加工误差统计分析实验指导
加工误差统计分析实验报告

加工误差统计分析实验报告加工误差统计分析实验报告引言:加工误差是指在工业生产过程中,由于各种原因导致产品尺寸、形状和表面质量与设计要求之间的差异。
加工误差的控制对于保证产品质量、提高生产效率和降低成本具有重要意义。
本实验旨在通过对加工误差进行统计分析,探讨误差来源及其影响因素,为工业生产过程中的质量控制提供参考依据。
实验设计:本实验选取了一台数控铣床进行实验,以铣削加工尺寸为研究对象。
首先,我们选择了一种常见的零件,对其进行加工。
然后,通过测量加工后的尺寸与设计要求进行对比,得到加工误差数据。
最后,我们对这些数据进行统计分析,探究加工误差的分布规律和影响因素。
实验过程:1. 加工准备:选择合适的刀具、夹具和工艺参数,进行加工准备工作。
2. 加工操作:按照设计要求进行铣削加工,并记录下每次加工后的尺寸数据。
3. 尺寸测量:使用测量工具对加工后的零件进行尺寸测量,并记录测量结果。
4. 数据整理:将测量得到的数据整理成表格,方便后续的统计分析。
统计分析:1. 加工误差分布:通过绘制加工误差的频率分布直方图,我们可以观察到误差值的分布情况。
通常情况下,加工误差符合正态分布,但也可能存在其他分布形式,例如偏态分布或双峰分布。
通过分析分布形式,可以判断加工过程中是否存在特殊的误差来源。
2. 加工误差与加工参数的关系:通过对加工误差与加工参数(如切削速度、进给速度等)进行相关性分析,可以了解不同参数对加工误差的影响程度。
这有助于我们确定合适的工艺参数范围,以减小加工误差。
3. 加工误差与刀具磨损的关系:刀具磨损是导致加工误差增大的重要因素之一。
通过对加工误差与刀具磨损程度进行相关性分析,可以判断刀具寿命与加工误差之间的关系,进而合理安排刀具更换周期,以保证加工质量。
4. 加工误差与工件材料的关系:不同材料的加工性能不同,可能导致加工误差的差异。
通过对加工误差与工件材料进行相关性分析,可以了解不同材料对加工误差的影响程度,为材料选择和工艺优化提供依据。
机械制造技术基础实验教学大纲

机械制造技术基础实验教学大纲
实验项目数:2
实验学时数:2X2=4
授课对象:机设,材成
实验类型:验证性
一、实验项目名称:
1、刀具角度测量:主要设备:刀具角度测量仪
2、加工误差统计分析:主要设备:立式光学比较仪
二、实验目的:
1、掌握刀具角度测量方法;
2、加深对刀具角度定义的理解;
3、掌握加工误差统计分析的一般方法与过程;
了解加工误差产生的原因及减少加工误差的途径。
三、实验一般安排:
1、刀具角度测量实验:2人一组,各自测量等五个角度2次,取平均值;
2、加工误差统计分析实验:1人1组,每人测量10个数据;
四、实验前准备:
1、阅读与实验相关的理论章节;
2、阅读实验指导书;
3、准备实验记录纸;
五、实验一般要求:
1、认真做好实验前准备工作;
2、听从实验老师的一切安排;
3、实验数据经指导老师签字后才能生效;
4、试验后完成实验报告。
机械制造技术基础-A-实验指导书
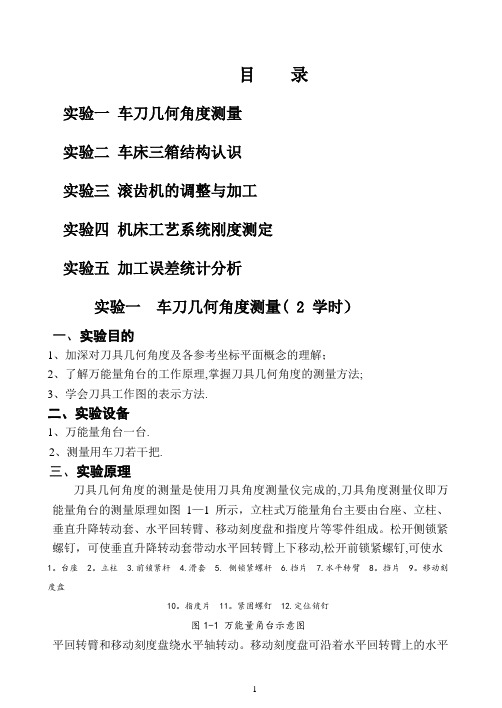
目录实验一车刀几何角度测量实验二车床三箱结构认识实验三滚齿机的调整与加工实验四机床工艺系统刚度测定实验五加工误差统计分析实验一车刀几何角度测量( 2 学时)一、实验目的1、加深对刀具几何角度及各参考坐标平面概念的理解;2、了解万能量角台的工作原理,掌握刀具几何角度的测量方法;3、学会刀具工作图的表示方法.二、实验设备1、万能量角台一台.2、测量用车刀若干把.三、实验原理刀具几何角度的测量是使用刀具角度测量仪完成的,刀具角度测量仪即万能量角台的测量原理如图1—1所示,立柱式万能量角台主要由台座、立柱、垂直升降转动套、水平回转臂、移动刻度盘和指度片等零件组成。
松开侧锁紧螺钉,可使垂直升降转动套带动水平回转臂上下移动,松开前锁紧螺钉,可使水1。
台座 2。
立柱 3.前锁紧杆 4.滑套 5. 侧锁紧螺杆 6.挡片 7.水平转臂 8。
挡片 9。
移动刻度盘10。
指度片 11。
紧固螺钉 12.定位销钉图1-1 万能量角台示意图平回转臂和移动刻度盘绕水平轴转动。
移动刻度盘可沿着水平回转臂上的水平槽水平移动,并根据测量需要紧固在某一确定位置。
指度片可绕螺钉销轴转动,其底部靠近被测量的表面,指针指示测量角度.用上述这些零件位置的变动,即可实现各参考平面内刀具角度的测量。
测量时,刀具放在台座上,以刀杆的一侧靠在两定位销内侧定位。
四、实验内容1)测量主偏角滑套上的“0”刻度对准立柱上的标定线,测量时只可上下移动,不得转动。
转动水平回转臂,使其上的“0”刻度线对准滑套上的标定线。
调整测量指度片,使指度片的底面与主切削刃重合,制度片的指针所指的角度为主偏角. 2)测量负偏角方法同上,只是让指度片的底面与副切削刃重合,指针所指读数为负偏角. 3)测量前角滑套上的“0”刻度对准立柱上的标定线后,再把滑套相对于标定线顺时针转动一个主偏角的余角,转动水平回转臂,使水平回转臂上的“90”刻度线对准滑套上的“90”刻度线,调整指度片,使指度片的底面与前刀面重合,制度片的指针所指的角度为。
加工误差统计分析实验报告

加工误差统计分析实验报告一、实验目的通过统计分析加工误差数据,探究加工工艺对产品加工误差的影响,并提出相应的改进措施。
二、实验原理加工误差是指产品实际尺寸与设计尺寸之间的差异,主要受到原材料、加工设备、操作工艺等因素的影响。
统计分析可以通过数学模型和数据处理方法,定量地描述和评估加工误差的分布情况,为加工工艺改进提供依据。
三、实验步骤1.随机选择一批相同产品进行加工,保持其他加工条件不变。
2.测量每个产品的实际尺寸,记录数据并整理成表格。
3.统计每组数据的平均值、方差以及标准差。
4.构建加工误差的概率分布函数,通过正态性检验和偏度、峰度检验判断数据是否符合正态分布。
5.进行加工误差数据的t检验,分析不同因素对加工误差的影响程度。
四、实验数据产品编号,实际尺寸 (mm)--------,--------------1,10.012,10.02...,...100,10.08五、数据处理及分析1.计算平均值、方差和标准差:平均值μ=(10.01+10.02+...+10.08)/100=10.05方差s^2=((10.01-10.05)^2+(10.02-10.05)^2+...+(10.08-10.05)^2)/99标准差s=√s^22.正态性检验:根据实验数据计算样本均值和样本标准差,绘制加工误差的概率密度分布曲线。
通过观察曲线形状以及进行偏度、峰度检验,判断数据是否符合正态分布。
3.t检验:根据产品加工误差数据,进行t检验来分析不同因素对加工误差的影响程度。
比如,可以比较不同机器加工出的产品误差是否有显著性差异。
六、实验结果分析1.样本加工误差符合正态分布,数据较为集中,无明显偏离。
2.通过t检验发现:不同机器加工出的产品误差差异不显著,说明机器之间的加工稳定性较好。
3.根据样本数据及数据处理结果,可以得到加工误差的基本分布情况,对加工工艺的控制和改进提供依据。
例如,可以调整机器参数、改进操作工艺等。
实验五 加工误差的统计分析

实验五加工误差的统计分析1.实验目的(1)掌握加工误差统计分析的原理和方法;(2)掌握统计分析法的应用。
2.原理根据加工一批零件的检验数据,运用数理统计的原理加以分析处理,从中找出误差的种类、大小及规律。
这就是加工误差的统计分析法。
3.试剂和仪器设备(1)型卧式车床;(2)外径千分尺();(3)硬质合金车刀;(4)试件(材料钢,尺寸);4.实验步骤(1)调好机床和刀具,用调整法加工一批试件(100件);(2)按加工顺序测量试件尺寸,并记录测量结果。
5.实验数据及其处理(1)以加工顺序为横坐标,实测尺寸为纵坐标,绘制点图;(2)绘制实验分布曲线图(直方图);(3)绘制图。
6.问题讨论(1)本工序点图说明了什么问题?(2)本工序的实验分布曲线图是否服从正态分布规律?(3)根据工序精度系数,本工序属于几级精度工艺能力?能否满足加工要求?(4)从图看,本工序的工艺过程是否稳定?如果不稳定,试分析其原因。
X—R控制图的操作步骤及应用示例用于控制对象为长度、重量、强度、纯度、时间、收率和生产量等计量值的场合。
X控制图主要用于观察正态分布的均值的变化,R控制图主要用于观察正态分布分散或变异情况的变化,而X-R控制图则将二者联合运用,用于观察正态分布的变化。
X-R控制图的操作步骤步骤1:确定控制对象,或称统计量。
这里要注意下列各点:(1)选择技术上最重要的控制对象。
(2)若指标之间有因果关系,则宁可取作为因的指标为统计量。
(3)控制对象要明确,并为大家理解与同意。
(4)控制对象要能以数字来表示。
(5)控制对象要选择容易测定并对过程容易采取措施者。
步骤2:取预备数据(Preliminary data)。
(1)取25个子组。
(2)子组大小取为多少?国标推荐样本量为4或5。
(3)合理子组原则。
合理子组原则是由休哈特本人提出的,其内容是:“组内差异只由偶因造成,组间差异主要由异因造成”。
其中,前一句的目的是保证控制图上、下控制线的间隔距离6σ为最小,从而对异因能够及时发出统计信号。
加工误差统计分析实验指导

加工误差统计分析实验指导加工误差是指在加工过程中由于各种原因导致加工零件的尺寸、形状等与设计要求不一致的现象。
对于加工误差的统计分析,可以帮助我们了解加工误差的分布规律、原因及其对产品质量的影响,进而采取相应的措施来提高加工精度。
本文将从实验设计、数据采集、误差分析和提高加工精度方面对加工误差进行统计分析。
实验设计:首先确定实验对象,可以选择一种常见的工程零件进行加工。
确定需要测量的尺寸和形状参数,并确定测量方法和仪器。
然后确定实验方案,包括样本数量和采样方法,并进行预试验,了解实验的可行性和可重复性。
数据采集:在进行加工过程中,根据实验方案采集数据。
首先进行初始测量,记录下每个样本的初始尺寸和形状参数。
然后进行加工操作,并根据实验方案确定的频次和时机进行测量。
注意在测量过程中保证测量误差的最小化,例如使用合适的仪器和测量方法,增加测量次数等。
最后对采集的数据进行整理和保存,便于后期的分析。
误差分析:对采集的数据进行误差分析是加工误差统计分析的核心步骤。
首先可以计算每个样本的误差值,即实际尺寸和目标尺寸之间的差值。
然后可以通过绘制误差分布直方图和概率图,来分析误差的分布特征和规律。
可以采用正态检验等统计方法来确定误差是否服从正态分布。
进一步分析可以从不同角度入手。
一方面,可以分析误差与加工参数的关系。
通过对比不同加工参数下的误差值的差异,确定加工参数对误差的影响。
例如,可以研究不同切削速度、进给速度和切削深度对误差的影响,找出最优的加工参数组合。
另一方面,可以分析误差与工艺环节的关系。
通过对比不同工艺环节下的误差值的差异,确定工艺环节对误差的影响。
例如,可以研究不同切削工具的磨损情况对误差的影响,找到最优的切削工具选择和更换策略。
提高加工精度:根据误差分析的结果,可以采取一些措施来提高加工精度。
例如,可以改进机床设备和加工工艺,在加工过程中加强质量控制,提高加工设备的精度和稳定性,优化加工参数的选择和调整策略等。
加工误差的统计分析实验报告

加工误差的统计分析实验报告实验报告-加工误差的统计分析一、引言加工误差是工业生产中常见的问题之一,直接影响着产品的质量和性能。
了解加工误差的统计分布和规律,对于优化加工工艺、提高产品精度具有重要意义。
本实验旨在通过统计分析加工误差数据,探讨加工误差的分布及其对产品质量的影响。
二、实验设计1.实验目标:观察加工误差的统计分布及其规律。
2.实验工具:数控加工机床,三坐标测量仪3.实验材料:其中一种金属材料4.实验步骤:a.设计并加工若干个样品b.使用三坐标测量仪测量每个样品的加工误差c.记录加工误差数据并进行统计分析三、实验结果1.加工误差数据记录表样品编号,加工误差(mm----------,--------------A,0.0B,0.0C,0.0D,0.0E,-0.0F,0.0G,0.0H,-0.0I,0.0J,0.02.加工误差的统计分析a. 加工误差的均值(μ):0.01mmb. 加工误差的标准差(σ):0.02mmc. 加工误差的方差(σ^2):0.0004mm^2四、结果分析1. 加工误差的均值与标准差分别表示了加工误差的集中程度和离散程度。
实验结果显示,加工误差的均值为0.01mm,说明整体上加工误差集中在一个较小的范围内。
而标准差为0.02mm,表明加工误差的离散程度较大。
2.通过加工误差的统计分布分析,可以更准确地评估加工精度的稳定性和可靠性。
3.经过正态性检验,加工误差近似符合正态分布,这与许多加工误差服从中心极限定理的理论支持一致。
五、结论1. 通过加工误差数据的统计分析,得出样品加工误差的均值为0.01mm,标准差为0.02mm,方差为0.0004mm^22.样品的加工误差数据近似符合正态分布,说明加工误差在一定程度上服从中心极限定理。
3.实验结果进一步表明,加工误差的集中程度较高,但其离散程度相对较大。
六、改进建议1.根据加工误差的分布规律,可以对加工工艺进行优化,减小加工误差的产生。
加工误差统计分析的常规方法(精)

实验二 加工误差统计分析的常规方法机械加工要保证产品质量,就要保证加工精度。
要保证加工精度就要确定误差,而确定误差主要有统计和分析计算法。
统计法又可分为分布曲线法和点图法两种。
一、 实验目的及要求:1.通过实验进一步了解:(1)大批量生产情况下,零件的统计特性及引起尺寸波动的原因。
(2)系统性误差和随机性误差的特性及其对零件加工精度的影响。
2.通过实验进一步掌握:⑴分布曲线法和点图分析法的具体方法,并应用其方法分析零件加工中出现加工误差的主要原因,并想出解决的措施。
⑵掌握分析和解决加工误差问题的四个阶段(调查、分析、测试、验证)的具体方法。
3.要求:⑴测试尺寸精度要求为0.001mm 。
⑵ 绘制分布曲线和X —R 图均用方格纸。
⑶书写整洁,计算准确,绘图精心。
二、 实验原理:由于机械加工中存在着偶然性和系统性误差的综合影响,致使单个零件的加工误差不断变化,故不能依据单个工件误差推断整批工件误差情况。
统计分析法就是以对生产现场的观察和对一定数量的工件测量所得结果为基础,用数理统计方法进行处理。
以确定由于全部作用因素的共同影响而得到的尺寸分布范围,研究误差的性质及其影响,评定加工精度。
1.对某一工序在一次调整下加工的一批零件,测量它们加工的实际尺寸。
再按尺寸大小将整批零件分布若干组,算出每组零件(频数)及其占全部零件的百分比(频率)。
以各组尺寸和频率(频数)为坐标可作出频率直方图。
当零件数目越多,尺寸间隔取得越小时,尺寸分布的折线将接近为曲线,称为实验尺寸分步曲线。
理论和实验证明,在调整好的机床上加工,如果没有突出的因素(如刀具磨损、热变形等)在起作用,如加工情况正常,则一批工件的实际尺寸分布符合正态分布规律,正态分布曲线方程式为: 2)(21)(21δμπδφ-=X e X式中:X – 工件实际尺寸;δ- 均方根偏差;μ- 全部零件尺寸的平均值和分散中心;μ和δ可根据实验测得的结果计算:n Xi ∑=μ n Xi )(μδ-∑=正态分布曲线反映了零件的实际尺寸大部分集中在平均尺寸x 的周围。
- 1、下载文档前请自行甄别文档内容的完整性,平台不提供额外的编辑、内容补充、找答案等附加服务。
- 2、"仅部分预览"的文档,不可在线预览部分如存在完整性等问题,可反馈申请退款(可完整预览的文档不适用该条件!)。
- 3、如文档侵犯您的权益,请联系客服反馈,我们会尽快为您处理(人工客服工作时间:9:00-18:30)。
加工误差统计分析实验
一、实验目的
1、巩固已学过的统计分析法的基本理论;
2、掌握运用统计分析法的步骤;
3、学习使用统计分析法判断和解决问题的能力。
二、实验设备与仪器
电感测量仪、块规、千分尺、试件(滚动轴承滚柱)、计算机。
三、实验原理和方法
在机械加工中,应用数理统计方法对加工误差(或其他质量指标)进行分析,是进行过程控制的一种有效方法,也是实施全面质量管理的一个重要方面。
其基本原理是利用加工误差的统计特性,对测量数据进行处理,作出分布图和点图,据此对加工误差的性质、工序能力及工艺稳定性等进行识别和判断,进而对加工误差作出综合分析。
1、直方图和分布曲线绘制
1)初选分组数k
2
找出样本数据的最大值X imax和最小值X imin,并按下式计算组距:
式中:k——分组数,按表选取;
X max和X min——本组样本数据的最大值和最小值。
选取与计算的d值相近的且为测量值尾数整倍数的数值为组距。
3)确定组界
各组组界为:
min (i1)d
2
d
X+-± (i=1,2,…,k),为避免样本数据落在组
界上,组界最好选在样本数据最后一位尾数的1/2处。
4)统计各组频数
频数,即落在各组组界范围内的样本个数。
频率=频数/样本容量
5)画直方图
以样本数据值(被测工件尺寸)为横坐标,标出各组组界;以各组频数为纵坐标,画出直方图。
6)计算总体平均值与标准差
平均值的计算公式为 1
1n i i X X n ==∑ 式中:X i ——第i 个样本的测量值;
n ——样本容量。
标准差的计算公式为
s =7)画分布曲线
若研究的质量指标是尺寸误差,且工艺过程稳定,则误差分布曲线接近正态分布曲线;若研究的资料指标是形位误差或其他误差,则应根据实际情况确定其分布曲线。
画出分布曲线,注意使分布曲线与直方图协调一致。
8)画公差带
按照与以上分布曲线相同的坐标原点,在横轴下方画出被测零件的公差带,以便与分布曲线相比较。
公差根据试件类型、规格查国标手册可得到。
2、X -R 图绘制
1)确定样组容量,对样本进行分组
样组容量一般取m=2~10件,通常取4或5,即对试件尺寸依次按每4~5个一组进行分组,将样本划分成若干个样组。
2)计算各样组的平均值和极差
对于第i 个样组,其平均值和极差计算公式为
1
1m
i ij j X X m ==∑, max min i i i R X X =- 式中:i X ——第i 个样组的平均值;
i R ——第i 个样组的标准差;
ij X ——第i 个样组第j 个试样的测量值;
max i X ——第i 个样组数据的最大值;
min i X ——第i 个样组数据的最小值。
3)计算X -R 图的控制线
X -R 图的控制线为 样组平均值X 图的中线 1
1m k i i m X X k ==∑ 样组平均值R 图的中线
1
1m k i i m R R k ==∑ 样组平均值X 图的上控制线 2U X X A R =+ 样组平均值R 图的上控制线 1U R D R = 样组平均值X 图的下控制线 2L X X A R =- 样组平均值R 图的下控制线 2L R D R =
式中:A 2、D 1、D 2——常数,见下表;
以组序号为横坐标,分别以各样组的平均值X 和极差R 为纵坐标,画出X -R 图,并在图上标出中线和上、下控制线。
3、工序能力系数计算
工序能力系数P C 按下式计算:=6P T C σ(或P C P
δ=) 根据工艺能力系数P C 的大小,可将工艺分成5个等级。
(1) 1.67P C >,为特级,说明工艺能力过高,不一定经济。
(2)1.67 1.33P C ≥>,为一级,说明工艺能力足够,可以允许一定的波动。
(3)1.33 1.00P C ≥>,为二级,说明工艺能力勉强,必须密切注意。
(4)1.000.67P C ≥>,为三级,说明工艺能力不足,可能会出现少量不合格品。
(5)0.67P C ≤,为四级,说明工艺能力不行,必须加以改进。
一般情况下,工艺能力不应低于二级。
4、判别工艺过程稳定性
所谓工艺过程的稳定,从数理统计的原理来说,一个过程(工序)的质量参数的总体分布,其平均值X 和均方根差σ在整个过程(工序)中若能保
持不变,则工艺过程是最稳定的。
不满足,即表示工艺过程不稳定。
四、实验步骤
1.对试件进行编号;
2.按试件的基本尺寸选用块规;
3.调校电感测量仪;
4.在电感测量仪上按序号顺次测量试件的外径,为保证测量的准确性和可靠性可在其上测量三个点,取其平均值,把结果填入表中。
5.清理实验现场,收拾所用仪器、量具、工具等。
6.整理实验数据,绘图。
五、思考题
(1)分布图主要说明什么问题?(2)X-R图主要说明什么问题?
(3)分析产生加工误差的主要因素有哪些?(4)分析工艺过程稳定(或不稳定)的原因。