超速磨削技术在机械制造领域的发展与应用
超高速磨削技术在机械制造中的分析

超高速磨削技术在机械制造中的分析【摘要】随着科学技术不断发展与进步,为了提高机械制造的质量与效率,我国已经逐渐引进了超高速磨削技术。
随着这些年的应用逐渐增加,超高速磨削技术在机械制造中的应用经验越来越丰富。
本文首先概述了超高速磨削技术,对其原理及优势等进行了分析,然后就其在机械制造中的应用进行了详细分析。
【关键词】超高速;磨削技术;机械制造1.超高速磨削技术概述1.1技术分析超高速磨削技术属于超高速加工技术中主要的一种,而超高速加工技术指的是利用超硬材料的刃具,通过提高其切削速度与进给速度来实现材料加工精度、切除率及加工质量提高的一种技术。
就目前来看,超高速加工切削速度往往随着不同的材料及切削方式而不同。
超高速加工技术包括了很多方面,比如说超高速进给单元制造技术、超高速加工用刀具制造技术、超高速切削与磨削机理研究等,其在我国制造业中的应用越来越深入。
其中,最为先进的一种技术为超高速磨削技术。
1.2磨削技术原理在高速或超高速磨削加工中,其余参数保证不便的情况下,砂轮速度大幅度提高,单位时间中磨削区产生的磨粒数就会增加,而磨粒切下之后的磨屑厚度则会相应减小,这样就会使得每颗磨粒被切削后厚度也会变薄。
加之在超高速磨削过程中,磨速极高,每颗磨粒形成时间十分短,在上述情况下,每颗磨粒承受的磨削力则会大大减小,使得总磨削力大大降低。
这样,短暂的时间内所形成的高应变率往往与普通磨削之间有着天壤之别,主要表现在磨削工件表面时,弹性变形层会逐渐变浅,而磨削沟痕的两侧因为塑性流动而产生的隆起高度会降低。
当然,由于上述机理作用,也会使得磨屑形成中的滑擦距离变小,工件表面层的残余及硬化应力倾向也会逐渐减小。
1.3超高速磨削技术优势就目前我国使用超高速磨削技术相关经验效率来看,其主要有以下几个方面的优势:1.3.1磨削效率得到了大大的提升。
1.3.2磨削力得到了明显的降低,同时零件加工的精度也得到了一定的提高。
1.3.3砂轮的耐用度得到了提高,从而延长了机械的使用寿命。
有关超高速磨削技术在机械制造领域中的应用分析
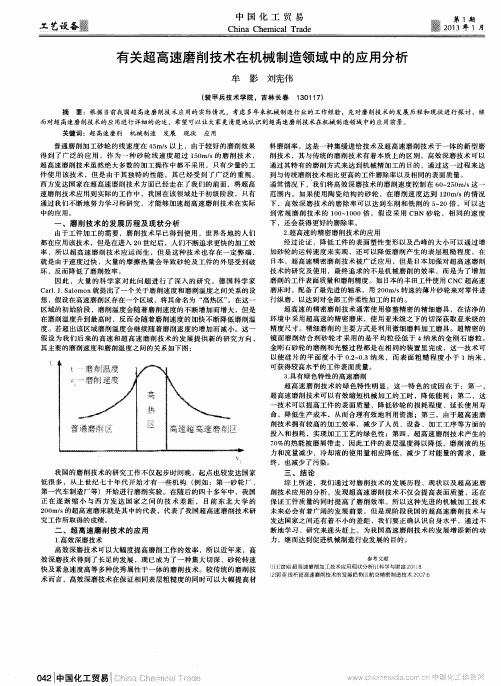
料 磨削率 。这 是一种 集缓 进 给技 术及 超高 速磨 削技 术于 一体 的新 型磨 削 技术 ,其 与传统 的磨 削技 术有 着本 质上 的 区别 。高效 深磨 技术 可 以 通 过其特 有 的磨 削方式 来达 到机 械精 加工 的 目的 ,通过 这一 过程 来达
到 与传统 磨削技 术相 比更高 的工件磨 除率 以及 相 同的表面质 量 。 通 常情 况下 ,我们将 高效 深磨 技术 的磨 削速度 控制 在 6 0 ~ 2 5 0 m/ s 这 一
壬艺设备
中国 化 工 贸易
Ch i n a Ch e mi c a l Tr a d e
第 1期
2 0 1 3年 1月
有关超高速磨削技术在机械制造领域 中的应用分析
牟 影 刘宪伟
1 3 01 1 7 ) ( 装 甲兵技 术学 院 ,吉 林长春
摘 要 :根据 当前我 国超 高速磨 削技术应 用的实际情 况,考虑 多年来机械 制造行 业的工作经验 ,先对磨削技术的发展 历程和现状进行探讨 ,继 而对超 高速磨 削技术的应用进行 详细的论述 ,希望可以让大家更清楚地认识到超 高速磨削技 术在机械制造领域 中的应用前景。
簪
‘
的工 件表面 质量 。 3 . 具有绿 色特性 的高速 磨削 超高 速磨 削技 术 的绿 色特 性 明显 ,这 一 特 色 的成 因 在于 :第 一 , 超 高速磨 削技术 可 以有效 缩短 机械 / J U T . 的 工时 ,降低 能 耗 ;第二 ,这 技 术可 以提 高工件 的表 面质 量 ,降低 砂轮 的 损耗程 度 、延 长使 用寿 命 ,降低 生产 成本 ,从而 合理 有效 地 利用 资源 ;第 三 ,由于 超高 速磨
、
超高速加工技术
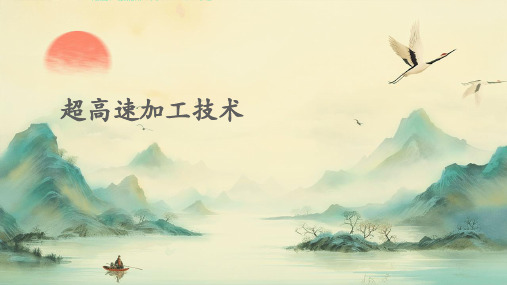
应用案例二:汽车发动机缸体加工
总结词
提高缸体质量和加工效率
详细描述
在汽车发动机缸体加工中,超高速加工技术能够提高缸体的加工效率和精度,同时降低废品率。通过高速旋转的 刀具和高效的切削液系统,可以快速去除材料,减少切削力和热量的产生,提高缸体的表面质量和耐久性。
应用案例三:模具钢材料加工
总结词
提高模具寿命和加工效率
发展趋势
随着新材料、新工艺的不 断涌现,超高速加工技术 正朝着智能化、绿色化、 复合化等方向发展。
主题重要性
促进制造业转型升级
满足市场需求
超高速加工技术的应用有助于提高生 产效率、降低成本,推动制造业向智 能化、柔性化、绿色化方向转型升级。
随着市场对产品品质和性能要求的不 断提高,超高速加工技术的应用能够 满足消费者对高品质产品的需求。
超高速加工技术能够大幅提高航空航天材料的加工效率,缩 短生产周期,降低制造成本,同时保证零部件的加工精度和 质量。
汽车制造
汽车制造领域需要大量高精度零部件 ,超高速加工技术能够快速、准确地 加工出汽车发动机缸体、缸盖、变速 器壳体等复杂零部件。
超高速加工技术能够提高汽车零部件 的加工效率,降低生产成本,同时提 高零部件的耐磨性、耐腐蚀性和疲劳 强度等性能。
数字化
超高速加工技术将向数字化方向发展, 实现数字化的加工模型和加工过程的 仿真与优化。
05
超高速加工技术的实际案例
应用案例一:航空叶片加工
总结词
提高加工效率,降低生产成本
详细描述
超高速加工技术应用于航空叶片加工,能够显著提高加工效率,缩短生产周期, 降低生产成本。通过高转速的刀具和精确的数控系统,可以快速、准确地完成 叶片的切削和磨削,提高表面质量和精度。
高速磨削

高速磨削高速磨削是国内外正在大力研究并逐步推广的一种先进的机械加工方法 , 它是近代磨削加工技术发展的一种新工艺 , 与普通磨削相比 , 其优点是能够大大提高被加工工件的精度 , 降低零件表面粗糙度。
随着科学技术的不断进步和发展 , 对零件的加工精度和生产率提出了更高的要求 , 高速磨削技术更加显示出它的重要性。
1 国外高速磨削技术的现状与发展趋势早在上世纪 50年代 , 国外就已经开始研究高速磨削 , 到 60年代 , 许多国家在高速磨削方面的研究更加得到普遍重视 , 并取得了许多成功经验 , 如日本京都大学工学部冈村健二郎教授首先提出了高效磨削理论 , 当时在日本也是盛行一时。
德国阿亨大学Optiz教授系统地发表了 60m /s高速磨削的实验结果。
在 70年代 , 高速磨削在许多工业国家迅速发展 , 60m /s以上高速磨床品种超过 50种 , 少数磨床磨削速度达到 125m /s, 到了 80年代 , 许多国家继续在提高磨削速度上进行努力 , 但是高速磨削并未按原先预料的情况发展 , 它受到许多条件的制约 , 如受到机床结构、动态特性、砂轮速度及磨料耐磨性等的限制 , 实际上在这个时期磨削速度的提高也受到了一定的限制。
近年来 , 高速磨削加工技术又有了很大发展 , 主要表现在以下几个方面 :(1)高速磨削机理方面。
在越过能产生磨削热损伤的国限带之后 , 磨削用量进一步加大不仅不会使热损伤加剧 , 反而会使其不再发生。
这一发现 , 开拓出一个广阔的高速磨削参数领域 , 为实现超高速的磨削提供了理论基础 , 加上人造金刚石和立方氮化硼在砂轮制造中的大量应用 , 高速磨削得以再度兴起 , 并实现了线速度高于普通磨削 5 - 6倍甚至更高的超高速磨削。
(2)高速磨削的有利环节。
继喷雾润滑轴承和空气润滑轴承之后 , 利用磁力承受负荷的磁悬浮轴承已进入实用阶段 , 它的转速可以在主轴强度所能承受的限度内任意提高。
超高速磨削技术在机械制造中的应用分析
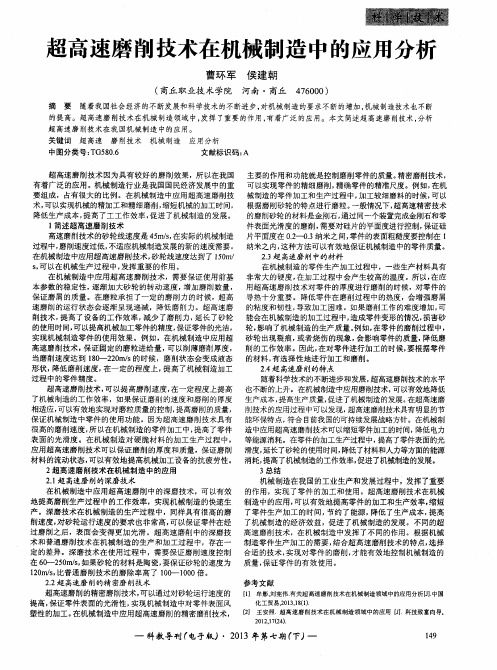
定 的差 异 。深 磨技 术在 使 用 过 程 中 ,需 要 保 证 磨 削速 度 控 制 在6 0 -2 5 0 m / s , 如果砂轮的材料是陶瓷, 要保证砂轮的速度为 1 2 0 m/ s , 比普 通磨 削技术 的磨除率高 了 1 o 0 —1 o O 0倍 。 2 . 2 超 高速磨削的精 密磨 削技术 参考文献
主要的作用和功能就是控制磨削零件的质量 。 精密磨削技术, 可 以实现零件的精 细磨削 , 精确零件 的精准尺度。例如, 在机 械 制造 的零 件 加工 和 生 产 过程 中 , 加 工较 细 磨 料 的时 候 , 可 以 根据磨削砂轮的特 点进行磨粒。 一般情况下, 超高速精密技术 的磨 削砂 轮 的 材料 是 金刚 石 , 通 过 同一 个装 置完 成金 刚 石和 零 件表面光滑度 的磨削 , 需要对硅片的平面度进行控制, 保证硅 片平面度在 O . 2 一O _ 3 纳米之间, 零件 的表面粗糙度要控制在 1 纳米之 内, 这种方法可 以有效地保证机械制造中的零件质量。 2 产材料具有 非常大的硬度 , 在加工过程 中会产生较高的温度。所 以, 在应 用 超 高速 磨 削技 术 对 零 件 的 厚 度进 行 磨 削 的 时候 ,对 零件 的 导热十分重要 。降低零件在磨削过程 中的热度,会增强磨屑 的粘度和韧性 , 导致加 工困难 。如果磨削工作的难度增加, 可 能会在机械制造的加工过程 中, 造成零件变形 的情况 , 损害砂 轮, 影响了机械制造的生产质量 。 例如, 在零件的磨削过程中, 砂轮 出现裂痕 , 或者烧伤 的现象 , 会影 响零件的质量, 降低磨 削的工作效率。因此 , 在对零件进行加工的时候 , 要根据零件 的材料 , 有选择性地进行加工和磨削 2 . 4超 高速磨 削的特点 随着科学技术的不断进步和发展, 超高速磨削技术的水平 也不断的上升。在机械制造中应用磨削技术, 可以有效地降低 生产成本, 提高生产质量, 促进 了机械制造的发展。 在超高速磨 削技 术 的应 用过 程 中 可 以发现 , 超 高速 磨 削 技术具 有 明显 的节 能环 保特 点 , 符 合 目前 我 国 的可 持续 发展 战 略方针 。在 机械 制 造 中应 用超 高速 磨 削技 术 可 以缩 短零 件加 工 的时 间, 降低 电力 等能源消耗。在零件 的加工生产过程中, 提高 了零件表面的光 滑度, 延长了砂轮的使用时间, 降低 了材料和人力等方面的能源 消耗, 提高了机械制造 的工作效率, 促进了机械制造的发展。 3总结 机械制造在我 国的工业生产和发展过程中,发挥了重要 的作用,实现 了零件 的加工和使用。超高速磨削技术在机械 制造中的应用, 可 以有效地提高零件 的加工和生产效率 , 缩短 了零件 生产加工 的时间, 节约 了能源 , 降低 了生产成本 , 提高 了机械制造 的经济效益,促进 了机械制造的发展。不同的超 高速 磨 削 技 术 ,在机 械制 造 中发 挥 了不 同的作 用 。 根据 机 械 制造 零 件 生 产加 工 的需 要 , 结 合 超 高 速 磨 削技 术 的特 点 , 选 择 合 适 的技 术 , 实 现对 零件 的磨 削 , 才 能有 效 地控 制 机 械制 造 的 质量 , 保 证 零 件 的有 效 使 用 。
高速强力磨削在机械加工中的发展与应用
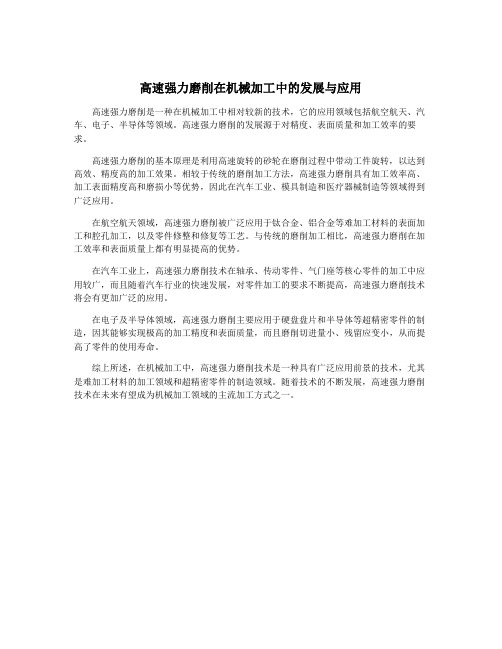
高速强力磨削在机械加工中的发展与应用
高速强力磨削是一种在机械加工中相对较新的技术,它的应用领域包括航空航天、汽车、电子、半导体等领域。
高速强力磨削的发展源于对精度、表面质量和加工效率的要求。
高速强力磨削的基本原理是利用高速旋转的砂轮在磨削过程中带动工件旋转,以达到高效、精度高的加工效果。
相较于传统的磨削加工方法,高速强力磨削具有加工效率高、加工表面精度高和磨损小等优势,因此在汽车工业、模具制造和医疗器械制造等领域得到广泛应用。
在航空航天领域,高速强力磨削被广泛应用于钛合金、铝合金等难加工材料的表面加工和腔孔加工,以及零件修整和修复等工艺。
与传统的磨削加工相比,高速强力磨削在加工效率和表面质量上都有明显提高的优势。
在汽车工业上,高速强力磨削技术在轴承、传动零件、气门座等核心零件的加工中应用较广,而且随着汽车行业的快速发展,对零件加工的要求不断提高,高速强力磨削技术将会有更加广泛的应用。
在电子及半导体领域,高速强力磨削主要应用于硬盘盘片和半导体等超精密零件的制造,因其能够实现极高的加工精度和表面质量,而且磨削切进量小、残留应变小,从而提高了零件的使用寿命。
综上所述,在机械加工中,高速强力磨削技术是一种具有广泛应用前景的技术,尤其是难加工材料的加工领域和超精密零件的制造领域。
随着技术的不断发展,高速强力磨削技术在未来有望成为机械加工领域的主流加工方式之一。
磨削技术的发展及关键技术-文献综述

磨削技术的发展及关键技术摘要:砂带磨削几乎能用于加工所有的工程材料,作为在先进制造技术领域有着"万能磨削"和"冷态磨削"之称的新型工艺,砂带磨削已成为与砂轮磨削同等重要的不可缺少的加工方法。
综观近几年来国内外各类机床及工具展览会和国际生产工程学会的学术会议,结合砂带磨削在国内外各行业的应用状况,可以看出砂带磨削在制造业中发挥着越来越重要的作用,有着广泛的应用及广阔的发展前景。
关键字:磨削砂带机床技术Keyword:Grinding Abrasive belt Machine tool Technology一,前言砂带磨床是一种既古老而又新兴的工艺。
近30多年来,粘满尖锐砂粒的砂布或砂纸制成一种高速的多刀多刃连续切削工具用于砂带磨床之后,砂带磨削技术获得了很大的发展。
这种砂带磨削技术远远超越了原有的只用来加工和抛光的陈旧概念。
现在砂带磨床的加工效率甚至超过了车、铣、刨等常规加工工艺,加工精度已接近或达到同类型机床的水平,机床功率的利用率领先于所有的金属切削机床,应用范围不仅遍及各行各业,而且对几乎所有的材料,无论是金属还是非金属都可以进行加工。
长期以来不大引人注意的砂带磨削工艺现在正进入现代化发展的新阶段。
而数控磨床又是磨床的发展方向,所以研究数控砂带磨床本有很大的意义。
【正文】一.磨削技术的发展及关键技术1.磨削技术发展史高速高效磨削、超高速磨削在欧洲、美国和日本等一些工业发达国家发展很快,如德国的Aachen大学、美国的Connecticut大学等,有的在实验室完成了速度为250m/s、350m/s、400m/s的实验。
据报道,德国Aachen大学正在进行目标为500m/s 的磨削实验研究。
在实用磨削方面,日本已有200m/s的磨床在工业中应用。
我国对高速磨削及磨具的研究已有多年的历史。
如湖南大学在70年代末期便进行了80m/s、120m/s的磨削工艺实验。
超高速磨削技术特点
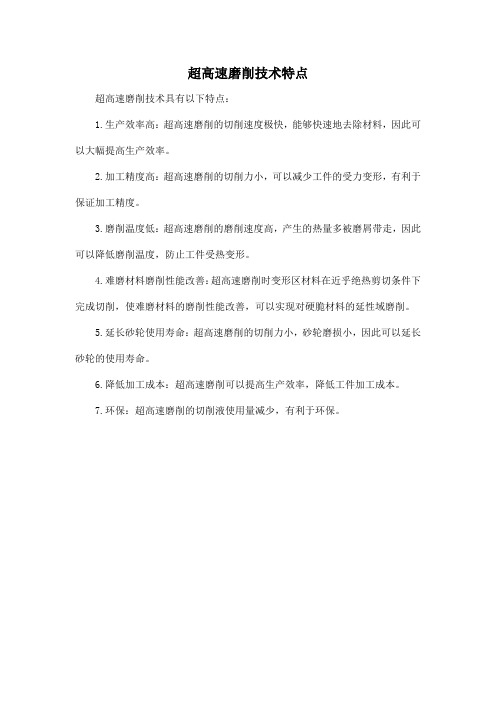
超高速磨削技术特点
超高速磨削技术具有以下特点:
1.生产效率高:超高速磨削的切削速度极快,能够快速地去除材料,因此可以大幅提高生产效率。
2.加工精度高:超高速磨削的切削力小,可以减少工件的受力变形,有利于保证加工精度。
3.磨削温度低:超高速磨削的磨削速度高,产生的热量多被磨屑带走,因此可以降低磨削温度,防止工件受热变形。
4.难磨材料磨削性能改善:超高速磨削时变形区材料在近乎绝热剪切条件下完成切削,使难磨材料的磨削性能改善,可以实现对硬脆材料的延性域磨削。
5.延长砂轮使用寿命:超高速磨削的切削力小,砂轮磨损小,因此可以延长砂轮的使用寿命。
6.降低加工成本:超高速磨削可以提高生产效率,降低工件加工成本。
7.环保:超高速磨削的切削液使用量减少,有利于环保。
- 1、下载文档前请自行甄别文档内容的完整性,平台不提供额外的编辑、内容补充、找答案等附加服务。
- 2、"仅部分预览"的文档,不可在线预览部分如存在完整性等问题,可反馈申请退款(可完整预览的文档不适用该条件!)。
- 3、如文档侵犯您的权益,请联系客服反馈,我们会尽快为您处理(人工客服工作时间:9:00-18:30)。
超高速磨削技术在机械制造领域的发展与应用一、概述通常将砂轮线速度大于45 m/s的磨削称为高速磨削,而将砂轮线速度大于150 m/s的磨削称为超高速磨削。
高速超高速磨削技术是磨削工艺本身的革命性跃变,是适应现代高科技需要而发展起来的一项新兴综合技术,它集现代机械、电子、光学、计算机、液压、计量及材料等先进技术成就于一体。
高速超高速磨削在德国、日本和美国等发达国家发展比较快。
德国著名磨削专家Taw akoli T 博士将其誉为“现代磨削技术的最高峰”。
日本先端技术研究学会把超高速加工列为五大现代制造技术之一。
国际生产工程学会(CIRP)将超高速磨削技术确定为21世纪的中心研究方向之一,并进行合作研究。
1.高速磨削技术的发展高速加工和超高速加工的概念是由德国切削物理学家Salomon C博士1931年首先提出,他发表了著名的Salomon曲线,创造性地预言了超越Talor切削方程式的非切削工作区域的存在,提出如能够大幅度提高切削速度,就可以越过切削过程产生的高温死谷而使刀具在超高速区进行高速切削,从而大幅度减少切削工时,成倍地提高机床生产率。
他的理论成为后来的高速超高速磨削的理论依据。
磨削加工是一种古老而自然的制造技术,应用范围遍布世界各地,然而数千年来磨削速度一直处于低速水平。
20 世纪后,为了获得高加工效率,世界发达国家开始尝试高速磨削技术。
但人们很快就发现,当磨削速度提高到一定程度时,磨削温度会急剧上升,从而导致砂轮失效和工件表面磨削烧伤,这使磨削速度的提高受到很大限制。
1929 年德国切削专家Carl.J.Salomon 博士提出了关于切削速度与切削温度之间关系的假设,他断言在高速切削区,存在一个“热沟”,在“热沟”区,切削温度随切削速度的提高而急剧上升,直到切削温度达到最高点,之后温度随速度的提高而下降。
当切削速度越过“热沟”后,继续提高切削速度将会使切削温度明显下降。
Salomon 博士关于“热沟”的假设被后来的实验和科学研究所证实。
这一创造性的科学论断为磨削加工朝高速和超高速磨削加工发展指明了方向,为超高速磨削技术研究开辟了广阔空间。
2.国内外研究现状(1)国外超高速磨削加工技术进展高速超高速磨削加工技术在美国和欧洲这样的发达国家和地区发展相当迅速。
超高速磨削加工技术的初步探索是始于上世纪60年代,即便是在那个时候研究中的磨削速度就已经达到了210-230m/s。
欧洲在高速超高速磨削的研究方面始终处于领先地位。
德国Aachen大学、Bremen大学在高效率深切削的高速磨削研究方面取得了高水平成果,研究人员采用高速度、快进给、深切入进行超高速磨削实验,可得到高质量的磨削效果。
柏林技术大学机床加工工艺研究所和霍伦霍夫研究院生产设备和设计技术研究所开展了创新型磨削工艺,开发出了高速双面磨削工艺。
德国Aachen 工业大学在超高速磨削研究中采用圆周速度500m/s 的超高速砂轮进行了实验。
美国马萨诸塞州立大学的S.Malkin等在研究超高速磨削实验时采用了149m/s 的砂轮速度和电镀金刚石砂轮硅研究分析了超高速磨削砂轮的地貌和磨削机理。
美国的Edgetek Machine 公司采用单层CBN 砂轮推出圆周速度可达203m/s的超高速磨床。
日本高速超高速磨削技术近十年来发展迅速,2000年,日本进行了500m/s的超高速磨削实验,其目的主要研究磨削过程的综合性能以及超高速磨削机理的分析,其在超高速磨削领域已经处于国际领先地位。
欧洲超高速磨削技术的发展起步较早,最初超高速磨削的基础研究是在20 世纪60年代末期,实验室磨削速度已达210~230m/s。
20世纪70年代末期,超高速磨削采用CBN砂轮,意大利的法米尔(Famir)公司在1973年9月西德汉诺威国际机床展览会上,展出了砂轮圆周速度120m/s 的磨轴承内环外沟槽的高速磨床。
1980年德国Bremen大学的Werner教授开创了高效深磨的概念,是Bremen 大学出资由德国Guhring Automation公司于1983年制造了世界上第一台高效深磨的磨床,功率60kW,转速10kr/min,砂轮直径400mm,砂轮线速度209m/s。
Bremen大学较早地开展了高效深磨技术研究,该方法是用高线速度、深切入、快进给进行磨削,可得到高效率、高质量的磨削效果。
瑞士Studer公司也曾用改装的S45型外圆磨床进行280m/s的磨削试验。
1989年,德国纳霍斯公司推出了80 m/s的CN磨床。
居林自动化公司于1992年制造成功140~160 m/s的CBN 磨床。
到1990年,英国W.B.Rowe等人进行了200 m/s的超高速磨削试验研究。
20世纪90 年代初,已经实现了最高砂轮线速度350m/s的磨削实验。
到目前为止,德国阿亨工科大学正在进行砂轮线速度为500 m/s的超高速磨削试验研究。
目前,实际应用的砂轮线速度在200~250m/s之间。
美国20世纪60年代中期开始提高陶瓷砂轮的线速度。
辛辛那提-米拉克隆公司到1969年已生产了100多台高速磨床,其中有80 m/s的无心磨床。
本迪克斯公司1970年生产了91 m/s的切入式高速磨床。
1971年,美国Carnegie-Mellon 大学制造了一种无中心孔的钢质轮,在其周边上镶有砂瓦,其试验速度可达185m/s,工作速度达到125 m/s,用于磨削不锈钢锭和切断,也可用于外圆磨削。
1993年,美国的Edgetek Machine公司首次推出的超高速磨床,采用单层CBN砂轮,圆周速度达到203 m/s,用以加工淬硬锯齿等可以达到很高的金属切除率。
美国Connecticut大学磨削研究与发展中心的无心外圆磨床,最高磨削速度可达250 m/s。
2000年美国马萨诸塞州立大学的Malkin S等人,以149 m/s砂轮速度,使用电镀金刚石砂轮通过磨削氮化硅研究砂轮的地貌和磨削机理。
日本在20世纪70年代中期,不少工厂生产磨削速度为45 m/s和60 m/s的磨床,三井精机于1972年生产了磨削速度为80 m/s的高速磨床,切入成型磨铸铁工件,加工时间仅为59 s。
1985年前后,在凸轮和曲轴磨床上,磨削速度达到了80 m/s。
1990年10月底在第五届“日本国际机床展览会”上,日本推出了磨削速度为120m/s的高速磨床。
之后,开始开发160 m/s以上的超高速磨床。
1993年前后,使用单颗粒金刚石进行了250 m/s超高速磨削试验研究。
1996年日本又推出了125 m/s CBN砂轮平面磨床。
至2000年,日本已进行500 m/s超高速磨削试验。
Shinizu等人为了获得超高磨削速度,利用改制的磨床,将两根主轴并列在一起;一根作为砂轮轴,另一根作为工件主轴,并使其在磨削点切向速度相反,取得了相对磨削速度为VS+VW的结果,砂轮和工件间的磨削线速度实际接近1000 m/s。
(2)国内超高速磨削技术研究现状相对于欧美日等发达国家的超高速磨削加工技术发展状况而言,我国高速超高速磨削加工发展滞后了。
国内从50年代开始研究,其最高速度达到50m/s,到70年代提高到125m/s,90年代研究速度又提高到200m/s,如今部分高校研究机构已经在实验室将速度提高到250m/s。
东北大学超高速磨削方面的研究成绩突出,研制了我国第一台超高速实验磨床,其圆周速度200m/s,最高砂轮线速度达250m/s。
国内高校以及研究机构对超高速磨削加工技术的各个方面开展了研究,包括传热机理、高速深磨加工技术、单颗粒CBN高速磨削力、电镀CBN 超高速砂轮设计、超高速磨削摩擦磨损、超高速磨削砂轮表面气流场的、超高速磨削机理、点磨研究和高速磨料流磨削等多个方面,湖南大学、哈尔滨工业大学、天津大学、东北大学、清华大学等高校在超高速磨削方面都取得了大量的研究成果,其中部分研究成果已经达到国际先进水平。
二、超高速磨削的原理与特点1.超高速磨削技术的工作原理超高速磨削技术的基本前提是参数保持固定值,砂轮在运行过程中其速率会不断加快,从而使磨削粒的数量持续累积,利用磨削粒来实现磨削厚度的控制,除此之外超高速磨削技术还能够打薄磨屑的厚度,降低单个磨粒的磨削力,在运行当中使整体的磨削力变低"超高速磨削技术的本质是高速度、高水平,相比一般的高速磨削,其产生单个磨屑的时间明显较少,技术人员应该明了解磨屑的形成时间不同其高应变率也会出现差异,主要体现在:塑性流动环境中磨削沟痕的凸起高度降低,加工工件的表面的变形轻微,工件表面的硬化程度以及剩余应力均下降,磨屑产生时耕犁以及滑擦的间隔变小。
根据以上性质可以得出结论:超高速磨削技术使磨粒运行速率变高!应变率滞后于温度,同时进给效率上升,能够实现跨域的易烧板块,拓宽了磨削技术的参数变化范畴。
在高速超高速磨削加工过程中,在保持其它参数不变的条件下,随着砂轮速度的大幅度提高,单位时间内磨削区的磨粒数增加,每个磨粒切下的磨屑厚度变小,则高速超高速磨削时每颗磨粒切削厚度变薄。
这导致每个磨粒承受的磨削力大大变小,总磨削力也大大降低。
超高速磨削时,由于磨削速度很高,单个磨屑的形成时间极短。
在极短的时间内完成的磨屑的高应变率(可近似认为等于磨削速度)形成过程与普通磨削有很大的差别,表现为工件表面的弹性变形层变浅,磨削沟痕两侧因塑性流动而形成的隆起高度变小,磨屑形成过程中的耕犁和滑擦距离变小,工件表面层硬化及残余应力倾向减小。
此外,超高速磨削时磨粒在磨削区上的移动速度和工件的进给速度均大大加快,加上应变率响应的温度滞后的影响,会使工件表面磨削温度有所降低,因而能越过容易发生磨削烧伤的区域,而极大扩展了磨削工艺参数的应用范围。
2.超高速磨削技术的优越性超高速磨削适合加工超硬材料,同时超高速磨削对高塑性难加工金属材料也有一定的磨削效果。
与普通磨削相比,超高速磨削具有如下优越性:磨削力和工件受力变形小、高材料去除率、工件表面粗糙度降低、加工精度和加工质量好、高加工效率。
(1)大幅度提高磨削加工效率,减少磨床设备使用的台数磨削技术的发展史与磨削速度的提高紧密相连。
磨削效率始终是磨削技术发展的重要里程碑。
经过半个多世纪的发展,磨削速度提高了10多倍,比磨削去除率增加近百倍。
(2)提高加工精度并降低磨削力磨削力是反映磨削过程的重要物理量之一,超高速磨削时可以降低磨削力。
当进给量不变时,超高速磨削其磨屑厚度变薄,加工精度得到提高。
由于砂轮线速度增大,单位时间内参加磨削的磨粒数大大增加,单颗磨粒的切削厚度变薄,降低了每颗磨粒的磨削力,从而导致磨削力减小。
而当磨削速度进一步提高时,超高速磨削冲击成屑,砂轮和工件面的摩擦区由固态向液态转变,从而超高速磨削磨削力得到急剧下降。