[精品]2017年丰田的成本控制剖析
成本控制案例:丰田汽车的成本企划

成本控制案例:丰田汽车的成本企划2009-3-24 14:12中华会计网校【大中小】【打印】【我要纠错】成本企划(target costing或target cost management)是近年来管理会计的研究主题之一。
随着顾客嗜好渐趋多样化、生产技术革新加速,导致产品生命周期日益缩短、竞争日趋激烈等,企业不仅要跟时间赛跑,且须在有限的前置时间(lead time)内开发设计出具高品质、多机能、低成本(价格)等具竞争优势的新产品,方能在战场上占有一席之地。
根据过去经验显示,由于生产设备、方法、技术等生产条件与产品设计式样等在企划设计阶段几乎都已确定,产品成本的大部分(约8成)便随之底定(Clark &Fujimoto、Shields &Young、加登),因此,若待产品设计制造完成后再从事改善,不但可能需花费额外的成本,且降低成本的空间有限,尤其在自动化已趋普及的今日,进入制造阶段后,可改善的空间与成果更是受到限制,如欲大幅降低成本及掌握创造利益的机会,则应在进入制造阶段之前就对成本加以管理控制。
因此,为使设计开发出品质与机能达一定预期水准,且其成本不超过目标成本的新产品,于企划设计阶段进行成本管理的“成本企划”则愈益受到重视。
降低成本,创造利润,综合性管理制度在台湾,大家较耳熟能详的日式管理制度,莫过于以“及时生产”(Just In Time:JIT)制度为代表的丰田式生产管理体系。
然而,实际上在日本国内及欧美各国,日本创始的管理会计制度——“成本企划”所受到的重视并不亚于JIT,近年来更有日益重要的趋势,甚而有超越JIT 的说法;那是因JIT仅为生产阶段之一的生产管理制度,而成本企划则是进入生产阶段前的各阶段降低成本与利润管理的综合性经营管理制度。
在日本,许多知名的大企业,例如:丰田汽车(Toyota)、日产汽车(Nissan)、松下电器(Matsushita)、日立制作所(Hitachi)、东芝(Toshiba)、夏普(Sharp)、佳能(Canon)、卡西欧、村田机械等皆已采用成本企划。
丰田公司成本控制案例研究

丰田公司成本控制案例研究摘要:在竞争激烈的21世纪,市场经济不断地发展和深入,越来越多的人投入到商业经营中,并且逐渐成为社会经济的主力力量。
而企业在激烈的市场竞争中处于不败之地的法宝之一就是成本优势,成本优势进而转换成价格优势,使企业在与竞争对手的相同产品质量条件下降低成本获得更多的市场份额。
成本俨然成为企业生存发展之本,因此企业必须把成本控制作为经营管理的首要任务。
本文以丰田公司为案例研究对象,对该公司的独特的成本控制方法——适时制生产方式进行分析,并就召回事件进行剖析,旨在了解成本控制对企业的重要性及需要吸取的教训。
关键词:成本控制;适时制生产方式;库存1.引言 (2)2.适时制生产方式的发展和核心理念 (3)3.适时制在丰田公司的应用情况 (4)4.均衡化生产与设备装换调整 (5)5.全面质量管理 (6)6.合理化建议与良好协作关系 (7)7.召回事件反映的问题及反思 (7)8.结论 (8)参考文献 (9)在企业的发展中,成本控制处于非常重要的地位。
它不仅是一个财务概念,更是一个战略概念。
企业要想达到理想的成本目标,就必须努力控制成本,减少费用支出,实现科学的成本管理,只有这样才能取得良好的经济效益。
有效的成本控制可以看作是企业在激烈的市场竞争中成功与否的关键因素,成本控制不仅是单纯的降低成本费用,而是要求企业建立一个目标明确、方案可行、措施得当的成本控制计划。
企业只有将成本降低至行业平均水平之下,这个企业才能长久存活下去;但若是企业能够将成本与行业平均水平拉开距离,这时企业才具备了竞争优势。
适时制生产方式作为一种生产库存制度,是为了提高产品生产质量逐步形成的,旨在将原材料的库存量减少到一个生产班次刚好需要的数量。
在这种情况下,库存不存在替代品,生产的产品都要求是合格的。
这一方式对企业成本控制的意义在于:它不仅大幅度降低了企业的库存费用,而且可以提高采购物资的质量。
企业应当建立并不断完善制度,做好采购成本控制的基础工作。
追求完美的管理方式——丰田成本管理的分析

差 。是 导 致 丰 田产 品 的质 量 事故 的 根 本 原 因。
件 的 供 应 商 ,通 过 竟标 方式 降 低采 购 成
本 。供 应链 既稳 定 又 灵 活 ,充分 保 证 采
购成 本维 持 在一 个合理 的较 低水 平 上 。
商 ,日本 丰 田汽 车公 司从 1933年 创 立至
(二 )准 时 生 产 (JIT1方 式
大 野 耐一 等 人 的共 同 努 力 ,综 合 了单 件
避 免 过 量 生 产 ,当生 产 线 生 产 完所 需 的
生 产 和 批 量生 产 的特 点 和 优 点 ,创 造 了
丰 田有 一种 独 特 的成 本 管理 模 式被 零 件 ,或 生 产 产 品 时 发 生 异 常 及质 量缺
一 种 多 品种 、小 批 量 混 合 生产 条 件 下 高 称 为 成本 企 划 。成 本 企划是 基 于 目标 成 陷 ,机 器会 自动 停 止工 作 ,从 而 避免 了 过
市 场 需 求 多样 化 的新 阶 段 ,制 造 业 对 质 完美 的管 理 方 式 ,丰 田的 成 本 管 理 方 式 证 准量 、准 时 ,同时 避免 过 量生 产造 成 的
量 的 要 求 越 来 越 高:如 何 有 效 地 组 织 多 的 确 值 得 学 习 ,但 误 区也 值 得 我 们 深 入 成本 和浪 费 。这 不仅 仅 局限 于 丰 田总 装
一 、 丰 田 生 产 方 式 的 由 来
今 ,自有 其 独 特 而 有 效 的 经 营 之 道 ,其
以控 制 成本 为核 心 的 丰 田生 产 理念
一 度 被 视 为 日本 管 理模 式 的典 范 ,至 今 决 定 了丰 田采 用 从市 场 实际 需 求 出发 的
丰田的成本逻辑

丰田的生产方式风靡全球,但它的成本秘密到底是什么?布鲁斯·汉德森是一家美国公司的董事长,他的公司主要生产空调系统和设备控制器,同时也是丰田公司的供应商。
在为丰田公司生产设备的经历中,布鲁斯·汉德森逐渐成为丰田生产方式的拥护者,并写了一本名为《精益企业》的书来进行推广。
在书里,他列出了企业推行丰田生产方式(又称“精益生产”)所面临的困难,其中第一条就是“高层管理者缺乏对精益企业的战略性了解”。
然而,布鲁斯·汉德森穷尽一书,也没有显明而有力的逻辑来说服那些高层管理者。
精益生产,这一丰田公司制胜全球的法宝,虽然广为业界所知晓,而且众多研究者都熟知它的基本目标是降低成本,但管理者们往往会问,成本到底降在哪里?换言之,精益生产的成本效应如何体现?这一问题并未明朗,即使是精益生产的创立者大野耐一也未曾向大家详解背后的真意。
事实上,从管理会计学的角度重新审视精益生产,我们会发现长期以来潜藏的成本秘密,这一秘密足以触动更多的管理者更加深入地了解精益生产,进而加速其推广和普及。
节拍优先精益生产似乎并不是一个规律性的东西,有很多只可意会不可言传的地方。
一个直观的感受是,对生产节拍的控制是丰田公司一个铁的原则。
所谓节拍(tact time),是指将生产时间细化到每一件产品之上。
比如,如果月产量为4000辆车,作业时间为20天,每天两班制工作共16个小时,那么生产节拍即是每辆4.8分钟。
在丰田公司,构筑每辆4.8分钟的持续出货机制比什么都重要。
为保证生产节拍,即使用人海战术,或者加大设备投资,或者在易产生次品的工序准备安全库存也在所不惜,而绝对不会妥协于成本的制约。
如果丰田公司也将成本优先于节拍,恐怕就会变成“普通公司”了。
丰田公司曾在它的一个制造厂制定了发动机的出品时间,早上开始铸铁,晚上就要组装为成型汽车,在院子里能开动起来。
在确保节拍的基础上,大野耐一提出了“不管是生产1辆还是1000辆,单位成本都要一样”这一与传统观点完全相悖的口号。
丰田汽车的物流成本管理

丰田汽车的物流成本管理
丰田汽车是世界上著名的汽车品牌之一,它拥有一套严密的物流体系,能够在全球范围内快速、高效地管理着物流成本。
本文将介绍丰田汽车的物流成本管理,主要从成本控制、仓储物流和运输物流三个方面进行阐述。
一、成本控制
丰田汽车对物流成本进行了严格的管理和控制。
首先,丰田汽车在物流管理上注重自我改进,通过自主研发先进技术和流程管控体系,提高效率,降低成本。
其次,丰田汽车实施物流共享,和国内外的物流企业、流通企业和相关呼吸合作,形成了共赢的合作模式。
最后,丰田汽车实行物流全链条控制,对供应链上的生产、库存、采购和销售环节进行综合管理,全面优化物流成本结构。
二、仓储物流
丰田汽车的仓储物流以减少库存、提高物流效率为主要目标,通过物流中心布局、物流设备配置和物流信息系统等手段实现。
丰田汽车的物流中心强调以人为本,按照人性化的操作流程进行物流管理,避免不必要的人为损耗。
同时,丰田汽车还注重仓储管理的标准化、规范化和信息化,通过流程再造和信息化手段降低管理成本,提高物流效率。
三、运输物流
丰田汽车的运输物流注重绿色物流、舒适物流和智能物流。
丰田汽车的运输物流路线规划合理、车辆配置科学,同时注重车辆的
节能环保和舒适性。
丰田汽车还在车辆智能化方面实施了一系列的技术创新,包括GPS全球定位系统、计算机集成管理系统和车载通信系统等,提高物流智能化水平,从而降低运输成本。
总结起来,丰田汽车的物流成本管理是以成本控制为基础,以仓储物流和运输物流为手段,通过科学规划、前瞻性部署和先进技术,实现物流的高效率、低成本和高品质。
无节制的压缩成本就是陷入困境的丰田模式

无节制的压缩成本就是陷入困境的丰田模式丰田汽车召回事件近日不断扩大,从一开始的8款车型的加速踏板故障,到后来的最新节能型油电混合车的刹车装置故障,直到最近的小型卡车的传动轴故障,令这个国际汽车制造业的巨人备受公众指责,几十年来辛苦形成的高品质形象也倍受打击。
目前虽然丰田的上层已经出面道歉,表示愿意与各方合作,尽快解决其产品质量问题,以期恢复消费者的信心,但一些国际商业研究机构并不认为,这仅仅是一次技术事故而已。
随着越来越多相关信息的披露,甚至很多日本的研究人员都开始怀疑,是否丰田引以为傲的管理模式(The T oyota Way),已经到了需要被大刀阔斧改革的时候。
二次世界大战结束以后,日本的工业界开始全面向美国学习,而最令日本的企业家感兴趣的,是福特的生产方式和统计学方法在质量控制中的应用。
当时急于摆脱困境的丰田公司,派出了大野耐一和新乡重雄全面地学习福特的管理系统,并以此为基础开始构建丰田自己的生产体系。
丰田管理专家的过人之处在于,并没有迷信和照搬福特的管理思想,而是很快发现了其中的优点和缺点,并提出了自己的天才构想。
由于在管理上的杰出贡献和创举,大野耐一至今仍被丰田尊称为 Kamisama,意即“天神”。
JIT(Just-in-Time)就是大野和新乡在1950年代时,通过对福特的管理体制改造后的一大发明,通过这种卓有成效的管理革命,使丰田公司从50年代初期时的步履维艰,得到快速发展,并最终成为世界主要汽车厂商之一。
JIT 的基本含义很简单,就是要消灭一切生产中可能的物质和时间浪费,具体就在于尽可能的减少仓储、生产和运输过程中的浪费,从而大大降低总成本。
其核心理念,就是“在正确的时间、正确的地点,使用正时送达的材料,生产合格的产品,不差分秒”。
这一成本控制的理念后来发展成为着名的“丰田生产系统(TPS)”,于70年代在日本全面推广,并于80年代被美国企业广泛接受并使用。
具体说来,那个时候在丰田的管理人员看来,福特管理体系的一大缺点是把工人视为简单的劳动力而已,并没有把工人的积极性和智慧应用在生产中。
丰田生产方式读后感成本控制的智慧
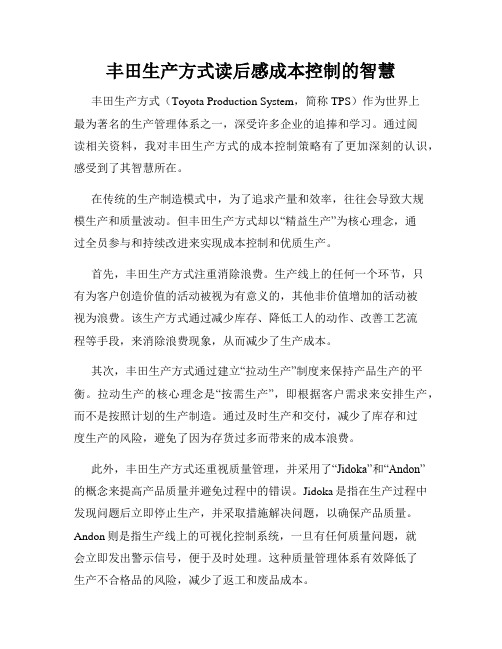
丰田生产方式读后感成本控制的智慧丰田生产方式(Toyota Production System,简称TPS)作为世界上最为著名的生产管理体系之一,深受许多企业的追捧和学习。
通过阅读相关资料,我对丰田生产方式的成本控制策略有了更加深刻的认识,感受到了其智慧所在。
在传统的生产制造模式中,为了追求产量和效率,往往会导致大规模生产和质量波动。
但丰田生产方式却以“精益生产”为核心理念,通过全员参与和持续改进来实现成本控制和优质生产。
首先,丰田生产方式注重消除浪费。
生产线上的任何一个环节,只有为客户创造价值的活动被视为有意义的,其他非价值增加的活动被视为浪费。
该生产方式通过减少库存、降低工人的动作、改善工艺流程等手段,来消除浪费现象,从而减少了生产成本。
其次,丰田生产方式通过建立“拉动生产”制度来保持产品生产的平衡。
拉动生产的核心理念是“按需生产”,即根据客户需求来安排生产,而不是按照计划的生产制造。
通过及时生产和交付,减少了库存和过度生产的风险,避免了因为存货过多而带来的成本浪费。
此外,丰田生产方式还重视质量管理,并采用了“Jidoka”和“Andon”的概念来提高产品质量并避免过程中的错误。
Jidoka是指在生产过程中发现问题后立即停止生产,并采取措施解决问题,以确保产品质量。
Andon则是指生产线上的可视化控制系统,一旦有任何质量问题,就会立即发出警示信号,便于及时处理。
这种质量管理体系有效降低了生产不合格品的风险,减少了返工和废品成本。
此外,丰田生产方式注重人力资源的培养和发展。
它通过培训和培养,使每个工人都具备多项技能,能够灵活地在不同的岗位间工作,实现生产过程的灵活性和高效性。
这样不仅提高了员工的工作满意度和幸福感,还减少了流程中的瓶颈,促进了整个生产效率的提升。
总的来说,丰田生产方式通过消除浪费、建立“拉动生产”制度、注重质量管理和培养员工等措施,实现了成本控制的智慧。
它不仅仅是一种生产管理体系,更是一种智慧的应用与传承。
丰田汽车成本企划实施案例分析

丰田汽车成本企划实施案例分析丰田汽车公司作为全球知名的汽车制造商,其成功的秘诀在于不断改进和创新。
在成本控制方面,丰田汽车公司同样有着一套独特的成本企划实施案例。
本文将对丰田汽车公司成本企划的实施背景、具体案例以及所带来的启示进行分析。
丰田汽车公司的成本企划始于20世纪70年代,当时正值全球石油危机,汽车行业面临着严峻的挑战。
为了应对这一挑战,丰田汽车公司开始着手实施成本企划,旨在降低生产成本、提高产品竞争力。
丰田汽车公司通过对供应链的优化,实现了对原材料采购、零部件制造等环节的成本控制。
具体措施包括:采用招标方式进行原材料采购,以获取更优的价格;对零部件制造进行精细化管理,减少浪费。
这些措施使得丰田汽车公司在供应链环节降低了成本。
丰田汽车公司通过对生产流程进行优化,提高了生产效率,降低了生产成本。
具体措施包括:采用流水线生产方式,减少生产中的浪费;引入机器人等自动化设备,提高生产效率;实施精益生产理念,持续改进生产过程中的问题。
这些措施使得丰田汽车公司在生产环节进一步降低了成本。
丰田汽车公司通过对研发成本进行控制,实现了对新产品开发成本的降低。
具体措施包括:对产品设计进行模块化处理,减少零配件数量;引入计算机辅助设计技术,提高设计效率;对技术研发进行精细化管理,减少不必要的开支。
这些措施使得丰田汽车公司在研发环节降低了成本。
丰田汽车公司的成本企划实施案例为我们提供了以下几点启示:精细化管理是成本控制的关键。
丰田汽车公司在各个环节都实施了精细化管理,从而减少了浪费,提高了效率。
技术创新是降低成本的重要手段。
丰田汽车公司通过引入新技术、新工艺,提高了生产效率,降低了生产成本。
供应链管理是成本控制的重要环节。
丰田汽车公司通过对供应链的优化,降低了原材料采购和零部件制造的成本。
持续改进是降低成本的核心。
丰田汽车公司通过持续改进生产过程中的问题,不断优化生产流程,提高了生产效率。
丰田汽车公司的成本企划实施案例为我们提供了宝贵的经验。
- 1、下载文档前请自行甄别文档内容的完整性,平台不提供额外的编辑、内容补充、找答案等附加服务。
- 2、"仅部分预览"的文档,不可在线预览部分如存在完整性等问题,可反馈申请退款(可完整预览的文档不适用该条件!)。
- 3、如文档侵犯您的权益,请联系客服反馈,我们会尽快为您处理(人工客服工作时间:9:00-18:30)。
《丰田的成本控制剖析》听课笔记关键词:丰田成本控制、精益生产、全面质量控制课前说明:本课主要开拓视野。
丰田的成本控制是多年积累,经历了诸多的坎坷和障碍,日本人发挥执拗精神,逐渐形成的。
一、丰田公司相关背景丰田降成本的新闻:丰田公司2009年12月22日:未来三年把零部件成本削减30%–丰田汽车公司正寻求相应措施,以达到在未来三年把零部件成本削减30%的目标。
–综合外电2009年12月22日报道,丰田汽车公司正加大成本削减力度,对现有车型零部件采购进行评估,并加强了设计技术以提高新车效能。
通过以上措施,丰田希望能够使公司重新回到可持续增长的轨道。
–消息人士透露,丰田在21日的供应商会议上称,仍旧需要供应商的支持,以帮助其达到在未来三年把零部件成本削减30%的目标。
这对于丰田实现最早于下财年恢复盈利的目标至关重要。
2009年,同期其他公司也发布了类似的新闻;因为奥运结束,发生经济危机,次贷等,所有公司都在应对经济危机,日本怎么做呢?内部挖潜的机会不多,将目光面向外面,供应商,能否做到?丰田从历史上积累下来的思路、理念支持他能够做到!丰田对供应商的要求:《金融时报》12月23日报道,全球最大的汽车制造商丰田汽车近日在一次供应商会议上表示,公司期望在2013年推出新车型时,为多种零部件支付的成本将减少30%,此次对供应商的降价要求是公司近期历史上幅度最大的一次。
由于很多供应商都是丰田的子公司,这意味着相当于降价“指令”,希望重获业内利润领袖的地位。
挤压成本长期以来一直是丰田汽车的标志性做法,并在今年加大了力度。
丰田汽车宣布重组集团采购职能,全面精简管理流程,将原先的三个采购部门合并为两个。
仅靠供应商不大可能满足丰田汽车的要求,公司经理们放弃了奖金,就连总部的一些电梯也为了节约电费而被关闭。
丰田的“世界最合理的采购体系”,以选择世界上最有竞争力的供应商、并支持供应商提高竞争力为核心,由以下三个主要方面构成。
1.国际价格比较系统以丰田日本总部为中心运营的价格情报系统。
该系统为支持世界各地的丰田企业顺利实现世界最合理的采购,对在世界各地购入的零部件的成本竞争力进行比较、分析。
对世界各地的丰田企业采购的数万种零部件的价格情报、开发中的零部件、新供应商的报价等情报实行一元化管理,进而深入比较现有供应商与新供应商的成本竞争力。
通过该系统产生的世界最强的成本竞争力为世界各地的丰田企业所共有。
同时,在质量、交货期等方面也采用同样的措施。
2.新供应商、新技术开发工程该工程不是被动地等待、回应供应商的推销,而是主动鼓励和促进有竞争力的新供应商的进入,创造发现新技术的机会和场景。
通过该工程发掘的新供应商情报,全部输入到国际价格比较数据库中。
3.现有供应商的改善支持工程根据“相互信赖、共同繁荣”的基本方针,丰田支持现有供应商的改善工程。
该工程的核心是:在“丰田世界期待值制度”和“国际价格比较系统”所创造的世界最强的成本竞争力的基础上,向供应商提出改善目标即期待值。
供应商据此能够进一步提高竞争力,增加与丰田及其他汽车制造商的交易机会。
丰田所寻求的理想的供应商,既要在质量、价格、交货期、技术等各个方面有着最强的竞争力,又要与丰田拥有共同的理念,那就是“让顾客更满足”、“为创造适宜居住的地球和富裕的社会做贡献”。
即便有“最强的竞争力”,如果不能和丰田共同拥有上述理念,那么,仅仅是丰田的“供应商”,而不能成为丰田的合作伙伴。
提供有竞争力的产品,是实践“让顾客更满足”的理念的途径,而对这一理念的不懈追求,又是创造更有竞争力的产品的推进器。
丰田的历史1、1937年以前–纺织(日本爱知县丰田市)2、1937年以后开始生产汽车,投资1200万日元,年产1800辆。
备注:1908-1927年仅T型车就生产1500万辆,相当于后几年每年100万辆以上。
3、1945年,生产设施毁坏殆尽。
9月份组建小型轿车厂。
之后的若干年,物资极度匮乏政府通货紧缩,贷款及其困难。
1949年年产量月10000量。
1949年丰田经历了历史上唯一一次严重劳资纠纷,员工裁掉1/3,管理层只留丰田喜一郎一人。
经过这场纠纷之后,劳资双方都懂得了一个共同的道理:没有企业的成长发展就没有职工生活的安定;反之,没有职工生活的安定也就没有企业的成长发展。
今天,丰田人把劳资关系看成是汽车两边的轮子,任何一边都不可或缺,正是因为当年曾经有过这样一次痛苦的经历。
而现在丰田所有的企业活动的成功也无不仰仗于建立在相互信任基础上的良好的劳资关系。
4、1950年,访问福特之后,提出把提高生产能力和产品质量作为目标实施技术革新是今后汽车工业发展的关键之所在,并且大胆投资引进最先进的生产设备,使得生产效率有了大幅度的提高,产生了巨大的经济效益。
5、1954年,开始“看板”生产方式。
看板生产方式成为零库存的基础之一。
6、1965年,日本汽车开始普及丰田一方面加紧开发性能更高的新车,同时为增强生产能力、提高质量水平而倾注了极大的努力。
7、1971年,政府废除外资投资日本汽车的限制丰田坚持独立作战8、1973年,石油危机,日本恶性通货膨胀丰田将新的起点瞄准在资源的有限性上,有力地开展了节省资源、节省能源、降低成本的运动。
QC周期活动空前普及,以最少经费争取最佳效果的意识已不仅局限于生产环节,还进一步扩大到了全公司的所有部门。
9、1974年,丰田率先走出低谷经历了这场石油危机之后,丰田深感有必要建立起一个能够迅速对市场变化做出反应的灵活的生产体制。
为此丰田废弃了原有的专用型设备,将其转变成为按车种划分,并能够灵活地随着市场变化而调整的泛用型设备。
10、2007年,飞跃到2007年,丰田产销量超过通用,成为世界第一。
更令人吃惊的是,就在这一年,日本丰田公司的利润,超过美国三大汽车公司福特、通用、克莱斯勒与德国奔驰、宝马利润的总和。
二、与丰田相关的几个重点管理创新:丰田的经验是美国总结出来的,丰田自己并没有总结。
丰田是个苦孩子,穷人孩子早当家,在紧张的环境压迫下,形成了一些独特的方法和理念。
1、TQM——全面质量管理1950年,戴明博士在日本开展质量管理讲座,日本人从中学习到了这种全新的质量管理的思想和方法。
当时,全面质量管理的思路和概念并没有像如今一样被完整地提出来,但是它对日本经济的发展起到了极大的促进作用。
到1970年,质量管理已经逐步渗透到了全日本企业的基层。
1987年标准化后成为ISO9000系列标准。
PDCA是英语Plan(计划)、Do(执行)、Check(检查)、Action(总结、处理)四个词的第一字母的组合。
2、精益生产其中“精”表示精良、精确、精美;“益”表示利益、效益等等。
精益生产就是及时制造,消灭故障,消除一切浪费,向零缺陷、零库存进军。
精益生产的特点是消除一切浪费,追求精益求精和不断改善。
U行生产线,多技能员工…3、JIT生产方式(零库存)准时生产方式基本思想可概括为“在需要的时候,按需要的量生产所需的产品”,也就是通过生产的计划和控制及库存的管理,追求一种无库存,或库存达到最小的生产系统。
4、7大浪费5、看板管理准时生产方式的看板旨在传达信息:“何物,何时,生产多少数量,以何方式生产、搬运”。
是拉式(Pull)生产系统。
6、5S -5S管理指整理、整顿、清扫、清洁和素养(东芝最先推出)——但丰田把他做到了极致,支撑了其他的在一些丰田公司的老厂区,丰田员工们使用的仍然是20 世纪七八十年代的设备,这些设备已经使用了30多年,可就是利用这些面临淘汰的设备,丰田制造出了具有世界品质的产品。
7、目标成本法目标成本——产品出来前就可以有标准成本、定额成本——大致可以等同,在产品出来后有七大浪费:第一种:等待的浪费第二种:搬运的浪费:U型生产线。
(国内生产空间一般都很大,追求喜大普奔,另一方面也是为占地。
)第三种:不良品的浪费:第四种:动作的浪费:如拿出手机看,设计早餐品种控制上厕所。
第五种:过度加工的浪费——如果盘中的雕花,最终一定会向消费者收费的。
第六种:库存的浪费:国内企业很多第七种:过量生产的浪费:国内特有的浪费:用料浪费。
可以总结所在公司的出诸多浪费,这就是提高效率的空间。
怎么提高效率的?日本的新日铁学习丰田,并将方法传到中国,中国宝钢的何桂萍合格品生产时间210天,日本丰田达到75%产能利用率时的合格产品净生产时间274天,巨大的差距。
怎么降低成本的?降完自己的成本,降供应商的成本——跟大哥混,就得跟大哥走。
供应商能否支撑下去,是可以计算出来的:供应商降价,提高销量,仍能保持与往年一样的利润。
丰田如何提高采购量——减少供应商的数量。
让供应商采用合并、替代等方法。
标准化,采用海外全球供应价格比较系统研发上降低成本:•背景:1993年,为了确保丰田始终处于汽车产业的霸主地位,公司决定不惜一切代价来设计、制造面向21世纪的首辆汽车。
–10名董事组成小组,提出设想–汽车代号G21–项目负责人:内山武司–成本不能超过正常车型的20%•由成功率5%,开始到最终成功–确定更高的目标–节省50%的油耗是不够的+ 5%–启用年轻、善于变更的工程师–预测可能出现的问题,尤其是生产方面的问题–建立“大房间”工作室,让所有的人都可以相互交流–建立电子邮件列表,共享信息+5%–提前时间期限(让工程师的想法尽快落到实处)(1997.6)+5%–尝试80种不同的引擎–试验20中不同的传输方式–从7种迥异的风格中作出选择–与松下合作开发汽车蓄电池+5%–拥有专业化的芯片制造技术+5%–将公司2/3的模型研发力量投入项目,组成50人(不同年龄)的外观评审小组+5%–使用已有的工作平台制造+5%日子不好过,倒逼出很多节约成本的办法,有多少企业能经受住这样的磨折?三、丰田成本控制深度剖析:了解人性•企业中做事的人决定成本–他的心态–他的能力–他的行为--决定成本发生的水平•企业人的特性–不懂的不做–不考核的不做–不激励的不做•在人身上下功夫丰田没有再考核、激励,凭的就是双方的绝对信任思维模式-成本金字塔2把钱花在哪里最好?丰田降低成本,主要是从效率、效果、浪费角度思考利润=收入-成本成本领先战略:综合成本最低or性价比最高成本结构、效率效果(能力及利用率)、浪费和资源占用所有成本,都因“事”产生,成本管理也要从“事”入手了解人性-成本管理视野与思路成本管理的举措包括:成本分析、要点与举措、责任人、成本环境改造、审查与绩效机制丰田做了前四个半。
国内能滚动几个圈,这与权力、能力、动力都有关。
问题解答:1、问:日本企业不注重绩效考核吗?答:不考核,日本公司多数不考核。
2、问:丰田的精准生产如何与一般规模生产的差异?答:规模化生产可以降低成本,因分摊的成本比例更小,但库存会比较高,这需要进行平衡。