喷漆检验记录表
油漆喷涂过程检验记录表

油漆喷涂过程检验记录表一、检验记录概述本文档记录了油漆喷涂过程中的检验记录,旨在确保油漆喷涂工艺的合规性和品质稳定性。
通过对喷涂过程中各项关键参数的检验与记录,能够及时发现问题并采取相应的措施进行纠正,确保油漆喷涂质量的一致性和满足相关标准要求。
二、检验记录细节以下为油漆喷涂过程中的具体检验记录:日期和时间- 检验日期:[填写日期]- 检验时间:[填写时间]喷枪参数检验- 喷枪压力检验:- 检验前喷枪压力:[填写数值(单位:MPa)]- 检验后喷枪压力:[填写数值(单位:MPa)]- 喷嘴检验:- 喷嘴直径:[填写数值(单位:mm)]- 喷嘴清洁程度:[填写清洁情况(良好/一般/不良)]- 喷涂速度检验:- 喷涂速度:[填写数值(单位:m/s)]- 喷涂速度是否稳定:[填写是否稳定(是/否)]油漆涂布检验- 涂布膜厚检验:- 涂布前膜厚:[填写数值(单位:μm)]- 涂布后膜厚:[填写数值(单位:μm)]- 膜厚是否均匀:[填写均匀情况(是/否)]- 涂布面积检验:- 涂布前面积:[填写数值(单位:m²)]- 涂布后面积:[填写数值(单位:m²)]- 面积覆盖率:[填写面积覆盖率(%)]涂层外观检验- 平整度检验:- 涂层平整度:[填写平整度评分(良好/一般/不良)]- 色度检验:- 颜色编号:[填写颜色编号]- 颜色匹配程度:[填写颜色匹配程度(完全匹配/基本匹配/不匹配)]- 光泽度检验:- 光泽度测量值:[填写光泽度测量值(单位:GU)]- 光泽度是否达标:[填写是否达标(是/否)]其他检验项目- 附加检验项目:[如有其他需要检验的项目,请具体列出]三、检验结果与处理根据油漆喷涂过程中的检验记录,对检验结果进行总结与处理,具体包括以下几个方面内容:- 对于合格的检验结果,进行相应的记录和归档,以备后续参考;- 对于不合格的检验结果,需及时报告相关部门,并采取相应的措施进行纠正,确保油漆喷涂质量的合规性。
检验标准(喷塑、喷漆、电镀、发黑)
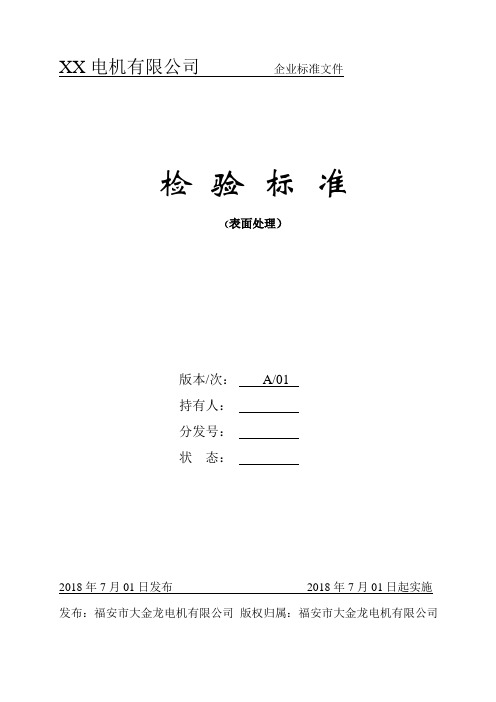
XX电机有限公司企业标准文件
检验标准
(表面处理)
版本/次:A/01
持有人:
分发号:
状态:
2018年7月01日发布2018年7月01日起实施发布:福安市大金龙电机有限公司版权归属:福安市大金龙电机有限公司
喷塑喷漆检验标准Q/YD02-2018 版次01
页次:4of5 生效日期2018/07/01
6.1.5 喷涂层均匀、完整,同批产品的光泽、纹理一致,颜色符合图号要求,且与双方封样色样比
较无明显差异。
6.1.6 点缺陷(含颗粒):
当d≤0.5mm(或s≤0.2mm2)且不连续时(ds≥5mm),不视为缺陷。
6.2 涂膜附着力:
6.2.1 划格结果附着力接收标准等级≤ISO等级:1级。
6.2.2 对比图片:
划格结果附着力按照以下的标准等级:
ISO等级:0
ASTM等级:5B
切口的边缘完全光滑,格子边缘没有任何剥落
ISO等级:1
ASTM等级:4B
在切口的相交处有小片剥落,划格区内实际破损不超过5%
ISO等级:2
ASTM等级:3B
切口的边缘和/或相交处有被剥落,其面积大于5%,但不到15%
ISO等级:3
ASTM等级:2B
沿切口边缘有部分剥落或整大片剥落,及/或者部分格子被整片剥落。
被剥落的面积超过15%,但不到35%。
喷涂质量检验标准

8.5¢6.35圆形橡皮.
8.6无水乙醇、棉质软布或脱脂棉.
8.7冲击试验仪及5倍放大镜.
表二 划格胶带附着力的评级表(JISK5400)
1.3零件的颜色、光泽和纹理均匀与标准色样板一致.
1.4颜色及外观质量均须全检.
1.5在不影响整体质量时,B级面允许有轻微补漆现象.
2.涂膜厚度检测.
2.1每批零件需抽检5件、每件测试时在零件平面区域进行,每件测5次记录其平均值于检验报告中.
2.2一般涂膜厚度要求见表<一>,图纸文件有特殊要求时以相应要求为准.
表<一>涂膜厚度对应表
序号
喷涂类型
涂膜厚度
返修品涂膜厚度
1
喷漆
30 ~ 50um
< 80um
2
油漆(洒点)
>30um
< 80um
3
平光粉
50 ~ 70um
< 125um
4
砂纹粉
60 ~ 80um
< 140um
5
桔皮粉
80 ~ 100um
< 180um
3.附着力检测:
3.1附着力一般在试片上进行检测(有特殊需要时在零件上进行);
零件涂膜表面不同位位置共做5次,然后观察涂膜表面应无任何剥落或割痕不良,则判合取5件直接在涂膜表面进行耐磨性测试.
5.2用直径为6.35的圆形橡皮垂直于涂膜表面,并施压力1.6kg左右,在行程25.4mm的范围内以每分钟
30次的速度往返摩擦30次.
5.3观察摩擦涂膜表面情况,无任何异常时判合格.
3.2每批零件附着力检查用百格刀或单面锋利刀片在涂膜上进行垂直交叉法划痕至底材金属,形成1mm2小方格,然后采用标准的胶带紧贴涂层5分钟左右,手持胶带一端与涂膜表面 垂直迅速地将胶带撕下,观察方格表面情况,要求100﹪附着,并按照表<二>:划格胶带法附着力的评级表(JISK5400)进行判定,达到5B能则判合格
电镀件、丝印、喷漆检验标准
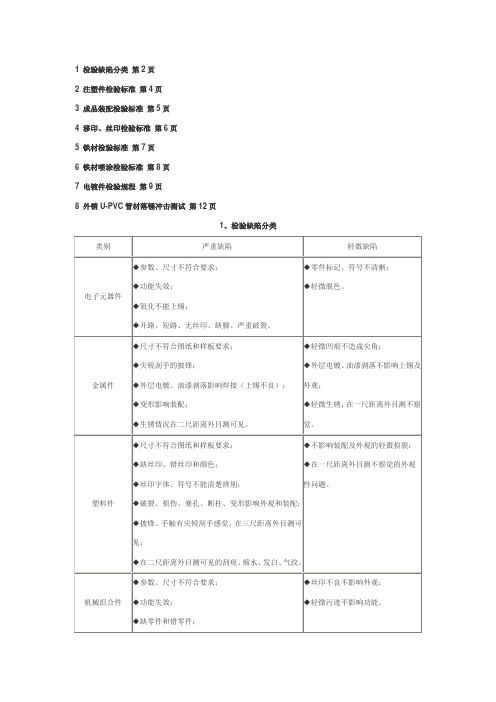
1 检验缺陷分类第2页2 注塑件检验标准第4页3 成品装配检验标准第5页4 移印、丝印检验标准第6页5 铁材检验标准第7页6 铁材喷涂检验标准第8页7 电镀件检验规程第9页8 外销U-PVC管材落锤冲击测试第12页1、检验缺陷分类页码:P2/2 2、注塑件检验标准页码:P1/13、成品装配检验标准页码:P1/14、移印、丝印检验标准页码:P1/15、铁材检验标准页码:P1/16、铁材喷涂检验标准页码:P1/17、电镀件检验规程1目的制定本标准以有效地控制电镀产品的质量。
2范围本标准适用于公司产品的零部件镀锌层的质量验收。
3术语3.1表面缺陷镀层表面缺陷是指镀层表面上特别是镀件的主要表面上的各种针孔、麻点、起皮、起泡、削落、阴阳面、斑点、烧焦、雾状、树状各海绵状沉积层,以及应当镀覆的部位等。
3.1.1针孔从镀层表面贯穿到镀层底部或基本金属的微小孔道。
3.1.2麻点在电镀过程中由于种种原因而在电镀表面形成的小坑。
3.1.3起皮镀层呈片状脱落基体现象。
3.1.4起泡在电镀中由电镀层与底金属之间失去结合力而引起一种凸起状缺陷。
3.1.5削落由于某些原因(例如不均匀的热膨胀或收缩)引起的镀层表面的破裂或脱落。
3.1.6阴阳面指镀层表面局部亮度不一或色泽不均匀缺陷,多数情况下在同类产品中表现出一定的规律。
3.1.7斑点指镀层表面的类似色斑、暗斑等缺陷。
它是由于电镀过程中沉淀不良、异物粘附或钝化液清洗不干净造成。
3.1.8烧焦镀层在过高电流的情况下形成的黑暗色、粗糙松散、质量差的沉积物,其中含有氧化物或钝化液清洗不干净造成。
3.1.9雾状指镀层表面存在程度不同的云雾状覆盖物,多数产生于光亮镀层表面。
页码:P1/33.1.10树枝状结晶电镀时在阴极上(特别是边缘和其他高电流密度区)形面的粗糙、松散的树状或不规则突起的沉积物。
3.1.11海绵状镀层现基体材料结合不牢固疏松多孔的沉积物。
3.2镀层厚度的术语3.2.1主要表面制件上某些已处理或待处理覆盖的表面,在该表面上覆盖层对制作的外观和(或)使用性能是重要的。
检验标准(喷塑、喷漆、电镀、发黑)
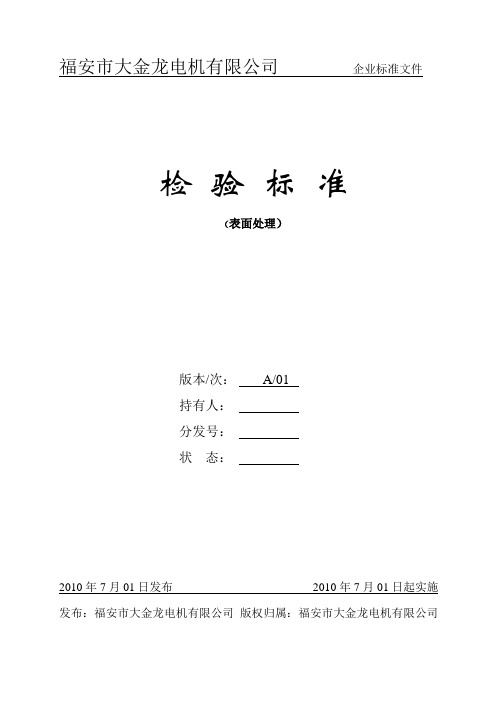
福安市大金龙电机有限公司企业标准文件
检验标准
(表面处理)
版本/次:A/01
持有人:
分发号:
状态:
2010年7月01日发布2010年7月01日起实施发布:福安市大金龙电机有限公司版权归属:福安市大金龙电机有限公司
Q/YD02-2010 版次01
页次:4of5 生效日期2010/07/01
6.1.5 喷涂层均匀、完整,同批产品的光泽、纹理一致,颜色符合图号要求,且与双方封样色样比
较无明显差异。
6.1.6 点缺陷(含颗粒):
当d≤0.5mm(或s≤0.2mm2)且不连续时(ds≥5mm),不视为缺陷。
6.2 涂膜附着力:
6.2.1 划格结果附着力接收标准等级≤ISO等级:1级。
6.2.2 对比图片:
划格结果附着力按照以下的标准等级:
ISO等级:0
ASTM等级:5B
切口的边缘完全光滑,格子边缘没有任何剥落
ISO等级:1
ASTM等级:4B
在切口的相交处有小片剥落,划格区内实际破损不超过5%
ISO等级:2
ASTM等级:3B
切口的边缘和/或相交处有被剥落,其面积大于5%,但不到15%
ISO等级:3
ASTM等级:2B
沿切口边缘有部分剥落或整大片剥落,及/或者部分格子被整片剥落。
被剥落的面积超过15%,但不到35%。
编制:江智平审核:批准:。
整机涂装工艺规程及检验标准

涂装工艺、检验标准、质量要求一、工艺流程及技术要求油漆涂装工艺流程:1、铸件、结构件→抛丸室→手动抛丸→清理→人工打磨→喷底漆→自然干燥。
2、滑块部件:高性能及其变形产品系列产品,L36系列、L31系列、E36系列、E31系列等整体闭式半闭式单双点产品,JF36系列、JK36系列机床,F75G 系列、VH系列、SH系列机床-滑块、连杆(含连杆盖)在机加工完成后,转油漆工序按成品油漆标准进行涂装(不含滑块斑马线),转装配总装后不再油漆。
(使用带防护吊具,生产全过程注意油漆面防护)3、机身部件:(1)高性能等整体机身机床(不含VH系列、SH系列),机身在机加工完成后,转油漆工序,其内腔按成品油漆标准进行涂装,侧面安装电箱部位喷成机床主色;机床在完成传动部分装配(不再需翻身)后,机床立放进行成品油漆。
(使用带防护吊具,生产全过程注意油漆面防护)(2)其余分体机床的上横梁、立柱、底座及VH系列、SH系列机床机身,在机加工完成后转油漆工序,外表面及内腔均按成品油漆标准进行涂装;机床装配完成后不再油漆。
(使用带防护吊具,生产全过程注意油漆面防护)4、其他部件(导轨、工作台板除外):钣金件、走台围栏、蜗轮箱、大齿轮(刷黄漆)、管路等需油漆的机床所有的其他部件,转油漆工序完成成品油漆后进行装配。
(使用带防护吊具,生产全过程注意油漆面防护)5、导轨、工作台板、滑块斑马线:所有机床的导轨、工作台板、滑块斑马线在完成性能交验合格后进行成品油漆。
(使用帆布带吊绳、台板起吊专用工装安装工作台板)二、结构件(铸件)涂装工艺规程及检验标准1、抛丸1.1对转入抛丸工序的工件进行核实确认,并规范填写《抛丸工序记录表》,保证产品的可追溯性。
1.2操作前首先检查风机、管路输送等设备是否运转正常;喷丸服、视镜是否完好、输气管是否通畅,确认合格后方可经行抛丸工序的操作。
1.3经抛丸后的工件应达到表面无锈点、氧化皮、污垢。
要求达到瑞典分级表Sa2.5级,钢面呈均匀银白色金属光泽。
喷漆过程检测记录表
异常情况记录
异常情况
原因分析
处理措施
负责人
处理日期
检测结果汇总
-检测项目总数:XX
-合格项目数:XX
-不合格项目数:XX
-合格率:XX%
备注
-若出现不合格项目,应详细记录原因及处理措施,并由负责人签字确认。
-检测记录表应保存至少一年,以备查阅。
-若检测结果存在争议,应重新进行检测。
喷漆过程检测记录表
检测项目检测Biblioteka 目检测标准检测结果
备注
喷漆前表面处理
表面应清洁、无油污、锈迹等
合格
喷漆厚度
应符合产品要求
合格
喷漆均匀度
颜色应均匀一致,无明显色差
合格
喷漆干燥度
喷漆后应完全干燥
合格
喷漆后表面光泽度
应符合产品要求
合格
喷漆后硬度
应符合产品要求
合格
喷漆后附着力
应符合产品要求
合格
检测人员
-检测人员:XXX
请根据实际情况填写以上内容,以确保喷漆过程的质量符合要求。
喷漆过程质量检验记录表
喷漆过程质量检验记录表1. 检验记录
2. 检验项目说明
2.1 喷漆颜色
检验喷漆颜色是否符合要求,与样品对比确认。
2.2 喷漆涂层厚度
使用涂层厚度测量仪器,测量喷漆涂层的厚度,确保在规定范围内。
2.3 喷漆涂层附着力
使用附着力测试仪器,测试喷漆涂层与基材之间的附着力,确保附着力良好。
2.4 喷漆表面光泽度
使用光泽度测试仪器,测试喷漆表面的光泽度,确保光泽度符合要求。
2.5 喷漆表面平整度
视觉检查喷漆表面是否平整,无明显凹凸或起泡。
2.6 喷漆涂层硬度
使用硬度测试仪器,测试喷漆涂层的硬度,确保硬度符合要求。
3. 结论
以上检验记录表中的项目均符合要求,喷漆过程质量良好。
喷漆检验报告
06 附录
检验原始数据记录
检验日期:XXXX年XX月XX 日
检验人员:XXX
02
01
检验设备:显微镜、色差仪、
光泽度计
03
检验步骤:按照GB/T 97962008标准进行样品的制备、
观察和测量
04
05
检验结果:附表1-1
喷漆样品照片及对比分析图
喷漆样品照片:附图1-1至附图1-5 对比分析图:附图1-6
04 检验结果与分析
喷漆外观质量检查结果
总结词
表面光滑、色泽均匀
详细描述
经过仔细检查,喷漆表面光滑,无颗粒、气泡等缺陷,色泽均匀一致,无明显 色差。
喷漆附着力测试结果
总结词
符合标准、性能良好
详细描述
根据附着力测试标准,喷漆与基材的附着力表现出色,无剥落、起泡等现象,符 合质量要求。
喷漆耐磨、耐腐蚀性能检测结果
详细描述
将本次检验的喷漆样品与已知标准或样品进行对比分析,结 果显示本次检验的喷漆在外观质量、附着力、耐磨、耐腐蚀 等方面均表现出优异的性能,达到预期目标。
05 结论与建议
检验结论概述
本次检验对喷漆的外观、附着力、耐 磨性等指标进行了全面检测,综合评 估了喷漆的质量。
喷漆的附着力、耐磨性等性能指标均 达到预期要求,能够满足使用要求。
《汽车行业喷漆技术规范》 《家具行业喷漆技术规范》 《建筑行业喷漆技术规范》
客户要求及合同约定Fra bibliotek01客户提供的特殊技术要求及图 纸
02
合同中约定的质量要求和验收 标准
03
客户提供的样品或色卡进行比 对
03 检验方法和流程
取样方法
随机取样
在生产线上随机选取一定数量的 喷漆产品作为样本。
喷漆特殊过程力确认表
2#样件参数
3#样件参数
醇酸漆:稀释剂=2:1
10kg:5kg
10kg:5.1kg
10kg:5.2kg
油漆粘度15-25s
15s
20s
25s
压力0.4-0.6Mpa
0.4 Mpa
0.5Mpa
0.6Mpa
烘干温度180-200℃
180℃
190℃
200
干燥时间12小时
12小时
12小时
12小时℃
特殊过程能力确认记录
工序名称
喷漆
产品名称
日期
过程控制文件
喷漆作业指导书
过程设备
名称
型号规格
设备能力确认
空压机
设备完好,能满足工艺要求
人员能力
姓名
培训情况
人员能力确认
×××××
经过作业指导书培训
能掌握调漆喷漆工艺要求
材料确认
材料名称
型号规格
确认结果
漆
现场使用的油漆与作业指导书一致
工艺参数确认
工艺参数要求
产品质量要求
检验项目
质量要求
1#件实测
2#件实测
3#件实测
外观
均匀、无流挂、色泽光亮
符合
符合
符合
漆面附着力
等级
符合
符合
符合
漆膜厚度
60-80μm
68μm
73μm
78μm
工作环境要求Fra bibliotek适宜确认结果
符合要求
过程确认结论
经确认该工序能力能满足要求
确认人