纱线染色
混纺纱线染色工艺
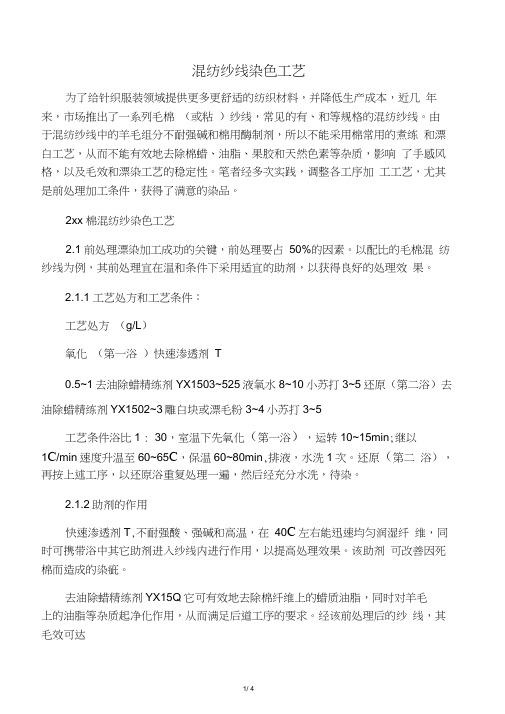
混纺纱线染色工艺为了给针织服装领域提供更多更舒适的纺织材料,并降低生产成本,近几年来,市场推出了一系列毛棉(或粘)纱线,常见的有、和等规格的混纺纱线。
由于混纺纱线中的羊毛组分不耐强碱和棉用酶制剂,所以不能采用棉常用的煮练和漂白工艺,从而不能有效地去除棉蜡、油脂、果胶和天然色素等杂质,影响了手感风格,以及毛效和漂染工艺的稳定性。
笔者经多次实践,调整各工序加工工艺,尤其是前处理加工条件,获得了满意的染品。
2xx 棉混纺纱染色工艺2.1 前处理漂染加工成功的关键,前处理要占50%的因素。
以配比的毛棉混纺纱线为例,其前处理宜在温和条件下采用适宜的助剂,以获得良好的处理效果。
2.1.1 工艺处方和工艺条件:工艺处方(g/L)氧化(第一浴)快速渗透剂T0.5~1去油除蜡精练剂YX1503~525液氧水8~10小苏打3~5还原(第二浴)去油除蜡精练剂YX1502~3雕白块或漂毛粉3~4小苏打3~5工艺条件浴比1 : 30,室温下先氧化(第一浴),运转10~15min;继以1C/min速度升温至60~65C,保温60~80min,排液,水洗1次。
还原(第二浴),再按上述工序,以还原浴重复处理一遍,然后经充分水洗,待染。
2.1.2助剂的作用快速渗透剂T,不耐强酸、强碱和高温,在40C左右能迅速均匀润湿纤维,同时可携带浴中其它助剂进入纱线内进行作用,以提高处理效果。
该助剂可改善因死棉而造成的染疵。
去油除蜡精练剂YX15Q它可有效地去除棉纤维上的蜡质油脂,同时对羊毛上的油脂等杂质起净化作用,从而满足后道工序的要求。
经该前处理后的纱线,其毛效可达12.7cM/30min 。
双氧水是氧化剂,它的加入可去除羊毛和棉纤维上的部分杂质,尤其是天然色素。
但温度不能过高,否则会引起两种纤维降解而使强力受损。
雕白块或漂毛粉是还原剂,还原性强而稳定,不仅能进一步改善两种纤维组分的白度,并且还能除去纱线上残存的氧化剂,确保纱线质量。
小苏打(碳酸氢钠)是一种极弱的碱剂,主要调节工作液的pH 值至8~8.5,因为双氧水和雕白块都需在碱性条件下发生作用,并且随碱性的增强作用加大。
腈纶纱线染色工艺与机理探究

腈纶又叫聚丙烯腈纤维,指丙烯腈质量分数大于85%的丙烯腈共聚物或均聚物纤维[1]。
由于纯聚丙烯腈纤维结构紧密、染色性差,为改善其染色性能,实际生产过程中通常采用丙烯腈和其他单体共聚的方法来生产腈纶。
在腈纶纤维中引入含有阴离子基的第三单体,使得腈纶能够采用阳离子染料染色[2-4]。
腈纶纤维具有柔软、密度小、保暖性好、不被虫蛀等优良特性,有“合成羊毛”的美称,被广泛应用于服装、装饰及针织领域,深受消费者喜爱[4-5]。
我国腈纶的产量占到了世界的近40%,市场需求量巨大[6-7]。
阳离子染料作为腈纶纤维染色的专用染料,其应用推广也随着腈纶纤维的发展而不断扩大[8]。
腈纶纱线染色工艺与机理探究摘要:使用日本化药红GRL-ED 、黄3RL-ED 、蓝GSL-ED 3只染料对腈纶纱线进行染色,利用单因素试验研究了染液pH 、染色温度、浴比对腈纶纱线染色K /S 值的影响,并分析其上染速率曲线、染色提升力和耐皂洗色牢度情况。
结果表明:当染液pH 为5、染色温度为98℃、浴比为1∶10时腈纶纱线染色的K /S 值最大,上染效果最好。
最优工艺条件下3只染料染色后的腈纶纱线均具有优异的耐皂洗色牢度。
3只染料上染腈纶纱线的上染速率曲线和提升力曲线变化趋势相近,配伍性较好,可用于拼色染色。
关键词:腈纶纱线;阳离子染料;染色工艺中图分类号:TS193.5文献标志码:A 文章编号:1005-9350(2024)03-0020-04Abstract:Three dyes,Nippon kayaku Red GRL-ED,Yellow 3RL-ED,and Blue GSL-ED,are utilized for stainingacrylic yarns.The impacts of the pH of the dyeing solution,dyeing temperature,and bath ratio on the K /S value of acrylic yarn dyeing are investigated through single-factor experiments.Besides,the dyeing rate curve,dyeing improvement force,and soap fastness are analyzed.The results demonstrate that the K /S value of acrylic yarn dyeing is the highest and thedyeing effect is the best,when pH of dyeing solution is 5,dyeing temperature is 98℃and bath ratio is 1∶10.Under the optimal process conditions,the acrylic yarn dyed with the three dyes exhibits excellent soaping fastness.The dyeing rate curve and lifting force curve of acrylic yarn dyed with these three dyes display similar trends.It indicates good compatibili⁃ty suitable for color matching dyeing.Key words:acrylic yarn;cationic dye;dyeing processResearch on the dyeing process and mechanism of acrylic yarn收稿日期:2023-06-20基金项目:山东省重点研发计划资助项目(2022ZDPT02)作者简介:陈时阳(1997—),男,硕士,主要从事绿色印染产品的开发。
色纺纱工艺流程

色纺纱工艺流程色纺纱工艺是指在纺纱过程中通过染料对纱线进行着色的工艺。
它是纺纱工艺中的一个重要环节,对于提高纱线的品质和色彩的均匀度至关重要。
下面将介绍一下色纺纱的基本工艺流程。
首先,原材料准备。
色纺纱工艺中最主要的原材料就是纱线和染料。
纱线可以由纺纱厂根据客户的要求提供,通常是由棉、毛、麻、丝等天然纤维经过清洗、梳理、精细加工等工艺得到的。
染料则可以根据不同的需要选择,常见的染料有酸性染料、中性染料和阳离子染料等。
其次,染料配方设计。
根据客户的要求和市场需求,染料师会根据染色的种类、纱线用途和颜色要求设计染料配方。
染料配方包括染料的种类、比例和添加剂的选择等。
在染料配方中,要注意控制染色过程中的温度、浴比、时间等因素,以确保染色的效果和纱线质量。
然后,染色工艺处理。
染色工艺处理是指将染料配方和纱线放入染色机中进行染色。
染色机可以根据不同的染色要求选择,常见的有梭式染色机、喷射式染色机和气流染色机等。
在染色过程中,要根据染料的特性和纱线的要求控制好温度、浴比和时间等因素,以确保染色效果的均匀和纱线质量的稳定。
接着,漂洗和水洗。
染色后的纱线要经过漂洗和水洗工艺,以去除残留的染料和添加剂,防止染料的渗透和脱色。
漂洗一般采用碱性漂洗剂,而水洗则是使用清水进行。
漂洗和水洗过程中要控制好温度和时间,以确保染色的彻底和纱线的品质。
最后,干燥和整理。
染色工艺完成后,纱线要经过干燥和整理工艺进行最后的处理。
干燥可以采用自然晾干或者机械烘干的方式,以确保纱线的干燥和收缩。
整理则是使用整理机对纱线进行整理,使其成为整齐的纱线。
整理过程中要注意控制整理机的速度和张力,以确保纱线的外观和质量。
综上所述,色纺纱工艺流程包括原材料准备、染料配方设计、染色工艺处理、漂洗和水洗、干燥和整理等环节。
每一环节都需要科学合理的操作和控制,以确保染色的效果和纱线质量的稳定。
色纺纱工艺的发展不仅提高了纱线的表面色彩效果,也提升了纱线的品质和市场竞争力。
涤纶筒子染色常见问题分析
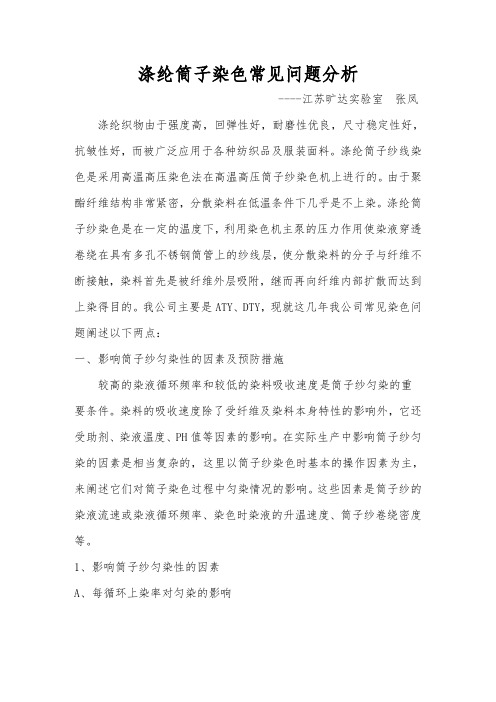
涤纶筒子染色常见问题分析----江苏旷达实验室张凤涤纶织物由于强度高,回弹性好,耐磨性优良,尺寸稳定性好,抗皱性好,而被广泛应用于各种纺织品及服装面料。
涤纶筒子纱线染色是采用高温高压染色法在高温高压筒子纱染色机上进行的。
由于聚酯纤维结构非常紧密,分散染料在低温条件下几乎是不上染。
涤纶筒子纱染色是在一定的温度下,利用染色机主泵的压力作用使染液穿透卷绕在具有多孔不锈钢筒管上的纱线层,使分散染料的分子与纤维不断接触,染料首先是被纤维外层吸附,继而再向纤维内部扩散而达到上染得目的。
我公司主要是ATY、DTY,现就这几年我公司常见染色问题阐述以下两点:一、影响筒子纱匀染性的因素及预防措施较高的染液循环频率和较低的染料吸收速度是筒子纱匀染的重要条件。
染料的吸收速度除了受纤维及染料本身特性的影响外,它还受助剂、染液温度、PH值等因素的影响。
在实际生产中影响筒子纱匀染的因素是相当复杂的,这里以筒子纱染色时基本的操作因素为主,来阐述它们对筒子染色过程中匀染情况的影响。
这些因素是筒子纱的染液流速或染液循环频率、染色时染液的升温速度、筒子纱卷绕密度等。
1、影响筒子纱匀染性的因素A、每循环上染率对匀染的影响由于纤维对染料的吸收作用,染液内染料浓度在染液流向方向上逐渐减少,引起染液流向下方纤维时染料的吸收量下降,即染料的吸尽作用。
反映染料吸尽作用最直接的指标是染液每循环一次纤维吸收染料的百分率,即每循环上染率。
每循环上染率越大,吸尽作用越强烈,所得的筒子纱匀染性越差。
B、流速对匀染程度的影响经过筒子纱的染液流速或筒子纱染色时染液的循环频率,是决定筒子纱染色质量的重要参数。
同一纤维品种用同样的染化料在相同条件下染色时,染料的最终平衡上染率是不变的,而达到匀染所需要的时间随染液流速的增加而减小。
也就是说,在相同的染色时间内,流速越高,筒子纱的匀染程度就越好;流速越低,筒子纱的匀染程度就越差;但流速过大易出现毛羽等疵病,因此,控制好流速也是非常重要的,一般是要控制在25~30 L·(min.kg)。
纱线染色市场分析报告

纱线染色市场分析报告1.引言1.1 概述纱线染色市场是纺织行业中的重要组成部分,它直接影响着纺织品的色彩和质感。
随着消费者对纺织品品质和创新设计的需求不断增加,纱线染色市场也面临着新的机遇和挑战。
本报告旨在对纱线染色市场进行全面的分析,探讨市场的概况、趋势以及竞争格局,为行业相关从业者提供决策参考。
文章结构部分的内容可以包括以下内容:1.2 文章结构:本报告分为引言、正文和结论三大部分。
在引言部分,我们将对纱线染色市场进行概述,介绍文章的结构和目的,并对市场进行总结;在正文部分,我们将分析纱线染色市场的概况、趋势和竞争格局;在结论部分,我们将对纱线染色市场的发展前景进行展望,并提出相关建议,最后进行总结。
通过本报告的结构安排,我们将全面深入地分析纱线染色市场,为读者提供全面的市场分析和发展展望。
1.3 目的目的部分的内容应该是对撰写这篇长文的目的进行阐述。
我们可以写上以下内容:目的部分旨在阐明本报告的研究目标和意义。
通过对纱线染色市场进行深入分析,我们旨在全面了解市场的现状、趋势和竞争格局,为相关行业从业者提供可靠的市场信息和发展建议,帮助他们更好地把握市场机遇,提升竞争力。
同时,本报告还将对纱线染色市场的发展前景进行展望,为行业发展提供参考,促进行业健康可持续发展。
1.4 总结总结:纱线染色市场是一个充满活力和潜力的市场,在近年来持续保持稳定增长的态势。
通过对市场概况、趋势分析以及竞争格局的分析,我们可以看出市场竞争激烈,但也存在着很大的发展空间。
随着消费者对品质和个性化的需求不断增长,纱线染色市场将面临更多的机遇和挑战。
因此,未来纺织行业需要继续加强技术研发和产品创新,以满足市场需求,促进行业健康可持续发展。
2.正文2.1 纱线染色市场概况纱线染色市场是纺织行业中的重要分支,随着人们对服装和家居用品设计的不断追求,纱线染色市场也呈现出蓬勃发展的态势。
在过去几年中,纱线染色市场规模不断扩大,市场需求稳步增长,成为纺织行业中的重要利润点。
纱线染色的6种方式
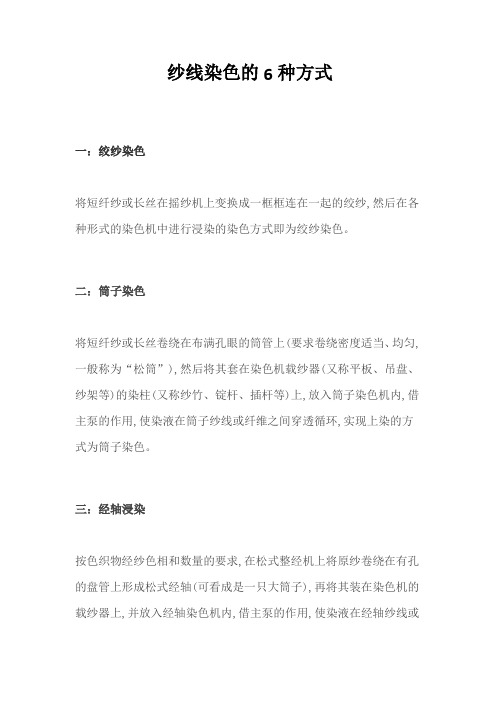
纱线染色的6种方式一:绞纱染色将短纤纱或长丝在摇纱机上变换成一框框连在一起的绞纱,然后在各种形式的染色机中进行浸染的染色方式即为绞纱染色。
二:筒子染色将短纤纱或长丝卷绕在布满孔眼的筒管上(要求卷绕密度适当、均匀,一般称为“松筒”),然后将其套在染色机载纱器(又称平板、吊盘、纱架等)的染柱(又称纱竹、锭杆、插杆等)上,放入筒子染色机内,借主泵的作用,使染液在筒子纱线或纤维之间穿透循环,实现上染的方式为筒子染色。
三:经轴浸染按色织物经纱色相和数量的要求,在松式整经机上将原纱卷绕在有孔的盘管上形成松式经轴(可看成是一只大筒子),再将其装在染色机的载纱器上,并放入经轴染色机内,借主泵的作用,使染液在经轴纱线或纤维之间穿透循环,实现浸染,以得到色泽均一的经纱的方法叫作经轴染色。
四:经轴轧染经轴轧染主要应用在色经白纬的牛仔布的生产加工中。
它是将一定数量的稀轴引入各个染槽,经反复多浸、多轧、多次透风氧化后,实现靛蓝(或硫化、还原、直接、涂料)染料的染色。
预烘干后再进行浆纱,便可得到色泽均一的经轴纱,可直接供织造使用。
经轴轧染时的染槽可以是多个(片状机)或一个(环状机),这种与浆纱联合使用的设备被称为片状染浆联合机。
五:纱束轧染(球经染色)这也是牛仔布经纱的特殊染色方法,其染色过程是先将400~500根原纱集束呈球状,然后再将若干束(如12束、18束、24束、36束)纱线在多个染槽中反复多浸、多轧、多次透风氧化,实现靛蓝染料染色后,再分经、浆纱。
腈纶丝束也可以进行纱束轧染。
六:纱线特殊染色方法如同织物一样,纱线也有局部染色,如印节、段染、扎染、印花、拔染、渐变等。
1,印节按设计要求,在铺开的绞纱上每隔设定距离印上一小节(如0.5~1cm)颜色,可以是相同色彩,但大部分为五彩色。
必须注意,其间距必须是无规律的不等距,否则布面上会出现“龟背”或“山水画”。
2,段染将若干染料同时淋滴在铺开的绞纱的不同部位,经真空吸液或轧液后,再固色、洗净。
纱线特殊染色方法的介绍
纱线特殊染色方法的介绍纱线特殊染色方法的介绍纱线是一种常见的纺织材料,用于制作各种织物。
为了使纱线更加丰富多样,人们发展出了一些特殊的染色方法。
这些方法可以在纱线中添加各种颜色和效果,使其具有独特的视觉效果和质感。
以下是几种常见的纱线特殊染色方法的介绍。
1. 手染:手染是最基本的染色方法之一,也是最常见的。
它通常在家庭或小型工作室中进行。
手染时,将纱线浸泡在染料中,然后用手搓揉或拍打纱线,使染料均匀渗透到整根纱线中。
手染可以使用单一颜色的染料,也可以混合多种颜色来创建独特的效果。
2. 细节染色:细节染色是一种将染料应用于纱线的特定区域的方法。
这种方法通常使用刷子、海绵或喷雾器来精确地涂抹染料。
通过细节染色,可以在纱线上创建花纹、图案或渐变效果。
3. 双色渐变:双色渐变是一种将两种不同颜色的染料应用到纱线上,使它们渐变过渡的方法。
这种方法通常使用两个不同颜色的染料盘或容器。
将纱线一端浸泡在第一个染料中,然后逐渐将其移到第二个染料中,使两种颜色渐变地结合在一起。
4. 扎染:扎染是一种通过将纱线绑紧,使染料只能渗透到某些部分的方法。
这种方法可以使用橡皮筋、绳子或线将纱线捆绑成不同的形状,然后将其浸泡在染料中。
当纱线解开时,染料只会在未被绑紧的部分渗透,从而创造出独特的纹理和图案。
5. 水染:水染是一种在水中浸泡纱线,使染料均匀分散的方法。
这种方法通常使用水溶性染料,纱线在浸泡过程中,染料会在水中均匀分散,并渗透到纱线中。
水染可以创建出柔和、温和的颜色效果。
以上是几种常见的纱线特殊染色方法的介绍。
这些方法不仅可以为纱线增添丰富的颜色和效果,还可以创造出独特的纹理和图案,使纺织品更加吸引人。
无论是手工爱好者还是纺织品设计师,都可以根据自己的需要和创意,选择适合的染色方法来打造独特的纱线作品。
纱线印染工艺流程
纱线印染工艺流程
纱线印染工艺流程主要包括以下几个步骤:
1. 前处理:纱线首先经历清洗去杂,去除天然油脂、杂质和残留的纺丝助剂,提高其吸湿性与亲和力,确保后续染色均匀;
2. 染色准备:根据设计颜色调配染料配方,进行染液的制备;
3. 纱线染色:将预处理过的纱线浸入染液中,通过精确控制温度、时间和pH值等条件,促使染料与纤维发生化学键合,实现染料的固着;
4. 后处理:染色后的纱线经过清洗以去除浮色,接着进行皂洗、酸洗、还原清洗等步骤,确保染色牢度和色泽纯正;
5. 干燥与整理:纱线经过脱水、烘干处理,并根据需要进行上油、柔软整理等工序,提高纱线的手感和后续加工性能;
6. 检验与包装:最后对染色成品进行质量检测,包括色牢度、强度等物理指标,确认合格后进行分类、卷绕和包装入库。
合成纤维长丝纱线的吸湿性性能与染色性能的关系
合成纤维长丝纱线的吸湿性性能与染色性能的关系合成纤维长丝纱线的吸湿性能与染色性能的关系合成纤维长丝纱线作为一种常见的纺织原料,其吸湿性能和染色性能对于纺织品的品质和性能具有重要影响。
本文旨在研究合成纤维长丝纱线的吸湿性能与染色性能之间的关系,探讨不同因素对其性能的影响,并为纺织行业提供技术支持。
首先,合成纤维长丝纱线的吸湿性能是指其吸湿性的能力。
吸湿性能的好坏直接影响纺织品的舒适性和透气性。
合成纤维的吸湿性受到纤维本身结构的影响,以及纺纱过程和后续处理的影响。
纤维的吸湿性能主要与其化学结构和表面形态有关。
一般来说,具有羟基、氨基等基团的纤维具有较好的吸湿性能。
在纺纱过程中,纺丝液中加入适量的吸湿剂可以改善合成纤维的吸湿性能。
吸湿剂可以增加纺丝液的溶解度,提高纤维的拉伸性能和机械性能。
同时,在纤维的后续处理过程中,采用适当的处理方法也可以改善纤维的吸湿性能。
例如,经过特殊处理的纺织品表面会形成微细凸起的纤维结构,有助于增强纤维的吸湿性能。
其次,合成纤维长丝纱线的染色性能是指其接受染料的能力。
染色性能的好坏直接影响纺织品的色牢度和色彩效果。
合成纤维的染色性能主要与其化学结构和纺纱工艺有关。
一方面,纤维的聚合度、形态特征和分子结构会影响染料分子与纤维之间的相互作用,从而影响染色效果。
另一方面,纺织品中添加的染料助剂和染色剂的选择和使用方法也会对染色性能产生重要影响。
在合成纤维的制备和加工过程中,通过控制纺丝液的成分和添加助剂,可以调节纤维的染色性能。
例如,适当选择染料分子与纤维之间相互作用力较强的染料助剂,可以提高染料在纤维上的附着力,从而提高染色的牢度。
此外,合成纤维的表面处理也可以提高其接受染料的能力。
常见的表面处理方法包括接枝聚合、等离子体处理等。
综上所述,合成纤维长丝纱线的吸湿性能和染色性能直接影响纺织品的品质和性能。
通过对纤维结构的调控、纺纱工艺的改进以及后续处理方法的选择,可以改善纤维的吸湿性能和染色性能。
纱线后处理要求
纱线后处理要求纱线后处理是指在纱线生产过程中,对纱线进行一系列的加工和处理,以使纱线具有更好的质量和性能。
纱线后处理的要求非常重要,它直接影响到纱线的品质和使用效果。
下面将详细介绍纱线后处理的要求。
纱线后处理要求在不输出http地址的情况下进行。
这是因为纱线后处理的要求通常是属于企业的内部流程和控制标准,不需要向外界公开。
因此,在文章中不会提及具体的http地址。
纱线后处理的要求不包括公式。
纱线后处理的要求主要是一些实际操作和处理步骤,不涉及具体的公式计算。
因此,在文章中不会出现公式的描述。
纱线后处理的要求包括以下几个方面。
首先是纱线的清洗要求。
纱线在生产过程中会受到环境、机器和人员等多种因素的污染,因此需要进行清洗。
清洗要求包括清洗剂的选择、清洗时间和温度的控制,以及清洗后的干燥处理。
其次是纱线的染色要求。
染色是纱线后处理中非常重要的一环。
染色要求包括染料的选择、染色剂的浓度和温度的控制,以及染色后的固色处理。
染色的要求直接影响到纱线的色彩鲜艳度和牢固度。
纱线后处理还包括纱线的整理要求。
整理是指对纱线进行整齐、平整和光滑的处理,以便于后续的加工和使用。
整理要求包括纱线的整型、张力的控制和卷绕的要求。
纱线后处理还需要考虑纱线的增强要求。
纱线的增强是指对纱线进行强化处理,以提高纱线的强度和耐磨性。
增强要求包括增强剂的选择、增强时间和温度的控制,以及增强后的干燥处理。
纱线后处理还需要考虑纱线的包装要求。
包装是指将处理好的纱线进行包装,以便于运输和销售。
包装要求包括包装材料的选择、包装形式的确定,以及包装后的标识和质量检验。
纱线后处理的要求是非常重要的,它直接关系到纱线的质量和性能。
纱线后处理的要求包括清洗、染色、整理、增强和包装等方面。
在进行纱线后处理时,需要注意控制各个环节的参数和操作,以确保纱线的质量和性能符合要求。
- 1、下载文档前请自行甄别文档内容的完整性,平台不提供额外的编辑、内容补充、找答案等附加服务。
- 2、"仅部分预览"的文档,不可在线预览部分如存在完整性等问题,可反馈申请退款(可完整预览的文档不适用该条件!)。
- 3、如文档侵犯您的权益,请联系客服反馈,我们会尽快为您处理(人工客服工作时间:9:00-18:30)。
纱线染色一、纱线染色特点在纺织品的生产过程中,染色在哪个阶段进行,受若干因素的影响。
从经济角度来看,染色在织造生产工序的前道进行,其成本是最低的。
在织造前道工序进行纱线染色,可选用坚牢度较好的染料,某些色花可以在后续织造工序中得到改善。
纱线染色一般能获得良好坚牢的匀染效果,可与本色纱线按不同设计要求织造,从而获得较高经济价值,并可缩短交货周期,所以产品具有高的重现性。
通常认为,纱线染色所得产品与织物染色所得产品相比,更具有膨松和手感丰满等优点,这可能是因为当绞纱悬于染色机的杆上时,可以自由地充分松弛而不受任何限制,不仅可以让纱线完全膨松化,而且还可以让纱线自由退捻达到捻度均衡,从而消除纺纱时的张力。
纱线染色的另一种形式是筒子纱染色,从技术上讲,过去认为只有采用绞纱染色法进行染色才能生产出满意产品,但这种传统看法随着筒子纱染色法的出现正在逐渐改变。
一般说,纱线染色比织物染色成本要高。
但由于它具有交货快的优点,因而更容易适应流行色的变化,同时适应小批量、多品种的需要。
此外,纱线染色机械较为简单,从而在维修保养方面较为经济。
二、还原染料纱线染色还原染料是当前色织物纯棉纱线染色的一个主要大类品种。
染色后的纱线不仅色泽鲜艳,而且坚牢度十分优良,大多数日晒牢度均在6级以上,部分品种高达8级。
因此凡需要整理如煮练、漂白、丝光和热定形的色织布,都可用还原染料染色。
还原染料的品种很多,但按其化学结构可分为靛类和蒽醌类,纱线染色所用的还原染料,多以蒽醌型为主。
(一)染色基本方法蒽醌型结构的还原染料,它的隐色体钠盐易被棉纱所吸附,上染速率快,因此匀染性较差,染浴所需烧碱、保险粉量也较高。
在纱线染色过程中,1g蒽醌型还原染料在染浴中常需消耗烧碱和保险粉5~6g,此外染浴中还需要骨胶、平平加0等缓染剂,以降低染料的上染速率,有利于染液向纤维内部扩散,并提高其匀染效果,用量以0.2~0.5g/L为好。
在日常染色中染纱时间一般为15~2Omin,为改进色纱的匀染性和染色牢度,可适当延长染色时间至20~3Omin较为合理。
对少量需在较低温度下染色的还原染料,其隐色体钠盐被纱线吸附后,在空气中不易氧化,可选择适当的氧化方法和氧化剂,促进染料隐色体的转化、发色,然后用水洗涤或稀酸液处理,以去除残余碱剂和杂质,最后进行皂洗和水洗,完成纱线染色。
由于不同的还原染料具有不同的染色性能,故在纱线染色时,可根据其所需烧碱、保险粉、助剂的用量及染色温度、时间等条件的差别,选择适当的还原方式和染色方法。
(二)染色工艺和操作1.手工纱线染色白纱下缸后需连续提纱倒头7~9次(约5min),但间隔要求均匀一致。
2.往复式染纱机染色下缸时由两人依次抬纱,机器应处于只摆不转的状态,待白纱全部被染液浸透(相当于往复摆动3次的时间)才能使纱杆滚转。
有些匀染性要求高的和丝光纱线,还需在白纱下缸时结合手工操作,将纱左右摆动,并使其连续倒顺滚转4~5min,然后停止运转,但摆动仍需继续进行,以后每隔1min掉向、倒头一次。
染色1Omin后,每2~3min再转向倒头一次,倒头时必须使露出液面约1/3的色纱重新被浸没于染液内,防止产生深浅段头色花。
3.高温高压染纱机染色筒子纱染色可按正反方向由循环泵推动染液,每隔规定时间变换流向一次,先由中心向四周喷液(即正循环),时间为0.5~1.5min,再由四周向中心喷液(即反循环),时间为4.5~3.5min。
若是绞纱染色,则可始终采用正向循环液流染色,不适宜于表2-9 还原染料纱线染色工艺处方及条件反向循环,染液如由周围向中心循环时,势必造成绞纱上层密度越来越小,而下层密度则越来越大,形成液流短路,从而出现纱芯染色不透生成白芯、白斑和浅斑。
表2-9为还原染料纱线染色工艺。
在进行纱线染色前,应先对白纱质量进行检验,要求白纱外观洁净无斑渍,呈中性,堆放时间不得超过8h,并用湿布盖好。
在纱线染色装机时,应根据不同染纱设备按要求装填,防止因纱线装填不当所产生的染色疵病。
三、硫化染料纱线染色色织棉布深色品种如劳动布、元贡等所用的色纱,大都采用硫化染料染色。
硫化染料价格便宜,染色后的色泽丰满,水洗牢度较好,是纱线染色的常用染料之一。
硫化染料因其分子结构中含有较多的硫元素不溶于水,染色时必须借硫化钠还原溶解。
近年来又有水溶性硫化染料和防脆损硫化黑等出现,使硫化染料的应用又有了新的前景。
(一)染色工艺要点纱线的染前处理是保证纱线染色质量的关键。
硫化染料的染色有无光和丝光之分,个别染浅色的纱线还需经过漂白。
如果煮练不良,纱线毛效就差,或者丝光碱液浓度高低不一,漂白纱含氯较多等均会直接影响到染色质量。
因此染前必须对白纱进行认真检查,要求白度均匀,不能有黄斑、黑斑、碱斑、锈斑、污渍以及含氯等。
脱水后的白纱必须用湿布遮盖,防止表面风干,对于堆放过久的白纱,染前必须再经一次水洗,否则染后会产生局部白条或浅条色疵。
对于不经碱煮而仅用清水煮练的无光纱,因棉脂、蜡脂尚未去尽,堆放时间切忌过长,尤其在高温季节容易变质,染前需重新用80~70℃热纯碱液处理,严重的尚需酸洗,否则染色纱线易出现色泽浅而发白的现象。
由于硫化染料上染缓慢,故适宜采用高温染色,既有利于染料颗粒不断溶化变细,快速向纤维内层渗透和扩散,又可使纤维纱线受热膨化疏松,获得较好的匀染效果。
一般硫化染料的染色温度大致为75~80℃,手工染纱高温不便操作,温度控制在60~70℃。
温度过低,会影响染料的上染,得色变浅,并且使残液内染料浓度渐次递升,产生缸与缸之间的色差。
但也有部分染料适宜于低温染色,温度过高反而得色较浅,这主要是由于温度升高后使染料对纤维的直接性降低的缘故。
一般浅色纱线多采用低温染色,如劳动布的纬线染硫化漂灰等可在室温染色。
除此之外,染色温度与棉纱的丝光、无光,染纱机械等都有密切关系,一般无光纱染色温度高,而丝光纱较低。
高温高压染纱有密闭装置,染色温度可提高到100℃以上,而往复式染纱机若温度过高,易使纱线上浮,造成乱纱、断纱,故染色温度大都在70~80℃。
当硫化染料染深色时,由于染浴内染料浓度高,氧化速率快,染色后,纱线上未固着的染料和空气接触产生色淀而被吸附在色纱表面,容易造成红条、金铜色等疵病,使染色牢度下降。
为获得较好的匀染效果及染色牢度,一般的染色方法是将从染浴中取出的纱线立即再次浸入另一还原液中进行重新还原,逐步降低色纱本身的温度和被吸附的染液浓度,延缓氧化速率,达到色泽均匀、质量稳定,或通过还原液除去一部分色纱表面的浮色,这种工艺常称为闷缸。
用硫化染料染棉纱时,常用隐色体染色法,其中又以黑色和藏青色为最多,上染率一般为25%~30%,因此残留在染浴中的染料较多,故硫化染料染色后的残液通常被连续使用。
头缸染料投入量与续缸染料的补充量两者之间的比例,常称为头缸染料的加成数,如果加成数不对,就会影响头缸与续缸的得色深浅。
染浅色纱线时,头缸加成数可适当减少,而染深色纱线时应增加。
当上染率为25.4%时,头缸染料的加成数约为续缸染料的组2.5~4倍。
影响硫化染料染色的因素较多,除染料与硫化碱用量外,纱线的配棉、煮练质量、水质硬度、硫化碱含量等都直接影响纱线的上染率。
表2-10 丝光纱染色硫化黑处方(二)硫化染料染色工艺举例表2-10为在往复式染纱机上丝光纱染硫化黑色,纱重25kg,浴比1:40。
工艺流程:清水煮练(1OO℃,3h)→丝光(烧碱280Be)→中和(98%硫酸2.5~3g/L)→温水(40~50℃)→脱水→绷纱(绷松、绷直)→串杆→染色(70~75℃,20min)→温缸(35~40℃,5min)→水洗(冷洗,流动)→沥干→防脆处理(25~30℃,1Omin)→出缸→包布→脱水→绷烘。
四、不溶性偶氮染料染色不溶性偶氮染料是棉纱染色中常用的染料,多用于染制深浓色的大红、枣、酱、蓝、黄、棕、黑等色。
它以价格便宜、成本低廉、色泽鲜艳著称,但是摩擦牢度差,气候牢度也不够理想。
采用不溶性偶氮染料染棉纱时,首先将棉纱放在色酚类的钠盐溶液处理,使纤维吸收一定量的色酚钠盐,即打底。
然后再与胺类的重氮化合物或稳定的重氮盐溶液偶合,即显色,显色时打底剂与重氮化的显色基通过偶合直接在纤维上生成不溶性的偶氮染料。
这类染料染深色时日晒牢度好,染浅色时日晒牢度差,而且相差较大,故一般这类染料不宜染浅色。
(一)打底剂及其工艺由于打底剂结构的差异,使它对纤维的结合能力不同,一般可用两种方法来表示打底剂对纤维结合能力的大小。
一种是用吸收量表示,即每公斤棉纱于某一浓度的打底剂溶液中浸染时所吸收打底剂的克数;另一种是用吸收率表示,即被棉纱吸收的打底剂量与投入染浴的打底剂总量之比的百分数。
一般认为,棉纱对打底剂的吸收率越高,打底后残浴的浓度就越低,棉纱线上的浮色也越少。
因此,选用吸收率较高的打底剂,染后色纱上的浮色就少,摩擦和湿处理牢度也就较高。
影响棉纱对打底剂吸收率的因素很多,主要包括电解质含量、打底浴比、温度等。
此外,棉纱的前处理性能和丝光效果均对吸收率有影响。
值得注意的是棉纱线的品种、细度、捻度等对打底剂的吸收率也有一定的影响,在生产过程中应充分重视。
打底剂的溶解是在氢氧化钠存在下进行的,其溶解方法有热溶法和冷溶法两种,多以热溶法为主,所选用的色酚偶合能力应比较强。
实际生产中,若用无光纱打底,多数选用热溶法溶解打底,深度是以每公斤棉纱吸收打底剂的量来表示,6g以下为浅色,6~12g为中色,12g以上为深色,可加入食盐促染。
为提高打底液的稳定性,还可加入甲醛,续缸使用时也可加入食盐和甲醛,但打底液温度不能超过50℃,否则色酚的羟甲基化合物产生缩合而影晌其上染能力。
棉纱线的打底大都在往复式、喷射式染纱机上进行。
打底后的纱线用离心机脱水,脱水纱线的含液率按染色深浅严格控制,染中色或深色宜在70%以下,浅色纱的含水率为100%~120%。
在进行纱线打底时,所需时间控制在15~20min,以利于提高产量。
打底温度一般采用30~40℃,未经煮练的棉纱,打底温度可适当提高。
浴比以1:20为好,过小使打底操作不便,同时亦易造成打底不匀,浴比过大,造成打底剂浪费。
打底后纱线经脱水应立即进行显色,并应注意避免接触水滴、水蒸气、汗滴、酸气、氯气以及风吹和日光照射,以免影响染色质量。
1.打底工艺流程(往复式染纱机)白纱→串杆→打底→包布→脱水→绷纱、串杆。
2.打底工艺处方和条件打底棉纱线(无光)1小包(5kg)打底液浓度3g/L(不加食盐)脱水后含液率65%(脱水残液全部回收)打底温度30℃,打底时间3Omin,打底浴比1:20(浴量100L)。
(二)显色剂及其偶合反应显色剂包括色基和色盐两种,其中色盐可直接溶解于水而与纱线偶合显色,但色基的溶解性极差,并且本身与打底剂无偶合能力,需经重氮化反应后,在一定pH值下才能与打底剂偶合显色。