测量系统分析案例
MSA测量系统分析在制造业中的应用案例(1)

准确的测量可以减少生产过程中的浪费和返工, 降低生产成本。
增强企业竞争力
优化测量系统有助于企业提高产品质量和生产效 率,从而增强市场竞争力。
MSA测量系统分析概述
定义
MSA(Measurement System Analysis)是一种用统计学方法 评估测量系统的稳定性和准确性的技术。
测量误差来源
测量误差主要来源于测量设备、测量环境、测量人员和测量方法等 方面。
测量系统分析目的
通过对测量系统的分析,可以评估其稳定性和准确性,进而确保产品 质量和生产过程的可控性。
MSA测量系统分析方法与步骤
方法概述
MSA测量系统分析方法主要包括稳定 性分析、偏倚分析、线性分析、重复 性和再现性分析等。
04
应用案例一:汽车制造行业
汽车制造行业现状及挑战
市场竞争激烈
汽车制造行业面临国内外众多竞争对手,需要不断提高产品质量 和生产效率以保持竞争优势。
客户需求多样化
消费者对汽车的需求日益多样化,对产品质量和性能提出更高要 求。
制造技术不断更新
随着新技术、新工艺的不断涌现,汽车制造企业需要不断适应和 更新制造技术。
质量控制挑战
传统的质量控制方法往 往难以实现全面、准确 的质量评估,需要引入 更先进的测量和分析技 术。
MSA测量系统分析在机械制造中的应用
工序能力评估
通过MSA测量系统分析,可以对 机械制造过程中的各个工序进行 能力评估,确定工序的稳定性和 一致性。
误差来源识别
MSA可以帮助识别制造过程中的 误差来源,如设备误差、操作误 差、环境误差等,为改进生产过 程提供依据。
原理
通过对测量设备的重复性、再现性、稳定性等指标进行分析,判断 测量系统是否满足生产要求。
测量系统分析报告案例

测量系统分析报告案例1. 引言测量系统是工业生产中不可或缺的一部分,它用于测量和监控各种参数,以确保产品质量和生产效率。
本报告通过对一家汽车制造公司测量系统的分析,提供了有关系统性能和潜在问题的详细概述。
2. 测量系统概述该汽车制造公司的测量系统主要用于检测和校准汽车发动机的尺寸和形状等关键参数。
测量系统由一系列测量设备、传感器、数据采集与处理单元以及数据记录和分析软件组成。
该系统的主要功能是测量和分析发动机零部件的尺寸精度,以确保其符合设计要求。
3. 测量设备与仪器该测量系统使用了多种测量设备和仪器,包括:•进口高精度三坐标测量仪:用于测量发动机零部件的尺寸和形状,具有高精度和稳定性。
•光学测量仪:用于测量发动机零部件的表面质量和光学特性。
•数显卡尺:用于测量零部件的线性尺寸。
•温湿度传感器:用于监测测量环境的温度和湿度。
这些设备和仪器在整个测量过程中起着关键作用,确保了测量数据的准确性和可靠性。
4. 数据采集与处理在测量过程中,测量设备会通过传感器采集到大量的数据,而后将数据传输到数据采集与处理单元进行处理。
数据采集与处理单元使用专门开发的软件对数据进行实时分析和处理,并将结果记录到数据库中。
该软件具有以下功能:•数据过滤和校准:对采集到的原始数据进行滤波和校准,去除误差和噪音。
•数据分析:对测量数据进行统计分析和趋势分析,以评估测量过程的稳定性和可重复性。
•数据可视化:以图表和图形的形式呈现测量结果,便于分析和比较。
•数据记录和报告生成:将测量数据记录到数据库中,并生成详细的测量报告。
数据采集与处理系统在测量系统中起着至关重要的作用,确保了测量结果的准确和可靠性。
5. 系统性能分析为了评估测量系统的性能,我们进行了以下分析:5.1 精度分析通过与国际标准对比,我们对测量系统的精度进行了评估。
结果显示系统的测量误差在允许范围内,并与国际标准接近。
5.2 稳定性分析我们对测量系统的稳定性进行了分析,从测量结果的波动性和重复性两个方面进行了评估。
测量系统分析(MSA)-实例

03 实例测量系统分析
偏倚分析
确定测量系统的准确性
通过比较测量系统所得结果与已知标准值或参考值之间的差异, 评估测量系统的偏倚程度。
计算偏倚值
将测量系统的结果与标准值或参考值进行对比,计算出偏倚值。
判断偏倚是否可接受
根据所允许的偏倚范围,判断测量系统的偏倚是否在可接受的范围 内。
线性分析
1 2
测量系统分析(MSA)-实例
目录
• 测量系统分析概述 • 实例选择与数据收集 • 实例测量系统分析 • 实例测量系统评价 • 实例总结与改进建议
01 测量系统分析概述
定义与目的
定义
测量系统分析(MSA)是对测量系 统的误差来源、大小及分布进行评 估的过程。
目的
识别测量系统的变异性来源,确 保测量系统能够满足产品质量和 过程控制的要求。
测量系统分析的重要性
提高产品质量的可预测性和可靠性
01
通过对测量系统进行全面分析,可以了解测量误差的大小和分
布,从而更准确地预测产品质量。
优化生产过程控制
02
准确的测量数据是生产过程控制的基础,对测量系统进行有效
的分析有助于提高过程控制的稳定性和有效性。
降低成本
03
通过减少测量误差,可以减少重复测量、检验和返工等不必要
的操作,从而降低生产成本。
测量系统分析的步骤
确定分析范围和对象
明确需要分析的测量设备、工 具或方法,以及相关的操作人
员和环境条件。
数据收集
收集一定数量、具有代表性的 测量数据,包括重复测量、再 现性数据等。
数据分析
对收集到的数据进行统计分析 ,识别测量系统的变异性来源 。
结果评估与改进
测量系统分析在中的运用例
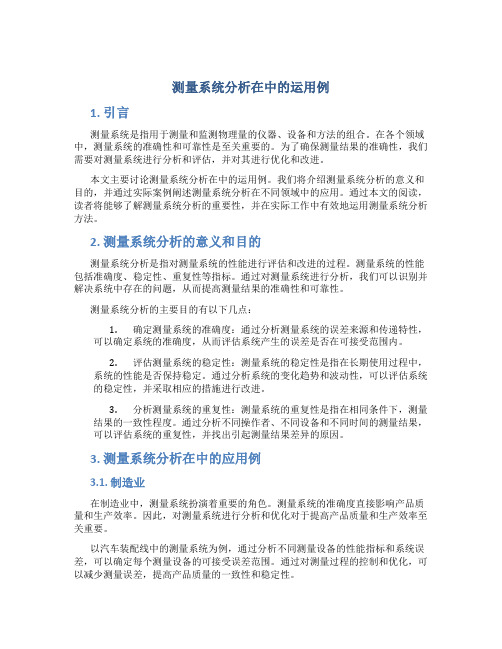
测量系统分析在中的运用例1. 引言测量系统是指用于测量和监测物理量的仪器、设备和方法的组合。
在各个领域中,测量系统的准确性和可靠性是至关重要的。
为了确保测量结果的准确性,我们需要对测量系统进行分析和评估,并对其进行优化和改进。
本文主要讨论测量系统分析在中的运用例。
我们将介绍测量系统分析的意义和目的,并通过实际案例阐述测量系统分析在不同领域中的应用。
通过本文的阅读,读者将能够了解测量系统分析的重要性,并在实际工作中有效地运用测量系统分析方法。
2. 测量系统分析的意义和目的测量系统分析是指对测量系统的性能进行评估和改进的过程。
测量系统的性能包括准确度、稳定性、重复性等指标。
通过对测量系统进行分析,我们可以识别并解决系统中存在的问题,从而提高测量结果的准确性和可靠性。
测量系统分析的主要目的有以下几点:1.确定测量系统的准确度:通过分析测量系统的误差来源和传递特性,可以确定系统的准确度,从而评估系统产生的误差是否在可接受范围内。
2.评估测量系统的稳定性:测量系统的稳定性是指在长期使用过程中,系统的性能是否保持稳定。
通过分析系统的变化趋势和波动性,可以评估系统的稳定性,并采取相应的措施进行改进。
3.分析测量系统的重复性:测量系统的重复性是指在相同条件下,测量结果的一致性程度。
通过分析不同操作者、不同设备和不同时间的测量结果,可以评估系统的重复性,并找出引起测量结果差异的原因。
3. 测量系统分析在中的应用例3.1. 制造业在制造业中,测量系统扮演着重要的角色。
测量系统的准确度直接影响产品质量和生产效率。
因此,对测量系统进行分析和优化对于提高产品质量和生产效率至关重要。
以汽车装配线中的测量系统为例,通过分析不同测量设备的性能指标和系统误差,可以确定每个测量设备的可接受误差范围。
通过对测量过程的控制和优化,可以减少测量误差,提高产品质量的一致性和稳定性。
3.2. 医疗领域在医疗领域,测量系统广泛应用于诊断、治疗和监测等方面。
iatf16949五大质量工具详解及运用案例

iatf16949五大质量工具详解及运用案例在汽车行业中,质量管理是至关重要的,因为质量问题可能导致严重的安全隐患和巨大的经济损失。
为了确保汽车制造商和供应商的质量标准,国际汽车任务力量(IATF)制定了一系列质量管理要求,其中包括了五大质量工具,分别是:流程流程图、测量系统分析(MSA)、统计过程控制(SPC)、故障模式与效应分析(FMEA)和8D问题解决方法。
本文将详细介绍这五大质量工具的概念和用途,并提供相关案例以展示它们的运用。
1. 流程流程图(Process Flow Diagram)流程流程图是一种用来描述和分析制造过程的工具,通过可视化地展示各个步骤和流程之间的关系,帮助人们理解整个制造流程,并识别潜在的质量问题和瓶颈。
流程流程图通常以图表的形式呈现,其中包含了输入、输出、关键步骤、检查点和控制点等信息。
案例:一家汽车制造商使用流程流程图来分析其汽车装配流程。
通过绘制装配线的各个步骤和工位,并标注每个步骤的输入和输出,该制造商能够清楚地了解到每个工位的功能和责任。
在制造过程中,该公司发现一个质量问题,通过对流程流程图的分析,他们发现问题出现在一个关键步骤上,因为该步骤的输入与输出不匹配。
通过对该步骤进行调整和改进,该制造商成功地解决了质量问题,提高了产品的质量和效率。
2. 测量系统分析(Measurement System Analysis,MSA)测量系统分析是一种用来评估和确认测量过程的可靠性和准确性的方法。
在汽车制造中,准确的测量是确保产品质量的关键,而测量系统分析则能帮助汽车制造商评估和优化其测量系统,确保其测量结果的可靠性。
案例:一家汽车零部件供应商使用测量系统分析来评估其测量设备的准确性。
通过进行重复性和再现性测试,他们能够确定测量设备的误差和变异程度。
在进行测量系统分析后,该供应商发现一个测量设备存在较大的误差,导致了产品质量的下降。
他们随后采取了纠正措施,修复了该设备,并通过再次进行测量系统分析确认了其准确性和稳定性。
MSA测量系统分析之Minitab中文应用案例(步骤清晰实用)精选全文

应多数值在控 制限外
在控制限外表示过程实际 的变差大,同时表明测量 能力高。
均值
部件对比图:可显示在研究过程中所测量的并按部件排列的所有测量结果。测量结果用 点表示,平均值用带十字标的圆形符号表示。 判断:1.每个部件的多个测量值应紧靠在一起,表示测量的重复再现性的变差 小。
2.各平均值之间的差别应明显,这样可以清楚地看出各部件之间的差别。 例:图中的7#、10#重复测量的精确度较其他点要差,如果测量系统的R&R偏大时,可 以对7#、10#进行分析。
所有点落在管理界限内 ->良好
大部分点落在管理界限外 ->主变动原因:部品变动
->良好
->测量值随部品的变动 ->测量值随OP的变动
->对于部品10,OP有较大分歧;
M--测量系统分析: 离散型案例(名目型):gage名目.Mtw
背景:3名测定者对30部品反复2次TEST
检查者1需要再教育; 检查者3需要追加训练; (反复性)
(2).在量具信息与选项栏分别填入相关资料与信息。
填入相关 资料
注:其他选项若无要求,选择 默认项,不做改动。
一般为6 倍标准差
零件公差 规格
4.5、结果生成:数据表与图表
图表分析表
数据会话表
5.结果分析: (1)图表分析
变异分量条形图:展示了会话窗口中的计算结果,此图显示整个散布中R&R 占的比重是否充分小。 判断:量具R&R,重复(Repeat), 再现性(Reprod)越小越好。
A—假设测定:案例:2sample-t.MTW (2): 2-sample t(单样本)
① 正态性验证:
<统计-基本统计- 正态性检验 : >
msa测量系统分析案例
MSA测量系统分析案例概述测量是制造过程中非常重要的一环,而测量系统分析(Measurement System Analysis,MSA)则是评估测量系统准确性和稳定性的一种方法。
通过进行MSA,可以确定测量系统的可靠性,进而评估生产过程的可控性和测量数据的可靠性。
本文将介绍一个MSA案例,以帮助读者更好地理解此概念。
案例背景某汽车制造公司在生产过程中使用一个测量系统来测量制动片的厚度。
这个测量系统包括一个数字测量仪(Digital Measuring Device,DMD)和一个人工操作员。
为了了解这个测量系统的性能,公司决定进行MSA分析。
数据收集为了进行MSA分析,公司选择了20个制动片样本进行测量。
每个样本被测量了10次,得到了200个测量值。
下表为这些测量值的示例(单位:毫米):样本编号测量1测量2测量3测量4测量5测量6测量7测量8测量9测量10110101010101010101010 29.89.79.910.11010.29.910.2109.8……………………………209.69.59.79.69.89.79.79.59.69.8 MSA分析步骤进行MSA分析通常需要按照以下步骤进行:首先,我们需要计算测量系统的准确度。
准确度可以通过计算测量值的均值与实际值之间的差异来评估。
下面是计算准确度的示例代码(使用R语言):markdown{r} # 计算每个样本的平均值 sample_means <- apply(samples, 1, mean)计算所有样本的平均值overall_mean <- mean(sample_means)计算每个样本的与实际值之间的差异differences <- abs(sample_means - actual_value)计算准确度(以均值差异的平均值表示)accuracy <- mean(differences) ```根据实际情况填写具体数值,上述代码将计算准确度并保存在变量accuracy中。
【参考文档】msa分析案例-优秀word范文 (14页)
本文部分内容来自网络整理,本司不为其真实性负责,如有异议或侵权请及时联系,本司将立即删除!== 本文为word格式,下载后可方便编辑和修改! ==msa分析案例篇一:MSA测量系统分析的案例分析MSA测量系统分析的案例分析从选矿生产过程中选取10个铁精矿样品,选用3名化检验人员,使用同一套检验系统,按不同的顺序分别检测10个样品,重复3遍。
检测结果数据如下表。
测量数据处理的结果及图表的解释本实验的测量结果数据的处理采用Minitable软件处理。
数据处理结果可用变差的方差分析表和图表两种方式来解释和说明。
其中,变差的方差分析表从各项方差占总变差的百分比来说明变异情况,图表则以图来说明。
1.变差的方差分析表本方法运用极差来计算方差,然后通过方差来计算各种变差及各变差占合计变异的比例,从而确定各变差的影响程度。
计算结果如表2。
由表2可知:。
(1)测量系统的合计量具R&R的研究变异值为17.38%,介于10%~20%之间,化检验系统变差较小,化验系统可以接受。
(2)测量系统的重复性为16.26%,介于10%~20%之间,波动较小,说明设备系统变差在可接受范围内。
但重复性(16.26%)较大,也是引起合计量具R&R偏高的主要原因,应引起注意,查明原因。
(3)测量系统的再现性和检验人员的变异都为6.15%,小于10%,说明检验人员间的变差波动很小。
化检验人员操作一致性较好。
(4)样品间的变异值为98.48%,变异显著,检验系统明显表示出样品间的品质差异。
(5)区别分类数(ndc)为7,大于5。
因此,化验系统能够满足测量的需要。
2.图表结果图表以较直观的方式来说明检验情况,并可以看出较细微的差异:(1)各变异分量各变异分量情况由图1显示,从图1可以看出样品间的变异是变异的主要来源,系统能够区分试样品位的变化。
(2)Xbar控制图图2Xbar控制图(平均值图)显示A,B,C三位化检验人员每件样品3次化验的平均值情况。
测量系统分析计算实例- 案例3 测量系统分析
测量系统分析计算实例- 案例3 测量系统分析案例案例3测量系统分析计算实例测量系统分析计算实例某企业主要生产型号为YSK30-6A电机,电机主要质量特征值为电机轴径向跳动量。
公差要求为0 ~ 0 .03毫米。
已知其质量特征值服从正态分布,质量特征值转化为测量时,由测量员进行a和b使用相同的测量仪器进行测量,使用的测量仪器是百分表。
为了了解测量系统的可靠性,采集了10个样品,并立即分发给检测员A和检测员B,每个样品测量3轮。
该过程中获得的数据如表3-1所示。
表3-1测量系统分析数据123123 10 .0250 .020 .020 .020 .020 .020 .0150 .0220 .030 .0450 .030 .0250 .040 .0330 .0140 .0150 .0150 .020 .0150 .0240 .0080 .010 .010 .010 .010 .010 .0150 .040 .040 .040 .040 .030 .0460 .0480 .0450 .0450 .030 .040 .0470 .010 .020 .010 .010 .0150 .01580 .010 .010 .010 .020 .010 .01590 .0250 .0250 .020 .020 .030 .02100 .0450 .030 .030 .030 .0250 .04操作轮这个问题属于典型的跨类型测量系统分析问题。
Minitab提供了两种测量R&R(交叉)的方法:均值范围法或方差分析法。
平均范围法将总体变化分为三类:分量之间的变化、重复性和再现性。
方差分析进一步将再现性分为操作者和操作者-成分交互作用。
在某种程度上,方差分析平均范围方法更准确,因为它考虑了操作者和组件之间的相互作用。
下面,将分别针对这两种方法对测量系统进行分析。
一、平均范围法1、打开工作表“测量系统分析.xls”。
组织数据,使每行包含样本名称、运算符和测量值,如图所示3-1显示。
MSA测量系统分析实战案例分享
沟通不畅
分析结果涉及专业术语和复杂数据,与非专业 人员沟通存在障碍。
结果应用不足
分析结果未得到充分应用,未能有效指导实践。
结果解读与沟通
解决方案
01
02
加强与业务人员的沟通 ,将专业术语转化为易 于理解的语言。
03
04
采用先进的数据可视化 工具,提高结果呈现效 果。
建立结果应用机制,确 保分析结果在实践中发 挥作用。
指定专业的测量人员,确保测量的准确性和一致性。
制定测量方案
明确测量的对象、方法、步骤和注意事项等,形成详细的测量方案 。
收集数据
进行实际测量
按照测量方案进行实际测量,并记录详细的测量数据。
数据整理
对收集到的数据进行整理,包括数据清洗、分类和汇总等。
进行分析
数据可视化
01
利用图表等方式将数据可视化,以便更直观地观察数据的分布
和规律。
统计分析
02
运用统计方法对数据进行深入分析,如描述性统计、方差分析
、回归分析等。
判断测量系统稳定性
03
通过数据分析判断测量系统的稳定性,如重复性和再现性等。
制定改进措施
识别问题
根据分析结果识别存在的 问题,如测量误差、设备 故障、操作不当等。
制定改进方案
针对存在的问题制定相应 的改进方案,如更换设备 、优化操作流程、提高人 员技能等。
实战案例二:某电子企业MSA测量系统 分析
案例背景
企业情况
某大型电子制造企业,专注于电 子元器件的生产和质量控制。
问题描述
企业在生产过程中,发现某些元 器件的测量数据存在波动,影响
了产品质量的稳定性。
分析目的
- 1、下载文档前请自行甄别文档内容的完整性,平台不提供额外的编辑、内容补充、找答案等附加服务。
- 2、"仅部分预览"的文档,不可在线预览部分如存在完整性等问题,可反馈申请退款(可完整预览的文档不适用该条件!)。
- 3、如文档侵犯您的权益,请联系客服反馈,我们会尽快为您处理(人工客服工作时间:9:00-18:30)。
测量系统分析案例
编制:史爱萍
测量系统分析案例
以我公司火炮主要部件“身管硬度检测程序”为例说明。
身管硬度检测程序:
1、物资部门检验人员根据外购器材复验收规范填写 “力学性能试验请
求单”,由物资部门按“力学性能试验请求单”试验项目要求取试
验“样品”,并附 “样品”交理化试验室试验人员。
2 、理化试验人员收到“力学性能试验请求单”及“样品”后,根
据“力学性能试验请求单”进行登记编号,并对样品进行标识。
3 、硬度试验(依据GB/T231.1布氏硬度试验方法进行) 3.1准备工作
3.1.1准备好原始记录;
3.1.2检查样品名称、材料、数量等是否符合;
3.1.3根据样品大小、形状选择工作台;
3.1.4打磨样品表面,使其表面粗糙度达Ra不大于1.6um;
3.2硬度试验程序
3.2.1应使用有效期内的标准硬度块进行检查,检查合格后方可进行以
下试验工作;
3.2.2将样品稳固地放在布氏硬度计工作台上,按GB/T231.1布氏硬度试验方法第7条试验程序进行试验,并作好相应的硬度原始记录。
3.3试验完毕,及时填写“力学性能试验报告单”,经另一试验人员审核后交理化室主任盖章,并通知物资部门领取“力学性能试验报告单”。
4、物资部门领取“力学性能试验报告单”后交检验,检验人员依据
YB475-93“火炮炮身零件用钢”第 3.1.3条硬度进行判断,作出硬度是否合格的结论。
测量系统分析案例
编制:史爱萍
测量系统分析案例
以五分厂洛氏硬度计(HRC-150A NO:118)周期检定为例说明。
洛氏硬度计周期检定程序:(参照JJG112-2003金属洛氏硬度计检定规程及硬度计说明书)
1、外观检查
1.1硬度计应有铭牌,标明制造厂名称、型号、出厂编号等。
1.2硬度计的主轴、加力杠杆、升降丝杠、缓冲机构、压痕深度测量装置等均应正常灵活地工作;丝杠无晃动;试验力无冲击。
1.3试台应稳固地安装在丝杠上,试台台面应光滑平整。
2、硬度计示值检定
2.1硬度计应针对其被使用的每一个标尺进行检定。
2.2根据硬度标尺,选取相应的总试验力和装上相应的压头。
2.3检定时,主试验力施加时间4~8s,总试验力保持时间(5±1)s;主试验力在(2~3)s内平稳卸除。
2.4检定时,标准硬度块贴合试台台面移动。
在标准硬度块的工作面上测定六点,第一点不计,其余五点均匀分布。
两相邻压痕中心间距离应不小于压痕直径的4倍,但至少为2mm。
压痕中心至硬度块边缘的距离应不小于压痕直径的2.5倍,但至少为1mm。
所测五点硬度的平均值与标准块硬度值之差为硬度计的示值误差,五点中最大值与最小值之差为硬度计的示值重复性。
做好相应的硬度计原始记录,检定结果应符合
JJG112-2003金属洛氏硬度计检定规程表3硬度计示值最大允许误差及示值重复性中的要求。
3、遇到以下情况者,测量结果无效
3.1试验过程中,硬度块产生位移;
3.2试验过程中受试验力作用时,受到外来冲击影响;
3.3试验记录有误;
4、检定结果的处理及检定周期
4.1检定合格的硬度计发检定证书(签字手续齐全),不符合的贴禁用标识。
4.2硬度计的检定周期:一年
测量系统分析案例
编制:史爱萍
测量系统分析案例
以我公司火炮主要部件“身管力学性能检测程序”为例说明。
身管硬度检测程序:
1、物资部门检验人员根据外购器材复验收规范填写 “力学性能试验请
求单”,由物资部门按“力学性能试验请求单”试验项目要求取试
验“样品”,并附 “样品”交理化室。
2、理化室根据力学性能试验请求单试验项目按排加工试样,加工好打
上编号后送力学性能试验。
2 、理化力学试验人员收到“力学性能试验请求单”及“样品”后,根
据“力学性能试验请求单”进行登记编号,并对样品进行标识。
3 、力学性能试验(依据GB/T228拉伸试验方法进行) 3.1准备工作
3.1.1准备好原始记录;
3.1.2检查样品名称、材料、数量等是否符合,测量试样尺寸,并计算其横断面积;
3.1.3根据样品大小、选择相应的辅具;
3.2拉伸试验程序
3.2.1正确使用夹具装入试样,并保证试样轴向受力;
3.2.2确定拉伸速度;
3.2.3正确记录各类试验数据及进行各关计算其检测结果表示符合标准要求;
3.3试验完毕,及时填写“力学性能试验报告单”,经另一试验人员审核后交理化室主任盖章,并通知物资部门领取“力学性能试验报告单”。
4、物资部门领取“力学性能试验报告单”后交检验,检验人员依据
YB475-93“火炮炮身零件用钢”第 3.2.1条表3力学性能数据进行判断,作出力学性能是否合格的结论。
测量系统分析案例
编制:史爱萍
测量系统分析案例
以五分厂洛氏硬度计(HRC-150A NO:118)周期检定为例说明。
洛氏硬度计周期检定程序:(参照JJG112-2003金属洛氏硬度计检定规程及硬度计说明书)
1、外观检查
1.1硬度计应有铭牌,标明制造厂名称、型号、出厂编号等。
1.2硬度计的主轴、加力杠杆、升降丝杠、缓冲机构、压痕深度测量装置等均应正常灵活地工作;丝杠无晃动;试验力无冲击。
1.3试台应稳固地安装在丝杠上,试台台面应光滑平整。
2、硬度计示值检定
2.1硬度计应针对其被使用的每一个标尺进行检定。
2.2根据硬度标尺,选取相应的总试验力和装上相应的压头。
2.3检定时,主试验力施加时间4~8s,总试验力保持时间(5±1)s;主试验力在(2~3)s内平稳卸除。
2.4检定时,标准硬度块贴合试台台面移动。
在标准硬度块的工作面上测定六点,第一点不计,其余五点均匀分布。
两相邻压痕中心间距离应不小于压痕直径的4倍,但至少为2mm。
压痕中心至硬度块边缘的距离应不小于压痕直径的2.5倍,但至少为1mm。
所测五点硬度的平均值与标准块硬度值之差为硬度计的示值误差,五点中最大值与最小值之差为硬度计的示值重复性。
做好相应的硬度计原始记录,检定结果应符合
JJG112-2003金属洛氏硬度计检定规程表3硬度计示值最大允许误差及示值重复性中的要求。
3、遇到以下情况者,测量结果无效
3.1试验过程中,硬度块产生位移;
3.2试验过程中受试验力作用时,受到外来冲击影响;
3.3试验记录有误;
4、检定结果的处理及检定周期
4.1检定合格的硬度计发检定证书(签字手续齐全),不符合的贴禁用
标识。
4.2硬度计的检定周期:一年。