钢制管道焊后热处理工艺规程完整
现场管道焊缝热处理施工工艺标准_20120516095519745

现场管道焊缝热处理施工工艺标准QB-CNCEC J22303-20061 适用范围本施工工艺标准仅适用于碳素钢、合金钢金属管道焊缝现场热处理作业。
2 施工准备2.1 技术准备2.1.1施工技术资料设计资料(管道施工图、材料表、设计说明及技术规定等)。
2.1.2 现行施工标准规范GB50235《工业金属管道工程施工及验收规范》GB50236《现场设备、工业管道的焊接工程施工及验收规范》HG20225《化工金属管道施工及验收规范》SY0401《输油输气管道线路工程施工及验收规范》SY0402《石油天然气工艺管道工程施工及验收规范》SH3501《石油化工剧毒可燃介质管道工程施工及验收规范》SH/T3517《石油化工钢制管道工程施工工艺标准》DL5007《电力建设施工及验收技术规范》(火力发电厂焊接篇)JGJ46《施工现场临时用电安全技术规范》2.1.3 热处理施工方案根据管道施工图、设计说明及不同材质的管道焊缝热处理要求,以及工期、工程量等现场实际状况,编制管道焊缝现场热处理施工方案。
热处理施工方案应明确:热处理工艺流程、施工方法、劳动力组织、施工机具、材料、质量目标、质量通病预防、职业健康安全环保技术措施。
2.2 作业人员2.3 材料的验收与保管2.3.1管道焊缝现场热处理主要材料见下表:2.3.2材料的验收及保管2.3.2.1 一般材料的验收及保管⑴脚手架钢管及扣件应检查确认符合质量要求并有序堆放;⑵保温用铁丝、防雨用的移动棚(罩)妥善保管存放。
2.3.2.2 特殊材料的验收及保管。
⑴用选定的保温材料、铁丝网、石棉布、细铁丝缝制保温毡;保温毡应保持干燥,存放在室内,或室外垫高的排架上,并应覆盖不得受潮。
⑵电加热器、热电偶端点焊接良好、接线柱螺栓完好,补偿导线无脱皮并整齐盘绕,均存放在室内。
2.4主要施工机具2.4.1 主要机械设备变压器(或交流焊机)、温控柜、履带式电加热器、绳式电加热器、指型电加热器等。
钢管热处理工艺流程
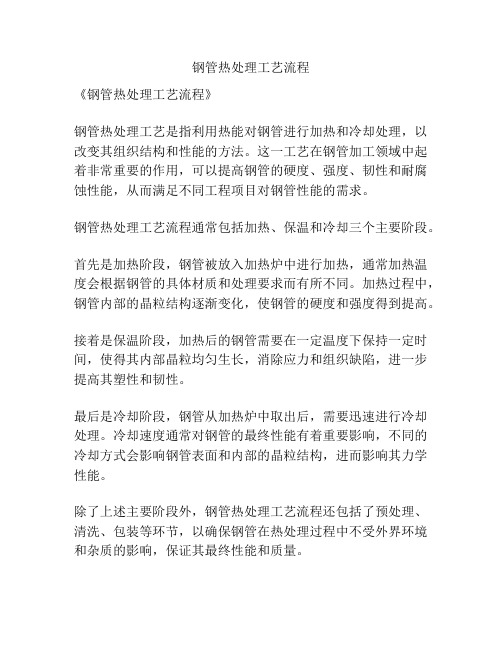
钢管热处理工艺流程
《钢管热处理工艺流程》
钢管热处理工艺是指利用热能对钢管进行加热和冷却处理,以改变其组织结构和性能的方法。
这一工艺在钢管加工领域中起着非常重要的作用,可以提高钢管的硬度、强度、韧性和耐腐蚀性能,从而满足不同工程项目对钢管性能的需求。
钢管热处理工艺流程通常包括加热、保温和冷却三个主要阶段。
首先是加热阶段,钢管被放入加热炉中进行加热,通常加热温度会根据钢管的具体材质和处理要求而有所不同。
加热过程中,钢管内部的晶粒结构逐渐变化,使钢管的硬度和强度得到提高。
接着是保温阶段,加热后的钢管需要在一定温度下保持一定时间,使得其内部晶粒均匀生长,消除应力和组织缺陷,进一步提高其塑性和韧性。
最后是冷却阶段,钢管从加热炉中取出后,需要迅速进行冷却处理。
冷却速度通常对钢管的最终性能有着重要影响,不同的冷却方式会影响钢管表面和内部的晶粒结构,进而影响其力学性能。
除了上述主要阶段外,钢管热处理工艺流程还包括了预处理、清洗、包装等环节,以确保钢管在热处理过程中不受外界环境和杂质的影响,保证其最终性能和质量。
总之,钢管热处理工艺流程是一个综合性的加工过程,需要严格控制各个环节的参数和操作,以确保钢管能够达到设计要求的性能,并满足使用需求。
只有专业的工艺流程和严密的操作才能保证钢管的质量和稳定性。
管道焊后热处理工艺流程说明综述
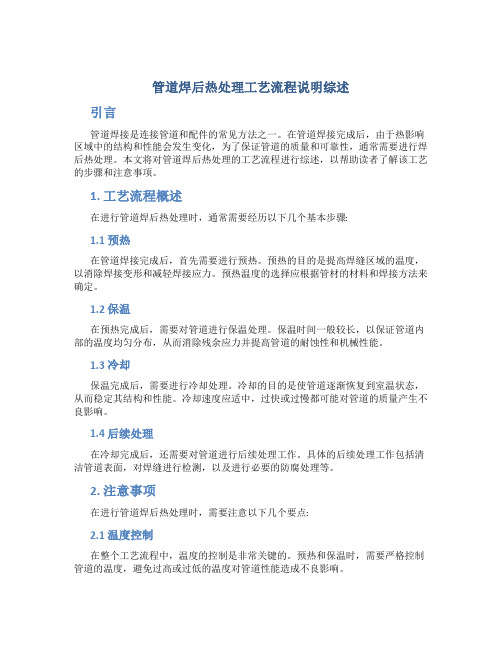
管道焊后热处理工艺流程说明综述引言管道焊接是连接管道和配件的常见方法之一。
在管道焊接完成后,由于热影响区域中的结构和性能会发生变化,为了保证管道的质量和可靠性,通常需要进行焊后热处理。
本文将对管道焊后热处理的工艺流程进行综述,以帮助读者了解该工艺的步骤和注意事项。
1. 工艺流程概述在进行管道焊后热处理时,通常需要经历以下几个基本步骤:1.1 预热在管道焊接完成后,首先需要进行预热。
预热的目的是提高焊缝区域的温度,以消除焊接变形和减轻焊接应力。
预热温度的选择应根据管材的材料和焊接方法来确定。
1.2 保温在预热完成后,需要对管道进行保温处理。
保温时间一般较长,以保证管道内部的温度均匀分布,从而消除残余应力并提高管道的耐蚀性和机械性能。
1.3 冷却保温完成后,需要进行冷却处理。
冷却的目的是使管道逐渐恢复到室温状态,从而稳定其结构和性能。
冷却速度应适中,过快或过慢都可能对管道的质量产生不良影响。
1.4 后续处理在冷却完成后,还需要对管道进行后续处理工作。
具体的后续处理工作包括清洁管道表面,对焊缝进行检测,以及进行必要的防腐处理等。
2. 注意事项在进行管道焊后热处理时,需要注意以下几个要点:2.1 温度控制在整个工艺流程中,温度的控制是非常关键的。
预热和保温时,需要严格控制管道的温度,避免过高或过低的温度对管道性能造成不良影响。
2.2 冷却速度冷却速度的选择应根据管道材料来确定。
过快的冷却速度可能导致管道的脆性增加,影响其耐久性;而过慢的冷却速度则可能引起残余应力的积聚,导致管道变形。
2.3 后续处理在管道焊后热处理完成后,还需要进行一些后续处理工作。
特别是对管道表面的清洁和焊缝的检测,以及防腐处理等。
这些后续处理工作的质量和细致程度将直接影响管道的质量和使用寿命。
管道焊后热处理工艺是保证管道质量和可靠性的重要环节。
通过对工艺流程的综述和注意事项的介绍,希望读者能够更好地理解和掌握该工艺的步骤和要点。
只有正确并严格地执行管道焊后热处理工艺,才能保证管道的性能和寿命,确保工业生产和生活的安全和可靠性。
焊后热处理办法

承压设备焊后热处理企业安全注册评审办法1 总则与适用范围1.1 总则为了规范承压设备焊后热处理,加强承压设备焊后热处理管理,保证承压设备焊后热处理质量,根据法规、标准和承压设备行业的需要制订本办法。
企业按自愿原则申请承压设备焊后热处理安全注册。
1.2 适用范围a)专业从事承压设备焊后热处理的企业;b)持有锅炉、压力容器和压力管道制造(安装)许可证的企业。
1.3 安全注册级别1.3.1 级别划分(1)I级(管道级):压力管道及管件I A级:主管壁厚≤25mm的焊后热处理;I B级:主管壁厚>25mm的焊后热处理。
(2)II级(容器级):容器(长度与外径比≤5)、球罐;(3)III级(塔器级):塔器、容器(长度与外径比>5)III A级:塔器级设备立置焊后热处理;III B级:塔器级设备卧置焊后热处理。
(4)各级别又划分为炉内焊后热处理(代号:N)与炉外焊后热处理(代号:W)1.3.2 评审合格级别的应用范围1.3.3定级或升级申请定级或升级的企业,评审小组需对一台(批)见证件进行评审。
2 工作程序承压设备焊后热处理企业安全注册评审工作程序包括申请、受理、驻地评审、现场评审、批准和发证。
2.1 申请2.1.1 申请承压设备焊后热处理企业安全注册评审的企业(以下简称“申请单位”)必须具备下列基本条件:a)具有企业独立法人资格,已在当地政府相关部门注册登记。
b)建立质量管理体系,并持续有效运行。
c)具有相应的焊后热处理技术人员与管理人员。
d)具备进行焊后热处理所需的加热设施、辅助装备、检、测温度系统和自动记录与调控系统。
e)具有相应的技术文件和工艺文件,以及相关的法规和标准。
f)具有承压设备焊后热处理业绩及相应的档案资料。
g)具有相应的规模和场地(所)。
2.1.2 凡符合2.1.1规定的“申请单位”根据本“办法”向全国锅炉压力容器标准化技术委员会(以下简称“锅容标委”)提交申请书。
2.2 受理2.2.1 “锅容标委”自收到申请书之日起1个月内进行初审。
12Cr1MoVG管道焊后热处理工艺控制要点

12Cr1MoVG管道焊后热处理工艺控制要点摘要:目前低合金耐热钢12Cr1MoVG在化工企业中使用非常广泛,由于其材料对延迟裂纹敏感的特性,在焊接过程中和焊接结束后易产生延迟裂纹,其形成的宏观裂纹以致贯穿裂纹与材料的韧性和残余应力大小有很大关系。
根据国家现行规范规程的规定,铬钼耐热钢管道焊后应及时进行焊后热处理来降低扩散氢含量,消除残余应力以避免焊缝裂缝的产生。
传统的热处理设备使用热处理以设备,现已唐山中浩化工有限公司厂外外管蒸汽管道低合金耐热钢12Cr1MoVG为例采用新方法焊后热处理的工艺控制要点关键词:热处理工艺控制要点12Cr1MoVG管道一、施工准备1.1技术准备熟悉施工图纸,编制合金钢管道焊后热处理方案明确需要进行焊后热处理的焊接接头如下:本工程中合金钢管12Cr1MoVG规格为Φ323.9×22.2,其所有的对接接头;合金钢管12Cr1MoVG上的对焊支管座;其他经焊接工艺评定需进行焊后热处理的管件;1.2人员准备由于本项目需要焊后热处理的焊口总数不多,且工作量较集中,场地方便,项目部指定一名技术员,负责编制焊接热处理施工方案和作业指导数等技术文件,指导并监督热处理人员的工作,整理热处理资料等;指定一名热处理工,负责按照热处理施工方案和作业指导书进行施工,记录热处理操作过程,完成自检等。
1.3 设备及辅助材料准备西门子S7-200PLC模块(可编程序控制器)、交流接触器、继电器、计算机、柔性陶瓷电阻加热器,配备一台里氏硬度计,以测量焊缝和母材的硬度值。
辅助材料有快速接长导线,串联导线、热电偶、补偿导线、接插件、硅酸铝岩棉毡、铁丝等。
快速接长导线供加热器与交流接触器连接,K形热电偶及补偿导线是用于测温;硅酸铝纤维毯耐温1000℃,主要用于热处理的保温;铁丝用于固定热电偶和绑扎硅酸铝纤维毯。
焊后热处理工艺及措施2.1加热方法本项目采用柔性陶瓷电阻加热的方法对管道焊缝进行加热。
管道焊热处理工艺
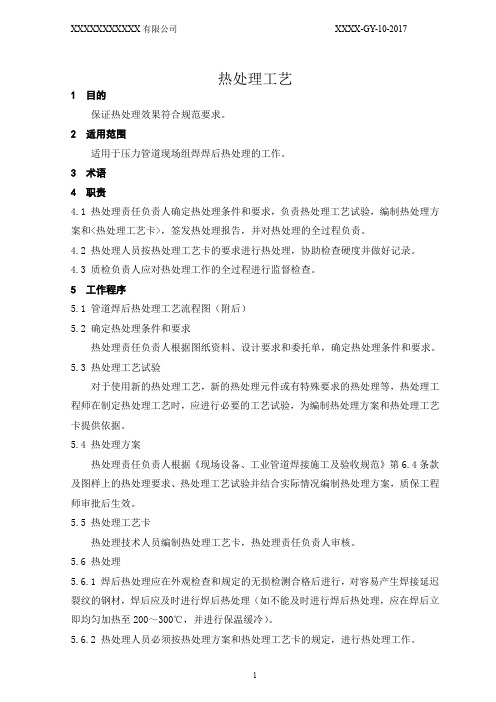
热处理工艺1 目的保证热处理效果符合规范要求。
2 适用范围适用于压力管道现场组焊焊后热处理的工作。
3 术语4 职责4.1 热处理责任负责人确定热处理条件和要求,负责热处理工艺试验,编制热处理方案和<热处理工艺卡>,签发热处理报告,并对热处理的全过程负责。
4.2 热处理人员按热处理工艺卡的要求进行热处理,协助检查硬度并做好记录。
4.3 质检负责人应对热处理工作的全过程进行监督检查。
5 工作程序5.1 管道焊后热处理工艺流程图(附后)5.2 确定热处理条件和要求热处理责任负责人根据图纸资料、设计要求和委托单,确定热处理条件和要求。
5.3 热处理工艺试验对于使用新的热处理工艺,新的热处理元件或有特殊要求的热处理等,热处理工程师在制定热处理工艺时,应进行必要的工艺试验,为编制热处理方案和热处理工艺卡提供依据。
5.4 热处理方案热处理责任负责人根据《现场设备、工业管道焊接施工及验收规范》第6.4条款及图样上的热处理要求、热处理工艺试验并结合实际情况编制热处理方案,质保工程师审批后生效。
5.5 热处理工艺卡热处理技术人员编制热处理工艺卡,热处理责任负责人审核。
5.6 热处理5.6.1 焊后热处理应在外观检查和规定的无损检测合格后进行,对容易产生焊接延迟裂纹的钢材,焊后应及时进行焊后热处理(如不能及时进行焊后热处理,应在焊后立即均匀加热至200~300℃,并进行保温缓冷)。
5.6.2 热处理人员必须按热处理方案和热处理工艺卡的规定,进行热处理工作。
5.6.3 焊后热处理的加热范围,应以焊缝中心为基准,每侧不应小于焊缝宽度的3倍,加热部分以外应进行保温。
5.6.4 热处理的测温必须准确可靠,应采用自动温度记录仪。
所有仪表、热电偶及其附件,应根据计量的要求进行标定或校验。
5.6.5 进行热处理时,测温点应对称布置在焊缝中心两侧,且不得少于两点,水平管道的测点应上下对称布置。
5.6.6 热处理责任负责人和质检负责人检查确认升/降温速度、温度、保温时间。
004管道焊前预热及焊后热处理
错误!未指定书签。
目录1.适用范围 (2)2..编制依据 (2)3.工程概况及工作量(以一台机组计) (2)4.作业人员资格及要求 (3)5. 施工主要机具、工具及材料计划 (3)6.施工准备 (4)7.作业程序 (4)8. 作业方法、参数及工艺要求 (5)9.不合格品的热处理 (8)10.质量检查及验收 (8)11.工序交接及成品保护 (8)12.安全和文明施工措施 (8)13.强制性条文 (11)14.技术记录 (18)1.适用范围1.1本作业指导书适用于天津天铁50MW燃机-蒸汽联合发电锅炉、汽机管道焊接的热处理。
2..编制依据2.1天津天铁50MW燃机-蒸汽联合发电焊接专业施工组织设计2.2《焊接工艺评定规程》DL/T868-20042.3《火力发电厂焊接技术规程》DL/T869—20122.4《火力发电厂焊接热处理技术规程》(DL/T819-2002)2.5《电力建设安全工作规程》第一部分:火力发电厂(DL5009.1-2002)2.6天津天铁50MW燃机-蒸汽联合发电相关图纸2.7溧阳恒正无损检测有限公司相关焊接工艺评定2.8《电力建设施工质量验收及评定规程》第七部分:焊接(DL/T5210.7-2010)2.9《工程建设标准强制性条文》(电力工程部分)(2011版)2.10《电力建设工程质量监督检查典型大纲》(火电、送变电部分)3.工程概况及工作量(以一台机组计)3.1工程概况本工程建设规模为50MW燃机-蒸汽联合发电机组。
本工程厂址地处邯郸市涉县更乐镇原天津铁厂动力厂运输部家属区内。
机组配套一台双压、无补燃、卧式自然循环余热锅炉,余热锅炉为杭州锅炉集团股份有限公司设计制造,其相应的附属系统由中冶京诚工程技术有限公司设计。
锅炉专业施工范围包括:锅炉本体、辅机、锅炉附属管道及设备、烟道、钢烟囱等。
本锅炉为双压、无补燃、无再热、自带整体式除氧器、卧式自然循环、露天布置余热锅炉,所有受热面管子水平布置,烟气为垂直流动,受热面内水和蒸汽的流动都是由自然循环完成的。
工业管道焊后热处理工艺规程
工业管道焊后热处理工艺规程1.适用范围本规程适用于含碳量小于或等于0.3%的碳素钢、低合金结构钢、低温钢、不锈钢、耐热耐腐蚀高合金钢现场焊接管道的焊后热处理。
焊后热处理是利用金属高温下强度的降低而把弹性应变转变成塑性应变以达到消除残余应力的目的。
在现场施工条件下的焊后热处理,系指对焊接接头进行高温回火,以降低接头残余应力,不包括其他各种形式的热处理,如固溶、调质及正火等。
2.引用标准GB50236 现场设备、工业金属管道焊接工程施工及验收规范SHJ517 石油化工钢制管道工程施工工艺标准SH3523 石油化工工程高温管道焊接规程SHJ520 石油化工工程铬钼耐热钢管道焊接技术规程SH3525 石油化工低温钢焊接规程SH2526 石油化工异种钢焊接规程3.操作工艺3.1工艺流程*仅适用于铬钼钢3.2施工准备3.2.1施工用材料及机具要求a)热处理所用保温材料应为无碱超细玻璃棉,且应有质量证明书或合格证。
b)热处理设备为可自动控制温度的固定盘柜式或手提式控制箱,并应配有自动打点记录仪。
管壁厚度小于或等于25mm的焊接接头宜用挠性指状加热器(镍铬电阻丝)加热,管壁厚度大于25mm的焊接接头,宜用感应法加热。
3.2.2作业条件a)热处理操作者应熟悉专业标准熟练掌握工艺、设备、测量仪表的使用方法。
b)热处理前应对焊缝进行确认,确认项目包括1)焊接工作已完成;2)焊缝外观经检查确认符合质量标准;3)其他要求的检验项目已检验合格,并取得检验合格通知单;4)除铬钼耐热钢以外焊缝的无损检测已检验合格,并已取得检验合格通知单。
3.3热电偶及加热器安装3.3.1每道焊口对称安装两支热电偶,热电偶安装在靠近焊缝边缘30mm内,管材与热电偶接触处应用砂轮机打磨出金属光泽,热电偶安装采用细铁丝捆扎,对于不锈钢管道,应用不锈钢捆扎,不得用电焊定位。
3.3.2电加热器缠绕范围为焊缝两侧各100-150mm,一根加热器缠绕多道焊缝时,必须保证热处理部位的相似性,即同性质、同规格缠绕的圈数及宽度相同。
钢质管道焊接规程
钢质管道焊接规程一、引言钢质管道的焊接是构筑建筑和工业设备中不可或缺的一个环节。
为了保证焊接质量和施工安全,制定一套严格的焊接规程是非常必要的。
本文将介绍钢质管道焊接规程的相关内容,以确保焊接作业满足技术标准和质量要求。
二、适用范围本规程适用于所有钢质管道的焊接作业,包括建筑工程和工业设备等方面。
三、材料准备1. 钢质管道的原材料必须符合国家标准或设计要求,材料合格证明文件应随同材料一同到场,备案。
2. 焊接材料的选用应符合设计要求,应具备相应的合格证书。
四、焊接设备1. 焊接设备必须经过定期检验和维护,以确保其正常工作。
2. 焊机的接地良好,接地电阻不大于4欧姆。
3. 焊机放置应稳固,不能有明显的振动和晃动。
五、焊接工艺1. 焊接工艺应根据设计要求确定,包括焊接方法、焊接参数等。
2. 焊工必须持有相应的焊工资格证书,并符合焊接工艺的要求。
3. 焊工应使用符合要求的个人防护装备,如焊接手套、面罩等。
4. 焊接前应对材料进行清洁处理,确保没有油污和杂质。
5. 焊接作业前应对焊缝进行预热,预热温度应符合设计要求。
6. 焊接作业中应保持焊机稳定电压,焊接电弧稳定。
六、焊缝检测1. 焊接完成后,应进行焊缝外观检查,确保焊缝无明显裂纹、夹渣等缺陷。
2. 对焊缝进行无损检测,包括超声波检测、射线检测等。
3. 检测结果应记录并备案,以备后续的质量验收。
七、焊后处理1. 焊接完成后,应对焊缝进行清理,去除焊渣等杂质。
2. 对焊缝进行除锈处理,确保焊缝表面光洁无锈蚀。
3. 焊缝的防腐处理应符合设计要求,选用防腐涂料或其他方式来保护焊缝。
八、验收标准1. 对焊接质量进行验收时,应参照国家相关标准和设计要求。
2. 焊缝的质量按照焊接工艺和工程要求进行判定。
3. 合格的焊接质量应符合焊接质量等级标准。
九、安全措施1. 焊接作业中应严格遵守安全操作规程,避免发生安全事故。
2. 焊接作业现场应进行安全防护,设置明显的安全警示标志。
压力管道焊接及焊后热处理施工工艺规程
压力管道焊接及焊后热处理施工工艺规程一、目的本规程旨在规范压力管道的焊接作业和焊后热处理工艺,确保管道焊接质量,满足安全运行的要求。
二、适用范围适用于工业和民用领域内所有需要进行焊接及焊后热处理的压力管道施工。
三、术语和定义3.1 压力管道指用于输送气体、液体等介质,并且其内部压力大于或等于一个规定值的管道。
3.2 焊接通过加热或加压,或两者并用,使两个分离的金属部分熔合成为一个整体的过程。
3.3 焊后热处理焊接完成后,为了改善焊接接头的组织和性能,对其进行的加热和冷却过程。
四、施工前的准备4.1 材料准备确认管道材料、焊材符合设计和施工要求。
检查管道和焊材的化学成分、机械性能是否符合标准。
4.2 设备和工具准备确保焊接设备(如焊机、热处理设备)处于良好状态。
准备必要的工具,如焊接夹具、量具、清洁工具等。
4.3 人员准备焊接操作人员必须持有相应的资格证书。
进行安全技术交底,确保所有人员了解施工要求和安全措施。
4.4 环境准备确保焊接区域清洁、无尘、通风良好。
检查焊接区域的温度、湿度是否符合焊接要求。
五、焊接工艺5.1 焊接方法选择根据管道材料、厚度、使用条件选择合适的焊接方法。
5.2 焊接坡口准备按照设计要求准备焊接坡口,确保坡口尺寸、形状符合标准。
5.3 焊接参数设定根据焊接方法和管道材料,设定焊接电流、电压、速度等参数。
5.4 焊接操作按照焊接工艺卡进行焊接操作,确保焊缝质量。
5.5 焊接检验焊接完成后,进行外观检查和无损检测,确保焊缝无缺陷。
六、焊后热处理工艺6.1 热处理方法选择根据焊接接头的性能要求,选择合适的热处理方法,如退火、正火等。
6.2 热处理参数设定确定热处理的温度、保温时间、冷却速度等参数。
6.3 热处理操作按照热处理工艺卡进行操作,确保热处理效果。
6.4 热处理检验热处理完成后,进行硬度测试、金相分析等,确保热处理质量。
七、施工安全7.1 安全防护操作人员必须穿戴必要的个人防护装备,如防护服、防护眼镜、手套等。
- 1、下载文档前请自行甄别文档内容的完整性,平台不提供额外的编辑、内容补充、找答案等附加服务。
- 2、"仅部分预览"的文档,不可在线预览部分如存在完整性等问题,可反馈申请退款(可完整预览的文档不适用该条件!)。
- 3、如文档侵犯您的权益,请联系客服反馈,我们会尽快为您处理(人工客服工作时间:9:00-18:30)。
锅炉管焊接热处理工艺规程
1 总则
本工艺规程适用于低碳和低合金钢锅炉管道焊接接头消除残余应力的焊后热处理,不涉及发生相变和改变金相组织的其他热处理方法。
2 、引用标准及参考文献
NB/T47015—2011 《压力容器焊接规程》
SH3501—2011 《石油化工有毒可燃介质管道工程施工及验收规》
GB50236—2011 《现场设备、工业管道焊接工程施工及验收规程》
3、焊前预热
3.1材料性能分析
部分锅炉管道采用低合金耐热钢,材料具有良好的热稳定性能,是高温热管道的常用材料,由于材料中存在铬、钼合金成分,材料的淬硬倾向大,施工中采用焊前预热、焊后热处理的工艺措施,来获得性能合格的焊接接头。
3.2管道组成件焊前预热应按表1的规定进行,中断焊接后需要继续焊接时,应重新预热,焊接是保持层间温度不小于150℃。
3.3 当环境温度低于10℃时,在始焊处100mm围,应预热到50℃以上。
表1 管道组成件焊接前预热要求
4 设备和器材
4.1焊后热处理必须采用自动控制记录的“热处理控制柜”控制温度。
4.2“热处理控制柜”需满足下列要求:
4.2.1能自动控制、记录热处理温度。
4.2.2控制柜、热电偶和补偿导线组合后的温度误差≤±10℃。
4.2.3柜所有仪表、仪器需经法定计量单位校验合格,使用时校验合格证须在有效期。
4.3热电偶
4.3.1焊接接头焊后热处理须采用热电偶测温控温。
4.3.2热电偶需满足如下要求:
4.3.2.1量程为热处理最高温度的1.5倍,精度等级为1.0;控温柜和补偿导线的组合温差波动围≤±10℃。
4.3.2.1按校验周期进行强制校验,使用时校验合格证须在有效期。
4.4加热器
4.4.1焊后热处理必须采用可实现自动指示控制记录的电加热绳或履带加热板加热。
4.4.2管壁厚大于25mm的焊接接头宜采用感应法加热。
4.5热处理设备由经培训合格的专人管理和调试,使用时应放置在防雨防潮的台架上。
4.6保温材料
热处理所用保温材料应为绝缘无碱超细玻璃棉或复合硅酸盐毡,且应有质量证明及合格证。
5 人员
5.1操作人员需经培训,熟悉专业标准,熟练掌握工艺设备、测量仪表的使用方法。
5.2操作人员热处理施工时必须严格遵守本规程和“热处理工艺指导书”的规定。
6 热处理时机
焊后热处理在无损检测反修合格后试压前进行;有再热裂纹倾向的材料,热处理后需进行无损检测。
7 热处理工艺及工艺试验
7.1工艺参数
7.1.1焊后热处理的加热温度按设计技术文件规定执行,设计技术文件未规定时按表1执行。
表1 常用锅炉管焊接接头热处理温度
7.1.2保温时间
7.1.2.1保温时间按下列规定计算,总保温时间不得少于30分钟。
a非合金钢为每毫米壁厚2.5 分钟。
b合金钢为每毫米壁厚3.0 分钟。
7.1.2.2焊缝的厚度按以下原则计算:
a等厚度全焊透对接接头的焊后热处理厚度按管壁厚计算。
b不等厚对接接头按其较薄一侧管壁厚度计算。
c接管与凸颈法兰相焊时按接管壁厚计算。
d接管与管板相焊时按其焊缝厚度计算。
e非受压元件与受压元件相焊时按焊接处的焊缝厚度计算。
7.1.3加热和冷却速度:
7.1.3.1焊件升温至300℃后,加热区升温速度按5125/δ℃/h计算,且不大于220℃/h,最小不低于55℃/h。
7.1.3.2焊件保温期间,加热区最高与最低温度之差不得大于80℃。
7.1.3.3保温后的冷却速度按6500/δ℃/h计算,且不大于260℃/h,最小不低于55℃/h,冷至300℃后可自然冷却。
7.2热处理操作:
7.2.1焊缝热处理前,应将管道两端的管口封闭,以防管气体流动。
与焊缝相邻近的阀门如不可拆除,应对阀体采取冷却措施,阀瓣应处于开启状态。
7.2.2热处理的加热围为焊缝两侧各不少于焊缝宽度的3倍,且不少于100mm,接管与容器相焊的整圈焊缝热处理时,加热带的宽度不得小于壳体厚度的6倍,加热区以外100mm围应予以保温。
7.2.3热电偶端点应埋置在离焊缝边缘30mm以的焊缝下侧(水平管),当焊缝两侧壁厚差大于5mm或公称通径大于300mm时,在焊缝对称位置放两支热电偶。
7.2.4电加热绳用缠绕法固定在管道上,履带式瓷加热板包覆管道后用3 mm 扎丝紧固,至少紧固两道。
7.2.4用软质保温材料包覆加热器,用3 mm扎丝紧固保温层,使用50mm厚保温材料保温时,层数不少于三层,保温层总厚度不小于150mm, 加热器两端应用保温材料封堵。
7.3热处理工艺试验:
7.3.1每项工程采用不同材质、不同热处理工艺时,工程开工前需先做热处理工艺试验。
7.3.2工艺试验由热处理责任师根据焊缝钢材的材质和规格编制热处理作业指导书,确定工艺参数,经技术负责人批准后执行。
7.3.3热处理试验后在试件上做硬度检验,切取试样进行拉伸、弯曲和冲击试验,试验报告作为热处理合格的依据。
7.3.4试验合格的热处理工艺参数和方法不得更改,否则应重新试验。
7.4热处理工艺卡
7.4.1热处理责任师根据试验合格的热处理工艺参数编制热处理工艺卡,经技术负责人批准后实施。
7.4.2热处理工艺卡的格式见附表。
8 监测与质量检验
8.1热处理过程中需对热处理温度进行观察和监测。
8.1.1在热处理过程中,操作人员应观察温度指示仪表有无异常,如发现异常时,应立即停止升(降)温并分析原因,找出问题处理完毕后方可继续处理。
8.1.2热处理过程中检验人员用单独热电偶仪表系统对处理焊口进行温度监测,以确定热处理控温系统温度的准确性和稳定性。
抽检比例不少于5%,若发现控制仪表温差超标应立即停止并分析原因,温差达标后方可继续处
理。
8.2 质量检验
8.2.1焊接接头的热处理质量,用硬度法按下列规定进行检查:
8.2.1.1要求作中间试件的焊接接头应在管子轴间的断口A(母材)B(热影响区)C(焊缝表面)D(焊缝外表面)等四处检查硬度。
8.2.1.2现场管道焊缝在其外表面A,B,C三处检查硬度。
8.2.1.3每处焊接接头各检查两个测点,取其硬度平均值。
8.2.1.4焊接接头的硬度检查数量:按设计技术文件执行,设计技术文件未规定时,按100%检测。
8.2.1.5测得的硬度值不应超过母材标准硬度的120%。
8.2.1.6不合格者应重新热处理和测定硬度。
8.2.2合金钢管和规要求作无损检测的低合金钢管及碳素钢,在硬度检验合格后实施无损检测,不合格部位返修后应重新进行热处理。
8.3 经焊后热处理合格的部位,不得再从事焊接作业,否则应重新进行热处理;若不可避免需在焊后热处理管道焊接非受压元件,若同时满足下列条件,焊后可不再进行热处理。
8.3.1管道为非合金钢或碳锰钢材料。
8.3.2角焊缝的计算厚度不大于10mm。
8.3.3按评定合格的焊接工艺施焊。
8.3.4角焊缝已进行100%表面无损探伤。
9、资料管理:
9.1热处理应有专人负责,并按规定格式作好原始记录和检测记录。
9.2热处理工序结束后,根据不同材质规格的管道焊缝分别出具热处理报
告,并附下列资料:
9.2.1热处理所形成的记录及硬度检测报告。
9.2.2热处理自动控制记录曲线(有焊口编号)。
10 安全专项:
10.1热处理部位有明显的警示和可靠的隔离措施
10.2热处理设备、管道接地良好
10.3加热器无裸露电阻线,各活接头绝缘良好
10.4热处理系统中的漏电保护装置正常可靠
焊接接头焊后热处理报告
编号:
焊接接头焊后热处理工艺卡
编号:
工艺卡编制人:批准:年月日年月日
焊接接头焊后热处理记录
编号:。