EBS-MRP提前期
MRP的数据处理逻辑—需求计算
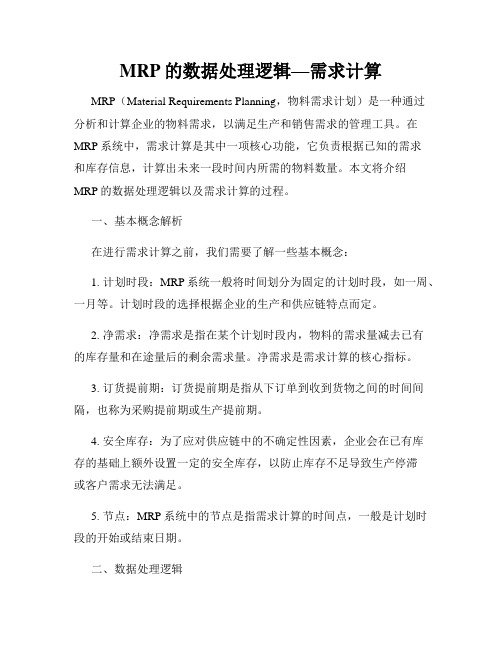
MRP的数据处理逻辑—需求计算MRP(Material Requirements Planning,物料需求计划)是一种通过分析和计算企业的物料需求,以满足生产和销售需求的管理工具。
在MRP系统中,需求计算是其中一项核心功能,它负责根据已知的需求和库存信息,计算出未来一段时间内所需的物料数量。
本文将介绍MRP的数据处理逻辑以及需求计算的过程。
一、基本概念解析在进行需求计算之前,我们需要了解一些基本概念:1. 计划时段:MRP系统一般将时间划分为固定的计划时段,如一周、一月等。
计划时段的选择根据企业的生产和供应链特点而定。
2. 净需求:净需求是指在某个计划时段内,物料的需求量减去已有的库存量和在途量后的剩余需求量。
净需求是需求计算的核心指标。
3. 订货提前期:订货提前期是指从下订单到收到货物之间的时间间隔,也称为采购提前期或生产提前期。
4. 安全库存:为了应对供应链中的不确定性因素,企业会在已有库存的基础上额外设置一定的安全库存,以防止库存不足导致生产停滞或客户需求无法满足。
5. 节点:MRP系统中的节点是指需求计算的时间点,一般是计划时段的开始或结束日期。
二、数据处理逻辑需求计算的数据处理逻辑可以总结为以下几个步骤:1. 收集数据:首先,我们需要收集相关的数据,包括物料的需求量、库存量、在途量以及供应链的参数配置等信息。
这些数据一般来源于企业的ERP系统或其他相关系统。
2. 计算净需求:根据收集到的数据,通过减法运算计算出每个计划时段内的净需求量。
具体计算公式如下:净需求 = 需求量 - 库存量 - 在途量如果净需求为正数,则表示物料需要进一步采购或生产;如果净需求为负数,则表示物料的库存超过了需求量,可以考虑减少采购或生产。
3. 考虑安全库存:在计算净需求的基础上,还需要考虑安全库存的影响。
如果净需求小于等于安全库存,则无需进行采购或生产;如果净需求大于安全库存,则需要进一步考虑采购或生产的计划。
ORACLE EBS MRP计划基础

物料需求计划(MRP) -- 基本概念
影响计划订单数的因数
最小定单数 最大定单数 固定定单批量 固定定单批量增量 整数控制 损耗率 利用率
物料需求计划(MRP) -- 基本概念
计划参数
考虑采购 包括批准的请购,批准的采购定单 考虑制造 包括标准与非标准的作业 考虑的仓库 所有项目/只计划项目 从计划开始日期计算或从工序开始日期计算
计划标准流程
订单 预测
主需求计划 粗能力计划 主生产计划 库存模块 BOM模块
物料需求计划
能力需求计划 车间模块 采购模块
两个概念
需求/供应
依赖需求/独立需求
依赖需求/独立需求
概念 定义 由何决定 举例
需求的类型 -- 依赖需求/独立需求
独立需求 需求不依赖于其他物品 预测和销售订单 最终物品 依赖需求 需求依赖于其他物品 计划计算时生成 子装配,组件,未加工材料
提前期(Lead
Times) -- 续
总提前期
处理提前期加上预处理提前期
累计制造提前期
处理提前期加上关键子装配的处理提前期
累计总提前期
处理提前期加上关键子装配和采购组件的处理提前期
总提前期 装配:制造 子装配:制造 组件:采购 累计制造提前期 处理前提前期 处理提前期 处理后提前期
累计总提前期
到岸日期(采购) = 到期日期- 处理后提前期 到岸日期(制造) = 到期日期
开始日期 = 到期日期 - 提前期偏置
定单日期 = 开始日期 - 处理前提前期
物料需求计划(MRP) -- 基本概念
计划定单数量 = 毛需求-供应 = (总需求+安全库存)-(手头量+计划接收)
采购提前期

采购提前期EBS使用—作者kiswind @ 11:02采购提前期即物料采购所需要的时间,在执行计划时,系统会根据需求需要时间、提前期,推算出你应当进行采购的日期(可参考Prasad Revur:传统库存计划与基于需求的计划)系统中的物料有“采购件”、“制造件”两种类型,制造件的提前期相对复杂。
在系统的BOM模块中可以计算制造件的提前期。
而采购件的提前期只有手工录入。
即使有工艺路线,也不会计算提前期。
采购件提前期的启用条件:要在MRP计划中正确的考虑采购件提前期,必须满足以下条件:1) planning_make_buy_code = 2 (采购).2) fixed_lead_time = null.3) variable_lead_time = null.在界面上,无法区分数据是空还是NULL。
如果是一个空格,系统会用默认值0代替,即产生错误的结果。
可以用以下SQL查询验证:selectplanning_make_buy_code,organization_id,fixed_lead_time,variable_lead_time,full_lead_time From mtl_system_items Where segment1 =‘&item’采购件提前期的构成及业务意义1) 何采购件的提前期都会考虑工作日历。
只在工作日考虑采购提前期,及假设休息日没有任何采购相关的业务。
2) 采购件的提前期计算逻辑如下:过账提前期/后加工提前期/Postprocessing Leadtime(从接收到入库的时间)+处理时间/加工中提前期/Processing Leadtime (供应商处理订单到交货给你的时间)+预提前期/预加工提前期/Preprocessing Leadtime (采购订单完成前需要的时间)3) 结果如下:到岸日期/dock date (在计划明细报表中可能看到) 指供应商将货物送到交货到站地的日期到岸日期=订单到期日-后加工提前期开始日期/start 指你将采购订单交到供应商的日期开始日期=到岸日期-加工中提前期订购日期/order date 是你开始录入采购订单的日期订购日期= 开始日期-预加工提前期4) 可以设置固定提前期(fixed leadtime)代替处理中提前期(对采购件两都意义和效果是一样的)。
oracle-EBS系统ASCP原理
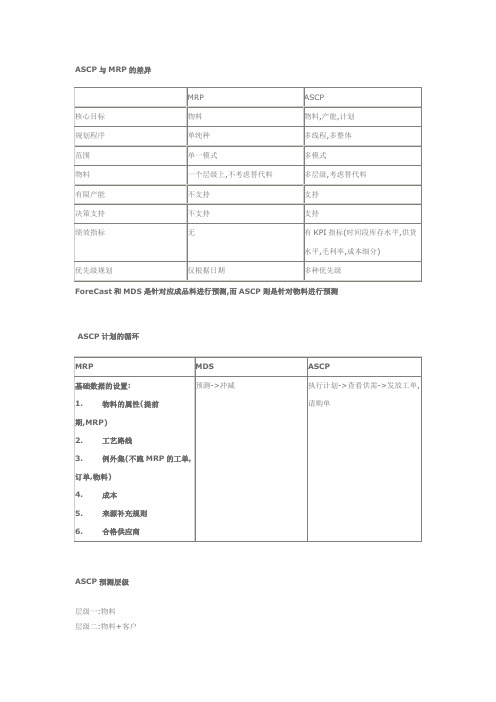
ASCP与MRP的差异ForeCast和MDS是针对应成品料进行预测,而ASCP则是针对物料进行预测 ASCP计划的循环ASCP预测层级层级一:物料层级二:物料+客户层级三:物料+客户+制造地点层级四:物料+客户+发送地点计划订单批量规则影响计划订单的数量,其优先级如下:固定供应天数>固定下单天数>固定下单批量>最小下单量>最大下单量>整数下单量会产生供给锁定的情况<1>没有需求只有供给<2>营销物料需求预测与生产物料需求预测有差异<3>工单与采购单都可能锁定装入/复制/合并生产排程装入的来源主要有:<1>预测<2>销售订单<3>预测+销售订单<4>多组织计划订单<5>主生产排程需求展开:是指物料需求规则中平衡需求与供给的程序展开主要取决于以下因素:<1>要采购的物料和要自制的物料<2>采购件和制造件的数量<3>采购件,制造件入库的时点<4>要采购的自制件工单开立时的时点预测区间型态预测区间型态表示进行销售预测时所使用的时区区间,在所选择的时间区间中指定预定的出货产品及数量型态分类:天以天为单位进行销售预测的区间周以周为单位进行销售预测的区间月以月为单位进行销售预测的区间一个料号可以同时使用多个区间型态ASCP替代料的寻路规则:先看主料是否有库存->没有则抓主料在需求日之前是否有PO->没有则看需求日之前是否有PO到货->没有则抓最优先替代料是否有库存->没有则抓主料后面的PO->没有则抓最优先级替代料的PO->没有则抓主料的计划单是否有料替代料的寻找会受采购提前期的影响,数量越小的越优先ASCP预测准确提升的影响因素1.考量历史销售状况2.广告.促销等其它因素3.搭配其它管理机制4.即时响应需求变化。
mrp计算注意事项
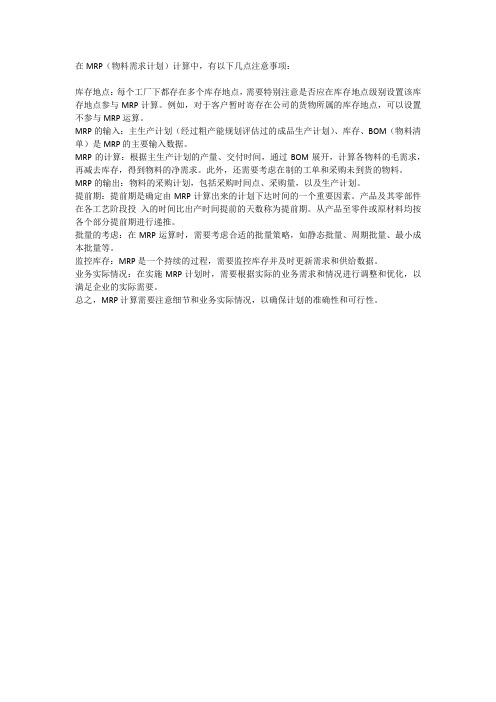
在MRP(物料需求计划)计算中,有以下几点注意事项:
库存地点:每个工厂下都存在多个库存地点,需要特别注意是否应在库存地点级别设置该库存地点参与MRP计算。
例如,对于客户暂时寄存在公司的货物所属的库存地点,可以设置不参与MRP运算。
MRP的输入:主生产计划(经过粗产能规划评估过的成品生产计划)、库存、BOM(物料清单)是MRP的主要输入数据。
MRP的计算:根据主生产计划的产量、交付时间,通过BOM展开,计算各物料的毛需求,再减去库存,得到物料的净需求。
此外,还需要考虑在制的工单和采购未到货的物料。
MRP的输出:物料的采购计划,包括采购时间点、采购量,以及生产计划。
提前期:提前期是确定由MRP计算出来的计划下达时间的一个重要因素。
产品及其零部件在各工艺阶段投入的时间比出产时间提前的天数称为提前期。
从产品至零件或原材料均按各个部分提前期进行递推。
批量的考虑:在MRP运算时,需要考虑合适的批量策略,如静态批量、周期批量、最小成本批量等。
监控库存:MRP是一个持续的过程,需要监控库存并及时更新需求和供给数据。
业务实际情况:在实施MRP计划时,需要根据实际的业务需求和情况进行调整和优化,以满足企业的实际需要。
总之,MRP计算需要注意细节和业务实际情况,以确保计划的准确性和可行性。
什么是制造项目的提前期?
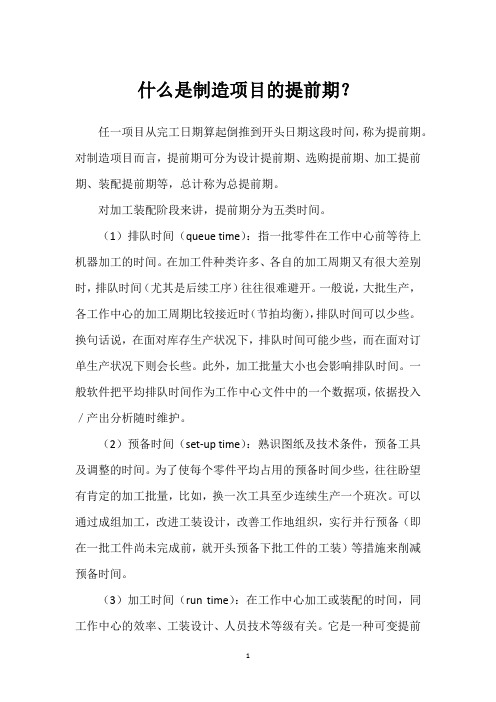
什么是制造项目的提前期?任一项目从完工日期算起倒推到开头日期这段时间,称为提前期。
对制造项目而言,提前期可分为设计提前期、选购提前期、加工提前期、装配提前期等,总计称为总提前期。
对加工装配阶段来讲,提前期分为五类时间。
(1)排队时间(queue time):指一批零件在工作中心前等待上机器加工的时间。
在加工件种类许多、各自的加工周期又有很大差别时,排队时间(尤其是后续工序)往往很难避开。
一般说,大批生产,各工作中心的加工周期比较接近时(节拍均衡),排队时间可以少些。
换句话说,在面对库存生产状况下,排队时间可能少些,而在面对订单生产状况下则会长些。
此外,加工批量大小也会影响排队时间。
一般软件把平均排队时间作为工作中心文件中的一个数据项,依据投入/产出分析随时维护。
(2)预备时间(set-up time):熟识图纸及技术条件,预备工具及调整的时间。
为了使每个零件平均占用的预备时间少些,往往盼望有肯定的加工批量,比如,换一次工具至少连续生产一个班次。
可以通过成组加工,改进工装设计,改善工作地组织,实行并行预备(即在一批工件尚未完成前,就开头预备下批工件的工装)等措施来削减预备时间。
(3)加工时间(run time):在工作中心加工或装配的时间,同工作中心的效率、工装设计、人员技术等级有关。
它是一种可变提前期,即每批零件加工时间=零件数量×单个零件加工时间。
(4)等待时间(wait time):加工完成后等待运往下道工序或存储库位的时间。
等待往往是由于搬运设施调配不当或下道工序力量不足造成的,也同传送批量有关。
因此,一些软件把等待时间合并到传送时间中去。
(5)传送时间(move time):工序之间或工序至库位之间的运输时间,若为外协工序则包括的内容更广。
同车间布置、搬运工具力量效率有关。
上述五类时间之和,即从下达任务开头到加工完成为止的时间,形成了加工件的生产提前期。
通常,一个零件在机床上的时间,即上述预备时间与加工时间之和,往往仅占生产提前期的5%~10%,而90%以上的时间消耗在排队、等待和传送上。
EBS-MRP计划单数量的计算逻辑

MRP基础 < 2 >——计划单数量的计算逻辑文档作者: 刘青创建日期: 2009-7-16更新日期: 2009-7-16文档版本: V1.0目录总体描述 (3)常见需求类型 (3)MDS主需求 (3)工作单需求 (3)计划单需求 (3)舍入订单数量 (4)舍入订单数量 (4)BOM产出率 (4)BOM产出率 (4)测试过程 (5)物料损耗率 (7)物料损耗率 (7)测试过程 (7)修改量使用实例 (8)业务需要 (8)方案设计 (9)遗留问题 (9)安全库存百分比 (10)安全库存百分比 (10)测试过程 (11)其他常用修改量 (13)最小最大订货量 (13)固定订货量 (14)固定供应天数 (14)固定批次增量 (15)测试过程 (15)小结 (16)总体描述上一回讲了提前期知识,相信大家已经明白了MRP的起始日和到期日是怎么算出来的,今天要讲的是MRP的计划单数量是怎么算出来的,大家一起来揭开MRP的黑箱呀。
文中提到的所有修改量,都是我在MRP实施过程中,先了解到客户的需求,然后才去系统里找的对应功能,所以,这些修改量的实用性还是很强的,希望能对MRP的新手有所帮助。
常见需求类型MDS主需求MDS行,或者手工录入,或者装载其他MDS,或者装载预测,或者装载销售订单。
不管MDS怎么来的,来了之后,它就作为我们的出货计划或者需求计划被确定下来。
我们想法设法,或者生产或者采购或者外协加工,就是为了在MDS的需求日期这一天能够拿得出来MDS要的数量。
比如一个可作为配件销售的半成品,MDS上写着下个月10号要出货800台,那么在下个月的10号这一天,此半成品的需求至少就有这800台了。
为什么是至少呢?因为这个半成品除了被直接销售以外,在生产成品的过程中也要用到它,为了满足别的东西的生产而带出来的需求,就是工作单需求和计划单需求。
工作单需求现在已经有一个生产任务正在进行,要生产液晶电视100台,要生产这100台液晶电视,需要100个液晶屏,100个液晶屏仓库已经发料了20个,还剩80个没有发料。
<O管理>OEBS名词解释
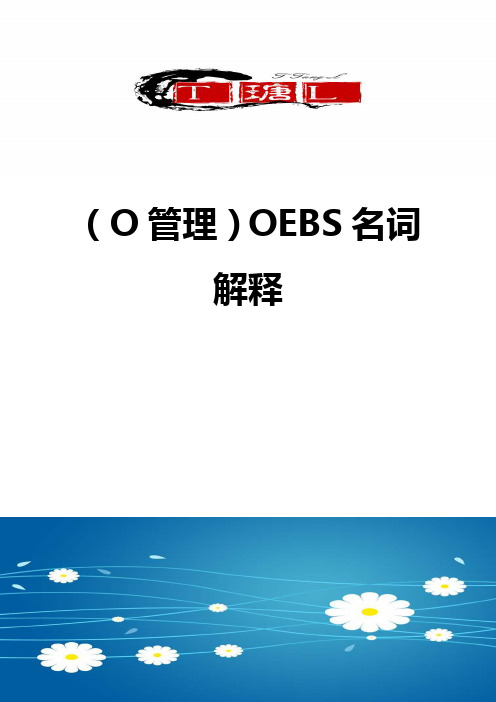
(O管理)OEBS名词解释OracleEBS名词解释ABCDEFGHIJKLMNOPQRSTUVWXYAABCclassification(ABC分类法)一种按重要性(如年度金额或公司的事务处理历史记录)递减顺序对物料进行分类的方法。
absorptionaccount(吸收帐户)记入库存或在制品价值的成本的抵销帐户。
例如,在对某物料执行采购订单接收时,如果物料定义了物料间接费用分摊率,则需要按物料间接费用成本借记库存估价帐户、贷记物料间接费用吸收帐户,以便将费用从总帐帐户“吸收”至库存。
月终时,再比较吸收帐户余额与总帐中发生的费用,并在损益表中冲销其间的差额。
accept(接受)一项活动,表示接受上一个审批人的审批结果。
AcceptableEarlyDays(容许提前天数)一种物料属性,计划流程使用它来确定何时为物料重新计划一个更早日期的订单。
仅当订单应在容许提前日期之前接收入库时,计划流程才会建议重新计划物料订单。
如果在短期内建立并储存过量库存比重新计划订单更为经济,则可以使用此属性。
此属性仅适用于离散计划物料,重复性计划物料的相应属性为超出百分比。
AcceptableRateDecrease(生产率降低容限)一种物料属性,计划流程使用它来确定计划时间栏内的物料当前日生产率的减少量。
计划流程建议的新日生产率不能小于当前日生产率与生产率减少容限额之差。
如果未定义此属性值,计划流程将假定在计划时间栏内可为物料建议新的日生产率无下限值;如果将此属性设置为零,计划流程将假定在计划时间栏内建议的任何生产率都不能小于当前日生产率。
在库存管理系统中,此属性值默认为零。
此属性使您可以通过限制短期生产率更改建议来尽量减少对车间计划的破坏,它仅适用于重复性计划物料。
AcceptableRateIncrease(生产率提高容限)一种物料属性,计划流程使用它来确定计划时间栏内的物料当前日生产率的增加量。
计划流程建议的新日生产率不能大于当前日生产率与生产率提高容限额之和。
- 1、下载文档前请自行甄别文档内容的完整性,平台不提供额外的编辑、内容补充、找答案等附加服务。
- 2、"仅部分预览"的文档,不可在线预览部分如存在完整性等问题,可反馈申请退款(可完整预览的文档不适用该条件!)。
- 3、如文档侵犯您的权益,请联系客服反馈,我们会尽快为您处理(人工客服工作时间:9:00-18:30)。
MRP基础 < 1 > ——提前期知识
文档作者: 刘青
创建日期: 2009-6-14
更新日期: 2009-4-14
文档版本: V1.0
目录
总体描述 (3)
提前期的业务实际 (3)
采购件的提前期 (3)
制造件的提前期 (3)
提前期的系统实现 (3)
物料属性 (3)
工艺路线 (4)
两个来源的关系 (6)
累计制造和累计总额 (7)
总体描述
MRP的意义,保证在合适的时间有能力供应合适的数量。
合适的数量,下次谈,这次,我们先搞定时间。
提前期的业务实际
采购件的提前期
预加工提前期:通常是指从计划部门知悉采购需求到借由采购部将这采购需求明确传递至
供应商的时间。
加工中提前期:是指从供应商知悉我们的采购需求到将相应物料送至我厂门口的时间。
后加工提前期:通常是指从我厂接收材料,到经过IQC检验完毕,物料被转移到良品仓可
以随时被产线领用了的时间,甚至可以包括一些简单的前加工时间。
制造件的提前期
预加工提前期:通常是指从计划部门下达派工单,到车间一切就绪正式开始生产的时间。
主要包括有,备料时间、机器预热时间、前加工时间等。
固定提前期:是指不会随着生产任务数量的变化而发生变化的提前期。
变量提前期:是指每增加一个单位的生产任务,相应要增加的提前期。
举例:产线开动,从第一颗材料送上产线到第一个产品完工下线共用了2天,接下来,每
隔1个小时就有一个产品可以完工下线。
类似这样的情况,我们就可以将固定提前期设置
为(2 - 1/24)Day,将变量提前期设置为1/24Day。
基础固定时间加上节拍变量时间,所
以,如果生产1台,提前期=(2 - 1/24)+1*1/24Day;如果生产2台,提前期=(2-1/24)
+2*1/24Day;如果生产100台,提前期=(2-1/24)+100*1/24Day。
提前期的系统实现
物料属性
主层控制物料的提前期批量;
组织层控制物料的各种提前期。
物料属性里的提前期是用于MRP运算的,使得MRP能够根据需求算出供应的订购日、起
始日、到期日。
采购件:在属性处设置其预加工、加工中、后加工提前期。
制造件:在属性处设置预加工、固定、变量提前期。
为什么不为制造件设置加工中提前期?
为制造件手工设置加工中提前期是没有意义的。
在参与MRP运算的时候,制造件的起始日期和到岸日期的间隔= 制造LD= roundup [ 物料属性固定LD +(物料属性变量LD * 离散任务数量)],只取了属性里的固定和变量,与属性里的加工中提前期毫无关系。
PS:roundup函数的意思是进位取整数。
工艺路线
工艺路线里的提前期是用于离散任务的日期控制的,根据离散任务的起始日期正向推出完成日期,或根据离散任务的完成日期倒推出起始日期。
在工艺路线里面,提前期的概念是通过被计划的时间类资源来体现的。
被计划、时间类、基准为批次的资源,可以理解为固定提前期。
各资源之间不用考虑偏置,直接相加即可,比如在工序10和工序20里各有一个被计划、时间类、批次基准的资源,分别为3Day和5Day,假设部门资源数量(24小时可用)和工序资源分配数量为1,
被计划、时间类、基准为物料的资源,可以理解为变量提前期。
各资源之间不用考虑偏置,直接相加即可,比如在工序10和工序20里各有一个被计划、时间类、物料基准的资源,分别为1HR和2HR,假设部门资源数量(24小时可用)和工序资源分配数量为1,则工艺路线反映出来的变量提前期为(1+2)/24Day。
注意:工艺路线利用资源确定提前期的时候,受两个因素影响:
➢部门资源数量和具体可用时间
➢工序资源分配数量
这两个地方的设置,决定了实际可用的资源数量,对于时间类的资源来说,也就是决定了部门可用的生产时间。
公式如下:
工艺路线固定LD=sum(被计划、时间类、批次基准的各资源使用量)/[ 部门资源可用时间*min(部门资源数,工序资源分配数)]
工艺路线变量LD=sum(被计划、时间类、物料基准的各资源使用量)/[ 部门资源可用时间
具体怎么算的,我们看一组例子。
设置
工艺路线提前期结果(Day) 部门资源数
部门资源可用时间 工序资源分配数
批次基准 资源使用量(Day)
物料基准 资源使用量(Day) 固定LD 变量LD 1 24小时可用 1 0.5 0.004 0.5 0.004 3 24小时可用 2 0.5 0.004 0.25 0.002 2 24小时可用 3 0.5 0.004 0.25 0.002 1 24小时可用 0.5 0.5 0.004 1 0.008 0.5 24小时可用 1 0.5 0.004 1 0.008 1 非24小时班次12HR 1 0.5 0.004 1 0.008 3 非24小时班次12HR 2 0.5 0.004 0.5 0.004 2 非24小时班次12HR 3 0.5 0.004 0.5 0.004 1 非24小时班次12HR 0.5 0.5 0.004 2 0.016 0.5
非24小时班次12HR
1
0.5
0.004
2
0.016
结合公式,相信不难理解提前期的逻辑。
一方面是工艺路线里的资源使用量,一方面是多
个因素决定的最终资源可供使用量,两相平衡之后得到提前期。
前面说过,工艺路线里的提前期是为了推算出工单上的起始或完成日期,这里的提前期具体是怎样算出来的呢?工单的完成日期与起始日期的差额= 加工中LD= roundup [ 工艺路线固定LD +(工艺路线变量LD * 提前期批量)]。
在物料属性和工艺路线的设置未做修改的前提下,不论离散任务的数量是多少,同一装配件的各工单的完成日期与起始日期的间隔是不变的。
因为这里的提前期用的是变量提前期乘以物料属性提前期批量,而MRP 在计算供应起始日期和到岸日期的间隔时用的是变量提前期乘以离散任务数量。
两个来源的关系 ➢ 区别:
物料属性对MRP 负责;
后加工
固定+变量*供应的数量
预加工
工艺路线对工单负责。
➢关系:
利用工艺路线-工具-计算提前期,可以:
把工艺路线里面通过时间类、被计划、批次基准的资源计算出来的工艺路线固定提前期更新到物料属性的固定提前处;
把工艺路线里面通过时间类、被计划、物料基准的资源计算出来的工艺路线变量提前期更新到物料属性的变量提前期处;
把roundup [ 工艺路线里的固定LD +(工艺路线里的变量LD * 提前期批量)]的值更新到物料属性的加工中提前期处。
利用工艺路线-工具-累计提前期,可以:
根据BOM和工艺路线的设置,计算出累计制造提前期和累计总额提前期并把结果更新到物料属性上显示。
累计制造和累计总额
公式如下:
加工中LD=roundup [工艺路线里的固定LD+(工艺路线里的变量LD * 提前期批量)]
累计制造LD=加工中LD+max[BOM组件的(累计制造-偏置天数)]
累计总额LD=预加工LD+加工中LD+max[BOM组件的(累计总额-偏置天数)]
我们拿个例子来看。
(1)物料属性设置
(2)BOM设置
注意组件都在工序1上,所以这个例子里偏置天数为零。
(3)工艺路线设置
(4)最终结果
(5)具体过程
a.采购件不存在累计制造。
b.采购件的累计总额=物料属性的预加工LD+加工中LD+后加工LD。
如:E4=W4+X4+Y4=6+20+1=27
c.制造件的固定LD=sum(制造件工艺路线里时间类、被计划、批次基准的资源使用量)
如:A1=R2=3Day
d.制造件的变量LD= sum(制造件工艺路线里时间类、被计划、物料基准的资源使用量)
如:B1=R1+R3=(1+1)HR=(1+1)/24Day=0.0833Day
e.制造件的加工中LD= roundup [工艺路线里固定LD+(工艺路线里变量LD * 提前期批量)]
如:C1=roundup(A1+B1*Z1)=roundup(3+0.0833*400)= roundup(36.32)=37Day
f.累计制造=加工中LD+max[BOM组件的(累计制造-偏置天数)]
如:D2=C2=15;D3=C3=8
如:D1=C1+max(D2,D3)=37+max(15,8)=52Day
发散思维:如果某子装配件是最下一层,其下只有原材料,则此子装配件的累计制造等于装配件本身的加工中提前期。
g.累计总额=预加工LD+加工中LD+后加工LD+max[BOM组件的(累计总额-偏置天数)]
如:E2=W2 +C2+max(E5-0)=1+15+32=48Day
如:E3=W3 +C3+max(E6-0)=2+8+15=25Day
如:E1=W1+C1+max(E2,E3,E4)=3+37+ max(48,25,27) =88Day
h.偏置天数=BOM装配件的加工中LD*工序偏置百分比
这个例子里所有的BOM组件都在工序1上,所以偏置百分比都是0。
如果把B-D000-0631-R1-01的BOM组件B-S005-000A-00-00放到存在偏置天数的工序上,计算累计制造和累计总额的时候就更有趣了。
提前期在现实业务里应该怎么考虑怎么使用,
CRP是如何利用资源进行能力分析,
嘿嘿,请听下回分解呀。