机械毕业设计英文外文翻译88创建焊接程序
锻造、铸造、焊接外文翻译

毕业设计(论文)外文翻译学生姓名:系别:机械工程系专业:机械设计制造及其自动化班级:学号:译文出处:Science and Technology Engl-ish for Mechanical EngineeringCasting、Forging and Welding1. CastingMetal casting is one of the oldest of all industries, both ancient and medieval history offering examples of the manufacture and use of casting. From simple axeheads poured from copper in open moulds some 5000 years age, casting in the pre-Christian world developed to a point at which elaborate bronze statuary could be produced in two-piece and cored moulds. By the end of the medieval period, decorated bronze and pewter casting had begun to be used in European church and domestic life.The widespread adoption of cast iron as engineering material awaited the success of Abraham Darby in 1790 in smelting in the coke blast furnace; this paved the way for the massive use of cast iron in construction during the years following the industrial revolution.Many foundries sprang up after the industrial revolution, the vast majority being for the manufacture of the cast iron then being used as a structural material. The quantity production of iron castings in the nineteenth century was not matched by a universal advance in quality and the engineering use of the products encountered more serious risks in a non-ductile material.Despite the skill of the molder in producing complex forms, there was little change in the metallurgical and engineering situation until the modern era brought a better understanding of the factors determining quality. With modern techniques of process control the rudimentary judgment of the operator could give way to objective measurements of metal temperature, molding material properties and other production variables. These improvements have been applied not only to cast iron but to a wide range of cast alloys.There are four basic casting methods: sand-casting, die-casting, investment-casting, and centrifugal casting.Sand-casting is the most widely used method employed in foundry. In this process, sand moulds are contained in metal molding boxes that have four sides but no top or bottom. During the molding operation the boxes are located togetherby pins so that they can be separated to remove the pattern, and replaced in the correct position before the metal is poured in. The boxes are clamped together, or the cope (top section) weighted down when pouring to prevent the cope from “floating away”from the drag (lower section) when the mould is full of molten metal. The sequence when molding the simple two-part mould to cast a bracket is illustrated as follows.At the first stage the pattern is seated on the moulding board. The pattern is covered with facing sand, which is a specially prepared sand of good quality, which can take a clean and smooth impression, and can resist the heat from the molten metal that will be in contact with it. The facing sand is backed up with molding sand, which is old facing sand from previous moulds. The molding sand is carefully rammed up so that it is fairly tight around the pattern to produce a good solid mould, yet permeable enough to allow the gases produced during casting to escape. The sand is finally leveled off.At the second stage the mould with the pattern still in position is inverted; the exposed sand lightly covered with parting sand, and the exposed pattern with facing sand.(The parting sand has no cohesion, and is introduced to permit a clean separation when the mould is opened up to remove the pattern .) The second molding box is located in position on the first box and filled with molding sand. Two or more plugs are introduced when the second box is being filled (these are removed later, leaving channels in the sand). One of these plugs is positioned to one side of the pattern. The sand is rammed up and leveled off.Now, at stage 3, to allow the pattern to be removed. This is done by screwing a bar with a threaded end into a suitable insert in the pattern, damping the sand around the pattern, and gently rapping the bar in all directions so that the pattern can be carefully withdrawn. To facilitate the removal of the pattern without scuffing the sides of the impression, all surfaces that lie in the direction of pattern removal are inclined slightly by a small amount (the draw angle).A groove called a gate is cut in the sand face to allow the channel producedby the plug that is outside the pattern to connect with the impression .The metal is poured through this channel (called the runner), and the gate prevents it from dropping straight into the impression and damaging it .The cross-section of the gate is slightly smaller than that of channel so that a full runner will always supply metal to the gate at a slight pressure.Finally, the mould is reassembled, carefully locating and securing the two sections. The top section is known as the cope, and the lower section is known as the drag. The sand in the cope is vented. These vents allow the sand to be rammed up more tightly at the earlier stages without the risk of gases being trapped in the molten metal and forming blowholes in the solid metal. A sand-feeding gate (also called a pouring or bowl) is added to make it easier to pour the metal into the runner. The molten metal is poured through the runner and the air will escape through the riser.The impression will be filled with molten metal when it is completely filled. Gases can escape through the runner and the riser, which also act as headers to supply the impression with more metal to compensate for the contraction of the metal when cooling in the molten state.2. ForgingForging is the plastic working of metal by means of localized compressive forces exerted by manual or power hammers, presses, or special forging machines. It may be done either hot or cold. however, when it is done cold, special names usually are given to the processes. Consequently, the terms“forging” usually implies hot forging done above the recrystallization temperature.Modern forging is a development form the ancient art practiced by the armor makers and the immortalized village blacksmith. High-powered hammers and mechanical presses have replaced the strong arm, the hammer, and the anvil and modern metallurgical knowledge supplements the art skill of the craftsman in controlling the heating and handling of the metal.Forge ability is the term used in the industry to denote a material relative resistance to deformation and its plasticity. While considerable disagreementexists as to precisely what characteristics the word “forge ability” should include, the term as used here is defined as the tolerance of a metal or alloy for deformation without failure, regardless of forging pressure requirements.Raw material used for forging is generally bar or billet stock hot rolled from ingots melted in open-hearth, electric arc, or vacuum arc furnace .other forms and shapes such as rolled slabs, plats, and stock produced by continuous casting techniques are occasionally used .for certain grades ,vacuum arc melting imparts better forge ability than does conventional arc melting . However, the major purpose of vacuum melting is the improvement of mechanical properties and cleanliness, not forging behavior.Equipment behavior influences the forging progress since it determines the feasibility of forging a part and affects the rate of deformation and the temperature conditions.The hammer is the most economical type of equipment for generating load and energy necessary to carry out a forging process, provided that the material being forged can support high deformation velocities. It is most commonly used hot forging equipment for repeated blows on the same workpiece and cannot be overloaded.There are various types of hammers: air-lift gravity drop hammers, power drop hammers, power drop hammers, Counterblow hammers ect. In a simple gravity drop hammer the upper ram is positively connected to a board, a belt, a chain or a piston. When forging the ram is lifted to a certain height and then dropped on the stock placed on the anvil. During the down stroke, the rain is accelerated by gravity and builds up the blow energy. The upstroke takes place immediately after the blow, the force necessary to ensure quick lift-up of the ram can be 3 to 5 times the ram weight. The operation principle of a power-drop hammer is similar to that of an air drop hammer. During the down stroke, in addition to gravity, the ram is accelerated by steam, cold air or hot air pressure. In an electro hydraulic gravity-drop hammer, the ram is lifted with oil pressure against an air cushion. The compressed air slows down the upstroke of the ram and contributes to its acceleration during the down stroke .thus; the electrohydraulic hammer also has a minor power hammer action.Press forging employs a slow squeezing action in deforming the plastic metal, as contrasted with the rapid-impact blows of a hammer. Hydraulic forging press is operated by large pistons driven by high-pressure hydraulic or hydrometric system. The squeezing action is carried completely to the center of the part being pressed, thoroughly working the entire section. These presses are the vertical type and may be either mechanically or hydraulically operated. The mechanical presses, which are faster operating and most commonly used, range in capacity from 5000 to 10000 tons.In the forging press a grater proportion of the total work put into the machine is transmitted to the metal than in a drop hammer. The machine and foundation absorb much of the impact of the drop hammer .press reduction of the metal is faster, and the cost of operation is consequently lower. most press forging s are symmetrical in shape ,having surfaces, which are quite smooth, and provide a closer tolerance than is obtained by a drop hammer .however ,drop forging can forge many parts of irregular and complicated shapes more economically. Forging presses are often used for sizing operations on parts made by other forging processes.For small forgings closed impression dies are used, and only one stroke of the ram is normally require to perform the forging operation .the maximum pressure is built up at the end of the stroke ,which forces the metal into shape .dies may be mounted as separate units, or all the cavities may be put into a single block. for small forgings individuals die units are more convenient .large ingots are now almost always forged with hydraulic presses instead of with steam hammers, since the work done by a press goes deeper. Further, the press can take a cooler ingot and can work to closer dimensions.The forging should be done at about the same temperature as rolling; the process improves the physical properties of the steel just as rolling does. In the final forging it is important not to have the steel too hot, for overheated steel will have poor mechanical properties when cooled. in heating for forging the temperature is usually judged by the eye, but where a large number of thesame patterns will be made, the pieces to be forged are heated in furnaces in which the temperature is indicated by pyrometers, and often is automatically controlled.3. weldingWelding techniques have become so versatile that it is difficult nowadays to define “welding”. Formerly welding was “the joining of metals by fusion”, that is, by melting, but this definition will no longer do. Welding was next defined as the “joining of metals by heat”, but this is not a proper definition either. Not only metals can be welded, so can many of the plastics. Furthermore several welding methods do not require heat. Every machinist is familiar with heatless welding method under some circumstances. Besides these, we can weld with sound and even with the famous laser. Faced with a diversity of welding methods that increase year by year, we must here adopt the following definition of welding:" welding is the joining of metals and plastics by methods that do not employ fastening devices”.There is also no uniform method of naming welding processes. Some processes are named according to the heat source or shielding method, other certain specialized processes are named after the type of joint produced. Examples are spot and butt welding. But an overall classification can not take account of this because the same type of joint may be produced by a variety of processes. Spot welding may be done by electric resistance, arc, or electron-beam processes and butt welding by resistance, flash or any of a number of other methods. Many welding processes are named depending on the heat applied, equipment used, and type of metal to be joined and the strength of the joint.Soldering is the process of joining two metals by a third metal to be applied in the molten state. Solder consists of tin and lead, while bismuth and cadmium are often included to lower the melting point. One of the important operations in soldering is that of cleaning the surface to be joined, this may be done by some acid cleaner. Soldering gives a satisfactory joint for light articles ofsteel, copper or brass, but the strength of soldering joint is rather less than a joint which is brazed, riveted or welded. These methods of metal are normally adopted for strong permanent joints.Pressure welding is known as the simplest method of welding two pieces of metal together. The ends of metal are heated to a while heat—for iron, the welding temperature should be about 1300℃—in a flame. At this temperature the metal becomes plastics. The ends are then presses or hammered together, and the joint is smoothed off. Care must be taken to ensure that the surfaces are thoroughly clean first, for dirt will weaken the weld. Moreover, the heating of iron or steel to a high temperature causes oxidation, and a film of oxide is formed on the heated surfaces. For this reasons, a flux is applied to the heated metal. At welding heat, the flux melts, and the oxide Particles are dissolved in it together with any other impurities which may be present. The metal surfaces are pressed together, and the flux is squeezed out from the center of the weld.Gas welding includes all the processes in which gases are used to obtain a hot flame. Those commonly used are acetylene, natural gas, and hydrogen in combination with oxygen. The maximum temperature developed by oxyhydrogen welding is 3600℉ (1980℃). Hydrogen is produced either by the electrolysis of water or by passing steam over coke. An oxyacetylene weld is produced by heating with a flame obtained from the combustion of oxygen and with or without the use of a filler metal. In most cases the joint is heated to a state of fusion, and as a rule, no pressure is used.Are welding is a process in which coalescence is obtained by heat produced from an electric arc. The electrode or filler metal is heated to a liquid state and deposited into the joint to make the weld. Contact is first made between the electrode and the work to create an electric circuit, and then, by separating the conductors, an arc is formed. The electric energy is converted into intense heat in the arc, which attains a temperature around 10 000°F (5500℃). Either direct or alternating current can be used for arc welding, direct current being preferred for most purposes. A d-c welder is simply a motor-generator set ofconstant-energy type, having the necessary characteristics to produce a stable arc. Arc welding uses commonly metal electrodes or carbon electrodes.Laser Welding is used because of laser’s high heat intensity. It can be operated in any transparent medium without contact with the workpiece, since the laser delivers its energy in the form of light. In welding, the power is delivered in pulses rather than as a continuous beam, the beam is focused on the workpiece and the intense heat produces a fusion weld. Laser welding is slow and is used only for special jobs involving small weldments. Its greatest use is found in the electronics industry.Explosion welding is a process that uses energy from the detonation of an explosive to join two pieces of metal. The explosion accelerates the pieces to a speed at which a metallic bond will form between them when they collide. The weld is produced in a fraction of a second without the addition of filler metal. This is essentially a room temperature process in that gross heating of the workpieces does not occur. The faying surfaces, however, are heated to some extent by the energy of the collision, and welding is accomplished through plastic flow of the metal on those surfaces. Welding takes place progressively as the explosion and the forces it creates advance from one end of the joint to the other. Deformation of the weldment varies with the type of joint. There may be no noticeable deformation at all in some weldments, and there is no loss of metal.译文:铸造、锻造和焊接1.铸造金属铸造是最古老的产业之一,远古时期和中世纪就有人使用和制造铸件了。
机械专业毕业设计外文翻译12

Development of a high-performance laser-guided deep-holeboring tool: optimal determination of reference origin for precise guidingAbstractA laser-guided deep-hole boring tool using piezoelectric actuators was developed to prevent hole deviation. To extend the depth o controll able boring further, the following were improved. The tool’s guiding error, caused by misalignment of the corner cube prism and the mirror in the optical head from the spindle axis, was eliminated using an adjustment jig that determined the reference origins of the two position-sensitive detectors (PSDs) precisely. A single-edge counter-boring head is used instead of the double-edge head used up to now The former was thought to be better in attitude control than the latter. A new boring bar, which was lower in rigidity and better in Controllability of tool attitude, was used. Experiments were conducted to examine the performance of the new tool in detail and to determin its practical application, using duralumin (A2017-T4) workpieces with a prebored 108-mm diameter hole. The experiments were performed with a rotating tool–stationary workpiece system. Rotational speed was 270 rpm and feed was 0.125 mm/rev. Tool diameter was 110 mm Asaresult,controlled boring becomes possible up to a depth of 700 mm under the stated experimental conditions.700 mm is the maximum machinable length of the machine tool. The tool can be put to practical use.Keywords: Deep hole-boring; Adaptive control; Laser application1.IntroductionTo bore a precise straight hole, a deep-hole boring tool should be guided toward a target. From this point of view, the laser-guided deep-hole boring tool was developed [1–6]. The latest tool using piezoelectric actuators could be guided to go straight toward the target,despitedisturbances up to a depth of 388 mm [6].In the present paper, before the performance of the tool is examined, the following points are improved to extend the depth. The tool’s guiding error, caused by misalignment of the corner cube prism and the mirror in the optical head from the spindle axis, is eliminated using a jig that deter- mines the reference origins of the two position-sensitive detectors (PSDs) precisely. A single-edge counter-boring head is used instead of the double-edge head used up to now. The former is thought to be better in attitude control than the latter. A new boring bar, which is 15% lower in both bending and torsional rigidity and which is better in controllability of tool attitude, is used.2. Experimental apparatusFigs. 1 and 2 show the tool head and the experimental apparatus, respectively [6]. The head is the same as that used in experiments up to now. One cutting edge of the double-edge counter-boring head is replaced by a guide pad,And six guide pads are removed[4].By removal of the guide pads, cutting oil is supplied better between the other guide pads and hole wall. The tool head consists of an optical head, a counter-boring head, piezoelectric actuators, and an actuator holder (Fig. 1). The optical head is attached to the front surface of the counter-boring head through an adjust- ment jig. The actuator holder is connected to a rotation stopper 14 behind the tool head by two parallel plates of phosphor bronze 6 (Fig. 2). A laser source 11, and PSDs 9, 10 are set in front of the tool. The rectangular coordinates XAnd Y are set on a plane perpendicular to the spindle rotation axis(Z-axis).The optical distancebetween a dichroic mirror in the optical head and PSD 10 for measuring tool inclina- tion is 2,040 mm [2].3. Method for detection of tool position and its inclinationFig. 3 shows the method used for measuring the tool position and its inclination. The laser beam, radiated from an argon laser, reaches the dichroic mirror 6 through the beam expander 5 and the half mirror 1. The dichroic mirror separates the two beams of wavelengths 514 nm (green) and 488 nm (blue). The green beam for measuring tool position passes through the dichroic mirror 6 and reachesthe corner cube prism 8. The reflected beam passes again through 6 and is deflected by the half mirror 1 toward dichroic mirror 2. By passing through the dichroic mirror 2, it reaches the PSD 9 used for measuring tool position. The blue beam for measuring tool inclination reaches the dichroic mirror 7 with an angle of incidence equal to 0°. The dichroic mirror 7 reflects the blue beam and trans- mits parts of the green beam, which are not completelyseparated by the dichroic mirror 6. The returning beam from the dichroic mirror 7 is deflected by the mirrors 6, 1, and 2, then passing through the dichroic mirror 4, and reaches the PSD 10 for measuring tool inclination. Re- flective characteristics of dichroic mirror 4 differs from that of dichroic mirror 7.4. Acquisition of data for controlling the toolData for tool attitude control are acquired from the two PSDs for tool position and its inclination every rotation of the counter-boring head. Until now, outputs of the two PSDs (measuring tool position and its inclination) some- times did not correspond well to the measured hole devia- tion. To determine what causes this, the following is exam- ined. The tool head with the optical head is supported by two V-blocks and is aligned on the Z-axis at the same longitudinal position as in the experiment. Then, the laser beam is radiated, and the optical head is rotated manually.Fig. 4 shows variations of outputs of two PSDs with encoder pulse during one rotation of the optical head fixed on the counter-boring head. Theoretically, outputs of two PSDs are constant during one rotation of the optical head corresponding to a 1,400 pulse of output of an encoder. Changes of X- and Y-outputs of tool position are caused by change of darkness of the laser spot because of interference and polarization of the laser beam. Changes of X- and Y- outputs of tool inclination are caused by inclination of the reflecting mirror in the optical head from the Z-axis. From the last experiment [6] on, tool position and its inclination are measured at rotational pulse position 700, where the brightness of the two PSDs are preferable at the same time.5. Misalignment of the optical parts in the optical headEven if the laser source and the PSDs for tool position and its inclination are aligned on Z-axis, hole deviation appeared. To discover its cause, the misalignment of the corner cube prism and inclination of reflecting mirror in the optical head from the Z-axis are examined.Fig. 5 shows all cases of alignment errors. Fig. 5(a) shows that the corner cube prism and the reflecting mirror are precisely aligned on the Z-axis. Figs. 5(b) and 5(c) are, the cases in which the corner cube prism is displaced by and the reflecting mirror is inclined byfrom the Z-axis, respectively.IncaseofFig.5(d),errorsofFigs.5(b)and(c) occur together. Fig. 5(e) shows the case when the optical head is inclined byduring the setup of the counter-boring head. Fig. 5(f) is the worst case, when all errors occur together. These errors cannot be eliminated by conventional adjustment. Therefore a new guiding strategy is developed to ensure that the tool can be guided straight, even if errors should occur.6. Optimal setup of reference origin for precise guidingFig. 6 shows the optimal setup method of reference origins. The laser source is aligned on the Z-axis [Fig. 6(a)] [6]. The optical head is fixed to the front surface of a cylindrical alignment jig through an adjustment jig. The alignment jig is inserted into the guide bush, which is fixed on a machine table, and the centers of both alignment jig and the optical head are aligned on Z-axis. Then the laser beam is radiated. Reflected beams reach the PSDs for tool position and its inclination. When the cylinder is rotated by hand, the rotational position, at which the output is most reliable, can be found. Next, the PSDs are moved until the spots lie at their centers. This position corresponds to the pulse position 700 of the encoder. The centers are reference origins for tool position and its inclination.At this rotational position,the optical head is fixed to the counter-boring head using the adjustment jig [Fig.6(b)].When the control starts, the tool head follows the alignment jig’s axis.7. Mechanism of tool displacementFig. 7 shows the mechanism of tool displacement. Fig. 7(a) shows the normal cutting condition [7]. The cutting force P is acting on the cutting edge and is counterbalanced by the guide pads. Fig. 7(b) shows the case where the tool is to correct for a deviation. A chain double-dashed line shows the hole wall before correction of hole deviation. A Directed line shows the direction of the correction.When the tool is controlled to incline toward the direction of the directed line, a cutting edge set ahead of the guide pads overcuts the hole wall. When the guide pad on the opposite side comes to the position of the overcutting zone, the cutting edge leaves a noncutting zone on the hole wall Opposite the overcutting zone.As a result,tool shifts toward the direction of the directed line.In the case of double-edge counter-boring head, the cut- ting force acting on one cutting edge is balanced by the force that acts on the other cutting edge [7]. As a result, the head is easy to vibrate, and the mechanism of tool displace- ment does not function well.Form: Precision Engineering 24 (2000) 9–14 开发高性能的激光制导deep-holeboring工具:最佳测定参考来源精确指导摘要激光制导深孔钻具使用压电致动器是防止孔偏差。
机械专业毕设翻译(焊接机器人)

运用对象导向型和分布式软件协助工业机器人焊接焊接机器人J. NORBERTO PIRES, ALTINO LOUREIRO, T. GODINHOP. FERREIRA, B. FERNANDO, and J. MORGADO著机器人常被用于工业焊接作业中,但这一运用并非一个简化的工艺流程。
难点在于机器人仍处于早期设计阶段,难以被利用和编程;复杂的焊接过程并不为人所熟知;人工人机界面并没有真正发挥作用。
本文将对上述问题加以讨论,并会涉及到以双重目标而设计,既能很好地服务于焊接的研究与开发,又能协助工业伙伴焊接的系统。
该系统用两种判例案例在一定程度上详细解释并显示了工业中常见的两种情况:一是是用于复杂构造并需要强焊接的多层对焊,二是多圆角焊接,例如焊接建筑行业中的构件。
背景激烈的竞争和市场动态特性使得实际市场更适合中/小型批量制造。
在这种情况下,与手工生产和复杂的自动设置相比,机器人生产设置显现出了最佳“单位成本”性能(图1) [1]。
图-1因此,在不远的将来,强大而更灵活的机器将为了处理小型企业的需求应运而生。
这些小型企业需要更多的远程接口,强大的程序设计语言,电力控制,及为高级编程而设计的先进的编程接口等。
这意味着作为几十年的设计成果,用户可以灵活存储(并仅为使用)。
机器人让人如此感兴趣在于它是一个巧妙的科学装置,构造精良,采用永久动力源,从编程角度看又不乏灵活。
但这并不一定意味着开放源码,相反,它为硬件及软件的实用提供了强大的编程接口和实际标准,使其能够在无限制情况下进入系统。
这在研究环境中极为重要,在这里可以良好的利用资源,去贯彻和检验新想法。
若可行,系统集成商(甚至研究员)将不需开放源码软件,至少不需为了传统机器人领域(工业机器人和移动式遥控机器人)开放。
事实上,如果这些领域的机器人技术拥有数十年的工程成就,取得了好的成果并成为了可信赖的机器,开源也将难以实现,因为这些成果是不易匹配的。
现代包装机械设备毕业课程设计外文文献翻译、中英文翻译
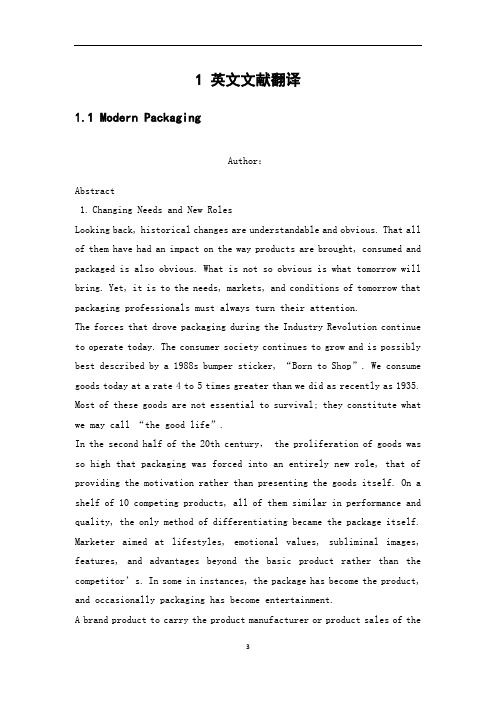
1 英文文献翻译1.1 Modern PackagingAuthor:Abstract1. Changing Needs and New RolesLooking back, historical changes are understandable and obvious. That all of them have had an impact on the way products are brought, consumed and packaged is also obvious. What is not so obvious is what tomorrow will bring. Yet, it is to the needs, markets, and conditions of tomorrow that packaging professionals must always turn their attention.The forces that drove packaging during the Industry Revolution continue to operate today. The consumer society continues to grow and is possibly best described by a 1988s bumper sticker, “Born to Shop”. We consume goods today at a rate 4 to 5 times greater than we did as recently as 1935. Most of these goods are not essential to survival; they constitute what we may call “the good life”.In the second half of the 20th century, the proliferation of goods was so high that packaging was forced into an entirely new role, that of providing the motivation rather than presenting the goods itself. On a shelf of 10 competing products, all of them similar in performance and quality, the only method of differentiating became the package itself. Marketer aimed at lifestyles, emotional values, subliminal images, features, and advantages beyond the basic product rather than the competitor’s. In some in instances, the package has become the product, and occasionally packaging has become entertainment.A brand product to carry the product manufacturer or product sales of theretailer’s label, usually by the buyer as a quality assessment guidance. In some cases, competing brands of product quality is almost no difference, a difference is the sale of its packaging. An interesting visually attractive packaging can give a key marketing advantage and convince impulse spending. However, the packaging should accurately reflect the quality of products/brand value in order to avoid the disappointment of consumers, encourage repeat purchases and build brand loyalty. Ideally, the product should exceed customer expectations.2. Packaging and the Modern Industrial SocietyThe importance of packaging to a modern industrial society is most evident when we examine the food-packaging sector. Food is organic in nature, having an animal or plant source. One characteristic of such organic matter is that, by and large, it has a limited natural biological life.A cut of meat, left to itself, might be unfit for human consumption by the next day. Some animal protein products, such as seafood, can deteriorate within hours.The natural shelf life of plant-based food depends on the species and plant involved. Pulpy fruit portions tend to have a short life span, while seed parts, which in nature have to survive at least separated from the living plant are usually short-lived.In addition to having a limited natural shelf life, most food is geographically and season-ally specific. Thus, potatoes and apples are grown in a few North American geographical regions and harvest during a short maturation period. In a world without packaging,we would need to live at the point of harvest to enjoy these products, and our enjoyment of them would be restricted to the natural biological life span of each. It is by proper storage, packaging and transport techniques that we are able to deliver fresh potatoes and apples, or the products derived from them, throughout the year and throughout the country. Potato-whole,canned, powdered, flaked, chipped, frozen, and instant is available, anytime, anywhere. This ability gives a society great freedom and mobility. Unlike less-developed societies, we are no longer restricted in our choice of where to live, since we are no longer tied to the food-producing ability of an area. Food production becomes more specialized and efficient with the growth of packaging. Crops and animal husbandry are moved to where their production is most economical, without regard to the proximity of a market. Most important, we are free of the natural cycles of feast and famine that are typical of societies dependent on natural regional food-producing cycles.Central processing allows value recovery from what would normally be waste by products of the processed food industry from the basis of other sub-industries. Chicken feathers are high in protein and, properly mill and treated, can be fed back to the next generation of chickens. Vegetable waste is fed to cattle or pigs. Bagasse, the waste cane from sugar pressing, is a source of fiber for papermaking. Fish scales are refined to make additives for paints and nail polish.The economical manufacture of durable goods also depends on good packaging.A product's cost is directly related to production volume. The business drive to reduce costs in the supply chain must be carefully balanced against the fundamental technical requirements for food safety and product integrity, as well as the need to ensure an. efficient logistics service. In addition, there is a requirement to meet the aims of marketing to protect and project brand image through value-added pack design. The latter may involve design inputs that communicate distinctive, aesthetically pleasing, ergonomic, functional and/or environmentally aware attributes. But for a national or international bicycle producer to succeed, it must be a way of getting the product to a market, which may be half a world away. Again, sound packaging, in this case distributionpackaging, is a key part of the system.Some industries could not exist without an international market. For example, Canada is a manufacturer of irradiation equipment, but the Canadian market (which would account for perhaps one unit every several years) could not possibly support such a manufacturing capability. However, by selling to the world, a manufacturing facility becomes viable. In addition to needing packaging for the irradiation machinery and instrumentation, the sale of irradiation equipment requires the sale packaging and transport of radioactive isotopes, a separate challenge in itself. In response to changing consumer lifestyles, the large retail groups and the food service industry development. Their success has been involved in a competition fierce hybrid logistics, trade, marketing and customer service expertise, all of which is dependent on the quality of packaging. They have in part led to the expansion of the dramatic range of products offered, technology innovation, including those in the packaging. Supply retail, food processing and packaging industry will continue to expand its international operations. Sourcing products around the world more and more to assist in reducing trade barriers. The impact of the decline has been increased competition and price pressure. Increased competition led to the rationalization of industrial structure, often in the form of mergers and acquisitions. Packaging, it means that new materials and shapes, increased automation, packaging, size range extension of lower unit cost. Another manufacturer and mergers and acquisitions, the Group's brand of retail packaging and packaging design re-evaluation of the growing development of market segmentation and global food supply chain to promote the use of advanced logistics and packaging systems packaging logistics system is an integral part of, and played an important role in prevention in the food supply or reduce waste generation.3. World Packaging.This discussion has referred to primitive packaging and the evolution of packaging functions. However, humankind's global progress is such that virtually every stage in the development of society and packaging is present somewhere in the world today. Thus, a packager in a highly developed country will agonize over choice of package type, hire expensive marketing groups to develop images to entice the targeted buyer and spend lavishly on graphics. In less-developed countries, consumers are happy to have food, regardless of the package. At the extreme, consumers will bring their own packages or will consume food on the spot, just as they did 2000 years ago.Packagers from the more developed countries sometimes have difficulty working with less-developed nations, for the simple reason that they fail to understand that their respective packaging priorities are completely different. Similarly, developing nations trying to sell goods to North American markets cannot understand our preoccupation with package and graphics.The significant difference is that packaging plays a different role in a market where rice will sell solely because it is available. In the North American market, the consumer may be confronted by five different companies offering rice in 30 or so variations. If all the rice is good and none is inferior, how does a seller create a preference for his particular rice? How does he differentiate? The package plays a large role in this process.The package-intensive developed countries are sometimes criticized for over packaging, and certainly over-packaging does exist. However, North Americans also enjoy the world's cheapest food, requiring only about 11 to 14% of our disposable income. European food costs are about 20% of disposable income, and in the less-developed countries food can take 95%of family income.4. The status and development trend of domestic and international packaging machineryWorldwide, the history of the development of the packaging machinery industry is relatively short, science and technology developed in Europe and America in general started in the 20th century until the 1950s the pace greatly accelerated.From the early 20th century, before the end of World War II World War II,medicine,food, cigarettes,matches,household chemicals and other industrial sectors, the mechanization of the packaging operations; the 1950s, the packaging machine widely used common electric switches and tube for the main components of the control system to achieve the primary automation; 1960s, Electrical and optical liquid-gas technology is significantly increased in the packaging machine, machines to further expand on this basis a dedicated automated packaging line; the 1970s, the micro- electronic technology into the automation of packaging machines and packaging lines, computer control packing production process; from the 1980s to the early 1990s, in some field of packaging, computer, robot application for service, testing and management, in preparation for the over-flexible automatic packaging lines and "no" automatic packaging workshop.Actively promoted and strong co-ordination of all aspects of society, and gradually establish a packaging material, packaging, printing, packaging machinery and other production sectors, and corresponding to the research, design, education, academic, management and organization, and thus the formation of independent and complete. The packaging of light industrial system, and occupies an important place in the national economy as a whole.Based on recent years data that members of the World Packaging Alliance output value of the packaging industry accounts for about 2% of the total output value of the national economy; in which the proportion of packaging machinery, though not large, but the rapid development of an annual average of almost growing at a rate of about 10%. Put into use at the packaging machine is now more than thousand species of packaging joint machines and automated equipment has been stand-alone equate. According to the new technological revolution in the world development trend is expected to packaging materials and packaging process and packaging machinery will be closely related to obtain the breakthrough of a new step, and bring more sectors into the packaging industry.China Packaging Technology Association was established in 1980. Soon, the China National Packaging Corporation have been born. Since then, one after another in the country organized a national and international packaging machinery exhibition, seminars, also published I had the first ever "China Packaging Yearbook and other packaging technology books. All this indicates that China is creating a new packaging historical perio d.1.2中文翻译现代包装1、不断变化的需求和新的角色,回顾以往,包装所带来明显的历史性变化是可以理解的, 一个产品包装方式的给他们的销量带来的影响也是显而易见的。
机械专业毕业设计外文翻译1

本科毕业设计(本科毕业论文)外文文献及译文文献、资料题目:High-rise Tower Crane designed文献、资料来源:期刊(著作、网络等)文献、资料发表(出版)日期:2000.3.25院(部):机电工程学院专业:机电工程及自动化High-rise Tower Crane designed under Turbulent Winds At present, construction of tower cranes is an important transport operations lifting equipment, tower crane accident the people's livelihood, major hazards, and is currently a large number of tower crane drivers although there are job permits, due to the lack of means to monitor and review the actual work of a serious violation . Strengthen the inspection and assessment is very important. Tower crane tipping the cause of the accident can be divided into two aspects: on the one hand, as a result of the management of tower cranes in place, illegal operation, illegal overloading inclined cable-stayed suspended widespread phenomenon; Second, because of the tower crane safety can not be found in time For example,Took place in the tower crane foundation tilt, micro-cracks appear critical weld, bolts loosening the case of failure to make timely inspection, maintenance, resulting in the continued use of tower cranes in the process of further deterioration of the potential defect, eventually leading to the tower crane tipping. The current limit of tower crane and the black box and can not be found to connect slewing tower and high-strength bolts loosening tightened after the phenomenon is not timely, not tower verticality of the axis line of the lateral-line real-time measurement, do not have to fight the anti-rotation vehicles, lifting bodies plummeted Meng Fang, hook hoists inclined cable is a timely reminder and record of the function, the wind can not be contained in the state of suspended operation to prevent tipping on the necessary tips on site there is a general phenomenon of the overloaded overturning of the whole security risks can not be accurately given a reminder and so on, all of which the lease on the tower crane, use, management problems,Through the use of tower crane anti-tipping monitor to be resolved. Tower crane anti-tipping Monitor is a new high-tech security monitoring equipment, and its principle for the use of machine vision technology and image processing technology to achieve the measurement of the tilt tower, tower crane on the work of state or non-working state of a variety of reasons angle of the tower caused by the critical state to achieve the alarm, prompt drivers to stop illegal operation, a computer chip at the same time on the work of the state of tower crane be recorded. Tower crane at least 1 day overload condition occurs, a maximum number of days to reach 23 overloading, the driver to operate the process of playing the anti-car, stop hanging urgency, such as cable-stayed suspended oblique phenomenon often, after verification and education, to avoid the possible occurrence of fatal accidents. Wind conditions in the anti-tipping is particularly important, tower cranes sometimes connected with the pin hole and pin do not meet design requirements, to connect high-strength bolts are not loose in time after the tightening of the phenomenon, through timely maintenance in time after the tightening of the phenomenon, through timely maintenance and remedial measures to ensure that the safe and reliable construction progress. Reduced lateral line tower vertical axis measuring the number of degrees,Observation tower angle driver to go to work and organize the data once a month to ensure that the lateral body axis vertical line to meet the requirements, do not have to every time and professionals must be completed by Theodolite tower vertical axismeasuring the lateral line, simplified the management link. Data logging function to ensure that responsibility for the accident that the scientific nature to improve the management of data records for the tower crane tower crane life prediction and diagnosis of steel structures intact state data provides a basis for scientific management and proactive prevention of possible accidents, the most important thing is, if the joint use of the black box can be easily and realistically meet the current provisions of the country's related industries. Tower crane safety management at the scene of great importance occurred in the construction process should be to repair damaged steel, usually have to do a good job in the steel tower crane maintenance work and found that damage to steel structures, we must rule out potential causes of accidents, to ensure safety in production carried out smoothly. Tower crane in the building construction has become essential to the construction of mechanical equipment, tower crane at the construction site in the management of safety in production is extremely important. A long time, people in the maintenance of tower crane, only to drive attention to the conservation and electrical equipment at the expense of inspection and repair of steel structures, to bring all kinds of construction accidents.Conclusion: The tower crane anti-tipping trial monitor to eliminate potential causes of accidents to provide accurate and timely information, the tower crane to ensure the smooth development of the leasing business, the decision is correct, and should further strengthen and standardize the use of the environment (including new staff training and development of data processing system, etc.).The first construction cranes were probably invented by the Ancient Greeks and were powered by men or beasts of burden, such as donkeys. These cranes were used for the construction of tall buildings. Larger cranes were later developed, employing the use of human treadwheels, permitting the lifting of heavier weights. In the High Middle Ages, harbour cranes were introduced to load and unload ships and assist with their construction – some were built into stone towers for extra strength and stability. The earliest cranes were constructed from wood, but cast iron and steel took over with the coming of the Industrial Revolution.For many centuries, power was supplied by the physical exertion of men or animals, although hoists in watermills and windmills could be driven by the harnessed natural power. The first 'mechanical' power was provided by steam engines, the earliest steam crane being introduced in the 18th or 19th century, with many remaining in use well into the late 20th century. Modern cranes usually use internal combustion engines or electric motors and hydraulic systems to provide a much greater lifting capability than was previously possible, although manual cranes are still utilised where the provision of power would be uneconomic.Cranes exist in an enormous variety of forms – each tailored to a specific use. Sizes range from the smallest jib cranes, used inside workshops, to the tallest tower cranes,used for constructing high buildings, and the largest floating cranes, used to build oil rigs and salvage sunken ships.This article also covers lifting machines that do not strictly fit the above definition of a crane, but are generally known as cranes, such as stacker cranes and loader cranes.The crane for lifting heavy loads was invented by the Ancient Greeks in the late 6th century BC. The archaeological record shows that no later than c.515 BC distinctive cuttings for both lifting tongs and lewis irons begin to appear on stone blocks of Greek temples. Since these holes point at the use of a lifting device, and since they are to be found either above the center of gravity of the block, or in pairs equidistant from a point over the center of gravity, they are regarded by archaeologists as the positive evidence required for the existence of the crane.The introduction of the winch and pulley hoist soon lead to a widespread replacement of ramps as the main means of vertical motion. For the next two hundred years, Greek building sites witnessed a sharp drop in the weights handled, as the new lifting technique made the use of several smaller stones more practical than of fewer larger ones. In contrast to the archaic period with its tendency to ever-increasing block sizes, Greek temples of the classical age like the Parthenon invariably featured stone blocks weighing less than 15-20 tons. Also, the practice of erecting large monolithic columns was practically abandoned in favour of using several column drums.Although the exact circumstances of the shift from the ramp to the crane technology remain unclear, it has been argued that the volatile social and political conditions of Greece were more suitable to the employment of small, professional construction teams than of large bodies of unskilled labour, making the crane more preferable to the Greek polis than the more labour-intensive ramp which had been the norm in the autocratic societies of Egypt or Assyria.The first unequivocal literary evidence for the existence of the compound pulley system appears in the Mechanical Problems (Mech. 18, 853a32-853b13) attributed to Aristotle (384-322 BC), but perhaps composed at a slightly later date. Around the same time, block sizes at Greek temples began to match their archaic predecessors again, indicating that the more sophisticated compound pulley must have found its way to Greek construction sites by then.During the High Middle Ages, the treadwheel crane was reintroduced on a large scale after the technology had fallen into disuse in western Europe with the demise of the Western Roman Empire. The earliest reference to a treadwheel (magna rota) reappears in archival literature in France about 1225, followed by an illuminated depiction in a manuscript of probably also French origin dating to 1240. In navigation, the earliest uses of harbor cranes are documented for Utrecht in 1244, Antwerp in 1263, Brugge in 1288 and Hamburg in 1291, while in England the treadwheel is not recorded before 1331.Generally, vertical transport could be done more safely and inexpensively by cranes than by customary methods. Typical areas of application were harbors, mines, and, in particular, building sites where the treadwheel crane played a pivotal role in the construction of the lofty Gothic cathedrals. Nevertheless, both archival and pictorial sources of the time suggest that newly introduced machines like treadwheels or wheelbarrows did not completely replace more labor-intensive methods like ladders, hods and handbarrows. Rather, old and new machinery continued to coexist on medieval construction sites and harbors.Apart from treadwheels, medieval depictions also show cranes to be powered manually by windlasses with radiating spokes, cranks and by the 15th century also by windlasses shaped like a ship's wheel. To smooth out irregularities of impulse and get over 'dead-spots' in the lifting process flywheels are known to be in use as early as 1123.The exact process by which the treadwheel crane was reintroduced is not recorded, although its return to construction sites has undoubtedly to be viewed in close connection with the simultaneous rise of Gothic architecture. The reappearance of the treadwheel crane may have resulted from a technological development of the windlass from which the treadwheel structurally and mechanically evolved. Alternatively, the medieval treadwheel may represent a deliberate reinvention of its Roman counterpart drawn from Vitruvius' De architectura which was available in many monastic libraries. Its reintroduction may have been inspired, as well, by the observation of the labor-saving qualities of the waterwheel with which early treadwheels shared many structural similarities.In contrast to modern cranes, medieval cranes and hoists - much like their counterparts in Greece and Rome - were primarily capable of a vertical lift, and not used to move loads for a considerable distance horizontally as well. Accordingly, lifting work was organized at the workplace in a different way than today. In building construction, for example, it is assumed that the crane lifted the stone blocks either from the bottom directly into place, or from a place opposite the centre of the wall from where it could deliver the blocks for two teams working at each end of the wall. Additionally, the crane master who usually gave orders at the treadwheel workers from outside the crane was able to manipulate the movement laterally by a small rope attached to the load. Slewing cranes which allowed a rotation of the load and were thus particularly suited for dockside work appeared as early as 1340. While ashlar blocks were directly lifted by sling, lewis or devil's clamp (German Teufelskralle), other objects were placed before in containers like pallets, baskets, wooden boxes or barrels.It is noteworthy that medieval cranes rarely featured ratchets or brakes to forestall the load from running backward.[25] This curious absence is explained by the high friction force exercised by medieval treadwheels which normally prevented the wheel from accelerating beyond control.目前,塔式起重机是建筑工程进行起重运输作业的重要设备,塔机事故关系国计民生、危害重大,而目前众多的塔机司机虽然有上岗证,由于缺少监督和复核手段,实际工作中违规严重。
机械专业毕业设计外文翻译--机械传动系统介绍

Transmission System introducedThe important position of the wheel gear and shaft can’t falter in traditional machine and modern machines. The wheel gear and shafts mainly install the direction that delivers the dint at the principal axis box. The passing to process to make them can is divided into many model numbers, used for many situations respectively. so we must be the multilayers to the understanding of the wheel gear and shaft in many ways.In the force analysis of spur gears, the forces are assumed to act in a single plane. We shall study gears in which the forces have three dimensions. The reason for this, in the case of helical gears, is that the teeth are not parallel to the axis of rotation. And in the case of bevel gears, the rotational axes are not parallel to each other. There are also other reasons, as we shall learn.Helical gears are used to transmit motion between parallel shafts. The helix angle is the same on each gear, but one gear must have a right-hand helix and the other a left-hand helix. The shape of the tooth is an involute helicoid. If a piece of paper cut in the shape of a parallelogram is wrapped around a cylinder, the angular edge of the paper becomes a helix. If we unwind this paper, each point on the angular edge generates an involute curve. The surface obtained when every point on the edge generates an involute is called an involute helicoids.The initial contact of spur-gear teeth is a line extending all the way across the face of the tooth. The initial contact of helical gear teeth is a point, which changes into a line as line as the teeth come into more engagement. In spur gears the line of contact is parallel to the axis of the rotation; in helical gears, the line is diagonal across the face of the tooth. It is this gradual of the teeth and the smooth transfer of load from one tooth to another, which give helical gears the ability to transmit heavy loads at high speeds. Helical gears subject the shaft bearings to both radial and thrust loads. When the thrust loads become high or are objectionable for other reasons, it may be desirable to use double helical gears. A double helical gear (herringbone) is equivalent to two helical gears of opposite hand, mounted side by side on the same shaft. They develop opposite thrust reactions and thus cancel out the thrust load. When two or more single helical gears are mounted on the same shaft, the hand of the gears should be selected so as to produce the minimum thrust load.Crossed-helical, or spiral, gears are those in which the shaft centerlines are neither parallel nor interesting. The teeth of crossed-helical fears have point contact with each other which changes to line contact as the gears wear in. for this reason they will carry out very small loads and are mainly for instrumental applications, and are definitely not recommended for use in the transmission of power. There is on difference between a crossed helical gear and a helical gear until they are mounted in mesh with each other. They are manufactured in the same way. A pair of meshed crossed helical gears usually have the same hand; that is, a right-hand driver goes with a right-hand driven. In the design of crossed-helical gears, the minimum sliding velocity is obtained when the helix angle are equal. However, when the helix angle are not equal, the gear with the larger helix angle should be used as the driver if both gears have the same hand.Worm gears are similar to crossed helical gears. The pinion or worm has a small number of teeth, usually one to four, and since they completely wrap around the pitch cylinder they are called threads. Its mating gear is called a worm gear, which is not a true helical gear. A worm and worm gear are used to provide a high angular-velocity reduction between nonintersecting shafts which are usually at right angle. The worm gear is not a helical gear because its face is made concave to fit the curvature of the worm in order to provide line contact instead of point contact. However, a disadvantage of worm gearing is the high sliding velocities across the teeth, the same as with crossed helical gears.Worm gearing are either single or double enveloping. A single-enveloping gearing is one in which the gear wraps around or partially encloses the worm. A gearing in which each element partially encloses the other is, of course, a double-enveloping worm gearing. The important difference between the two is that area contact exists between the teeth of double-enveloping gears while only line contact between those of single-enveloping gears. The worm and worm gear of a set have the same hand of helix as for crossed helical gears, but the helix angles are usually quite different. The helix angle on the worm is generally quite large, and that on the gear very small. Because of this, it is usual to specify the lead angle on the worm, which is the complement of the worm helix angle, and the helix angle on the gear; the two angles ate equal for a 90-deg. Shaft angle.When gears are to be used to transmit motion between intersecting shaft, some ofbevel gear is required. Although bevel gear are usually made for a shaft angle of 90 deg. They may be produced for almost any shaft angle. The teeth may be cast, milled, or generated. Only the generated teeth may be classed as accurate. In a typical bevel gear mounting, one of the gear is often mounted outboard of the bearing this means that shaft deflection can be more pronounced and have a greater effect in the contact of teeth. Another difficulty, which occurs in predicting the stress in bevel-gear teeth, is the fact the teeth are tapered.Straight bevel gears are easy to design and simple to manufacture and give very good results in service if they are mounted accurately and positively. As in the case of squrgears, however, they become noisy at higher values of the pitch-line velocity. In these cases it is often good design practice to go to the spiral bevel gear, which is the bevel counterpart of the helical gear. As in the case of helical gears, spiral bevel gears give a much smoother tooth action than straight bevel gears, and hence are useful where high speed are encountered.It is frequently desirable, as in the case of automotive differential applications, to have gearing similar to bevel gears but with the shaft offset Such gears are called hypoid gears because their pitch surfaces are hyperboloids of revolution The tooth action between such gears is a combination of rolling and has much in common with that of worm gears.A shaft is a rotating or stationary member usually of circular cross section, having mounted upon it such elementsas gears pulleys flywheels, cranks sprockets and other power-transmission elements Shaft may be subjected to bending tension compression or torsional loads acting singly or in combination with one another .When they are combined one may expect to find both static and fatigue strength to be important design considerations since a single shaft may be subjected to static stresses completely reversed, and repeated stresses, all acting at the same timeThe word “shaft” covers numerous wariations, such as axles and spindles. Anaxle is a shaft, wither stationary or rotating nor subjected to torsion load. Ashirt rotating shaft is often called a spindle.When either the lateral or the tosional deflection of shaft must be held to close limits, the shaft must be sized on the basis of deflection before analyzing the stresses The reasonfor this is that if the shift is made stiff enough so that the deflection is not too large, it is probable that the resulting stresses will be safe. But by no means should the designer assume that they are within acceptable limits. Whenever possible the power-transmission elements such as gears or pullets, should be located close to the supporting bearings. This reduces the bending moment, and hence the deflection and bending stress.Although the von Mises-Hencky-Goodman method is difficult to use in design of shaft, it probably come closest to predicting actual failure. Thus it is a good way of checking a shaft that has already been designed or of discovering why a particular shaft that has already been designed or of discovering why a particular shaft has failed in service. Furthermore, there are a considerable number of shaft-design problems in which the dimension are pretty well limited by other considerations, such as rigidity, and it is only necessary for the designer to discover something about the fillet sizes, heat-treatment, and surface finish and whether or not shot peening is necessary in order to achieve the required life and reliability.Because of the similarity of their functions, clutches and brakes are treated together. In a simplified dynamic representation of a friction clutch, or brake, two inertias I1and I2 traveling at the respective angular velocities W1 and W2, one of which may be zero in the case of brake, are to be brought to the same speed by engaging the clutch or brake. Slippage occurs because the two elements are running at different speeds and energy is dissipated during actuation, resulting in a temperature rise. In analyzing the performance of these devices we shall be interested in the actuating force, the torque transmitted, the energy loss and the temperature rise. The torque transmitted is related to the actuating force, the coefficient of friction, and the geometry of the clutch or brake. This is problem in static, which will have to be studied separately for each geometric configuration. However, temperature rise is related to energy loss and can be studied without regard to the type of brake or clutch because the geometry of interest is the hear-dissipating surfaces. The various types of clutches and brakes may be classified as fallows:Rim type with internally expanding shoesRim type with internally contracting shoesBand typeDisk or axial typeCone typeMiscellaneous typeThe analysis of all type of friction clutches and brakes use the same general procedure. The following step are necessary:1. Assume or determine the distribution of pressure on the frictionalsurfaces.2. Find a relation between the maximum pressure and the pressure at any point3. apply the condition of statical equilibrium to find (a) the actuating force, (b) the torque, and (c) the support reactions.Miscellaneous clutches include several type, such as the positive-contact clutches, overload-release clutches, overrunning clutches, magnetic fluid clutches, and others.A positive-contact clutch consists of a shift lever and two jaws. The greatest differences between the various types of positive clutches are concerned with the design of the jaws. To provide a longer period of time for shift action during engagement, the jaws may be ratchet-shaped, or gear-tooth-shaped. Sometimes a great many teeth or jaws re used, and they may be cut either circumferentially, so that they engage by cylindrical mating, or on the faces of the mating elements.Although positive clutches are not used to the extent the frictional-contact type, they do have important applications where synchronous operation is required.Devices such as linear driver or motor-operated screw drivers must run to definite limit and then come to a stop. An over load-release rype of clutch is required for these applications. These clutches are usually spring-loaded so as to release at a predetermined toque. The clicking sound which is heard when the overload point is reached is considered to be a desirable signal.An overrunning clutch or coupling permits the driven member of a machine to “freewheel” or “overrun” because the driver is stopped or because another source of power increase the speed of the driven. This type of clutch usually uses rollers or balls mounted between an outer sleeve and an inner member having flats machined around the periphery. Driving action is obtained by wedding the rollers between the sleeve and the flats. The clutch is therefore equivalent to a pawl and ratchet with an infinite number of teeth.Magnetic fluid clutch or brake is a relatively new development which has two parallel magnetic plates. Between these plates is a lubricated magnetic powder mixture. An electromagnetic coil is inserted somewhere in the magnetic circuit. Bu varying the excitation to this coil, the shearing strength of the magnetic fluid mixture may be accurately controlled. Thus any condition from a full slip to a frozen lockup may be obtained.机械传动系统介绍在传统机械和现代机械中齿轮和轴的重要地位是不可动摇的。
毕业设计(论文)外文资料翻译【范本模板】

南京理工大学紫金学院毕业设计(论文)外文资料翻译系:机械系专业:车辆工程专业姓名:宋磊春学号:070102234外文出处:EDU_E_CAT_VBA_FF_V5R9(用外文写)附件:1。
外文资料翻译译文;2.外文原文.附件1:外文资料翻译译文CATIA V5 的自动化CATIA V5的自动化和脚本:在NT 和Unix上:脚本允许你用宏指令以非常简单的方式计划CATIA。
CATIA 使用在MS –VBScript中(V5.x中在NT和UNIX3。
0 )的共用部分来使得在两个平台上运行相同的宏。
在NT 平台上:自动化允许CATIA像Word/Excel或者Visual Basic程序那样与其他外用分享目标。
ATIA 能使用Word/Excel对象就像Word/Excel能使用CATIA 对象。
在Unix 平台上:CATIA将来的版本将允许从Java分享它的对象。
这将提供在Unix 和NT 之间的一个完美兼容。
CATIA V5 自动化:介绍(仅限NT)自动化允许在几个进程之间的联系:CATIA V5 在NT 上:接口COM:Visual Basic 脚本(对宏来说),Visual Basic 为应用(适合前:Word/Excel ),Visual Basic。
COM(零部件目标模型)是“微软“标准于几个应用程序之间的共享对象。
Automation 是一种“微软“技术,它使用一种解释环境中的COM对象。
ActiveX 组成部分是“微软“标准于几个应用程序之间的共享对象,即使在解释环境里。
OLE(对象的链接与嵌入)意思是资料可以在一个其他应用OLE的资料里连结并且可以被编辑的方法(在适当的位置编辑).在VBScript,VBA和Visual Basic之间的差别:Visual Basic(VB)是全部的版本。
它能产生独立的计划,它也能建立ActiveX 和服务器。
它可以被编辑。
VB中提供了一个补充文件名为“在线丛书“(VB的5。
机械毕业设计中英翻译

英语原文:CAD/CAM is the technical expression, indicates the computer-aided design and the computer aided manufacturing.This is one item in the design and the production, carries out certain function technology about the use computer data.This technology is completing the design and the production direction to the place develops.In these two traditions was considered is in the production process out of the ordinary, independent function.In brief, CAD/CAM will be able to provide the technology base for the future complete computer production.Looked from the computer science angle that, the design and the manufacture process is one has, processing, the exchange and the management process about the product information.The people use the computer to take the main technical method, from forms in one's mind to the product to put in the market in the entire process information to carry on the analysis and processing, produces and utilizes each kind of numerical information and the graph information, carries on the product the design and the manufacture.The CAD/CAM technology is not the traditional design, the manufacture flow method simple reflection, also is not limits in the partial use computer takes the tool in the individual step or the link, but is unifies the computer science and the project domain specialized technology as well as human's wisdom and the experience take the modern scientific method as the instruction, in the design, in the manufacture entire process each completely manager, as far as possible use computer system completes the work which these duplication high, the labor big, the computation complex as well as depends on purely artificially completes with difficulty, but assists must replaces the engineers and technicians to complete the entire process, obtains the desired effec The CAD/CAM system as well as plans the hardware, the software for supports the environment, (subsystem) realizes through each function module to the product description, the computation, the analysis, optimized, the cartography, the technological process design, the simulation as well as the NC processing.But the generalized CAD/CAM integrative system also should include aspects and so on production plan, management, quality control.Since 1946 first electronic accounting machine has been born in US, people on unceasing computer technology Introduces the machine design? Manufacture domain.As early as in the 50's, for the first time develops successfully the numerical control engine bed, may realize through the different numerical control procedure to the different components processing Afterwards, Massachusetts Institute of Technology's servo laboratory succeeds with the computer manufacture numerical control paper tape, has realized the NC programming automation.In this foundation, the people proposed the following tentative plan: The APT software is feeds the path method realization computer assistance programming through the description, that, can not describe feeds the path, but is direct description components itself? From this has had the CAD initial concept.The entire 50's, the electronic accounting machine also is in the electron tube time, uses the machine language programming, the computer mainly uses in thescience computation, also only has the output function for it disposition graph equipment.CADCAM system basic compositionCAD/CAM system hardware dispositionCAD/CAM system software compositionCAD/CAM system software dispositionComputer aided manufacturing (CAM) may define for uses the computer system to design, to manage and controls a productive plan the movement, through direct or indirect planned production resources computer contact surface.If defines states, the computer aided manufacturing application has 2 big aspects:1) computer supervisory control.This is the direct application, the computer with the production process connection, uses in supervising directly and the control production process2) produces the support application.This is the indirect application, middle the productive plan, the computer uses in supporting the production operation, but is not the computer and the production process links directly.Charting productive forces increaseThe CAD/CAM system may undertake the one whole set new charting theory to be able to strengthen the productivity.Again completes next step, keeps firmly in mind the entire design to be possible to store up the system.When the planner receives one with has saved the blueprint specification similar work piece, he only must recollect, and adjusts it the work storage place, revises in the original blueprint not to conform to a new work piece request part, productivity enhances.The original work piece efficiency enhances, but this can enhance the next step working efficiency.This is a complete at times renewal database support, can facilitate the user to use Improve mapping analysisThe charting analysis is another important work, it can by certain synthesize the CAD/CAM system automatic operation.This in pipeline design, in particular an important application.The pipeline design paper very is usually complex moreover must conform to the precise industry specification.The other giftedCAD/CAM also can affect a company in other aspects the project system.It can enhance the entire physical process the efficiency, the permission present project plan and the report procedure appraisal.CAD/CAM can improve improves the quality of the product the guarantee technology.It can automatic accurate and the integrity document material, the maintenance partial data accurate and bill of materials accurate.DeficiencyCAD/CAM insufficient spot not that obvious, but they can destroy even the most perfect design, the biggest shortcoming is only can directly skips from the manual charting and the recordpreservation to CAD/CAM, the elephant installs a set of jet engine in the populace automobile.The automobile possibly can run quick somewhat, but if the foundation enhancement has not coordinated the heavy pressure, the entire automobile can disperse the frame.CAD/CAM applicationSKETCHPAD, the CAD/CAM technology has passed through very long chi.It is already applied in the middle of each widespread industry.It uses in each aspect, controls from the airplane to the weapon research, manufactures from the map to the movement medical service, from circuit analysis to building steel analysis.CAD/CAM is being applied in each kind of charting and the production, installs the schematic diagram from the movie to the large-scale long-distance monitoring direct set battleship, its application to is developing variously.Now CAD/CAM market.Now in the market has four kind of different CAD/CAM sellers.First is some subordinate companies sells comes from a big enterprise part or the branch CAD/CAM technology.The IBM CAD/CAM branch is an example.If belongs to Mc-Donnell-Douglas McAuto; Belongs to General Electric Lalma, with belongs to Schlumberger Applican, if the multi-large number CAD/CAM subordinate company the main corporation has the massive service intercourse, not only sale supervisory system moreover when one's position is lowly one's words carry no weight service office.When they control the massive accounts also with provides the service, these companies on in optimum condition, because they may extract the massive profits.But they must undertake the complex administrative chain of command, this obstructs in them makes the fast response to the market tendency, or their itself studies and outside the development department, the merge improves on again their new production line the new technical developmentCAD/CAM technology and the product development road of futureAfter many year promotions, the CAD technology already widely applied in professions and so on machinery, electron, astronautics, chemical industry, building.Played using the CAD technology enhanced the enterprise the rated capacity, the optimization design proposal, reduces technical personnel's labor intensity, reduction design cycle, beefed-up design roles and so on standardization.In recent years, our country CAD technology development and the application have obtained the considerable development, besides has carried on sinicizing and the re-development to many overseas softwares, but also was born many had the independent copyright CAD system, If high Chinese CAD, opens item CAD and so on, because these software price is cheap, conforms to our country national condition and the standard, therefore has received widespread welcome, has won the more and more big market share. But, our country CAD/CAM software no matter is from the product development level from the commercialization, the marketability degree all has not the small disparity with the developed country.Because the overseas CAD/CAM software appears early, the development and the application time is also long,therefore they develop quite maturely, now basically already has seized the international market.These overseas software company uses its technical and the fund superiority, starts vigorously to our country market march At present, the overseas some outstanding softwares, like UG, SolidWorks, Pro/Engineer, CATIA and so on, already have seized part of domestic markets.Therefore, our country CAD/CAM software prospect is unoptimistic.But, we also should see clearly own superiority, for instance understood our country market, provides the technical support to be convenient, price small advantage and so on.Not only under these premises, we importantly with the trend of the times, the track international newest tendency, observe each international standard, in international domestic forms the oneself unique superiority, must base the home, the union national condition, face the domestic economic development need,develops has oneself characteristic, conforms to CAD/CAM software which the Chinese is familiar with.。
- 1、下载文档前请自行甄别文档内容的完整性,平台不提供额外的编辑、内容补充、找答案等附加服务。
- 2、"仅部分预览"的文档,不可在线预览部分如存在完整性等问题,可反馈申请退款(可完整预览的文档不适用该条件!)。
- 3、如文档侵犯您的权益,请联系客服反馈,我们会尽快为您处理(人工客服工作时间:9:00-18:30)。
附录A一、创建焊接程序[焊缝的示教]。
焊接机器人程序编辑1、打开控制柜上的电源开关在“ON”状态。
2、将运作模式调到“TEACH”→“示教模式下”1.进入程序编辑状态:1.1.先在主菜单上选择[程序]一览并打开;1.2.在[程序]的主菜单中选择[新建程序]1.3.显示新建程序画面后按[选择]键1.4.显示字符画面后输入程序名现以“TEST”为新建程序名举例说明;1.5.把光标移到字母“T”、“E”“S”、“T”上按[选择]键选中各个字母;1.6.按[回车]键进行登录;1.7.把光标移到“执行”上并确认后,程序“TEST”被登录,并且屏幕画面上显示该程序的初始状态“NOPCEOO”、“ENDCOOL”1.8.编辑机器人要走的轨迹(以机器人焊接直线焊缝为例);2.把机器人移动到离安全位置,周边环境便于作业的位置,输入程序(001);2.1. 握住安全电源开关,接通伺服电源机器人进入可动作状态;2.2.用轴操作键将机器人移动到开始位置(开始位置电影摄制在安全病史和作业准备位置);2.3.按[插补方式]键,把插补方式定为关节插补,输入缓冲显示行中显示关节插补命令,‘M OVJ“→”“MOVJ,,VJ=0.78”2.4.光标放在“00000”处,按[选择]键;2.5.把光标移动到右边的速度“VJ=**”上,按[转换]键+光标“上下”键,设定再现速度,若设定速度为 50%时,则画面显示“→MOUVJ VJ=50%”,也可以把光标移到右边的速度,‘VJ=***' 上按[选择]键后,可以直接在画面上输入要设定的速度,然后按[回车]键确认。
2.6.按[回车]键,输入程序点(即行号 0001)3.决定机器人的作业姿态(作业开始位置的附近)3.1.用轴操作键,使机器人姿态成为作业姿态,然后移到相应的位置;3.2.按[回车]键,输入程序点 2(0002);3.3.保持程序点 2 的姿态不变,移向作业开始位置;3.3.1.保持程序点 2 的姿态不便,按[坐标]键,设定机器人坐标为直角坐标系,用轴操作键把机器人移到作业开始的位置(在移动前可以按手动速度[高][低]键选择焊枪在示教中移动的速度);3.3.2.光标在行号 0002 处按[选择]键3.3.3.把光标移动到右边的速度,VJ=***上按[转换]+光标”上下键,设定再现速度,直到设定的速度为所需速度(也可用光标移到速度 VJ=***上,按[选择]键后,输入需要的速度值,按 [回车]键确认即可);3.3.4.按[回车]键,输入程序点 3(行号 0003);3.3.4.1.把光标移动到“0003”上,按[引弧]键+[回车]键,输入“引弧”指令(行0004)(“引弧” 为“ARCON”)3.3.4.2.把光标移动到行号 0003 上按[引弧]键,在缓冲显示区显示出“ARCON’”指令以及引弧时的条件;3.3.4.3.对引弧指令中的附加引弧条件根据焊接工件的实际情况进行修改; 3.3.4.4.按[回车]键输入“引弧”指令(行号 0004);3.3.4.5.指定作业点位置(作业结束位置)3.3.4.6.用轴操作键把机器人移到焊接作业结束位置从作业开始位置到结束位置不必精确沿焊缝运动,为防止不碰撞工件移动轨迹可远离工件;3.3.4.7.按[插补方式]键,插补方式设定为直线插补(MOVL)亦可把光标放在“MOVJ”上,按[选择]键,然后按[转换]+光标上下键可以调整选择插补方式,然后按[回车]键;3.3.4.8.光标在行号 0004 上按[选择]键;3.3.4.9.把光标移到右边速度“V=***”上,按[转换]+光标上下键设定速度;3.3.4.10.按[回车]键,输入程序点 4(行号 0005); 3.4.按[收弧]键输入(收弧命令为“ARCOF”)3.5.把机器人移到不碰撞工件和夹具的位置;3.5.1.按手动速度[高]键,设定为高速(手动速度[高]键只是显示示教时的速度,再现中以定义的速度运行);3.5.2.用轴操作键把机器人移到不碰撞夹具的位置;3.5.3.按[插补方式]键,设定插补方式为关节插补(MOVJ);3.5.4.光标在行号 0006 上,按[选择]键→MOVJ VJ=15;3.5.5.把光标移到右边的速度 VJ=15 上,按[转换]+上下键,设定速度(也可按[选择]键后,直接输入要设定的速度,再按[回车]键登录速度;3.5.6.按[回车]键,输入程序点(行 0007)3.6.把机器人移到开始位置上;3.6.1 把光标返回到 0001 上,按[前进]键把机器人移动到程序点 1 上;3.6.2.再把光标移到行号 0007 上,按[回车]键,输入程序点 8(行 0008)二、确认所设定的程序中的轨迹操作; 1、把光标移到程序点 0001 上; 2、按手动速度[高][低]键设定速度键; 3、按[前进]键,通过机器人动作确认各程序点,每按一次[前进]键机器人移动到一个程序点; 4、亦可把光标移到程序点行 0001 上,按[连锁]+[试运行]键,机器人连续再现所有程序点,一个循环后停止运作;三、在焊接中,往往有时设定好的程序有许多与实际生产不适合,所以需要进行修该程序(包括又插入程序点、删除程序点、修改程序点的位置数据等); 1、插入程序点; 1.1.把程序内容打开(以在程序点 3、4、之间插入为列); 1.2.按[前进]键,除]键; 2.3.按[回车]键,程序点 3 被删除; 3、修改程序点的位置数据(以程序点 3 位列); 3.1.把光标移到程序点 3 上; 3.2.按[前进]键,使机器人回到程序点3 上; 3.3.用轴操作键把机器人移到修改后的位置; 3.4.按[修改]键; 3.5.按[回车]键,程序点的位置数据被修改; 4、设定焊接条件:(ARCON ARCOF ARCOF); 4.1.先打开程序内容; 4.2.把光标移到要进行焊接作业的程序点的前一个行号上; 4.3.按[引弧]键或[命令一览]键中选择程序[作业]中选择 ARCON 命令,缓冲显示区有 AR CON 指令及附加条件; 4.4.按[回车]键‘引弧“命令自动在程序中生成; 4.5.设定引弧条件的方式有三种(一、把各种条件作为附加项进行设定的方法,二、使用引弧文件的方法 ASF#(X),三、不带附加项) 5.用附加项设定焊接条件的方法; 5.1.在命令区选择 ARCON 指令,(缓冲区显示 ARCON 指令); 5.2.按[选择]键(显示详细编辑画面,选择“未使用”; 5.3.选择“未使用”(显示选择对话框); 5.4.选择“AC=**(在 ARCON 命令的附加项中已设定引弧条件时,显示详细编辑画面); 5.5.输入焊接条件(设定每个焊接条件); 5.6.按[回车]键(设定的内容显示在输入缓冲区中); 5.7.按[回车]键设定的内容登录到程序中; 5.8.不想登录设定的程序时,按[清除]键,回到程序内容画面; 6.使用引弧条件文件; 6.1.在命令区选择 ARCON 命令,(输入缓冲行显示 ARCON 命令); 6.2.按[选择]键,(显示详细编辑画面); 6.3.选择“未使用‘(显示选择对话框); 6.4.选择 ASF#() (显示详细编辑画面); 6.5.设定文件号(指定文件号 1~64 把光标移到文件号上,按[选择]键→用数值输入文件号按[回车]键; 6.6.按[回车]键,(设定的内容显示在输入行中); 6.7.按[回车]键,(设定的内容登录到程序中); 6.8.不想登录设定的文件内容时,按[清除]键,回到程序内容画面; 7.没有附加项的方法; 7.1.选择命令区 ARCON 命令(输入缓冲行显示 ARCON 的命令); 7.2.按[选择]键(显示详细编辑画面); 7.3.选择 ASF#() (显示选择对话框); 7.4.选择‘未使用“; 7.5.选择[回车]键,设定的内容在输入缓冲行中; 7.6.按[回车]键,设定的内容登录到程序中; 7.7.不想登录设定的内容时,按[清除]键,回到程序内容画面;四、分别设定焊接条件(电流、电压命令); 1.登录 AECSET 命令; 1.1.把光标移到地址区; 1.2.按[命令一览]键(显示命令一览对话框); 1.3.选择“作业”; 1.4.选择 ARCSET 命令(输入缓冲显示 ARCSET 命令);1.5.按[选择]键(显示详细编辑画面); 1.6.设定焊接条件(把光标移动到设定的项目上,按[选择]键,用数值键输入焊接条件,再按[回车]键,追加附加项时,在选择对话框中选择“未使用”删除附加项时也同样把光标移到想删除的附加项上,按[选择]键选择“未使用”; 1.7.按[回车]键(所设定的内容显示在缓冲区行); 1.8.按[回车]键把机器人移动到程序点 3 上; 1.3.用轴操作键把机器人移到想插入位置; 1.4.按[插入]键; 1.5.按[回车]键完成程序点插入,所插入程序点行号为(0004), 2、删除程序点(以 3、4 位列);2.1.按[前进]键,把机器人移到要删除的程序点 3 上;2.2.按[删(设定的内容被输入到程序中,当不想登录设定的内容时,按[清除]键,回到程序内容画面); 2.设定熄弧条件(填弧坑处理); 1.按[熄弧]键,输入熄弧命令(利用[命令一览]键进行 AECOF 命令登录时,选择命令中的“作业”; 2.登录ARCOF 方法; 2.1.按[熄弧]键 2.2.按[回车]键; 2.3.设定熄弧条件(ARCOF 有三种方法;一、把各种条件作为附加项进行设定;二、使用熄弧条件方法;三、不带附加项); 3.各条件设定为附加项的方法; 3.1.选择命令区的 ARCOF 命令(输入缓冲区显示 ARCOF 命令); 3.2.按[选择]键(显示详细编辑画面); 3.3.选择“未使用”(显示选择对话框); 3.4.选择“AC=”; 3.5.输入焊接收弧条件(设定各个焊接条件);3.6.按[回车]键(输入缓冲区行显示设定的条件); 3.7.按[回车]键(设定的内容被登录到程序中); 3.8.不想登录设定的内容时,按[清除]键,回到程序内容画面;4.使用熄弧条件方法; 4.1.选择命令区的 ARCOF 命令(输入缓冲行显示 ARCOF 命令);4.2.按[选择]键(显示详细的编辑画面); 4.3.选择“未使用”(显示选择对话框);4.4.选择“AEF#(); 4.5.设定文件号(1~12 把光标移到文件号上,按[选择]键确定用数值键输入文件号,按[回车] 键; 4.6.按[回车]键(设定的内容显示在输入缓冲行中); 4.7.按[回车]键(设定的内容被输入到程序中); 4.8.不想登录设定的内容时,按[清除]键,回到程序内容画面);五、不带附加项的内容; 1.选择命令区的ARCOF 命令(输入缓冲行显示 ARCOF 命令); 2.按[选择]键(显示详细编辑画面); 3.选择 AEF#()或 AC=*** (显示选择对话框); 4.选择‘未使用’; 5.按[回车]键(输入缓冲行显示设定的内容); 6.按[回车]键(设定的内容被输入到程序中); 7.不想登录设定的内容时,按[清除]键,回到程序内容画面; 8.确认动作(检查运行);把所设定的程序轨迹进行一次模拟实验,在再现模式中,调出‘检查运行’一行进行轨迹确认; 9.在程序的再现画面按[区域]键; 10.选择[实用]工具栏; 11.选择设定的特殊运行户(显示特殊运行画面); 12.选择‘检车运行’(每次按[选择]键有效、无效、交替交换; 13.选择‘有效’字样; 14.打开[伺服电源]键; 15.把光标移到程序点 1 上按下[START]键,机器人自行检查; 16.焊接条件的微调;六、焊接条件的微调; 1、进行焊接利用已经调整好的程序; 2、从焊缝外观进行焊接条件的微调(根据焊缝成型情况对焊接电流、电压等进行调整);七、生产; 1、把运作模式设定在‘再现’模式; 2、选择主菜单的[程序]一行中子菜单[选择程序]并打开; 3、把光标移到要选择用于焊接的程序中; 4、进行程序轨迹检查运行; 5、当检查完后,把光标移到‘0001’上,运作模式设定为‘再现模式’按下‘START’进行焊接。