5S及8大浪费
八大浪费
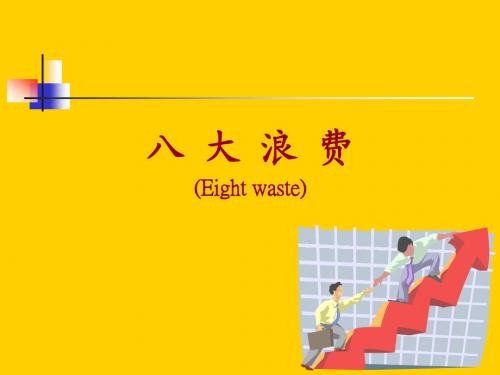
过 程 浪 费
2. 浪费的表现: 人(Man)﹕无功动作﹐等待 機(Machine)﹕等待(空载),生产力低,成本高 料(Material)﹕耗材﹐成本高 法(Method)﹕不增值﹐过度
过 程 浪 费
3. 浪费的产生: 流程(Flow)﹕流程设计﹔Layout﹔参数设定﹔ 制造系统柔性﹔浪费警觉性﹔条件 局限性﹔ 强度(Strength)﹕系统稳定性﹔标准﹔
放、反转、对准;作业步行、弯腰、转身;
(动作经济原则分析)
动 作 浪 费
勞動強度增加
滿意度低
(如例)
不必要裝PE袋 不必要的分開
动作经济原则法
分类:
关于人体的运用 关于工作场所的布置
关于设备工具的设计
动作经济原则法
关于人体的运用
1、双手应同时开始,并同时完成动作
2、除规定的时间外,双手不应同时空闭
準備作業
低價值的工作
无效的浪费
不具产值的作业
一. 不良品浪费
1. 浪费的定義:
生产过程中,因來料或制程不良,造成的 各种损失.
3. 浪费的产生:
供應
制造
不 良 品 浪 费
來料不良(Incoming)﹕供应商流出不良品﹔ 使用 物流破坏﹔进料检验﹑投入检查或后工序 未发现﹔制程不防呆﹔ 制程不良(Process)﹕作业者损坏﹔设备﹑治工 具不防呆﹔制程不防呆﹔
(勉强的作业姿态(伸背、弯腰);
3. 浪费的产生:
操作不经济(Handling)﹕动作不精简﹔动作多余 设计不合理(Design)﹕可同时完成但未同時﹔ 不必要但被增加﹔ 可同规格但不同﹔
动 作 浪 费
未考虑调整/转换/取放
物料需要翻找﹔
八大浪费演示文稿(汽车行业)
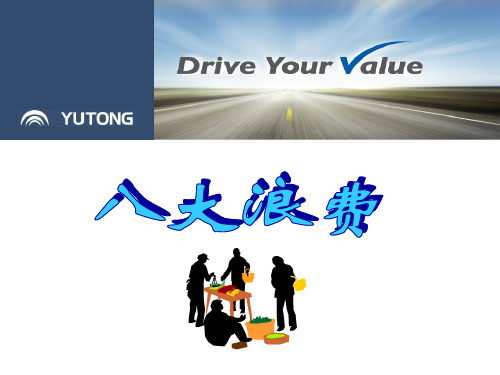
15
3.搬运的浪费
不必要的移动及把东西暂放在一旁
不必要的搬运、工作的移动、预置、改装以及长距离的搬 运流程和活性度差等
表现形式:
•搬运距离很远的地方,小批量的运输 •主副线中的搬运 •出入库次数多的搬运
长距离搬运在制品,
缺乏效率的运输,进 出仓库或在流程之间
搬运原料、零部件或
最终成品。
•破损、刮痕的发生
过多的库存会隐藏的问题点:
•没有管理的紧张感,阻碍改 善的活性化
•设备能力及人员需求的误判 •对场地需求的判断错误 •产品品质变差的可能性 •容易出现呆滞物料
对策:
5.库存的浪费
•库存意识的改革 •U型设备配置
•均衡化生产
•生产流程调整顺畅 •看板管理的贯彻 •快速换线换模 •生产计划安排考虑库存 消化
34
•因不良造成人员及工程增多的浪费
•材料费增加
对策:
7. 不良品的浪费
•自动化、标准作业 •防误装置
•在工程内做出品质保证
原因:
•标准作业欠缺 •过分要求品质 •人员技能欠缺 •品质控制点设定错误 •认为可整修而做出不良 •检查方法、基准等不完备 •设备、模夹治具造成的不良
“三不政策” •一个流的生产方式 •品保制度的确立及运行 •定期的设备、模治具保养 •持续开展“5S活动”
22
4.加工的浪费
因技术(设计、加工)不足造成加工上的浪费
原本不必要的工程或作业被当成必要
表现形式:
•在加工时超过必要以上的距离所造成的浪费
•冲床作业上重复的试模,不必要的动作
•成型后去毛头,加工的浪费 •钻孔后的倒角,纹孔作业的浪费
•最终工序的修正动作
采取不必要的步 骤,以处理零部件; 因为工具与设计不良 ,导致产生不必要的 动作及产生不必要的 瑕疵而造成缺乏效率 的处理;当提供超出 必要的较高品质产品 时,也会造成浪费。
5S及8大浪费

4S: Standardization–清洁
• 巩固前3个S的已有成就; • 完善规范、标准、制度; • 形成持续改善(消除浪费),并向其它领域进
一步深入
Implementation Guide
Employee Environment & Involvement
Workplace Organization
安全第一
Eliminate Waste
消除浪费
Each item has its own position. Each Operation has its standard and specifications. 每样资源有各自的位 置,每个操作都有标 准和规范
3S.Sweeping:
execute the rules 清扫:执行规定
诀窍在于-----
6. 资料
7. 办公用品
明确摆放点设立原则
使用频率高的东西,就近安放;
使用率低的首先考虑多余空间,其次考虑就近原则;
几乎不用的丢弃或入库。
2S: Simplifying – 整顿
整洁!有序!便于存取! 一目了然!
诀窍在于-----
• 建立划线、涂色、作标记等可视控制 • 颜色代码的规定 • 创造条件将物品整齐有序地安放好
工具箱
Clear up at any time. All resources are in the
stipulated places. All the operations follow their
standard and specifications. 随时清洁而且—资源都处在批准和指定的地方, 所有操作都遵循标准和规范
锤子在这里!
工具箱
精益生产管理八大浪费与解决方法(详细版)
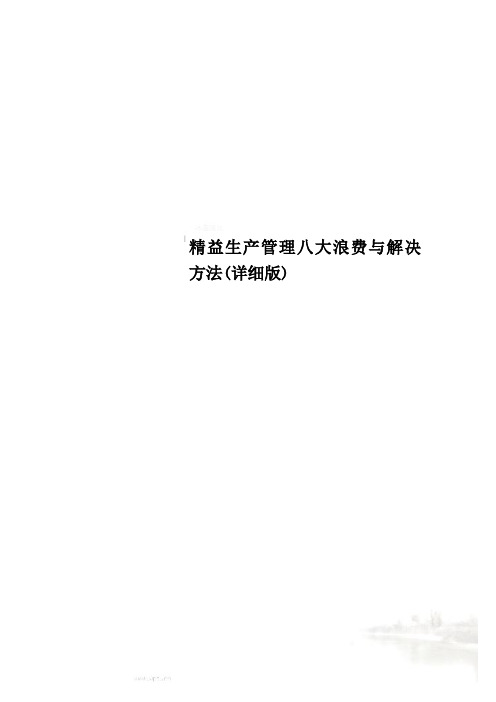
精益生产管理八大浪费与解决方法(详细版)精益生产管理八大浪费与解决方法八大浪费是丰田生产方式中非常重要的一个观念。
丰田人认为要消除浪费,持续改善,企业才能保持良性运转,竞争力才会提升。
在丰田改善是探入人心的,有个说法就是跟他们谈话5分钟没有听到他们讲3次改善就不算丰田人。
改善的对象是浪费,认识浪费是改善的第一步,企业现场林林总总,哪些是有价值的,哪些是浪费,不是一般人可以一目了然的。
丰田人在长期作业和改善过程中对于浪费的内容进行了总结,共七种,被称为七种浪费。
它们分别是制造过早(多)的浪费、库存的浪费、不良修正的浪费、加工过剩的浪费、搬运的浪费、动作的浪费、等待的浪费共七种。
后来人们又加了一种浪费-管理的浪费,合称八种浪费。
下面我们从实用性角度剖析这八种浪费。
一、精益生产管理中制造过早(多)的浪费定义:所谓制造过早(多)就是前制程制造太早/过多,大于客户(或后制程)当期的最小需要量。
制造过早(多)浪费是八大浪费中的首恶,在精益生产中则被视为最大的浪费。
福特式思维告诉大家,在同样的时间内,生产量越多,效率越高,成本越低,企业越赚钱,所以企业自然有大批量连续生产的初始动力。
作为一个整体的企业是如此,那么企业内各部门也是如此,特别是在一些制程较短,关联性较低的企业中,普遍实施计件工资,那么从最基础的员工开始就有多做、早做,甚至偷做的动力,在这种情况下,告知企业里所有人早(多)做是罪恶当然得不到掌声回应。
那么我们就来看看制造过早(多)的浪费。
制造过早(多)浪费的后果主要有三大类。
1.直接财务问题。
表现为库存、在制品增加,资金回转率低,制造时间变长,占用资金及利息,会造成库存空间的浪费,在现金流量表上很明显。
2.产生次生问题。
会产生搬运、堆积的浪费;先进先出的工作产生困难;产品积压造成不良发生,物流阻塞制程时间变长,现场工作空间变小,有滞留在库的风险,有不良品的风险。
3.掩盖问题。
为什么“制造过早(多)浪费是八大浪费中的首恶,在精益生产中则被视为最大的浪费”?因为它带给人们一个安心的错觉,掩盖了各种问题,以及隐藏了由于等待所带来的浪费,没有改善的动力,失去了持续改善的时机。
5S-八大浪费
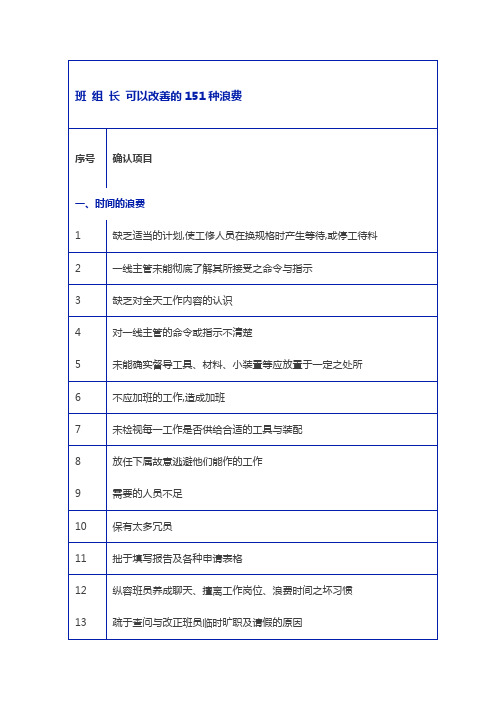
序号
确认项目
一、时间的浪费
1
缺乏适当的计划,使工修人员在换规格时产生等待,或停工待料
2
一线主管未能彻底了解其所接受之命令与指示
3
缺乏对全天工作内容的认识
4
对一线主管的命令或指示不清楚
5
未能确实督导工具、材料、小装置等应放置于一定之处所
6
不应加班的工作,造成加班
7
未检视每一工作是否供给合适的工具与装配
19
工作中不必要的谈话与查问
20
一线主管不能适当的安排自己的工作与时间
二、创意的浪费
1
未能倾听下属的建议
2
未能鼓励下属多提建议
3
在各种问题上不能广听部属的意见
4
不能广泛的研讯本身工作与业务之有关方法
5
未询问新进人员过去之工作经验,以获取有益的意见
6
未充分向其它部门(如生技等)请教
7
未考虑或指定适当人员处理所有有用的提案
13
未重视事理整顿的重要
14
未培养及督导物品用完要归定位
15
未彻底执行定期(每日、每周、每月)清理项目,以永久保持
6
纵容不满的员工煽动反抗公司的作法
7
一线主管未能给予那些尚不普及的公司规章予以全力支持
8
未能鼓舞部属间的友爱与合作的气氛
9
一线主管在本部门内轻率地批评公司政策与私人
10
在公司之教育活动上未与管理阶层诚心全力合作包括学徒训练、公布栏、提案制度等
八、空间的浪费
1
整理整顿
2
材料之不适当排放与储存
3
未充分注意材料在工厂中的途程计划
八大浪费
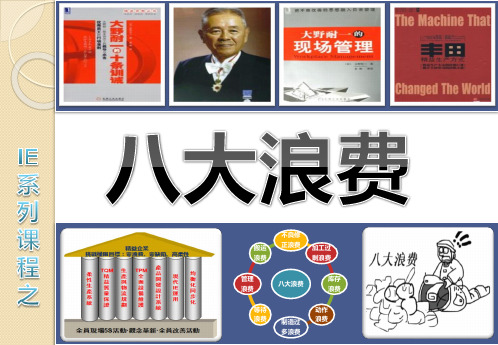
八大浪费
1
1 认识浪费
2 八大浪费详解
3 如何消除浪费
2
精益生产核心思想: 持续不断使浪费最小化、流动最大化的意识
精
适当的时间生 产必要数量的 市场急需产品
益 精 益 生 产
所有经营活动
都要有效有益,
•制订Check list发现并消 除;
设计不合理(Design):
•合理设计; •变成设计要素;
•设计验证与稽核;
•符合人体工效设计
32
7
动作浪费
1.员工需转身去取物料,包材,有 转身动作的浪费 2.长期作业员工易疲劳,不符合人 因工程
1.斜架供料,消除转身动作,降低疲劳 2.更符合人因工程,目视管理效果更好
(人員工作量不飽滿,設備稼動率低) 3.不均衡: 有時超負荷有時又不不飽和的狀態(差異狀態)。
4
浪費
不均衡
实质作业
・部件组装 ・喷涂 ・切削 ・冲压 ・焊接
作业
浪费
・等待 ・没有意义的搬运(临时放置) ・换手拿工具、部件 ・制造积压 ・部件的堆积 ・不合格品的修复
不产生附加价值的作业
・取部件、工具的行走 ・部件的开箱作业 ・部件的重新更换 ・按键按钮的操作 ・搬运作业
31
7
动作浪费
产生: 操作不经济(Handling): • 动作不精简;动作多余 设计不合理(Design): • 可同时完成但未同时; • 不必要但被增加; • 可同规格但不同; • 未考虑调整/转换/取放; • 物料需要翻找 改善方向: 操作不经济(Handling):
八大浪费及改善技法
根据明确的重点,观察现场 - 站在改善的角度,观察所有现场情况
6.
7. 8.
不要花钱进行改善
车到山前必有路 5次问“为什么”,找出根本原 因
先做不花钱的改善 - 先做不花钱的改善后,再进行 设备改善
9.
三个臭皮匠,赛过一个诸葛亮
10. 改善是无止境的 22
22
发现浪费的5个重点
“三现”主义(现场、现实、现物) - 将现场和现物分别当作管理单位和管理对象,并直接观察现实情况,获取信息,从而做 出判断 对作业进行反问 - 站在作业当中有浪费因素的观点,详细揭示作业工序
非附加价值做作业
“每次运输材料,成本都会上涨,可价值却不一定增 加”
4 Henry Royce, Rolls-Royce共同创办人
4
传统七种浪费
七种浪费 纠错型浪费 过度生产浪费 多余动作浪费 物料运输浪费 等待浪费 过量库存浪费 多余工序浪费
5
2.浪费的种类
1.过度生产浪费
2.纠错浪费
3.多余动作浪费 4.物料运输浪费 5.等待浪费 6.过量库存浪费 7.多余工序浪费 8.员工能力浪费
6
过度生产浪费
这是最糟糕的浪费方式,直接导致了其他六种浪费 过度生产浪费是指生产比实际所需更多的产品,或是生产产品 的速度超过实际所需的速度。 这种浪费增加了物料、运输、库存、人员和能源的额外成本, 是一个急需解决的问题。 在装配线上提前操作,然后等待下一次操作,这是另一种过度 生产浪费。
原因:
•生产线布置不当,物流混乱 •设备配置、保养不当
•实施目视管理
•加强进料控制
•生产计划安排不当
•工序生产能力不平衡 •材料未及时到位
注意:
•自动化不要闲置人员 •供需及时化 •作管理点数削减
八大浪费Eight waste
八大浪费Eight waste浪费:不产生任何附加价值的动作,方法,行为和计划所做的对最终的产品和顾客没有意义大野耐一:减少一成的浪费,就等于增加一倍的销售额八大浪费需熟记:等产返作制存管搬等待浪费:材料,作业,搬运,检查等活动之等待面造成的浪费过生产浪费:生产多于或快于客户的所需求而造成的浪费返工浪费:不能一次性满足客户的需求动作浪费:生产作业时调整位置,翻转产品,取放工具物料等不必要的动作浪费制程浪费:作业的流程过多,过长,重复,或强度过剩库存浪费:现有库存大于客户需求所造成的浪费管理浪费:由于事先管理不到位造成问题,对其采取相应对策进行补救而产生的额外浪费搬运浪费:对产品做不必要的移动消除一切浪费,提高效率是精益生产的核心思想(真假)浪费中最严重的是搬运(真假)5M1E/鱼骨图Explain details(含义)4M1E:Man (人) Machine (机器) Material (材料) Method (方法) Measurement (测量) Environment (环境)工序的质量受5M1E 即人,机,料,法,环境,测量六大方面的影响。
它为我们的现场管理者的管理活动提供了一种具体化,系统化的思维。
鱼骨图的三种类型:整理问题型(各要素与特性值间不存在原因关系,而是结构构成团系)原因型(鱼头在右,特性值通常以“为什么~~”来写)对策型(鱼头在左,特性值通常以“如何提高/改善~”来写)5W1H法:What (做什么) Where(何地)When(何时)Who(何人)How(如何做)Why(为何)头脑风暴法(Brain Storming—BS):一种通过集思广益,发挥团体智慧,从各种不同角度找出问题所有原因或构成要素的会议方法。
BS四大原则:严禁批评,自由奔放,多多益善,搭便车。
品质成本品质意识:1.老客户流失2.一老带30新3.市场占有率下降4.东西卖不出去5.成本扩大 6.返工造成加班和误交期7.企业形象差=没钱赚“好品质需要成本,我们把为了取得好品质而付出的费用称作品质成本”品质成本包含:预防成本鉴定成本内部故障成本外部故障成本故障相关损失品质成本=合格品成本+不合格成本(质量成本=预防成本+鉴定成本)+(内部故障成本+外部故障成本+相关故障损失费用)IE七大手法IE(Industrial Engineering)指工业工程。
班组成本控制之八大浪费
库存之“三不” 不大批量采购 不大批量生产 不大批量搬运
库存的浪费
库存浪费产生的原因: 集群式,大批量生产 供应商不稳定 呆滞物品未及时处理 视库存为当然,生产过剩 无计划/提早生产
对策: 一个流生产方式的设计 快速换模换线实施 供应商管控机制
异常物品处理流程标准制定 库存意识的改革
管理看板运用,产线管理导入
提早生产或生产了过多的、超过客户或下游工序所需要的量
这种浪费被视为 脱离了准时化生产(JIT)的原则,比需要的时候提前生产或生产数量超过了生产计划最必大要的的浪量费而!产生的库存。
由于过量生产掩盖了等待、动作、加工、搬运等浪费,又引起搬运工具、存放托盘增加等2次性浪费。
造成的浪费 ➢工序间积压在制品,交货期变长,过度占用空间 ➢工资提前支付 ➢产品积压造成不良发生 ➢提前用掉了费用(材料费、人工费)而且还增 加了产品的保管费用
实现的方法或手段
行程距离缩短
改善效果或下一步
间距缩短至20mm,花费时间 变为2s,降低3s
动作的浪费
改善前
改善后
现状问题点描述
实现的方法或手段
冲床行程过大,模具冲压时间花费2s
行程距离缩短
改善效果或下一步
冲压行程缩短,花费时间变为 1.5s,降低0.5s
动作的浪费
改善前
换模与生产 时间长
工具不合理 仓库功能区块化
对策:
整流化按工序流程配置设备 不能连接的工序尽可能的靠近 按客户需求设计产能,少人化
一个流生产方式
库存管理三原则(库位、数量、 FIFO)的贯彻,物料车设计 仓库设置在生产线附近 (店铺规划)
搬运浪费
在实际作业中减少搬运浪费的对策
1、通过改善物品的放置位置来缩短搬运距离;(就近放置) 2、通过改善作业位置来消除搬运作业; 3、缩短工位(设备・工程)之间的距离来减少搬运浪费; 3、通过辅助治具来替代人员的搬运作业;
8大浪费识别和改善制度理念
8大浪费识别和改善制度理念"8大浪费"是指在生产和运营过程中可能发生的8种浪费,这个概念起源于精益生产(Lean Production)和精益制造(Lean Manufacturing)的理念。
这些浪费是:1. 过产(Overproduction):生产超过实际需求的产品或服务。
2. 等待(Waiting):由于等待原因,造成人员、设备或信息流的停滞。
3. 运输(Transportation):在产品或信息流的运输中发生的浪费。
4. 不合格产品(Defects):生产出不符合质量要求的产品,需要重新加工或修复。
5. 过度加工(Overprocessing):对产品进行超出客户要求的过度处理。
6. 库存(Inventory):高于实际需求的产品或原材料的存储。
7. 不充分利用员工潜能(Underutilized Talent):没有充分发挥员工的能力、创造力和经验。
8. 不合理的运动(Unnecessary Motion):在工作过程中发生的不必要的动作或移动。
要识别和改善这些浪费,可以采用以下制度和理念:1. 精益生产(Lean Production):采用精益制造的方法和工具,通过持续改进来最大程度地减少浪费。
2. 5S方法:整顿、整理、清扫、清洁、素养是5S方法的关键步骤,有助于提高工作效率、减少浪费。
3. 持续改进(Continuous Improvement):实施Kaizen(改善)文化,鼓励员工参与改进工作流程和去除浪费的活动。
4. 价值流映射(Value Stream Mapping):通过绘制价值流图,识别和分析价值流中的浪费,以便有针对性地进行改进。
5. JIT(Just-In-Time)生产:通过减少库存,根据实际需求进行生产,降低过产和库存浪费。
6. 质量管理:强调预防性的质量管理,减少不合格产品的产生。
7. 员工培训和发展:提供培训和发展机会,充分发挥员工的潜能,鼓励创新和改进。
- 1、下载文档前请自行甄别文档内容的完整性,平台不提供额外的编辑、内容补充、找答案等附加服务。
- 2、"仅部分预览"的文档,不可在线预览部分如存在完整性等问题,可反馈申请退款(可完整预览的文档不适用该条件!)。
- 3、如文档侵犯您的权益,请联系客服反馈,我们会尽快为您处理(人工客服工作时间:9:00-18:30)。
定区:每个人负责的区域范围.
2S: Simplifying– 整顿
明确整顿归类的依据 1. 工具 2. 原材料/成品/半成品 整洁!有序!便于存取! 3. 另部件 一目了然! 4. 报废品 诀窍在于----5. 垃圾 6. 资料 7. 办公用品 明确摆放点设立原则 使用频率高的东西,就近安放; 使用率低的首先考虑多余空间,其次考虑就近原则; 几乎不用的丢弃或入库。
• 定义:对产品不产生价值的任何人员的设备的运作 • 表现
– – – – – – – – – – – 人找工具 大量的弯腰,抬头和取物 设备和物料距离过大引起的走动 需要花时间确认或辨认 人或机器“特别忙” 办公室、生产场地和设备规划不合理 工作场地没有组织 人员及设备的配置不合理 没有考虑人机工程学 工作方法不统一 生产批量太大
2S: Simplifying– 整顿 关键在于建立规则堵住混乱出错的根源:
1.控制现场物品数量
2.定置管理 3.标准化管理 4.可视化管理 5.确立改善点/问题
―五定”管理 定置/定人/定时/定量/定区(岗)
定置:从人、物、场所相互关系的内在联系上找解决生产现场 各工序存在问题的方法。 定人:确定管理责任人和管理责任区 定时:给责任人充分的时间去执行(3次/天) 定量:任何库存有最大最小量,行动有数量规定.
精益
保护最大财富,保持流畅生产
八种浪费--Downtime
Defect Over-production Waiting Non-utilized resource Transportation Inventory Motion Extra Processing
八种浪费—纠正错误
• 定义:对产品进行检查,返工等补救措施 • 表现
3S: Sweeping - 清扫
• 在必要时立刻清扫和拖洗工作区 域,清理产生的杂物 • 发现、纠正: – 错误的位置; – 不正确的库存; – 不受控的缺损; – 不安全的隐患; – 不正常的设备; – 不齐全、合适的工具器具等; – 不按计划数量生产.
Implementation Guide
The 5S is not a passing rule. It is a lifestyle. 5S不是暂时规则,而应 化为日常的生活方式
2S.Simplifying Access:
make stipulations 整顿:做规定
Each item has its own position. Each Operation has its standard and specifications. 每样资源有各自的位 置,每个操作都有标 准和规范
Eliminate Waste
4S. Standardization:
reinforce the previous success and make improvements 清洁:巩固已有成就和改 善(重新标准化)
消除浪费
3S.Sweeping:
execute the rules 清扫:执行规定
工具箱
T R A S H
TOOLS
T O W E L S
G L O V E S
3S: Swee和标准 精益
节省时间、 避免出错、 消除烦躁情绪和无限制变差
Two-point Inspection
I checked it, but let me know if there are any problems.
• 定义:有消耗/支出,但没有完全发挥作用 • 表现
– – – – – – – – – 使用但作用不大 不使用也没关系 可以发挥的作用但没有发挥 较有价值但闲置或无用武之地 设计/配置不合理 无计划采购 状况改变后无用 错误的采购或招聘 没有正确使用
• 起因
消除浪费的四步骤
第一步:
了解什么是浪费
第二步:
– – – – – – – – – – 需要额外的进货区域 停滞不前的物料流动 发现问题后需要进行大量返工 需要额外资源进行物料搬运(人员、场地、货架、车辆等) 对客户需求的变化不能及时反应 生产能力不稳定 不必要的停机 生产换型时间长 生产计划不协调 市场调查不准确
• 起因
八种浪费—过量加工
• 定义:又叫“过分加工的浪费”,一是指多余的加工;另 一方 • 表现
– 额外的时间和人工进行检查,返工等工作 – 由此而引起的无法准时交货 – 企业的运作是补救式的,而预防式的
• 起因
– 生产系统不稳定 – 过度依靠人力来发现错误 – 员工缺乏培训
八种浪费—纠正错误
错误的结果
– 源头 – 生产线尽头 – 码头 – 顾客 1元 10元 100元 1000元
八种浪费—过量生产
5S: Self-Discipline –修养
• 员工自律; • 员工具有改善技巧; • 员工具有识别浪费的能力和强 烈改善意识; • 公司自动持续改进; • 改进不断产生效益;
精益
消除大量浪费,达到准精益
6S: Safety – 安全
• 安全第一; • 员工具有安全意识; • 员工具有识别危险的能力和强 烈改善意识; • 公司有完善的安全管理机制; • 公司有安全防范的手段;
2S: Simplifying – 整顿
整洁!有序!便于存取! 一目了然! 诀窍在于-----
• 建立划线、涂色、作标记等可视控制
• 颜色代码的规定
• 创造条件将物品整齐有序地安放好
……
3S: Sweeping - 清扫 所有操作都 遵循 指定的 批准的 规范和标准 精益
节省时间、 避免出错、 消除烦躁情绪和无限制变差
4S: Standardization–清洁
4S的改善流程:
• • • •
O/P K S C
(Observation/Problem) 观察/出现的问题 (Kaizen)改善 (Standardization)重新标准化 (Continuous Improvement)循环改进
精益
减少变差范围--降低废品、节约时间、消除过程浪费
材料、零件的过早消耗 难以判断什么时间什 托盘、物料箱的占用 么地方会发生问题 铲车、物料车的占用
为什么会过量生产
对开工率的错误认识 停线是不可以的错误想法 可以对付设备故障,不良品,缺勤等问题 对付生产负荷的不均衡 生产组织不合理,非单件流
掩 盖 了 应 暴 露 解 决 的 问 题
0
成本
价格
精益组织
精益6S现场管理
1S.Sorting:
整理 :
Categorize and clear up useless resources 区分并清除不 用和 没 用的资源
6S. Safety
安全
Safety is first . 安全第一
5S. Self-Discipline/
Culture: cultivate a manner 修养:习惯
Full Involvement 让每个员工积极参 与
Facilitate and advance standardization with an aim to ensure and supervise the achievement of the first 3S 推进改善和标准化,保证、监 督前3S的完成。
Clear up at any time. All resources are in the stipulated places. All the operations follow their standard and specifications. 随时清洁而且—资源都处在批准和指定的地方, 所有操作都遵循标准和规范
精益5S及8种浪费
内部培训教材
Agenda
• 什么是精益
• 精益5S
• 8大浪费
• 消除8大浪费的方法
精益是什么?
精益
Lean
瘦,没有多 余的赘肉
消除一切浪费
价格 -利润 -成本的方程式
过去、垄断
利润
成本
价格
批量产品
0
土地、人工、货币、原材料、水电煤
现在
客户和竞争
批量产品
利润
0
成本
价格
将来
利润
工序步骤, 工作要素, 库存……可以组合 在一起吗? 工序步骤, 设备, 工作方法, 信息流……可 以被减少吗? 工序步骤, 设备, 工作方法, 信息流……可 以被跟方便的东西取代吗? 工序步骤, 设备, 工作方法, 信息流…… 的次序可以更换吗?
Error Proofing
Jig
The part won’t go on unless it’s oriented properly
I’ll check it out before I do the next operation. jamming pin
CONTROL
WARNING The light goes on if the machine fails.
1S: Sorting –整理
把要和不要的分 开,处理不要资 源,留下要的。
精益 节省空间、较合理使 用资源,初步控制库存
2S: Simplifying– 整顿
简单、清晰、可操作、防错 物料色卡 零件号 最多需要数量 库址
所有资源都有 指定的 批准的 位置 有量化规定
锤子在这里!
精益
工具箱
节省时间、 避免出错、 消除烦躁情绪
八种浪费—无聊的搬运
• 定义:对物料的任何移动 • 表现
– – – – – – – – – – 需要额外的运输工具 需要额外的储存场所 需要额外的搬运人员 大量的盘点工作 产品在搬运中损坏 生产计划没有均衡化 生产换型时间长 工作场地缺乏组织 场地规划不合理 物料计划不合理
• 起因