五金(塑胶)涂装不良对策分析
浅谈塑料件涂装与漆膜常见弊病处理

浅谈塑料件涂装与漆膜常见弊病处理随着生产制造技术的不断发展,塑料件越来越广泛地应用于各个领域。
为了满足消费者对产品色彩的需求,以及延长产品使用寿命,制造商们越来越注重塑料件的涂装和漆膜处理。
但是,塑料件涂装和漆膜存在常见的弊病,如果不及时处理,会严重影响产品的使用寿命和外观质量。
本文将从常见的塑料件涂装和漆膜弊病入手,介绍处理方法和预防措施。
一、常见弊病1.涂层起泡涂层起泡是由于表面存在油脂、水汽、灰尘等杂质,或涂装环境湿度过大,涂装前表面处理不彻底等原因造成。
涂层起泡严重影响外观质量,同时容易使涂层破裂、脱落。
2.熔融爆裂塑料件涂装时,由于过高的烤漆温度或烘烤时间过长,容易导致熔融爆裂。
熔融爆裂会造成漆膜厚薄不一,表面质量不良,且会导致产品变形、缩水等问题。
3.漆膜脱落漆膜脱落是由于涂装前表面处理不彻底,或使用低质量的涂料和油漆导致的。
漆膜脱落会造成外观质量不良,同时降低产品的保护性能。
4.色差问题色差问题是由于批次、环境、产品材质等原因造成。
色差严重影响产品的美观度,同时也会对消费者的体验产生不良影响。
二、处理方法1.涂层起泡涂层起泡时,应尽快将起泡处涂层抹平,避免涂层分裂。
如果局部分裂,应使用专业液体修补材料粘合分裂处。
避免涂装环境湿度过大,同时在涂装前应彻底清洁表面。
2.熔融爆裂熔融爆裂时,应尽快将产品取下,让其自然冷却,避免继续加热会导致更大的熔融爆裂。
同时应检查烤漆温度和烤漆时间是否合适,排除设备故障,及时调整涂装参数。
3.漆膜脱落漆膜脱落时,需要重新涂装。
在涂装前应彻底清洗表面,确保完全去除油脂和灰尘。
选择质量可靠的涂料和油漆,同时控制好涂料的厚度和均匀度。
4.色差问题色差问题时,需要通过设备调整和涂料配料解决。
同时在使用工具和设备时应尽量保持稳定,尽量避免因操作失误或设备故障造成的色差。
三、预防措施1.加强表面处理对于压铸、注塑或挤出件等塑料产品,在经过模具成形或切割后,表面会产生一定程度的氧化,油脂,灰尘等杂质,这些杂质直接影响后续涂装的质量。
涂装不良缺陷产生原因和预防措施

14.遮 盖 力 差
形式: 透过面漆可以看见少许底漆颜色,颜色不均匀,甚至 有发花的现象
成因: 1.面漆在喷涂前未充分搅拌,油漆与固化剂未充分混合 2.使用的稀释剂不正确 3.油漆粘度太低 3.油漆本身遮盖力差
预防: 1.喷涂前要将油漆充分搅拌 2.使用正确的调配粘度及配套的稀释剂 3.选用品质高的油漆
﹑
8.起 泡
形式: 1.潮湿起泡以不同的形状﹑尺寸,在不同的区域以不同的 密度发生 2.发生在漆层与漆层之间(底漆表面)或整个油漆结构 (素材件表面) 3.因涂层是密闭的,故在干燥和低温气候下气泡现象也会 减少 成因: 1.欲喷涂表面未进行充分和彻底清洁(由于使用不洁净的 水或手汗留在工件表面而导致水中可溶性盐的污染,擦拭 印像是清晰可见的气泡排列的“串珠”),当喷涂面漆后, 工件长时间存放于潮湿环境而形成的潮湿效应 2.空气压缩机的水分没有完全被过滤 3.进行湿打磨后,水分没有完全挥发 预防: 1.保证工件表面水分完全挥发﹑干燥 2.确保工件表面彻底清洁并无手汗 3.保证空气压缩机的油水彻底分离
欲喷涂表面未进行充分和彻底清洁由于使用不洁净的水或手汗留在工件表面而导致水中可溶性盐的污染擦拭印像是清晰可见的气泡排列的串珠当喷涂面漆后工件长时间存放于潮湿环境而形成的潮湿效应2
塑料件的涂装不良缺陷
• 常见的涂装缺陷,及分析和改进
• 涂装环境对涂装的影响
1.剥
落
形式: 1.整个油漆结构 2.涂层与涂层间
13.云 斑
形式: 云斑一般出现于大面积喷涂金属银粉漆的时候,呈现像 云彩般,又称“喷花”现象 成因: 1.喷涂金属银粉漆时,漆层不均匀 2.喷涂金属银粉漆后,挥发时间不充足,或喷涂第一层罩 光清漆时,漆膜太湿,令部分金属银粉漆被清漆溶解,金 属漆内的银粉颗粒浮起而改变其位置 3.喷涂气压过大或过小,或喷涂金属银粉漆时,过厚或过 薄,致使金属银粉漆排列不均匀 4.喷涂环境温度过高,或使用了不适合温度的稀释剂 5.使用了与金属银粉漆不配套的清漆 预防: 1.按照油漆的施工要求进行喷涂 2.按照喷涂温度调配稀释剂 3.注意油漆的厚度并掌握好喷涂的流平时间
涂装前处理不良对策
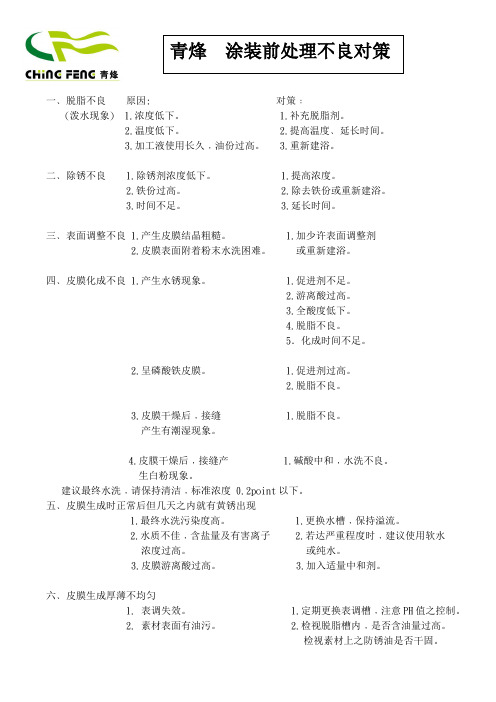
一﹑脱脂不良 原因: 对策﹕(泼水现象) 1.浓度低下。
1.补充脱脂剂。
2.温度低下。
2.提高温度﹑延长时间。
3.加工液使用长久﹐油份过高。
3.重新建浴。
二﹑除锈不良 1.除锈剂浓度低下。
1.提高浓度。
2.铁份过高。
2.除去铁份或重新建浴。
3.时间不足。
3.延长时间。
三﹑表面调整不良 1.产生皮膜结晶粗糙。
1.加少许表面调整剂2.皮膜表面附着粉末水洗困难。
或重新建浴。
四﹑皮膜化成不良 1.产生水锈现象。
1.促进剂不足。
2.游离酸过高。
3.全酸度低下。
4.脱脂不良。
5.化成时间不足。
2.呈磷酸铁皮膜。
1.促进剂过高。
2.脱脂不良。
3.皮膜干燥后﹐接缝 1.脱脂不良。
产生有潮湿现象。
4.皮膜干燥后﹐接缝产 1.碱酸中和﹐水洗不良。
生白粉现象。
建议最终水洗﹐请保持清洁﹐标准浓度 0.2point 以下。
五﹑皮膜生成时正常后但几天之内就有黄锈出现1.最终水洗污染度高。
1.更换水槽﹐保持溢流。
2.水质不佳﹐含盐量及有害离子 2.若达严重程度时﹐建议使用软水浓度过高。
或纯水。
3.皮膜游离酸过高。
3.加入适量中和剂。
六﹑皮膜生成厚薄不均匀1. 表调失效。
1.定期更换表调槽﹐注意PH 值之控制。
2. 素材表面有油污。
2.检视脱脂槽内﹐是否含油量过高。
检视素材上之防锈油是否干固。
青烽 涂装前处理不良对策原因: 对策﹕七﹑素材生成皮膜后﹐短时间内在底部出现黄锈1.最终水洗不良﹐有害离子随水流 1.更换水洗槽﹐保持溢流。
聚集底部或使用气枪吹落素材上之积水。
八﹑皮膜生成产生明显条纹1.喷嘴方向偏差。
1.调整喷嘴方向。
2.除油不佳。
2.调整脱脂浓度﹐加强脱脂工程。
3.第一﹑二水洗不佳。
3.更换水洗槽。
4.表调老化。
4.含铁量过高时﹐必须更新。
注﹕脱脂后第一道水洗全碱污染度在5point以下﹐第二道水洗全碱污染度在2point以下﹔皮膜化成后第一道水洗全酸污染度在2point以下﹐第二道水洗全酸污染度在0.2point以下。
涂装作业产生缺陷的原因及其防治措施
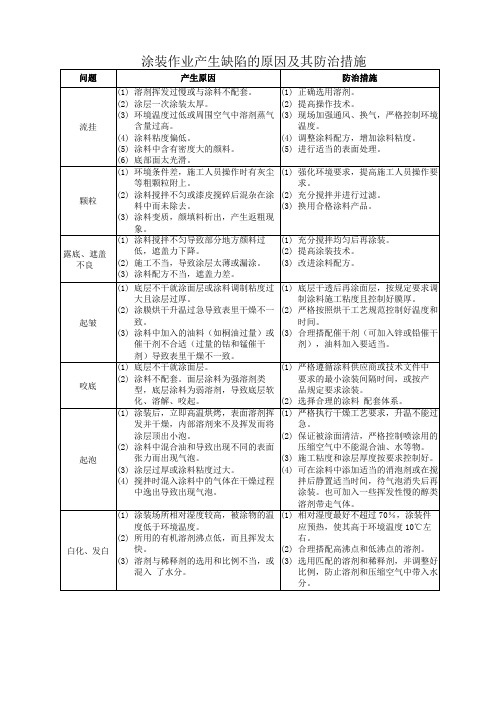
(3)施工粘度和涂层厚度按要求控制好。
(4)可在涂料中添加适当的消泡剂或在搅拌后静置适当时间,待气泡消失后再涂装。也可加入一些挥发性慢的醇类溶剂带走气体。
白化、发白
(1)涂装场所相对湿度较高,被涂物的温度低于环境温度。
(2)所用的有机溶剂沸点低,而且挥发太快。
(1)严格按照产品说明进行配比使用。
(2)选择合适的性差,释 放气泡性差。
(2)涂料中混入油、水,造成干燥时涂膜表面出现针孔。
(3)涂料干燥不当,表层快速干燥成膜底层溶剂蒸发时冲破表层涂膜出现针孔。涂装环境湿度过大或被涂物表面有污物和小孔。
(1)选择合适的涂料,施工时调整合适的粘度。
(1)底层干透后再涂面层,按规定要求调制涂料施工粘度且控制好膜厚。
(2)严格按照烘干工艺规范控制好温度和时间。
(3)合理搭配催干剂(可加入锌或铅催干剂),油料加入要适当。
咬底
(1)底层不干就涂面层。
(2)涂料不配套。面层涂料为强溶剂类型,底层涂料为弱溶剂,导致底层软化、溶解、咬起。
(1)严格遵循涂料供应商或技术文件中 要求的最小涂装间隔时间,或按产 品规定要求涂装。
露底、遮盖不良
(1)涂料搅拌不匀导致部分地方颜料过低,遮盖力下降。
(2)施工不当,导致涂层太薄或漏涂。
(3)涂料配方不当,遮盖力差。
(1)充分搅拌均匀后再涂装。
(2)提高涂装技术。
(3)改进涂料配方。
起皱
(1)底层不干就涂面层或涂料调制粘度过大且涂层过厚。
(2)涂膜烘干升温过急导致表里干燥不一致。
(3)涂料中加入的油料(如桐油过量)或催干剂不合适(过量的钴和锰催干剂)导致表里干燥不一致。
塑胶产品喷涂异常的处理

浅谈喷涂异常处理喷涂产品技术员,QC和生产人员,如果对喷涂的异常处理有些了解的话,就会对工作有新帮助,就可以通过新遇到的质量缺陷进行分析找出其原因以及要采取的改善对策,从而提高产品质量的鉴别能力,下面就喷涂日常出现的异常处理,行业内要作的物性测试作些简单的介绍。
一.浅谈喷涂异常处理:1.变色:由于油漆质量不好会产生一系列的不良现象,异色就是其中之一。
之所以会出现异色、变色由以下几种原因造成:(1)涂料中颜料的密度不同,密度大的颜料下沉,轻的浮在上面(2)含铅式铜系颜料与硫化氰起化学反应变黑。
改善对策:(1)彻底均匀搅拌后再使用,(2)有硫化氰的环境不使用含铅式含铜系颜料2.发哑、发白:如果天气温度过重,硝基漆易泛白,或移植释剂配比不当会出现喷漆产品光泽度不够颜色发哑(发暗)改善对策:(1)可先低温预热被涂物,或加入10—20%的防白剂,喷漆场所应尽量保持恒温,恒湿状态,可防止喷涂产品发白(2)当空气中的温度过高,大多是在一些比较简陋的喷漆场所,可将喷涂完毕之产品放在烘炉内烘烤几分钟可防止喷漆品颜色发哑3:附着力不够:由于一些油漆质量不好或塑胶素材脏污,油漆喷上会出现脱漆或涂膜本身无法附着于素材表面或底部.改善对策:1)如果油漆质量不良应该调换,也可使用较稀释剂调漆,或适当加入一定比例固化剂;<我公司目前不用>(2)为防止产品表面由于脏污不清洁而造成的脱漆,必须于喷漆前先将素材清洁干净后方可喷涂.《我社采用前处理/静电除尘》4.针孔,油点:产品喷涂后在溶剂挥发到初期结膜阶段,由于溶剂的急剧挥发,特别是受高温烘烤时漆膜收缩来不及补足空档,而形成一系列小穴即针孔,如果溶剂使用不当,或温度加热高,过快就易产生针孔,当喷漆环境相对过高,或喷涂设备的油水分离器失灵,喷涂时水分随空压机经喷嘴与涂料同时喷出,也会造成喷涂后出现表面针孔.改善对策:(1)烘烤型涂料粘度要适中,喷涂后要在恒温下静置约5—10分钟,烘烤时,先低温预热后按规定温度和时间使溶剂能正常挥发;(2)使用适当稀释剂,避免加热过于剧烈;(3)喷涂面漆时,喷漆环境相对温度应于65%以下为宜,检查油水分离器的可靠性,空气压缩机经过滤,杜绝油和水及其它杂质带进涂料中。
涂装不良现象与改善对策

涂装不良现象和改善对策一、流漆10-1技术资料标准用纸 发生源 产生因素改善方法涂 料 面1.粘度太低 2.干燥能力不够 3.防垂流剂不足 1.提高涂料粘度 2.添加快干溶剂 3.请涂料厂微调 技 术 面1.喷涂方法错误 2.喷幅太窄 3.喷涂距离太近 4.膜厚太厚1.修正喷涂方式 2.适当调整宽幅 3.修正喷涂距离 4.吐出量调小,喷涂次 数减少,运行速度 加快其 他1.悬挂方式 2.温湿度不稳1. 改善(变)悬挂置放 方式 2.随温差调整二、油点10-2发生源产生因素改善方法涂料厂 涂料生产过程污染 1.轻微:使用快干溶剂克服 2.严重:由涂料厂解决 涂装场 1. 使用到不洁空桶或工具 2.不同系统涂料混合 1.保持搅拌区工具不受污染 2.做好标示管制 成型场 1.模具油污染2.离型剂、油、过程污染1.成型时模具清洗 2.使用水性离型剂 *以清洁剂洗擦素材 其它1.压缩机油水混入 2.手套或手不洁接触 3.室内污染 4.外围工厂污染1.实施定期保养 2.保持干净、清洁 3.避免使用高挥发油脂类 制品4.改变或提高供气口 5.使用密壁式涂装室三、桔皮10-3发生源 产生因素改善方法涂 料 面 涂料平坦性不良 涂料厂调整流平剂 技 术 面 1.涂料粘度太高 2.干燥速度太高 3.喷涂气压太低 4.涂料吐出量太小 1.降低涂料粘度 2.改用慢干溶剂 3.提高喷涂气压 4.加大涂料吐出量 其 他1.温度太高 2.喷涂技术1.使用慢干溶剂 2.降低涂料粘度 3.喷涂方法教导四、剥离10-4发生源 产生因素改善方法涂 料 面1.涂料设计不良 2.涂料系统不同3.下层涂膜受上层涂膜/溶剂破坏/浸蚀 1.涂料厂对策 2.以同系统涂料作业3.反应固化前或待完全 固化后再覆涂 技 术 面1. 半固化涂膜被溶解(二液化)2.研磨破坏层(见素材)受溶剂渗透,旧涂膜,吸收液体,气体而膨胀凸起1. 固化前或待完全固化后再覆涂2.改善研磨方式3.改用浸蚀力较弱溶剂五、皱纹不良现象有分:小皱纹、不规则皱纹、线状形皱纹发生原因改善对策上层溶剂浸蚀同系统涂料更改溶剂下层涂膜产生下层涂膜软化不同系统涂料对喷须测试验,以避免造成不良10-5六、龟裂10-6发生原因 改善对策涂层与涂层之间膜厚差异太大,干燥能力差别又遇高温烘烤,涂膜收缩产生不良 1. 控制膜厚和下层及上层干燥对喷时间 2.控制烘烤温度 弹性大的下涂料上面覆盖弹性小涂料引起调整涂料10-7八、白化不良现象:部份涂膜变白光泽消失10-8发生原因 改善对策空气中的水份在涂膜形成中凝集而成水白状使用高沸点溶剂或防白化剂 通常在下雨或高温度处拉卡(LACQUER )漆最易产生九、脱漆10-9发生源 产生因素处理对策涂料面1无法附着素材 2无法附着下层 1涂料重设计 2涂料重设计 技 术 面素材 面 1喷错底涂 2未喷底涂3未洗净或用错洗净液 4油污 1喷涂正确底涂 2喷上底涂 3使用正确洗净液 4保持产品清洁 涂 层 面 1涂层不相溶 2受污染1涂料重设计 2保持产品清洁其 他1干燥后再覆盖(二液) 2未研磨(二液) 3底涂研磨掉1未干燥前覆盖 2研磨至亲水性 3底涂修补10-1010-1110-1210-13。
涂装不良缺陷产生原因和预防措施课件 (一)

涂装不良缺陷产生原因和预防措施课件 (一)涂装不良缺陷是指涂装过程中出现的各种质量问题,这不仅会影响产品的外观,还会影响产品的性能和使用寿命,因此应该尽力避免这种问题的发生。
下面我们将介绍涂装不良缺陷产生的原因和预防措施。
一、产生原因1.涂装前表面处理不彻底:表面处理不彻底可能导致油污、灰尘等因素存在,这些因素会影响涂装的粘合力,导致涂层起泡、起皮等问题。
2.涂料质量不佳:涂料的品质影响着涂装的品质,如果采用质量不佳的涂料,就容易产生涂层厚度不均、发白、开裂等现象。
3.涂装条件不合适:湿度、温度等因素都会影响涂层的品质,如果涂装条件不合适,就会出现涂层缺陷,比如崩边、干裂等。
4.施工不规范:工人的技术不熟练、经验不足,或者跟不上生产工艺的变革,都可能导致涂层质量的下降,比如出现漏涂、滴涂、刷痕等问题。
二、预防措施1.完善表面处理环节:表面处理是涂装前不可或缺的步骤,只有彻底完成了表面处理,才能保障涂层的粘合度和平稳度,预防涂装不良缺陷产生。
2.选用优质涂料:优质的涂料可以保证涂层的品质,能够防止出现斑、裂、崩等情况,因此选择适用于产品的涂料非常重要。
3.合理的涂装条件:涂装前要做好湿度、温度等环境因素的调试,尤其在特殊的季节,如雨季、高温季节等,应特别注意调整涂装参数,以保证涂层的品质。
4.规范化的施工流程:制定规范的施工流程,包括参数、设备、工具和操作员等,能够大大提高工作效率,保证涂装质量,并避免因人为错误导致的涂装不良缺陷。
总结:涂装不良缺陷的产生,很大程度上源于环节的不同,通过展示涂装前所需注意的事项和涂装过程中的不同纰漏导致的敷层缺陷,可以让厂家查漏补缺,在涂装过程中,尽力降低产品的损耗率和不良品率,提升涂装生产效果和运营效益。
常见涂装质量问题分析
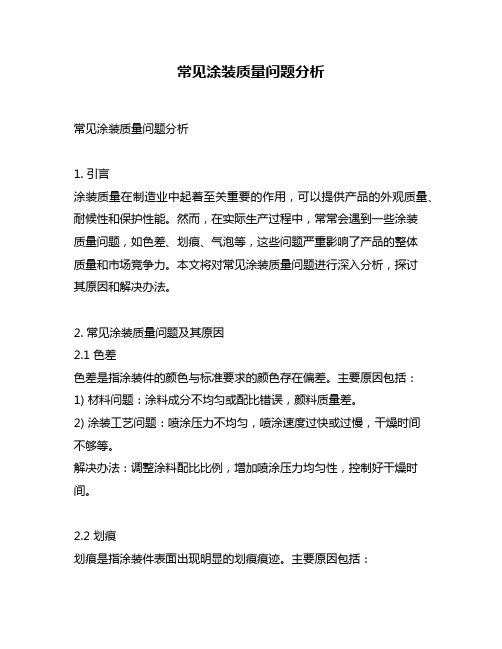
常见涂装质量问题分析常见涂装质量问题分析1. 引言涂装质量在制造业中起着至关重要的作用,可以提供产品的外观质量、耐候性和保护性能。
然而,在实际生产过程中,常常会遇到一些涂装质量问题,如色差、划痕、气泡等,这些问题严重影响了产品的整体质量和市场竞争力。
本文将对常见涂装质量问题进行深入分析,探讨其原因和解决办法。
2. 常见涂装质量问题及其原因2.1 色差色差是指涂装件的颜色与标准要求的颜色存在偏差。
主要原因包括:1) 材料问题:涂料成分不均匀或配比错误,颜料质量差。
2) 涂装工艺问题:喷涂压力不均匀,喷涂速度过快或过慢,干燥时间不够等。
解决办法:调整涂料配比比例,增加喷涂压力均匀性,控制好干燥时间。
2.2 划痕划痕是指涂装件表面出现明显的划痕痕迹。
主要原因包括:1) 材料问题:使用硬度不足的刷子或湿润的布进行擦拭操作,引起表面划痕。
2) 工艺问题:涂装工艺中未做好防护措施,导致划痕。
解决办法:使用适当的擦拭工具,加强涂装工艺中的防护措施。
2.3 气泡气泡是指涂装件表面出现的小气泡或大气泡。
主要原因包括:1) 材料问题:涂料中含有挥发性溶剂,涂装时未对涂料进行适当的搅拌。
2) 工艺问题:涂装时喷涂压力过大,喷涂速度过快,导致气泡的产生。
解决办法:使用无挥发性溶剂的涂料,加强对涂料的搅拌,控制喷涂压力和速度。
3. 对涂装质量问题的理解和观点涂装质量问题不仅仅对产品的外观质量造成了影响,还可能影响产品的使用寿命和性能。
对涂装质量问题的分析和解决非常重要。
通过对涂装工艺的不断改进和技术的创新,可以减少涂装质量问题的发生,提高产品的整体质量和市场竞争力。
4. 总结回顾涂装质量问题是制造业中常见的问题之一,其中包括色差、划痕和气泡等。
这些问题的存在严重影响了产品的外观质量和市场竞争力。
通过分析和解决这些问题的原因,我们可以采取相应的措施,如调整涂料配比比例、增加喷涂压力均匀性等。
通过不断改进涂装工艺和技术,可以提高产品的整体质量和市场竞争力。
- 1、下载文档前请自行甄别文档内容的完整性,平台不提供额外的编辑、内容补充、找答案等附加服务。
- 2、"仅部分预览"的文档,不可在线预览部分如存在完整性等问题,可反馈申请退款(可完整预览的文档不适用该条件!)。
- 3、如文档侵犯您的权益,请联系客服反馈,我们会尽快为您处理(人工客服工作时间:9:00-18:30)。
調整油量大小 檢討塗裝方法, 檢討塗裝方法,必要時分兩次塗裝 參照 SONY 或相關權威標準 更換油漆 各細節確認, 各細節確認,規范化作業 根據油漆特性調配後限時內塗裝 確認烤箱溫度與時間, 確認烤箱溫度與時間,必要提高溫度或延長 幹燥時間(必須做好相關試驗及記錄) 幹燥時間(必須做好相關試驗及記錄)
塗裝作 1. 作業流程安排不合理
2. 作業者操作方法不熟悉
根據實際需要進行工序排程 根據實際需要進行工序排程 培訓統一標準化作業 採用靜電除塵後限時再塗裝 ( 定時點檢控制進出風量大小 排風量稍大於 抽進風量) 抽進風量)
業方法 3. 塗裝前除塵不足
1. 抽進風量與排出風量比例失衡
設備保養 點檢不足
粗糙異色 5. 不安定的塗料供給
6. 氣管、 氣管、油管壓力不暢 氣管、油管壓力太大或太小 膜厚不均 7. 氣管、油管壓力太大或太小
色差
8.
噴槍油量調整不適
積油少油 9. 噴槍行走速度太慢或太快
10. 塗裝次數、角度、行走路線不穩定 塗裝次數、角度、
飛油發亮 11. 塗膜厚度不均勻
12. 塗裝距離太近或太遠 13. 生地品油污附著 14. 幹燥異常 15. 氣候潮濕 1. 2. 3. 塗裝後幹燥預熱時間過短 塗裝後預熱溫度過高 幹燥溫度或時間異常 異物附著 油漆調配異常 生地品潮濕 生地品處理不徹底 塗裝操作方法異常 水櫃水簾水滴外濺至部品上
硬度 不足
鉛筆硬度
5. 烤箱異常
烤箱內溫度均勻度、 烤箱內溫度均勻度、溫度檢測器與時間控制 器、風戽等點檢確認
測定 NG
6. 生地品本身材質或表面處理有污不潔
確認生地品狀況, 確認生地品狀況,改善部品表面光滑度前處 品狀況 理、白電油擦拭塗裝表面
7. 8. 1. 2.
塗裝方法存在漏失 塗膜不均 從業人員品質意識不強 操作工序不熟悉
檢討塗裝方法 檢討塗裝方法 新進人員品質意識培訓與定期考核 新進人員品質意識培訓與定期考核 配制相關防靜電器具作業 重新調整, 重新調整,結合實際操作規劃 確認調整預熱幹燥條件與制定作業方法
傷
碰傷刮傷 3. 人員作業防護措施不足
4. 5. 工序安排缺乏整體連慣性 塗裝品油漆未完全幹燥作業
制定新進檢查人員培訓方法, 制定新進檢查人員培訓方法,根椐客戶與產 進檢查人員培訓方法 外觀品從業檢查人員個人主觀意識較 品特性由專職品質擔當不得少於一周理論 培訓( 培訓 ( 每種塗裝品塗裝目的及重點主外觀 面、次外觀面要求與實物外觀限度)與實物 次外觀面要求與實物外觀限度) 考核,考核合格方可上崗, 考核,考核合格方可上崗,減少因人為誤判 而造成損失 明確客戶判定標準, 明確客戶判定標準,品質擔當人員必須具有 個人主見及與客戶保持密切聯系
1.
單板塗裝時間超長
( 單板塗裝時間盡量縮短 改善塗裝方法或減 少單板塗裝數量, 分鐘內完成) 少單板塗裝數量,盡量控制 1 分鐘內完成)
其他
2. 3. 4. 5.
人員走動性頻繁, 人員走動性頻繁,空氣流動性大 人員著裝不適 人員著裝不適 塗裝區濕度太低空氣過於幹燥 塗裝區周圍環境污染
控制人員走動性及塗裝室內門開啟頻率 無塵服標準著裝作業 採用噴水提高濕度 確保 100,000 級以上塗裝空間並定時保養 , 第二頁
五金(塑膠) 五金(塑膠)表面塗裝常見不良分析
不良 不良因素 名稱 塵點 異物
1. 2.
第一頁 共三頁
原 因 分 析
前處理清洗不徹底 待塗裝品放置時間過長
改 善 對 策
確認表面前處理效果 表面處理完成品限時內塗裝 放置場所確保環境無塵不潮濕 盡量採用防靜電材質,特別避免使用紙箱、 盡量採用防靜電材質,特別避免使用紙箱、 紙板或木卡板
12. 室內外溫差太大,部品潮濕塗裝 室內外溫差太大,
室內溫度控制 18-27℃,確保部品幹燥 ℃ 定時點檢或追加 AIR 過濾器 前處理工序確認部品無污無油脂, 前處理工序確認部品無污無油脂,必要時用 品無污無油脂 白電油擦拭後再塗裝
掉漆
13. AIR 管殘留水份 14. 表面前處理不徹底
15. 噴槍時出油量過大 16. 塗裝方法存在漏失 17. 信賴性試驗方法與判定不合理 1. 2. 3. 4. 油漆本身硬度不足 油漆調配、 油漆調配、攪拌等作業不規范 調配後放置時間超時塗裝 幹燥條件異常
油漆調配後放置時間太長 幹燥溫度太高或太低 幹燥時間太長或太短 幹燥烤箱異常
盡量確保調配後 4H 內使用完畢 設定溫度確認 設定時間確認 烤箱內溫度均勻度、 烤箱內溫度均勻度、溫度檢測器與時間控制 器、風戽等點檢確認
9.
生地品與油漆本身不兼容
更換油漆或檢討塗裝方法 改善生地品表面光滑度前處理、 改善生地品表面光滑度前處理、追加添加劑 第三頁
部品不潔 3. 待塗裝品放置場所不適
4. 部品包裝材質易附塵
1.
調漆場所防塵效果差 油漆過濾網網目不適 調配器具不潔 調漆作業不規范 調配完成存放防塵不足 調配完成放置超時
確保場所無塵, 確保場所無塵,定時點檢確認 不同油漆選擇配套專用過濾網 確保器具整潔, 確保器具整潔,定時點檢確認 器具整潔 制定標準作業指書按規作業 調配完成做好密封防塵 4H 內使用完畢 選用鋁材、銅材、 選用鋁材、銅材、尼龍等材質 參照部品實況與塗裝方法專用定制 根據實際定時保養, 根據實際定時保養,一般 2H/次 次
氣泡 泡 水泡
4. 5. 6. 7. 8. 9.
10. AIR 管道中殘留水份
掉漆
輕碰輕刮 膠紙磨擦
1. 2. 3. 4.源自作業手法不規范, 作業手法不規范,掉漆判定方法是否正確 油漆材料本身特性達不要求 油漆或調配劑失效或使用錯誤 油漆調配、 油漆調配、攪拌作業不規范
耐腐性等 信賴性試 驗 NG
5. 6. 7. 8.
油漆 不潔
2. 3. 4. 5. 6.
噴塗治 1. 治具材質選用不適
2. 治具設計欠佳
具不潔 3. 治具使用清潔時間超長或破損 供油供氣 1. 作業完了未及時保養油管
2. 噴槍、 噴槍、油管系統不潔 過濾器、 系統不潔 3. 過濾器、氣管系統不潔
作業完了及時保養, 作業完了及時保養,確認各接頭無漏油漏氣 定時保養 定時保養, 定時保養,排放
外觀檢查判定基 準不明確
個人擔當權責、 強,個人擔當權責、判定方法與品質意 識等不統一 廠內與客戶之間判定不統一 新機種產量判定
10. 生地品表面光滑附著力差 生地品表面光滑附著力差 光滑
五金(塑膠) 五金(塑膠)表面塗裝常見不良分析
不良 不良因素 名稱 原 因 分 析 改 善 對 策
增加油漆附著力或白電油擦拭 11. 氣候潮濕,濕度大 氣候潮濕,
共三頁
部品表面用白電油擦拭預熱後再塗裝, 部品表面用白電油擦拭預熱後再塗裝,必要 時追加除濕機降低濕度
2. 3. 4. 5. 6. 7.
水櫃水簾流量太少 水櫃內水位太高或太低 各道進出風道濾網附塵多 抽進風含塵量大 噴槍型號選擇不當 幹燥線或烤箱附塵多
以水滴不外濺為準 控制於上下水位限內(確認頻度: 控制於上下水位限內(確認頻度:4H/次) 次 各道濾網按實際需要定時清潔保養或更換 加強初效進風隔層過濾及周圍環境塵埃 根據塗裝部品實況選槍型 定時保養清潔
五金(塑膠) 五金(塑膠)表面塗裝常見不良分析
不良 不良因素 名稱
1. 2. 3. 4.
共三頁
原 因 分 析
塗裝材質粗糙 油漆調配有誤 油漆粘度太大或太小 油漆粘度太大或太小 油漆攪拌不均勻
改 善 對 策
確認選別不良材質, 確認選別不良材質,調整相關參數 重新調配再次確認油漆噴塗效果 根據氣候與部品要求以實際為準 按標準化作業, 按標準化作業,必須攪拌 10min 以上 採用自動油漆供應機連續塗裝 確認氣管、 確認氣管、油管接頭及壓力閥狀況 確認氣管、 確認氣管、油管壓力閥壓力於正常范圍內 調整最佳狀態 調整最佳狀態 調整最佳狀態, 調整最佳狀態,參數固定 塗裝手法矯正, 塗裝手法矯正,統一標準 調整最佳狀態 確認表面前處理狀況、 確認表面前處理狀況、白電油擦拭 幹燥條件及烤箱確認 幹燥條件及烤箱確認 油漆預熱或增加除濕機 根據實況調整預熱時間 根據實況調整預熱時間 確認溫度與時間並檢測烤箱狀況 確認表面前處理狀況、 確認表面前處理狀況、白電油擦拭 重新調配再次確認油漆噴塗效果 確認部品狀態, 確認部品狀態,必要時預熱後塗裝 確認表面前處理狀況、 確認表面前處理狀況、白電油擦拭 確認作業工序及相關參數 調整水簾流量, 調整水簾流量,以水滴不外濺為準 壓力閥定時排氣或追加壓力 壓力閥定時排氣或追加壓力 規范化作業, 規范化作業,參照相關塗裝信賴性實驗基準 油漆再檢討更新 確認材質並確保有效期內使用 統一規范化作業, 統一規范化作業,不定時確認