减速机轴断裂分析
浅述减速机高速齿轮轴断裂失效及处理

浅述减速机高速齿轮轴断裂失效及处理摘要:减速机是现代企业生产过程中用途比较大的一种机械设备,如果发生故障付给企业生产带来严重损失。
某企业在生产过程中减速机高速齿轮轴出现了断裂现象,针对这一问题相关技术人员进行了专业的检测与分析后,确定了故障原因,进而制定了相应的解决处理措施,恢复了减速机的性能。
关键词:减速机;高速齿轮;断裂;检测;故障某生产企业所用减速机高速轴突然产生早期断裂现象,通过现场查看可知,电机和减速机间的耦合器均已完全脱离,且壳体破碎,其它和这一高速轴一同参与运转的齿轮轴,均在事故产生之后发生不同程度的弯曲变形。
此高速轴属于典型的齿轮轴,发生断裂后齿面依然保持完好,未发生变形与断齿。
现围绕这一减速机高速轴实际情况,对其断裂失效作如下深入分析。
1对高速齿轮轴断裂情况进行检测1.1减速机高速齿轮的基础资料基础资料的收集是进行减速机高速齿轮轴断裂检测工作的重要基础,对后续检测工作的正常开展,以及得到准确的检测结果均有重要作用和意义,应引起相关人员的重视。
此次研究的主要对象为3C710NE型减速机,其速比、输入功率和输入转速分别为1:2.034、710kW和741r/min。
根据生产单位提交的相关工艺图纸,其硬度需要达到59-62HRC的要求[1]。
1.2对齿轮成分的检测对于该减速机,其高速齿轮轴以17CrNiMo6钢为主要原材料,在取样后,用光谱测定仪与碳硫仪进行成分含量测定,测定结果为:碳含量0.18%、锰含量0.57%、硅含量0.27%、磷含量0.011%、硫含量0.003%、铬含量1.73%、镍含量1.55%、钼含量0.28%。
通过对相关资料的查证可知,该原材料为德国牌号,成分方面的技术要求为:碳含量在0.15~0.19%范围内、锰含量在0.40~0.60%范围内、硅含量在0.15~0.40%范围内、磷含量不得小于0.025%、硫含量不得小于0.025%、铬含量在1.50~1.80%范围内、镍含量在1.40~1.70%范围内、钼含量在0.25~0.35%范围内。
图解减速机高速轴断裂的5个原因分析及7个预防措施

图解减速机高速轴断裂的5个原因分析及7个预防措施在生产实践经验得知,硬齿面减速机高速轴很容易发生断裂,如某国外减速机的高速轴经常在两处发生断裂:图1 减速机高速轴断裂实例一处在联轴器同高速轴的配合端面部位:图2 断轴A另一处在轴承同轴的配合端面部位:图3 断轴B1. 减速机高速轴断裂原因图4 断轴A的断口这是高速轴断裂的A断口形貌,从图中可以看到疲劳源位于键槽底部的尖角处。
断口具有疲劳源区、疲劳扩展区和静断区,高速轴是典型的疲劳断裂。
图5 断轴B的断口这是高速轴断裂的B断口形貌,这也是一个疲劳断裂断口,静断区很小,说明轴中的名义应力并不大。
断裂轴的断口特征:•断口是疲劳断口,轴是疲劳断裂。
•轴的断裂部位大部分正好位于联轴器与轴过盈配合的边缘处。
•最早的疲劳裂纹大都发生在平键键槽的尖角处或过渡圆角处。
•轴的断口垂直于轴的轴线,基本上是一种高强度钢弯曲扭转型断口。
正常情况下,减速机高速轴通常仅承受转矩作用。
对以往多次断轴案例进行疲劳强度计算结果表明,疲劳强度安全系数通常可达2以上,高速轴应该是安全的,轴不可能断裂。
经检查轴的材料、热处理质量也都符合技术要求。
但是,高速轴还是经常断裂,可以说是减速机的多发病了!原因一:键槽的应力集中观察很多带键槽的断轴断口,可以看到最早的疲劳裂纹往往发生在平键键槽尖角处,很明显键槽的应力集中和轴的截面面积减小影响了轴的强度。
特别是键槽底部的圆角r(图6)对应力集中的影响很大。
图中所示是某矿用减速机高速轴的键槽,键槽底部的圆角r就很小,加大了键槽的应力集中。
图6 带键槽的断轴断口轴受纯扭转时,键槽和配合边缘处的有效应力集中系数Kτ见图7所示。
当轴的抗拉强度Rm=900MPa时,键槽的有效应力集中系数Kτ=2。
因此键槽对轴的削弱是很大的。
图7 过盈连接的应力集中和接触应力分布原因二:联轴器同轴的过盈配合当轴断裂部位正好是联轴器同轴过盈配合的边缘处,过盈配合对轴的强度影响很大。
减速机输入轴断裂失效分析
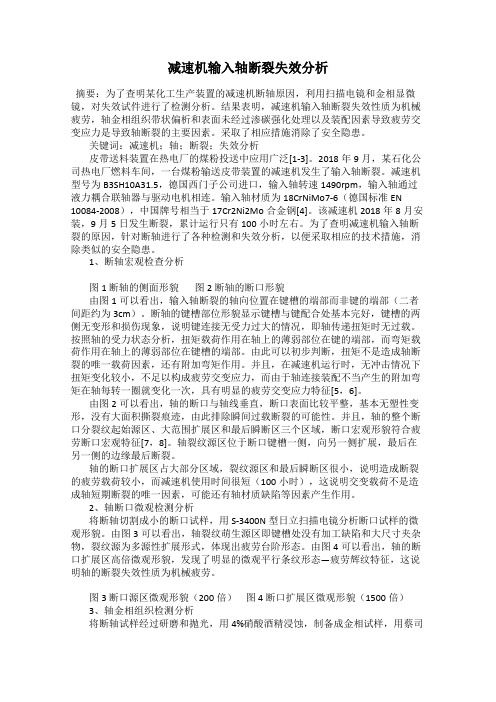
减速机输入轴断裂失效分析摘要:为了查明某化工生产装置的减速机断轴原因,利用扫描电镜和金相显微镜,对失效试件进行了检测分析。
结果表明,减速机输入轴断裂失效性质为机械疲劳,轴金相组织带状偏析和表面未经过渗碳强化处理以及装配因素导致疲劳交变应力是导致轴断裂的主要因素。
采取了相应措施消除了安全隐患。
关键词:减速机;轴;断裂;失效分析皮带送料装置在热电厂的煤粉投送中应用广泛[1-3]。
2018年9月,某石化公司热电厂燃料车间,一台煤粉输送皮带装置的减速机发生了输入轴断裂。
减速机型号为B3SH10A31.5,德国西门子公司进口,输入轴转速1490rpm,输入轴通过液力耦合联轴器与驱动电机相连。
输入轴材质为18CrNiMo7-6(德国标准EN 10084-2008),中国牌号相当于17Cr2Ni2Mo合金钢[4]。
该减速机2018年8月安装,9月5日发生断裂,累计运行只有100小时左右。
为了查明减速机输入轴断裂的原因,针对断轴进行了各种检测和失效分析,以便采取相应的技术措施,消除类似的安全隐患。
1、断轴宏观检查分析图1 断轴的侧面形貌图2 断轴的断口形貌由图1可以看出,输入轴断裂的轴向位置在键槽的端部而非键的端部(二者间距约为3cm)。
断轴的键槽部位形貌显示键槽与键配合处基本完好,键槽的两侧无变形和损伤现象,说明键连接无受力过大的情况,即轴传递扭矩时无过载。
按照轴的受力状态分析,扭矩载荷作用在轴上的薄弱部位在键的端部,而弯矩载荷作用在轴上的薄弱部位在键槽的端部。
由此可以初步判断,扭矩不是造成轴断裂的唯一载荷因素,还有附加弯矩作用。
并且,在减速机运行时,无冲击情况下扭矩变化较小,不足以构成疲劳交变应力,而由于轴连接装配不当产生的附加弯矩在轴每转一圈就变化一次,具有明显的疲劳交变应力特征[5,6]。
由图2可以看出,轴的断口与轴线垂直,断口表面比较平整,基本无塑性变形,没有大面积撕裂痕迹,由此排除瞬间过载断裂的可能性。
减速机齿轮断裂原因分析
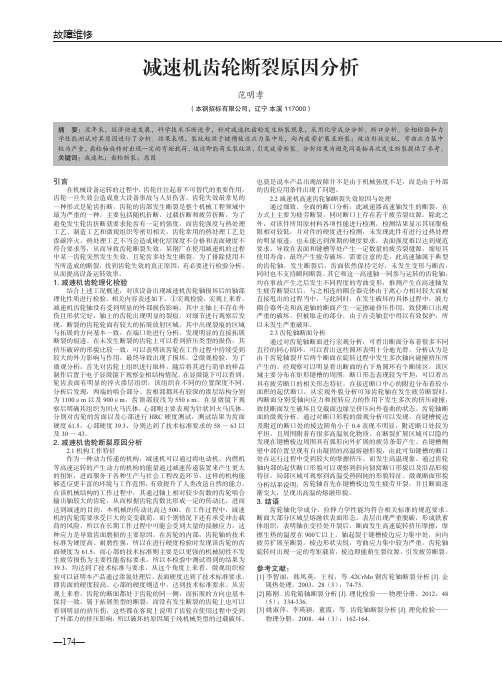
故障维修减速机齿轮断裂原因分析范明孝(本钢招标有限公司,辽宁 本溪 117000)摘 要:近年来,经济快速发展,科学技术不断进步,针对减速机齿轮发生断裂现象,采用化学成分分析、断口分析、金相检验和力学性能测试对其原因进行了分析。
结果表明,裂纹起源于键槽棱边应力集中处,向内疲劳扩展至断裂;棱边形状尖锐,弯曲应力集中较为严重,齿轮轴旋转时出现一定的弯矩载荷,棱边即能萌生裂纹源,引发疲劳断裂。
分析结果为避免同类轴再次发生断裂提供了参考。
关键词:减速机;齿轮断裂;原因引言在机械设备运转的过程中,齿轮往往起着不可替代的重要作用,齿轮一旦失效会造成重大设备事故与人员伤害。
齿轮失效最常见的一种形式是轮齿折断,齿轮的齿部发生断裂是整个机械工程领域中最为严重的一种,主要包括随机折断、过载折断和疲劳折断,为了避免发生轮齿折断就要求轮齿有一定的强度,而齿轮强度与热处理工艺、制造工艺和微观组织等密切相关,齿轮常用的热处理工艺是渗碳淬火,热处理工艺不当会造成硬化层深度不合格和表面硬度不符合要求等,从而导致齿轮断裂失效。
某钢厂在使用减速机的过程中某一齿轮突然发生失效,且轮齿多处发生断裂。
为了排除使用不当所造成的断裂,找到齿轮失效的真正原因,有必要进行检验分析,从而提高设备运转效率。
1.减速机齿轮理化检验结合上述工况概述,对该设备出现减速机齿轮轴损坏后的轴部理化性质进行检验,相关内容表述如下。
①宏观检验,宏观上来看,减速机齿轮轴没有受到明显的外部损伤影响,其中主轴上不存在外伤且形状完好,轴上的齿轮出现明显的裂痕。
对细节进行观察后发现,断裂的齿轮轮面有较大的拓展放射区域,其中出现裂痕的区域与拓展的方向基本一致,在端口处进行分析,发现明显的直接拓展断裂的痕迹。
在未发生断裂的齿轮上可以看到挤压类型的损伤,其挤压破碎的形貌比较一致,可以表明该齿轮在工作过程中持续受到较大的外力影响与作用,最终导致出现了损坏。
②微观检验,为了微观分析,首先对齿轮上组织进行取样,随后将其进行简单的样品制作后置于电子显微镜下观察金相结构情况。
断轴关键在分析原因

断轴关键在分析原因减速机高速轴断裂是一种经常会出现的严重事故,导致的原因也有多种,或者是由几种因素共同导致的结果。
常见的原因有如下几种:1.耦合器选型偏大,减速机选型偏小,使得减速机高速轴承担的径向荷载较大;2.耦合器平衡有问题,在高速旋转时给减速机和电机轴施加了较大的交变附加荷载;3.减速机高速轴轴材质、热处理的问题-存在内应力或裂纹;4.驱动单元组装或运输过程中甚至是驱动装置底座基础不平焊接后使底座变形导致电机轴和减速机轴的同心度超差;5.设备使用过程中的野蛮操作和维护不到位也可能造成设备的损坏......因此,仅从减速机高速轴断裂的表面现象还不能准确的判断原因所在,需根据实际情况进行分析:1.根据胶带机的参数校核部件的选型:胶带机轴功率、电机功率、电机转速-看耦合器规格、减速机额定功率和使用系数等参数,检验部件选型是否正确;2.了解胶带机工作过程中的噪音、震动、设备温升等情况,看是否存在耦合器平衡问题、电机轴和减速机轴不同心等问题;3.可以从中控室调取该胶带机的电流记录,反算胶带机的实际消耗功率,看是否存在严重超载或其它原因导致的减速机服务系数不够的情况;4.查看安装调试记录或安装指导书,看该耦合器内所加液体量是否过多,导致启动曲线过硬同时增加了减速机轴的径向荷载。
关于驱动单元的一点建议:1.设备部件规格并非越大越有利,尤其是耦合器的规格常参考电机功率,目前好多设计院在计算胶带机功率时的系数选择很保守,导致耦合器规格偏大;2.目前SEW、FLENDER公司的竞争也非常激烈,所以在设备选型时的服务系数裕度不大,尤其是电厂胶带机的工作条件相对较好的情况下,其服务系数更小,导致高速轴很细;3.耦合器作为传递扭矩的联轴器,其重心靠近减速机侧,这对难以承受径向力的减速机高速轴不利(部分厂家采取将耦合器反装的方法来改善该矛盾,但会破坏耦合器的功率传递曲线,使耦合器充油量与传递功率偏离说明书给出的曲线);4.胶带机安装调试说明书和运行维护手册中应强调指出:严格控制每条胶带机耦合器的充油量,并根据功率曲线给出具体数值,保证胶带机启动曲线的平滑同时控制轴端的径向荷载;5.电机轴可承受径向荷载,减速机高速轴一般不承担径向荷载,所以电机轴的直径要比减速机轴颈粗,再加上进口材料的性能较好,使得减速机高速轴的直径更细,因此在与减速机厂家签订技术协议时一定要明确:耦合器的重量由减速机和电机共同承担,以避免断轴事故发生时减速机厂家推诿责任(实际上减速机不承担耦合器重量是无法实现的,目前耦合器的正确安装方发就是将重型靠近减速机侧);6.减速机的具体选型型规格建议由减速机厂家来确定,胶带机厂家要提供正确的轴功率、电机功率、速比等选型所必须的参数,以引起减速机厂家在选型时的重视程度-避免因竞争激烈,人为降低设备规格的情况发生;7.在设备安装调试结束后,转交业主和培训的过程中一定明确设备的正常使用要求,严禁超载并进行正常的维护和巡检,从使用和维护的角度避免断轴等恶性事故的发生-设备是否正常只有使用者才最清楚!这个问题已经讨论了一年多了,大家还在关心和热议。
减速机高速齿轮轴断裂失效分析

减速机高速齿轮轴断裂失效分析摘要:本文通过分析减速机高速轴位置的断口的宏观上的特性,及表面的金相组织,化学成分以及硬度等方面的物理性质加以观察和分析,同时进行相关的测试。
由实验所得数据结果显示出,减速机的高速轴并未按照图纸上的要求选用42crmo钢;在使用之前也没有按照所规定的进行调制处理。
由于键槽并未按照规定的位置设计以及原材料组织上的缺陷导致其发生早期断裂现象而导致最终失效。
关键词:高速轴;魏氏体组织;;断裂;失效中图分类号:tg115 文献标识码:a 文章编号:1674-7712 (2013)02-0151-01在某工厂二辊压机构中的减速机高速轴上线运行13天后出现了断裂的现象。
在之前给出的图纸样例中提到了,这个轴的制造图纸上对于原材料的要求是42crmo锻钢,硬度为270~300hb,调质热处理。
同时还要对端口位置的宏观上的形态,金相组织,物理性质如硬度以及化学成分等进行相应的观察和测试,进而为今后这类轴零件的生产量的提升,以及在具体应用时候的使用提供有效的理论参考。
进而防止断裂一类的事件发生。
一、对于检测结果的分析和研究(一)端口宏观相貌的观察结果。
轴同轴间的过渡和链接的位置是减速机高速轴发生断裂的最主要的地方。
此处直径大小发生突变,最为关键的是这是轴的直径最小的地方。
结构圆角的常见现象由于截面形状的变化以及轴间和轴的相交位置的几何关系处于垂直的状态而导致必将会出现的应力集中现象。
端口经常见到的形貌特点便是具有很高的脆性以及较为平整,例如一种极为常见的是扭转应力所导致的断裂口。
只有受力的地方才是裂纹出现的根源,及轴键槽的受力的一面。
应力的大小和半径的大小呈现反比的关系,也就是说半径较小的地方应力则很大。
半径最小的便是轴键槽的根部位置,在此处经常出现应力集中地现象从而承受很大的拉应力;如果不进行强化处理就会提高出现裂纹(这种裂纹是由于疲劳产生的),对于轴类具有很强的破坏性,出现提前失效,很大程度上减少了其寿命。
煤磨主减速机高速轴断裂的分析和处理

煤磨主减速机高速轴断裂的分析和处理摘要:我国经济水平和我国煤矿行业的快速发展,煤矿产业中常见的皮带运输机在实际使用时会发生故障,如减速机输入轴断裂,这种故障是煤矿用皮带机故障中最常见也是最严重的故障,对煤矿开采人员的生命安全有严重影响。
在煤矿作业时,导致减速机断轴的因素较多,为此,需结合煤矿设施情况与皮带机的应用实践,进行断轴原因的分析,并采取改进措施,降低减速机断轴问题的发生几率。
关键词:减速机;高速轴;断裂;过盈对接引言减速机是一种由封闭在刚性壳体内的蜗杆传动、齿轮传动、齿轮-蜗杆传动所组成的独立部件。
减速机是一种相对精密的机械,常作为原动件与工作机之间的减速传动装置。
一般说来,减速机在原动机和工作机或执行机构之间起匹配转速和传递转矩的作用,使用它可以降低转速,增加转矩。
按照传动的布置形式又可分为展开式、分流式和同进轴式减速机;按照传动级数不同可分为单级和多级减速机;按照齿厂轮形状可分为圆柱齿轮减速机、圆锥齿轮减速机和圆锥-圆柱齿引轮减速机。
1减速机概述减速机是煤矿生产中最重要的设备,从某种程度上来说,减速机的运行状况直接影响着煤矿生产的稳定性与安全性,如果减速机运行中出现各种故障或者其他问题,将直接影响着煤矿生产的运行状况,进而威胁着人们的生命财产安全。
具体来说,减速机指的是一种以多种形式的将能源转化成电能的机械设备,在当前社会中,减速机被广泛应用到各个行业中,比如农业生产建设、国防、科技以及日常生活中。
减速机的内部结构十分复杂,主要是由原动机、压缩机机以及其他动力机械驱动组成的,其工作原理主要是根据电磁力和电力感应定理,借助对空气施加压力来提升气体的运行速度,并且通过导电材料和电磁感应进行电路和磁路的相互交换,以此达到能源转换,满足不同领域的需求。
伴随着空气动力学研究的不断深化以及科学技术的不断发展,减速机的应用范围进一步扩大,减速机能够将气体沿着一定方向流向叶轮的压缩机当中,总之,减速机是一种转换能量与压力的一种机械设备,因此,探究减速机的断齿原因以及检修管理具有现实意义。
起重机减速机齿轮轴断裂原因分析及改进措施探讨

起重机减速机齿轮轴断裂原因分析及改进措施探讨摘要:起重机在钢铁等冶炼行业中有着十分重要的应用,而减速机作为起重机中非常关键的设备,对整个起重机的使用性能有直接的影响。
起重机的主起升减速机在实际使用的过程中,会出现减速机齿轮轴断裂的情况,从而导致起重机的主钩会出现溜钩的事故,严重威胁现场作业安全。
针对这种情况,本文对起重机减速机齿轮轴的材质、力学性能以及制造安装精度等多个方面多齿轮轴断裂的原因进行分析,明确具体原因,在此基础上提出改进措施,避免起重机减速机齿轮轴出现断裂的情况,从而保证作业现场的安全。
关键词:起重机减速机;齿轮轴断裂;原因;改进措施0引言在起重机中,减速机是传递扭矩非常重要的部件,其各级齿轮轴在实际工作的过程中,会受到起重机制动时产生的冲击载荷作用以及正常运行时的扭转力作用。
在这两种力的作用下,会对减速机运行的性能产生影响,而为了保证起重机能够安全稳定的运行,必须确保各个零部件的可靠性。
本文以某型起重机为例,其主升减速机在运行过程中出现高速齿轮轴断裂的情况,导致起重机的主钩出现溜钩事故。
该型起重机的额定载重为90t,跨距为22m,主减速机齿轮传动比为50,输入轴的最小直径为70mm,齿轮轴使用的材料为42CrMo。
为了避免起重机在后续使用的过程中出现重大的安全事故,本文以此为分析案例,对起重机中减速机高速齿轮轴断裂的原因从多个角度进行分析,明确具体的原因,制定相应的改进措施,从而保证起重机的使用安全。
1断裂情况减速机齿轮轴断裂的具体情况如图1所示,根据实际情况,发现断裂的位置是在轴径70mm与轴径85mm之间的台阶处,通过观察发现齿轮轴此处的台阶没有明显的圆角,并且加工质量较为粗糙。
在高速轴油封的位置发现多条因摩擦而产生的光带。
整个端面呈暗灰色并且垂直于主轴线。
在断面的起始区域存在较多的小台阶,台阶处没有较为明显的圆角,在接近表面的部位存在摩擦挤压过的痕迹,并且有多个裂源,导致出现多源疲劳特征。
- 1、下载文档前请自行甄别文档内容的完整性,平台不提供额外的编辑、内容补充、找答案等附加服务。
- 2、"仅部分预览"的文档,不可在线预览部分如存在完整性等问题,可反馈申请退款(可完整预览的文档不适用该条件!)。
- 3、如文档侵犯您的权益,请联系客服反馈,我们会尽快为您处理(人工客服工作时间:9:00-18:30)。
减速机轴断裂分析
董毅,李晓玲,刘臻祥,周玉英
(内蒙古北方重工业集团有限公司,包头014033)
摘要:某减速机使用30多小时后,齿轮减速机轴发生弯曲,该轴在进行冷校直时发生断裂。
通过对断裂轴的断口宏微观分析、金相检验以及硬度测定,认为该轴是在应力集中条件下承受对称旋转弯曲载荷作用,产生早期疲劳断裂。
造成疲劳断裂的原因是由于热处理工艺不合理,致使材料力学性能未达到设计要求,导致轴的疲劳抗力降低,加之圆角加工较差,工作时产生应力集中,加速了轴的疲劳断裂。
关键词:减速机;轴;疲劳断裂;退刀槽
某煤矿从国外购进的减速机,安装使用30h余后,齿轮减速机轴发生弯曲,无法正常使用,在对弯曲的减速机轴进行冷校直时,轴突然发生断裂。
查阅减速机轴的有关技术资料,该轴采用17CrNiMo6钢制造,轴整体经调质处理后,表面进行中频处理,使轴表面及退刀槽根部洛氏硬度达到59~62HRC。
1 理化检验
1.1 断轴宏观分析
断裂位于减速机轴表面退刀槽根部,见图1。
图1 轴断裂位置(mm) 图2 宏观断口形貌
宏观断口见图2,断口表面有较明显的贝壳状花样,属于典型的疲劳断裂。
断口由疲劳裂源区、裂纹扩展区和瞬间断裂区三个区域组成。
仔细观察断口裂纹源区,其表面较平坦,尺寸在距表面5mm范围内(图2A处)。
裂纹扩展区贝纹线比较扁平。
瞬间断裂区在裂源的对面,呈椭圆形,断口形貌为纤维状,表明减速机轴主要受旋转弯曲应力。
断口瞬断区域较小、较圆约占整个断口面积的1/6,说明轴整体受力较小,属典型的高周疲劳断裂。
由疲劳区及贝纹线的形态可知,疲劳裂纹扩展过程中两侧较快,说明退刀槽根部有应力集中现象。
1.2 断口微观分析
用AMRAY21000B型扫描电镜观察样品断口,断裂起源于轴表面退刀槽根部,该处有机加工刀痕,见图3;裂纹扩展区可见疲劳条纹,见图4;瞬断区为细小韧窝。
图3 断裂源形貌200×图4 裂
纹扩展区疲劳条纹400×
1.3 化学成分分析
化学成分分析试样取自断口附近,分析结果(质量分数)列于表1,化学成分符合技术要求。
1.4 洛氏硬度检测
在断口附近取样,将横截面磨平,从边缘向心部逐点进行硬度测定,结果均在36~37HRC范围内;沿轴的纵向表面测定硬度,结果在38~39HRC范围内。
从硬度结果看出,轴的表面硬度与心部硬度相近,且均低于设计要求。
1.5 金相检验
在裂源附近取样进行金相分析,非金属夹杂物为A2,B1,D1e(按GB10561-1989评定);晶粒度7.5级(按GB6394-1986评定);疲劳源区及表面与心部显微组织均为回火索氏体,见图5。
图5 疲劳源区显微组织500×
通过金相组织分析,认为该轴是在调质热处理状态下,未经任何表面处理直接投入使用的。
2 分析与讨论
(1)减速机轴纵向表面与轴横端面的洛氏硬度检测结果表明,失效轴硬度值在36~39HRC,远低于技术要求的59~62HRC,显然与设计要求不符。
(2)该轴从表面至心部的组织为回火索氏体,说明该轴是在调质热处理状态下使用的,这与所测得轴的洛氏硬度相吻合。
轴的工作状态要求其表面硬度较高、耐磨,心部硬度相对较低,韧性较好。
通常情况,轴表面一般经高频或中频处理后才使用[1],而失效轴的调质使用状态与理论要求的高频或中频表面处理使用状态不相符,由于工艺上的不合理,造成轴的疲劳抗力降低。
(3)从减速机轴断裂的位置看,疲劳起源于轴的退刀槽应力集中处。
从微观断口看,有明显的三个区域即裂纹源区、扩展区和瞬断区,属典型的疲劳断裂。
断口贝纹线比较扁平,裂纹扩展前沿线两侧的裂纹扩展速度较大,瞬断区在裂纹源的对面,由此可见,失效轴主要受旋转弯曲应力。
而从瞬断区较小较圆看,失效轴整体受力较小[2]。
根据上述断口分析结果及断裂形貌,认为轴断裂属中等名义应力集中条件的旋转弯曲产生的疲劳断裂。
轴在承受旋转弯曲应力的作用下,由于轴的表面硬度较低,加上退刀槽应力集中,使轴在正常工作应力下在退刀槽处过早的产生疲劳裂纹,随着循环载荷的作用,疲劳裂纹不断向基体内扩展,致使轴的有效承载尺寸减少,并产生弯曲,当进行冷校直时,对轴的凸起方向施加一定向下的外力时,导致轴的断裂。
3 结论
减速机轴断裂是由于热处理工艺不合理致使材料力学性能低于设计要求,以及退刀槽底部有应力集中存在,造成轴的疲劳强度降低,产生疲劳裂纹和弯曲变形,在校直过程中发生断裂。