MRP通用计算公式
MRP计算原理

MRP计算原理:根据主生产计划(MPS)、库存计划、物料清单(BOM),制定物料需求计划(MRP)主要公式:毛需求量=独立需求量+相关需求量计划库存量=上期库存量+本期订单产出量+本期预计入库量-毛需求量净需求量=本期毛需求量-上期库存量-本期预计入库量+安全库存量净需求量=毛需求量+已分配量- 计划收到量-现有库存量作个转换或许就很容易理解了:净需求量=毛需求量-[(现有库存量-已分配量)+计划收到量]毛需求量:总共需要的需求量[(现有库存量-已分配量)+计划收到量]:目前可满足的需求量净需求量:还需要满足的需求量MRP计算是对所有零件进行“供给”和“需求”的平衡计算。
计算的顺序按照零件的低阶码由小到大顺序平衡计算。
其中不能平衡掉的零件“需求”需求量,是MRP的计算结果。
MRP的计算结果分“外购件”和“自制件”两类,分别对应于零件的外购、自制两类属性。
其中,“外购件”的采购时间是需求时间提前一个供应商的交货周期;“自制件”的生产时间有两种情况:1. 如果该项对应的需求为独立需求,则开工时间按照其需求时间提前一个其BOM的生产工期时间。
2. 如果该项对应的需求隶属某成品,则其开工时间按照隶属成品的工艺路线计算提前时间。
MRP的计算分以下几个步骤:1. 展开需求成品的BOM,获得单位成品的物料需求。
需求成品主要源于MPS计算结果、生产任务、未分解任务的工令单。
2. 展开需求成品的工艺路线,获得单位成品的作业需求。
3. 展开需求成品的资源需求,获得单位成品的资源需求。
4. 需求成品需求数量和时间于步骤1展开的BOM交叉乘积,获得展开后实际的物料需求、作业需求和资源需求。
5. 按照优先级顺序:“未分解任务的工令单、生产任务、MPS计算结果”,计算作业的“开工时间”、“完工时间”;以及对应资源的需求时间,并且把作业需求量和资源需求量按时间比例分解到每一个工作日。
6. 计算作业的“开工时间”、“完工时间”时,系统按照【系统参数表】中的“生产排程约束”参数是否为1来判断是否考虑工作中心的“饱和日最低负载率”来计算有限能力排程,如果参数为0,系统则按企业是无限生产能力来排程。
MRP运算
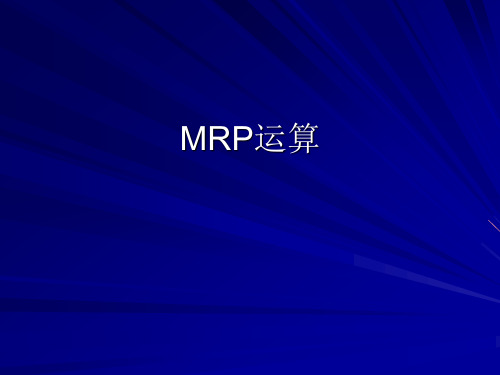
3 库存信息,物料可用量
4 还缺什么?何时定货? 4 建议的加工及采购计划
(量)
(期)
制造业的通用公式 (生产什么 用到什么) - 已有什么 = 还缺什么
快速运算
(逐级展开)
X A (1) C (2) O (1)
X
时段
MPS 计划产出量 计划投入量
A
时段
MRP 计划产出量
计划投入量
加
工C
计时段 划 计划接收量
– 根据计划产出量、提前期和合格率计算的投入数量 – 安排产品什么时候开始生产;
毛需求量
净需求量
客戶需B求rowser
销售预销测售部门订单
预计可用 库存量
计划投入量
计划员
工厂
生产
计划产出量
入库
发运
成品仓库
计划接收量
返回
结构层次 0
10000
方桌 销售X件
件 1.0
独立需求件 相关需求件
产品结构树
X[1]
Y[1]
MRP
MPS
B(1)
C
D(2)
B(1)
U
E(2)
MRP
B(3) F(3)
X
提前期=1 批量=1 现有量=0
时段 4 5 6 7 89
计划产出量
10
计划投入量
10
时段 毛需求
4 5 6 7 89 10
H(3) F(3)
Y
提前期=1 批量=1 现有量=0
时段 4 5 6 7 89
计划产出量
10
10
10
10
10
5
提前期=1
现有量=0
1 2 3 4 5 6 7 8 9 10 11 12
MRP计算原理

MRP计算原理:根据主生产计划(MPS)、库存计划、物料清单(BOM),制定物料需求计划(MRP)主要公式:毛需求量=独立需求量+相关需求量计划库存量=上期库存量+本期订单产出量+本期预计入库量-毛需求量净需求量=本期毛需求量-上期库存量-本期预计入库量+安全库存量净需求量=毛需求量+已分配量- 计划收到量-现有库存量作个转换或许就很容易理解了:净需求量=毛需求量-[(现有库存量-已分配量)+计划收到量]毛需求量:总共需要的需求量[(现有库存量-已分配量)+计划收到量]:目前可满足的需求量净需求量:还需要满足的需求量MRP计算是对所有零件进行“供给”和“需求”的平衡计算。
计算的顺序按照零件的低阶码由小到大顺序平衡计算。
其中不能平衡掉的零件“需求”需求量,是MRP的计算结果。
MRP 的计算结果分“外购件”和“自制件”两类,分别对应于零件的外购、自制两类属性。
其中,“外购件”的采购时间是需求时间提前一个供应商的交货周期;“自制件”的生产时间有两种情况:1. 如果该项对应的需求为独立需求,则开工时间按照其需求时间提前一个其BOM的生产工期时间。
2. 如果该项对应的需求隶属某成品,则其开工时间按照隶属成品的工艺路线计算提前时间。
MRP的计算分以下几个步骤:1. 展开需求成品的BOM,获得单位成品的物料需求。
需求成品主要源于MPS计算结果、生产任务、未分解任务的工令单。
2. 展开需求成品的工艺路线,获得单位成品的作业需求。
3. 展开需求成品的资源需求,获得单位成品的资源需求。
4. 需求成品需求数量和时间于步骤1展开的BOM交叉乘积,获得展开后实际的物料需求、作业需求和资源需求。
5. 按照优先级顺序:“未分解任务的工令单、生产任务、MPS计算结果”,计算作业的“开工时间”、“完工时间”;以及对应资源的需求时间,并且把作业需求量和资源需求量按时间比例分解到每一个工作日。
6. 计算作业的“开工时间”、“完工时间”时,系统按照【系统参数表】中的“生产排程约束”参数是否为1来判断是否考虑工作中心的“饱和日最低负载率”来计算有限能力排程,如果参数为0,系统则按企业是无限生产能力来排程。
金蝶MRP计算公式相关参数解释
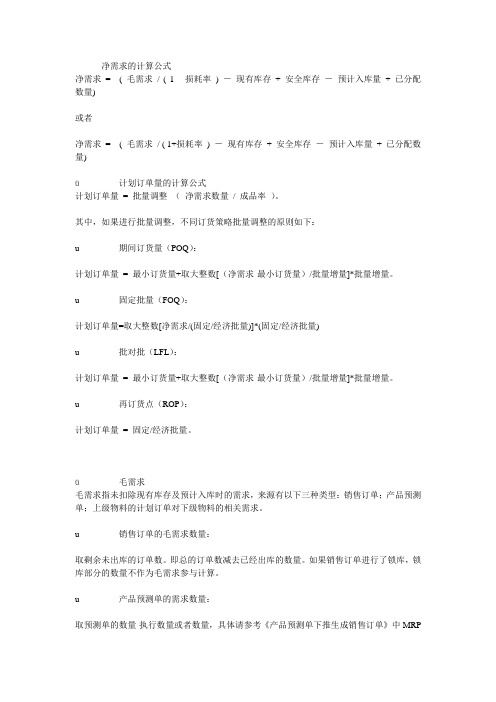
净需求的计算公式净需求= ( 毛需求/ ( 1 - 损耗率) -现有库存+ 安全库存-预计入库量+ 已分配数量)或者净需求= ( 毛需求/ ( 1+损耗率) -现有库存+ 安全库存-预计入库量+ 已分配数量)ü计划订单量的计算公式计划订单量= 批量调整(净需求数量/ 成品率)。
其中,如果进行批量调整,不同订货策略批量调整的原则如下:u 期间订货量(POQ):计划订单量= 最小订货量+取大整数[(净需求-最小订货量)/批量增量]*批量增量。
u 固定批量(FOQ):计划订单量=取大整数[净需求/(固定/经济批量)]*(固定/经济批量)u 批对批(LFL):计划订单量= 最小订货量+取大整数[(净需求-最小订货量)/批量增量]*批量增量。
u 再订货点(ROP):计划订单量= 固定/经济批量。
ü毛需求毛需求指未扣除现有库存及预计入库时的需求,来源有以下三种类型:销售订单;产品预测单;上级物料的计划订单对下级物料的相关需求。
u 销售订单的毛需求数量:取剩余未出库的订单数。
即总的订单数减去已经出库的数量。
如果销售订单进行了锁库,锁库部分的数量不作为毛需求参与计算。
u 产品预测单的需求数量:取预测单的数量-执行数量或者数量,具体请参考《产品预测单下推生成销售订单》中MRP计算时,需求数量的取数原则。
u 上级物料的计划订单对下级物料的相关需求:取审核的计划订单的建议订单量ü已分配量任务单计划确认字段为“Y”,单据状态为“计划”或“确认”或“下达”且作废标志不为“Y”的才计入已分配;已分配量指被其他销售订单、生产任务占用的物料数量,包括以下几种类型:u 拖期的销售订单(订单剩余数量);u 生产任务、委外订单相关联的投料单中没有领用物料的数量;u 物料替代清单中替代料的实际替代量。
ü预计入库量任务单计划确认字段为“Y”,单据状态为“计划”或“确认”或“下达”且作废标志不为“Y”的才计入预计入库量;预计入库单据包括以下几种类型:u 生产任务单和委外订单(总计划生产数-已完工入库),在计算预计入库量时,联副产品也可以作为预计入数量;u 采购申请单(数量-审核的采购订单数,采购申请单行关闭的不考虑)u 采购订单(总的订单数- 已入库数量)u 计划订单(建议订单量)u 物料替代清单(被替代料的实际需求量)。
MRP运算

一、MRP运算(Material Requirement Planning),它的感化是将指定的订单中所须要的原材料的用量做统计,以使临盆部分、仓库明白得当前临盆这些产品须要若干的原材料,这是因为在一样的工业企业里,产成品它是有专门多的原材料构成的(即在ERP里称之为BOM),然则鄙人订单时,一样只会选择某一个产成品,而可不能列出它是由哪些原材料构成的,只是到临盆部分时,他们所要关怀的是临盆产品时所需的原材料数量,而并非单单的产品数量,因此现在MRP运算的感化能够表现出来了。
二、全然逻辑净需求=毛需求+估量出-估量入-期初库存+安稳库存可按自由项匹配响应的BOM分化,如找不到响应的BOM,体系按默认版本BOM分化虚项及生成子订单物料不生成筹划订单,按净需求分化下级物料三、MRP的全然义务1.从最终产品的临盆筹划(自力需求)导出相干物料(原材料、零部件等)的需求量和需求时刻(相干需求);2.依照物料的需求时刻和临盆(订货)周期来确信其开端临盆(订货)的时刻。
四、主临盆筹划主临盆筹划是确信每一个体的最终产品在每一个体时刻段内临盆数量的筹划。
那个地点的最终产品是指关于企业来说最终完成、要出厂的完成品。
平日包含如下内容:1、要临盆什么器械?2、什么时刻须要?3、要临盆若干?主临盆筹划是自力需求,主假如依照客户合同或者对市场的推测,把在一准时代内须要临盆的产品一一推测,使之成为展开物料需求筹划的重要依照。
主临盆筹划是MRP的泉源,因此,其的重要性是不问可知的。
若其包含的以上三个重要参数出缺点,则下面的运算确信是缺点的。
因此,主临盆筹划编制时,必定要精确,不然,不只不克不及给企业带来效益,反而会给企业带来损掉。
NC对主临盆筹划的说明:包含主需求筹划和主临盆筹划,可知足工业企业临盆筹划制订与治理的要求,并供给主临盆筹划的生成仿照与才能分析。
主需求筹划是主临盆筹划的驱动数据,其重要来源是发卖订单与发卖推测,并可在不合的时区设定不合的需求归并策略。
MRP运算

当物料被多个最终产品使用时:
如果层次码< 如果层次码<低层码: – 各种最终产品对物料的毛需求汇总并保存; 如果层次码=低层码: – 毛需求汇总,然后求净需求,并求计划产出量
X[1]
Y[1]
B(1) MRP
C
D(2) MRP
B(1)
U
E(2)
B(3)
F(3)
7 10 8 9
H(3)
F(3)
X
MPS
制造业的通用公式 (生产什么 用到什么) 用到什么) - 已有什么 = 还缺什么
快速运算
MPS
X
时 段 计划产出量 计划投入量
提前期=1
现有量=0
1
2 10
3 10
4 10
5 10
6 10
7 10
8 10
9 10 11 12 10 10 10 5
A
(逐级展开)
提前期=1 段
现有量=0
MRP
时
1 10
毛需求 现有库存 计划产出量 计划投入量
MRP
库存的使用要 优先满足层次 低的物料需求
X
时 段 计划产出量 计划产出量
提前期=1 批量=1 现有量=0 提前期 批量 现有量
1 2 3 4 5 6 10 7 10 8 9
MPS
第 一 层
B
时 段
提前期=1 批量=1 现有量=10 提前期 批量 现有量
时 段 计划产出量 计划投入量
时 段
提前期=1 批量=1 现有量=0 提前期 批量 现有量
4 5 6 10 4 5 6 10 7 8 9
Y
时 段 计划产出量 计划投入量
时 段
提前期=1 批量=1 现有量=0 提前期 批量 现有量
MRP

mrpMRP(Material Requirement Planning 物料需求计划)是被设计并用于制造业库存管理信息处理的系统,它解决了如何实现制造业库存管理目标——在正确的时间按正确的数量得到所需的物料这一难题。
MRP是当今众所周知的ERP的雏形,MRP与ERP的库存管理思想又源于求解制造业基本方程。
简介MRP(Material Requirement Planning)物料需求计划:美国生产与库存控制协会(APICS:American Production and Inventory Control Society)对物料需求计划的定义:物料需求计划就是依据主生产计划(MPS)、物料清单、库存记录和已订未交定单等资料,经由计算而得到各种相关需求(Dependent demand)物料的需求状况,同时提出各种新订单补充的建议,以及修正各种已开出订单的一种实用技术。
从MRP到ERP制造资源计划(Manufacturing Resources Planning简称MRPⅡ:将公司高层管理与中层管理结合在一起,以制造资源计划为活动核心,促使企业管理循环的动作,达到最有效的企业经营。
其涵盖范围包含了企业的整个生产经营体系,包括经营目标、销售策划、财务策划、生产策划、物料需求计划、采购管理、现场管理、运输管理、绩效评价等等各个方面。
企业怎样才能在规定的时间,规定的地点,按照规定的数量得到真正需要的物料,换句话说,就是库存管理怎样才能符合生产计划的要求,这是物料需求计划所解决的。
MRP起初出现在美国,并由美国生产与库存管理协会倡导而发展起来的。
MRP是一种以计算机为基础的编制生产与实行控制的系统,它不仅是一种新的计划管理方法,而且也是一种新的组织生产方式。
MRP的出现和发展,引起了生产管理理论和实践的变革。
MRP是根据总生产进度计划中规定的最终产品的交货日期,规定必须完成各项作业的时间,编制所有较低层次零部件的生产进度计划,对外计划各种零部件的采购时间与数量,对内确定生产部门应进行加工生产的时间和数量。
mrp运算逻辑
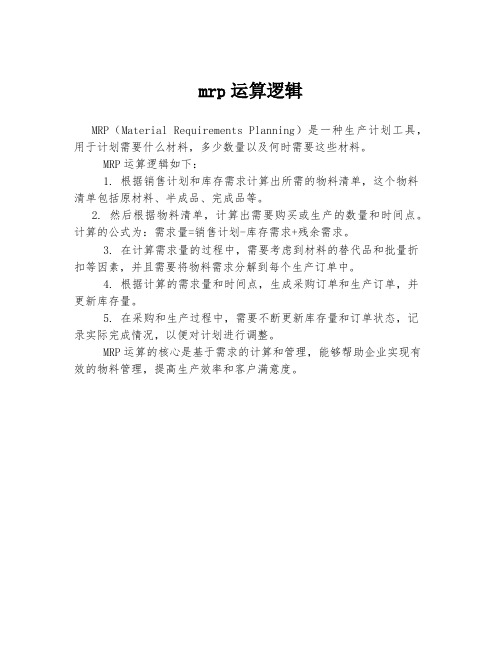
mrp运算逻辑
MRP(Material Requirements Planning)是一种生产计划工具,用于计划需要什么材料,多少数量以及何时需要这些材料。
MRP运算逻辑如下:
1. 根据销售计划和库存需求计算出所需的物料清单,这个物料清单包括原材料、半成品、完成品等。
2. 然后根据物料清单,计算出需要购买或生产的数量和时间点。
计算的公式为:需求量=销售计划-库存需求+残余需求。
3. 在计算需求量的过程中,需要考虑到材料的替代品和批量折扣等因素,并且需要将物料需求分解到每个生产订单中。
4. 根据计算的需求量和时间点,生成采购订单和生产订单,并更新库存量。
5. 在采购和生产过程中,需要不断更新库存量和订单状态,记录实际完成情况,以便对计划进行调整。
MRP运算的核心是基于需求的计算和管理,能够帮助企业实现有效的物料管理,提高生产效率和客户满意度。
- 1、下载文档前请自行甄别文档内容的完整性,平台不提供额外的编辑、内容补充、找答案等附加服务。
- 2、"仅部分预览"的文档,不可在线预览部分如存在完整性等问题,可反馈申请退款(可完整预览的文档不适用该条件!)。
- 3、如文档侵犯您的权益,请联系客服反馈,我们会尽快为您处理(人工客服工作时间:9:00-18:30)。
MRP通用计算公式:
净需求=毛需求+已分配量+安全库存-计划在途-实际在途-可用库存
毛需求量:
不考虑库存、制造、采购的需求量,相对于净需求而言。
如果是独立需求,那么毛需求=主生产计划需求量/(1–料品不良率)。
如果是相关需求,那么毛需求=上层料品的下达量。
其中独立需求是指某一存货项目的需求与其他项目需求没有关联,如生产的最终产品,它是企业生产的可以销售的产品项目通常位于产品结构表的最上层。
而相关需求是指某一存货项目的需求是由另一项目需求有关并可因而推算,如半成品、原料。
它是可以通过最终产品的需求量而计算得到半成品、原料的需求量。
成品的毛需求即订单欠交量(生产欠交量)。
一阶半成品或物料的毛需求即是抓的成品的净需求。
而二阶或其以下的半成品或物料的毛需求又是抓的二阶或上一阶半成品的净需求。
已分配量:
尚保存在仓库中(假想入足库的状况)但已分配给制单的料品数量。
实际上就是物料控制档中欠发数量。
即已分配量=应发数量-实发数量。
安全库存量:
为防止各种异常导致缺料从而特地额外增加的需求量,通常也可以理解为备品数量
计划在途量:
跑出MRP后从已生成了采购计划到生成采购单的中间过程的需采购数量实际在途量:
分为采购在途和制造在途。
采购在途:
已审核未结案的采购单的欠交数量。
制造在途:
已审核未结案的制造单的未入库数量
可用库存量:
一般是指所有仓别中可用的的良品实物库存数量(可用库存=库存量-安全存量.)但对于跑MRP时运算公式中的可用库存则是本次抓上一笔订单(制造单)的预计结存,是理论可用库存!
其实假想有按日期先后顺序下的三个订单(制造单)
A、
B、C,A的预计结存就是B的可用库存,B的预计结存就是C的可用库存.依此类推下去就是本次跑MRP时的物料的可用库存就是用到或生产些物料的上一笔订单或制造单的预计结存量.预计结存量:
预计结存量=下达量+可用库存+在途量+计划在途量-毛需求-已分配量,是物料整体上的存量结算
净需求量:
依MRP计算公式计算出来的数量.
逾期计划量:
指在物料的需求日期之后总的的物料计划在途数量.
逾期在途量:
指在物料的需求日期之后的总的物料采购在途数量.
下达量:
指物料的实际下达量,通常就是净需求量实际下达的需求量,其数据来源为净需求量,但可能由于料品订货规则不同而和净需求量有一定的差异。
料品订货规则计算方法
1净需求下达量=净需求
2按固定批量下达量=求整(净需求/批量)*批量求整为有余进一
3按固定期间下达量=净需求
4按主生产计划下达量=净需求注:
(库存量= 0,已分配量= 0)其含义就是不考虑库存和已分配量
5按最小批量如果净需求<批量则下达量=批量
如果净需求>批量则下达量=净需求
说明:
(1)应具有BOM(面向生产的物料清单)BOM准确率达到95%
(2)应具有库存主档(料品库存量记录)库存帐准确率达到95%
(3)所有单据日清日结达成率达到95%.
(4)每一个料品均应知其提前期(前置期),在料品主档中设定(订货提前期、检验提前期、准备提前期)
(5)MRP运算是按照物料来运算的,而不是按批号!运算时的已分配量是该物料在物料
控制档里的所有(全部的批次物料的需求日期<=当前批次物料的需求日期)未发数量累加量,在途、在途量、可用库存同理!
(6)MRP运算特征:
第一个用到该物料/半成品的订单的对应的该物料的MRP结果是抓该物料的所有已分配量、所有可用库存、所有在途(采购/制造)、所有计划在途.而用到该物料/半成品的第二个订单除了可用库存是抓第一个用到该物料/半成品的订单的该物料的MRP运算结果的预计结存外,其它的均为
0."以引类推下去,就是除了第一个用到该物料的订单是抓所有外,其它都是后一个订单的可用库存抓上一个订单的预计结存,其它量均为0,已分配量亦如此.对于成品而言在途量也是第一个订单抓所有的在途,其它的都是后一个订单的可用库存抓上一个订单的预计结存.。