过程检验规程(精编文档).doc
过程检验规程
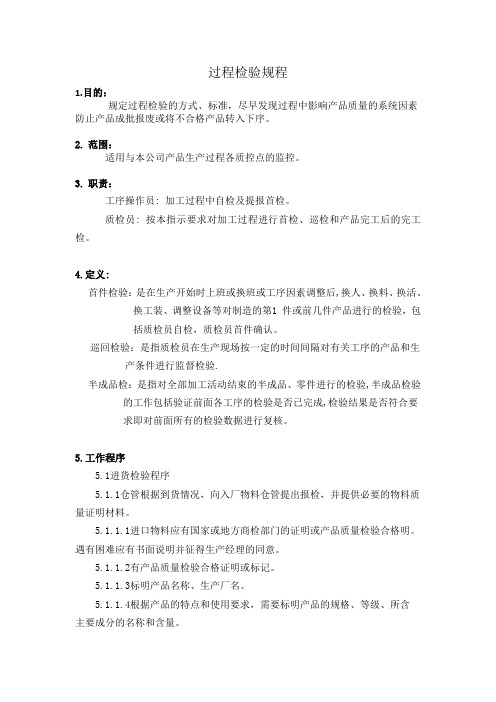
过程检验规程1.目的:规定过程检验的方式、标准,尽早发现过程中影响产品质量的系统因素防止产品成批报废或将不合格产品转入下序。
2.范围:适用与本公司产品生产过程各质控点的监控。
3.职责:工序操作员: 加工过程中自检及提报首检。
质检员: 按本指示要求对加工过程进行首检、巡检和产品完工后的完工检。
4.定义:首件检验:是在生产开始时上班或换班或工序因素调整后,换人、换料、换活、换工装、调整设备等对制造的第1 件或前几件产品进行的检验,包括质检员自检,质检员首件确认。
巡回检验:是指质检员在生产现场按一定的时间间隔对有关工序的产品和生产条件进行监督检验.半成品检:是指对全部加工活动结束的半成品、零件进行的检验,半成品检验的工作包括验证前面各工序的检验是否已完成,检验结果是否符合要求即对前面所有的检验数据进行复核。
5.工作程序5.1进货检验程序5.1.1仓管根据到货情况,向入厂物料仓管提出报检,并提供必要的物料质量证明材料。
5.1.1.1进口物料应有国家或地方商检部门的证明或产品质量检验合格明。
遇有困难应有书面说明并征得生产经理的同意。
5.1.1.2有产品质量检验合格证明或标记。
5.1.1.3标明产品名称、生产厂名。
5.1.1.4根据产品的特点和使用要求,需要标明产品的规格、等级、所含主要成分的名称和含量。
5.1.1.5对于限期使用的产品,需标明生产日期和安全使用期。
5.1.1.6对于使用不当容易造成产品本身损坏或者可能危及人身的产品,要有警示标志或中文警示说明。
裸装物品应每批标明产品标识。
5.1.2入厂物料仓管依据检验规范,及时对进厂物料进行检验。
5.1.3入厂物料仓管对检验后的合格品与不合格品分别作出标记:合格标记为蓝色印章或标签,不合格标记标签,对一些量大且难以作标记的特殊物料可按区域分开并做好标记和记录。
5.1.4入厂物料仓管核实安全认证及是否符合清单要求,若不符合清单要求,无论关键件性能是否检验合格均不得使用。
过程质量检验操作规程

过程质量检验操作规程过程质量检验操作规程一、目的与范围1. 目的:为了保障产品质量,对过程质量进行检验,减少质量问题的发生。
2. 范围:适用于所涉及的过程质量检验。
二、术语与缩写1. 过程质量检验:对生产过程中的质量进行检验,确保产品质量符合要求。
2. 质量问题:产生在生产过程中的不合格品或质量不符合要求的问题。
三、检验内容1. 质量计划:确保生产过程中质量计划的正确执行。
2. 设备检验:对涉及生产过程中使用的设备进行检验,确保设备的正常运行。
3. 物料检验:对生产过程中使用的物料进行检验,确保物料符合质量要求。
4. 工艺检验:对生产过程中的工艺进行检验,确保工艺操作符合要求。
5. 产品检验:对产出的产品进行检验,确保产品质量符合要求。
四、检验标准1. 质量计划:根据质量计划中的要求进行检验。
2. 设备检验:按照设备操作手册中的要求进行检验。
3. 物料检验:按照物料质量要求进行检验。
4. 工艺检验:按照工艺规程进行检验。
5. 产品检验:按照产品质量要求进行检验。
五、检验方法1. 质量计划:对质量计划的执行情况进行检查和复核。
2. 设备检验:通过设备操作手册中的操作步骤进行检验。
3. 物料检验:按照物料质量要求进行检验。
4. 工艺检验:按照工艺规程进行检验。
5. 产品检验:按照产品质量要求进行检验。
六、检验记录与报告1. 检验记录:对检验过程中的关键环节进行记录,包括检验时间、检验人员、检验结果等。
2. 检验报告:对检验结果进行汇总总结,包括合格品数量、不合格品数量、不符合要求的情况等。
七、检验程序1. 质量计划:质量计划由质量部门制定并下发给相应的执行人员。
2. 设备检验:根据设备操作手册执行设备检验。
3. 物料检验:收到物料后,按照质量要求进行检验。
4. 工艺检验:在生产过程中,根据工艺规程进行检验。
5. 产品检验:产出产品后,按照质量要求进行检验。
6. 检验记录与报告:对检验过程和结果进行记录与报告。
过程检验规程

过程检验规程1目的和适用范围1.1为确保各类产品加工过程的检验和试验符合产品标准的要求,明确规则过程检验和试验的项目.程序和方法,特制定本标准。
1.2本标准适用于本厂生产制造过程的各类毛坯.零部件的检验过程。
2引用标准GB/T1348-1988球墨铸铁件GB/T9437-1988耐热铸铁件GB/T9439-1988灰铸铁件JB/T5000.4-1998重型机械通用技术条件铸铁件JB/T5000.6-1998重型机械通用技术条件铸钢件JB/T5000.7-1998重型机械通用技术条件铸钢件补焊JB/T5000.9-1998重型机械通用技术条件切削加工件JB/T5000.10-1998重型机械通用技术条件装配JB/T6397-1992大型碳素结构钢铸件JB/T6404-1992大型高锰钢铸件3检验依据和总要求3.1在与顾客签订销售合同时,合同及技术协议中的各项技术要求均应成为过程检验和试验的依据。
3.2按合同规则的图样.技术标准应是过程检验和试验的依据。
3.3本标准第2章引用的各项标准均应成为过程检验和试验的依据。
3.4各类热加工毛坯.零部件.机械加工件.装配过程的检验和试验应按工艺流程和本标准规则的程序进行。
3.5检验人员应掌握各类过程产品的检测方法,按本标准的规则,对各项检验内容进行检验,并实施质量记录。
3.6各项检验所使用的量具.仪器.仪表等,必须经过计量部门校准合格后方可使用,并应根据规则定期检定。
4铸铁件的检验程序和要求4.1灰口铸铁件的检验我厂灰口铸铁件种类主要为HT200,HT300,HT350几种,检查员首先要对木模进行检验检验合格后才能造型,铸铁件检验有以下项目。
4.1.1铸件形状和尺寸检测:铸件在铸造过程及随后的冷却.落砂.清理.热处理和放置过程中会发生变形,使其实际尺寸与铸件图规则的基本尺寸不符。
为此,国家标准规则《铸件尺寸公差与机械加工余量》GB/T6414-1999,以此为依据来检验铸件的尺寸。
过程检验规程

1 目的和适用范围验证半成品入库验收得到满足,保证未经测量的或不合格的产品不入库。
本规程适用半成品入库验收和在制半成品的检验。
2 检验依据1)可依据的国家或行业标准有:GB 2314-2008 电力金具通用技术条件GB/T 2317.1~3-2008 电力金具试验方法DL/T 768.1~7-2002 电力金具制造质量2)相应的技术图样、工艺文件。
3 职责3.1生产部各事业部负责所有在制品加工质量控制。
3.2质管部质检科负责在制品首检、巡检和完工检中的外观、尺寸检验。
3.3 质管部实验室负责对在制品、半成品入库等进行化学性能、机械性能及电气性能的试验。
4 管理要求4.1过程检验产品验收本公司主要生产分类为:铜铝类、铜类、铝类、铸造类、冲(锻)压类。
4.1.1操作员将<首检/自检记录表>交由过程检验员对再制品的外观、尺寸质量等进行检验,检验后,填写<首检检验台帐>。
4.1.2在制产品应严格按照工艺流程生产每道工序都应该有相关责任人的签名,否则检验员有权利连同产品退回上工序完成相关程序后进行。
4.1.3 生产批量足够时,由检验员人员执行巡检,将巡检的实际情况记录在巡检记录表上。
巡检过程中,当工艺要求时(如,铜铝焊接(摩擦焊、闪光焊、钎焊)产品,材料退火或回火后的硬度、导电率等),应按7.3随机取样进行试验。
4.1.4半成品转序或入库时,过程检验员必须执行完工检验,并在<生产流程卡>检验栏中签字和填写完工检验记录。
必要时,按7.1的取样数量取样填写<送检单>交实验室进行相关试验,实验室接到<送检单>后,务必在15~30分钟完成试验。
(铸造铝合金产品必须通过热处理后方能送检)无检验员签字代表此产品未经过检验不得转序或入库。
4.1.5 检验判定后的半成品,按最终判定结果在容易识别的端部(或其它不易被磨损处)贴3-5枚标识,如合格、让步、返工、不合格等。
过程质量检验操作规程完整

a) 质量部巡检员需按照产品生产工序、图纸得相关要求对每个正在作业得工位进行巡检,每班3次。
过程检验需关注得内容主要包括:产品参数、工艺参数、操作规范性等方面。
b) 对特定岗位(关键工序或需重点控制岗位),质量部巡检员需对经该岗位加工后得半成品进行抽验。
抽检对象为即将转移到下道工序得半成品,抽检水平为特殊抽样水平S-4,每班3次。
c)如巡检结果符合图纸及作业得要求,则生产线可继续生产。
若过程检验结果不符合图纸及作业得要求则按照4、2、2执行。
d) 质量部巡检员需将当日巡检发现得不符合项作整理并汇总,第二日将质量巡检记录提交给对口得质量负责人,质量负责人将当日巡检过程得不符合项整理归类,形成日报发给各部门相关负责人,并组织讨论与建立纠正预防措施及跟踪其实施得有效性。
e) 质量记录:质量部巡检员需将每次巡检结果如实记录在相应得巡检记录表格中(附件二);过程检验中发现得不符合项汇总记录到《过程质量控制巡检、抽验异常反馈表》(附件三)。
4、2 不合格处置4、2、1 首件检验不合格处置a) 若首件检验不合格,不得进行批量生产,立即通知生产工艺或相关人员进行现场分析评审。
b) 相关评审人员需作出评审结论,对该批产品立即整改或换规格生产、放指标生产,并签字确认。
c) 生产线人员与质量部巡检员需对纠正措施进行复检,并重新制作首件直至合格后方可进行批量生产。
4、2、2 过程检验不合格处置a) 过程检验中发现不符合时,质量部巡检员需及时向班长或相关人员反馈,要求操作工现场纠正,并对纠正后得结果进行跟踪。
b) 过程抽验中发现轻微缺陷时,质量部巡检员在做好记录后,需通知生产班长或作业员立即修复。
c) 过程抽验中严重或致命缺陷时,质量部巡检员在做好记录后,还立即通知相关人员,现场评审,或组织将已生产得产品进行全数返工检验,及时遏制不良品流入下道工序,并对改善措施进行持续跟踪。
4、3 质量记录保存保存期限一年。
5 附件5、1抽样检查表5、2记录表单表单号表单名称见附件DMKZL2017002-01 首件检验记录表附件一DMKZL2017002-02 巡检记录表附件二DMKZL2017002-03 巡检异常反馈表附件三DMKZL2017002-04 焊接组对首件检查记录表附件四。
过程检验规程
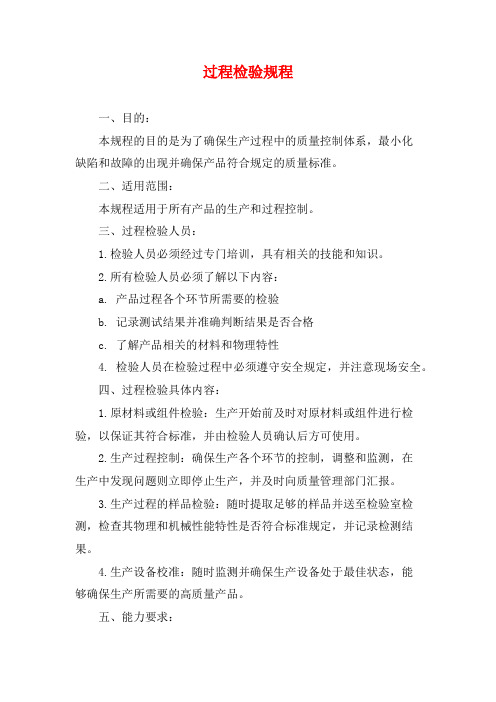
过程检验规程一、目的:本规程的目的是为了确保生产过程中的质量控制体系,最小化缺陷和故障的出现并确保产品符合规定的质量标准。
二、适用范围:本规程适用于所有产品的生产和过程控制。
三、过程检验人员:1.检验人员必须经过专门培训,具有相关的技能和知识。
2.所有检验人员必须了解以下内容:a. 产品过程各个环节所需要的检验b. 记录测试结果并准确判断结果是否合格c. 了解产品相关的材料和物理特性4. 检验人员在检验过程中必须遵守安全规定,并注意现场安全。
四、过程检验具体内容:1.原材料或组件检验:生产开始前及时对原材料或组件进行检验,以保证其符合标准,并由检验人员确认后方可使用。
2.生产过程控制:确保生产各个环节的控制,调整和监测,在生产中发现问题则立即停止生产,并及时向质量管理部门汇报。
3.生产过程的样品检验:随时提取足够的样品并送至检验室检测,检查其物理和机械性能特性是否符合标准规定,并记录检测结果。
4.生产设备校准:随时监测并确保生产设备处于最佳状态,能够确保生产所需要的高质量产品。
五、能力要求:1.检验人员必须对测试设备进行日常维护,以确保它们的准确性。
2.检验人员必须按时,按规定检查样品。
3.检验人员必须具备明确并准确地记录检测事件,包括所采取的行动和结果,以便数据能够用于持续改进工作。
4.检验人员必须了解管理系统的各种手册,并能够熟练操作。
5.检验人员必须定期参加培训和熟悉相关职业知识。
六、不符合检验规程的纪律1.如不符合检验规程,则不得继续进行生产过程。
2.如有违规行为的人员,则必须立即通知生产经理或质量管理部门,让其采取适当措施。
七、适用的标准适用于ISO 9001标准八、检验记录检测员必须在检测文档中正确记录检测结果。
九、修订本规程将在生产过程中持续监测,以确保其始终符合生产需求,并进行适当的修订。
十、指示本规程将通过内部通知、通讯和培训落实至所有员工。
十一、一般条款1.本规程应成为生产过程控制规程的一部分,以支持ISO质量体系。
产品过程检验规程
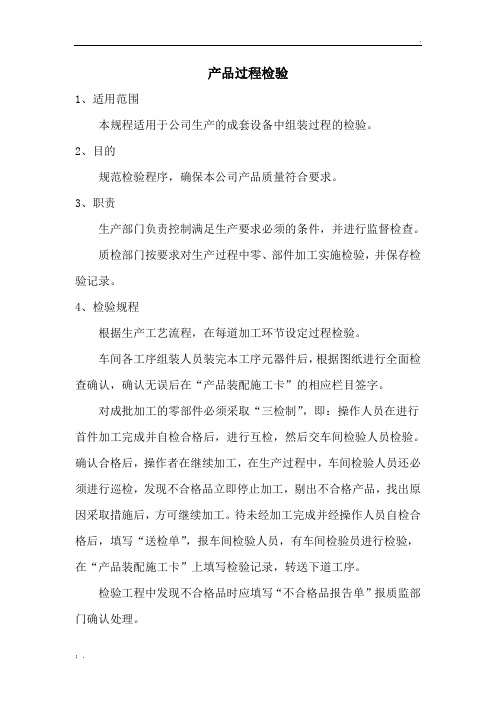
产品过程检验
1、适用范围
本规程适用于公司生产的成套设备中组装过程的检验。
2、目的
规范检验程序,确保本公司产品质量符合要求。
3、职责
生产部门负责控制满足生产要求必须的条件,并进行监督检查。
质检部门按要求对生产过程中零、部件加工实施检验,并保存检验记录。
4、检验规程
根据生产工艺流程,在每道加工环节设定过程检验。
车间各工序组装人员装完本工序元器件后,根据图纸进行全面检查确认,确认无误后在“产品装配施工卡”的相应栏目签字。
对成批加工的零部件必须采取“三检制”,即:操作人员在进行首件加工完成并自检合格后,进行互检,然后交车间检验人员检验。
确认合格后,操作者在继续加工,在生产过程中,车间检验人员还必须进行巡检,发现不合格品立即停止加工,剔出不合格产品,找出原因采取措施后,方可继续加工。
待未经加工完成并经操作人员自检合格后,填写“送检单”,报车间检验人员,有车间检验员进行检验,在“产品装配施工卡”上填写检验记录,转送下道工序。
检验工程中发现不合格品时应填写“不合格品报告单”报质监部门确认处理。
成品总装完成并经装配人员自检合格后,连同“产品装配施工卡”及该产品的其他图样一并送到质监部门,由质检部门进行最终全面检验。
检验人员根据检验结果(除巡检外),对被检产品还应进行“合格”或“不合格”的检验状态标识。
对检验过程中发现不合格产品均须及时作出明显的“不合格”标识,随后对不合格品按《不合格品控制程序》进行处理。
根据型式试验报现场生产产品要满足一致性的要求。
5、验项目、检验要求、检验方法。
过程检验规程

过程检验规程1 目的规范现场作业人员操作流程,确保产品生产过程受控。
2 范围适用于生产现场检验。
3 职责3.1 现场检验员负责检验产品,根据检验标准判定产品是否符合要求;3.2 质量检验部负责不合格品的处理;3.3 生产制造部组织不合格品的评审,生产制造部、质量检验部参加评审。
4 工作程序4.1 首件检验4.1.5 换班、机器调整、停机等作业情况发生变化时,需重新做首检确认。
4.2 巡检a)检验员若发现不合格,应及时通知操作人员立即停止加工,并对已加工的产品进行全检,检验员对加工者全检合格的产品再次进行抽检,抽检合格后,才能流入下道工序。
b)工序生产中出现批量不合格品(10件以上),检验开具《临时停止生产通知单》经主管领导批准后,通知操作工及带班立即停止生产、调整机器,合格后重新执行首检;C)对于上一时段生产的产品进行隔离并做待检标识,开具《不合格品报告单》报告质量部,等待处理;d)按“返工/返修作业指导书”要求通知生产制造部进行全检,检验员对全检合格的产品再次进行抽检,抽检合格才能流入下道工序,检验过程中需做好《返工/返修处理记录》,对发现的不合格品进行隔离和标识,按《不合格品控制程序》规定执行。
4.3 工序例外放行若因生产急需来不及出具检验报告时,由车间填写《紧急/例外放行审批单》,经上级主管领导批准后方可放行,对放行产品需做好“紧急放行”标识,同时在放行后24小时内需完成相应检验,发现不合格立即追回,按《不合格品控制程序》执行。
4.4生产中产生的不合格品入库a)对于料废,做好缺陷标识,在《料废退料单》上盖检验员章。
b)对加工报废产品,做好缺陷标识,在《报废单》上盖检验章。
4.5记录要求5.质量记录《首件送检通知单》《加工工序检验记录》《临时停止生产通知单》《不合格品报告单》《返工/返修处理记录》《紧急/例外放行审批单》《首检检验报告单》《报废单》编制:审核:批准:。
- 1、下载文档前请自行甄别文档内容的完整性,平台不提供额外的编辑、内容补充、找答案等附加服务。
- 2、"仅部分预览"的文档,不可在线预览部分如存在完整性等问题,可反馈申请退款(可完整预览的文档不适用该条件!)。
- 3、如文档侵犯您的权益,请联系客服反馈,我们会尽快为您处理(人工客服工作时间:9:00-18:30)。
【最新整理,下载后即可编辑】
过程检验规程
1.目的:
规定过程检验的方式、标准,确保生产过程中产品质量能够及时控
制,防止不合格产品转入下道工序。
2.范围:
适用于本公司过程加工的产品
3.职责:
工序操作工: 加工过程中自检.
过程检验员: 按本指示要求对加工过程进行首检、巡检和产品完工后的成品检.
4. 定义:
首件检验:是在生产开始时上班或换班或工序因素调整后,换人换料换活换工装调整设备等对制造的第1 件或前几件产品进行的检
验.包括操作工自检,操作工互检和检验员首件确认。
巡回检验:是指检验员在生产现场按一定的时间间隔对有关工序的产品和生产条件进行监督检验.
半成品检:是指对全部加工活动结束的半成品零件进行的检验,半成品检验的工作包括验证前面各工序的检验是否已完成,检验结
果是否符合要求即对前面所有的检验数据进行复核。
5. 运行程序:
5.1操作工首检:
5.1.1首次加工按图纸要求自检合格。
5.1.2向过程检验员报首检结果,提交样件最少2件。
5.1.3首件未经检验合格不得继续加工或作业。
5.3检验员首检:
5.3.1过程检验员对首次加工样件,按《工序检验标准》要求作首件检验。
5.3.2首件判定后,过程检验员应对首件合格件打上确认标识,以便作业参照,并保留到该批产品完工.
5.3.3首检记录:首检过程如实记录于【生产过程首检、巡检质量记录表】中.
5.4操作工自检:
5.1.6首检合格,过程加工可正式量产作业,操作工应在量产中保持一定频次
的自检 (每0.5小时一次自检),以保证质量的稳定。
5.5个别装配难度大的零件或测量难度大的零件,首检按操作工→车间管理人员→检验员,三方确认原则执行
5.6巡检:
5.6.1过程检验员应对量产过程进行巡检作业,检验频次:2小时至少巡检1
趟,每个机位产品最少抽样3-5件,检验标准参见《工序检验标
准》,根据实际情况对关键特性、重要特性、工艺上有特殊要
求对下道工序的加工装配有重大影响的和内外部质量信息反馈
中出现质量问题多的薄弱环节加强巡检频次。
5.6.2巡检中若发现不合格品应在发现当时通知工序操作工停机,复检确认
无误后开具【不合格评审单】按【不合格品控制程序】处理.
如在巡检过程中不良的改善效果不佳时,应适当调整增加巡查
的频次.
5.6.3巡检记录:检验员每2个小时在【生产过程首检、巡检质量记录
表】中如实填写记录,每日上班首检时必须把前一天已填满的
【生产过程首检、巡检质量记录表】收回。
巡检员必须认真收
集、整理并装订成册,妥善保管。
5.6.4巡回检验要抽检产品还需检查影响产品质量的生产因素,从人、
机、料、测几个方面去监督和控制,发现问题时及时指导操作
工或联络有关人员加以纠正,问题严重时要适时开具【不合格
评审单】,按【不合格品控制程序】执行。
5.7工序检验标准:
5.8半成品检:
5.8.1 车间全部加工完工的零件要进行半成品完工检,由物流仓库开具
【报检单】向半成品完工检员进行报检,完工检标准依5.7执行.
5.8.2 半成品检发现的不良应当时反馈到工序责任车间及对应工序巡检
员.
5.8.3 球壳车间所有半成品检工作完成后,如有必要,可对半成品检产品
由挑选工进行全检, 挑出的缺陷件由半成品检验员依【不合格品
控制支持程序】处理.
5.8.4 半成品检记录:半成品检结果记录于【产品检验记录表】中。
6.0半成品检标准:
6.1 过程检验后的状态标识
6.1.1合格品: 检验员签认绿色标签
6.1.2不合格品:检验员签认红色标签
6.1.3待检/返工品:检验员签认黄色标签
7. 记录:
生产过程首检、巡检质量记录单
检验记录表
《合格》标签
《不合格》标签
《返工/待检》标签
编制:审核:批准:日期:。