关键元器件和原材料的控制程序
关键元器件和原材料的控制程序
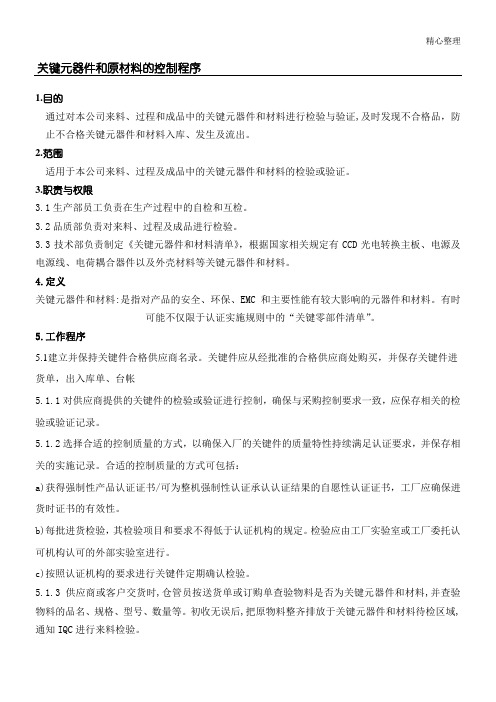
精心整理关键元器件和原材料的控制程序1.目的通过对本公司来料、过程和成品中的关键元器件和材料进行检验与验证,及时发现不合格品,防止不合格关键元器件和材料入库、发生及流出。
2.范围适用于本公司来料、过程及成品中的关键元器件和材料的检验或验证。
3.职责与权限3.13.23.34.定义5.5.15.1.15.1.2a)货时证书的有效性。
b)每批进货检验,其检验项目和要求不得低于认证机构的规定。
检验应由工厂实验室或工厂委托认可机构认可的外部实验室进行。
c)按照认证机构的要求进行关键件定期确认检验。
5.1.3供应商或客户交货时,仓管员按送货单或订购单查验物料是否为关键元器件和材料,并查验物料的品名、规格、型号、数量等。
初收无误后,把原物料整齐排放于关键元器件和材料待检区域,通知IQC 进行来料检验。
5.1.4品质部IQC按公司来料检验标准及指导书的检验方式和内容进行检验,并将检验结果如实填写在《来料检查报告》中。
5.1.5对公司无法检验的材料,要求供应商提供检验报告,由IQC依检验标准进行确认。
IQC检验完毕,将《来料检查报告》(注明是关键元器件或材料)交主管审核做出合格或不合格判定,作为验收判定。
5.1.6IQC依检验结果,对物料做合格或不合格的标识,检验合格的来料由仓管员办理入库手续。
5.1.7经检验之不合格品,IQC人员应填写《品质异常处理报告》经经理确认后通知采购部,具体按《不合格品控制程序》实施。
5.1.85.1.95.25.2.15.2.25.2.35.2.45.35.3.1QA《抽5.3.25.3.3经5.3.4保持生产作业指南、照片、图纸或样品等加以控制,确保最终产品与认证样品一致。
5.4关键元器件和材料的定期确认检验5.4.1关键元器件和材料的定期确认检验参照《例行检验和确认检验控制程序》5.5测试标准5.5.1a)GB4943《信息技术设备的安全》b)GB9254《信息技术设备无线电骚扰限值和测量方法》c)GB17625.1《电磁兼容限值谐波电流发射限值(设备每相输入电流≤16A)》5.6检测项目5.6.1a)安全检测项目产品的安全检测项目原则为GB4943规定的全部适用项目。
关键元器件质量控制程序
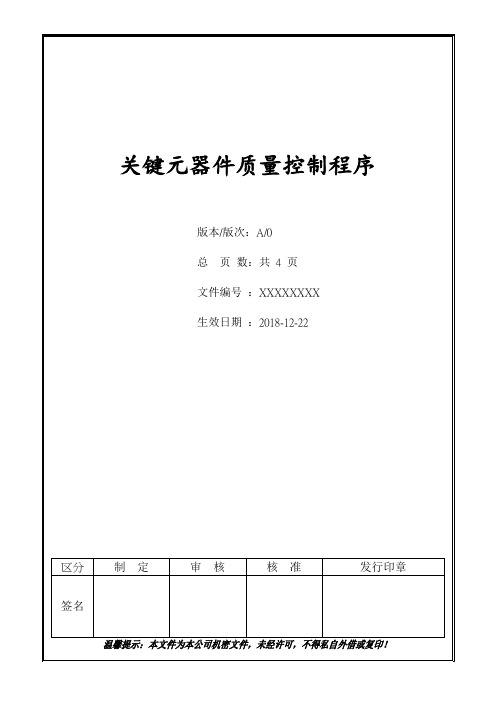
4.2.1采购员在具体实施采购时,必须从《合格供方名单》中选择供应商进行采购。如果因各种原因需从《合格供方名单》之外的供应商处进行采购时,则应按照《外部提供的过程、产品和服务控制程序》的规定,先对该供应商进行调查评价,评价合格再向3C认证机构提出变更申请,经批准后方可实施采购。
4.1.2为确保关键件的质量特性持续满足规定的技术质量要求,提供关键件的合格供应商必须满足以下要求:
(a)获得CCC证书或可为最终产品强制性认证承认的自愿性产品认证结果,应确保其证书状态的有效;
(b)没有获得相关证书的关键件,其定期确认检验应符合产品认证实施规则/细则的要求。
采购部在对提供关键件的供应商进行调查、选择、评价和年度再评价以及实施采购过程中,必须严格按照以上要求执行,对提供关键件的供应商的其他控制方案,其控制效果应不低于上述(a)或(b)的要求。
关键元器件质量控制程序
版本/版次:A/0
总页数:共4页
文件编号:XXXXXXXX
生效日期:2018-12-22
区分
制定
审核
核准
发行印章
签名
温馨提示:本文件为本公司机密文件,未经许可,不得私自外借或复印!
修订记录
制定/修订日期
修订内容摘要
页次
版本/版次
总页数
新制订
--
A/0
4
1.目的:
确保本公司已通过3C认证的产品符合《强制性产品认证实施规则工厂质量保证能力要求》对认证产品关键元器件的质量控制要求。
2.范围:
适用于对公司所有已通过3C认证的产品关键件的质量控制。
3.职责:
3.1品质部是认证产品关键件的质量控制的主管部门,负责认证产品关键件质量控制的全程监控和管理。
3C关键原材料控制程序
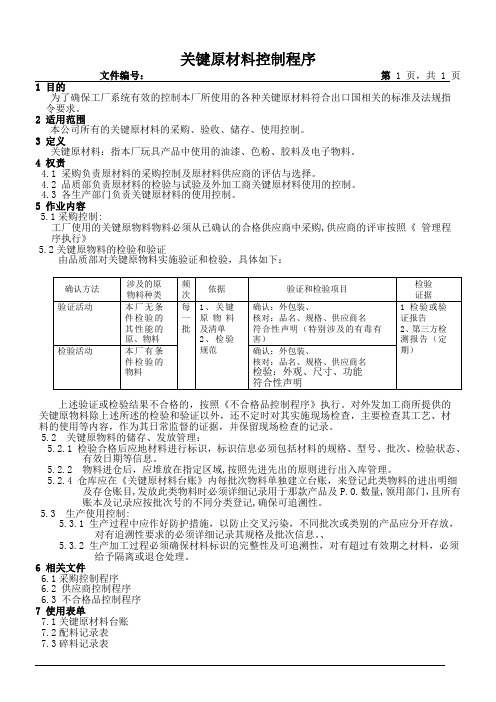
文件编号:第 1 页,共 1 页1 目的为了确保工厂系统有效的控制本厂所使用的各种关键原材料符合出口国相关的标准及法规指令要求。
2 适用范围本公司所有的关键原材料的采购、验收、储存、使用控制。
3 定义关键原材料:指本厂玩具产品中使用的油漆、色粉、胶料及电子物料。
4 权责4.1 采购负责原材料的采购控制及原材料供应商的评估与选择。
4.2 品质部负责原材料的检验与试验及外加工商关键原材料使用的控制。
4.3 各生产部门负责关键原材料的使用控制。
5 作业内容5.1采购控制:工厂使用的关键原物料物料必须从已确认的合格供应商中采购,供应商的评审按照《管理程序执行》5.2关键原物料的检验和验证由品质部对关键原物料实施验证和检验,具体如下:上述验证或检验结果不合格的,按照《不合格品控制程序》执行。
对外发加工商所提供的关键原物料除上述所述的检验和验证以外,还不定时对其实施现场检查,主要检查其工艺、材料的使用等内容,作为其日常监督的证据,并保留现场检查的记录。
5.2 关键原物料的储存、发放管理:5.2.1 检验合格后应地材料进行标识,标识信息必须包括材料的规格、型号、批次、检验状态、有效日期等信息。
5.2.2 物料进仓后,应堆放在指定区域,按照先进先出的原则进行出入库管理。
5.2.4 仓库应在《关键原材料台账》内每批次物料单独建立台账,来登记此类物料的进出明细及存仓账目,发放此类物料时必须详细记录用于那款产品及P.O.数量,领用部门,且所有账本及记录应按批次号的不同分类登记,确保可追溯性。
5.3 生产使用控制:5.3.1 生产过程中应作好防护措施,以防止交叉污染,不同批次或类别的产品应分开存放,对有追溯性要求的必须详细记录其规格及批次信息。
、5.3.2 生产加工过程必须确保材料标识的完整性及可追溯性,对有超过有效期之材料,必须给予隔离或退仓处理。
6 相关文件6.1采购控制程序6.2 供应商控制程序6.3 不合格品控制程序7 使用表单7.1关键原材料台账7.2配料记录表7.3碎料记录表文件编号:第 2 页,共 1 页7.4 关键原材料检验或验证记录。
关键元器件和材料定期确认检验控制程序

关键元器件和材料定期确认检验控制程序质量体系文件关键元器件和材料定期确认检验控制程序发行部门:品质部文件编号:YXD-QP-04版本:A1编制:审核:批准:2010年01月22日发布 2010年02月01日实施一、目的对关键元器件和材料的检验/验证及定期确认检验,保证关键元器件的产品质量持续达到认证产品要求。
二、范围本程序适用于认证产品的关键元器件和材料的检验/验证及定期确认检验。
三、职责品质部:负责对关键元器件和材料的检验/验证及定期确认检验。
采购部:负责要求供应商及时对检验或验证中出现问题的关键元器件和材料进行处理。
四、程序4.1关键元器件和材料的检验/验证对生产购进的关键元器件和材料,仓库保管员核对送货清单确认物料品名、规格、数量等无误、包装无损后,置于待检区。
检验员根据本公司检测能力,严格按照《进料检验规范》执行,在些标准中明确规定了检测频率、抽样方法、检测项目、检测内容、检测方法、判断依据、使用的检测设备等。
对于无检测能力的项目,由供应商自行检验或验证,并提供相关的检测报告。
对重要的关键元器件和材料,并且本身是生产厂家的,本公司要求其提供产品的检验标准,若是中间商的则要求提供质量保证协议、每批产品的检验记录、合格证明等文件。
一般的关键元器件除本公司内部检验外,只需要求提供质量证明,并填写《IQC 检验报告》。
仓库保管员根据合格记录或标识办理入库手续;验证不合格时,检验员在物料上贴“不合格”标签,按《不合格品控制程序》进行处理。
采购及时跟进不合格品的处理.紧急放行当生产急需来不及验证,在可追溯的前提下,由生产车间填写《紧急(例外)放行申请单入经生产负责人批准后,一联留存,一联交品质部,一联交仓库。
仓库保管员根据批准的《IQC检验报告》按规定数量留取同批样品送检,其余由检验员在领料单上注明“紧急放行”后放行;车间在其后生产记录上也应注明“紧急放行”。
在放行的同时,检验员应继续完成该批产品的检验:不合格时品质部负责对该批紧急放行产品进行追踪处理。
13关键元器件、材料的检验验证和确认控制程序
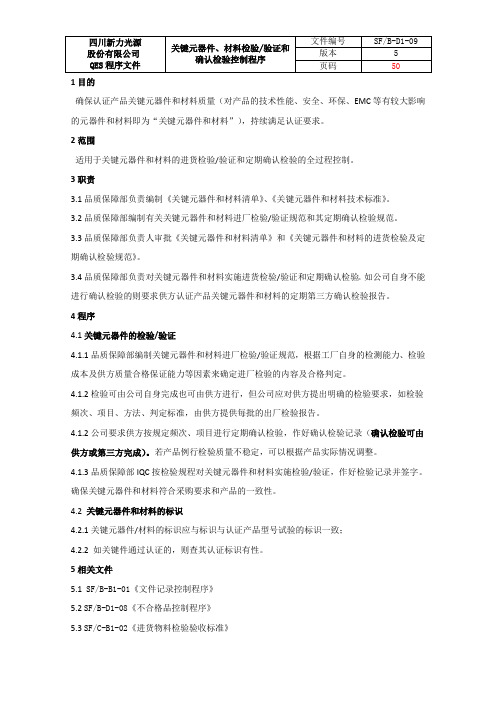
1目的确保认证产品关键元器件和材料质量(对产品的技术性能、安全、环保、EMC等有较大影响的元器件和材料即为“关键元器件和材料”),持续满足认证要求。
2范围适用于关键元器件和材料的进货检验/验证和定期确认检验的全过程控制。
3职责3.1品质保障部负责编制《关键元器件和材料清单》、《关键元器件和材料技术标准》。
3.2品质保障部编制有关关键元器件和材料进厂检验/验证规范和其定期确认检验规范。
3.3品质保障部负责人审批《关键元器件和材料清单》和《关键元器件和材料的进货检验及定期确认检验规范》。
3.4品质保障部负责对关键元器件和材料实施进货检验/验证和定期确认检验。
如公司自身不能进行确认检验的则要求供方认证产品关键元器件和材料的定期第三方确认检验报告。
4程序4.1关键元器件的检验/验证4.1.1品质保障部编制关键元器件和材料进厂检验/验证规范,根据工厂自身的检测能力、检验成本及供方质量合格保证能力等因素来确定进厂检验的内容及合格判定。
4.1.2检验可由公司自身完成也可由供方进行,但公司应对供方提出明确的检验要求,如检验频次、项目、方法、判定标准,由供方提供每批的出厂检验报告。
4.1.2公司要求供方按规定频次、项目进行定期确认检验,作好确认检验记录(确认检验可由供方或第三方完成)。
若产品例行检验质量不稳定,可以根据产品实际情况调整。
4.1.3品质保障部IQC按检验规程对关键元器件和材料实施检验/验证,作好检验记录并签字。
确保关键元器件和材料符合采购要求和产品的一致性。
4.2 关键元器件和材料的标识4.2.1关键元器件/材料的标识应与标识与认证产品型号试验的标识一致;4.2.2 如关键件通过认证的,则查其认证标识有性。
5相关文件5.1 SF/B-B1-01《文件记录控制程序》5.2 SF/B-D1-08《不合格品控制程序》5.3 SF/C-B1-02《进货物料检验验收标准》5.4 SF/C-D1-12《关键元器件/材料定期确认规范》6质量记录6.1 SF/R-E1-04《合格供方名单》6.2SF/R-E1-05《采购计划》6.3 SF/R-B1-01《关键元器件/材料清单》6.4 SF/R-B1-02《新材料认证申请表》6.5 SF/R-D1-08《进货检验记录》6.6 SF/R-D1-09《电源控制器检验记录》6.7 SF/R-D1-10《进货不合格品通知单》6.8 SF/R-D1-08《不合格品报告单》6.9供方或第三方提供的合格证明和有关检验报告。
关键元器件和材料的检验验证控制程序
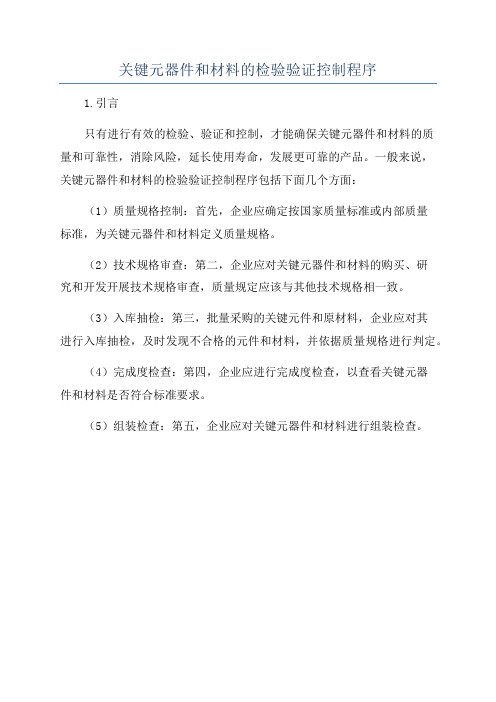
关键元器件和材料的检验验证控制程序
1.引言
只有进行有效的检验、验证和控制,才能确保关键元器件和材料的质
量和可靠性,消除风险,延长使用寿命,发展更可靠的产品。
一般来说,
关键元器件和材料的检验验证控制程序包括下面几个方面:
(1)质量规格控制:首先,企业应确定按国家质量标准或内部质量
标准,为关键元器件和材料定义质量规格。
(2)技术规格审查:第二,企业应对关键元器件和材料的购买、研
究和开发开展技术规格审查,质量规定应该与其他技术规格相一致。
(3)入库抽检:第三,批量采购的关键元件和原材料,企业应对其
进行入库抽检,及时发现不合格的元件和材料,并依据质量规格进行判定。
(4)完成度检查:第四,企业应进行完成度检查,以查看关键元器
件和材料是否符合标准要求。
(5)组装检查:第五,企业应对关键元器件和材料进行组装检查。
关键原材料确认控制程序THOP
2 范围
适用于对获证产品所涉及到的关键元器件和材料的检验或验证。
3.职责
3.1 品质部负责编制检验规范,负责对关键元器件和材料的检验或验证。 3.2 采购部负责对检验或验证中出现问题的关键元器件和材料的处理。
4 程序认证
4.1 零部件的进货检验 4.1.1 对获证产品生产所需购进的关键元器件和材料等物资, 仓库保管员核对送货单, 确认配件名称、 型号规格、数量等无误、包装无损后通知品质部检验员进行检验或验证。 4.1.2 检验员根据《零部件进货检验标准》和《零部件入厂抽样方案》进行抽样检验,并填写《零部 件进货检验报告》,对每批进货来的证书有效性进行确认。 A) 仓库管理员根据合格的《零部件进货检验报告》办理入库手续; B)验证不合格时,检验员在零部件上贴“不合格”标签,按《不合格品控制程序》进行处理。 C)零部件进货检验过程必须控制好关键零部件和原材料的一致性。 4.1.3 根据本工厂的检测能力,按照《零部件进货检验标准》对关键元器件和材料进行检验或验证。 编制《零部件进货检验标准》,应明确规定了检测频率、抽样方法、检测项目检验内容、检测 方法、判别依据、使用的检测设备等。对于无检测能力的项目,由供应商自行检验或验证。对 重要的关键元器件和材料,并且本身是生产厂家的,本工厂要求其提供产品的检验标准,若是 中间商的则要求提供质量保证协议、每批产品的检验记录、合格证明等文件。
关键原材料确认控制程序
文件编号 版 本
TH-OP-038 A/0 灯具事业部
制订单位 制造中心品质部 生效日期 2014. 04. 16
批
准
审
核制ຫໍສະໝຸດ 作文件修订履历页 序 号 修订日期 修订内容摘要 版本变更状况
传阅签名:
1/3
关键元器件和材料的检验验证控制程序
乐清市华菱电气有限公司关键元器件和材料的检验/验证、定期确认控制程序文件编号:HL/QP-0206版本:A/1受控状况:分发号:2009年10月28日发布2009年11月10日实施1.目的对关键元器件和材料特性进行监视和测量,以检验/验证关键元器件和材料符合要求。
2. 范围对外协外购的关键元器件和材料的检验/验证进行控制。
3. 职责3.1技术质检科负责关键元器件和材料的检验/验证的控制。
3.2生产供应科负责送检和检验合格后关键元器件和材料的保管并负责制定《原材料检验规范》或《检验卡片》。
4. 程序4.1元器件和材料的分类公司将原材料、外购件、外协件,按重要性分为A、B、C三类,即:A类:直接影响最终产品使用或安全性能的物资(关键元器件和材料);B类:不影响产品使用性能或稍有影响但可以补救的物资;C类:包装及辅助材料等起辅助作用的物资。
4.2 关键元器件和材料的识别、确定生产供应科根据认证实施细则,结合产品特点,编制《关键零部件和材料明细表》,经质量负责人审核后实施。
4.3关键元器件和材料的进厂检验/验证4.3.1 生产供应科采购回关键元器件和材料,将元器件和材料放于“待检”区域,并及时报检。
由仓库保管员填写《送检单》,报技术质检科检验员进行检验。
4.3.2 技术质检科检验员接到《送检单》后,核对送检产品及数量,按照《原材料检验卡片》进行检验/验证。
检验卡应规定:检验项目、检验标准、检验器具、检查水平、合格质量水平、抽样数、允收数和拒收数及验收准则等。
4.3.3检验合格的元器件和材料,由零件仓库保管员根据《关检单》中检验员签字确定合格后方可检收入库。
对进货验证的材料和元器件由供方提供质检报告,其内容包括化学成份、机械性、电性能等。
4.3.4不合格品的处理4.3.4.1检验中发现的不合格品,由质检员作好标识,按照《不合格品控制程序》进行处理(返工、退货和降级处理)。
4.3.4.2生产供应科根据不合格情况,决定是否需填写《供立质量评定单》。
关键零部件和材料质量控制程序
秦皇岛市XX医学系统有限公司质量管理体系文件文件名称关键零部件和材料质量控制程序文控标识文件编号CMS-02-A01 版本 C编制部门品质部生效日期2017/6/1发布签署姓名职位签署签署日期编制毕X梅质保工程师审核会签审核——批准杨X山总经理发放范围□市场部□销售管理部□研发中心□采购部□生产部□仓储部□物流部□电子商务部□技术支持中心□人力资源部□品质部□办公室□国际贸易部□发放方式□电子文档□纸文档□光盘+签署页归档方式□电子文档编写/打开软件:_______________ □纸文档□光盘+签署页更改记录版本/修订次数更改页修改码更改单号更改主要内容生效日期加盖红色受控印章的硬拷贝文件受控。
使用前,请核实文件是否为有效版本。
l 目的对供方提供的关键元器件和材料进行检验或验证,以确保其满足认证所规定的要求。
2 范围适用于公司CCC认证产品所涉及到的关键元器件和材料的检验或验证。
3 职责3.1 研发中心负责《关键零部件清单》和《关键零部件和材料采购技术要求》制定。
3.2 品质部负责对关键零部件和材料的检验和定期确认检验及认定工作。
3.3 采购部负责关键零部件和材料的采购、入库及供方控制,以及检验或验证中出现问题的关键零部件和材料的处理。
4 程序4.1 检验或验证4.1.1 公司CCC认证产品生产所需购进的关键零部件和材料等物资到货后,采购部填写《进料单》随物资交库房,库房核对品名、规格、数量等无误、包装无损后通知品质部检验员进行检验或验证。
4.1.2 品质部检验员根据《进货检验指导书》和(或)采购技术要求进行检验或验证,并填写《进货检验报告单》,在《进料单》上签字确认。
4.1.3 库房将验收合格的物资办理入库手续;不合格物资执行《不合格品控制程序》。
4.1.4 库房、品质部等相关部门在验收过程中,应按《标识和可追溯性控制程序》标识好采购关键零部件和材料的检验和试验状态。
4.1.5 根据《进货检验指导书》和(或)研发中心编制的《关键零部件和材料采购技术要求》确定检验或验证方法:本身是生产厂家的,公司要求其提供产品的检验标准;若是中间商的则要求提供质量保证文件、每批产品的检验记录、合格证明等文件。
关键元器件和材料的检验与定期确认控制程序
20+20 (450V)
GB/T12747.1 GB/T12747.2
3.端子与外壳间交流电压 试验 4.内部放电器件试验
每批来料要求供应 商提供 CQC 报告
5.电容器损耗角正切测量
6.密封性试验
YBYKC-S
1.静负载
3.
壳体
3.0mm 厚 GB/T20641
2.防护等级验证
ABS 绝缘板
3.绝缘材料性能
5.2 物管部按关键元器件清单进行物料采购。
5.3 关键元器件和原材料的检验/验证
5.3.1 对购进的关键元器件/材料,物管部核对送货清单确认物料品名、规格、数量等无误、包装无
损后,置于待检区、填写《进料检验报表》交给检验员。
5.3.2 品质部接到来料信息后,按照《进料检验规范》《抽样检验指引》等文件资料对来料进行检验
GB14082.2
5 熔断器 RS711BC 40A/63A GB13539.1
6
绝缘导 BVR-2.5mm²1.5mm² JB8734.2
线
10mm² 16mm²
GB5023.2
确认检验项目
确认频次
1.静负载 2.防护等级验证 3.绝缘材料性能 4.耐腐蚀验证 1.耐热性能试验 2.着火危险性能试验 3.介电性能 4.短路耐受强度验证
可视为对该关键件和材料进行了定期确认检验
5.4.4关键元器件/原材料没有获得 3C 证书或 CQC 自愿性认证证书的,物管部要求关键件和材料的供
应商提供检验报告或有能力的第三方检测机构出具的检验报告,供应商提供的报告中的检验项目符合
认证规定要求(元件名称,规格型号,确认项目,确认检验频次符合下表要求),品质部对报告进行
- 1、下载文档前请自行甄别文档内容的完整性,平台不提供额外的编辑、内容补充、找答案等附加服务。
- 2、"仅部分预览"的文档,不可在线预览部分如存在完整性等问题,可反馈申请退款(可完整预览的文档不适用该条件!)。
- 3、如文档侵犯您的权益,请联系客服反馈,我们会尽快为您处理(人工客服工作时间:9:00-18:30)。
关键元器件和原材料的控制程序
1.目的
通过对本公司来料、过程和成品中的关键元器件和材料进行检验与验证,及时发现不合格品,防止不合格关键元器件和材料入库、发生及流出。
2.范围
适用于本公司来料、过程及成品中的关键元器件和材料的检验或验证。
3.职责与权限
3.1生产部员工负责在生产过程中的自检和互检。
3.2品质部负责对来料、过程及成品进行检验。
3.3技术部负责制定《关键元器件和材料清单》,根据国家相关规定有CCD光电转换主板、电源及电源线、电荷耦合器件以及外壳材料等关键元器件和材料。
4.定义
关键元器件和材料: 是指对产品的安全、环保、EMC和主要性能有较大影响
的元器件和材料。
有时可能不仅限于认证实施规则中的
“关键零部件清单”。
5.工作程序
5.1 建立并保持关键件合格供应商名录。
关键件应从经批准的合格供应商处购买,并保存关键件进货单,出入库单、台帐
5.1.1 对供应商提供的关键件的检验或验证进行控制,确保与采购控制要求一致,应保存相关的检验或验证记录。
5.1.2 选择合适的控制质量的方式,以确保入厂的关键件的质量特性持续满足认证要求,并保存相关的实施记录。
合适的控制质量的方式可包括:
a)获得强制性产品认证证书/可为整机强制性认证承认认证结果的自愿性认证证书,工厂应确保进货时证书的有效性。
b)每批进货检验,其检验项目和要求不得低于认证机构的规定。
检验应由工厂实验室或工厂委托认可机构认可的外部实验室进行。
c)按照认证机构的要求进行关键件定期确认检验。
5.1.3 供应商或客户交货时,仓管员按送货单或订购单查验物料是否为关键元器件和材料,并查验物料的品名、规格、型号、数量等。
初收无误后,把原物料整
齐排放于关键元器件和材料待检区域,通知IQC进行来料检验。
5.1.4 品质部IQC按公司来料检验标准及指导书的检验方式和内容进行检验,并将检验结果如实填写在《来料检查报告》中。
5.1.5 对公司无法检验的材料,要求供应商提供检验报告,由IQC依检验标准进行确认。
IQC检验完毕,将《来料检查报告》(注明是关键元器件或材料)交主管审核做出合格或不合格判定,作为验收判定。
5.1.6 IQC依检验结果,对物料做合格或不合格的标识,检验合格的来料由仓管员办理入库手续。
5.1.7 经检验之不合格品,IQC人员应填写《品质异常处理报告》经经理确认后通知采购部,具体按《不合格品控制程序》实施。
5.1.8 来料急需生产而来不及作检验时,由生产部提出申请,经总经理批准可紧急放行,但生产过程中必须进行检验,并按规定对来料作好标识、记录,以便品质异常时紧急回收追踪。
5.1.9 关键元器件和材料在检验中发现不符合产品要求时应予以批退,不许特采。
并要求供应商回复,改进物料小批量验证合格后再正常生产。
5.2 制程中检验
5.2.1 在生产前,首先确认所需生产的产品的各种规格要求,在正常生产时,需进一步核对产品的各项品质要点。
5.2.2 生产部员工在生产过程中必须做好关键元器件和材料的自检、互检。
5.2.3 在线QC按相关标准对半成品进行检验,并填写《QC日报表》。
5.2.4 生产过程中发现的不合格品按《不合格品控制程序》处理。
5.3 成品检验
5.3.1 QA依《抽样计划表》对成品进行随机抽检,并将检验结果记录在《QA抽检报告》上,并根据《抽样计划表》中相关规定判定此批成品是否合格。
5.3.2 检验发现的不合格成品,看是否为关键元器件和材料引起,并按《不合格品控制程序》处理。
5.3.3 经QA检验合格的成品由生产部入库,QA定期公地成品按公司型式实验项目进行实验,对关键器件的一致性进行确认,并填写《例行实验报告》。
5.3.4 对最终产品的安全造成重要影响的关键工序、结构、关键件等应能在生产过程中通过建立和保持生产作业指南、照片、图纸或样品等加以控制,确保最终产品与认证样品一致。
5.4 关键元器件和材料的定期确认检验
5.4.1 关键元器件和材料的定期确认检验参照《例行检验和确认检验控制程序》5.5 测试标准
5.5.1 a)GB4943《信息技术设备的安全》
b)GB9254《信息技术设备无线电骚扰限值和测量方法》
c)GB17625.1《电磁兼容限值谐波电流发射限值(设备每相输入电流≤16A)》
5.6检测项目
5.6.1 a)安全检测项目
产品的安全检测项目原则为GB4943规定的全部适用项目。
b)电磁兼容检测项目
产品的电磁兼容检测项目原则为GB9254和GB17625.1规定的全部适用项目。
6.相关文件
《不合格品控制程序》
《关键元器件定期确认检验程序》
7.相关记录
《来料检测表》
《成品检验报表》
《品质异常处理报告》
《抽样计划表》。