MRB作业流程
MRB作业办法

5.1特采处置方式
5.1.1会议决定通过对物料进行特采时。
5.1.2IQC对特采物料贴上特采物料标签,并在标签上注明特采原因,及使用条件。并发出《材
料不良通知单》给供应商分析改善。
5.1.3货仓在发特采物料给给生产时,必须在发料单上写明原因,使用条件。
5.1.4生产在领用特采物料上线时,必须通知工程和品管并依据工程的特采物料加工规范进行
加工。
5.1.5品管IPQC对特采物料上线需作特别追踪,一旦发生不良或异常,即通知停线,以免造成报废。
5.2返工处理方式
5.2.1会议决定通过对物料进行返工时。
5.2.2在第一时间通知供应商过来返工,若供应商未到我司处理,则由我司人员进行挑选,按14元/小时的单价,向供应商扣除返工工时费用。
5.2.3由IQC发出《材料不良通知单》要求供应商分析改善。
1.0目的
界定不良或可疑问题物料的处理方式,以免误用,造成品质问Байду номын сангаас。
2.0范围
适用于物料不良而无法判定处理方式。
3.0定义
MRB:(Material Review Board)物料评审委员会。
4.0权责
4.1成员构成:IQC+PMC+工程+采购
4.1.1IQC:将REJ之物料检验单立即交PMC并立即发出CAR。
4.1.2PMC:
a.填上材料上线日期。
b.依据材料紧急程度,决定是否召开MRB会议。如果是,则通知相关人员开会;如果不是,则将单据退还IQC,由IQC办理退货事宜。
4.1.3工程:做相关之实验,以作为WAIVE(特采)或其它决定依据。
4.1.4参与讨论执行MRB之结论(如向厂商扣款及要求及时补货等)。
MRB作业流程范文

MRB作业流程范文MRB(Material Review Board)是一种用于处理非符合性材料的流程,旨在确保公司的产品质量和安全性。
本文将详细介绍MRB作业流程,包括定义、流程步骤、成员职责和案例分析等内容。
一、定义MRB是一种用于处理供应商提供的非符合产品或公司内部制造的非合格产品的流程。
当发现产品不符合规格要求,或者供应商提供的原材料没有达到公司的质量标准时,就需要通过MRB流程进行处理。
MRB流程对于确保公司产品质量和安全性具有重要意义。
二、流程步骤1.收集信息:当发现非符合材料或产品时,必须及时收集相关信息,包括产品规格、质量标准、供应商信息等。
2.建立MRB小组:根据非符合材料的类型和严重程度,建立相应的MRB小组。
通常,MRB小组由质量经理、工艺工程师、供应商负责人等组成。
3.审查非合格材料/产品:MRB小组对非合格材料/产品进行审查,确定非合格的原因和严重程度。
审查过程中,可能需要对材料/产品进行测试、测量和分析等。
4.制定纠正措施:根据审查结果,制定相应的纠正措施。
这些措施可能包括修复、更换供应商、修改工艺流程等。
5.执行纠正措施:对于纠正措施,MRB小组负责执行,并确保纠正措施的有效性和可行性。
6.监控纠正措施:MRB小组需要监控纠正措施的实施过程,并定期评估其有效性。
如发现纠正措施无效,需要重新制定并执行新的纠正措施。
7.记录和报告:整个MRB流程的过程和结果都需要进行记录和报告,以供以后参考和审查。
三、成员职责1.质量经理:负责监督和协调整个MRB流程的执行,确保纠正措施的正确性和有效性。
2.工艺工程师:负责对非合格材料/产品进行技术分析,确定非合格的原因,并提供建议和支持纠正措施的制定和实施。
4.质量控制员:负责执行纠正措施,并监控其有效性。
同时,确保符合产品能够满足公司的质量要求。
四、案例分析公司在生产过程中发现原材料不符合公司的质量标准,需要进行MRB处理。
1.收集信息:收集有关原材料、供应商和质量标准的相关信息。
MRB作业指引

MRB作业指引1.0目的:严格控制资源浪费,规范MRB作业流程。
2.0范围:适用於PCB半成品及成品。
3.0使用工具:8倍镜修理刀黑色油性不脱色笔卡尺4.0作业流程:NG5.0作业步骤及内容:5.1 制程不良板需MRB确认的,须先由各工序责任人确认之后,方可於MRB确认,且有待MRB确认之型号及数量。
5.2 对客户退货板需MRB确认的,MRB作业按《顾客抱怨与投诉处理程序》7.0执行。
5.3 MRB审查员收到制程待打报废之板,应先认真核对型号及数量,确认无误后按质量检验规范《制程检验规范》和《成品检验规范》进行全检审查。
6.0审请报废板由MRB审查后,作以下两种方式处理:6.1 修理:PCB可以通过修理来达到或满足客户收货要求的,则退回相关部门修理。
6.2 报废:不能修理之板作报废处理且有相关部门主管或以上职级批准后方能生效。
7.0 报废品处理:7.1 制程半成品/成品单只打“X”仍可以收货的,需用黑色油性不脱色笔在PCB 正反两面打上“X”标记,如有客户要求,则按客户要求选择报废标记。
7.2 MRB审查员审查完之后,需将报废板之型号、工序、数量、及缺陷记入《物料异常报告单》中,报废板暂用红色(不良品)胶框存放,待相关工序查核后,按加工类型分类送至废品仓。
8.0 注意事项:8.1 MRB审查员对不能判定报废之板,须及时向直属上司反映,切忌自作主张。
8.2严格控制报废板,杜绝报废板再次外流。
8.3 品质审查标准:如客户没有要求,按本厂质量检验规范《制程检验规范》和《成品检验规范》或者IPC—A—600F进行检验、收货。
如有客户标准,则按客户标准进行检验、收货。
8.4凡是从事MRB作业活动,需由组长级或以上职级人员担任执行,其他任何人员无权从事MRB作业活动。
(特殊情况可以指定人员担任)8.5 MRB审查员有义务接受相关部门之监督。
9.0 参考文件:1.IPC—A—600F2.《制程检验规范》《成品检验规范》3.《客户投诉与退货处理程序》4.《物料异常报告单》。
MRB作业规范(WH-WI-076)

5.3.2.2當處理方式為特采時按【檢驗與不合格管制程序】提出申請。
5.3.2.3若為成品不符合客戶規格值特采時,可由業務或品管直接聯絡客戶,向客戶提出讓步申請,當客戶同意及書面通知後方可特別採用。
5.5 MRB執行與檢查:
5.5.1相管部對各部門MRB處理的方案執行情況進行檢查,若有不符合按【糾正預防管制程序】進行處理。
5.6 MRB記錄:
5.6.1MRB會議時由品管部記錄MRB處理的最終方案。
5.6.2記錄的保存依【品質記錄管制程序】進行處理。
5.2.2.3如有需要可要求其他相關單位參加,參加人員為核簽處理意見。
5.3 MRB處理決定:
MRB處理分為挑選、重工、報廢及特采四種方式。
5.3.1挑選/重工:
5.3.1.1條件:是指對不合格批量不可採用不良品進行挑選或加工後,將良品投入生產使用狀況,不良品按【檢驗與不合格管制程序】處理。
5.3.1.2若為來料需要內部進行挑選或重工時,由採購向供應商提出相應的扣款。
5.1.1.4公司高層認為有必要時.
5.2 MRB提出準備:
5.2.1當需要進行MRB評審時,由提出部門根據緊急程度判定是否召開MRB會
議或會簽形式,如需舉行會議由提出部門通知MRB小組人員的會議時間
﹑地點﹑會議事項等。
5.2.2MRB小組組成:
5.2.2.1材料MRB:製造,品管,生管,採購。
5.2.2.2(半)成品MRB:製造,品管,生管,業務。
7.0使用表單:
無
8.0附件:
8.1附件一:MRB作業流程
MRB作业指导书 -

MRB作业指导书 -引言概述:MRB(Material Review Board)作业指导书是一份重要的文档,用于指导MRB 团队在产品质量问题浮现时的处理流程。
本文将从五个大点出发,详细阐述MRB 作业指导书的内容和重要性。
正文内容:1. MRB作业指导书的概述1.1 MRB作业指导书的定义和目的1.2 MRB作业指导书的适合范围和使用对象1.3 MRB作业指导书的重要性和作用2. MRB作业指导书的组成部份2.1 问题描述和分类2.2 MRB团队的组成和职责2.3 问题解决流程和决策制定2.4 数据分析和记录2.5 问题解决方案的评估和验证3. MRB作业指导书的具体步骤3.1 问题发现和报告3.2 MRB团队的召集和会议3.3 问题分析和数据采集3.4 解决方案的制定和评估3.5 解决方案的实施和验证4. MRB作业指导书的注意事项4.1 保持信息的准确性和及时性4.2 持续改进和更新指导书4.3 建立有效的沟通和合作机制4.4 遵守相关法规和标准5. MRB作业指导书的效益和应用案例5.1 优化问题解决流程,提高效率5.2 提高产品质量和客户满意度5.3 降低成本和风险总结:MRB作业指导书是一份重要的文档,它指导MRB团队在产品质量问题浮现时的处理流程。
本文从概述、组成部份、具体步骤、注意事项和效益等方面详细阐述了MRB作业指导书的内容和重要性。
通过合理使用MRB作业指导书,企业可以提高问题解决效率,优化产品质量,降低成本和风险,从而提升竞争力和客户满意度。
因此,建议企业建立和完善MRB作业指导书,并持续改进和更新,以适应不断变化的市场需求和质量管理要求。
MRB流程
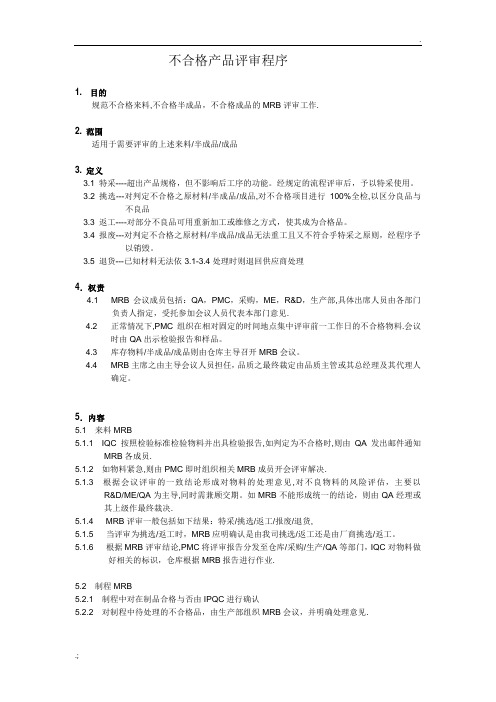
不合格产品评审程序1. 目的规范不合格来料,不合格半成品,不合格成品的MRB评审工作.2. 范围适用于需要评审的上述来料/半成品/成品3. 定义3.1 特采----超出产品规格,但不影响后工序的功能。
经规定的流程评审后,予以特采使用。
3.2 挑选---对判定不合格之原材料/半成品/成品,对不合格项目进行100%全检,以区分良品与不良品3.3 返工----对部分不良品可用重新加工或维修之方式,使其成为合格品。
3.4 报废---对判定不合格之原材料/半成品/成品无法重工且又不符合乎特采之原则,经程序予以销毁。
3.5 退货---已知材料无法依3.1-3.4处理时则退回供应商处理4.权责4.1 MRB会议成员包括:QA,PMC,采购,ME,R&D,生产部,具体出席人员由各部门负责人指定,受托参加会议人员代表本部门意见.4.2 正常情况下,PMC组织在相对固定的时间地点集中评审前一工作日的不合格物料.会议时由QA出示检验报告和样品。
4.3 库存物料/半成品/成品则由仓库主导召开MRB会议。
4.4 MRB主席之由主导会议人员担任,品质之最终裁定由品质主管或其总经理及其代理人确定。
5.内容5.1 来料MRB5.1.1 IQC按照检验标准检验物料并出具检验报告,如判定为不合格时,则由QA发出邮件通知MRB各成员.5.1.2 如物料紧急,则由PMC即时组织相关MRB成员开会评审解决.5.1.3 根据会议评审的一致结论形成对物料的处理意见,对不良物料的风险评估,主要以R&D/ME/QA为主导,同时需兼顾交期。
如MRB不能形成统一的结论,则由QA经理或其上级作最终裁决.5.1.4 MRB评审一般包括如下结果:特采/挑选/返工/报废/退货,5.1.5 当评审为挑选/返工时,MRB应明确认是由我司挑选/返工还是由厂商挑选/返工。
5.1.6 根据MRB评审结论,PMC将评审报告分发至仓库/采购/生产/QA等部门,IQC对物料做好相关的标识,仓库根据MRB报告进行作业.5.2 制程MRB5.2.1 制程中对在制品合格与否由IPQC进行确认5.2.2 对制程中待处理的不合格品,由生产部组织MRB会议,并明确处理意见.5.3 库存品MRB5.3.1 仓库定期对库存品进行清点并送检,由QA部依据相关检验标准进行检验,如检验不合格,由出具不合格检验报告。
mrb流程
mrb流程MRB(Material Review Board)流程是一种流程管理方法,用于处理产品制造过程中出现的不合格品,确保产品符合质量标准。
下面将介绍MRB流程的具体步骤。
首先,在产品制造过程中,若发现有不合格品,责任人员应及时将其报告给质量管理部门。
质量管理部门将组成MRB小组,由质量工程师、制造工程师、供应商负责人等组成。
接下来,MRB小组将收集相关的不合格品信息,包括不合格品数量、类型、原因等,并对其进行分类。
这样可以帮助找出引起不合格品的根本原因,进而采取相应的措施。
然后,MRB小组将对不合格品进行分析和评估。
他们会评估不合格品对产品质量和客户满意度的影响,以及可能存在的安全隐患。
同时,他们也会分析不合格品的原因,包括制造过程、供应链质量等方面的问题。
在完成分析和评估后,MRB小组将制定相应的纠正措施和预防措施。
纠正措施主要是针对当前不合格品的问题进行处理和修复,确保产品符合质量要求。
预防措施则是为了避免类似问题再次出现,可以通过调整制造过程、优化供应链质量等方式来提升产品质量。
接下来,MRB小组会与相关部门进行沟通,并制定实施方案。
他们会与制造部门、采购部门等进行协调,以确保纠正措施和预防措施能够得到有效实施。
一旦实施方案得到批准,MRB小组将对其进行跟踪和监控。
他们会进行定期的检查和评估,确保纠正措施和预防措施的有效性。
如果发现问题依然存在,他们会及时调整方案,以保证产品质量满足要求。
最后,MRB小组会对整个MRB流程进行总结和汇报。
他们会记录整个处理过程中的问题、纠正措施和预防措施的有效性,并将其汇报给相关部门和管理层。
通过汇报,可以促使企业持续改进,并减少类似问题的发生。
总的来说,MRB流程的目的是确保产品质量符合要求,提升客户满意度。
通过对不合格品的分析、评估和处理,可以找出引起问题的根本原因,并采取相应的措施,从而提升产品质量和企业绩效。
MRB流程是一个有效的管理工具,可以帮助企业提高制造过程的稳定性和可靠性。
MRB作业流程范文
MRB作业流程范文MRB(Materials Review Board)作为一个重要的制造工艺控制手段,对于产品制造过程中的原材料选择和使用具有关键性的作用。
本文将详细介绍MRB的工作流程。
一、MRB作业流程概述1.问题发现:问题可以由多个渠道发现,如质量抽样检测、自行发现等。
问题发现可以包括产品不合格、零部件损坏、制造过程中的异常等。
2.问题报告:问题被发现后,需要将问题报告提交给MRB团队。
问题报告应包括问题的详细描述、触发问题的原因和发现问题的具体位置等信息。
3.问题分析:MRB团队负责对问题进行详细的分析。
分析包括原材料的制造工艺、生产过程中的工艺参数、设计规范和质量要求等方面。
4.问题解决:根据问题分析结果,MRB团队将提出相应的解决方案。
解决方案可以包括原材料的更换、制造工艺的调整、生产工艺参数的变更等。
5.问题关闭:经过一段时间的实践验证,如果解决方案有效并得到确认,MRB团队将关闭该问题。
如果问题仍存在或解决方案不可行,则需要重新进入问题解决流程。
二、MRB作业流程详细解析1.问题发现问题发现可分为内部发现和外部发现两种情况。
内部发现:公司内部通过生产质量抽样检测、过程异常统计等方式发现问题。
外部发现:供应商、客户或第三方检测机构通过检测报告、客户投诉等方式发现问题。
2.问题报告问题报告需要包括以下内容:问题描述:清楚描述问题的性质、影响范围和可能的原因。
问题位置:指出问题所在的部件、工序、供应商等。
影响程度:描述问题对产品质量和制造周期的影响,以及可能引起的额外成本。
3.问题分析问题分析是MRB的核心环节,对问题进行深入分析,为解决方案的制订提供依据。
总体分析:全面了解问题的性质、影响范围,并确定解决问题的必要性。
根本原因分析:通过追溯问题发生的根本原因,如质量不合格的原因、工艺参数设置错误等。
影响评估:对问题的影响范围、可能引起的成本和时间延误进行评估。
4.问题解决问题解决是MRB的目标,需要提出解决方案并实施。
MRB作业指导书-
MRB作业指导书-1.0 目的: 通过规范的MRB作业流程使不合格品得到妥善处理,并且避免不合格的再发生。
2.0适用范围: 适用于本公司发现的不合格品的评审。
3.0 职责3.1.品保部监督责任单位对MRB的正确填写;负责整个公司所有零件MRB信息的统计、分析、改善追踪。
3.2各责任部门负责正确填写MRB单信息。
3.3生产部负责确定返工或返修工时和方案。
4.0定义MRB:材料审查会议;针对所有检验工作站发现产品异样状态,暂时不能确定是否为何缺陷的一种处理办法(包括进料检验,过程检验,成品/出货检验及客户退回的产品)。
5.0作业指导流程5.1 不合格品发现时机5.1.1进料检验中发现的不合格品5.1.2 生产过程中发现的不合格品5.1.3 成品/出货检验中发现的不合格品5.1.4 客户拒收的不合格品5.2不合格品处置5.2.1标识5.2.1.1发现不合格品的人员应按《标识和可追溯性控制程序》的规定,在不良品上用黄色标签做好待处理标识,黄色标签上写清楚项目名称、零件号、数量、不良现象、作业者等信息。
当不良问题集中在物品的某一点或某一区域时(如外观有瑕疵…),则还应使用箭头标示使不良点明显化。
5.2.1.2客户拒收物料在进行MRB评审后必须破坏原有合格证,防止不合格品误当合格品使用。
5.2.2 隔离发现人员在做好标识后,立即将不合格品隔离到工序内指定的不合格品区域中。
5.2.3填写MRB单5.2.3.1 MRB单填写要求:a. 进货检验、生产现场操作人员发现时,通知检验员,由检验员领取并填写MRB单。
b.仓库收到客户退货时,应该核对所有退货实物和清单上的零件号、数量是否一致,并按照合格品要求在客退品区域摆放整齐,不允许磕碰、撞伤;核对正确后通知品保部相关人员并由其领取并填写MRB单。
c.仓库呆滞品需要处理时,由仓库人员领取并填写MRB单。
d. 其它情况MRB单的填写视实际情况,由品保部确认MRB单的填写方式。
不良品仓作业流程
1.MRB流程及相关单据一:IQC判定原物料不良,但尚未最终判定,仍需做进一步测试及判定之后方能确定我方或者厂商做报废处理的物料,即入MRB(24)库位.二:由IQC打印出该物料MRB单据(一式两联),并以邮件的方式通知不良品仓负责人,同时将该物料的系统帐入(24)库位.三:不良品仓负责人收到邮件之后,需尽快核对数量后在单据上签字, 需确认物料上必须有IQC所贴的不良品标签(黄色标签),并将该物料及对应单据拿至不良品仓保管,等待相关部门人员处理.(需注意:物料与对应单据必须同时进出,直至该物料处理结束. 当该物料最终处理结束后,将单据交由文员处留存).2.RTV流程及相关单据此RTV流程要分两种状况进行操作.第一种状况就是原材料来料时被IQC检验出的批量次的不良,此种状况按以下流程进行作业: 一: IQC判定原物料不良,需退回原厂商返工或者报废的物料,即入RTV(25)库位.二:由IQC打印出该物料RTV单据(一式两联),并以邮件的方式通知不良品仓负责人,同时将该物料的系统帐入RTV(25)库位.三:不良品仓负责人收到邮件之后,需尽快核对数量后在单据上签字, 需确认物料上必须有IQC所贴的不良品标签(红色标签),并将该物料及对应单据拿至不良品仓保管,等待相关部门人员处理.需注意:物料与对应单据必须同时进出,直至该物料处理结束.当该物料最终处理结束后,将单据交由文员处保管.第二种状况就是生产线作业人员在生产过程中所发现的不良品, 此种状况按以下流程进行作业: 一:生产线将发现的不良品累积退回产线物料组,由物料人员拿至IQC处确认,经IQC确认后,确定为原材料不良,也就是能够认定为原厂商责任的物料,将其打入RTV(21)库位,并在物料上加贴不良品标签(红色标签).二:由物料组负责退料的人员将这些物料整理出准确的清单之后,退至不良品仓.三:不良品仓负责人在接收退料人员所退物料时,应与其一起将物料点清.需要注意:(1).在清单上必须附有一份一式三联的原材料退料单.(2).在原材料退料单上必须有生产主管以及退料员的签字.(3).在退料清单上必须有IQC确认人员的签名.(4).每颗料的最小包装上必须有IQC所贴的不良标签(红色标签).四:不良品仓负责人确认数量无误后,在原材料退料单上签字确认,并将物料放至规定宾位,方便相关部门人员的处理.最后将单据的第一联给文员做帐,将数据做入系统.第二联由不良品仓留存,第三联有物料组留存.3.SCRAP流程及相关单据一:生产线作业员在操作的过程中,所造成的物料不良,经产线QC确认之后,退至物料组,由物料员退至不良品仓进行报废.二:物料员整理出清单,携物料至不良品仓退料,不良品仓负责人在接收退料人员所退物料时,应与其将物料当面点清.需要注意:(1). 在清单上必须附有一份一式三联的原材料退料单.(2).在原材料退料单上必须有生产主管以及退料员的签字.(3).在退料清单上必须有产线QC和生产部经理的签名.三:不良品仓负责人确认数量无误后,在原材料退料单上签字确认,并将物料放至规定箱子,方便相关部门人员的处理.然后将单据的第一联给文员做帐,将数据做入系统.第二联由不良品仓留存,第三联有物料组留存.(需要注意:报废物料在退料时应区分保税与非保税,在摆放时也要做严格区分).4.换货流程及相关单据一:由采购通知产商将不良品换回二:采购及时通知不良品仓负责人,告知换货的时间和换货的数量,并开好出厂放行单三:不良品仓负责人及时将货物准备好,并到采购处拿取出厂放行单四:厂商过来换货时,与其当面将数量点清,同等数量交换.并让换货人在出厂放行单上签名及记录车牌号码.同时保安也需确认所换物料的数量,并签名.五:将换好的良品放置于仓库待检区,由不良品仓负责人开出规定使用的换货单据(一式两联),将换货单交于IQC待验.(并在自制的表格中做记录,防止一旦单据丢失无法追查.)六:IQC根据换货单将货物验完之后,在换货单上签名并通知不良品仓负责人.由不良品仓负责人将物料与换货单同时交给良品仓,由仓管员确认数量无误后,签名后接收,再放入规定宾位(.注意:,若出现所换物料再次不良,那不良品仓负责人需将换货单与货物一起拿回不良品仓,等待采购处理). 七:由不良品仓负责人将换货单第一联交给文员做帐,将不良品库位帐转入良品库位.第二联由不良品仓负责人留存.5.特采流程及相关单据一:经IQC与相关部门人员共同确认,原先不良的物料可以接收使用,由IQC以邮件或者电话的方式通知不良品仓.二:不良品仓负责人接到IQC的通知,应尽快开出规定使用的特采单据(一式两联),要求IQC相关人员在特采单据上签名.同时将货物与单据一起交给良品仓.三:良品仓的仓库管理员在拿到特采单据和货物时,必须与不良品仓负责人一起将货物数量点清,方可在单据上签名,并将货物入库.四:特采单据第一联交于文员做帐,将不良品仓系统库存转入良品仓库位,且此联由文员留存.第二联由不良品仓留存.6.RMA流程及相关单据此RMA流程分三种状况进行操作.第一种状况是通力(KONE)反馈一:收货区收料员收到通力反馈的货物,必须在外盒上标示到货日期,并且签名.然后将货物放置在规定区域.二:不良品仓负责人定时到固定区域取出反馈回来的货物(注:需在每周五之前取出,并处理结束),并至文员处拿来相应的反馈单(一式三联).三:不良品仓负责人根据货物中附带单据上的反馈单号,一一将相对应反馈单找出并做仔细核对,确认无误后在反馈单上签上名字,收货日期,以及实收数量.四:然后将货物与签完字的反馈单对应放入同一包装袋,并且在包装袋上写上收货日期和反馈单号后放到规定区域.五:通知CQC对反馈货物进行判定,并测试.六:CQC判定结束后,将反馈货物重入不良品仓, 不良品仓负责人要与其核对数量,并在反馈单上签上名字,入库日期,及所入库位.(注意:这时如果判定是客户责任的要入RMA(26)库位,如果是厂商责任的要入RTV(25)库位).七:最后将反馈单的第一联给文员做帐,此联文员留存.第二联由CQC留存.第三联由采购留存.第二种状况是 EINI反馈一:收货员收到反馈货物后通知不良品仓负责人二: 不良品仓负责人拿到货物后,先到文员处将对应的反馈单(一式两联)找出,核对序列号无误后在反馈单上签上名字,收货日期,及实收数量.并将货物放置于规定区域,等待处理,且通知CQC.(注意:此机种版本类型比较多,不同的版本应分区域放置,不可混放.)三: 最后将反馈单的第一联给文员做帐,此联文员留存.第二联由CQC留存.第三种状况是产线各机种的不良反馈一:销售提前通知并开出货物反馈清单(一式两联)二: 收货员收到反馈货物后通知不良品仓负责人三: 不良品仓负责人拿到货物后,将货物与销售开出的反馈清单进行核对,若核对数据无误,就在反馈单上签上名字,接收日期,及实收数量.若核对数据有误,立即通知负责此机种的销售员,做进一步核实.四: 最后将反馈单的第一联给文员做帐,此联文员留存.并通知CQC处理. 第二联由CQC留存.*注: RTV------R21,SZ21,R25,SZ25MRB------R24,SZ24RMA------SZ26SCRAP------SRP1, SRP2。
- 1、下载文档前请自行甄别文档内容的完整性,平台不提供额外的编辑、内容补充、找答案等附加服务。
- 2、"仅部分预览"的文档,不可在线预览部分如存在完整性等问题,可反馈申请退款(可完整预览的文档不适用该条件!)。
- 3、如文档侵犯您的权益,请联系客服反馈,我们会尽快为您处理(人工客服工作时间:9:00-18:30)。
MRB作业流程(同特采流程)
1.0 目的
1.1建立不良品信息沟通及处理平台,及时处理不良品,加强品质管控;
1.2快速合理的进行品质缺陷判定,明确品质责任承担;
2.0范围
2.1 本文件适用于生产急用但与品质标准存在差异,需承担客诉风险之物料,且制造加工单位(含供应商)自身无法处理的物料管理,包括下述内容:
2.1.1进料类【外协加工/采购物料经检验判退物料】;
2.1.2制程在途类【制程加工在途物料/半成品及配件经检验判退物料】;
2.1.3仓储类【仓储半成品及配件等物料经检验判退物料】;
3.0 权责
3.1 MRB小组组长:判定不合格物料处理结果以及责任承担单位;
3.2 MRB小组成员:参与不合格物料评估并执行MRB决议,明确品质异常经济责任承担;
4.0 具体内容
4.1 MRB小组成员界定
4.1.1 MRB小组组长—品质部经理;
4.1.2 MRB小组成员—生产部、计划部、采购部、技术部、销售部(相关业务员);
4.1.3必要时将临时邀请相关人员;
4.2物料异常产生及MRB提出
4.2.1公司所有外协加工/采购物料由品质部IQC人员予以检验,如发现来料与品质标准存在差异,但属于生产急用之物料,由采购科/计划科填写《紧急放行单》,品质部召集召开MRB会议;
4.2.2制程在途与仓储异常物料,本车间无法修补的,由车间填写《产品质量异常信息反馈单》反馈至品质部,由品质部判定是否召集召开MRB会议;
4.3 MRB评估
4.3.1计划科:提供客户交期、计划编制、出货排程及补单安排;
4.3.2 生产部:提供异常物料所造成进度影响,明确执行单位能否协助代加工/挑选,并承诺完成时间;
4.3.3 技术部:评估异常物料能否正常使用,并提供技术支持;
4.3.4 采购科:供应商信息沟通,供应商生产状况及供应商之回复,明确MRB产生费用归属,回复供应商返工之完成时间并办理退货、补货手续;
4.3.5 业务部:客户沟通及确认;
4.3.6 品质部:明确异常物料品质影响程度,判定结果【特采/返工/代加工/挑选/
退货/正常使用】,判定责任承担单位并跟进MRB执行结果确认;
4.3.7责任承担按《品质异常经济责任承担管理办法》实施;
4.4 MRB评估决议及决议执行
4.4.1 MRB评估内容须达成决议【特采/返工/代加工/挑选/退货/正常使用】并由品质部以《MRB评审记录表》记录存档,并通过公司邮箱传递相关部门;
4.4.2 MRB小组成员须在《MRB评审记录表》签名确认;
4.4.3 属生产部协助供应商代加工/挑选,则由生产部记录耗损的成本【工时/材料】,并填写《返修耗时/耗料记录表》上报采购科/财务部门;
4.4.4 属品质部MRB全检执行挑选或代加工的(包括本厂制程产生的不良),由品质部负责将MRB产生费用及责任进行划分,并填写《返修耗时/耗料记录表》上报采购科/财务部,财务部执行扣款;
4.5 MRB执行结果监督及确认
4.5.1 品质部对MRB决议执行之结果予以监督,并判定是否符合要求;
4.6 MRB全检组成人员
4.6.1品质部品检科下属检验人员为主要实施人员;
4.6.2 生产执行车间属MRB临时实施人员;
4.7 实施
4.7.1《MRB作业管理办法》自颁发日起实施;
5.0 附件
5.1《产品质量异常信息反馈单》;
5.2《MRB评审记录表》;
5.3《返修耗时/耗料记录表》;
5.4《紧急放行单》;
5.5《品质异常经济责任承担管理办法》;
MRB的全称是Material Review Board, 中文意思是材料审查会议,它是针对所有检
验工作站发现产品异样状态暂时不能确定是否为缺陷的一种处理办法。
MRB包括进料检验,过程检验,出货检验以及客户退回的产品。
根据不确定缺陷发现的位置,MRB会议可由不同的人召集。
如在进料检验过程中发现原材料有异常,当进料检验工程师不能确定时,他可召集MRB会议。
MRB可邀请项目经理,采购工程师,过程控制工程师,计划参加,如有必要可以邀请质量经理和生产经理加入以加速问题的解决。
通过MRB会议一般可得出下列结论:1.继续使用; 2.需要返工后使用; 3. 报废; 4.退回供应商要求换货。
MRB能使相关的人在第一时间知道问题的存在,并且能加快问题的解决。