电 镀 标 准
电镀件外观检验标准
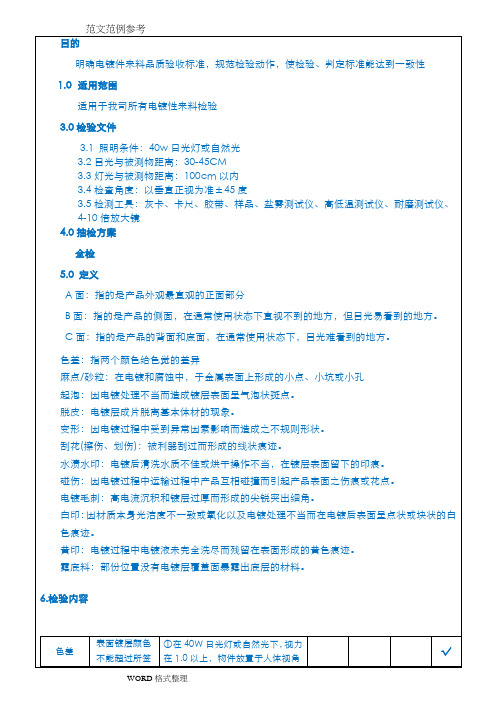
黄印:电镀过程中电镀液未完全洗尽而残留在表面形成的黄色痕迹。
露底料:部份位置没有电镀层覆盖面暴露出底层的材料。
6.检验内容
色差
表面镀层颜色不能超过所签样品0.5级
在40W日光灯或自然光下,视力在1.0以上,物件放置于人体视角45度处,无明显色异。
8不可接受b级面及边角碰伤面积1mm边角碰变形bc级面其组装后不影响产品的整体外观边角碰变形其组装后影响整体外观物体外表碰伤bc级面其凹凸痕面积5mm?深度高05mm不刮手物体外表碰伤bc级面其凹凸痕面积5mm?深度高05mm刮手抛光砂痕电镀件外表处理后不能有明显的砂痕外表抛光粗糙在30cm远的距离视力10以上在自然光或40w日光灯下与人视线水平位观察无明显砂痕外表抛光粗糙经电镀后仍不能遮掩不可接受电镀生锈电镀件内外外表不能有生锈氧化现象电镀件外外表生锈不可接受盐雾测试8小时不能腐蚀到镀层外表叻架层可节受有腐蚀水渍水印
√
不可擦拭
√
B,C级面,水渍水印、白印、黄印面积≦10mm²,且周边印痕30cm处观察不明显
√
不可擦拭
√
电镀毛刺
电镀件表面不能有毛刺
电镀件外表面不能有毛刺
√
露底材
表面不允许有镀层露底料的情况
电镀件表面不允许有镀层露底料的现象
√
电镀件电极点周围未镀上的痕迹,其大小在组装后可遮盖或其内部在组装后在不拆卸的情况下,看不见为准。
√
不可擦拭污渍面积0.5mm≦X≦1mm,A级面:不可接受
√
B级面,在10 mm内,只能有1处
√
C级面,在10 mm内,只能有2处
√
物件表面残留有不可辨别的污物,液体、血液等,不可接受。
电镀质检标准
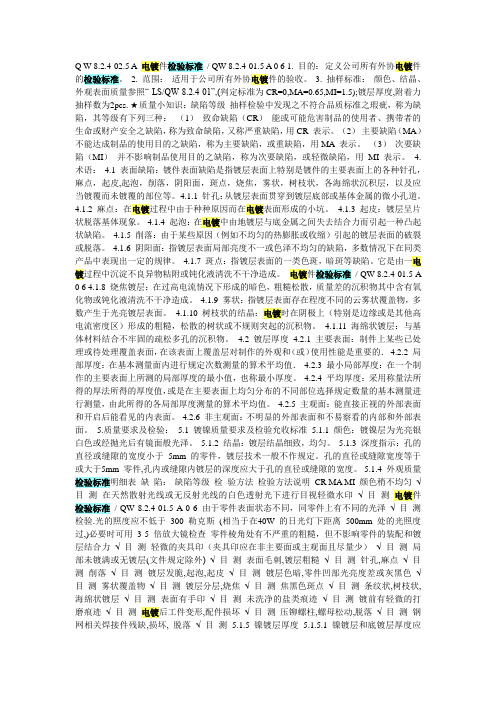
Q W 8.2.4-02.5 A 电镀件检验标准/ QW 8.2.4-01.5 A 0 6 1. 目的:定义公司所有外协电镀件的检验标准。
2. 范围:适用于公司所有外协电镀件的验收。
3. 抽样标准:颜色、结晶、外观表面质量参照“ LS/QW 8.2.4-01”,(判定标准为CR=0,MA=0.65,MI=1.5);镀层厚度,附着力抽样数为2pcs. ★质量小知识:缺陷等级抽样检验中发现之不符合品质标准之瑕疵,称为缺陷,其等级有下列三种:(1)致命缺陷(CR)能或可能危害制品的使用者、携带者的生命或财产安全之缺陷,称为致命缺陷,又称严重缺陷,用CR 表示。
(2)主要缺陷(MA)不能达成制品的使用目的之缺陷,称为主要缺陷,或重缺陷,用MA 表示。
(3)次要缺陷(MI)并不影响制品使用目的之缺陷,称为次要缺陷,或轻微缺陷,用MI 表示。
4.术语:4.1 表面缺陷:镀件表面缺陷是指镀层表面上特别是镀件的主要表面上的各种针孔,麻点,起皮,起泡,削落,阴阳面,斑点,烧焦,雾状,树枝状,各海绵状沉积层,以及应当镀覆而未镀覆的部位等。
4.1.1 针孔:从镀层表面贯穿到镀层底部或基体金属的微小孔道。
4.1.2 麻点:在电镀过程中由于种种原因而在电镀表面形成的小坑。
4.1.3 起皮:镀层呈片状脱落基体现象。
4.1.4 起泡:在电镀中由地镀层与底金属之间失去结合力而引起一种凸起状缺陷。
4.1.5 削落:由于某些原因(例如不均匀的热膨胀或收缩)引起的镀层表面的破裂或脱落。
4.1.6 阴阳面:指镀层表面局部亮度不一或色泽不均匀的缺陷,多数情况下在同类产品中表现出一定的规律。
4.1.7 斑点:指镀层表面的一类色斑,暗斑等缺陷。
它是由一电镀过程中沉淀不良异物粘附或钝化液清洗不干净造成。
电镀件检验标准/ QW 8.2.4-01.5 A 0 6 4.1.8 烧焦镀层:在过高电流情况下形成的暗色,粗糙松散,质量差的沉积物其中含有氧化物或钝化液清洗不干净造成。
塑胶材料表面电镀检验标准
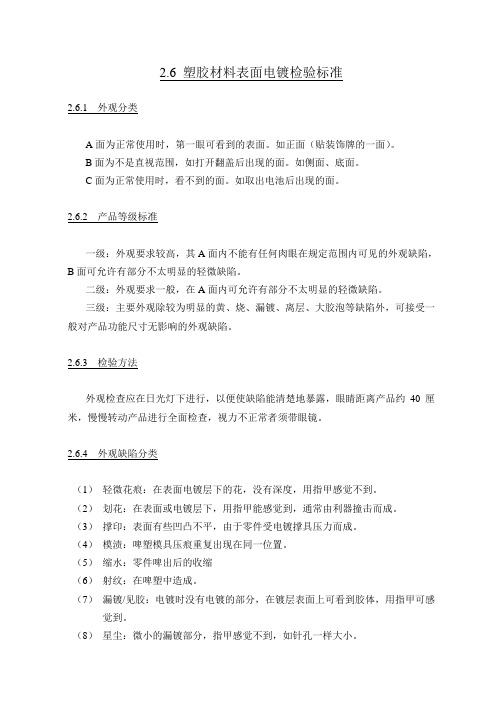
2.6 塑胶材料表面电镀检验标准2.6.1 外观分类A面为正常使用时,第一眼可看到的表面。
如正面(贴装饰牌的一面)。
B面为不是直视范围,如打开翻盖后出现的面。
如侧面、底面。
C面为正常使用时,看不到的面。
如取出电池后出现的面。
2.6.2 产品等级标准一级:外观要求较高,其A面内不能有任何肉眼在规定范围内可见的外观缺陷,B面可允许有部分不太明显的轻微缺陷。
二级:外观要求一般,在A面内可允许有部分不太明显的轻微缺陷。
三级:主要外观除较为明显的黄、烧、漏镀、离层、大胶泡等缺陷外,可接受一般对产品功能尺寸无影响的外观缺陷。
2.6.3 检验方法外观检查应在日光灯下进行,以便使缺陷能清楚地暴露,眼睛距离产品约40厘米,慢慢转动产品进行全面检查,视力不正常者须带眼镜。
2.6.4 外观缺陷分类(1)轻微花痕:在表面电镀层下的花,没有深度,用指甲感觉不到。
(2)划花:在表面或电镀层下,用指甲能感觉到,通常由利器撞击而成。
(3)撑印:表面有些凹凸不平,由于零件受电镀撑具压力而成。
(4)模渍:啤塑模具压痕重复出现在同一位置。
(5)缩水:零件啤出后的收缩(6)射纹:在啤塑中造成。
(7)漏镀/见胶:电镀时没有电镀的部分,在镀层表面上可看到胶体,用指甲可感觉到。
(8)星尘:微小的漏镀部分,指甲感觉不到,如针孔一样大小。
(9)黄(无铬层):没电上铬,淡黄色的镍层暴露,通常发生在产品边缘或孔四周。
(10)电镀不良:电镀面很粗糙,指甲能感觉到。
(11)压力纹:贯穿零件表面,通常从零件某角落或边缘处开始。
(12)地图纹:从电镀件表面看,不规则,不平滑,指甲感觉不到,通常由光剂不平引致。
(13)电镀泡:在电镀层里有空气或聚集了电镀液。
(14)离层:电镀层与零件间的附着力不够,镀层脱落。
(15)烧:电流过大等引致在镀件尾端或边缘附近镀层色泽阴暗或灰白。
(16)毛刺:电镀时在高电流密度区镀层的过高堆积,过高的电流密度产生了粗糙(毛刺)。
(17)云雾状:由于电镀条件的变化,电镀件表面缺少光泽。
塑胶材料表面电镀检验标准

德信诚培训网
更多免费资料下载请进: 好好学习社区
塑胶材料表面电镀检验标准
1 外观分类
A 面为正常使用时,第一眼可看到的表面。
如正面(贴装饰牌的一面)。
B 面为不是直视范围,如打开翻盖后出现的面。
如侧面、底面。
C 面为正常使用时,看不到的面。
如取出电池后出现的面。
2 产品等级标准
一级:外观要求较高,其A 面内不能有任何肉眼在规定范围内可见的外观缺陷,B 面可允许有部分不太明显的轻微缺陷。
二级:外观要求一般,在A 面内可允许有部分不太明显的轻微缺陷。
三级:主要外观除较为明显的黄、烧、漏镀、离层、大胶泡等缺陷外,可接受一般对产品功能尺寸无影响的外观缺陷。
3 检验方法
外观检查应在日光灯下进行,以便使缺陷能清楚地暴露,眼睛距离产品约40厘米,慢慢转动产品进行全面检查,视力不正常者须带眼镜。
4 外观缺陷分类
(1) 轻微花痕:在表面电镀层下的花,没有深度,用指甲感觉不到。
(2) 划花:在表面或电镀层下,用指甲能感觉到,通常由利器撞击而成。
(3) 撑印:表面有些凹凸不平,由于零件受电镀撑具压力而成。
(4) 模渍:啤塑模具压痕重复出现在同一位置。
(5) 缩水:零件啤出后的收缩
(6) 射纹:在啤塑中造成。
(7) 漏镀/见胶:电镀时没有电镀的部分,在镀层表面上可看到胶体,用指甲可感觉到。
(8) 星尘:微小的漏镀部分,指甲感觉不到,如针孔一样大小。
(9) 黄(无铬层):没电上铬,淡黄色的镍层暴露,通常发生在产品边缘或孔四周。
(10)电镀不良:电镀面很粗糙,指甲能感觉到。
解读国家标准GB21900-2008《电镀污染物排放标准》
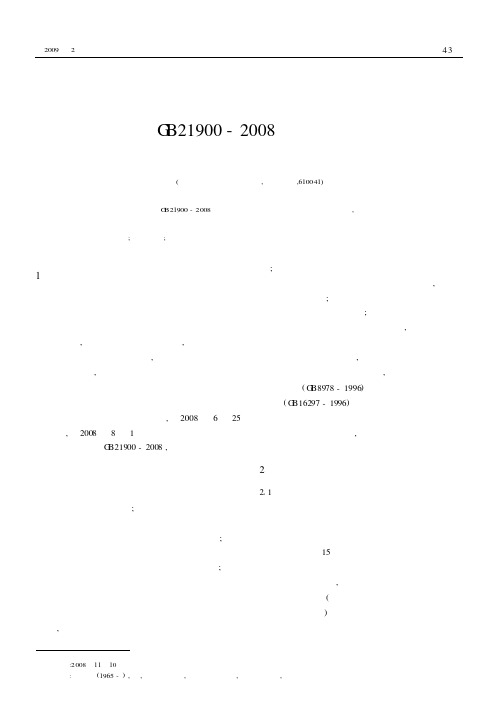
涂 装 与 电 镀
43
标准化
解 读 国 家 标 准 GB21900 - 2008《 电 镀 污 染 物 排 放 标 准 》
黄大江 (兴达表面技术信息公司 ,四川成都 ,610041)
摘 要 本文介绍了国家标准 GB21900 - 2008《电镀污 染物排放 标准》的主 要技术 内容 ,分析了 该标准的 特点及 与 相关标准的关系 。 关键词 电镀污染物 ;国家标准 ;标准分析
大气污染物排放浓度限值适用于单位产品实际 排气量不高于单位产品基准排气量的情况。若单位 产品实际排气量超过单位产品基准排气量 ,须将实
测大气污染物浓度换算为大气污染物基准气量排放 浓度 ,并以大气污染物基准气量排放浓度作为判定 排放是否达标的依据。大气污染物基准气量排放浓 度的换算 ,可参照采用水污染物基准水量排放浓度 的计算公式。
力为 101325Pa (即 1 标准大气压 ,760mmHg 柱) 时的
状态。标准规定的大气污染物排放浓度均以标准状
态下的干气体为基准 。
212 水污染物排放控制要求
水污染物排放限值见表 1。
现有 企业 ( 即标 准实 施之 前已 有的 企业) , 自
2009 年 1 月 1 日至 2010 年 6 月 30 日执行表 1 中现
车间或生产设 施废水排放口
8
总 铜 ,mg/ L
110 015
013
企业废水总排 放口
9
总 锌 ,mg/ L
210 115
110
企业废水总排 放口
10
总 铁 ,mg/ L
510 310
210
企业废水总排 放口
11
总 铝 ,mg/ L
五金电镀件检验标准

五金电镀件检验标准五金电镀件是一种常见的金属表面处理工艺,通过电化学方法在金属表面镀上一层金属或非金属的薄层,以改善其外观和性能。
在工业生产中,五金电镀件广泛应用于汽车、家电、机械设备等领域。
为了确保五金电镀件的质量,制定了一系列的检验标准,以保证产品的稳定性和可靠性。
首先,五金电镀件的外观检验是非常重要的一项内容。
外观检验主要包括表面光洁度、镀层附着力、镀层厚度等指标。
表面光洁度是指镀件表面的光泽度和平整度,应满足相关标准规定的要求。
镀层附着力是指镀层与基材之间的结合力,通常采用划格法或剥离试验来进行检验。
镀层厚度是指镀层的厚度,通常采用磁感应法或X射线荧光法来进行测量。
这些外观检验指标的合格与否直接影响着五金电镀件的质量和使用寿命。
其次,五金电镀件的耐蚀性检验也是至关重要的。
耐蚀性是指五金电镀件在不同环境条件下的抗腐蚀能力,通常包括盐雾试验、湿热试验、酸碱盐溶液腐蚀试验等。
盐雾试验是模拟海洋气候条件下的腐蚀环境,通过在盐雾箱中进行连续喷雾测试,来评定五金电镀件的耐蚀性能。
湿热试验是模拟高温高湿条件下的腐蚀环境,通过在恒温恒湿箱中进行连续测试,来评定五金电镀件在潮湿环境下的抗腐蚀能力。
酸碱盐溶液腐蚀试验是模拟酸碱盐溶液中的腐蚀环境,通过浸泡试验来评定五金电镀件在不同化学介质中的耐蚀性。
这些耐蚀性检验指标的合格与否直接影响着五金电镀件在不同环境下的使用性能。
最后,五金电镀件的尺寸检验也是必不可少的。
尺寸检验主要包括外径、内径、长度、厚度等尺寸参数的测量。
通过量具测量或三坐标测量仪进行尺寸检验,来确保五金电镀件的尺寸符合设计要求。
尺寸检验的合格与否直接影响着五金电镀件在装配和使用过程中的匹配性和稳定性。
综上所述,五金电镀件的检验标准涵盖了外观、耐蚀性和尺寸等多个方面,通过严格执行检验标准,可以有效保证五金电镀件的质量和稳定性。
只有通过严格的检验,才能确保五金电镀件在使用过程中能够发挥出最佳的性能,为各行业的生产和应用提供可靠的保障。
电镀、电泳件外观检验标准
气泡:指因为电泳工艺原因产品表面出现的气泡。
脱落:指电泳产品表面涂漆层掉。
漏漆:指电泳产品要求电泳面实际未涂漆。
花斑:指电泳前因基本材料腐蚀、或者材料中的杂质、或者材料微孔等原因所造成的、与周围材质表面不同光泽或粗糙度的斑块状花纹外观。
黑点:指电泳产品表面存在的黑色圆点。
发黄:指电泳产品表面的颜色显示黄色状态。
极重要
B面
次要外露面
指产品的侧面、向下外露面、边位、角位、接合位、内弯曲位。或物料装配成产品后,对产品的外观要求、客户使用无影响或此面对功能调试没有影响。
重要
C面
不易看到的面
指产品安装后的隐藏位、遮盖位。或物料装配成产品后,对参数调试无影响,纯属设计需要或此面有喷漆要求,或非喷漆面不外露面。
一般重要
B面残留有面积1mm2≤S≤2mm2的污渍,10cm2内不超过1处
C面内残留有面积1mm2≤S≤2mm2的污渍,10cm2内不超过2处
斑点
产品表面能有明显的凹凸点及异色点(如:麻点、亮点、氧化点)
产品表面有大片密密麻麻的斑点
A面10cm2内有大面积S≥0.3mm2的斑点不超过1个
A面10cm2内有面积0.08mm2≤S<0.3mm2的斑点不超过2个
B面:严重擦花/刮花/划伤面积S>0.3mm2
C面:轻微擦花/刮花/划伤面积1.5mm2≤S≤3mm2
C面:严重擦花/刮花/划伤面积S>3mm2
碰伤
产品表面不能有明显的碰伤现象
A面或B面有明显的、损伤镀层的碰伤,不可接受
A面有不损伤镀层的碰伤,面积S≥1mm2,不可接受
B面及边角碰伤面积S>1.5mm2,组装后影响整体外观
B面10cm2内有面积S≥0.3mm2的斑点不超过2个
电镀品标准
2.2.1、镀层试验;
2.2.1.1、试验方法:根据标准JISH8501:1999的电解式试验方法测定有效面。
2.2.1.2、评定标准:
镀层
试验条件
镀层标准(单位:μm)
备注
塑料件
锌合金
铜或铜合金
铜(Cu)
SC 2
≥15
≥5
不要求
所有塑料镀件的铜层要求应不超过30μm。
镍(Ni)
SC 2
3、当镀层厚度合格,但盐雾不合格时,盐雾实验的结果,不合格的部分盐雾等级需达7级时,作为整批产品特采盐雾判定的依据。
电镀品检验标准受控类型受控文件副本号编号02005版本10生效日期2008612实施日期页码对应条款编制审核批准电镀品检验标准文件编号02005页码13版本10生效日期20080612一外观标准
编制
审核
/
批准
电镀品检验标准
受控类型
受控文件
副本号
编号
***-***-02-005
版本
1.0
生效日期
2008.6.12
1.2.2.6、流痕、水痕;A面不允许有这些不良现象;B、C面依照限度样品为准;D面允许有这些不良现象;具体范围大小依照限度样品为准。
电镀品检验标准
文件编号
***-**-02-005
页码
2/3
版本
1.0
生效日期
2008.06.12
1.2.2.7、镀红、发白;A、B面不允许有这些不良现象;C、D面允许有这些不良现象,具体范围
发白:电镀表面因电流过大导致的烧焦状态,像层雾覆盖在电镀品上一样。一般出现在边角或加电极的部位。
针孔:电镀表面因基体的密实度较差原因,在抛光时未发现,继而在电镀后发生的表面有孔状的缺陷。
电镀产品验收标准
电镀产品验收标准产品验收标准/Parts inspection criteria一.不合格分类单位产品的质量特性不符合规定,称为不合格。
不合格按质量特性不符合的严重程度来分类:A类不合格:单位产品的极重要质量特性不符合规定,或者单位产品的质量特性极严重不符合规定,称为A 类不合格。
(相当于严重缺陷/Critical)B类不合格:单位产品的重要质量特性不符合规定,或者单位产品的质量特性严重不符合规定,称为B类不合格。
(相当于重缺陷/Major)C类不合格:单位产品的一般质量特性不符合规定,或者单位产品的质量特性轻微不符合规定,称为C类不合格。
(相当于轻缺陷/Minor)二.不良缺陷术语缺陷名称缺陷说明点缺陷具有点形状的缺陷,测量尺寸时以其最大直径为准。
颗粒在喷漆件表面上附着的细小颗粒积漆在喷漆件表面出现局部的油漆堆积现象阴影在喷漆件或塑料件表面出现的颜色较周围暗的区域桔纹在喷漆件或电镀件表面出现大面积细小的像桔子皮形状的起伏不平透底在喷漆件表面出现局部的油漆层过薄而露出基体颜色的现象。
鱼眼由于溶剂挥发速度不适而造成在喷漆件表面有凹陷或小坑。
多喷超出图纸上规定的喷涂区域剥落产品表面上出现涂层或镀层脱落的现象。
毛絮油漆内本身带有的,或油漆未干燥时落在油漆表面而形成的纤维状毛絮色差产品表面呈现出与标准样品(客户承认样品)的颜色的差异,称为色差。
光泽不良产品表面呈现出与标准样品(客户承认样品)光泽不一致的情况。
手印在产品表面或零件光亮面出现的手指印痕异色点在产品表面出现的颜色异于周围的点多胶点因模具方面的损伤而造成局部细小的塑胶凸起缩水当塑料熔体通过一个较薄的截面后,其压力损失很大,很难继续保持很高的压力来填充在较厚截面而形成的凹坑亮斑对于非光面的塑料件,由于壁厚不均匀,在壁厚突变处产生的局部发亮现象。
硬划痕由于硬物摩擦而造成产品表面有深度的划痕细划痕没有深度的划痕飞边由于注塑参数或模具的原因,造成在塑料件的边缘或分型面处所产生的塑料废边熔接线塑料熔体在型腔中流动时,遇到阻碍物(型芯等物体)时,熔体在绕过阻碍物后不能很好的融合,于是在塑料件的表面形成一条明显的线,叫做熔接线。
电镀检验标准(喷塑喷漆电镀发黑)
电镀检验标准1、目的规范检验操作,发现、控制不良品,防止批不良品输入下道工序。
同时给检验工作提供引导及接收标准。
2、范围适用于进料、外协制品回厂、成品的检验接收及顾客退货的挑选检验。
3、定义喷塑、喷漆件检验过程的参照标准(电泳漆件检验参照喷漆件检验标准)。
4、职责4.1 品质部负责不合格的发现、记录、标识及隔离,组织处理不合格品。
4.2 制造部参与不合格品的处理。
4.3 采购部负责进料中不合格品与供应商的联络。
4.4 管理者代表负责不合格品处理的批准。
5、工作程序外观(目测)5.1 喷涂种类(如:塑粉或漆)、颜色与图纸要求及客户、我司、供应商三方确认的色板是否一致。
5.2 一般情况下,产品喷涂表面外观在使用时要求100%进行检验(员工自检),检验方式依据本标准。
进料、外协回厂或过程验收则采用抽检,抽检操作方式依据《抽检规范》。
特殊产品根据产品的具体要求检验。
5.3 外观缺陷:有缩孔、针孔、杂质点、漏底、涂层厚度明显不均、流泪、预处理不良有锈、表面有污斑、不光滑、不平整、桔皮、花斑、凹坑等。
5.4 外观和颜色检验的环境:5.4.1 色板采用客户样件或经客户认可的签样。
5.4.2 应在标准光源对色灯箱CAC-600箱内(无设备条件时则要求在天然散射光线或光照度不低于2×40w光源环境下),以目视方法进行。
光照度通常在D65(特殊情况下用F/A,其次高标准要求时用CWF/TL84),背景颜色为中灰色。
5.4.3 检查距离:被测品与眼睛的距离为500mm,检验时在±15°范围内旋转。
涂膜附着力(划格实验)5.5涂膜附着力检验(基体金属为铁、钢、铝及铝合金):5.5.1 采用划格—胶带粘贴法测定漆膜附着力,每批次以一件或两件检验则可。
不合格时可用加严检验。
5.5.2 检验方法:使用锋利刃口的刀片(刃口宽要求0.05mm,刃口达到0.1mm时必须重新磨刃口),沿能确保得到直线切口的导向器,刃口在相对涂面35-45度角,均速划线。
- 1、下载文档前请自行甄别文档内容的完整性,平台不提供额外的编辑、内容补充、找答案等附加服务。
- 2、"仅部分预览"的文档,不可在线预览部分如存在完整性等问题,可反馈申请退款(可完整预览的文档不适用该条件!)。
- 3、如文档侵犯您的权益,请联系客服反馈,我们会尽快为您处理(人工客服工作时间:9:00-18:30)。
电镀标准2009-02-27 18:56电镀标准名称标准编号摘要铝及铝合金电镀前表面准备方法 JB/T 6986-93本标准规定了铝及铝合金电镀前一般应进行的表面准备方法,包括清洗、表面调整处理、浸镀、预镀等。
适用于铝及铝合金(包括常用铸铝、变形铝合金)的表面准备。
不适用于电铸用铝和铝合金模芯的表面准备。
引用标准 GB1173 铸造铝合金技术条件 GB3190铝及铝合金加工产品的化学成份 GB5270金属基体上的金属覆盖层术语清洗cleaning 清除工件表面油污或外来物的工艺过程。
表面调整处理conditioning 把工件表面状态转变成适合于以后工序进行成功处理的工艺过程。
电镀准备方法的选用铝件电镀前表面准备工艺过程一般为清洗------表面调整-------浸镀-------预镀,经过热处理的铝件,清洗前还需采用机械磨光、抛光加工或酸、碱浸蚀以除去热处理氧化膜。
选用表面准备方法时,应注意区别下述情况:a.铝件的材料牌号(对照G B1173和GB3190); b.铝件的制造方法,例如是铸造或压力加工方法制造等;c.铝件是否经过热处理。
其它镀前准备方法的选用根据不同的情况,实际生产中也可采用清洗------表面调整-------阳极氧化,或吹砂------清洗-----表面调整---------出光等镀前准备工艺。
除浸锌外,也可浸镀镍、镍锌合金、铁等重金属,在选用这些工艺过程时,电镀后的铝件应按GB5270规定的方法进行试验,电镀层必须符合结合强度良好的要求。
清洗和表面调整的处理清洗清洗工艺由蒸汽除油,有机溶剂清洗,可溶性乳化剂清洗,铝材料清洗剂清洗及相应的水漂洗工序组成。
常用的有热碳酸盐-磷酸盐水溶液清洗液。
油污严重的铝件开始清洗时可采用弱碱性或弱酸性溶液清洗。
表面调整处理的目的 a.除去铝件表面原有的氧化膜;b.除去表面有害的微量成份。
常用的表面调整处理溶液通常的表面调整处理是在中等温度的氢氧化钠溶液中浸渍后充分的水漂洗,再浸入硝酸-氟化氢铵溶液以除去表面挂灰,然后水漂洗干净。
为了防止氢氧化物和氟化物对环境的污染,也可选用硫酸-过氧化氢溶液代替硝酸-氟化氢铵溶液。
热处理铝件的表面调整经过热处理的铝件,要求进行机械加工或磨光的,可用抛光、磨光的方式除去氧化膜,然后进行适当的表面调整处理,不能进行机械加工或磨光的铝件表面应选用酸浸蚀的方法除去氧化膜,常用的酸浸蚀的溶液为热的硫酸-铬酸溶液,也可采用某些行之有效的专利浸蚀液。
轧制铝件的表面调整处理采用工业纯铝如L5、L6,防锈铝如LF21等轧制型材准备的铝件,用碳酸盐-磷酸盐溶液清洗后,于室温在硝酸中浸渍能得到满意的效果。
铝镁合金的表面调整处理铝镁合金零件如防锈铝L F2,锻铝LD2、LD31等的表面处理调整处理可采用热硫酸浸蚀,本方法对于锻铝等变形铭镁合金和铸造的铝镁合金均较理想,浸蚀时间与合金类型有关,一般铸铝的浸蚀时间较短。
含硅铸铝合金件的表面调整处理含水量硅量较高的铸铝合金,如ZL101、ZL101A、ZL102、ZL1 08、ZL109等在硝酸-氢氟酸混合液中进行表面调整处理。
该溶液也可用于表面不宜进行磨、抛光加工的热处理后的铸件除去热处理氧化膜。
浸镀和预镀经过清洗和表面调整处理后的铝件表面应浸镀或浸镀并预镀,常采用浸锌、浸锌并预镀铜、浸锌并预镀镍、浸锡并预镀青铜方式进行。
某些牌号或经过某些方式热处理之后的铝件,为了得到理想的效果,往往要对上述工艺或槽液稍作修改。
浸锌理想的浸锌层应该是薄而均匀一致,结晶细致且有一定的金属光泽,与基体结合牢固。
浸锌层的质量受合金的类型、表面调整处理工艺和浸锌工艺的影响。
锌层的沉积量一般为15~50微克/平方厘米,相应的厚度为20~72纳米,理想的沉积量不家宜超过30微克/平方厘米,过多的沉积量易形成海绵状锌层,与基体的结合强度也差。
浸锌分一次浸锌和二次浸锌。
浸锌后的铝件,通常在电镀其他金属之前采用适当的工艺在浸锌层上预镀一层铜,也可以在浸锌层上直接电镀银、黄铜、锌或铬。
选用的电镀工艺应适合在锌上电镀,并且工件应带电入槽。
浸锌溶液一般较浓,工件的带出液将使溶液成份发生变化,故应按化验结果经常补充组份,以保证浸锌层质量。
浸锌溶液的种类较多,而且不同类型的铝件,常常选用不同的浸锌溶液,无论选用何种浸锌溶液,以后的电镀层均应满足GB5270规定的结合强度试验要求。
二次浸锌第一次浸锌层粗糙多孔、附着不良,可采用二次浸锌。
二次浸锌后能得到细致、均匀略具金属光泽的锌层。
两次浸锌可在同一槽中进行,也可先在较浓的溶液中,后在较稀的溶液中进行。
为了获得理想的锌层,有时甚至要进行多次浸锌。
第一层锌在硝酸溶液中退除。
第一次浸锌时间为45秒;第二次浸锌时间为30秒。
注意事项浸锌时的挂具不能用铜或铜合金,以防止铜和铝或铝合金接触发生置换,应将挂具上的钢丝、铜或铜合金镀镍后再作浸锌使用,或者选用铝丝或非金属材料作为浸锌挂具。
浸锌并预镀铜经清洗,表面调整处理,一次浸锌或二次浸锌后的铝件,可在氰化镀铜溶液中预镀铜,充分水洗后再转入其他电镀溶液中电镀。
浸锌并预镀镍经清洗,表面调整处理,一次浸锌或二次浸锌后的铝件,也可在接近中性的镍槽中预镀镍,然后作进一步的电镀。
浸锡并预镀青铜在潮湿的腐蚀性环境中,浸锌层易发生横向腐蚀而使电镀层剥落。
在此情况下可采用浸锡后预镀青铜。
浸锡铝件按规定进行清洗调整后,充分漂洗再在含有锡酸盐的某些专利浸锡溶液中进行浸镀或带电入槽闪镀锡后预镀青铜。
预镀青铜浸锡后不用水漂洗即可在适宜的氰化电解液中预镀青铜,然后充分水洗再转入其他电镀槽中电镀。
本标准中要使用某些腐蚀性和剧毒性药品,应采取适当的安全措施。
氰化物和酸处理工序之间一定要有充分的水漂洗工序。
金属覆盖层钢铁上的镉电镀层 GB/T 13346-921 主题内容与适用范围本标准规定了钢铁上的镉电镀层的技术要求和检验方法。
适用于在各种条件下防止钢铁腐蚀的镉电镀层。
不适于未加工成形的板材、带材、线材的镉电镀层。
也不适用于可能同食物或饮料接触的物件的镀层。
本标准不适用于:(1)未加工成型的板材、带材或线材的镉电镀层;(2)可能同食物或饮料接触的物件的镀层(镉的毒性对人体会造成严重的危害)。
2 引用标准 GB1238金属镀层及化学处理表示方法。
GB4955金属覆盖层厚度测量阳极溶解库仑方法。
GB4956磁性金属基体上非磁性覆盖层厚度测量磁性方法。
GB5270金属基体上金属覆盖层(电沉积层和化学沉积层)附着强度试验方法。
GB6458金属覆盖层中性盐雾试验(NSS试验)。
GB6462金属和氧化物覆盖层横截面厚度显微镜测量方法。
GB6463金属和其他无机覆盖层厚度测量方法评述。
GB9800电镀锌和电镀镉层的铬酸盐转化膜。
GB1260 9电沉积金属覆盖层和有关精饰计数抽样检查程序。
GB/T12611金属零(部)件镀覆前质量控制技术要求。
3 术语(1)主要表面制件上某些已作或待作覆盖的表面,在该表面上覆盖层对制件的外观和(或)使用性能是重要的。
(2)局部厚度在基本测量面内进行规定次数厚度测量的算术平均值。
(3)最小局部厚度在单个工件的主要表面上测得的局部厚度最小值。
4 镀覆前零(部)件的基体金属的质量应达到GB/T12611的规定,否则,供需双方另行商定。
5 需方应向供方提供的资料(1)本标准号(GB/T13346);(2)对镀层厚度的要求;(3)主要表面用图纸或适当标记指明;(4)基体金属的性能、表面状态和加工精度;(5)镀层表面外观要求;(6)镀前和镀后的热处理要求;(7)铬酸盐或其它转化膜的类型。
应注意:只在当需方特别要求时,才能省去铬酸盐转化膜或应用代用的转化膜;(8)抽样或检验要求;(9)镀前准备和电镀过程的任何特殊要求和限制;(10)镉电镀件的包装、储存或运输要求。
6 镀层表示方法镉电镀层的表示方法按GB1238的规定。
7 镀层厚度系列(1)使用条件、使用寿命镉镀层在海洋气氛条件下具有优良的耐蚀能力,选取镉镀层的厚度,取决于使用环境的严酷程度和(或)使用寿命的长短。
Fe/Cd 5 c一般仅用于干燥的室内环境,如果使用环境比较严酷和(或)使用寿命较长,则应采用较厚的镉镀层。
金属覆盖层工程用镍电镀层 GB 12332-901 主题内容与适用范围本标准规定了黑色金属和有色金属上的工程用镍电镀层的要求。
适用于工程用镍电镀层,也适用于最小厚度在30μm以上的防护装饰性镍镀层。
不适用于主要用于装饰目的的镍镀层和最小厚度在30μm以下的防护装饰性镍镀层。
2 引用标准 GB11379金属覆盖层工程用铬电镀层 GB12609电沉积金属覆盖层和有关精饰计数抽样检查程序 GB3505表面粗糙度术语表面及其参数 GB4340金属维氏硬度试验方法GB4955金属覆盖层厚度测定阳极溶解库仑方法 GB5270金属基体上金属覆盖层(电沉积层和化学沉积层)附着强度试验方法 GB6462金属和氧化物覆盖层横断面厚度显微镜测量方法GB9797金属覆盖层镍+铬和铜+镍+铬电镀层3术语 3.1主要表面指工件上某些已电镀或待电镀的表面,该表面上的镀层对工件的外观和(或)使用性能是重要的。
3.2最小局部厚度在一个工件的主要表面上所测得的局部厚度的最小值,也称最小厚度。
4抽样为了检查镀镍层是否符合本标准第7章的各项要求,应按GB12609的规定抽样。
5需方应向供方提供的资料 a.本标准的标准号,即GB12332。
b.基体金属的型号或规格,以及它的冶金学状态。
c.电镀前是否需要除应力的处理。
d.电镀前是否需要引入压应力的处理,例如喷丸。
e.有关主要表面和不需电镀的所有表面的详细说明。
f.对前处理有什么特殊要求和限制,例如用喷砂了取代酸的前处理。
g.对底镀层有什么要求。
h.镍层的最小厚度,如果使用底层,则是电镀层的总厚度;如果有要求,最大厚度也要说明,特别是对于磨损的或加工超差的工件修复。
这些厚度是指电镀件经过所有机械加工之后的镀层厚度。
i.所需的镍层的类型,即暗的、光亮的、低应力的等。
j.镍层最后的表面精饰状态,如电镀后不加工的,机械加工的或抛光的。
k.允许缺陷的类型和(或)大小,这些缺陷在每一件,每一平面或每平方分米面上缺陷的数目。
l.电镀后是否需要热处理。
m.其他特殊的要求,如硬度、表面粗糙度等。
6基体金属电镀前的处理 6.1一般规定供方应对工件主要表面进行检查,确认是否有明显的表面缺陷,如气孔、裂纹和不合要求的覆盖层,或者任何对最后的精饰不利的其他缺陷。
所有缺陷都应在作任何处理之前提请需方注意。
6.2消除应力的热处理若有规定,电镀之前工件应当消除应力。
常用的处理条件列于表1,也可采用不同于表1的处理条件,如适当提高温度和缩短时间,但应由你俩但应由供需双方商定。