瓷器还是会有极少数的气泡。
元代以前(包括元代)大多数窑口都采用的是干法施釉工艺,而且干法施釉工艺最大的优势就是,可以一次性把釉施的很厚,施完釉后,马上就可以入窑烧制。
由于采用的是干法施釉,所以瓷器出窑后,几乎全部都是亚光。
因为釉厚,所以玉质感非常强。
大家想想是不是这样?元代青花瓷器采用干法施釉工艺施釉,是不是在凉干的素坯上,用调制好的青花钴料在上面绘画,青花钴料调制时是不是得加一点水调制,大家想想,瓷坯凉干后,工匠在上面用青花钴料绘画,然后再采用干法施釉工艺施釉。
施好釉后,由于瓷坯是干的,釉粉又是干的,所以不用再次进行第二次凉干了,马上就可以入窑烧制。
这样的话,瓷器出窑后,就会出现这样一个特征:有青花纹饰的地方,釉下面可以看到气泡(青花钴料是用水调配的)白釉部分,釉下面就没有气泡。
大家想想是不是这个样子,偶而白釉部分某个部位有一两个特别小的气泡。
分析坯釉配方及烧成对辊棒痕的关系与直接影响

分析坯釉配方及烧成对辊棒痕的关系与直接影响做价值的传播者,一路同行,一起成长关于我们及时获得最新陶瓷行业信息资讯,掌握最实用的墙地砖生产技术知识,了解最新陶瓷/建陶/窑炉/瓷砖行业人才招聘!摘要分析了在烧成过程中影响砖坯变形的因素, 并对砖坯在窑炉烧成过程中各种受力导致辊棒痕产生的根源进行了详细受力分析。
采用高温显微镜法和热膨胀曲线, 在大生产条件下对比研究釉的熔融性能与坯釉膨胀系数等对砖形 (辊棒痕) 的影响, 认为釉料固化温度高低是导致辊棒痕产生的重要根源之一, 而釉面粘度、表面张力、光泽度是加强辊棒痕视觉的重要因素。
陶瓷砖的烧成是有液相参与的烧结过程,伴随着熔融、软化、收缩等一系列烧结现象的出现,因坯釉性能不同、烧结状态不同、窑内热气体传热速度不同等导致砖形随之变化,当这种变化超过一定范围就会成为缺陷或痕迹留在制品上,表现为可以测量到的变形或峰谷之间的光泽差异,即砖坯变形,而辊棒痕则是砖坯在运行的前半部平行于辊棒方向的波浪变形。
1砖坯在烧成过程中变形的影响因素烧成过程中砖坯变形影响因素和砖坯在行进过程的受力分析图,分别见图1、图2、图3、图4所示。
当已经出现轻微弯曲时的砖坯从辊棒间隙前进至下一条辊棒时,砖坯受力图如图3所示。
从图3中可以看出,砖坯在最软的时候,重力G使它向下掉弯,摩擦力F使它前进,同时F力有促使砖弯曲变形的趋势;砖坯在软化时与辊棒接触面增大;表面张力N可以将坯拉伸向上,当行进至下一根辊棒位置时,已经弯曲的砖坯还会受到辊棒对弯曲砖坯的瞬间阻力,受摩擦力的作用又会将坯拉伸至辊棒上。
当砖坯软化至冷却收缩时,重力G+L2+F使砖坯向下掉弯,L3 使砖坯整体向上凹。
在砖坯匀速通过,急冷风压力稳定情况下,L1使砖坯拉向上,L2在重力G与 L3和阻力的作用下,使砖坯掉角呈弯弧状。
砖坯冷却过程受力分析图如图4所示。
从图2、图3、图4可以看出, 重力G是始终存在的, 如何使砖坯在软化时高温粘度大, 减少变形这是涉及坯料配方的问题;同时釉料有加剧坯体软化的作用, 烧成制度对变形的影响也同样存在。
坯釉配方对陶瓷烧成及其质量的影响
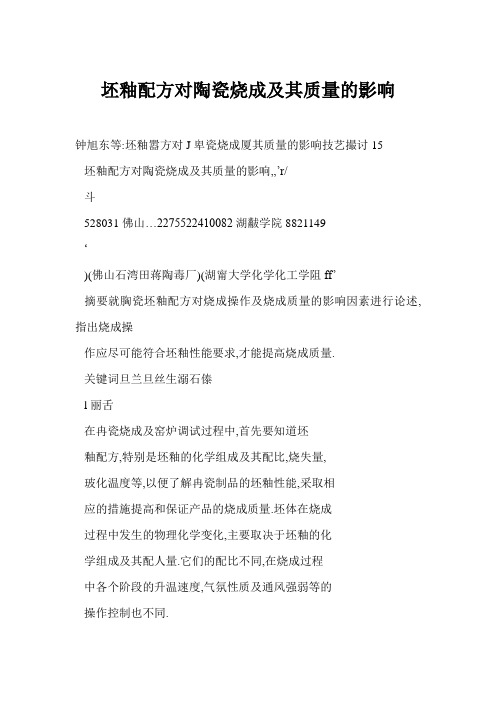
坯釉配方对陶瓷烧成及其质量的影响钟旭东等:坯釉嚣方对J卑瓷烧成厦其质量的影响技艺撮讨15坯釉配方对陶瓷烧成及其质量的影响,,’r/斗528031佛山…2275522410082湖黻学院8821149‘)(佛山石湾田蒋陶毒厂)(湖甯大学化学化工学阻ff’摘要就胸瓷坯釉配方对烧成操作及烧成质量的影响因素进行论述,指出烧成操作应尽可能符合坯釉性能要求,才能提高烧成质量.关键词旦兰旦丝生溺石傣l丽舌在冉瓷烧成及窑炉调试过程中,首先要知道坯釉配方,特别是坯釉的化学组成及其配比,烧失量,玻化温度等,以便了解冉瓷制品的坯釉性能,采取相应的措施提高和保证产品的烧成质量.坯体在烧成过程中发生的物理化学变化,主要取决于坯釉的化学组成及其配人量.它们的配比不同,在烧成过程中各个阶段的升温速度,气氛性质及通风强弱等的操作控制也不同.我国生产日用瓷,建筑瓷,卫生瓷,电瓷等的陶瓷坯料和釉料,其化学组成一般为SiO,Al,,FezOs CaO,MsO,K20,№2o和TiO2等;此外,有些还有Mn,,Pb,v,Ni,Cu,Zn,Co,Cr,Ba,P,Li等一些微量元素,这些微量元素的存在对烧成过程和烧成质量也产生一定的影响.本文就陶瓷坯釉的主要化学组成,它们的性质及其配人量对成瓷的影响进行讨论,以便使烧成操作尽可能符合坯釉性能要求,提高制品的烧成质量.2坯釉化学组成对烧成的影响2’1二氧化硅最纯的SiO晶体无色透明,称为水晶.熔点在1713℃.它是石英的主要成份.用作陶瓷原料的石英呈乳白色或灰色.坯料中SiO:是从石英,高岭土(或瓷土),长石中引入的.在长石质坯料中一般含65%一75%,釉料中含62%一75%.它在烧成过程中的1100—1200℃段,与一部分Al~Oa作用生成针网状的莫来石晶体,构成瓷坯骨架,增加瓷器的白度和机械强度;同时,还可以减少坯体在烧成过程中的收缩和变形:是产生玻璃液相不可缺少的成份.但坯料中古SiO:过多,泥料的可塑性就差,成型困难,烧成温度也很高.当坯料中SiO含量超过80%时,瓷器将出现自行炸裂现象.因为石英晶体在烧成过程中发生多次晶型转变体积随之发生变化.这种釉裂及坯裂均在烧成过程中及开窑后产生.由于石英晶体在烧成过程中发生多擞晶型转化.即:一石英一囊石英些一方石英里培硅石英1【573t:180-27哪碱碘聃这种转化又可分为慢速转化和快速转化二种:慢速转化,例如q一石英,~鳞石英,一方石英之间的相互转化,它们属于高温稳定的晶型排列于横的方向,由于它们在晶体结构上彼此不同,因此转化很慢.在慢速转化时虽然体积膨胀很大,但由于转变速度慢,时间长,体积膨胀不甚剧烈,而且在高温下坯体中由于有矿化剂存在,已经出现藏相,藏相的存在起缓冲作用,抵消了因体积膨胀应力所造成的破坏作用,所以危害不大.而快速转化,例如鳞石英的,p,晶型之间的相互转化,由于它们在晶体结构上彼此大致相似,因此转变速度较快.在这种转变过程中虽然体积膨胀较小,例如B一石英转变为一石英,体积膨胀0.8%.但由于转变速度快,来势猛,容易引起制品破坏.因此,在低温晶型转化温度阶段,例如573℃和180—270℃应注意缓慢升温或缓慢冷却,以避免因石英晶体转化而伴随的体积变化产生应力过于集中导致制品破坏.2’2三氧化二铝AI~O~耐火度很高,熔点在2050℃.它主要从l6江苏陶瓷.HANC,$UCERAMICS2OOO年6月第33喜第2期长石和高岭土中引入,坯料中的Al,是成瓷的主要成份,一般含l9%一24%,釉料中含¨%一15%.在高温下,它与SIOz作用生成奠来石晶:lIO0℃AI20,+siO2—-+A13?SiO2ll∞一I200~C2(A】2O3?SiO2)+A】3——÷3AI203?25iO2它构成瓷坯骨架提高瓷质的机械强度,化学稳定性及热稳定性.但是,坯料中含A1O,过多时,烧成温度要提高;当坯料中Al抑,含量低于15%时,则又降低烧成温度趋于易熔.当A1O,含量较多时,中火保温开始温度可迟一点,烧还原焰温度可高一些.如果在烧还原焰前,升温平稳,不进行中火保温,也不会产生起泡的毛病.2.3三氧化二铁三氧化二铁呈红褐色(猪肝色或砖红色),熔点在l560℃.它对瓷质的有害作用很大.瓷坯中含0.8%Fe2O,时,还原焰烧成后呈灰色;Fe20,含量大于1%时,呈黄色.Fe,含量必须在06%以下,烧成的瓷器才是白色.在氧化气氛中烧成时,0.35的Fe:0,已经出现明显的黄色.釉料中铁质影响更大, 要求含铁量在0.25以下以保证在一般烧成条件下烧成白色的瓷器.当瓷坯中Fe,含量较多时,必须采用还原焰烧成使FeO,还原成FeO.因为采用氧化焰饶成时, 在l230一l270℃之前Fe2O,是稳定的,当温度升高到ll50一l300℃时,Fe203按下式进行分解:6Fe2O,——qFejO?+O22Fe2O,———+4FeO+02生成Fe∞,和4FeO,放出大量的氧气.由于这时坯体内含有大量的液相而液相牯度又大,放出的氧气跑不出去使制品起泡和膨胀.这种现象常发生在坯俸碳紊烧得最不完全的地方,因为此处粘士微粒结合力减弱.如果采用还原焰烧成,在l000一l1CO℃坯体中的Fe03开始还原成FeO:Fe203+Co一2FeO+CO22Fe2O3+C——qFeO+CO2在坯体完全烧结之前此反应已结束.因此,在还原烧成时不会因为Fe0,分解而产生气泡;同时, FezO,变成FeO后产品色泽呈现”白里泛青”.采用还原焰烧成还有降低熔质牯度的作用,因而可以加速制品的烧结.此外,还可以促使硫酸盐在熔釉前得到充分的分解,避免瓷件起泡和膨凸. 为了保证氧化铁在液相开始大量产生前进行还原,还原焰开始温度比临界温度降低40—50~Co FeO,在棕色或红色釉料中是一种主要的着色荆,它在颜色釉中由于氍人量的多少不同而呈黄, 棕,红色.2.4氧化钾,氧化钠氧化钾和氧化钠是长石中引入的,长石有如下几种:钾长石:K?Al2O,?6SiO2;钠长石:Na2O?Al2O,?6SiO2;钙长石:CaO?Al20,?2O2.其中,钾长石最好,但难找到纯的钾长石,往往都是几种长石混合存在,如钾钠长石,钠钙长石.长石属非可塑性原料在坯料中起瘠化作用,可减少坯体收缩和干燥时间.长石是熔剂矿物,在烧戚越程中可降低坯体烧成温度.加热后成玻璃液相熔解游离石英及Al抑,生成硅酸一氧化铝一碱土金属氧化物三元系统的玻璃状态物质,使莫来石针状结晶继续增长.CaO+SiO2—-+Casj03(液相)K20+sjO2—-+K2SiO3(液相)Na2O+Si0=—-+Na2SiO3(液相)Al3+SiO2—-+AJ20,?Si022(Al203?Si02)+Al203—-+3Al203?2SiO2适当的长石熔成玻璃态后填充各结晶颗粒之间使坯体致密无空隙,提高瓷件的机械强度.当坯料中含SiO和AI:O,过多时.适当配人长石可使烧成温度降低.但长石质过多在烧成中会产生如下的缺陷:a.坯件中长石质过多,造成玻璃液相过多,烧成后瓷件冷热性能差,容易炸裂,机械强度低.b.烧成温度低且烧成范围狭窄,不能快速升温,使烧成操作带来困难;烧成温度略高一点,则制品产生变形和过瓷化现象.因此,坯料中长石用量必须适当,在配料中控制Na抑含量在1%以下,钾钠总量不超过5%为宜,否则会急剧降低烧成温度和热稳定性.五5氧化镁氧化镁星白色粉状,熔点在28C0~C,耐火度高.在坯釉中少量引人MgO,助熔剂作用比较强,使用钙和镁的化合物助剂时,可以在较低的温度下(与长石比较)烧结或产生熔融现象.当Mgo含量过多会使瓷器透明度降低.在长石质瓷中Mgo含量过多产品产生龟裂.在长石质瓷坯料中Mgo含量极钟旭末等:坯釉配方对陶t烧成度其质量的彰响技艺柳t17 小(一般在1%以下),主要用于釉料(一般含2%一5%).釉料中用MO作熔剂,釉的玻化温度范围广,烧成温度易于控制;同时,可提高瓷质强度.用MgO作熔剂之釉强度好,滑石釉就是按这个道理采用的.但是纯粹的滑石耐火度太高,现代采用白云石即CaCO,,Mgco的复合盐类Mg(C03)代替,可使玻化温度及机械强度得鲴良好的性能,烧成操作易于控制.土6氧化钙氧化钙熔点为2570℃,在坯料中一般要求含量越少越好(在l%以下).在釉料中引入少量的CaO,它与SiO:作用生成稳定的硅酸钙使釉呈好的机械强度和光泽.高温下釉易于流动,低温时增加釉的牯度.釉料中一般古0.3%一9%.但CaO含量超过18%会使釉面变得无光,瓷件的强度降低, 熔融范围变窄,如果在烧成操作中掌握不当易产生吸烟,发黄等毛病.在配釉时,不应单独取caC0,作熔剂,因为它作熔剂时中火保温要早开始早结束.开始烧还原焰温度在95℃以下.停火时,温差不能过大;还原时, 还原焰不能过强,过强易产生吸烟;过弱又易严生形变,烧还原焰温度过高易产生赤变;过低,CaCO, 又难于分解完全,易产生瓷泡.2.7氧化钛氧化钛是陶瓷制品中有害杂质,在烧成中起加深铁质的着色作用.在高温还原气氛中,部分TiO 被还原成BO,呈蓝色到紫色.在还原气氛中可能形成组成为FeO?Ti0:的尖晶石(在H中由12o0℃)呈深黑色.但是,在氧化气氛中不能形成尖晶石.由于TiO使瓷质呈不好的色泽.因此在坯料中应控制TiO含量在0.2%以下.3烧失量对烧成的影响烧失量是指在1000~C以下有机物质分解,水分蒸发所失去的重量.烧失量大时,坯体总收缩事增大,容易使制品产生变形.I~ttt:,在烧成操作中要注意中火保温时间长些,升温速度不能过快,保沮时.通风要强;烧失量少时,可减少保沮时问或减弱通风,保温时间,通风速度可略快些.坯料中,要求烧失量要小.4玻化温度对烧成的影响在烧成操作中,除了要了解坯釉化学组成的性质外.还必须了解玻化温度对烧成的影响,才能更好地控制止火温度.影响玻化温度的因素主要有Ti02?Ah03的配比和熔剂含量,当TiO和Al,含量较多时,烧成温度高;当溶剂多时,烧成中玻璃液相生成较多,液相生成的温度亦较早,有能使烧成温度降低的好处, 同时,可使瓷质致密;但液相过多,瓷件的机械强度,冷热性能降低.停火温度决定于坯釉的玻化温度范围,玻化范围广时,停火温度范围大,反之停火温度范围小.所谓停火温度范围,是指在正常停火温度以下或以上某温度点,在这个范围内停火能保证产品不生烧,不过火,瓷质性能良好.当窑内温差大时,停火温度范围必须缩小,最低和最高点要向正常停火点靠拢.5结语综上所述,陶瓷配方对烧成及其产品质量的影响因素主要有坯釉化学组成及其配比,烧失量,玻化温度等.坯釉的化学组成及其配比不同,烧成后的瓷件性能不同.因此,坯釉配方应严格控制坯釉的化学组成及其配入量,使其尽可能达到最佳盼坯釉性能.同时,在烧成操作中,必须根据不同的坯釉性能制订合理的烧成翩度,使烧成操作尽可能符合坯釉性能要求,才能提高陶瓷的烧成质量. EffectsofBatchinRofBodyandGlazeonCeramicFiringandQuality ZhongXudongHitghirong(528031FoshanShishanGardenPlotCeramicsFactory)(410082HunanUnive rsityChemistryCombinationInstitute) AbstractTheefrectsofhatchingofbodyandghzeOilfiringoperationandfiringq ualityhavebeendiscussed.Therearehigherqua1ityfiringceramicswhentheoperationoffiring kilnmeetthere-quirementsof西azeandbodyaspossible. KeywordCeramicsGlaze—bodyFire.。
浅析原料陈化处理对制砖产品质量的影响
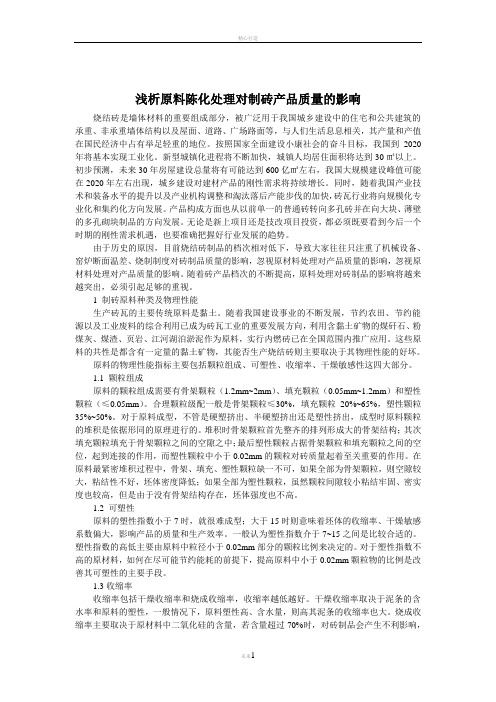
浅析原料陈化处理对制砖产品质量的影响烧结砖是墙体材料的重要组成部分,被广泛用于我国城乡建设中的住宅和公共建筑的承重、非承重墙体结构以及屋面、道路、广场路面等,与人们生活息息相关,其产量和产值在国民经济中占有举足轻重的地位。
按照国家全面建设小康社会的奋斗目标,我国到2020年将基本实现工业化。
新型城镇化进程将不断加快,城镇人均居住面积将达到30㎡以上。
初步预测,未来30年房屋建设总量将有可能达到600亿㎡左右,我国大规模建设峰值可能在2020年左右出现,城乡建设对建材产品的刚性需求将持续增长。
同时,随着我国产业技术和装备水平的提升以及产业机构调整和淘汰落后产能步伐的加快,砖瓦行业将向规模化专业化和集约化方向发展。
产品构成方面也从以前单一的普通砖转向多孔砖并在向大块、薄壁的多孔砌块制品的方向发展。
无论是新上项目还是技改项目投资,都必须既要看到今后一个时期的刚性需求机遇,也要准确把握好行业发展的趋势。
由于历史的原因,目前烧结砖制品的档次相对低下,导致大家往往只注重了机械设备、窑炉断面温差、烧制制度对砖制品质量的影响,忽视原材料处理对产品质量的影响,忽视原材料处理对产品质量的影响。
随着砖产品档次的不断提高,原料处理对砖制品的影响将越来越突出,必须引起足够的重视。
1 制砖原料种类及物理性能生产砖瓦的主要传统原料是黏土。
随着我国建设事业的不断发展,节约农田、节约能源以及工业废料的综合利用已成为砖瓦工业的重要发展方向,利用含黏土矿物的煤矸石、粉煤灰、煤渣、页岩、江河湖泊淤泥作为原料,实行内燃砖已在全国范围内推广应用。
这些原料的共性是都含有一定量的黏土矿物,其能否生产烧结砖则主要取决于其物理性能的好坏。
原料的物理性能指标主要包括颗粒组成、可塑性、收缩率、干燥敏感性这四大部分。
1.1 颗粒组成原料的颗粒组成需要有骨架颗粒(1.2mm~2mm)、填充颗粒(0.05mm~1.2mm)和塑性颗粒(≤0.05mm)。
合理颗粒级配一般是骨架颗粒≤30%,填充颗粒20%~65%,塑性颗粒35%~50%。
色母粒用色料的相关要求

色母粒用色料的相关要求前言色母粒是一种采用高浓度色料和载体混合而成的塑料配方,通常用于塑料制品的着色。
在尽可能保持色泽稳定和均匀的前提下,选择适当的色料对于色母粒的制作显得尤为重要。
本文将介绍色母粒用色料的相关要求,以供参考。
色料的选择稳定性色母粒用色料应具有较高的稳定性,经过加工后色泽不会褪色、变质或分解。
稳定性是一种持久的特性,必须经过各种严格的分析和试验来验证。
均匀度色母粒用色料必须具有良好的均匀度,以确保色母粒的每个颗粒都具有均匀的颜色。
这要求色料具有优异的溶解和分散性能,特别是在高浓度色母粒配方中。
兼容性色料必须与载体材料兼容,不会在加工过程中分离或出现其他问题。
色料的选择与载体材料密切相关,因此需要进行充分的试验和分析,确定最佳的色料选择方案。
涂布性和附着力涂布性是指色母粒加工过程中色料的涂布性能。
适合加工的色料应该具有良好的涂布性,使得色母粒可以均匀涂布在材料表面。
附着力则是指色母粒与材料表面之间的粘附能力,应具有良好附着力,以确保色母粒在加工和应用过程中不会脱落或者刮擦掉。
易于加工色料应该易于加工,以确保色母粒的加工过程稳定、可靠。
过于粉末化的色料会在加工过程中粘在生产设备上,导致生产中断,并大大影响加工质量。
因此色母粒用色料应该是易于流动、分散,且不会快速降解的粉末。
通量控制色母粒用色料的颜色通量应该准确控制,以确保加工的成品颜色稳定、一致。
颜色机理和控制精度会影响颜色通量的控制,而通量的准确控制可以通过实验室测试和精确计量来实现。
结论总的来说,色母粒用色料需要具备较高的稳定性、良好的均匀度、兼容性、涂布性和附着力、易于加工以及准确控制的颜色通量。
在实际生产中,应当充分考虑载体材料类型和颜色要求等因素,综合确定最佳的色料选择方案。
配合饲料加工工艺对产品质量的影响

配合饲料加工工艺对产品质量的影响
饲料加工工艺对产品质量有着重要的影响。
不同的加工工艺会对产品的口感、营养成分、储存稳定性、消化吸收率等方面产生影响。
以下将从几个方面探讨饲料加工工艺对产品质量的影响。
加工工艺会影响饲料的口感和颗粒度。
饲料经过适当的研磨和造粒处理,颗粒的大小均匀度会得到提高,这样动物在食用时更容易咀嚼和吞咽,提高了饲料的口感。
相反,如果加工工艺不当导致颗粒过大或过小,可能会影响动物对饲料的摄食和消化吸收能力。
加工工艺对饲料的营养成分也有一定的影响。
加工过程中可以通过破壁、蒸煮等方式使某些有机物质更易被动物吸收。
对于植物性蛋白质饲料,经过脱脂处理能够减少抗营养因子的含量,从而提高蛋白质的利用率。
加工工艺还可以破坏一些酶的活性,从而降低饲料中的抗营养因子的含量,改善饲料的营养价值。
加工工艺还可以改善饲料的储存稳定性。
将饲料进行干燥处理可以降低其含水量,减少微生物和霉菌的繁殖,延长了饲料的保质期。
加工工艺还可以通过添加防腐剂等方式保护饲料的品质,防止饲料变质。
加工工艺还可以提高饲料的消化吸收率。
对于干燥颗粒饲料,研磨和造粒处理可以增加饲料的比表面积,提高消化酶的接触面积,有利于饲料中营养成分的消化吸收。
加工过程中还可以通过破壁处理等方式改善饲料中纤维素的消化,提高动物对纤维素的利用率。
- 1、下载文档前请自行甄别文档内容的完整性,平台不提供额外的编辑、内容补充、找答案等附加服务。
- 2、"仅部分预览"的文档,不可在线预览部分如存在完整性等问题,可反馈申请退款(可完整预览的文档不适用该条件!)。
- 3、如文档侵犯您的权益,请联系客服反馈,我们会尽快为您处理(人工客服工作时间:9:00-18:30)。
关键词 : 通体大理石 ; 干混色料 ; 检测方法 ; 控制指标
1 前言
2 0 1 6 年 的佛 山春季 陶博会上 。通体 大理石 瓷砖无 疑 是全场最闪耀的产品之一 ,近 2 0 家陶企的集体推出, 让
响到色料 的呈色特 征和呈 色强度 ,为产 品 的主要检验 项 目。标准草 案规定要检测色料 的 D1 0 、 D 5 0 、 D 9 0和 D1 0 0 。
( 5 ) 釉 面缺陷和温度 目前市 场流行 的深色 系列 通体大 理石 产 品 .特别 是
对坯体干混 色料 而言 . 一般采用筛分析 进行粗放型检 黑色 、 棕 色等 , 在 色料 比例 增加 较 多 的情形 下 , 更 容 易在 比如 釉 面针孔 、 分层 开裂 、 验即可, 具体规定坯用色料过 3 2 5目 筛。 筛余不大于 1 . 0 %。 相对 应工 序 出现潜 在 的缺 陷 , 温度 明显 变化引起 的砖型和 收缩的波动 等。因此 , 除 了常 ( 3 ) 返潮性 、 流动性 和分 散性
如 性 ,直接 与普 通陶瓷 坯体粉 料混合 ,在粉 料颗 粒表 面着 混 色料 的 主要检 测 方法 和关 键 控制 指标 主要有 哪 些 ; 色, 大大简化 了有 色粉料 的制备工 艺 , 达 到 了优 化生 产工 何 对坯用 干混色 料原料进 行质 量控 制和验 收分 析 ;如何
根据检测 数据对 原料性 能进行有 效评 价并 指导 生产 和工 序的目的, 同时也降低了生产制造成本与管理成本。 坯 用干 混工艺在 国内墙 地砖企 业应 用 已有 十几 年历 艺参数调整。本文将围绕 以上问题展开重点分析和探讨 有不 当之处恳请行 业专家指 正 。 史, 具有 省 工序 、 低库 存 、 易转 产 、 环保 等 多方 面优 势 , 特 交流 ,
4 . 1检测的主要设备 及仪器 工序检测 的主要设备及 仪器有快 速球磨 机 、 打饼器 、 电子天平 、 色差仪、 加湿器、 湿度计 、 干燥箱 、 振动筛、 流速
其 中: W一水分含量 ; g 一 试样重 ; g 厂 干试 样重
干混色 料含水率 的大小对 于干混色料 的分散 性影 响
3 0 0 ~ 6 0 0 包 以 内共取至少 6 个 的研究最近进 展 ,总结 出如下几个 主要 的关键 技术 指标 在卸 货过程或待检 区取样 。 点 ,采 取上 中下层 各取 2个 点 ; 6 0 0 ~ 1 0 0 0包 共取 至少 8 坯用 干混色料 的验 收关键 过程控制指标见表 2 。 个点。 上 中下层 各取 3 个点, 每 包每个 点取样 大概 为 2 0 ~
表 1常用坯用干混色料 的品种 、 结构和使用量排名1 4 1
3 坯用干混色料性能关键技术指标
样, 抽取 的色料检验 完后放在指定 位置保存 备案 , 保 存 时 间l 2 个月。
. 3 取抽样 笔者查 阅了大量近年来 与坯用 色料分类命 名 与检测 4 取样 方法 :原 料 到厂后 由物控 组负 责抽 取样 品 。 需 验 收等主题相关 资料 ,结合 近年来行业 在 于混色料 领域
4 坯用干混色料验 收主要方法
r 艟橙 嚣、 、 l B ' c , D 匹 ) I
一
3 0 g 阎 。 4 . 4关键指标简介
( 1 ) 含水率 用精度 0 . 0 1 g 的电子天平称取 5 0 g 试样 于不锈钢小
, 锵 —一 入 仓 I
黼. {
有 行业 人士 预测 , 到 现 在 的 陶瓷砖 粉 料大 多都 是通 过湿 法 工艺 制 备 . 有 这款 新兴 产品进 发出强大 的生命 力 , 通 体大理 石瓷砖将 迎来 全 面爆 发 期 , 生产 厂家 色粉料 ( 或 称 色泥 、 色粒 ) 也 是 通过 湿法 工 艺将 色料 与坯 今年 年底 , 越来 料配方 料加水球 磨 喷雾 干燥造 粒 。由于在 生产制 造过 程 或达 上百家 。正是看 到这 一产 品的风 向和市场潜力 , 中, 有 色粉料 的使用量 小 、 品种多 , 要 求储存 系统 复杂 , 加 越 多的色釉 料企业 重新将 目光 瞄向 干混色 料 .但 从 现 阶 国内干混色料 的技术水平仍 然 良莠不 齐 。 对 于生 工过 程经 常需 要洗 球 洗塔 ( 球 磨 机与 喷雾 干燥 塔 ) , 造 成 段来 看 , 如何 区别坯 用干混 色料 和常规 坯用 色料 , 干 诸多不 便 。干混色料是 利用其 相较 于普通 色料 的高分 散 产 企业来 说 .
别适 合个性 化定制 和快速 排转产 .近年来 对 陶瓷 色料 的 表 面改性技术 和加 工工艺 的进展很 快 .为适 应抛光 砖二
常用坯用干混色料 的种 类
常用坯 用干混 色料 的种类见 表 1 。
次坯用干粒 料等装饰 材料的需求直 线上升 。【 1 】
比较大 。 水分 太大色 料容易结块 起色斑 , 严 重影 响产品档 杯、 秒表、 不锈钢盘 、 量筒 、 窑炉、 不锈钢碟 、 放射性检测仪 次和效果 , 一般最好 控制在 l %以内。 等。 ( 2 ) 筛余 4 . 2 标准样与原料备案管理 陶瓷色料是一种粉体 . 其颗粒特征及颗粒分布直接影 已定点采 购 的干混 色料 由物控组 建立 相对应 的标准
l 饶 后 理 化 l 螭I
黻一
1
【 潜一
碟中, 放 入烘箱 中 ( 一 般设定 温度 1 2 0 + 5 %) , 烘于 至恒重
越 濯 约1 h , 烘 干的试样重 为 g 克, 水分计算公式为 :
W =g l - g 2 x1 0 0 %
g l
图 1坯用干混色料检验验收流程
浅谈坯用干混色料性能对生产应用 的影 响
陈志川
( 东莞市唯美装饰材料有 限公 司 , 东莞 5 2 3 0 0 0 )
摘 要: 本文阐述了在陶瓷砖生产和开发实践中坯用干混色料性能指标
对生产应用影 响关 系 ,重点探讨 企业如何对坯用干混色料原料 进行质
量控制和验收分析 , 如何根据检测数据对原料性能进行有效评价 , 指导