无菌制剂车间
无菌灌装车间的要求

无菌灌装车间的要求一、引言无菌灌装车间是生物制药企业生产无菌制剂的重要环节,其要求严格的无菌操作和环境控制,以确保产品的安全性和质量。
本文将详细介绍无菌灌装车间的要求,包括无菌操作流程、环境控制、设备要求和人员培训等方面。
二、无菌操作流程1. 无菌操作前的准备在进入无菌灌装车间之前,操作人员应进行严格的洗手和穿戴无菌衣物,包括洗手液、手套、面罩、帽子和无菌服等。
同时,应对无菌操作区域进行消毒处理,确保无菌环境。
2. 灌装操作(1)灌装设备的选择和验证无菌灌装车间应配备符合GMP要求的灌装设备,包括注射器灌装机、封口机和贴标机等。
这些设备应经过验证,确保其能够满足无菌操作的要求。
(2)灌装过程的无菌操作操作人员应在无菌操作台上进行灌装操作,操作过程中应注意避免污染。
灌装液体应经过高温灭菌或过滤处理,以确保无菌状态。
同时,操作人员应定期更换手套、面罩和无菌服,避免交叉污染。
(3)灌装后的处理灌装完成后,灌装产品应立即进行封口和贴标操作。
封口过程应保证封口的完整性和无菌性,贴标过程应确保标签的准确性和粘贴牢固。
三、环境控制1. 空气质量控制无菌灌装车间应配备高效过滤器,过滤空气中的微粒和微生物,使车间内的空气满足GMP要求。
同时,应定期检测车间内的空气质量,确保其符合相关标准。
2. 温湿度控制无菌灌装车间的温度和湿度应保持在合适的范围内,以确保产品的稳定性和质量。
温湿度控制设备应具备自动调节和报警功能,以及备用设备,以防止突发情况影响生产。
3. 无菌操作区域的清洁和消毒无菌操作区域应定期进行清洁和消毒,以防止细菌和其他微生物的滋生。
清洁和消毒操作应符合GMP要求,并有相应的记录和验证。
四、设备要求1. 灌装设备的材质和设计无菌灌装车间的灌装设备应采用不锈钢材质,具备良好的耐腐蚀性和易清洁性。
设备的设计应符合GMP要求,便于操作和维护。
2. 过滤器的选择和更换无菌灌装车间的过滤器应选择合适的类型和规格,以满足空气质量的要求。
制剂车间防火防爆说明

制剂车间防火防爆说明医药制剂品种极多,配方千变万化。
制剂室可分为普通制剂室、无菌制剂室及中药制剂室二类,防火要点各有不同。
1.普通制剂室的防火要求(1)普通制剂使用的大量乙醇。
如条件不允许分室储存时,应固定存放在制剂室的一角,远离明火热源,且不受行人来往影响。
配制外用药时往往要加入丙酮,其防火要求与乙醇相同。
制剂室中的液状石蜡、配剂、凡士林等亦应注意保管,与明火及性质相抵触的药物(如高锰酸钾)进行隔离。
(2)制剂室常用火棉胶套封瓶口,火棉胶套是硝酸纤维制品,浸在的80%乙醇与20%乙醚的混合液中,遇明火极易燃烧,应在铁皮桶中密封储藏。
如遇铁皮桶渗漏,应立即捡出,转移到不漏的铁皮桶内。
使用火棉胶套封口时。
应在排气罩下进行,排气用的轴流式风机应防爆。
有通风橱的、应在通风橱内操作,并存放一定时间,待火棉胶套硬化,溶剂挥发后取出。
剥下的或破碎的零星火棉胶,必须放在有盖的铁皮或搪瓷桶内,严禁随便乱丢或投放纸篓内。
下班时废火棉胶必须从制剂室内取出,及时处理掉,或浸没在水中。
(3)制刊室应通风良好。
电炉、煤气火等明火的位置应固定。
2.无菌制剂室无菌制刹主要是注射剂,人医院里用量甚大,故生产量也多,多为水溶液。
但是有些制剂原料需经过精制,才能用于制备注射剂。
精制多为实验室规模,有时要使用乙醚和苯等易燃液体,其防火要求与前述的系列化检验和实验室防火相同。
3.中药制剂室(1)中药制剂室经常生产流浸膏。
生产中乙醇液的加热不得用明火,宜用蒸汽加热浓缩。
浓缩回收乙醇时,应该用真空浓缩器,冷却要完善,以免乙醇蒸气逸出。
室内应通风良好,可开气窗以加强自然通风,否则应设有防爆的机械通风。
室内的电气设备应防爆。
(2)渗流是一种动态浸出法,大都用乙醇为浸出剂,渗流结束出药渣时,乙醇会大量挥发。
因此,药渣应先用水淋洗,把乙醇洗去,然后出渣;但仍须通风良好,出渣时杜绝明火。
无菌灌装车间的要求
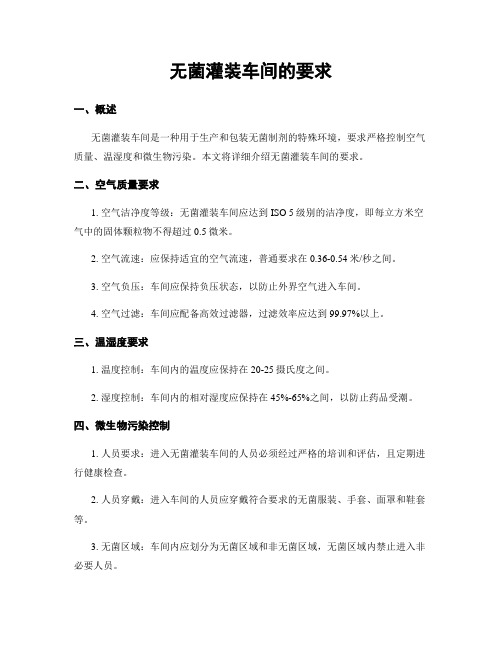
无菌灌装车间的要求一、概述无菌灌装车间是一种用于生产和包装无菌制剂的特殊环境,要求严格控制空气质量、温湿度和微生物污染。
本文将详细介绍无菌灌装车间的要求。
二、空气质量要求1. 空气洁净度等级:无菌灌装车间应达到ISO 5级别的洁净度,即每立方米空气中的固体颗粒物不得超过0.5微米。
2. 空气流速:应保持适宜的空气流速,普通要求在0.36-0.54米/秒之间。
3. 空气负压:车间应保持负压状态,以防止外界空气进入车间。
4. 空气过滤:车间应配备高效过滤器,过滤效率应达到99.97%以上。
三、温湿度要求1. 温度控制:车间内的温度应保持在20-25摄氏度之间。
2. 湿度控制:车间内的相对湿度应保持在45%-65%之间,以防止药品受潮。
四、微生物污染控制1. 人员要求:进入无菌灌装车间的人员必须经过严格的培训和评估,且定期进行健康检查。
2. 人员穿戴:进入车间的人员应穿戴符合要求的无菌服装、手套、面罩和鞋套等。
3. 无菌区域:车间内应划分为无菌区域和非无菌区域,无菌区域内禁止进入非必要人员。
4. 空气净化:车间内应配备空气净化设备,如紫外线灯、空气消毒器等,以杀灭空气中的微生物。
5. 表面消毒:车间内的工作台、设备和容器等应定期进行消毒处理,以防止表面污染。
五、设备要求1. 灌装设备:车间内的灌装设备应具备自动化控制功能,以减少人为操作带来的污染风险。
2. 过滤器:灌装设备中的过滤器应定期更换,以确保过滤效果。
3. 检测设备:车间内应配备适当的检测设备,如微生物培养基、菌落计数器等,用于监测微生物污染情况。
六、清洁和消毒要求1. 定期清洁:车间内应定期进行清洁,包括地面、墙壁、天花板等。
2. 清洁剂选择:清洁剂应符合无菌要求,且不得对药品产生污染。
3. 消毒剂选择:消毒剂应具备杀菌效果,且不得对设备和环境造成伤害。
七、记录和文件要求1. 温湿度记录:应定期记录车间内的温湿度情况,并保存相关记录。
2. 空气洁净度记录:应定期进行空气洁净度检测,并保存相关记录。
无菌灌装车间的要求

无菌灌装车间的要求一、简介无菌灌装车间是制药企业生产无菌药品的关键环节,要求在生产过程中保持无菌状态,确保药品的质量和安全性。
本文将详细介绍无菌灌装车间的要求,包括环境要求、设备要求、人员要求和操作要求。
二、环境要求1. 空气洁净度要求:无菌灌装车间应达到GMP要求的100级别洁净度,即空气中不得超过100个直径大于0.5微米的颗粒物。
2. 温度和湿度控制:车间内的温度应保持在20-25摄氏度,湿度应保持在45%-60%之间,以确保无菌环境的稳定性。
3. 照明要求:车间内的照明应均匀、充足,避免影响操作人员的视觉判断。
三、设备要求1. 灌装设备:应选用符合GMP要求的无菌灌装设备,确保灌装过程中不会引入外界污染物。
2. 过滤设备:应配备有效的过滤设备,对进入车间的空气进行过滤,去除悬浮颗粒物和微生物。
3. 消毒设备:应配备有效的消毒设备,对车间内的空气、设备和工具进行定期消毒,以保持无菌状态。
四、人员要求1. 培训要求:无菌灌装车间的操作人员应接受相关的无菌操作培训,了解无菌操作的原理和要求,熟悉相关的操作规程。
2. 穿戴要求:操作人员应穿戴符合要求的无菌服装,包括无菌手套、无菌口罩、无菌帽子等,以防止人员对无菌环境的污染。
3. 卫生要求:操作人员应保持良好的个人卫生习惯,定期进行身体检查,确保不携带病原微生物进入车间。
五、操作要求1. 入场前准备:操作人员应在进入车间前进行必要的准备工作,包括洗手、更换无菌服装等,确保自身的无菌状态。
2. 操作规程:操作人员应按照相关的操作规程进行操作,包括灌装、封口、贴标等环节,确保操作的准确性和无菌性。
3. 废弃物处理:操作人员应按照规定的程序将废弃物进行分类处理,避免对无菌环境造成污染。
4. 定期验证:无菌灌装车间应定期进行验证,包括空气洁净度检测、设备消毒效果验证等,以确保无菌环境的稳定性和可靠性。
六、总结无菌灌装车间的要求包括环境要求、设备要求、人员要求和操作要求。
某制药厂无菌制剂车间百级层流的空调设计

浅谈某制药厂无菌制剂车间百级层流的空调设计摘要:百级层流在药品生产过程中是一个重要的区域,主要负责工艺生产线作业的核心区域,在药品生产过程中起到至关重要的作用,在无菌制剂车间一般分装压塞、冻干以及轧盖等工序都需在百级层流内进行操作,应尽可能降低污染的风险,百级层流对温湿度及压力等环境因素要求也很高。
本文从某制药厂无菌制剂车间百级层流的改造入手,浅谈药厂百级层流的空调设计。
关键词:制药厂洁净区;百级洁净区;空调设计;通风系统中图分类号:s611文献标识码:a文章编号:本项目为无锡某外资药厂无菌制剂车间百级层流改造,本建筑为集装箱式厂房,生产区设置在底楼,楼板高约3.8m,可用空间3.2m,设备机房设在一楼,楼板高约3.8m,可用空间3.2m。
主要改造的房间为19#冻干间、20#转运间、23#轧盖间,此项目是非常有特点的一个百级层流项目,依据各房间的要求不同采用了三种层流型式的空调设计,详细说明如下:一、以19#房间层流laf01为例说明组合式空调箱+液槽龙骨+刀架过滤器+侧下回风型式的系统设计laf01主要用于保护冻干后未轧盖的小瓶从冻干机出来到转运间的操作,需要覆盖整个转运通道,安装在19房间内(吊顶标高2.6m,洁净级别b级),规格为异型(见图1),面积约为14m2,距地2.6m高,转运车高2.2m。
图1 laof01平面图图2 系统原理图图3 a-a节点图图4 a-a断面气流模拟1、空气流程:部分风通过19房间侧墙下回风口、回风管回到空调机组内,经降温、加压、中效过滤后,再经送风管及散流板送入不锈钢静压箱内,另一部分风回到ahs-02,经热湿过滤加压后,经散流板后送入不锈钢静压箱内,两者混合后,满足温湿度要求的风经高效过滤器过滤后送入层流工作区内,扩散后回到19房间内,再通过19房间的回风口回到夹道内,一部分回到循环空调机组内,另一部分风回到ahs-02回风系统内,层流形成一个完整的循环系统,对洁净室的压力无影响,房间压力及湿度由ahs02空调系统保证。
关于无菌制剂车间自动配料系统性能测试技术的研究

灭菌产品,而非最终灭菌产品作为高风险的品种,其配制过程,则需要尽可能的采取措施,防止污染和交叉污染,采用具备自动清洗和自动灭菌功能的自动化配料系统进行无菌药品的配制,可以有效降低微生物污染的风险,符合GMP的要求。
无菌制剂车间的自动配料系统,位于车间的C级洁净区,是无菌药品生产过程中最关键工序配料所使用的设备,为下一工序提供符合质量要求的中间体。
按照无菌药品工艺规程完成该配料过程,是产品质量有保证的前提,而自动配料系统安装完成后,需对该系统进行设计、安装、运行以及性能等测试,性能测试则作为整个过程中的重中之重。
本文侧重研究自动配料系统的性能测试方面,设计了数项测试技术,验证其压力保持、升降温速度、称重功能、搅拌功能、在线清洗(CIP)以及在线灭菌(SIP)等功能,通过测试数据结果证明该自动配料系统能够按照既定工艺完成药品的配制工序,提高了无菌药品中间体的质量。
Part 1›自动配料系统描述及工作原理自动配料系统主要用于药品生产过程中产品的配制过程,主要由浓配罐、稀配罐、无菌储罐、缓冲罐、管道以及P1C控制系统组成,整套系统具有精密采水定容、系统在线CIP和SIP、吹干保压等功能,系统的排水口具有隔断排水装置,防止灭菌后冷却形成的负压倒吸,稀配罐按工艺进行定容,经过药液过滤器过滤暂存罐,可以在暂存罐对其进行无菌取样。
在取得灌装机供液信号后,将药液经除菌过滤器过滤后压入缓冲罐,供灌装机灌装药液。
以上自动配料系统的配料罐均采用不锈钢SUS3161,罐体设有夹套,可加热、冷却或保温。
内表面采用镜面抛光,无卫生死角,全封闭的设计确保物料始终处在隔离状态下。
封头均经旋压加工,搅拌装置采用卫生级机械密封,接口采用ISO标准快装卡箍式均符合GMP标准。
设备配有C1P重模块。
自动配料系统的工作原理,首先是在浓配罐进行药液配制,然后在稀配罐按药品工艺进行定容,药液经过除菌过滤器过滤至无菌储罐(可在无菌储罐对其进行无菌取样),在取得灌装机供液信号后,最终将药液经除菌过滤后压入缓冲罐,供灌装机灌装药液,其稀配罐和无菌储罐均配置无菌空气呼吸器和称重模块,并配有CIP清洗喷头,可通过视镜进行观察,其法兰式快开人孔装置可提供物料的进入。
无菌无车间管理制度

无菌无车间管理制度一、概述无菌无菌车间是生产医疗器械、药品等高要求产品的特殊生产场所,为了确保产品的质量和有效防止交叉污染,需要建立严格的管理制度。
本制度的制定旨在规范无菌无菌车间的管理行为,确保车间干净、卫生,杜绝交叉污染,保证产品的质量和安全。
二、管理范围本制度适用于无菌无菌车间的运营和管理,包括但不限于生产设备、操作规范、人员管理、清洁消毒、环境监测等方面。
三、车间环境1.车间应设有进出口划分区域,禁止非相关人员在车间出入口停留,并设有专门的进出通道。
2.车间内地面、墙壁、天花板等均应平整、无裂缝、无积尘,应保持清洁干净。
3.车间内应配备必要的通风换气设施,确保空气流通。
设有适当数量的洁净工作台、无菌操作台等。
4.车间内应配备必要的温湿度控制设备,确保生产环境达到要求。
5.车间内应定期进行无菌度检测、微生物检测等环境监测工作。
四、设备管理1.设备应定期进行维护、保养、清洁,并建立设备台账、维修记录。
2.设备使用前应进行启动、验证,确保设备正常运转。
3.设备操作人员应接受专业培训,掌握设备操作规程。
4.设备使用后应及时清洁消毒,避免交叉污染。
五、人员管理1.车间人员应接受相关岗位培训,了解无菌操作规范、安全操作规程。
2.车间人员进出车间前应穿着清洁工作服、鞋套、帽子等符合无菌要求的服装。
3.车间人员应保持个人卫生,禁止患有传染病的人员进入车间。
4.车间人员操作时应遵守无菌操作规程,严格执行无菌操作步骤。
六、操作规范1.车间操作人员应按照无菌操作规范进行操作。
操作前应进行手部消毒、穿戴相应的无菌器具。
2.严格执行无尘、无菌的操作要求,杜绝交叉污染的可能性。
3.严格执行产品检验、包装规范,确保产品的质量。
七、清洁消毒1.车间应定期进行清洁消毒工作,清洁消毒工作人员应接受专业培训。
2.清洁消毒工作要求添加适量的消毒剂、杀菌剂,确保车间无菌度达标。
3.清洁消毒工作应定期进行验证,确保清洁消毒效果。
八、环境监测1.车间应定期进行无菌度检测、微生物检测等环境监测工作。
【案例】无菌药品生产车间的改造设计
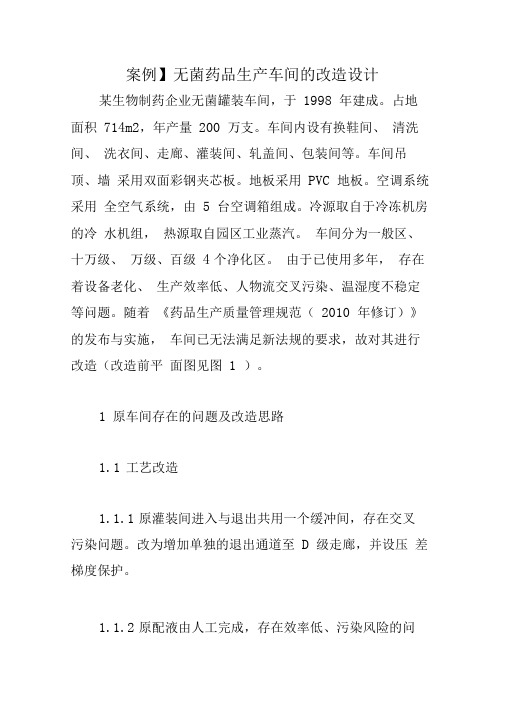
案例】无菌药品生产车间的改造设计某生物制药企业无菌罐装车间,于1998 年建成。
占地面积714m2,年产量200 万支。
车间内设有换鞋间、清洗间、洗衣间、走廊、灌装间、轧盖间、包装间等。
车间吊顶、墙采用双面彩钢夹芯板。
地板采用PVC 地板。
空调系统采用全空气系统,由5 台空调箱组成。
冷源取自于冷冻机房的冷水机组,热源取自园区工业蒸汽。
车间分为一般区、十万级、万级、百级4个净化区。
由于已使用多年,存在着设备老化、生产效率低、人物流交叉污染、温湿度不稳定等问题。
随着《药品生产质量管理规范(2010 年修订)》的发布与实施,车间已无法满足新法规的要求,故对其进行改造(改造前平面图见图1 )。
1原车间存在的问题及改造思路1.1工艺改造1.1.1原灌装间进入与退出共用一个缓冲间,存在交叉污染问题。
改为增加单独的退出通道至D 级走廊,并设压差梯度保护。
1.1.2原配液由人工完成,存在效率低、污染风险的问题。
改为增加独立配液间,并增加自动配液系统,设层流罩保护。
1.1.3原称量与配液在同一间房间完成,存在交叉污染风险。
改为增加独立称量间,完成称量。
1.1.4原灌装间百级面积过大,存在能耗大、难控制的问题。
改为B 级背景+灌装区A 级层流保护,灌装机设置围挡。
1.1.5原冻干后成品由人工手持托盘转运,存在效率低、污染风险的问题。
改为增加小车进行转运。
1.1.6原轧盖后至包装采用人工转运的方式,效率低、且无直接转运通道。
改为转盘转运,并将轧盖背景区域洁净级别提升为C 级。
1.1.7原轧盖机没有抽风装置,也没有自动剔除装置,容易形成二次污染。
改为替换轧盖机带抽风、自动剔除装置。
1.1.8原轧盖没有排风,容易形成二次污染,改为增加排风。
1.1.9原两间洗衣间存在功能重复。
改为将其合并,增加大功率洗衣烘干机。
1.10 原车间缺少在线粒子检测间及设备,改为增加独立的在线粒子检测间及设备。
1.11 原车间缺少可在灌装间外部观察灌装操作的观察窗,改为在灌装间与准备间之间增加观察窗。
- 1、下载文档前请自行甄别文档内容的完整性,平台不提供额外的编辑、内容补充、找答案等附加服务。
- 2、"仅部分预览"的文档,不可在线预览部分如存在完整性等问题,可反馈申请退款(可完整预览的文档不适用该条件!)。
- 3、如文档侵犯您的权益,请联系客服反馈,我们会尽快为您处理(人工客服工作时间:9:00-18:30)。
A B C D E* E F
<1 10 100 200 200 500 ---
<1 5 50 100 100 400 ---
<1 5 25 50 50 -----
<1 5 -----------
<1 5 -----------
* 对于注射剂的活性成分;
(a) (b)
上述数字是平均值 耽搁沉降菌的碟子的暴露可能少于4个小时
Clean rooms • 2010-10-20/23 • Page 7
生产无菌药品的房间
洁净级别的比较
中国 (2009征求意 见稿) A B C D (350 000)
拜耳先灵医药 A B C D E* E
欧洲 A B C D
FDA 100 10 000 100 000 100 000
ISO 14644 5 7 8 9
洁净室
无菌产品
最终灭菌产品
非最终灭菌产品
传统的洁净房间
隔离操作器
RABS 屏障系统
Clean rooms • 2010-10-20/23 • Page 31
传统式洁净间(紊流型)
Clean rooms • 2010-10-20/23 • Page 32
传统式洁净间(紊流型)
• 通过以下方式保护洁净区域:
Clean rooms • 2010-10-20/23 • Page 3
生产无菌药品的房间
EU GMP 指南, 附录 1-无菌药品的生产
每立方米空气中(允许的大于或者等于下列粒径 的最多颗粒数量 每立方米空气中 允许的大于或者等于下列粒径)的最多颗粒数量 允许的大于或者等于下列粒径 静态 洁净级别 A B C D 0.5µm 3 520 3 520 352 000 3 520 000 5.0µm 20 29 2 900 29 000 动态 0.5µm 3 520 352 000 3 250 000 未规定 5.0µm 20 2 900 29 000 未规定
• 称量、配制和灌装区域的工作人员应在脱去E级洁净服后,穿D级洁净 服
• 灌装区域的工作人员应在脱去E级洁净服后,穿C级洁净服
Clean rooms • 2010-10-20/23 • Page 15
最终灭菌产品的区域概念
物流
Clean rooms • 2010-10-20/23 • Page 16
清洁后的包装材料 D
Clean rooms • 2010-10-20/23 • Page 9
生产无菌药品必要的洁净级别
最终灭菌产品 • • • • • 产品溶液制备 (称量、配制、过滤) 必须在至少D级环境下进行 当产品受到微生物污染的风险很高或者有异常风险时,则溶液制备 应在C级条件下进行 灌装应在至少C级环境条件下进行 当产品易于受到环境污染时--例如:广口瓶暴露若干秒--灌装 则应在C级环境中的局部A级条件下进行 膏剂、乳膏剂、混悬剂和乳剂等通常在C级条件下进行制备和灌装
• 灌装区域的工作人员应在脱去E级洁净服后,穿B级洁净服 • 灌装区域应采取A级层流空气罩保护,在A级环境中进行操作前应对手和前臂 消毒
Clean rooms • 2010-10-20/23 • Page 23
Clean rooms • 2010-10-20/23 • Page 24
非最终灭菌产品的区域概念
Clean rooms • 2010-10-20/23 • Page 10
无菌药物生产的必要洁净级别
非最终灭菌产品 • • • • • • 无菌原辅料、直接接触药品的包装材料应在B级环境中的局部A级条 件下中进行操作 清洗后直接接触药品的包装材料的材料应在至少D级条件下进行处 理 产品溶液的制备过程(称量、配制、无菌过滤) 必须在至少C级环境 下进行 无菌产品溶液的处理、灌装和压塞及无菌物料的处理应在B级环境 中的局部A级条件下进行 未完全压塞(部份密封)的产品容器(冻干产品)的转运应在B级环境 中的局部A级条件下进行 压塞后,但未最终密封的容器应在达到A级洁净级别的空气保护下 进行处理
Clean rooms • 2010-10-20/23 • Page 21
非最终灭菌产品
Clean rooms • 2010-10-20/23 • Page 22
非最终灭菌产品的区域概念
人员流向
• 车间人员必须通过人员缓冲间进入车间,并且更换成相应的车间E级洁净服 • 称量、配制和灌装区域的工作人员应在脱去E级洁净服后,穿D级洁净服 • 清洗设备(最终淋洗)和灭菌锅物料装卸人员应在脱去E级洁净服后,穿D级 洁净服
生产无菌制剂的房间
Hubert Appolt Beijing 2010-10-20/22
内容
• 洁净级别 • 必要的洁净级别 • 区域(Zone)概念 / 人流 / 物流 • 洁净房间的概念
Clean rooms • 2010-10-20/23 • Page 2
生产无菌药品的房间
• 以下的PPT内容是欧洲以及拜耳先灵医药对无菌制剂产品生产的要 求。 • 另外,生产商还需要遵守上市国家的其他规定
最终灭菌产品的区域概念
物流 • 物料应通过物料通道进入车间,必要时应进行清洁和检查 • 需要进入称量、配制和灌装区域的物料,应在另一个连接D级区域的 物料通道内,对外包装进行清洁和消毒。 • 用于灌装房间的物料应在D级区域进行清洁。 • 清洁后待灌装的物料,如瓶子、胶塞等,应通过另一个物料通道进入 C级区域 • 灌装、密封后的容器可通过一个通道离开灌装区域,进入到E级区或 者无级别区域
洁净级别
楼梯 楼梯 库房隧道
EX仓库
货梯
物料缓冲间
技术区域
培养室
仓库
档案室
车间 人员缓冲间
货梯
洗衣房 楼梯 楼梯
D 302 楼地下一层
人员缓冲间 洁净级别 E F
Clean rooms • 2010-10-20/23 • Page 28
洁净级别
公用工程区域
层流罩
人员缓冲间
过滤区
灭菌器
制备区
参观人员区
生产无菌药品的房间
拜耳先灵医药的洁净级别
推荐的微生物限度 (a) 洁净级别
cfu/立方米空气 沉降菌 cfu / 4 立方米空气 样品 小时 (b) (直径 直径 90 mm)
洁净服 平皿接触法 cfu 手套 / 碟(直径 55 5 手指 cfu/手套 接触法 擦拭法 直径 手套 接触法/擦拭法 cfu/25cm² mm)
浮游菌 cfu / 碟 手套
(直径 55 mm) 直径 5 手指 cfu/手套 手套
A B C D
<1 10 100 200
<1 5 50 100
<1 5 25 50
<1 5 -
(a) (b)
上述数字是平均值 单个碟子的暴露时间可能少于4个小时
Clean rooms • 2010-10-20/23 • Page 6
动态
Clean rooms • 2010-10-20/23 • Page 8
静态
洁净级别
无菌药品
最终灭菌产品 称量 D 配制 过滤 灌装 密封 灭菌 D* D C** C –
非最终灭菌产品 称量 C 配制 过滤 灌装 密封 轧盖 C C A/B A/B ~A
* C 级,当有异常风险时 ** A/C 级 ,当有异常风险时
B A
D D级环境中的隔离操作器 A
Clean rooms • 2010-10-20/23 • Page 13
最终灭菌产品的区域概念
人员流向
Clean rooms • 2010-10-20/23 • Page 14
最终灭菌产品的区域概念
人员流向 • 车间人员必须通过人员缓冲间进入车间,并且更换相应的车间E级洁 净服
帘子 窗/门 正压 / 气流
Clean rooms • 2010-10-20/23 • Page 33
传统式洁净间(紊流型)
• 洁净的环境 • 方便实施介入操作 在设备设置过程中 在生产过程中进行介入操作 手工取样
Clean rooms • 2010-10-20/23 • Page 19
Clean rooms • 2010-10-20/23 • Page 20
最终灭菌产品的区域概念
特殊风险产品的物料流向 • 物料应通过物料通道进入车间,必要时应进行清洁和检查 • 需要进入称量、配制和灌装区域的物料,应在另一个连接D级区域的 物料通道内,对外包装进行清洁和消毒。 • 用于灌装房间的物料应在D级区域进行清洁 • 清洁后待灌装的物料,如瓶子、胶塞等,应通过另一个的物料通道进 入C级区域 • 灌装、密封后的容器可通过一个通道离开灌装区域,进入到E级区或 者无级别区域
物流 • 清洁后待灌装的物料,如瓶子、胶塞等应通过一个灭菌锅/隧道式灭菌 器进入到A级区域 • 配制后的液体应通过固定管道系统(含有除菌过滤步骤)送到灌装区 域。如果系统使用的是可移动式储罐,则该储罐必须通过装有强烈消 毒工序的物料通道(进入到灌装区域)。 • 灌装、密封后的容器应经过一个通道离开灌装区域,进入到E级区或 者无级别区域
*对于用于注射剂的活性成分; ** 有产品暴露的区域
Clean rooms • 2010-10-20/23 • Page 5
生产无菌药品的房间
EU GMP 指南, 附录 1-无菌药品的生产
推荐的微生物限度 (a) 洁净级别
cfu/立方米空气 沉降菌 cfu / 4 立方米空气 样品 小时 (b) (直径 直径 90 mm)
Clean rooms • 2010-10-20/23 • Page 17
最终灭菌产品的区域概念
特殊风险的产品
Clean rooms • 2010-10-20/23 • Page 18