钒的选矿方法和步骤
一种制备金属钒的方法

一种制备金属钒的方法引言金属钒是一种具有重要工业应用价值的金属材料,广泛应用于冶金、化工、电子等领域。
目前已有多种方法制备金属钒,但由于成本高、工艺复杂等问题限制了其产量和应用范围。
本文将介绍一种简单、高效的制备金属钒的方法,开发出更可行的制备技术,以满足不同领域的需求。
材料与方法1. 原料准备:制备金属钒所需的主要原料为钒矿石,常见的有伴生钒矿、钒铁矿等。
此外,还需要一些辅助材料,如还原剂、助熔剂等。
2. 矿石选别:将采集到的钒矿石经过粉碎、磨矿等处理工艺,得到均匀的颗粒状物料。
通过重力分选、浮选等方法,将矿石中的杂质分离,得到纯净的钒矿石。
3. 还原提钒:将纯净的钒矿石与还原剂按一定比例混合,并加入适量的助熔剂。
将混合物装入高温炉中,采用还原反应提取钒。
温度、时间等参数需要根据具体情况进行优化。
4. 熔炼与精炼:通过还原提钒得到的钒合金需要经过熔炼和精炼工艺,以获得高纯度的金属钒。
采用真空熔炼、电炉熔炼等方法,调整合金成分和含杂质的浓度。
5. 产品成型:经过熔炼和精炼后的钒合金通过铸造、压延等工艺成型,制备出所需的金属钒产品。
结果与讨论采用上述制备方法制得的金属钒具有较高的纯度和良好的机械性能,符合工业应用的要求。
通过对不同矿石的处理和还原提钒工艺参数的优化,可实现钒的高效提取和合金化。
本方法相比传统的制备方法具有明显的优势。
首先,使用的原料广泛且资源丰富,提高了可行性和可持续性。
其次,制备工艺简单、操作方便,降低了制备成本和工艺控制的难度。
此外,还能达到较高的成品强度和韧性,提高了制品的使用寿命和稳定性。
然而,这种制备方法仍然存在一些不足之处。
例如,对原料矿石的加工和纯化过程可能存在能耗较高、流程复杂等问题,需要进一步优化。
同时,提高熔炼和精炼工艺的自动化程度,减少对人力的依赖,也是值得探索的方向。
结论通过本研究,我们成功开发了一种简单、高效的制备金属钒的方法,为工业生产中的钒材料提供了新的解决方案。
从含钒钢渣中富集钒的方法与流程
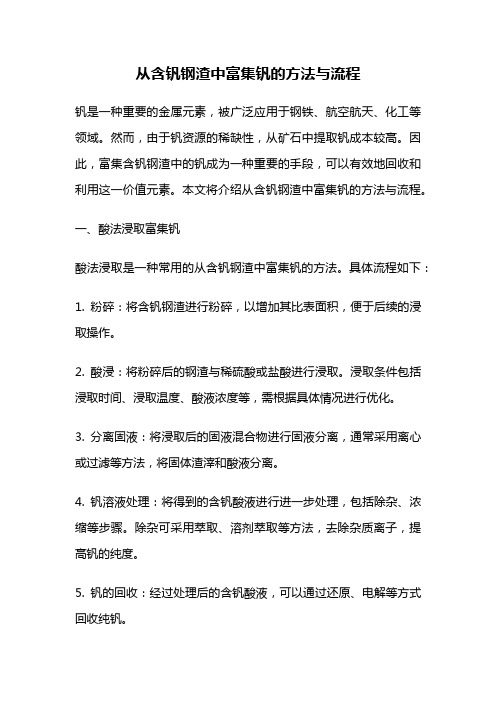
从含钒钢渣中富集钒的方法与流程钒是一种重要的金属元素,被广泛应用于钢铁、航空航天、化工等领域。
然而,由于钒资源的稀缺性,从矿石中提取钒成本较高。
因此,富集含钒钢渣中的钒成为一种重要的手段,可以有效地回收和利用这一价值元素。
本文将介绍从含钒钢渣中富集钒的方法与流程。
一、酸法浸取富集钒酸法浸取是一种常用的从含钒钢渣中富集钒的方法。
具体流程如下:1. 粉碎:将含钒钢渣进行粉碎,以增加其比表面积,便于后续的浸取操作。
2. 酸浸:将粉碎后的钢渣与稀硫酸或盐酸进行浸取。
浸取条件包括浸取时间、浸取温度、酸液浓度等,需根据具体情况进行优化。
3. 分离固液:将浸取后的固液混合物进行固液分离,通常采用离心或过滤等方法,将固体渣滓和酸液分离。
4. 钒溶液处理:将得到的含钒酸液进行进一步处理,包括除杂、浓缩等步骤。
除杂可采用萃取、溶剂萃取等方法,去除杂质离子,提高钒的纯度。
5. 钒的回收:经过处理后的含钒酸液,可以通过还原、电解等方式回收纯钒。
二、矩阵冶金法富集钒矩阵冶金法是另一种常用的从含钒钢渣中富集钒的方法。
具体流程如下:1. 热处理:将含钒钢渣进行热处理,使其中的钒转化为易溶性的钒化合物。
热处理温度和时间需要根据钢渣的组成和性质进行调控。
2. 酸浸:将经过热处理的钢渣与酸性溶液进行浸取。
浸取酸液的浓度和温度需要根据钢渣的特性进行优化。
3. 分离固液:将浸取后的固液混合物进行分离,得到固体渣滓和酸液。
4. 钒溶液处理:对得到的含钒酸液进行杂质去除和钒的富集。
杂质去除可以采用萃取、溶剂萃取等方法。
5. 钒的回收:经过处理后的含钒酸液,可以通过还原、电解等方式回收纯钒。
三、其他方法与流程除了酸法浸取和矩阵冶金法,还有一些其他方法可以用于富集含钒钢渣中的钒,如氧化焙烧法、浸出熔融法等。
这些方法具体流程与条件有所不同,但核心思想都是通过化学反应实现钒的富集与回收。
在实际应用中,根据含钒钢渣的成分和性质选择合适的方法进行钒的富集。
钒的选矿方法和步骤

钒的选矿方法和步骤:钒铁生产的主要原料是钒钛磁铁矿,经选矿富集后,通过高炉炼出含钒生铁,在雾化炉或转炉吹炼过程中提取钒渣。
钒渣经粉碎后配加钠盐(纯碱、食盐或无水芒硝)进行氧化钠化焙烧,使钒成为可溶的偏钒酸钠(NaVO3),浸取净化后加硫酸铵沉淀出多钒酸铵[(NH4)2V6O16],再经脱氨熔化,铸成片状五氧化二钒。
要求成分为V2O597~99%,P<0.05%,S<0.05%,Na2O+K2O <1.5%。
此外也从含钒铁精矿或含钒炭质页岩直接通过化学处理提取五氧化二钒。
电硅热法片状五氧化二钒用75%硅铁和少量铝作还原剂,在碱性电弧炉中,经还原、精炼两个阶段炼得合格产品。
还原期将一炉的全部还原剂与占总量60~70%的片状五氧化二钒装入电炉,在高氧化钙炉渣下,进行硅热还原。
当渣中V2O5小于0.35%时,放出炉渣(称为贫渣,可弃去或作建筑材料用),转入精炼期。
此时,再加入片状五氧化二钒和石灰,以脱除合金液中过剩的硅、铝等,俟合金成分达到要求,即可出渣出铁合金。
精炼后期放出的炉渣称为富渣(含V2O5达8~12%),在下一炉开始加料时,返回利用。
合金液一般铸成圆柱形锭,经冷却、脱模、破碎和清渣后即为成品。
此法一般用于含钒40~60%的钒铁冶炼。
钒的回收率可达98%。
炼制每吨钒铁耗电1600千瓦?时左右。
铝热法用铝作还原剂,在碱性炉衬的炉筒中,采用下部点火法冶炼。
先把小部分混合炉料装入反应器中,即行点火。
反应开始后再陆续投加其余炉料。
通常用于冶炼高钒铁(含钒60~80%),回收率较电硅热法略低,约90~95%钒和钻常呈铁的类质同像分别赋存于钛磁铁矿和黄铁矿中。
此类矿石的选矿,一般是先用弱磁选分出钒铁精矿,再用重选、强磁选、浮选、电选联合方法从尾矿中回收钛铁矿和用浮选回收黄铁矿。
钒铁精矿所含的钛是选矿无法除去的,可以在冶炼中分离。
为了满足高钛渣炼铁必需的渣量,过分提高钒铁精矿的铁品位,有时是不合理的。
从磁选尾矿中回收钛的流程,首先要保证得到优质钛精矿。
铁矿石提取钒的原理

铁矿石提取钒的原理
铁矿石提取钒的原理主要包括以下几个步骤:选矿、矿浆造粒、焙烧还原、浸出和分离。
1. 选矿:首先需要对铁矿石中的不同矿石类型进行选矿,选择富含钒的矿石。
常见的富钒铁矿石主要有伊利石、斜方铁矿和镁铁矿等。
通过矿石的物理和化学性质,以及矿石的矿物成分进行分析和鉴定,确定矿石的品位和适用性。
2. 矿浆造粒:选取的铁矿石经过粉碎和分类处理后,得到一定粒度的矿浆。
矿浆通常会经过搅拌和调整浓度等工艺控制,以便在后续的工艺步骤中顺利进行。
3. 焙烧还原:将矿浆经过干燥处理,然后进行焙烧还原工艺。
焙烧还原利用高温氧化反应将铁矿石中的钒氧化物转化为钒酸钠,同时还原出水合钒酸钠。
这一步骤的目的是将矿石中的钒转化为溶解性的钒化物。
4. 浸出:通过将焙烧还原后的矿石与酸溶液进行浸入反应,使其中的钒化物溶解在酸溶液中。
常见的浸出剂有硫酸和氯化物等。
在浸出过程中,还可能需要控制温度、浓度和压力等工艺参数,以提高钒的浸出率。
5. 分离:将钒溶液与其他杂质进行分离。
分离过程中,可以通过一系列的分离技术,如萃取、离子交换、溶液蒸馏和晶体分离等,将杂质与钒溶液分离。
通过调整分离工艺参数,可获得纯度较高的钒产品。
总的来说,铁矿石提取钒的原理是通过选矿、矿浆造粒、焙烧还原、浸出和分离等一系列工艺步骤,通过合适的化学反应和物理分离,将铁矿石中的钒转化为溶解性的钒化物,并分离出钒溶液中的杂质,最终得到纯度较高的钒产品。
含钒铁矿石提钒途径选择

含钒铁矿石提钒途径选择钒是钢中的重要合金元素, 它可提高钢的韧性, 细化结晶粒度, 改善耐磨性能及热硬度, 因而广泛用于多种合金钢中。
我国钒资源十分丰富, 含钒铁矿以攀枝花和西昌地区蕴藏最多, 另外, 还有马鞍山和承德。
从含钒铁矿石提钒的途径有多种, 按其在炼钢流程中的前后可分为1、前提钒法又称直接法, 即由精矿提钒。
2、中提饥法又称间接法, 即由铁水吹钒渣, 再由钒渣提钒。
3、后提钒法即由铁水炼钢, 再由含钒钢渣提钒。
从含钒铁矿石提钒的流程归纳如下图一、前提饥法之一—钠化焙烧本法使用含V2O5 0.75~0.8的铁精矿, 用芒硝或纯碱作附加剂, 在回转窑内氧化焙烧, 水浸提钒。
该法虽然工艺流程短, 回收率比较高,达70~75. 但消耗高, 生产能力仅为间接法的十四分之一。
因此不适合大规模生产。
该法的原材料和能源消耗列于表。
所产铁尾矿可供炼铁用, 但不大受欢迎。
本法优点是钒回收率较钠化焙烧法更高。
厂小产量大, 劳动生产率高, 单耗低, 产品纯度高。
在有条件的地方可以推广采用。
二、前提饥法之二—钠化球团本法是用细磨的纯净铁矿粉, 加芒硝或纯碱造球, 在竖窑中氧化焙烧, 水浸提钒。
浸出采用固定床逆流浸洗, 设备简单。
国内有承德钢铁厂已进行半工业试验, 国外有芬兰奥、木两厂工业生产, 达到的指标列于表2:本法优点是钒回收率较钠化焙烧法更高。
规模小产量大, 劳动生产率高, 单耗低, 产品纯度高。
三、中提饥法—钒渣法本法是将含钒铁矿在高炉中炼得的含钒铁水用铁矿粉或空气氧化, 得到含。
一的钒渣, 再用焙烧水浸法提钒。
采用此工艺的有南非的摇包法和通用的转炉双联法, 以及马鞍山的槽炉法, 攀钢的雾化炉法。
本法优点是, 在用铁水炼钢之前将钒富集于钒渣中, 可使以后的水法提钒效率提高。
缺点是, 增加了中间环节, 系统回收率较低。
另外, 如果吹饥安排得不好, 会对炼钢有影响, 同时增加了吹钒渣的设备投资和使操作复杂化。
钒原矿的矿石选别的实验研究

钒原矿的矿石选别的实验研究钒原矿是一种重要的稀有金属矿石,含有丰富的钒资源。
对钒原矿进行矿石选别实验研究,对于提高钒资源的利用效率和降低开采过程中的成本具有重要意义。
本文将分析钒原矿的矿石选别技术,并介绍实验研究的方法和结果。
一、矿石选别技术的选择在钒原矿的矿石选别过程中,常用的技术包括重选、浮选、磁选等。
根据钒原矿的矿石特性和选别要求,合理选择矿石选别技术非常重要。
重选是钒原矿的常用选别技术之一。
通过重力作用,将矿石中的矿物按照密度差异进行分离,达到提高钒品位和回收率的目的。
重选的主要优点是操作简单、成本相对较低,适用于粗颗粒的矿石选别。
浮选是一种常用的钒原矿选别技术。
该技术利用矿物与气泡的吸附作用,使矿石中的有用矿物与废石迅速分离,达到提高钒品位的目的。
浮选的优点是适用于细颗粒的矿石选别,并且可以适应复杂的矿石成分。
磁选是一种应用广泛的钒原矿选别技术。
利用磁性矿物和非磁性矿物之间的磁性差异,通过磁场的作用将矿石中的有用矿物分离出来。
磁选的优点是适用于具有一定磁性的矿石,同时可以实现自动化操作和高度回收率。
根据钒原矿石的特性和选别要求,可以综合应用重选、浮选和磁选等技术,以达到最佳的选别效果。
二、实验研究方法与结果为了探究钒原矿的矿石选别效果,我们设计了以下实验研究。
首先,收集钒原矿的样品,并加以粉碎和磨矿处理,以获得符合实验要求的磨矿产品。
然后,采用不同选别技术对磨矿产品进行实验研究。
选择适当的设备和试剂,按照操作流程进行选矿操作。
在实验研究中,我们对不同选别技术的矿石选别效果进行了对比。
通过测定钒原矿的品位、回收率以及废石率等指标,评估选别技术的选矿效果。
实验结果显示,浮选技术在提高钒品位方面具有显著优势。
通过调节浮选工艺参数和试剂种类,可以有效地将矿石中的有用矿物与废石分离,达到较高的钒品位和回收率。
此外,磁选技术也可以实现较好的矿石选别效果。
通过选择适当的磁场强度和磁性分选机,可以有效地将矿石中的有用矿物分离出来,同时减少废石的产生。
钒粉的制作工艺
钒粉的制作工艺
钒粉是由钒矿经过一系列的加工和处理工艺制得的粉状钒产品。
以下是一般的钒粉制作工艺流程:
1. 钒矿选矿:首先对原料钒矿进行选矿处理,去除杂质和低品位矿石。
选矿过程可以包括破碎、筛分、浮选、磁选等工艺步骤。
2. 钒矿矿浆制备:将选矿过程中得到的高品位钒矿通过破碎和磨矿等工艺步骤,制成适合后续处理的矿浆。
3. 硫酸浸出:将钒矿矿浆进行硫酸浸出过程。
在高温和高压的条件下,将硫酸与钒矿反应,使得其中的钒溶解到溶液中。
4. 钒溶液处理:将钒溶液进行进一步的处理和净化。
可能包括沉淀、过滤、中和、浓缩、离子交换等工艺步骤,以去除杂质和提纯钒溶液。
5. 钒溶液还原:将钒溶液进行还原处理,使得其中的钒以金属钒的形式析出。
还原反应可以使用还原剂,如氨水、二氧化硫等。
6. 钒粉干燥和粉碎:将还原得到的金属钒进行干燥处理,以去除水分。
然后将干燥的钒金属进行粉碎,得到所需的钒粉。
具体的钒粉制作工艺可能会因钒矿种类、工艺设备和生产要求等因素而有所不同。
这里提供的是一般的制作工艺流程,实际操作过程中可能会有进一步的细节和改进。
在实际生产中,需要根据具体条件和要求进行调整和优化。
钒钛磁铁矿选矿工艺流程
钒钛磁铁矿选矿工艺流程钒钛磁铁矿是一种重要的金属矿石,具有富含钒、钛和铁等元素的特点。
其选矿工艺流程一般分为粗碎、粗选、中碎、中选和精选等几个环节。
以下是一份基本的钒钛磁铁矿选矿工艺流程。
首先,将原矿进行粗碎。
采用破碎机或颚式破碎机对原矿进行粗碎,将矿石破碎成较小的颗粒。
根据原矿的特性和要求,可以选择不同的破碎设备和破碎粒度。
接下来,进行粗选。
将粗碎后的矿石通过振动筛、螺旋分选机等设备进行粗选,将其中的矿石和非矿石分离。
这一步可以去除一部分余石、泥土等非矿石物质,减少后续处理的工作量。
然后,进行中碎。
将粗选后的矿石再次进行碎磨,使颗粒尺寸更加细小。
中碎一般采用圆锥破碎机或球磨机等设备,通过机械破碎和摩擦磨损的方式,使矿石颗粒更加均匀地分布。
接着,进行中选。
中选主要通过重选机、浮选机等设备实现。
重选机利用矿石颗粒与介质(如水、重稀浆等)的密度差异,进行物理分离。
浮选机则是利用具有选择吸附性质的药剂将有用矿石吸附在气泡上,使其上浮,而非矿石则沉入矿浆底部。
最后,进行精选。
精选是将中选后的产品经过一系列加工步骤,提纯和分离出所需的钒、钛等金属。
精选一般采用磁选机、重选机、浮选机等设备,通过差异化的物理和化学性质,将矿石中的有用成分进一步提纯。
需要注意的是,在钒钛磁铁矿的选矿过程中,还需要进行矿石磨矿、脱水、脱泥、浮渣处理等环节,以及废水处理、固废处理等环节,以达到环保、节能、高效的要求。
总之,钒钛磁铁矿的选矿工艺流程是一个复杂的过程,需要根据矿石的特性、产品的要求和生产的具体情况进行灵活调整和改进。
通过适当的破碎、粗选、中碎、中选和精选等环节的组合和优化,可以实现对钒钛磁铁矿的高效、低成本的开采和加工。
钒如何提炼的原理
钒如何提炼的原理钒的提炼是指将钒化合物从矿石中分离出来,使其成为纯净的钒金属。
钒的提炼过程主要包括矿石选矿、钒化合物的还原与提纯等步骤。
下面我将详细介绍钒的提炼原理。
首先,矿石选矿是钒提炼的第一步。
矿石选矿是通过重力分离和浮选等方法将含有钒的矿石从其他无价值的岩石中分离出来。
常见的含钒矿石主要有钒钛磁铁矿、伊利石矿以及含钒钒酸钙矿等。
通过矿石选矿,可以提高钒的含量和浓度,为后续的提炼工艺提供了较好的原料。
钒的提炼主要是通过还原钒化合物来获得纯净的钒金属。
常见的还原剂有焦炭、石灰石以及钠等。
其中,焦炭是最常用的还原剂。
原理是利用焦炭在高温下与钒矿石中的氧化钒反应,生成CO和CO2气体,使钒氧化物从固态转变为气体形式,从而实现钒的分离。
接下来,是对钒气体的处理与提纯。
一种常用的方法是采用冷却浓缩法。
这是通过将钒气体冷却至足够低的温度,使其凝结成液体。
此时,液态的钒气体可以与液体中的杂质分离,达到提纯的效果。
进一步的提纯可以通过电解法或浸出法来实现,以去除残留的杂质,使钒金属达到较高的纯度要求。
另外,值得注意的是,钒的提炼还会受到矿石性质的影响。
比如,钒钛磁铁矿中的钒主要以三氧化二钒(V2O3)的形式存在,而伊利石矿则主要以五氧化二钒(V2O5)的形式存在。
因此,不同的矿石需要采用不同的提炼方法和工艺,以获得最佳的提炼效果。
总结起来,钒的提炼原理是通过矿石选矿、还原和提纯等步骤,将钒化合物从矿石中分离出来,获得纯净的钒金属。
矿石选矿能够提高钒的含量和浓度,还原过程通过还原剂将钒氧化物转变为气体形式分离钒元素,提纯过程通过冷却浓缩、电解或浸出等方法去除杂质,使钒金属达到较高的纯度要求。
不同的矿石需要采用不同的提炼方法和工艺,以获得最佳的提炼效果。
这些步骤和方法的应用和改进,使得钒的提炼过程更加高效和经济。
钒的工艺流程
钒的工艺流程钒是一种重要的金属元素,常用于制备合金和催化剂等领域。
以下是钒的工艺流程的详细介绍:1. 钒矿的选矿处理:钒矿通常来自于钒矿石,如石钒合金矿、钒钛铁矿等。
首先需要对钒矿进行选矿处理,通过物理和化学方法将其中的杂质去除,使得钒的含量达到一定的标准。
2. 钛钒磨合布:将选矿后得到的钒矿进行磨合,与钛矿混合在一起。
这一步骤的目的是将钒与其它金属元素(如钛)进行分离,得到含有较高钒含量的矿石。
3. 钛钒磨矾法:将经过磨合后的钒钛矿与石碱进行熔炼反应,生成氧化物结晶。
然后对结晶进行分离、干燥等处理,得到锥钒矿。
4. 锥钒焙烧:将锥钒矿进行焙烧处理,通过控制焙烧温度和时间,使得含氧化钒的矿石中的氧化物得到还原,产生金属钒。
5. 钒的精炼:经过焙烧得到的金属钒通常还含有杂质元素,需要进行进一步的精炼处理。
常用的方法有火法精炼和湿法精炼。
- 火法精炼:通过将钒与其他金属元素进行氧化、还原、蒸馏等步骤,使得杂质被除去,得到纯度较高的钒。
- 湿法精炼:将含有钒的溶液通过电解、溶剂萃取等方式进行处理,去除其中的杂质,得到纯净的钒。
6. 钒的制备:将精炼得到的钒与其他金属元素进行合金化处理,制备出相应的钒合金。
钒合金常用于钢铁冶金、航天航空等领域。
7. 废渣处理:在钒的生产过程中,会产生大量的废渣和废水。
这些废渣和废水需要经过处理,以确保环境污染的最小化。
一般会采用化学处理、沉淀、过滤等方式处理废渣和废水。
综上所述,钒的工艺流程主要包括钒矿的选矿处理、钛钒磨合布、钛钒磨矾法、锥钒焙烧、钒的精炼、钒的制备以及废渣处理等步骤。
通过这些步骤,能够将含有钒的矿石处理成为纯净的钒或钒合金,以满足不同领域的需求。
同时,在整个工艺流程中,也需要关注环境保护,合理处理废渣和废水,减少对环境的影响。
- 1、下载文档前请自行甄别文档内容的完整性,平台不提供额外的编辑、内容补充、找答案等附加服务。
- 2、"仅部分预览"的文档,不可在线预览部分如存在完整性等问题,可反馈申请退款(可完整预览的文档不适用该条件!)。
- 3、如文档侵犯您的权益,请联系客服反馈,我们会尽快为您处理(人工客服工作时间:9:00-18:30)。
钒的选矿方法和步骤:
钒铁生产的主要原料是钒钛磁铁矿,经选矿富集后,通过高炉炼出含钒生铁,在雾化炉或转炉吹炼过程中提取钒渣。
钒渣经粉碎后配加钠盐(纯碱、食盐或无水芒硝)进行氧化钠化焙烧,使钒成为可溶的偏钒酸钠(NaVO3),浸取净化后加硫酸铵沉淀出多钒酸铵[(NH4)2V6O16],再经脱氨熔化,铸成片状五氧化二钒。
要求成分为V2O597~99%,P<0.05%,S<0.05%,Na2O+K2O <1.5%。
此外也从含钒铁精矿或含钒炭质页岩直接通过化学处理提取五氧化二钒。
电硅热法
片状五氧化二钒用75%硅铁和少量铝作还原剂,在碱性电弧炉中,经还原、精炼两个阶段炼得合格产品。
还原期将一炉的全部还原剂与占总量60~70%的片状五氧化二钒装入电炉,在高氧化钙炉渣下,进行硅热还原。
当渣中V2O5小于0.35%时,放出炉渣(称为贫渣,可弃去或作建筑材料用),转入精炼期。
此时,再加入片状五氧化二钒和石灰,以脱除合金液中过剩的硅、铝等,俟合金成分达到要求,即可出渣出铁合金。
精炼后期放出的炉渣称为富渣(含V2O5达8~12%),在下一炉开始加料时,返回利用。
合金液一般铸成圆柱形锭,经冷却、脱模、破碎和清渣后即为成品。
此法一般用于含钒40~60%的钒铁冶炼。
钒的回收率可达98%。
炼制每吨钒铁耗电1600千瓦?时左右。
铝热法
用铝作还原剂,在碱性炉衬的炉筒中,采用下部点火法冶炼。
先把小部分混合炉料装入反应器中,即行点火。
反应开始后再陆续投加其余炉料。
通常用于冶炼高钒铁(含钒60~80%),回收率较电硅热法略低,约90~95%
钒和钻常呈铁的类质同像分别赋存于钛磁铁矿和黄铁矿中。
此类矿石的选矿,一般是先用弱磁选分出钒铁精矿,再用重选、强磁选、浮选、电选联合方法从尾矿中回收钛铁矿和用浮选回收黄铁矿。
钒铁精矿所含的钛是选矿无法除去的,可以在冶炼中分离。
为了满足高钛渣炼铁必需的渣量,过分提高钒铁精矿的铁品位,有时是不合理的。
从磁选尾矿中回收钛的流程,首先要保证得到优质钛精矿。
研究了重选、浮选、重选一浮选、重选一强磁选一浮选、重选一强磁选等各种流程。
钛铁矿精矿用电选精选,可将二氧化钛品位提高到48%以上。
钛铁矿的浮选是在酸性矿浆中进行的,浮选黄铁矿回收钴应在浮选钛铁矿前进行,如果矿石含有碳酸盐矿物,必须预先浮出。
沉积型含钒炭质板岩也是我国钒矿资源中重要的一种,目前还处在研究阶段。
矿石中钒呈微粒嵌布的钒云母等矿物或吸附状态存在,用选矿方法不易富集,因而研究了湿法冶金提钒。
矿石先经煅烧除去炭质,然后进行钠化焙烧和水浸出。
水浸残渣再,酸浸可以进一步提高钒的浸出率。
有时原矿先经浮选富集成含钒粗精矿,再焙烧浸出,可以显著降低酸耗。
现在有些时候选矿和冶炼也在逐渐融合,目的都是提高品位.。