精益生产改善提案各部们指标一览表
精益生产五大指标

5、 DTD:Dock to Dock有效生产周期
• 定义:指从原材料到发运 产品之间的总运转时间间 隔;用于测量原材料转化 成成品发运的速度,也就 是通过工厂的速度,而不 是加工工艺的速度。
Ó ¶ Ð Á È µ ò º
1、BTS:Build To Schedule生产计划完成率
定义:BTS是在指定的生产日按照正确的生产 顺序完成生产计划的比例情况。 是三个(总的数量是否满足符合性、品种是否 满足符合性、顺序是否满足符合性)不同的计 算值的乘积;
作用:用来显示工厂、生产线 以正确顺序、在正确时间、产出 正确产品的执行程度 。
每天客户需求数量
例子:
节拍时间 = (60 x 17.0) - ((15+15+30+20)x2) 258 件 860 分钟 x 60 秒/分 258 件 = = 860 分钟 258 件
ABC 装配线 节拍时间
=
200 秒/件
争取使每一工位每3分20秒生产一件合格品
需要多少操作工?
• The number of operator is calculated by dividing the sum of the operator work ( value added + non value added )by the Module Takt Time • 操作工的数量等于总的单件产品的人工工 作量除以单条生产线之节拍时间
精益生产五大指标
1、BTS:Build To Schedule 生产计划完成率 2、FTT:First Time Through 首次通过率 (一次交验合格率) 3、OEE:Overall Equipment Effectiveness 设备综合利用率 4、TT:TAKT Time 节拍时间 5、DTD:Dock to Dock 有效生产周期
精益生产自主改善之提案改善
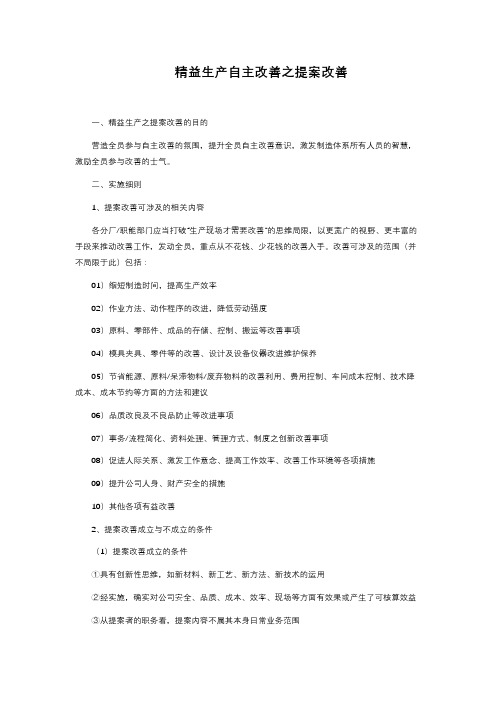
精益生产自主改善之提案改善一、精益生产之提案改善的目的营造全员参与自主改善的氛围,提升全员自主改善意识,激发制造体系所有人员的智慧,激励全员参与改善的士气。
二、实施细则1、提案改善可涉及的相关内容各分厂/职能部门应当打破“生产现场才需要改善”的思维局限,以更宽广的视野、更丰富的手段来推动改善工作,发动全员,重点从不花钱、少花钱的改善入手。
改善可涉及的范围(并不局限于此)包括:01)缩短制造时间,提高生产效率02)作业方法、动作程序的改进,降低劳动强度03)原料、零部件、成品的存储、控制、搬运等改善事项04)模具夹具、零件等的改善、设计及设备仪器改进维护保养05)节省能源、原料/呆滞物料/废弃物料的改善利用、费用控制、车间成本控制、技术降成本、成本节约等方面的方法和建议06)品质改良及不良品防止等改进事项07)事务/流程简化、资料处理、管理方式、制度之创新改善事项08)促进人际关系、激发工作意念、提高工作效率、改善工作环境等各项措施09)提升公司人身、财产安全的措施10)其他各项有益改善2、提案改善成立与不成立的条件(1)提案改善成立的条件①具有创新性思维,如新材料、新工艺、新方法、新技术的运用②经实施,确实对公司安全、品质、成本、效率、现场等方面有效果或产生了可核算效益③从提案者的职务看,提案内容不属其本身日常业务范围④与提案者本身业务相关,但涉及其它部门业务的内容(2)提案改善不成立的条件①同一个人的同一内容的提案②已经在工作中实施的相同内容的项目、提案时间较晚的同一内容的项目(重复申报)③改善对其它各方面产生了相当大的副作用④针对专门问题组成的专门机构,进行的改善工作,技改投资等⑤无创意性的希望、批判、投诉、牢骚或不满等⑥无创意、无窍门的5S(如现场整理、整顿之类)⑦提案内容不在合肥工厂任何部门能力范围内的提案,例如:需要事业部部门或者其它产品公司解决的提案。
⑧从提案者的职务看,提案内容属其本身日常业务范围⑨提案内容不切实际,或者无可实施性、无可操作性⑩提案虽然符合成立条件,但实施投入较大,且相对改善效益较小(3)提案改善类型提案人在提案报告中必须确认该提案所属类型,提案改善类型分为以下几类:①品质改善:包括降低产品不良,防止不良产生的方法改善等;②工艺改善:通过优化产品设计,提高产品性能,提高生产效率,增强客户满意度的改善等;③成本改善:包括可降低生产、采购、管理、能源方面成本的改善,且对改善效果能进行明确的经济核算;④IE改善:包括通过IE手法,优化作业动作与流程、减少空间浪费,提升效率的改善;⑤管理改善:包括优化工作流程,提高运营、办事效率,提高员工士气,改善环境,增强安全等方面的改善;⑥设备改善:包括降低设备停机时间,提高设备使用效率,制作工装、容器的改善。
质检班精益生产改善提案

质检班精益生产改善提案1作为一个生产制造企业,精益管理包含了精益设计和精益生产。
精益设计在于主要减少在生产过程中不必要的材料成本浪费和作业成本浪费。
而精益生产则是通过尽可能的优化生产流程,提高生产效率和品质,从而达到精益生产管理的目标。
2对于工厂企业来说,原材料成本一般会占了总成本中较高的份额,所以精益设计非常重要,是节约成本的关键因素。
工厂企业要做好精益设计,需要非常深厚的技术沉淀,有经验丰富的技术工程师。
如果一定要使设计完美,需要经过很长时间的反复的模拟、改善、优化的过程,而在实际生产经营活动中时间总是有限的,因此精益设计就是通过在生产中的实践,不断对产品、工艺和流程进行改善优化的过程,这就是持续改进的的过程。
工厂企业的产品生产是先有订单后安排生产,所以向用户保质保量保节点地交付产品,形成实质性的产品交易是锻造企业精益管理的目标。
精益生产的核心是识别解决生产中的瓶颈,最好是提前进行评估,找出瓶颈,直接解决或找到替代方案。
精益管理的核心在于对一个具体的产品订单,在现有资源的条件下,评估瓶颈和风险,在有限的时间节点要求内,以最快的速度最有效最经济的方法完成设计和解决瓶颈问题,打通工艺路线,保质保量保节点完成生产交付,形成实际的产品交易,取得货款回收权,在此基础上开展持续各项改进工作。
3综上所述,精益管理是现代企业的一个基础课,企业要保持稳定发展的势头,精益管理是必不可少的能力,只有每一个管理者和员工都对精益管理有深入的认识,才会在管理中真正把精益细节做到位,才能使企业从中受益。
因此为激励员工共同参与公司质量改善,以达到降低成本、提升品质、增强公司经营效益,可以通过进行开展精益改善提案活动。
精益改善提案活动是指在准时交货、生产效率、库存、生产周期、质量管理、设备管理、现场工作环境、员工整体素质、剔除浪费、管理提升等方面的方法流程前后发生可对比的改变,带来实际性正面效果的临时性变革活动。
精益改善提案项目是指一系列独特的、复杂的并相互关联的活动,这些活动有着一个明确的目标或目的,必须在特定的时间、预算、资源限定内,依据规范完成。
精益生产评价表
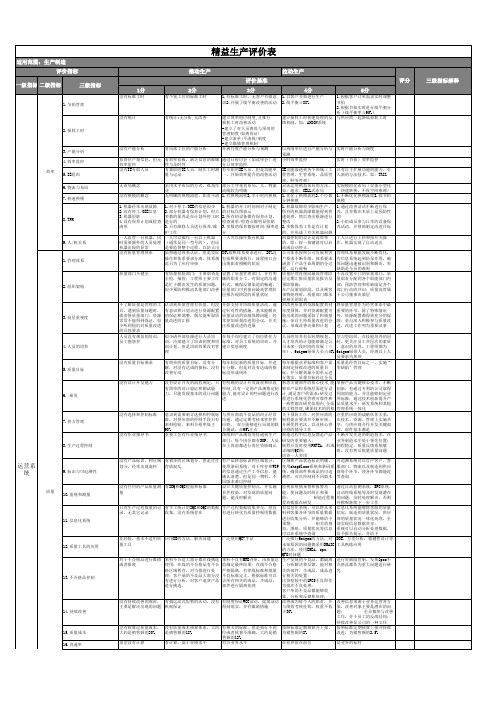
量与记录
一,开始效率提升的改善活动 程管理、生管系统、品质管 入新的方法技术。如:TRIZ
理、财务管理)
无布局概念
采用水平布局的方式,孤岛作 部分工序垂直布局,人、物流 灵活运用精益布局的方法。 实现模组化布局(设备小型化
业
动线较为明确
如:超市、CELL式布局
、快速转换,不收空间束缚)
没有换模的概念
部;预防管理和零缺陷是各个
很少预防和推动其他部门改善 质量部门可直接向最高管理阶 在产品策划阶段,以及顾客 部门行动的共识;质量高管属
层报告现阶段的质量状况
事物处理时,质量部门都承 于公司董事决策层
担相关的职责
不了解质量是管理的工 认识到质量管理有价值,但没 开始支持并协助质量活动,通 对改善质量的资源配置列到 将质量管理作为经营体系中最
进行挑选。
部件进行隔离处理
为批次不良处理;
客户单的不良品都能够收
集,分析和反馈和处理;
没有持续改善的规范, 有搞运动式短暂的活动,没有 有制度保证WCC活动,提案活动 改善成为每个人的职责,并 改善信息来源于业务运营各方
主要是解决出现的问题 机制保证
得到落实,并有激励措施
与绩效考核挂钩,权重不低 面,改善对象主要是潜在的问
质量 10.监视和测量
11.信息化系统
12.质量工具的应用
13.不合格品控制
14.持续改善
15.质量成本 16.直通率
精益生产评价表
推动生产
拉动生产
评价基准
评分
1分
2分
3分
4分
5分
没有标准工时
有个别工位的标准工时
1.有标准工时,无客户节拍意 1.以客户节拍进行生产
通用汽车精益生产主要指标介绍

2024/6/30
27
例子
方案A:
过程#1 = P1 ;过程#2 = P2 ;……过程#= Pn 第一季度91天的可利用时间小时数是2184; n = 过程数; 直接时间能力利用 可用时间 = 2184 × n 91天的总直接时间小时数 = S.T.P1 + S.T.P2 ……+ S.T.Pn 直接时间能力利用 = 总的直接时间小时数/可用小时数 计划维修,加班时间和闲置时间能力利用来的计算方法重 复即可。
应用/信息
• 设备能力利用的计算应考虑在每个要汇报的工厂 中所有的生产过程/设备,可以考虑加权,以 更 真实地反应设备的利用状况。
• 当总计几个工厂或部门时,有必要考虑根据预计 更换价值对每个工厂和部门进行加权。不应使用 所有的其它加权方法(例如:使用直接劳力方 法)。把资金密集的单一的过程与多个低成本过 程简单相加,将曲解其真实的设备能力利用率, 这种状况更显加权的重要。
2024/6/30
29
通用汽车精益生产 DMS--主要指标6
生产率
2024义: 是指在一段时间内发出产品的总工时数与这段时间内总工 作小时数的比值.
• 目的:在工厂,部门,小组的水平上,用作判断一段时间内生产率 提高速率的工具,是年度值。
• 公式: 生产率 = 总发货工时数 (到客户) /总工作小时数(薪金人员和直 接人员)(包括加班工时)
100点/小时 或 • 标准工时/件=时间/件(小时)=0.03945 小 时/件.(例) • 总发货工时 = (36,370 件/月*0.03945小时 /件)= 1434运送小时/月.
×100 – 闲置时间比率%=(停工时间小时数/可利用时间)×100 – 总的比率 = 100%
改善专案实施方案(精益生产必看)
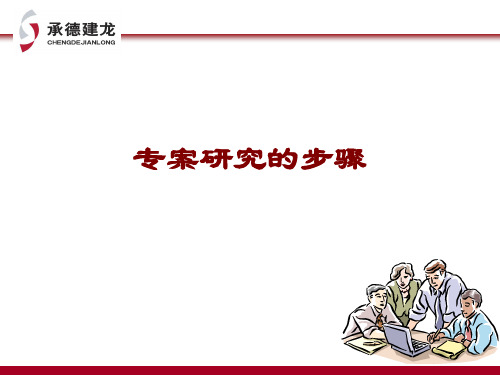
作业条件、作业环境如何?
材料品质状况如何?
材料
材料库存数量是否合适?
材料存放、搬运方式好不好?
作业标准内容是否合适?
方法
作业前后的准备工作是否经济高效?
前后工序的衔接好吗?
作业安全性如何?
使用问题检查表,
逐条对照找出问题点
STEP2选定题目
1.选题方向
(1)生产及设备效率改善;(2)产品品质及价值改善;
3.1.作用
•加工工序中是否存在不合理﹑停滞等作业现象,取消它们;
•合并一些过于细分或重复的工作,提高产线平衡率;
•检查是否有导致相同作业动作无价值重复的作业程序,改变它们避
免重复作业;
•分析搬运、物流状况,调整布局,以减少搬运,提高物流效率;
•整理加工工序流程,使其合理、平衡、经济
STEP2选定题目
降本增效
P
D
C
A
专案改善
方针管理
– 选择降本
增效点
– 立项
方针确定
– 设定月和
年度目标
– 设定目标值
设定标杆值
– 制定改善
方案
– 对策制定
制定执行方案
– 方案实施
– 对策实施
– 按月统计
降本增效
成效
– 检讨与分
析
方案实施
– 效果确认
方针检讨
– 标准化
前言
面对微利时代的冲击
赚一块不如省一块
改善
赚钱要看别人的脸色
找到问题根源
墙裂被修好
采取
措施
拉上窗帘
为什么 每天用清 墙壁上 燕子多 蜘蛛多 飞虫多 环境适宜 开窗户
墙会裂? 洁剂冲洗 有鸟粪
精益生产改善提案
精益生产改善提案
插件工序动作分析要素调查汇总
汇总动作改善提案问题分析
一、料盘改成随意组装可减少作业空间的占用并减小动作距离
二、椅子改成高矮可调控可减轻身体疲劳
三、防静电手腕改成无绳可便于元器件的取放
说明:由于插件动作改善提案最终并未能根据改善建议进行改善(经评审,椅子改成高矮可调暂不实施;可组装料盘与无绳防静电手腕正在联系中),所以无改善后的分析及具体改进的经济性分析。
并插件动作改善提案动作要素不能量化,所以无法形成图示。
精益生产:公司生产效率提升改善项目报告
制作夹具,简化工艺 普通焊机改为储能式焊接机,减少后工序作业
人员 手动大螺丝改为自动打螺丝
月份
6月 6月 6月 6月 6月 6月 6月 6月
10
19系列天花灯固定器改善
螺丝加固定器改为半牙螺丝,取消固定器
6月
4.过程亮点展示
4.1、98,143系列压线扣工艺改善
1.压线扣单价0.03元 ,预计每年省1万元
54229.5
线外人员出勤
3298 457 488 1528 3595.5 9366.5
UPPH 151.98 35.15 39.78 76.96
2.70 345.67
数据分析 基准值 129.30 29.97 35.21 66.33
2.30
提升比率 17.54% 17.28% 12.98% 16.02% 17.56%
确认
2
953A 670 17 498 11 477 11 6 10.07%
3
9225N 650 19 535 13 483 13 6 8.52%
4
923N 650 19 535 13 479 13 6 7.63%
组装
5
9825 530 23 424 16 402 16 7 9.21%
6
983
530 23 424 16 419 16 7 11.02%
生物颗粒
优
高效,熔炼,安全 方便,灵活,节能 低碳,环保,恒温
4.过程亮点展示
4.7、异形插件机方案拟定
改善前视频
改善后方案视频
4.过程亮点展示
4.8、筒灯自动化生产线方案确认
筒灯自动化线视频
4.过程亮点展示
精益生产改善提案管理办法
. . .XXXXXXX公司精益生产改善提案实施办法批准:审核:编制:生效日期:年月日1.目的挖掘员工潜能,激发员工的活力和创造力,以主人翁的态度,推进企业技术进步,推动全员参与改善工作,实现经济效益最大化,为促进企业的快速发展做贡献。
2.适用围本办法适用于高强紧固件有限公司群众性改善提案的管理与组织工作。
参与对象为高强紧固件有限公司所有员工,重点对象是各生产班组一线员工。
3.引用文件《员工提案管理制度》、《精益生产理念》4.术语4.1班组本办法中,除特殊注明的,所称班组指生产一线班组。
4.2改善提案4.2.1改善提案的定义针对现状,提出的更好的法、措施或设想。
主要包括针对质量、成本、交货期、安全、环境面的问题及对策,基本要素包括:针对的问题、准备采取的措施、以及预计达到的效果。
4.2.2按提案提出对象来分:个人提案:指员工个人提出来的一些比较简单易行的改善提案或建议。
团队提案:指员工或团体提出针对公司业务流程(包括物料、品质、成本,机器等)等面的一些大的改善项目。
4.2.3本办法所称改善提案,均须符合公司有效建议的要求。
4.2.4. 精益生产改善提案的一般围。
4.2.4.1 现场类主要包括:工具、设备、仪器、装置的创新、改进;生产工艺、操作法、制造技术的进步;安全隐患排除;安全生产、劳动保护、环境保护的法和手段的创新、改进;物资储藏、运输技术的创新、改进;节约能源;更有效地利用原料、材料、设备及自然条件的技术措施;4.2.4.2经营管理和服务类主要包括:在现场管理、管理技术上有创新,对提高经营管理、提高经营效益或成本效益有指导作用;在工作组织、制度规定等面提出的办法或改进案,对提高工作效率、员工满意度或服务质量有显著效果4.2.4.3提案如果属于下列各项围,视为不适当提案不予受理:攻击团体或个人的投诉、抱怨等;个人意见、诉苦或要求改善待遇、福利等;与曾经提出或者曾经采用过的提案容相同或者相近者;属于本身工作职责围的提案。
精益生产全套表格
├─第一│表1-1 5S 活动推行日程打算表.doc│表1-10 现场改善清扫清单.doc│表1-11 现场改善清洁清单.doc│表1-12 现场改善素养清单.doc│表1-13 现场巡察判定表.doc│表1-14 生产现场5S 评分标准表.doc │表1-15 划线识别系统表.doc│表1-16 可视化治理清单.doc│表1-17 时间铺张自检表.doc│表1-18 等待铺张自检表.doc│表1-19 库存铺张自检表.doc│表1-2 5S 训练打算表.doc│表1-20 材料与供给品铺张自检表.doc │表1-21 机器设备铺张自检表.doc│表1-22 人力铺张自检表.doc│表1-23 处理意外事故铺张自检表.doc │表1-24 空间铺张状况自检表.doc│表1-25 动作效率检查表.doc│表1-3 5S 训练签到记录表.doc│表1-4 5S 问题改善通知书.doc│表1-5 5S 治理达标申请书.doc│表1-6 5S 治理评比申诉表.doc│表1-7 5S 治理问题提醒单.doc│表1-8 现场改善整理清单.doc│表1-9 现场改善整顿清单.doc│├─其次│表2-1 产品用料分析表.doc│表2-10 各单位出入物料搬运分析表.doc │表2-11 物料搬运分析表.doc│表2-12 物料搬运途径分析表.doc│表2-13 搬运设备打算表.doc│表2-14 搬运作业工作分析表.doc│表2-2 物料需求分析.doc│表2-3 物料ABC 分析表.doc│表2-4 物料需求打算.doc│表2-5 呆料处理报表.doc│表2-6 废料处理报表.doc│表2-7 滞料处理记录表.doc│表2-8 滞料处理汇报表.doc│表2-9 呆料废料处理打算表.doc│├─第三│表3-1 TPM 改善打算.doc│表3-10 改善事例记录.doc│表3-11 简易型提案格式.doc│表3-12 一般型提案格式.doc│表3-13 设备不正常点分析.doc│表3-14 发电机开机前点检表.doc│表3-15 发电机运行中点检表.doc│表3-16 发电机〔房〕周期点检表.doc│表3-17 抱负工厂评价表单.doc│表3-18 TPM 提案评价表.doc│表3-19 TPM 娴熟度评价.doc│表3-2 TPM 推动人员推举表.doc│表3-20 设备综合效率水平评价表.doc│表3-21 设备保修水平自我评价.doc│表3-3 设备自主保全诊断表.doc│表3-4 组装自主保全诊断表.doc│表3-5 自主保全诊断表〔仓库、放置场所〕.doc │表3-6 全员诊断申请书.doc│表3-7 物品报废及处理申请表.doc│表3-8 自主保全活动报告书.doc│表3-9 TPM 会议记录.doc│└─第四表4-1 月份质量问题分析表.doc表4-10 检验托付单.doc表4-11 进厂零件质量检验表.doc表4-12 零件检验报告表.doc表4-13 材料检验报告表.doc表4-14 材料试用检验通知单.doc表4-15 进厂检验状况每日报表.doc表4-16 说明书质量检验表.doc表4-17 设备验收单.doc表4-18 特采、让步使用申请单.doc表4-19 退货单.doc表4-2 年度质量问题统计表.doc表4-20 供货商质量统计表.doc表4-21 供给商质量评价表.doc表4-22 供给商质量治理检查表.doc表4-23 供给商根本资料表.doc表4-24 供给商考核表.doc表4-25 供给商现场评审表.doc表4-26 供给商综合评审表.doc表4-27 合格供给商名单.doc表4-28 质量预防费用统计表.doc表4-29 质量鉴定费用统计表.doc表4-3 质量教育年度打算表.doc表4-30 质量内部故障统计表.doc表4-31 质量外部故障统计表.doc表4-32 质量本钱统计报表.doc表4-33 质量本钱统计报表补充资料.doc表4-34 产品质量本钱损失估量表.doc表4-35 质量改进费用汇总表.doc表4-36 取消订单损失报告表.doc表4-37 质量会议工资费用计算表.doc表4-38 质量培训费用计算表.doc表4-39 质量嘉奖费用计算表.doc表4-4 质量教育长期打算表.doc表4-40 不行修复废品损失计算表.doc表4-41 可修复废品损失计算表.doc表4-42 产品质量停工报告表.doc表4-43 质量事故处理费用计算表.doc表4-44 产品降级、降价处理损失报告表.doc表4-45 间接质量费用安排表.doc表4-46 车间质量治理费用月报.doc表4-47 车间质量损失费用月报表.doc表4-48 主要产品单位质量本钱表.doc表4-49 产品质量改进记录表.doc表4-5 本企业产品与竞争对手产品质量比较表.doc表4-50 产品质量改进分析表.doc表4-51 质量因素改善结果记录表.doc表4-6 质量治理小组活动报告表.doc表4-7 质量治理小组会议报告表.doc表4-8 质量治理小组活动成果报告表.doc表4-9 质量治理小组活动企业大会用表.doc│├─第五│表5-1 生产效率记录表.doc│表5-10 标准作业时间争论.doc│表5-11 标准作业时间核定.doc│表5-12 标准作业时间测定.doc│表5-13 流水线工序平衡测定表.doc│表5-14 流水线瓶颈工序分析表.doc│表5-15 流水线非平衡工序分析与改善表.doc│表5-16 流水线各工序动作分析、改善表.doc│表5-17 流水线各工序操作规程指导表.doc│表5-18 流水线关心工装及标识使用考察表.doc │表5-2 设备利用率分析表.doc│表5-3 生产效率不佳缘由分析表.doc│表5-4 生产作业改善打算表.doc│表5-5 生产作业改进建议报告.doc│表5-6 生产作业流程程序图.doc│表5-7 生产作业流程分析.doc│表5-8 人机协作分析表.doc│表5-9 生产时间争论记录表.doc│├─第六│表6-1 工厂设置安全检查表.doc│表6-10 电气安全检查表.doc│表6-11 锅炉安全检查表.doc│表6-12 管线和阀门安全检查表.doc│表6-13 带压及真空排放安全检查表.doc │表6-14 机械安装安全检查表.doc│表6-15 操作安全治理检查表.doc│表6-16 防灾设施安全检查表.doc│表6-17 安全嘉奖通知.doc│表6-18 安全罚款通知.doc│表6-19 分厂安全考核用表.doc│表6-2 工厂平面布置安全检查表.doc│表6-20 打算部门安全考核表.doc│表6-21 企管部门安全考核表.doc│表6-22 生产调度部门安全考核表.doc │表6-23 设备工具部门安全考核表.doc │表6-24 动力部门安全考核表.doc│表6-25 产品设计部门安全考核表.doc │表6-26 安保部门安全考核表.doc│表6-27 人事部门安全考核表.doc│表6-28 工艺部门安全考核表.doc│表6-29 物资治理部门安全考核表.doc │表6-3 建筑标准安全检查表.doc│表6-30 后勤部门安全考核表.doc│表6-4 车间环境安全检查表.doc│表6-5 厂内运输安全检查表.doc│表6-6 原、材、燃料安全检查表.doc│表6-7 工艺操作安全检查表.doc│表6-8 生产设备安全检查表.doc│表6-9 仪表治理安全检查表.doc。