SMT生产用PCB技术要求及标准
SMT工艺流程及各工位操作规范

SMT工艺流程及各工位操作规范概述表面贴装技术(Surface Mount Technology,简称SMT)是一种电子组装技术,广泛应用于电子产品的制造过程中。
本文将介绍SMT工艺流程的各个环节,以及各个工位的操作规范。
SMT工艺流程SMT工艺流程可以分为以下几个步骤:1.元件和PCB准备:在工艺开始之前,需要准备好元件和PCB板。
元件应进行分类、清洁和盘装。
PCB板应进行清洁和定位。
2.印刷:将焊膏粘贴到PCB板上。
3.安装:将元件粘贴到PCB板的焊膏上,这一步骤也称为贴片。
4.回流焊接:使焊膏熔化,并固定元件到PCB板上。
5.检查:检查焊接质量,包括元件是否安装正确,焊点是否合格。
6.清洗:清洗PCB板和元件以去除焊膏残留物。
7.测试:对已焊接的PCB板进行功能和性能测试。
8.包装:将已测试合格的PCB板进行包装,以备下一步骤的使用。
工位操作规范1. 元件和PCB准备工位•元件分类:根据元件相关规格和封装形式,进行分类并放置在对应位置,以便后续使用。
•元件清洁:使用适当的清洁剂和工具对元件进行清洁,以去除表面的污垢和油渍。
•元件盘装:根据所需数量,将清洁的元件装入元件盘,确保装盘过程中元件之间的间隔适当。
•PCB清洁:使用清洁剂和无尘布对PCB板进行清洁,确保表面干净无污垢。
•PCB定位:使用适当的夹具或模板,确保PCB板在后续工艺过程中位置准确。
2. 印刷工位•选择合适的印刷机:根据PCB板的尺寸和要求,选择适合的印刷机进行操作。
•调整印刷机参数:根据焊膏的特性和PCB板的要求,调整印刷机的速度、压力和刮刀角度等参数。
•焊膏印刷:将焊膏均匀地印刷到PCB板上,确保覆盖面积和厚度均匀一致。
3. 安装工位•选择合适的贴片机:根据PCB板的尺寸和元件的要求,选择适合的贴片机进行操作。
•调整贴片机参数:根据元件封装形式和PCB板的要求,调整贴片机的速度、压力和放料方式等参数。
•元件安装:将元件粘贴到已上焊膏的PCB板上,确保位置准确。
PCB质量接收标准

注意:1.当生产指示中有与以下项目相冲突时,需以生产指示为准。
2.当生产指示及以下项目未列举时,需以《质量检验规范》标准为准。
3.以下所提到的SMT包括BGA。
一.线路图形1.板面残铜:每面<=1处。
最大尺寸 <=0.5mm,离最近导体>=0.2mm.2.焊盘与SMT要求:1)焊盘无缩锡现象。
2)SMT和插装焊盘未有锡凸、划伤或缺损现象,针孔造成SMD的长或宽减少<=10%.3.孔:1)孔壁上出现的镀铜层破洞,不可超过1个,且破孔数不超过孔总数的5%,横向<=90度,纵向<=板厚的5%。
2)孔壁上出现的附着层(如锡层)破洞,不可超过3个,破孔面积未超过孔面积的10%,且破孔数不超过孔总数的5%。
3)A:对于阻焊塞孔或阻焊盖孔的孔,孔内或孔口残留的铅锡应满足:过电孔残留锡珠直径不大于0.1mm,含锡珠的过电孔不可超过板上过电孔总数的 1%;*但无SMT板的过电孔和单面SMT板的过孔焊接面可不受此限制。
B:对于非阻焊塞孔的孔,孔内或孔口残留的铅锡应满足:孔径<=0.35mm的过孔,且在焊接中无铅锡露出孔口或流到板面,允许铅锡塞孔;对于孔径>0.35mm的过孔,如铅锡塞孔或焊接中有铅锡露出孔口或流到板面则不接受。
4)金属化孔的孔电阻应小于1 mΩ5)孔壁粗糙度不超过30um,玻璃纤维突出不超过20 um.4.导体间锡拉间:缺陷在组件面不超过50% ,SS面小于30%。
5.大焊盘上的聚锡:缺陷在CS面不超过整个焊盘面积的50%,SS面小于30%,同时聚锡处锡高须小于0.051 mm.6.SMT之间及SMT到线的蚀刻间距要求仅需要大于或等于4 mil即可。
二、修补1.补线要求:a)导线拐弯处不允许补线;b)内层不允许补线;c)特性阻抗控制的线、差分线不允许补线。
d)过孔不允许补线;e)相邻平行导线不允许同时补线;f)断线长度大于2mm的不允许补线;g)焊盘周围不允许补线,补线点距离焊盘边缘大于3mm;h)同一导体补线最多1处;每板补线<=5处;每面<=3处;补线板的比例<=8%;三、阻焊1.阻焊膜(绿油)1)绿油圈到开窗的有孔PAD间距>=0.051mm;2)过电孔绿油盖焊环有锡圈或过孔开窗的板,允许绿油入孔数目<=过孔总数的5% ,不允许塞孔。
SMT印制板设计规范

SMT印制板设计规范SMT(Surface Mount Technology)印制板设计规范是关于电子产品印制板设计的一系列要求和准则,旨在确保PCB(Printed Circuit Board)的制造过程能够顺利进行,并最终得到高质量的印制板产品。
下面是一些SMT印制板设计规范的重要内容。
1.印制板尺寸和布局:-确定印制板的实际尺寸,包括长度、宽度和厚度,并在设计中使用正确的尺寸参数。
-设计合理的布局,确保所有元件和走线的正确安装和连通,以提高印制板的性能和可靠性。
2.元件安装规范:-元件安装应遵循适当的引脚布局,确保元件安装在正确的位置并正确连接。
-元件的排列应便于制造和维修,并保证元件之间的足够间距和空间。
3.安装孔和固定装置:-印制板上的孔和固定装置应符合标准尺寸和设计规范,并确保能够正确安装印制板。
-孔的位置和尺寸应准确,以确保印制板和配件之间的稳定连接。
4.线宽和间距:-确定正确的线宽和间距参数,以提供足够的电流传输能力,并避免线路之间的干扰或短路。
-确保线宽和间距符合制造商的要求和能力,并能满足所需的电子器件和电流要求。
5.反焊和覆盖层:-在印制板上使用适当的反焊材料,以便在组装过程中保护印制电路和焊点,并提供良好的可焊性。
-配置适当的覆盖层,以保护印制板免受外部环境的影响,并提供适当的绝缘和防护。
6.引脚和焊盘:-准确标记元件引脚的位置和方向,确保正确的引脚连接和组装。
-焊盘的尺寸和形状应适合所使用的元件,并提供良好的焊接质量和可靠性。
7.电源分离和地面规范:-正确的电源分离和地面规范是确保印制电路的稳定性和性能的重要因素。
-确定正确的分离点和连接方式,以确保电源的稳定和地面的良好连接。
8.文件和制造要求:-提供准确和详细的PCB设计文件,包括图纸、尺寸和布局等信息,以供制造商参考。
-了解制造商的要求,并根据实际制造要求进行设计和调整。
总之,遵守SMT印制板设计规范对于确保PCB的制造质量和性能至关重要。
PCB技术要求及标准

PCB技术要求及作业指导一、目的根据公司现有的设备加工能力并结合IPC标准,规范生产用印刷电路板(PCB)的工艺制作,增加基板定位方式的通用性,更好地提高生产效率及生产灵活性。
二、适用范围适用于公司电力自动化事业部硬件设计管理和PCB基板的工艺设计指导。
三、具体内容主要对PCB命名标识和硬件文档设计;以PCB的外形、元件区域设计、基准点(Mark)、定位孔及PCB重要线宽、器件间的间距等方面提出PCB设计的技术要求。
(注:本PCB技术要求及作业指导仅供PCB设审核流程使用)1.硬件设计文档命名规定将同一组件的硬件设计文档分为以下三种:(1)研发原始文档(2)PCB加工文档(3)生产文档命名规则如下:ST6006BHMI __ D __ 080514日期:6位数08年05月14日单下画线(半角)文档类型:D—研发原始文档M--PCB加工文档P--生产文档单下画线(半角)文件名(英文数字)2.硬件设计文档内容2.1研发文档研发文档除了设计的PCB和SCH目录外,还应有以下4个目录:2.2 PCB加工文档PCB加工文档含有两个目录(1)PCB目录:存放需要加工的PCB文件(2)加工说明目录:存放PCB的开孔、外型等说明2.3 生产文档生产文档只含存放元件的BOM和在PCB上的元件布置图的生产说明。
3.硬件设计文档细则3.1 SCH及其PCB在以文件名命名的目录中含有两个目录,它们分别是SCH目录和PCB目录,其中SCH目录只能存放SCH文件和与SCH相关的文件;PCB目录只能存放PCB文件及其PCB相关的文件。
SCH文件采用A4篇幅,如果SCH文件超过一张,则采用Project进行管理。
3.2设计说明设计说明含版本历史和设计说明3.3加工说明加工说明采用16色BMP或GIF图形格式,采用PROTEL SE中的import进行输入存档。
3.4生产说明生产说明中含有BOM和PCB上的元件布置图,其中PCB上的元件布置图为PDF格式,如果是两面安装的元件,在其文件名后用下画线标识出TOP戓BOTTOM。
PCB设计工艺要求

目的:明确设计PCB过程中的工艺各项要求,做到标准化设计。
以提高开发效率及方便生产。
适用范围:适用于本公司的电话机产品设计。
职责:各开发工程师及PCB Layout工程师按规定执行。
1、单面板要求:1:线径、线距不小于0.3mm,建议为0.35mm以上。
(半玻纤板及玻纤板不小于0.18mm)。
2:焊盘和焊盘之间的间距不小于0.5mm。
3:走线至板边距离板不小于0.8mm。
4:过孔至板边距离不小于1.6mm。
5:元件焊盘孔径不小于0.7mm。
6:丝印文字线宽不小于0.18mm,SMT不小于0.13mm。
7:板的碳桥宽度不小于2.0mm。
碳桥与碳桥之间的距离不小于1mm。
碳桥越短越好,最长不能超过15mm。
(除非特殊限制,但需项目工程师以上人员同意才能使用)8:板边宽的部分离焊盘必须大于3mm以上,SMT板大于5mm。
9:固定螺丝的孔位直径5mm以内不能有元件实体;与非地线的铜皮直径距离为5mm。
2、双面板要求:1:线径、线距(金板)不小于0.15mm。
(锡板不小于0.18mm)2:线边距板边不小于0.8mm。
3:孔边距板边不小于1.6mm。
4:孔径不小于0.35mm。
5:丝印文字线宽不小于0.18mm,SMT不小于0.13mm。
6:板边宽的部分离焊盘必须大于3mm以上,SMT板大于5mm。
7:焊盘和焊盘之间的间距不小于0.5mm8:固定螺丝的孔位直径5mm以内不能有元件实体;与非地线的铜皮直径距离为5mm。
9:双面板PCB螺丝孔位不能灌铜(锡浆板除外)。
3、PCB设计布局及走线等基本要求:1、所有元件放置要有规律,同一工作部分电路尽量靠在一起,避免走长线;电阻要平插元件尽量排成行,如无特殊要求尽量减少直立元件插件。
2、外线进线部分(包括压敏电阻)必须靠在一起,因开关电路以前的电路属于高压部分,此走线不要太长越短越好,铜皮走线线径不能小于0.45mm;,不要靠近其它信号线和CPU的IO口,避免对它的干扰。
SMT工艺设计规范
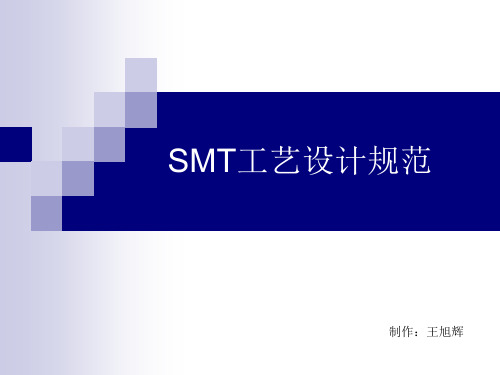
2.4 PCB焊盘设计 焊盘设计总的规则是元件的焊盘投影必须落在PCB焊盘之内,且周围留有一定的剩余 面积以利形成带弧度的焊接表面,焊盘设计应对称,双端元件两个焊盘尺寸一致。
各类型元件的焊盘具体尺寸见图表1及图示。
W L D
1)焊盘长度L=元件焊盘长度+元件焊盘高度+0.25 (mm) 2)焊盘宽度W=元件宽度+0.25 (mm) 3)焊盘间距D=元件焊盘间距-0.25(mm) 4)具体尺寸见表1 表1 普通片状元件的焊盘设计尺寸备查表
5mm 宽的工艺边 贴片完成后去除
2.3 PCB拼板设计 2.3.1对于尺寸小于50×50mm的PCB,可以设计成拼板,如图所示。但拼板后的总尺寸又 不能超出L510×W460mm的范围(包括附加的工艺边),各小拼板的方向尽量保持一致,并维 持长边在PCB的流向方向,丝印文字正对人眼。各拼板之间采用V-CUT半切口连接,如图7所 示。即两面各切入1/3的深度,中间保留1/3的板厚,可用手工很方便的分离。 在电路设计中 可直接将PCB实体拷贝拼接在一起,板间留0.3mm的余量用于切口,但注意应将完全靠边的 铜箔线路从板边往内收缩至少0.75mm,避免PCB切口加工时刀具伤及铜箔线路。采用V-CUT 拼板的PCB厚度一般不超过3.5mm。 2.3.2从设备的综合利用率和生产效率出发,我们公司自动贴片机基本按1+1配置,为最大限 度的提高设备单位产能,这样对我们前期拼板及拼板后元件有一个基本的规定,当拼板后元 件点数不少于420点,这样就达到SMT设备生产效率最大化。
焊盘从引脚弯折处开始,到元件脚边缘结束,四周再向外延伸0.3mm。 晶体管焊盘设计
焊盘从元件脚弯折处开始,到元件脚边沿结束,四周再向外延伸0.3mm。
普通集成电路芯片焊盘设计
SMT钢网设计基本要求
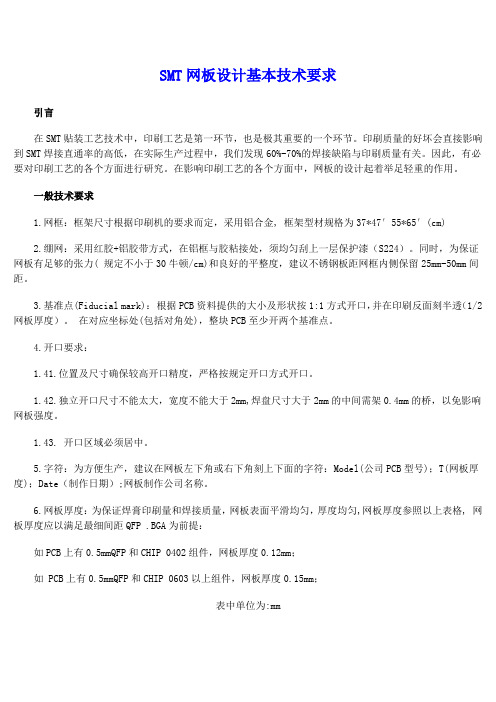
SMT网板设计基本技术要求引言在SMT贴装工艺技术中,印刷工艺是第一环节,也是极其重要的一个环节。
印刷质量的好坏会直接影响到SMT焊接直通率的高低,在实际生产过程中,我们发现60%-70%的焊接缺陷与印刷质量有关。
因此,有必要对印刷工艺的各个方面进行研究。
在影响印刷工艺的各个方面中,网板的设计起着举足轻重的作用。
一般技术要求1.网框:框架尺寸根据印刷机的要求而定,采用铝合金, 框架型材规格为37*47′55*65′(cm)2.绷网:采用红胶+铝胶带方式,在铝框与胶粘接处,须均匀刮上一层保护漆(S224)。
同时,为保证网板有足够的张力( 规定不小于30牛顿/cm)和良好的平整度,建议不锈钢板距网框内侧保留25mm-50mm间距。
3.基准点(Fiducial mark):根据PCB资料提供的大小及形状按1:1方式开口,并在印刷反面刻半透(1/2网板厚度)。
在对应坐标处(包括对角处),整块PCB至少开两个基准点。
4.开口要求:1.41.位置及尺寸确保较高开口精度,严格按规定开口方式开口。
1.42.独立开口尺寸不能太大,宽度不能大于2mm,焊盘尺寸大于2mm的中间需架0.4mm的桥,以免影响网板强度。
1.43. 开口区域必须居中。
5.字符:为方便生产,建议在网板左下角或右下角刻上下面的字符:Model(公司PCB型号);T(网板厚度);Date(制作日期);网板制作公司名称。
6.网板厚度:为保证焊膏印刷量和焊接质量,网板表面平滑均匀,厚度均匀,网板厚度参照以上表格, 网板厚度应以满足最细间距QFP .BGA为前提:如PCB上有0.5mmQFP和CHIP 0402组件,网板厚度0.12mm;如 PCB上有0.5mmQFP和CHIP 0603以上组件,网板厚度0.15mm;表中单位为:mm元件间距网板厚度元件间距网板厚度QFP SQIC SOP TSOP 1.27 0.2/.03 LCC 1.27 2.0 0.8 0.18BGA1.5 0.15 0.65 0.18 1.27 0.15 0.5 0.12/0.15 1 0.12 0.4 0.12 0.8 0.12 0.3 0.1 0.65 0.1PLCC 1.27 2.0 0.5 0.1 印锡网板开口形状及尺寸要求1.总原则:依据IPC-7525 钢网设计指南要求,为保证锡膏能顺畅地从网板开孔中释放到PCB焊盘上,在网板的开孔方面,主要依赖于三个因素:1.)面积比/宽厚比 (Area Ratio/Aspect Ratio)面积比(Area Ratio)>0.66 (见下图)2.)网孔孔壁光滑。
PCB板生产标准

PCB板生产标准
1. 引言
本文档旨在制定适用于PCB板生产的标准,以确保生产过程中的质量和一致性。
本标准覆盖了从原材料采购到最终产品质检的各个环节。
2. 材料要求
- PCB板的基材应符合国际标准,并具有良好的绝缘性和耐热性。
- 铜箔表面应经过适当处理,确保良好的粘附性和电导性。
- 化学药剂和溶剂应符合相关的环保标准。
3. 设计要求
- PCB板的设计应满足特定的电路布局要求,并保证电路的稳定性和可靠性。
- 电路板上的元件布局应合理,方便生产和维修。
- PCB板的尺寸和孔径应符合预定的尺寸公差要求。
4. 生产工艺
- PCB板的生产过程应严格遵循相关的工艺流程,并采取可靠
的质量控制措施。
- 单板和多层板的制作应确保层间绝缘和电路连通的可靠性。
- PCB板的焊接过程应符合国际标准,并确保焊点的良好质量。
5. 质量检验
- PCB板生产过程中应进行多项质量检验,包括尺寸检验、外
观检验、电气性能测试等。
- 检验结果应详细记录,有助于追溯产品质量问题的原因和责任。
6. 维护与修复
- PCB板在生产后可能需要维护和修复,应采取适当的措施保
证修复后的电路性能和质量。
7. 参考标准
以下标准对于PCB板的生产和质量控制具有重要参考价值:
- 国际电工委员会(IEC)标准
- 美国国家标准协会(ANSI)标准
- 欧洲电子工程师协会(EENA)标准
以上是对PCB板生产标准的简要描述,完整的标准可以根据实际要求进行进一步制定和完善。
- 1、下载文档前请自行甄别文档内容的完整性,平台不提供额外的编辑、内容补充、找答案等附加服务。
- 2、"仅部分预览"的文档,不可在线预览部分如存在完整性等问题,可反馈申请退款(可完整预览的文档不适用该条件!)。
- 3、如文档侵犯您的权益,请联系客服反馈,我们会尽快为您处理(人工客服工作时间:9:00-18:30)。
SMT生产用PCB技术要求及标准
1、目的
根据集团公司现有的设备加工能力并结合IPC标准,规范生产用印刷电路板(PCB)的工艺制作,增加基板定位方式的通用性,更好地提高生产效率及生产灵活性。
2、适用范围
该要求适用于海信电器股份有限公司在海信通信有限公司SMT车间生产用的所有PCB基板的工艺设计。
3、具体内容
主要对PCB的外形、无元件区域设计、基板识别点(Fiducial Mark)、坏板标识(Bad Mark)、定位孔、拼板数标识、流向标识及顶面(TOP面)和底面(BOTTOM 面)标识等方面提出PCB设计的工艺要求。
(参考图1)
3.1 PCB的外形要求
3.1.1
3.1.2 PCB四角必须倒圆角(如图2),半径不少于2mm。
图2
3.2 PCB标识
生产用PCB应包含如下方面的标识:
3.2.1 生产时的流向标识符(箭头),在工艺边上用丝印作标识。
3.2.2 TOP 和BOTTOM 面的基板面标识,在流向箭头的始端用T或B表示(如图
3、图5和图6所示)。
图3
3.2.3拼板子板序号标识:拼板中每块子板应有相应的序号(与各自的Bad Mark相对
应),子板编号根据实际情况在基板的TOP面按照由左至右、由上至下的“Z”
形(如图5),和基板的BOTTOM面按照由右至左、由上至下的反“Z”形(如
图6)顺序分别进行编号。
3.3 无元件区域
PCB 无元件区域如图1所示,为生产时用于在导轨上传输时导轨占用区域和使用工装时的预留区域。
关于区域的面积,对于顶面(TOP面)四周至少要求有5mm的区域不能排布元器件, 对于底面(BOTTOM面)四周至少要求有5mm的区域不能排布元器件。
3.4 PCB 识别标识(Fiducial Mark)和元件贴装校准标识(Local Fiducial Mark)
3.4.1 整拼板至少有三个Fiducial,并且呈L形分布
3.4.2 Fiduical Mark类型首选为圆形,直径为0.5~2.5mm,优选1mm(周边有反差标
记Φ2.5mm);其次为方形,边长为0.5~2.5mm,优选1mm
3.4.3 Fiduical Mark要求表面洁净、平整,边缘光滑、齐整,颜色与周围的背景色有
明显区别。
3.4.4 TOP面的Fiduical Mark和BOTTOM面的Fiduical Mark的设置不能呈对称排
布,优先选用图示中提供的参考位置尺寸:图5表示的是顶面设计,图6为底面
设计。
3.4.5 对于细引脚间距且尺寸较大(大于30×30mm)的元件,要求设计元件贴装校
准标识(Local Fiducial Mark),表示的要求同3.4.2、3.4.3。
3.4.6 对应网板的Fiduical Mark 应与pcb 的Fiduical Mark 一一对应。
3.5 Bad Mark
3.5.1 Bad Mark 包含Master Bad Mark 和Local Bad Mark两种,如图1所示。
Bad Mark 数量= 整拼板包含的子板总数+1(Master bad mark)
3.5.2 Bad Mark 直径至少为1.5mm;颜色为White或者Black,要求与基板的背
景颜色有明显的对比和反差。
3.5.3 两Bad Mark 点的间距至少为2.5mm。
3.5.4 若拼板中有某一子板坏,要求将其对应的Bad Mark 点涂掉(白色涂成黑色
或黑色涂成白色)。
3.6 定位孔
3.6.1 定位孔直径3-
4.5mm,优选4mm。
3.6.2 定位孔的位置必须按照要求设置,如图7所示:
其中尺寸a、b、c有如下的要求:60mm≤a=b=10N mm (N=6,7,8,9,10,11,12……),
c>10mm。
海信电器股份有限公司开发中心
二零零四年十月。