一种含钒钢渣提钒的方法
从含钒钢渣中富集钒的方法与流程
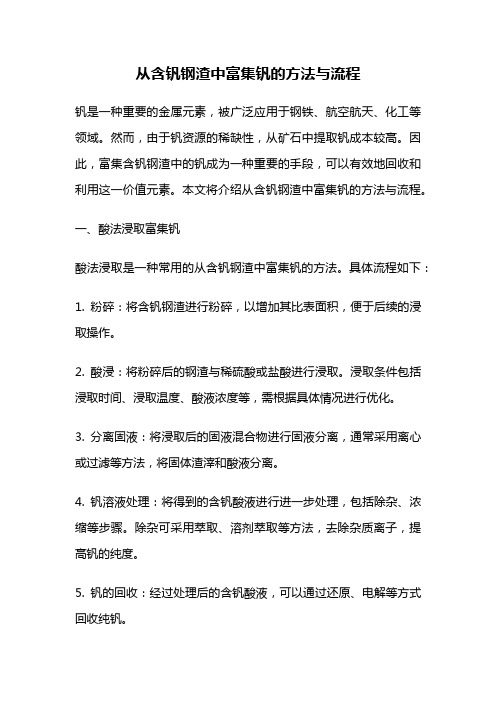
从含钒钢渣中富集钒的方法与流程钒是一种重要的金属元素,被广泛应用于钢铁、航空航天、化工等领域。
然而,由于钒资源的稀缺性,从矿石中提取钒成本较高。
因此,富集含钒钢渣中的钒成为一种重要的手段,可以有效地回收和利用这一价值元素。
本文将介绍从含钒钢渣中富集钒的方法与流程。
一、酸法浸取富集钒酸法浸取是一种常用的从含钒钢渣中富集钒的方法。
具体流程如下:1. 粉碎:将含钒钢渣进行粉碎,以增加其比表面积,便于后续的浸取操作。
2. 酸浸:将粉碎后的钢渣与稀硫酸或盐酸进行浸取。
浸取条件包括浸取时间、浸取温度、酸液浓度等,需根据具体情况进行优化。
3. 分离固液:将浸取后的固液混合物进行固液分离,通常采用离心或过滤等方法,将固体渣滓和酸液分离。
4. 钒溶液处理:将得到的含钒酸液进行进一步处理,包括除杂、浓缩等步骤。
除杂可采用萃取、溶剂萃取等方法,去除杂质离子,提高钒的纯度。
5. 钒的回收:经过处理后的含钒酸液,可以通过还原、电解等方式回收纯钒。
二、矩阵冶金法富集钒矩阵冶金法是另一种常用的从含钒钢渣中富集钒的方法。
具体流程如下:1. 热处理:将含钒钢渣进行热处理,使其中的钒转化为易溶性的钒化合物。
热处理温度和时间需要根据钢渣的组成和性质进行调控。
2. 酸浸:将经过热处理的钢渣与酸性溶液进行浸取。
浸取酸液的浓度和温度需要根据钢渣的特性进行优化。
3. 分离固液:将浸取后的固液混合物进行分离,得到固体渣滓和酸液。
4. 钒溶液处理:对得到的含钒酸液进行杂质去除和钒的富集。
杂质去除可以采用萃取、溶剂萃取等方法。
5. 钒的回收:经过处理后的含钒酸液,可以通过还原、电解等方式回收纯钒。
三、其他方法与流程除了酸法浸取和矩阵冶金法,还有一些其他方法可以用于富集含钒钢渣中的钒,如氧化焙烧法、浸出熔融法等。
这些方法具体流程与条件有所不同,但核心思想都是通过化学反应实现钒的富集与回收。
在实际应用中,根据含钒钢渣的成分和性质选择合适的方法进行钒的富集。
一种含钒钢渣提钒方法
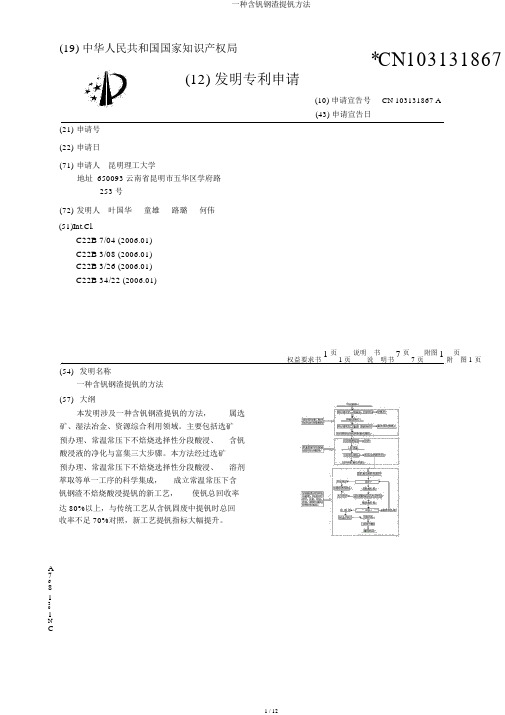
一种含钒钢渣提钒方法(19) 中华人民共和国国家知识产权局*CN103131867(12)发明专利申请(10) 申请宣告号CN 103131867 A(43) 申请宣告日(21)申请号(22)申请日(71)申请人昆明理工大学地址 650093 云南省昆明市五华区学府路253 号(72)发明人叶国华童雄路璐何伟(51)Int.Cl.C22B 7/04 (2006.01)C22B 3/08 (2006.01)C22B 3/26 (2006.01)C22B 34/22 (2006.01)权益要求书1页1页说明说书明书7页7 页附图1附页图 1 页(54)发明名称一种含钒钢渣提钒的方法(57)大纲本发明涉及一种含钒钢渣提钒的方法,属选矿、湿法冶金、资源综合利用领域。
主要包括选矿预办理、常温常压下不焙烧选择性分段酸浸、含钒酸浸液的净化与富集三大步骤。
本方法经过选矿预办理、常温常压下不焙烧选择性分段酸浸、溶剂萃取等单一工序的科学集成,成立常温常压下含钒钢渣不焙烧酸浸提钒的新工艺,使钒总回收率达 80%以上,与传统工艺从含钒固废中提钒时总回收率不足 70%对照,新工艺提钒指标大幅提升。
A768131NCCN 103131867 A 权利要求书1/1 页1.一种含钒钢渣提钒的方法,其特点在于详尽步骤包括以下:(1)将含钒钢渣破碎、磨矿后在依照旧规工艺在磁场强度为 0.08T ~ 0.25T 的条件下进行弱磁选,获取的磁性物质为磁性铁精矿,其余为磁选尾矿,尔后将磁性铁精矿加水调整至矿浆浓度 15 ~ 30wt%,在冲程 6 ~ 14mm、冲次 280 ~ 440r/min 的条件下依照旧规工艺进行重选,获取的比重要的物质为重选精矿,比重小的物质为重选尾矿;(2)在常温常压条件下进行Ⅰ段预浸除杂,将步骤( 1)中获取的重选精矿在硫酸溶液中依照固液比 1 :1 ~ 6g/ml 混杂并调整混杂液的pH 值为 3 ~ 4,在搅拌强度为 100 ~ 500 转/min 的条件下搅拌浸出0.5 ~ 6h,经固液分别获取Ⅰ段浸渣和含铁酸浸液;在常温常压条件下进行Ⅱ段浸出提钒,将Ⅰ段浸渣在硫酸溶液中依照固液比 1 :1 ~ 6g/ml 混杂并调整混合液的 pH 值为 0.3 ~ 2,经固液分别获取Ⅱ段浸渣和含钒酸浸液;(3)第一将步骤(2)中的含钒酸浸液依照旧规工艺依次进行萃前氧化、酸度调治和萃取,萃取的上层清液为负载有机相,基层为萃取废液,上基层分别后将负载有机相进行冲洗除杂,在常温条件下,将负载有机相加入活性硫酸盐溶液中,依照对照 O/A=1~ 6 的条件下冲洗 3 ~ 15min,冲洗达成后获取的上层清液为载钒有机相,基层为冲洗废液,将上基层分别,即可获取载钒有机相和冲洗废液,冲洗废液按老例工艺办理后返回浸出;(4)将步骤(3)中获取的载钒有机相依照旧规工艺进行反萃,反萃后获取的上层液为卸载有机相,基层液为反萃液,卸载有机相返回萃取步骤使用,反萃液依照旧规工艺进行铵盐沉钒,将铵盐沉钒获取的积淀产品依照旧规工艺进行煅烧分解,最后制得的精钒产品。
- 1、下载文档前请自行甄别文档内容的完整性,平台不提供额外的编辑、内容补充、找答案等附加服务。
- 2、"仅部分预览"的文档,不可在线预览部分如存在完整性等问题,可反馈申请退款(可完整预览的文档不适用该条件!)。
- 3、如文档侵犯您的权益,请联系客服反馈,我们会尽快为您处理(人工客服工作时间:9:00-18:30)。
(10)申请公布号 (43)申请公布日 2013.06.05C N 103131867 A (21)申请号 201310077492.X(22)申请日 2013.03.12C22B 7/04(2006.01)C22B 3/08(2006.01)C22B 3/26(2006.01)C22B 34/22(2006.01)(71)申请人昆明理工大学地址650093 云南省昆明市五华区学府路253号(72)发明人叶国华 童雄 路璐何伟(54)发明名称一种含钒钢渣提钒的方法(57)摘要本发明涉及一种含钒钢渣提钒的方法,属选矿、湿法冶金、资源综合利用领域。
主要包括选矿预处理、常温常压下不焙烧选择性分段酸浸、含钒酸浸液的净化与富集三大步骤。
本方法通过选矿预处理、常温常压下不焙烧选择性分段酸浸、溶剂萃取等单一工序的科学集成,构建常温常压下含钒钢渣不焙烧酸浸提钒的新工艺,使钒总回收率达80%以上,与传统工艺从含钒固废中提钒时总回收率不足70%相比,新工艺提钒指标大幅提升。
(51)Int.Cl.权利要求书1页 说明书7页 附图1页(19)中华人民共和国国家知识产权局(12)发明专利申请权利要求书1页 说明书7页 附图1页(10)申请公布号CN 103131867 A*CN103131867A*1/1页1.一种含钒钢渣提钒的方法,其特征在于具体步骤包括如下:(1)将含钒钢渣破碎、磨矿后在按照常规工艺在磁场强度为0.08T ~0.25T 的条件下进行弱磁选,得到的磁性物质为磁性铁精矿,其余为磁选尾矿,然后将磁性铁精矿加水调整至矿浆浓度15~30wt%,在冲程6~14mm 、冲次280~440r/min 的条件下按照常规工艺进行重选,得到的比重大的物质为重选精矿,比重小的物质为重选尾矿;(2)在常温常压条件下进行Ⅰ段预浸除杂,将步骤(1)中得到的重选精矿在硫酸溶液中按照固液比1:1~6g/ml 混合并调整混合液的pH 值为3~4,在搅拌强度为100~500转/min 的条件下搅拌浸出0.5~6h ,经固液分离得到Ⅰ段浸渣和含铁酸浸液;在常温常压条件下进行Ⅱ段浸出提钒,将Ⅰ段浸渣在硫酸溶液中按照固液比1:1~6g/ml 混合并调整混合液的pH 值为0.3~2,经固液分离得到Ⅱ段浸渣和含钒酸浸液;(3)首先将步骤(2)中的含钒酸浸液按照常规工艺依次进行萃前氧化、酸度调节和萃取,萃取的上层清液为负载有机相,下层为萃取废液,上下层分离后将负载有机相进行洗涤除杂,在常温条件下,将负载有机相加入活性硫酸盐溶液中,按照相比O/A=1~6的条件下洗涤3~15min ,洗涤完毕后得到的上层清液为载钒有机相,下层为洗涤废液,将上下层分离,即可得到载钒有机相和洗涤废液,洗涤废液按常规工艺处理后返回浸出;(4)将步骤(3)中得到的载钒有机相按照常规工艺进行反萃,反萃后得到的上层液为卸载有机相,下层液为反萃液,卸载有机相返回萃取步骤使用,反萃液按照常规工艺进行铵盐沉钒,将铵盐沉钒得到的沉淀产品按照常规工艺进行煅烧分解,最终制得的精钒产品。
2.根据权利要求1所述的含钒钢渣提钒的方法,其特征在于:所述含钒钢渣产生于含钒铁水的炼钢过程,具体成分包括V 2O 5 1~5wt%,CaO 40%~60wt%,TFe 10%~25wt%。
3.根据权利要求1所述的含钒钢渣提钒的方法,其特征在于:所述含钒钢渣破碎、磨矿后的粒度为小于74μm 的占含钒钢渣的55wt%以上。
4.根据权利要求1所述的含钒钢渣提钒的方法,其特征在于:所述含钒酸浸液在萃取之前按照常规工艺进行萃前氧化是将含钒酸浸液中的钒离子全部氧化为5价,溶液颜色从蓝绿色变成棕黄色,酸度调节是调整含钒酸浸液pH 为1.0~2.5。
5.根据权利要求1所述的含钒钢渣提钒的方法,其特征在于:所述活性硫酸盐为硫酸钠或硫酸铵,浓度为0.2~0.8mol/L 。
权 利 要 求 书CN 103131867 A一种含钒钢渣提钒的方法技术领域[0001] 本发明涉及一种含钒钢渣提钒的方法,属选矿、湿法冶金、资源综合利用领域,具体是一种常温常压下含钒钢渣不焙烧酸浸提钒的新工艺,即“含钒钢渣选矿预处理-常温常压下不焙烧选择性分段酸浸提钒”。
背景技术[0002] 含钒钢渣产生于含钒铁水的炼钢过程,有以下特点:一,它一般是废弃资源,量大价低;二,钙和铁含量高、钒含量低;三,钒的分布比其它含钒矿物要复杂得多,分散、细小、弥散于多种矿物相中。
这种既分散又细小的人造矿,属极难处理矿,难以直接选矿分离。
[0003] 从含钒钢渣中提钒主要有两类途径。
一是对钢渣进行火法冶炼,炼出高钒渣,再进一步提钒。
该法易产生磷在铁水中的循环富集,加重炼钢脱磷任务。
俄罗斯下塔吉尔钢铁联合公司对该法进行了有益探索,但未见成功报道。
攀钢在上世纪80年代以来开展了矿热炉熔炼含钒钢渣试验,取得了成功,但要完全打通流程,仍需做大量工作。
二是将钢渣作为原料直接提钒,这一般需要经过湿法冶金的过程。
传统的湿法提钒多为钠化焙烧的工艺,但该工艺污染重、回收率低,而且不适于钢渣提钒。
科研工作者还对含钒钢渣不焙烧直接酸浸提钒和钠化焙烧-碳酸化浸出提钒工艺进行过研究,钠化焙烧-碳酸化浸出工艺打通了全流程,钒总回收率为55%~60%,但该工艺物耗量大、生产成本高,仅适用于品位较高的原料;钢渣不焙烧直接酸浸提钒工艺虽有浸出率高的优点,但耗酸量太大,成本过高,在探索试验之后没有进一步研究,该工艺尚未打通。
再加上,钒、铁分离是钢渣提钒的关键,而不焙烧直接酸浸提钒,大量铁离子亦会与钒一起进入浸出液,造成浸出液难以净化,严重影响后续工艺。
现有的净化除铁方法虽多,但这些方法主要是针对溶液,却忽视了从溶液中铁杂质产生的源头即浸出工序来除铁。
如能浸出阶段实现钒、铁分离,则可在净化除杂等方面更具优势,其工艺应用前景广阔。
[0004] 还有研究致力于空白焙烧-碱浸、氧压浸出等以降低焙烧污染并提高转化率,但碱浸成本高、指标不理想,而氧压酸浸如何实现工业生产还有待进一步研究。
近30多年还出现了一些新技术,如矿浆电解、微生物浸出、选择性析出等,其原理与方法都具有普遍适用性、部分已用于钢渣提钒的研究,但技术尚不成熟,多处于实验室研究阶段。
[0005] 对于含钒钢渣的选矿预处理,目前也无成熟的工艺。
基于“含钒钢渣难以直接选矿分离”的观念,现有工艺往往首先就将“选矿技术”排除在外,殊不知提钒技术是一个大整体,很多意义不大的单元筹合起来整体意义就大了。
况且,现今提钒成本高、能耗大,最主要的原因还是钒品位太低,若能够通过初步的选矿稍稍提高钢渣中的钒品位无疑具有重要的现实意义。
[0006] 总之,现行的提钒工艺方法虽多,但普遍存在污染重、回收率低等缺点,而且难以适应含钒钢渣的特点,推广应用受到限制。
发明内容[0007] 为解决现有提钒工艺方法所存在的一些问题,如污染重、回收率低、不适于含钒钢渣特点、钒与铁难以高效分离、选矿预处理无成熟工艺等,本发明提供一种含钒钢渣提钒的方法,是清洁高效的提钒新工艺,新工艺为选冶联合工艺,完全针对了含钒钢渣的特点,取消了焙烧工序、清洁环保,并通过单一工序的科学集成,提钒指标大幅提升。
[0008] 本发明的目的是这样实现的,所述的含钒钢渣提钒的方法,主要包括选矿预处理、常温常压下不焙烧选择性分段酸浸、含钒酸浸液的净化与富集三大步骤,具体步骤包括如下:(1)将含钒钢渣破碎、磨矿后在按照常规工艺在磁场强度为0.08T~0.25T的条件下进行弱磁选,得到的磁性物质为磁性铁精矿,其余为磁选尾矿,然后将磁性铁精矿加水调整至矿浆浓度15~30wt%,在冲程6~14mm、冲次280~440r/min的条件下按照常规工艺进行重选,得到的比重大的物质为重选精矿,比重小的物质为重选尾矿;含钒钢渣破碎、磨矿至符合的细度(大于>55%-200目即可)后进行选矿预处理。
选矿预处理分两步(即弱磁选和重选),考虑到磁选设备比重选设备处理能力大,而且先选出磁性矿物后可增加不同矿物的密度差异,有利于提高选钒脱钙效果,因此按先弱磁选后重选的预处理方式进行。
钢渣中的金属铁、磁性铁等磁性较好,进入弱磁选精矿得到铁精矿,含钒矿物磁性很弱,留存于弱磁选尾矿中。
[0009] 通过弱磁选预处理,铁精矿可回收含钒钢渣中约20%的铁,从而减少铁在后续浸出液中的累积,含钒的弱磁选尾矿则进入重选预处理工序。
[0010] 根据不同矿物之间的磁性等的差别,先进行选矿预处理方式一即弱磁选,磁场强度为0.08T~0.25T,目的是尽量回收铁并减少钒的损失。
通过预处理方式一,可得到铁精矿和含钒的磁选尾矿,精矿可回收钢渣中约20%的铁,从而减少铁在后续浸出液中的累积,含钒尾矿则进入预处理方式二;工艺矿物学研究表明,含钒钢渣主要由硅酸三钙、钙钛氧化物、铁镁相、f-CaO、金属铁等组成。
其中,f-CaO不含钒、硅酸三钙含钒量低于钢渣钒品位,且f-CaO、硅酸三钙比重较小,因此,可采用重选法预先抛除掉钢渣中比重较小的f-CaO和部分解离的硅酸三钙,以为后续浸出提供便利。
[0011] 根据钢渣中主要矿物比重和粒度的差异,对弱磁选尾矿进行重选(即预处理方式二),重选可采用水力旋流器、跳汰或摇床,并分别得到重选精矿和重选尾矿,其钒在重选精矿中富集,并进入后续的浸出工序,重选尾矿抛弃处理即可;预处理方式二可抛除轻质钙等部分耗酸杂质,避免其对浸出的危害,预处理后不焙烧常温常压下直接酸浸,浸出率提高约10%、节省酸耗约15%、浸出时间缩短约1/2、过滤效率也大大提高。
[0012] 同时,通过上述的两步选矿预处理,抛掉了不含钒的金属铁、f-CaO和部分含钒较低的硅酸三钙等,预处理后钒有所富集,V2O5品位提高1%或以上,为后续湿法提钒创造了有利条件。
[0013] (2)(常温常压下不焙烧选择性分段酸浸)在常温常压条件下进行Ⅰ段预浸除杂,将步骤(1)中得到的重选精矿在硫酸溶液中按照固液比1:1~6g/ml混合并调整混合液的pH值为3~4,在搅拌强度为100~500转/min的条件下搅拌浸出0.5~6h,经固液分离得到Ⅰ段浸渣和含铁酸浸液(“铁液”);在常温常压条件下进行Ⅱ段浸出提钒,将Ⅰ段浸渣在硫酸溶液中按照固液比1:1~6g/ml混合并调整混合液的pH值为0.3~2,经固液分离得到Ⅱ段浸渣和含钒酸浸液;钒、铁分离是钢渣酸浸提钒的关键。
为在浸出阶段即实现钒与铁的分离,选矿预处理后的钢渣(即重选精矿)在常温常压下采用 “选择性分段酸浸”新方法进行浸出:钒浸出率高达95%左右。
“选择性分段酸浸”新方法,即浸出剂分段添加、浸出分两段进行,Ⅰ段预浸除杂、Ⅱ段浸出提钒,Ⅰ段、Ⅱ段浸出时的液固比控制在1:1~5:1、浸出时间不低于0.5h 、浸出剂可采用硫酸。