PLC在连铸机结晶器液位控制中的应用
关于PLC控制在钢厂连铸中的应用研究

紧 密流畅 , 为铸 件质 量提 高和 经济 效 益增 长作 出 了较大 贡献 。 1 PL C应 用 于 钢 水 连 铸 流 程
钢 厂 连铸 的 主 要任 务 是将 精 炼后 的钢 水连 续 铸造 成 钢坯 , 精
动 控制 , 效地 提高 了温 度控 制精 度 。 有
2 2 自动 定 尺 .
生 产过 程控 制还应 包 括对 设定 参数 的存 储 与修 改 ,对 日常操 作 的
监 控和 故障 的处 理和 记录 。因此 ,钢 厂连 铸 自动 化控 制 要求 P C L
系 统能 够实 时可靠 , 将多 工序 信 息建立 联 网 。 并 2 P c 控 制 主 要 电气 设 备 系 统 L
近 年来 , 编程 逻 辑控 制器 即 P C在 工业 自动 化 控制 系 统 [ 可 L { 】
得到 了普遍 运用 和快 速发 展 , 其操 作性 强 、 定 可靠 、 口多 样 、 稳 接 组
线 的组合 ,因此这 个 次 方程 依形 状 可 以简化 为几 乎重 合 的分段
式一 次 模拟 公式 :
式 中 , 为实 际铸坯 长度 ; 为修 正 系数 ; 为理 论铸坯 长 度 。 , J £ 修 正系 数 的选 取 至关 重 要 , 了根 据在 线 实际测 量 值来 进 除 行 判 断 , 要 通 过员 工 操 作时 , 量 最 终切 割 铸坯 长 度 , 程序 参 还 测 在 数 预 留修正 框 内输入 实 际数据 。 对整 个 定尺 系统 进行 二次 修 正 。 来 这 样主 要是 为 了防 止拉矫 系 统受 到其 他 因素 影响而 非 正常 工作 产
基于S7-300 PLC的结晶器液位控制系统设计

第37卷第4期 齐 齐 哈 尔 大 学 学 报(自然科学版) Vol.37,No.4 2021年7月 Journal of Qiqihar University(Natural Science Edition) July,2021基于S7-300 PLC的结晶器液位控制系统设计缸明义1,宁平华1,潘小波1,唐开元2,3(1.马鞍山职业技术学院 电气工程系,安徽 马鞍山 243031;2.中钢集团马鞍山矿山研究总院股份有限公司,安徽 马鞍山 243000;3.金属矿山安全与健康国家重点实验室,安徽 马鞍山 243000)摘要:针对连铸机的结晶液位采用拉速控制导致控制过程不稳定,影响铸坯质量的问题,提出了一种结晶器塞棒式流量控制方案,并进行了软硬件设计。
采用西门子S7系列的PLC完成了液位的PID闭环控制,并增加了自动开浇功能,完全实现系统的自动控制,提高生产效率和铸坯质量。
关键词:连铸;结晶器液位控制;PID中图分类号:TF341.6;TP273 文献标志码:A 文章编号:1007-984X(2021)04-0010-06连铸指的是通过连铸机来浇注钢液,并且进行冷凝以及后续的切割,由此得到铸坯。
所以连铸工艺的运行会影响整个炼钢生产过程,同时还将极大地影响到成材率及最终质量。
对于钢铁工业领域来说,连铸的作用是不可或缺的,所以目前也非常重视其模型构建以及工艺控制过程等的研究[1]。
其中,尤为值得关注的就是如何准确地检测结晶器中的液位并且予以合理控制的问题,因为如果液位发生波动,将会有保护渣被卷进液态钢里,由此对最终的铸坯质量造成影响,严重时还有可能发生钢液漏出或是溢出的现象[2-3]。
本文对此进行软硬件设计,采用流量控制法中的塞棒控制,在液位的调节过程中将拉速作为扰动,根据实际需要改变塞棒的开度,使结晶器液位稳定在给定值,很好地解决了控制系统不稳定的突出问题。
1 结晶器的工作原理由该部件之后,将会得以迅速且均匀的降温冷却,由此就有一个初生坯壳得以形成,它通常有较好的表面质量以及均匀的厚度,确保整个连铸过程得以完成。
结晶器液面自动控制
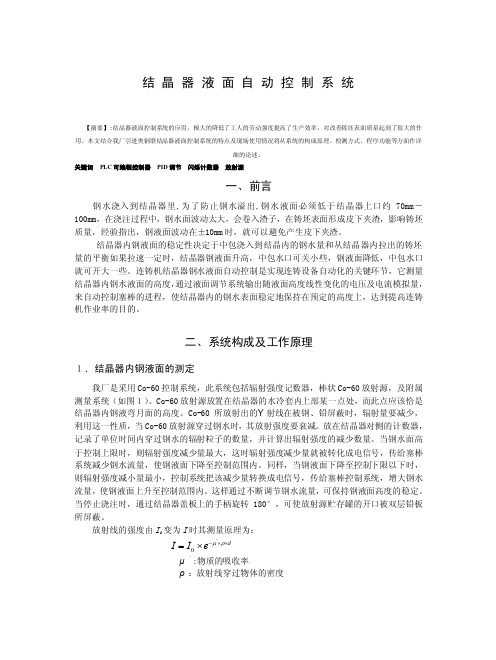
结 晶 器 液 面 自 动 控 制 系 统【摘要】:结晶器液面控制系统的应用,极大的降低了工人的劳动强度提高了生产效率,对改善铸坯表面质量起到了很大的作用。
本文结合我厂引进奥钢联结晶器液面控制系统的特点及现场使用情况将从系统的构成原理、检测方式、程序功能等方面作详细的论述。
关键词 PLC 可编程控制器 PID 调节 闪烁计数器 放射源一、前言钢水浇入到结晶器里,为了防止钢水溢出,钢水液面必须低于结晶器上口约70mm -100mm ,在浇注过程中,钢水面波动太大,会卷入渣子,在铸坯表面形成皮下夹渣,影响铸坯质量,经验指出,钢液面波动在±10mm 时,就可以避免产生皮下夹渣。
结晶器内钢液面的稳定性决定于中包浇入到结晶内的钢水量和从结晶器内拉出的铸坯量的平衡如果拉速一定时,结晶器钢液面升高,中包水口可关小些,钢液面降低,中包水口就可开大一些。
连铸机结晶器钢水液面自动控制是实现连铸设备自动化的关键环节,它测量结晶器内钢水液面的高度,通过液面调节系统输出随液面高度线性变化的电压及电流模拟量,来自动控制塞棒的进程,使结晶器内的钢水表面稳定地保持在预定的高度上,达到提高连铸机作业率的目的。
二、系统构成及工作原理1.结晶器内钢液面的测定我厂是采用Co-60控制系统,此系统包括辐射强度记数器,棒状Co-60放射源,及附属测量系统(如图1)。
Co-60放射源放置在结晶器的水冷套内上部某一点处,而此点应该恰是结晶器内钢液弯月面的高度。
Co-60所放射出的Υ射线在被钢、铅屏蔽时,辐射量要减少,利用这一性质,当Co-60放射源穿过钢水时,其放射强度要衰减。
放在结晶器对侧的计数器,记录了单位时间内穿过钢水的辐射粒子的数量,并计算出辐射强度的减少数量。
当钢水面高于控制上限时,则辐射强度减少量最大,这时辐射强度减少量就被转化成电信号,传给塞棒系统减少钢水流量,使钢液面下降至控制范围内。
同样,当钢液面下降至控制下限以下时,则辐射强度减小量最小,控制系统把该减少量转换成电信号,传给塞棒控制系统,增大钢水流量,使钢液面上升至控制范围内。
板坯连铸系统中PLC控制功能与技术实现论文大全

板坯连铸系统中PLC控制功能与技术实现论文大全第一篇:板坯连铸系统中PLC控制功能与技术实现论文大全板坯连铸系统简介以板坯连铸机生产工艺的特点为分级依据,可以把板坯连铸系统分为基础自动化系统以及过程控制计算机系统两级系统,其中一级为自动化系统,是运行基础;二级带有部分管理功能。
基础自动化系统是一套完整的电/仪一体化系统,在系统运行中起着非常重要的作用,它能够完成各工艺装置的顺序控制以及相关操作,可以对工艺参数进行设置,还可以对工艺参数与设备状态进行显示与预警,对工艺流程进行监控。
另外,其还有通信功能。
过程控制计算机系统有质量跟踪、参数设定以及铸机的模型计算的功能。
除此之外,对于网络的相关配置问题,通过PLC 与上位机之间的信息转换与以太网相连接,利用TCP/IP 协议完成数据转换。
板坯连铸系统中 PLC 控制功能说明2.1 大包回转台及中间罐车控制一方面,对装有合格钢水的钢水包,一般要通过行车的吊运运至大包回转台的钢包臂上,此时包臂会运转到浇注位置等待浇铸。
另一方面,提前预热好的中间罐通过中间罐车运送至结晶器的上方,此时中间罐会下降以完成对中就位;在准备工作完成后,钢水罐开始下降,到达指定位置后就要手动开启滑动水口,随之钢水就会通过长水口流入中间罐,等到中间罐内的钢水质量达到指定要求后就需要人工开启中间罐塞棒,这时钢水就会通过侵入式水口流入结晶器内,从而完成这一工序。
2.2 送引锭、脱引锭控制(1)送引锭:当送引锭指令发出后,引锭杆存放小车会向下反转运行,当引锭杆到达切割后辊道位置时四个对中缸将开始进行对中,随之切割前、切割下、切割后辊道自动运行,将引锭杆送至水平扇形段内。
当引锭杆尾部离开 2# 光电管时,切割后辊道就会停止运行,当其到达 1# 光电管时,切割下及切割前辊道就会停止运行,随之辊道就会以 5 米/分的速度在扇形段内运行,与此同时解码器也开始对其进行跟踪记录,最后将引锭杆送入结晶器下口。
基于S7-200PLC的连铸结晶器液位控制系统任务书
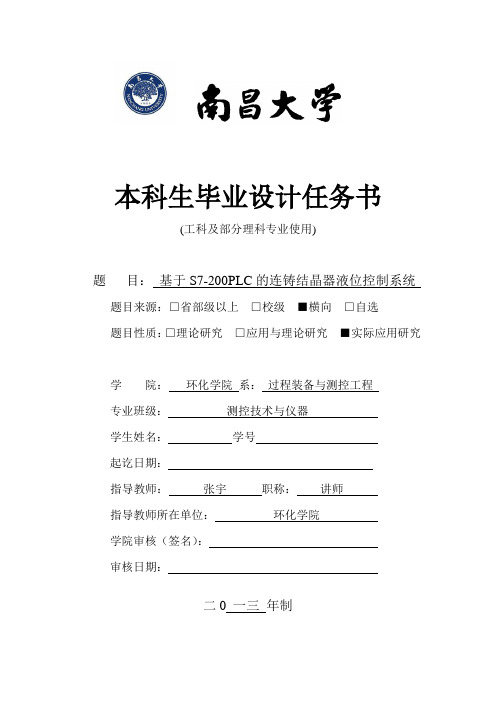
本科生毕业设计任务书
(工科及部分理科专业使用)
题目:基于S7-200PLC的连铸结晶器液位控制系统题目来源:□省部级以上□校级■横向□自选
题目性质:□理论研究□应用与理论研究■实际应用研究
学院:环化学院系:过程装备与测控工程
专业班级:测控技术与仪器
学生姓名:学号
起讫日期:
指导教师:张宇职称:讲师
指导教师所在单位:环化学院
学院审核(签名):
审核日期:
二0 一三年制
说明
1.毕业设计任务书由指导教师填写,并经专业学科组审定,下达到
学生。
2.进度表由学生填写,每两周交指导教师签署审查意见,并作为毕
业设计工作检查的主要依据。
3.学生根据指导教师下达的任务书独立完成开题报告,3周内提交给
指导教师批阅。
4.本任务书在毕业设计完成后,与论文一起交指导教师,作为论文
评阅和毕业设计答辩的主要档案资料,是学士学位论文成册的主要内容之一。
冶金连铸电气中PLC控制系统设计分析

冶金连铸电气中PLC控制系统设计分析近年来,我国的冶金行业得到了较为快速的发展。
对于冶金行业而言,要想在目前愈发激烈的市场竞争环境中获得更好的发展,就需要做好自身生产效率的提升。
自动化控制技术的出现为冶金行业的工作开展带来了好的机遇,在本文中,将以西门子公司S7系列的PLC为例,对PLC在连铸控制系统中的应用进行一定的研究。
1冶金连铸PLC自动控制系统的程序设计冶金连铸的自动化控制系统是采用分散控制方式进行控制。
PLC是可编程逻辑控制器,在工业控制系统中得到了广泛的应用。
在冶金连铸自动控制系统中,主要包括以下几个方面的功能:1.1监控站操作系统在连铸操作室中,一般具有两台操作站,两者具有相同的工作内容,在实际操作中处于相互备用的状态。
在CRT监控中,主要通过基础自动化系统的应用对其功能进行实现,且能够在不受到时间因素影响的同时对机组状况、能源介质以及设备运行等情况实现随时的掌握,且能够通过键盘鼠标等设备的应用实现程序的操作。
1.2二冷水系统PID调节在冶金连铸的过程中,需要对氩气流量以及水流量等进行控制,并且对这些因素的控制要求非常高,尤其是水流量的流速、以及氩气流量的流速等,要求需要保持稳定的数值。
在冶金连铸PLC自动控制系统的程序设计中,采用西门子PLC来代替智能仪表。
PID调节中使用FB41,可以通过模拟PID调节系统的控制面板来进行控制调节,可以实现PID调节中的手电调节和自动调节的切换,只需要手动输入PID参数,就可以进行系统的自动化控制了。
1.3拉矫自动控制系统铸机拉速调节方面,主要通过铸机综合本地控制箱实现控制,通过持续方式的应用将信号对PLC的模拟量模板进行发送,而当模板在完成模拟量信号接收之后,则可能通过通讯网络的应用对变频器输出拉速实现控制。
同时,其通过制造工艺以及模拟量信号的应用进行快速计算,对同拉速具有良好匹配特征的振动参数进行计算,使用通讯网络将相关参数对电机的变频装置进行发送,以此在使振频同拉速间的匹配进行实现,进而对铸坯过程中拉矫电机的负荷量进行降低。
PLC在冶金连铸电气控制系统中的应用
PLC在冶金连铸电气控制系统中的应用摘要:随着冶金行业的飞速发展,导致市场竞争加剧。
对冶金行业而言,为了在激烈的市场竞争环境中获得更好的发展,就需要不断提升生产质量与生产效率。
而PLC技术在冶金行业中的应用,就为冶金行业生产的企业发展带来了良好的机遇。
关键词:PLC;冶金连铸;电气控制系统引言在我国经济发展过程中,金属冶炼行业是一项非常关键的工业,冶金行业的生产效率直接影响着我国经济发展效率。
在具体落实经济发展工作的过程中,金属制品逐渐被应用于建筑、船舶制造以及其他一些大型工程之中。
就冶金连铸技术而言,该项技术能够有效缩短金属制品的制作时间,但是,以往的冶金连铸金属借助的是人工操作,效率低下。
本文就PLC在冶金连铸电气控制系统中的应用展开探讨,以期为相关工作起到参考作用。
1PLC技术配置及优势1.1配置PLC控制系统由2套PLC柜体、2台控制站、1台工程师站和1台网络打印机组成其硬件配置,设置2台控制站是防止紧急情况控制失灵,保证系统的可靠性。
冶金自动化生产的主机和辅助机器上运用了两套控制站,容错以太网接口模块、S7-400控制处理器、电源模块、冗余模块、I/O模块等构成其主要组成部分。
而IntelCPU2.8GHZ是2台控制站和1台工程师站的主要配置,运用的是WindowsXPsp3操作系统和19LCD显示器,具有4GBRAM的存储容量。
而其软件配置包括控制站的编程软件STEP7V5.5SP2、2台控制站FIX6.15运行版的监控软件、1台FIX6.15开发版的工程师站监控软件。
1.2优势1.2.1自动化程度高自动化程度高,也是PLC应用在冶金连铸电气控制系统改造工作中的一个主要优势,由于PLC属于逻辑控制,所有的指令都是根据是否满足所有条件而选择触发的,当液态钢加工完毕之后,系统就会触发蜗杆,将液态钢导入到连铸工作区,当连铸工作区的传感器感应到钢水到位之后,就会出发相应的机械设备动作,然后在加工完成之后,将加工成型的钢铁制品导出生产流水线,整个生产过程节省了大量的人力资源,而且有效的提高了整个生产流水线的工作效率,以及实际生产钢铁制品的产品质量,能够确保统一型号钢材的生产误差不超过1%。
基于PID控制的连铸机结晶器液压震动系统的应用
的位 置 , 系 统 由两 个 独 立 的液 压 缸 组 成 , 每 个 液 压 缸 有 一 个 伺 服 阀来 控 制 结 晶器 液 压 缸 位 置 , 结 晶器 将 以 一 定 的 频 率 、 行 程 和 波 形来振动 。
内部 质 量 的 要求 。 结 晶器 液 压 震 动 的作 用 主 要 表 现 在 两 个 方 面 : 1 ) 防止 铸 坯 在 凝 固过 程 中 与结 晶 器 铜 壁 发 生 粘 结 而 出现 坯 壳拉裂或漏钢事故。 在结 晶器 上 下 振 动 时 按 振 动 曲线 周 期 性 地 改 变 钢 液 面 与 结 晶 器铜 壁 的 相 对 位 置 ,对 坯 壳 有 一 个 强 制 脱 模 的作 用 , 并 使 得 拉 漏 的坯 壳 在 结 晶 器 内部 得 以 焊 合 。
结 晶器 是 连 铸 设 备 中 的铸 坯 成 型设 备 ,人们 称 它 是 连 铸 机
的 心脏 。它 的功 能 是 将 连 续 不 断地 注入 其 腔 内 的 高 温 钢 液 通 过
结 晶 器 必 须 在 浇 注 期 间 保 持 振 动 。如 果 振 动 是 以不 正 确 的 频率 、 振幅或波 形进行 , 则会引起较差 的表面质量 , 增 加 结 晶 器 润滑粉的消耗 , 或者可能引起漏钢 。
级 计 算 机 系 统 的 模 型 设 定 数 据 、连 铸 机 一 级 控 制 系统 操 作 员设 定 数 据 及 来 自控 制 器 本 身 自带 的控 制 面 板 的人 工 设 定 ,然 受 下 载 到控 制 器 实 现 震 动 控 制 。此 控 制 方 式 较 好 的满 足 了 冶 金 工 艺 的要 求 , 对 板 坯 的 内 部 和表 面质 量 起 到 很 好 的效 果 。 系 统 在 宝 钢
PLC在连铸电磁搅拌中的应用
PLC在连铸电磁搅拌中的应用摘要:文中阐述了电磁搅拌对铸坯质量的影响,分析了电磁搅拌装置的控制系统构成和控制原理及信号保护环节。
并从系统的通信网络构成阐述了电磁搅拌模型及其操作方式。
关键词:电磁搅拌控制原理搅拌模型1.概述我公司的3#连铸机为全套引进意大利DANIELI公司机型和设备,该机为4机4流、弧型弯曲半径8m,产品为40G、20MnSi45#、60SiMn,产品规格为150×150mm、切长10m,拉速0.5—6m/min,正常拉速为2.2m/min,年产量为34.2万吨。
该机采用了结晶器电磁搅拌、结晶器液面自动控制、冷却水自动控制等一系列先进技术,其控制系统由六套S5—135UPLC一级控制,两台Siemens SICOPY32R 兼容机MMI,实现连铸生产的铸坯质量跟踪、二冷水参数计算、设备管理、钢种分析及全过程自动控制。
系统采用6块CP143模块,通过8入2出以太网连接器,经TRANCEIVER收发器与MMI及二级连接。
连铸结晶器电磁搅拌(EMS)作为提高连铸坯质量的一种有效手段,在现代化连铸机中被广泛采用,由于结晶器内部采用旋转磁场,使得钢液在水平方向上旋转,通过钢液旋转把较轻的氧化物夹杂和气泡与较重的钢液分离,并促其上浮;其次,提高了连铸内部质量,通过搅拌使得钢液在凝固过程中产生强制流动,钢液过热度快速降低,从而扩大生产重轨及较硬线等高碳钢是极为重要的。
在系统运行中磁感应强度在0.02—0.03T时开始出现效果,0.04T以上效果更好,但太大会出现负偏析(白亮带),因此最大磁感应强度应控制在0.08以下,搅拌频率一般在10Kz以下,通常为2Kz。
2.电磁搅拌控制系统2.1.系统构成电磁搅拌器电流为三相正弦交流电,在相位上互差1200,其主接线图如图1所示;系统有断路器、变流器、输出接触器和漏电流检测装置及APC控制器、PLC等构成。
2.2.控制原理搅拌频率给定和电流给定经控制器运算后,传输至变流器的通信模块,变流器中具有电流调节器和无环流逻辑控制器,根据控制器的给定信号,变流器输出电流产生磁场。
SIEMENS S7 400 PLC 在天铁集团炼钢厂连铸机自控系统中的应用
SIEMENS S7 400 PLC 在天铁集团炼钢厂连铸机自控系统中的应用王巍天铁集团炼钢厂计算机中心关键词:PLC 、ET200M、WinCC、STEP 7、MPI、PROFIBUS DP、工业以太网、变频器我厂小方坯连铸机在自动化控制系统中,以及网络控制中存在以下几个特点和功能:1、实现拉矫机与结晶器连锁控制,闭环调节。
2、改善二冷水配水调节。
3、网络控制(实现利用PROFIBUS网络控制拉矫机变频器和结晶器变频器的连锁运行,利用MPI来实现3台PLC之间的通讯实现数据共享,利用工业以太网来实现WinCC操作站与PLC设备的连接实现数据交换与共享。
4、对重要数据要进行实时监控记录,生成报表以便查询5、上位机操作站具备调整设备运行参数(火焰切割机、拉矫机、结晶器、输坯辊道等设备参数和下配水表规程)的功能,参与过程控制。
具体特点和功能说明:我厂小方坯连铸机自控部分是由SIEMENS S7 400 PLC设备3套、SIEMENS ET 200M 远程站5个、WinCC上位机操作站一台、EMERSON TD 3000 变频器16台、EMERSON TDS-PA01适配器16个、SIEMENS OSM 光纤收发器一个等设备组成。
来组成连铸机的自控系统。
具体见图一所示:(图二)(图一)一、实现拉矫机与结晶器连锁控制,闭环调节。
拉矫机是采用直传多点矫正渐进式拉矫机。
实现拉矫机与结晶器闭环控制调节主要设备为:SIEMENS S7 400 PLC设备、EMERSON TD3000 变频器、EMERSON TDS-PA01适配器。
其控制方法为:如(图 一)所示拉矫机变频器、结晶器变频器通过PROFIBUS DP 网络与SIEMENS S7 400(CPU 414-2DP )连接组成网络,实现拉矫机与结晶器联锁控制。
我厂连铸机为6米弧4 流小方坯连铸机,每台拉矫机带有M1、M2、M3三个主动辊其半径相等,而三台主动辊的输出转速各不相同。
- 1、下载文档前请自行甄别文档内容的完整性,平台不提供额外的编辑、内容补充、找答案等附加服务。
- 2、"仅部分预览"的文档,不可在线预览部分如存在完整性等问题,可反馈申请退款(可完整预览的文档不适用该条件!)。
- 3、如文档侵犯您的权益,请联系客服反馈,我们会尽快为您处理(人工客服工作时间:9:00-18:30)。
PLC在连铸机结晶器液位控制中的应用
作者:魏哲明陈洁
来源:《数字化用户》2013年第04期
【摘要】介绍了唐钢方坯连铸机结晶器液位控制系统的组成、功能特点以及应用情况,以及基于西门子S7系列PLC的液位闭环过程控制的功能图软件设计方法。
由于不同的连铸机结晶器液位控制的思路是类似的,因此不同的系统控制程序修改后是可以移植的。
采用功能阁的方法编制PLC的程序具有思路清晰,逻辑严谨,可移植性高等特点。
采用PID串级控制器井按照功能图方法编写的程序经过工程实践,结晶器液位在稳定工作时其控制精度在左3mm 以内,系统响应速度快,运行自定可靠,同时减少了编程开发调试时间。
【关键词】连铸结晶器液位控制 PLC 自动控制
一、引言
在我国的钢铁连铸领域,特别是方坯连铸机领域中,自动化水平是相对较低的,在科技快速发展的今天,技术水平落后已经尤为突出。
连铸自动化水平的提高,直接关系到对保证铸坯质量、提高连铸机的劳动生产率、增加连铸机的金属收得率起着非常重要的作用。
为了提高产品的市场竞争力以及与世界接轨,是世界冶金生产的发展方向。
因此,实现PLC自动控制系统在连铸生产过程中非常重要。
结晶器液位控制是连铸生产中的重要环节。
稳定的液位有利于使铸坯初期坯壳生成,提高凝固坯壳生长的均匀性,有助于液相穴内的杂物上浮,降低铸坯纵裂纹指数,减少表面夹渣,提高铸坯质量,同时大大减少连铸机生产中的拉漏、溢钢事故。
二、自动控制系统设计
结晶器内的液位控制采用流量控制,通过调节中间包裹棒与水口之间的缝隙控制钢水流量,以达到控制结晶器内液位目的。
控制器设计为串级控制,共有两个控制器,包括塞棒开度控制和液位控制两个控制环,其中开度环采用P控制器,塞棒位置传感器检测塞棒的实际位置,通过控制器控制液压缸的伺服阀从而控制塞棒位置。
液位控制采用PID控制器,将液位检测信号反馈到液位控制器,经调节算法进行运算,得到塞棒调节的位移量,再将位置量传送到开度P控制器。
P控制器最终输出信号控制比例阀。
开度按制作为内环,液位作为主控制器,这种控制器结构能够改善系统的动态特性,提高系统的工作频率。
三、自动控制系统构成
连铸机的自动控制系统由公用PLC、流用PLC、液位PLC、火切机PLC、电磁搅拌PLC 组成。
液位PLC的控制是在正常浇钢条件的情况下,为每个流的液位和拉速控制。
连铸机共有两台中包车,可以一台浇铸,另一台预热准备。
中包车的塞捧由电动缸驱动升降,调节塞棒与水口的间隙。
控制系统主要由PLC、组态软件、及液位检测、液压系统等组成。
检测元件包括,结晶器液位检测部分,镭目公司提供的Cs-137检测仪及前端处理柜,前端处理带有滤波及平滑算法,信号转换为4 -20mA;塞棒位置检测传感器等。
每流包括铸流及液位PLC各一套。
两个中间包车的液位由一套PLC控制,采用西门子的S7-300系列PLC,铸流PLC采用西门子S7-400。
S7-300与流PLC通过Profibus-DP网进行通信,编程环境为西门子Step7。
电动缸系统机构包括紧急阀门,手自动切换阀,液压伺服阀,液压缸等。
Intouch上位机软件用于实现过程显示,液位及参数设定,过量报警处理级当前趋势及历史趋势显示等功能。
四、自动控制工艺过程
液位控制系统的工作模式分为手动模式,自动模式及自动开始浇铸方式。
浇铸前中包车在停止位,通过人工检查并安装,对传感器、电动缸等机构进行测试,检测系统是否正常。
一切正常后,将中包车开到浇铸位准备浇钢并查看塞棒位置,检查完成后即开始浇铸。
开始浇钢后,人工撬杠塞棒并手动调整钢水液位,控制液位在一定范围内;待液位平稳恒定并出现自动液位投入信号,浇钢工切换到自动方式。
此后,系统将按照设定值自动调节。
浇钢工可以通过按钮调节液位设定值。
当然,系统也可以自动开浇,开始时大包向中间包内下流,中间包中钢水到达浇钢下流量后,浇钢工可以按下自动开浇,这时塞杆将打开较大开度,快速向结晶器内部注钢,如果液位在3秒内达到10%则关掉塞杆,等待3秒后再次向结晶器内注钢,如果液位大于20%再次关押塞棒,同时启动结晶器振动台冰开启二冷水;等待4秒s,自动启动拉矫机,250ms后拉速和液位控制自动投入,开始闭环调节,整个自动开浇过程完成,系统切换到正常浇铸过程。
如果自动控制中液位降低过多,系统将向流发出减少拉速的指令,防止漏钢,如果系统发生意外故障,将会自动关闭塞杆。
当液位过高时,到达一定值时,关闭中间包塞棒,防止溢钢,液位过低时,降低拉速,防止漏钢。
五、自动控制程序设计
程序的结构设计分为工艺步序管理,手动操作控制,系统监控,模式管理,输入输出控制,设定值计算,PID控制,阀组管理,零点探测等部分。
工艺管理部分负责控制自动开浇,拉速调节等工艺部分的功能;手动操作用于开环塞杆位移控制;系统监控负责对系统各个部分的状态作出判断,如果发生故障则作出相应处理;输出控制用于对液压旁路阀,比例阀部分输出;设定值计算用于计算从流PLC传过来的设定数据,PID控制器包括位量与液位两个控制器,是整个过程控制程序的核心,主要进行PID计算;零点探测用于在开浇前进行的零点探测,标定传感器等内容。
六、结束语
方坯连铸及西门子PLC自动控制系统能够圆满的完成各项控制任务。
保证设备的稳定性,而其系统响应速度快,性能可靠,完全可以实现全自动浇钢过程。
实践证明,该系统设计合理,安全可靠,提高了铸坯质量,保证了方坯连铸机的作业率,减轻了工人的劳动强度,为唐钢取得良好的经济效益。
同时也充分地表明,西门子PLC在唐钢方坯连铸机自动控制系统中的应用很成功的。