液压管路清洗技术标准修订稿
液压管道循环酸洗、油冲洗技术综述

液压管道循环酸洗、油冲洗技术综述液压管道在长期使用过程中,由于介质的腐蚀、沉积物的积累以及摩擦磨损等原因,往往会导致管道内部出现生锈、结垢等问题,进一步影响管道的正常运行和寿命。
为了解决这些问题,液压工程中常常运用循环酸洗和油冲洗技术。
本文就对液压管道循环酸洗、油冲洗技术进行综述。
液压管道酸洗技术液压管道酸洗原理液压管道通常采用酸洗的方法,其中最常用的是循环酸洗技术。
循环酸洗技术是通过对管道内部使用酸洗液进行旋转强制流动,使酸洗液在管道内能够充分接触管道表面,并能够去除管道内部的氧化铁锈、沉积物等杂质,从而达到对管道进行有效清洗和去腐蚀的目的。
循环酸洗工艺可以除去钢铁表面氧化物和油污等,改善金属表面状况、优化表面质量、加强表面粗糙度,有利于严密联接。
液压管道酸洗过程液压管道酸洗过程包括管道内部酸洗、中和、清洗、漂洗、除锈处理等环节。
在实际应用中,酸洗剂的类型和浓度、流量、流速、反应时间等也会因管道材质、壳体结构、管径大小以及管道使用情况的不同而有所不同。
液压管道酸洗注意事项在进行管道酸洗之前,首先需要根据管道的实际材质、管径大小等情况选择合适的酸洗液浓度和配方。
在酸洗过程中,也需要注意控制酸洗液的浓度和酸洗时间,避免管道因长时间酸洗而出现损坏、变形等问题。
另外,酸洗过后也需及时中和清洗管道内部,避免出现酸碱中和不均衡导致的二次腐蚀问题。
此外,在进行酸洗前还需做好防护措施,戴好防护胶手套,做好防护工作,避免因酸液对皮肤、眼睛等造成的刺激和损伤。
液压管道油冲洗技术液压管道油冲洗原理在液压管道酸洗的基础之上,通常还会采用油冲洗技术,目的是清除管道内残留的杂质以及防止其再次沉积。
油冲洗技术是利用高速旋转的油涡片冲刷管道内壁表面,利用力的热与化学等特性去除管道内的污物或脱落的附着物。
同时通过油的切割作用,也能够有效去除摩擦产生的金属粉屑或铁锈等杂质,从而保证管道内部的清洁度和液压系统的正常运行。
液压管道油冲洗过程液压管道油冲洗过程由串联油箱、泵组、油冲系统和过滤系统组成。
液压设备管道冲洗试压安全技术专项方案优选稿

液压设备管道冲洗试压安全技术专项方案集团公司文件内部编码:(TTT-UUTT-MMYB-URTTY-ITTLTY-液压设备管道冲洗试压安全技术专项方案一、编制说明1.1目的为了进一步规范施工现场安全管理,有序控制宝钢三号高炉工程机装分公司施工职业健康安全与环境,根据上海市工程建设规范的要求,特制定本计划。
对安全管理要素和资源作业规定,使全体参战人员更好地遵守国家、上海市以及我公司有关安全生产法令、法规、规章制度,保证宝钢三号高炉工程机装分公司工程项目职业健康安全与环境目标的实现。
1.2适用范围1.3引用标准文件1.4安全保证计划管理二、工程概况此次高炉大修液压系统分为炉前液压系统和炉顶液压系统,总计管道15000m,总重量为60t。
2.1.炉前液压系统主要有一个液压站,4个阀架组成。
为炉前开铁口机、移盖机、泥炮提供动力;2.2.炉顶液压系统由一个液压站及三个阀架组成主要为上料阀、下料阀、上密封阀、下密封阀、均排压阀、放散阀提供动力。
三、主要施工内容3.1、炉前、炉顶液压站及中间配管冲洗、试压;四、主要施工措施4.1、液压设备及管道冲洗:出铁场液压系统和炉顶液压系统冲洗的主要方法基本相同,主要分为冲洗前、冲洗中、冲洗后三大步骤,只是各个系统回路连接不一样;4.2、液压设备及管道试压:炉体液压系统、出铁场液压系统试压的步骤基本相同,主要根据各系统工作压力等级不同从而试验压力不一样。
当冲洗完,经过施工方、业主及监理确认合格后对整个系统进行试压。
试压前,做好试压交底,试压人员清楚试压过程的每个步骤,然后逐级升压直到试压压力,注意试压过程中接头、法兰焊接处的检查及密封处的检查。
五、安全措施上述液压系统设备及管道冲洗、试压的方法大致是相同的,但由于设备所安装的位置不同,液压系统控制的设备不同,系统压力不同从而在安全管理方面必须更要严格要求,安全制度更应严格。
针对冲洗、试压带来的安全隐患及采取安全措施如下:5.1、液压设备及管道冲洗,炉顶液压设备及管道主要安装在高空位置,基本都在44.8米平台以上,而炉前液压管道在出铁场平台上10.2m处,在冲洗过程中带来的安全隐患很大。
液压管道冲洗方案-2-1
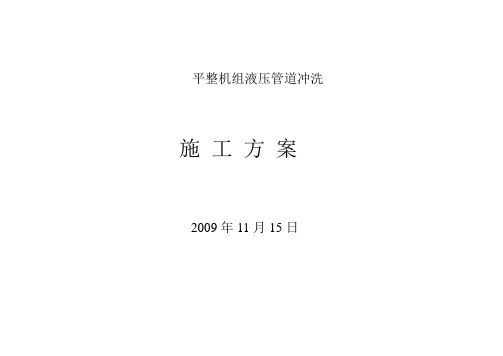
平整机组液压管道冲洗施工方案2009年11月15日根据业主单位的要求,平整液压机组冲洗采用体外泵循环冲洗。
现就设备的特点制定如下方案:根据现场管道配管的实际情况,将低压管道连接分为两组:1、以阀台前主管道为基础,P管、T管连通构成回路。
其中地下油库内的阀台两路主管一次连通,末端各加一个截止阀已达到控制管路清洗方向及流量的目的。
2、所有阀台以及最末端的两个阀台及后边执行机构管道与主管道连接,构成回路。
上述阀台前的P管路直径为Ф60~Ф114过流量为400~1200L/min才能达到紊流速度。
3、上述阀台需拆除移位方能满足连接要求,清洗合格后重新回装。
其余地面上阀台的P管、T管也直接连通,构成回路冲洗。
4、阀台的后边执行机构管道单独立连接成回路。
Ф40以下的管路用分流排连接成回路,每个出口分别安装截止阀,控制回路清洗方向及流速。
5、高压系统阀台在机上。
主管路连接方式与低压相同。
先连接主管路P、T。
末端在机上连通。
由于阀台后机上配管及其复杂,有些管路与设备连成一体,如需冲洗应由设备管路安装单位给出冲洗方案,并实施。
我们配合。
6、稀油润滑管路由站内主管路连接。
构成供油、回油直接连通。
在管路最低点安装截止阀或采用必要措施将残油放出。
保证不污染设备自身油箱。
7、污染检测:由甲方指定或手提检验设备在甲方监督下检测,每24小时取样一次,直到了检测达标为准。
8、滤油器选用2组串联使用。
一组为3μ另一组为5μ滤材。
每组过流量为1300x2=2600L/min。
当压差达到0.35Mpa时更换滤芯。
以上方案是否可行,请确认。
2009年11月15日。
q-208液压油管清洁度及试验指导书

核准审核制订文件名称文件编号液压油管清洁度及试验标准指导书版本号生效日期1、目的:统一公司液压件生产和检验要求,实施标准化作业。
2、适用范围:本标准规定了用于液压系统的零件、组件、管路和接头在出厂前进行检查后允许的内部清洁度要求。
3、相关文件:本标准参照和应用标准3.1、NS1638《液压系统的清洁度要求》3.2、KES56.1113.3、GB2828.14、专用词语:4.1、磁性物:使用磁铁能够吸附的颗粒物。
4.2、非磁性物:使用磁铁不能够吸附的颗粒物。
4.3、毛刺:机加工产生的飞边。
4.4、焊接异物:焊接产生的飞溅、焊瘤、氧化皮、焊渣等。
4.5、工件:通指液压系统的零件、组件、管路和接头。
4.6、异物:通指磁性非磁性颗粒物。
5、检验和试验判定基准:5.1、使用目测检查工件内部无可见毛刺、碰伤锐角、焊接异物、锈蚀等。
5.2、使用手感检查无任何颗粒物、手感尖锐毛刺。
5.3、使用称重试验方法收集工件内部异物重量符合以下要求:5.3.1、使用称重试验方法收集工件内部异物时采用5um过滤纸过滤。
5.3.2、液压硬管:收集异物重量(mg)≤0.01×内部表面积(㎝²)。
5.3.3、液压软管:收集异物重量(mg)≤0.006×内部表面积(㎝²)。
5.3.4、液压零件:收集异物重量(mg)≤0.006×内部表面积(㎝²)。
5.3.5、收集异物最大颗粒直径小于0.5mm;0.5mm颗粒物允许2个并且是非磁性物质,0.3~0.5mm颗粒物允许5个。
6、称重试验方法:6.1、试验仪器和设备:6.1.1、玻璃过滤器: 组件(照片1):300ML漏斗,铝合金夹子,直径50MM滤纸垫芯,1L抽滤瓶。
6.1.2、真空泵(照片2):25L/min抽气量,最大真空0.08Mpa。
6.1.3、过滤纸(照片3):直径Φ47mm,过滤颗粒规格5μm。
照片1 照片26.1.4、干膜干燥皿(照片4)照片3 照片4 照片56.1.5、平头不锈钢镊子(照片5)照片6 照片7 照片86.1.6、电子天平(照片6):精度0.1mg以下,推荐使用FA1004。
液压管路酸洗和循环冲洗的过程控制及检验

液压管路酸洗和循环冲洗的过程控制及检验执行标准∶《机械设备安装工程及验收通用规范》(GB 50231)《重型机械液压系统通用技术条件》(JB/T 6996)一,管路酸洗1.槽式酸洗:脱脂--水冲洗--酸洗--水冲洗--中和--钝化--水冲洗--干燥--喷防锈油(剂)--封口。
一次安装好的管路拆下来,置入酸洗槽,酸洗操作完毕并检验合格后,再将其二次安装。
此方法适用于管径较大的短管,直管,容易拆卸,管路施工量小的场合,液压站或阀站内的管道,法兰接头,短管路等均采用槽式酸洗法。
2.循环酸洗:水试漏--脱脂水冲洗--酸洗--中和--钝化--水冲洗--干燥喷防锈油(剂)。
条件允许,所有外部配管均推荐采用循环酸洗法进行酸洗。
组成回路的管道长度,可根据管径等现场实际情况确定,所有管路可以连成一个或多个回路,但单个回路不宜超过300m。
所选酸洗泵必须保证有足够大的流量,应使所有管道的内壁全部接触酸液且酸液出口呈紊流状态流出。
循环酸洗注意事项:(1)使用一台酸泵输送几种介质,因此操作时应特别注意,不能将几种介质混淆,严重时会造成介质浓度降低,甚至造成介质报废。
(2)循环酸洗应严格遵守工艺流程,统一指挥。
当前一种介质完全排出或用另一种介质顶出时,应及时准确停泵,将回路末端软管从前一种介质槽中移出,放入下一工序的介质槽内。
然后启动酸泵,开始计时。
酸洗完成后,管道内部呈青黑色,具体时间可根据实际酸洗效果适当调整。
二,循环冲洗液压系统的管道在酸洗合格后应尽快采用系统所使用的同品质的工作介质进行冲洗,且宜采用循环方式冲洗,并应符合下列要求:(1)液压系统外部管道采用独立循环泵冲洗。
(2)复杂管路可适当分区对各部分进行冲洗。
(3)保证足够大的冲洗速度,应使液流呈紊流状态且应尽可能高。
(4)冲洗液为液压油时应时油温尽可能高,但不宜超过60°C。
(5)循环冲洗要连续进行,冲洗时间通常在72h以上。
冲洗过程宜采用改变冲洗方向或对管子焊接处反复进行敲打,振动等方法加强冲洗效果。
液压管道冲洗方案

首钢京唐工程液压管道冲洗方案编制:审核:批准:编制单位:编制日期:目录一、编制依据 (1)二、工程概况 (1)三、方案确定 (1)四、管道油冲洗方案 (2)五、安全措施 (6)六、应急预案 (6)一、编制依据1、《机械设备安装工程施工及验收通用规范》GB502312092、《冶金机械液压润滑和气动设备工程安装验收规范》GB50387-20063、目前收到的施工图纸及相关资料。
二、工程概况液压系统分为高压系统和低压系统2个部分,高压系统采用不锈钢管,最大工作压力为240bar,冲洗精度等级要求达到NAS3级,低压系统采用碳钢管,最大工作压力为140bar;冲洗精度等级要求达到NAS5级,润滑管路冲洗精度要求达到NAS5级,各类液压、润滑管道的直径规格从16mm~140mm共18种,管道总长约2800m液压系统的组件寿命和工作状况很大程度上取决于所传送工作介质的清洁程度,则必须对介质输送管路进行清洁。
三、方案确定液压、润滑系统冲洗主要有线外冲洗及在线冲洗两种方法。
线外冲洗是指采用专用的冲洗系统线外冲洗需很大的冲洗设备投资过大,而且一台冲洗设备不能同时冲洗两套系统,加上需要换油进行二次冲洗,这将使冲洗工期拖长在线冲洗是指利用液压系统主油泵、油箱及工作介质对管道进行冲洗,冲洗油泵、油箱用冲洗液进行冲洗,在线冲洗工期短能满足工程进度需要,不需要线外的专门冲洗设备,对大型的液压系统操作相对简单,但在线冲洗对各道工序要求严格对各个环节严格控制。
由于冲洗管道后的回油都必须经过回油过滤器,所有冲下来的杂物都被回油过滤拦截,所以回油过虑器是冲洗中最关键的环节。
其优点是投资少,且冲洗一次完成,工期相对较短。
该方案为了加快冲洗进度,采用在线冲洗的方法。
四、管道油冲洗方案油冲洗是为了除去管路系统中的异物,防止管道受污染和使用油变质,导致液压系统工作性能差;并保证液压系统的比例阀及油缸等在系统工作中不致出现机构异常磨损、卡阻现象,以及过滤器堵塞现象。
液压管道油冲洗技术

新技术应用之一博思格钢铁(苏州)有限公司中国涂层项目剪切线、包装线的液压管道油冲洗技术苏州博思格工程是澳大利亚博思格钢铁公司的在华投资项目,外方对工程施工质量要求非常严格,并有自己的一套专门的施工技术规范,特别是对于液压管道的油冲洗技术,施工方法及专用设备都较为先进,值得借鉴。
液压管道的油冲洗是其安装过程中重要的一环,冲洗效果对以后设备的正常运行起到极为关键的作用。
博思格液压管道在进场施工前进行酸洗,管道现场安装完成经射线探伤合格后,采用PolyShot吹扫预清洁代替在线酸洗,然后进行油冲洗,冲洗过程中在线检测进行监控,油冲洗效果非常理想。
其主要技术特点为:(1)为了防止污染地面,所有液压管道均在场外酸洗,待涂过一遍底漆后再进场进行安装施工。
(2)管道进场安装结束后不再进行在线酸洗,而采用管道吹扫(PolyShot)的预清洁方式。
博思格液压管道的吹扫(PolyShot)采用澳大利亚维多利亚液压公司提供的Poly Shot 吹扫方法,工艺先进,效果非常好。
该方法利用压缩空气吹扫枪在已形成回路的管道口施加气压将吹扫绵(Shot)射吹出管道外,吹扫结果非常理想,对其后油冲洗时达到良好的冲洗清洁度起到至关重要的作用,具有工作成本低、有利于环境保护、清洗速度快、操作简单、效率高等优点,而且由于是干式清洗使工作场所非常干净,作业条件好。
使用的主要设备为德国西德福国际公司生产的一套STAUFF气动管路清洁系统(该产品有中国代理)。
STAUFF气动管路清洁系统由压缩空气发射装置(压缩空气手枪)、一套坚固的各种规格的“枪头”和不同材质和规格的清洁头即海绵弹丸三大部分组成。
其工作原理是靠空气推动高速运动的不同密度、不同材料的海绵清洁头通过管路而去除管路内表面的污物。
使用时只要将枪体连接到压缩空气源上(压缩机或压缩空气瓶),西德福气动管路清洁系统就能工作,可以在几秒钟之内将管子内部清洗干净。
气动枪所需压缩空气:工作压力为6-10巴的空压机或压缩空气瓶,容积为250-400升/分种。
液压系统污染后的冲洗规范和要求

液压系统污染后(管路)的冲洗规范和要求一.技术准备1. 此方法只针对液压系统管路的冲洗,不包括液压站、油缸、马达等用油设备。
2. 索要液压系统原理图,弄清系统回路,其中包括各种阀组的换向动作,如系统较大不利于冲洗,可将系统拆分为2~3个回路或更多回路。
3. 如无特殊要求,一般带阀组冲洗(尽量带阀组冲洗)。
4.根据冲洗流速v>6m的要求,结合管径大小、管路长短、阀组多少(即考虑管道阻力)选择适合的冲洗液压站(大、中、小)。
5.落实原有液压站接口(入口)和各用油设备如马达、油缸接口(出口)形式和尺寸。
6.如有必要应到现场实地观察设备形状、结构,以便综合考虑冲洗实施方案。
二.材料准备1.加工各种接口所需连接件2.准备各种必要的连接软管(我们冲洗站接口尺寸为SAE2″、SAE1 1/2″、SAE1 1/4″重型)。
3.过滤器中的滤芯提前换好,另备数个滤芯。
4.备好现场冲洗的所需工具。
三.现场施工1.冲洗现场业主须提供75Kw电机的电源和50平方的3+1备用电缆。
2.业主备好冲洗用液压油(最好用今后工作使用的相同品牌和型号的液压油)。
3.冲洗液压站放在离管路接口较近的地方,接好电源后试车,调好电机转向。
4.连接好冲洗回路的各个接口,不用的端口封堵好。
5.打开冲洗站的所有截门,包括出油口、回油口、旁通回路。
6.冲洗站启动后,流量应逐渐加大,此时调节旁路截门,直至关闭。
7.冲洗开始后,应每隔20分钟用橡胶锤敲打管路各处,使管内杂质污物随震动流出。
8.冲洗2小时后管内油温应>40℃(随环境温度和管路长短不同有所不同),如温度过低可调节回油截门,使回油压力和流速加大,如温度>55℃应打开风冷降温。
9.如用设备所带液压站冲洗,过滤器应装在回油管路上,且回油口压力不应大于17bar,测压取样点放在过滤器的入口端。
10.冲洗2小时后并油温在40℃以上,即可用在线油品检测仪取样测试,油品指标好于NAS7级即完成冲洗,如未达标则继续冲洗,每2小时检测一次,直至合格达标。
- 1、下载文档前请自行甄别文档内容的完整性,平台不提供额外的编辑、内容补充、找答案等附加服务。
- 2、"仅部分预览"的文档,不可在线预览部分如存在完整性等问题,可反馈申请退款(可完整预览的文档不适用该条件!)。
- 3、如文档侵犯您的权益,请联系客服反馈,我们会尽快为您处理(人工客服工作时间:9:00-18:30)。
液压管路清洗技术标准公司标准化编码 [QQX96QT-XQQB89Q8-NQQJ6Q8-MQM9N]
RHQB 河南润华企业标准
RHQB/J201-2016
液
压
管
路
清
洗
技
术
标
准
2016-03-01发布 2016-03-01实施
河南润华通用装备有限公司发布
目录
液压管路清洗技术标准
1.适用范围
本标准规定了冲洗液压系统管路中固体颗粒污染物的方法。
这些污染物可能是在新液压系统的制造过程中或是在对现有系统的维修与改造的过程中被带入。
本标准补充但不代替供应商的要求,尤其当其要求比本标准的规定更为严格时。
液压管件的化学清洗和酸洗不适用与本标准。
2.引用标准
下列文件中的条款通过本标准的应用而成为本标准的条款。
凡是注日期的引用文件,其随后所有的修改单或修订版本均不适用于本标准。
凡是不注日期的引用文件,其最新版本适用于本标准。
GB/T 25133 液压系统总成管路冲洗方法
GB/T 17446 流体传动系统及元件
GB/T 14039-2002 液压传动油液固体颗粒污染等级代号
3.使用的设备、工具及材料
主要设备及工具
清洗泵、过滤器、油液颗粒计数器、力矩扳手、木槌。
材料
冲洗油、管接头、清洁塑料袋、堵头。
4.清洁度等级
冲洗的主要目的是为达到用户或供应商要求的系统或元件清洁度等级。
对于未规定清洁度等级的情况,可参见附录A的选择指南。
就铁路养护设备的液压管路清洗而言,可分为两类情况,即主油路和控制油路。
一般主油路液压传动系统中允许污染等级不应低于ISO4406:1999标准中的18/15级或NAS1638标准中的9级。
控制油路的污染等级不应低于ISO4406:1999标准中的16/13级或NAS1638标准中的7级。
5.冲洗要求
总则
5.1.1 要求冲洗的管路应建立专项文件来识别,并记录它们达到的清洁度等级。
5.1.2 冲洗方法宜与实际条件相适应。
但是,为保证获得满意的效果,应满足下列主要准则:
1)冲洗设备的油箱应至少清洁到与系统指定的清洁度相适应的水
平(见第4章);
2)注入系统的冲洗介质应通过合适的过滤器过滤。
3)冲洗设备的泵应尽可能地靠近管路的吸油口,以使流量损失最
小;
4)过滤器应靠近管路的回油口;吸油口也可以使用过滤器。
清除内表面颗粒
5.2.1 为了有效地清除液压管路的颗粒污染物,要求冲洗介质的流动状态为紊流。
介质的紊流流动能保证使管路系统中的颗粒污染物脱
落并通过过滤器清除。
应使用雷诺数(Re )大于4000的流动介质冲洗系统。
注:如果使用雷诺数小于4000的流体进行冲洗,管路中可能有层流段。
5.2.2 使用公式(1)和(2)可计算Re 和要求的流量(q v ): 21220V q Re
v d (1) 21220v d Re v q (2)
式中: q v ──流量,单位为升每分钟(L/min );
v ──运动粘度,单位为平方毫米每秒(mm 2/s );
d ──管路的内径,单位为毫米(mm )。
5.2.3 获得大于4000的Re 可能比较困难,Re 随着流量的增大或粘度的降低而增大。
降低粘度是获得紊流的首选方法。
减低粘度可通过提高冲洗介质温度或使用低粘度等级的系统工作介质。
震动、超声波或改变流向将有助于更快的使管路系统中的颗粒污染物脱落。
过滤器及颗粒的分离
1) 冲洗使用的过滤器决定了系统最终的清洁度等级和清洗时间。
2) 应选用具有合适过滤比的过滤器。
如果选用过滤比不合适的过
滤器,将出现达不到指定的清洁度等级或需要经过延长冲洗时
间才能达到的情况。
3) 过滤器应带有堵塞监控装置(如压差指示器)。
必要时应更换
滤芯,以保证压差在滤芯允许工作范围。
4)应尽可能使用大的冲洗过滤器。
最小冲洗过滤器应满足在冲洗
介质的实际粘度和最大流量下,通过清洁滤芯的最大的压降不
超过旁通阀或堵塞报警指示器设置值的5%.
6.液压系统中管路的冲洗
影响因素
为使液压系统管路达到满意的清洁度等级,需要考虑以下影响因素:
1)选择按GB/Z 19848-2005清洗过的元件,清洁度等级应至少与
规定的系统清洁度等级相同或更高。
元件供应商提供元件清洁
度等级的资料;
2)配接管路的初始清洁度;
3)采用合适的冲洗程序;
4)选择过滤比合适的过滤器,保证能在允许的时间周期内达到需
要的清洁度等级;
5)建立紊流状态,以移出并传输颗粒到过滤器。
系统处理
6.2.1 排净废油
最好在温度高的时候放掉废油。
清洗前应拆开一部分管路、阀、液压缸,检查其内部的锈蚀、污物黏附情况,并据此对油液污染程度和金属微粒作出分析,查明磨损部位并做好记录,以便采取相应的处理措施。
在拆除液压系统的管路之前应提前停机半个小时以上,使系统中的压力充分卸掉,以防在操作过程中系统中的残压对人员或机械造成伤害。
6.2.2 清洗油箱
必须用煤油清洗油箱中的油泥、锈、油漆剥落片等;对油箱内残油与杂质要用海绵吸干净,忌用棉纱破布,以防残留纱头在油箱埋下后患;油箱中的滤油器要经常检查清洗,发现损坏及时更换,清洗流程参见液压油箱清洗技术标准。
6.2.3 元件防护
系统中拆卸的液压元件应及时采用清洁塑料袋或堵头封堵保护。
管路处理
6.3.1 管路外表面处理
管路拆除前,为了维持其清洁度,应使用适当的清洗液或抹布对外表面进行处理,尤其是管接头处。
有氧化层和铁锈的管件应按照制造商和用户间达成的协议进行处理。
6.3.2 拆卸管路
在每根液压管路上做标记,保证清洗完成之后能装配回原位置。
主油路和控制油路的管路要分开码放,拆卸的管路要及时用清洁塑料袋或堵头封堵保护,并存放在清洁、干燥的地方。
管路冲洗
6.4.1 选择清洗油
当系统管路、油箱较干净时,可选用与工作油液相同黏度的清洗油;如系统内不干净,可选用黏度稍低的清洗油清洗。
清洗油应与系统工作介质、所有密封件的材质相容。
清洗油的用量视冲洗管路的多少而选定。
6.4.2 加热清洗油
热油能使系统内附着物容易游离脱落,如果现场条件允许可加热至50~60℃,清洗压力为~,清洗油流量应尽可能大些,以利于带走污物。
6.4.3 安装滤油器
在清洗回路中,进油口安装20μm的粗滤油器,回油口安装5μm 的精滤油器。
每隔半小时拆开滤油器清扫一次,视冲洗情况适时更换滤油器滤芯。
在被清洗管路的出油口处增加采样点,用颗粒计数器检测油样,知道满足要求时停止。
6.4.4 应使液压泵间歇运转
为使清洗效果好,应使液压泵转转、停停。
在清洗过程中应用木槌轻轻敲击油管数次,以促使污物尽快脱落,管路的弯曲和焊接部位要多敲击,但不可用力过猛,以防损坏油管,敲击时间占清洗时间的15%。
6.4.5 确保清洗液流动为紊流状态
为了有效的清洗,清洗液流动必须成为紊流状态,即保证雷诺数在4 000以上才能确保清洗效果好;否则,清洗液应增加流量,升高温度,降低黏度。
小流量室温下清洗,一般效果较差。
注:当冲洗效果较差时可参考公式(1)和(2)计算Re和要求的流量q v
6.4.6 排净清洗油
清洗终了应将管路中的清洗油排除干净,可松开管路排油后并用压缩空气吹扫,或加入工作油液带走清洗油。
排净清洗油后,应尽快安装管路,以防管路内凝结水汽、进入杂质等。
液压管路的安装
6.5.1 在液压管路的安装过程中,应避免对管路进行焊接、钎焊或加热。
以防止产生氧化层。
如果不可避免,则管路应重新清洗和保护。
6.5.2 在安装过程中,管路和元件所有的保护元件应尽可能在最后阶段移去,并且在安装的过程中应徒手安装不能穿戴手套等劳保用具。
7.最终清洁的检验
最终清洁度等级应按照GB/Z 20423验证,并应在冲洗操作完成前形成文件。
附录 A
(资料性附录)
系统清洁度等级要求指南
系统可能需要搞清洁度的应用场合
当高可靠性为控制要素或系统包含下列元件是,系统需要高的清洁度:
1)比例阀或伺服阀;
2)小流量的流量控制阀和减压阀,特别是在承受高压降的条件下;
3)工作状态接近性能等级的马达和泵。
系统可能需要中等清洁度的应用场合
当元件在供应商和用户一直同意的非正常工况下运行,且总时间又相对受控制时,系统应规定中等清洁度。
满足系统高、中等清洁度要求的介质中固体颗粒污染物等级指南
表给出了满足系统高、中等清洁度要求的介质中固体颗粒污染物等级的指南。
表满足运行系统高、中等清洁度要求的介质中固体颗粒污染物等级的指南。