压铸工艺参数(速度)教案(精)
压铸工艺-影响压铸件质量的主要工艺参数

过高的速度将产生不利影响 气体不能充分逸出而形成气泡。
金属液成雾状进入型腔并粘附于型壁上,不能与 后来的金属液融合而形成夹杂等表面缺陷。
定期检查型芯是否变形 使用模具时要充分预热并且严格按工艺规程操作 对浇口方案及型芯型腔能否冷却等铸造方案进行重新论证 针对铸件的收缩情况对铸件形状进行改动 改进模具的材料或硬度
修复模具被冲蚀的部分 改进浇口位置、模具结构和铸造方案 改进模具的材料或硬度
检查浇注温度、循环时间、保压时间及模具温度等参数是否正确, 并严格遵守工艺规程 检查金属液化学成分是否合格 如果是由于局部过热造成局部收缩,可调节该部分的冷却水量或改 变浇口位置和金属液成分
产生漩涡,包住空气及冷金属,使铸件产生气孔 及氧化夹杂缺陷。
冲刷模具型腔,加剧磨损,缩短模具使用寿命
速度设定 一速 2000±500MM/S 二速 4000±2000MM/S 切换位置 20±10MM
3、压力
压射力是压铸机压射机构中推动压射活塞 运动的力。压射力是由泵产生压力油,并 通过蓄压罐,在压射缸内传递给压射活塞, 再由压射活塞传递给压射冲头,进而推动 金属液填充入模具型腔中。
(2)金属液温度
①浇注温度的作用及影响
提高浇注温度可以提高金属液的流动性, 有利于铸件表面质量的改善,但气体在金 属液内的溶解度及金属液的氧化增加,使 压铸模的寿命减短,并且易造成粘模。
低的浇注温度会降低金属液的流动性,但 可采用增大排气槽深度来改善排气条件; 由于低温的金属液在压射过程中产生涡流、 包气的可能性减小,铸件内在质量提高, 减小了因壁厚差而在厚壁处产生缩松及气 孔的可能性,同时减少了金属液对模具的 熔蚀及粘模,从而延长了模具使用寿命。
压铸工艺参数课件

若设Q为金属熔体的流量(m3/s) , Sa 为内浇口截面积(m参数
3、压实压力
压实压力pk是指压射缸压力与增压压力叠加后的压射压力pe ,乘 以压射活塞面积A1与冲头面积A0之比。设压射活塞直径d1 ,冲头直径 d0 ,则
常用留模时间见下表
单位: h
13
压铸工艺参数
1.4 温度参数
1、浇注温度
金属液从压室至充满型腔的平均温度称为浇注温度。为了保证铸 件质量、提高模具寿命,浇注温度应尽可能低,一般为合金液相线以 上20~50℃,实际采用的压铸合金浇注温度,见下表。
14
压铸工艺参数
1.4 温度参数
2、模具温度
模具温度是重要的工艺参数之一。压铸模在工作前必须预热,绝 不允许用冷或未预热到足够温度的模具进行压铸,推荐的预热温度见 下表。
5
压铸工艺参数
1.2 速度参数
1、冲头速度
在压射的第一阶段冲头 以临界恒速或恒加速向前, 将金属熔体推进至浇口处,此 时熔体流动速度就是第一级压 射速度,如右图所示。在形成 曲线充型段任选两点,测量行 程距离和充型时间,则可得出 冲头速度:
冲头速度=测量的距离/相应充型时间
6
压铸工艺参数
1.2 速度参数
模具设计与制造
压铸工艺参 数
1
压铸工艺参数
传统压铸机常配以三级压射系统,第一级是将金属熔体慢速渐进推 至内浇口,第二级是将金属熔体在短的充型时间内快速充满型腔,第三 级为增压压实段,即铸件在高压下紧实(借助于增压控制系统)。
三级压射曲线
实时压射控制压铸机压铸曲线
2
压铸工艺参数
1.1 压力参数
压铸工艺参数

压铸工艺参数
一、压铸机参数
1.锁模力:压铸机锁模力是指压铸机在关闭模具时施加在模具上的力量,这个参数的选取要根据铸件的大小和形状来确定。
2.注射压力:指压铸机在注入合金液态金属时向模腔施加的压力,需
要根据合金的液态流动性来设定。
3.注射速度:指合金液态金属进入模腔的速度,需要控制在合适的范
围内,既要保证充模完全,又要避免过快造成气孔和模具损坏。
二、模具参数
1.冷却系统:合理的冷却系统可以提高铸件的质量和生产效率,可以
通过冷却水的流量、温度和冷却通道的设计来控制。
2.喷油系统:喷油系统用于在压铸之前,在模具表面形成一层润滑膜,减少金属与模具的摩擦,需要控制喷油量和喷油位置。
3.模具温度:模具温度会影响合金凝固速度和铸件表面质量,可以通
过加热、降温等方式来控制。
三、材料参数
1.合金成分:合金成分是对压铸件的力学性能和化学性能有很大影响
的因素,需要根据产品的要求选择合适的合金成分。
2.熔化温度:合金的熔化温度会影响注入流动性和凝固速度,需要根
据合金的熔化温度范围进行控制。
3.熔金温度:熔金温度是指合金进入模腔前的温度,需要根据合金的熔点和凝固温度来确定。
除了以上介绍的参数,还有一些其他的因素也会影响压铸工艺,比如模具的设计、铸件的几何形状以及工艺操作等。
这些参数和因素都需要通过实践和不断探索来确定和优化,以提高压铸的质量和效率。
对于不同的产品和工艺需求,压铸工艺参数也会有所差别,因此需要根据具体情况进行调整和优化。
压铸工艺

第三部分压铸工艺一、工艺参数1、压力参数:①压射力用压射压力和压射比压来表示,是获得组织致密、轮廓清晰的压铸件的主要因素,在压铸机上其大小可以调节。
②压射压力压射时压射油缸内的油压,可以从压力表上直接读出,是一个变量,当压铸机进入压射动作时产生压射压力,按照压射动作分段对应的称为一级压射压力(慢压射压力)、二级压射压力(快压射压力)等;增压阶段后转变为增压压力,此时的压射压力达到极大值。
③压射比压压射时压室内金属液在单位面积上所受的压力,简称比压。
可通过改变压射力或更换不同直径的压室及冲头来进行调整。
计算公式为:比压=压射力÷(冲头直径)²×4/π2、速度参数:①压射速度压射时冲头移动的速度。
按照压射过程的不同阶段,压射速度分为慢压射速度(低速压射速度)和快压射速度(高速压射速度)。
一般慢压射速度的选择根据“压室充满度”(即压室内金属液的多少,用百分比快压射速度,是在一定填充时间条件下确定的。
根据铸件的结构特征确定其填充时间后,可用以下公式进行计算:快压射速度=坯件重量/合金比重/压室内截面积/填充时间×[1+(N-1)+0.1]式中“坯件重量”含浇冒系统;“N”为型腔穴数;“填充时间”可查表得到。
按此公式计算出来的快压射速度,是获得优质铸件的理论速度,实际生产中选其1.2倍;对有较大镶嵌件的铸件时可选1.5~2倍。
②内浇口速度金属液在压力作用下通过内浇道导入型腔时的线速度,称为内浇口速度。
内浇口速度对铸件质量有着重要影响,主要是表面光洁度、强度和塑性等方面。
内浇口速度的大小可通过查表得到,调节的方法有:调整压射速度、改变压室直径、调整比压、改变内浇口截面积。
铸件平均壁厚、填充时间、内浇口速度对照表3、时间参数:①填充时间金属液自开始进入型腔到充满铸型的过程所需要的时间。
影响填充时间的因素有:金属液的过热度、浇注温度、模具温度、涂料性能与用量、排气效果等。
压铸工艺之速度

1.压射速度压射速度是指压室内压射冲头推动熔融金属液的移动速度。
图5-5示意压铸过程中速度的变化:图5-5 压力和速度变化曲线(1)第一阶段:低速压射V1当金属液浇注入压室后,压室内金属液的充满度一般在45%~70%左右,其余的空间被空气充填着。
低速压射是为了使金属液平稳流动,空气能顺利排出。
参考数据:低速射出速度:V1:0.1~0.5 m/s;薄壁件、外表装饰件:0.25~0.35 m/s;耐压、强度高件:0.15~0.25 m/s(2)第二阶段:高速压射金属液到达内浇口时,可进行高速切换,使金属液在高压高速下充填。
经验数据:高速压射速度V2: 0.2~4.5 m/s以上。
高速射出加速时间t1: 0.01s。
增压时间t2: 0.01s。
(3)如何选择高速压射起点压铸的基本特点之一是快速充型,在整个快速压射阶段,金属液以30 ~ 60 m/s的速度,以射流的形式进入型腔,金属液会包卷气体,在这种情况下可考虑让气孔分布在何处不影响关键部位。
由于成型部位型腔的截面积远大于内浇口的截面积,当压射冲头的运动速度不大于0.8 m/s的时候,金属液在型腔内以近似于层流的方式流动,这一阶段不会产生卷气。
从快速点开始直到充型结束.金属液都以射流的形式运动,这一阶段是包卷气体的过程,也是铸件易产生气孔的部位。
高速压射起点(见图5-6):1)选择①:卷气量大。
2)选择②~③:一般压铸件。
选择金属液进人内浇口,或金属液进入型腔某一位置时切换高速。
3)选择③~④:多用于大型机、大型铸件。
一个铸件易产生气孔的部位及对致密性的要求有所不同时,高速压射的起点可选择在不允许有气孔的部位之后。
如图5-7中的曲轴箱件,A部位内有润滑油通道,要求致密不渗油,所以快压射的起点设在位置2,从而保证了铸件内部质量要求。
----------------------------------------------------------------------------------------------------------------2.充填速度金属液进人型腔的充填速度高。
压铸工艺参数(压力)教案(精)
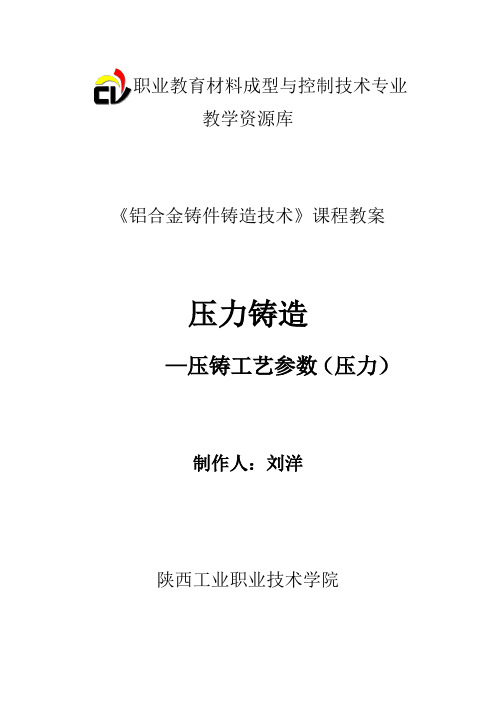
职业教育材料成型与控制技术专业教学资源库《铝合金铸件铸造技术》课程教案压力铸造—压铸工艺参数(压力)制作人:刘洋陕西工业职业技术学院压力铸造—压铸工艺参数(压力)一、压射力压射力是指压射冲头作用于金属液上的力,来源于高压泵,压铸时它推动金属液充填到模具型腔中。
在压铸过程中,作用在金属液上的压力并不是一个常数,而是随着不同阶段而变化。
压射力的大小由压射缸的截面积和工作液的压力所决定:y F 42D P g π⨯=式中 F Y —压射力(N);P g —压射缸内的工作压力(Pa),当无增压机构或增压机构未工作时,即为管道中工作液的压力; D —压射缸直径(m)。
增压机构工作时,压射力为:y F 422D P g π⨯=式中 P g2—增压时压射缸内的工作压力(Pa)。
二、压射比压比压是压室内金属液单位面积上所受的力,即压铸机的压射力与压射冲头截面积之比。
充填时的比压称压射比压,用于克服金属液在浇注系统及型腔中的流动阻力,特别是内浇口处阻力,使金属液在内浇口处达到需要的速度。
有增压机构时,增压后的比压称增压比压,它决定了压铸件最终所受压力和这时所形成的胀模力的大小。
压射比压可按下式计算:24dF P yb π=式中P b一压射比压(Pa);d—压射冲头(或压室)直径(m)。
比压与压铸机的压射力成正比,与压射冲头直径的平万成反比。
所以,比压可以通过改变压射力和压射冲头直径来调整。
在制订压铸工艺时,正确选择比压的大小对铸件的力学性能、表面质量和模具的使用寿命都有很大影响。
首先,选择合适的比压可以改善压铸件的力学性能。
随着比压的增大,压铸件的强度亦增加。
这是由于金属液在较高比压下凝固,其内部微小孔隙或气泡被压缩,孔隙率减小,致密度提高。
随着比压增大,压铸件的塑性降低。
比压增加有一定限度,过高时不但使延伸率减小,而且强度也会下降,使压铸件的力学性能恶化。
此外,提高压射比压还可以提高金属液的充型能力,获得轮廓清晰的压铸件。
压铸机工艺参数设定教案(精)
职业教育材料成型与控制技术专业教学资源库《铝合金铸件铸造技术》课程教案压力铸造—压铸机工艺参数设定制作人:刘洋陕西工业职业技术学院压力铸造—压铸机工艺参数设定一、冷室压铸机工艺参数设定1.射料时间射料时间大小与铸件壁厚成正比,对于铸件质量较大、压射一速速度较慢且所需时间较长时,射料时间可适当加大,一般在2S以上。
射料二速冲头运动的时间等于填充时间。
2.开型(模)时间开型(模)时间一般在2S以上。
压铸件较厚比较薄的开型(模)时间较之要长,结构复杂的型(模)具比结构简单的型(模)具开型(模)时间较之要长。
调节开始时可以略长一点时间,然后再缩短,注意机器工作程序为先开型(模)后再开安全门,以防止未完全冷却的铸件喷溅伤人。
3.顶出延时时间在保证产品充分凝固成型且不粘模的前提下,尽量减短顶出延时时间,一般在0.5S以上。
4.顶回延时时间在保证能顺利地取出铸件的前提下尽量减短顶回延时时间,一般在0.5S以上。
5.储能时间一般在2S左右,在设定时操作机器作自动循环运动,观察储能时间结束时,压力是否能达到设定值,在能达到设定压力值的前提下尽量减短储能时间。
6.顶针次数根据型(模)具要求来设定顶针次数。
7.压力参数设定在保证机器能正常工作,铸件产品质量能合乎要求的前提下,尽量减小工作压力。
选择、设定压射比压时应考虑如下因素:(1)压铸件结构特性决定压力参数的设定①壁厚:薄壁件,压射比压可选高些;厚壁件,增压比压可选高些。
②铸件几何形状复杂程度:形状复杂件,选择高的比压;形状简单件,比压低。
③工艺合理性:工艺合理性好,比压低些。
(2)压铸合金的特性决定压力参数的设定①结晶温度范围:结晶温度范围大,选择高比压;结晶温度范围小,比压低些。
②流动性:流动性好,选择较低压射比压;流动性差,压射比压高些。
③密度:密度大,压射比压、增压比压均应大;密度小,压射比压、增压比压均选小些。
④比强度:要求比强度大,增压比压高些。
(3)浇注系统决定压力参数的设定①浇道阻力:浇道阻力大,主要是由于浇道长、转向多,在同样截面积下、内浇口厚度小产生的,增压比压应选择大些。
压铸参数的计算(精)
∙压铸工艺参数的计算∙发布时间:2011-4-9 15:39:34 来源:互联网文字【大中小】∙文/哈尔滨爱迪压铸有限公司/朱丽、刘维刚、车宏伟、迟兰成摘要:许多压铸企业的技术人员都非常熟悉压铸工艺参数的计算与调节,但在实际生产中往往凭借经验,通过检验产品的好坏来调节工艺参数,为了麻烦而忽略了工艺参数的计算,往往都是用很大的速度、压力来使产品达到合格状态,这样使机床、模具损耗过快,浪费资源。
关键词:工艺参数、压力、速度、时间在压铸生产中,压铸机、压铸合金和压铸模是三大要素。
压铸工艺则是将三大要素作为有机的组合并加以运用的过程。
压铸生产时液态金属充型的过程,是许多矛盾着的因素得以统一的过程。
在影响充型的许多因素中,主要是速度、压力和时间等,通过速度的控制减少和消除压室内空气的卷入、雾化型腔内残留的气体; 通过压力的控制,增加产品的密实度,减少缩孔的形成; 通过时间控制,使产品不宜产生变型等缺陷。
利用计算工艺参数来优化模具、压铸机之间的匹配性。
因此,只有对这些工艺参数进行正确选择、控制和调整,使各种工艺参数满足压铸生产的需要,才能保证在其他条件良好的情况下,生产出合格的压铸件。
本文通过以力劲公司生产的DCC280卧式冷室压铸机上所生产的水泵壳体产品(附图为例,简单介绍一下压铸生产中主要工艺参数的计算。
一、速度参数(1低速速度压射冲头将注入压室的铝液平稳地推移到内浇口位置,使铝液完全充满到压射冲头与内浇口之间的压室空间内的过程就是低速过程(一般为0.1-0.3m/s。
设置时要注意防止空气卷入,防止铝液温度下降,导致过早凝固。
压室充满度=注入重量/压室截面积×空打行程×溶液密度X100%(压室充满度的标准一般为20-50%低速速度=0.7X√压室直径/压室充满度例题:压室直径:Φ50mm,注入重量:830g ,空打行程:368mm ,压室截面积:(π/4×52=19.63cm²,溶液密度:2.6 g/cm³压室充满度=(830/196.63×36.8×2.6X100%=44.18%低速速度=(0.7X√50/44.18=0.122M/S(2高速速度压射冲头将铝液完全充满到压室内(一般为1.5-2.5m/s。
压铸教案
三.讲授 新课
出示课题: 第一节 压铸压力和压铸速度
首先,我们看下压铸压力
一.压铸压力
(板书)
它有两种表现形式:压射力和压射比压
压射力的定义是这样说的:来源于高压泵,它是
教学难 点
压铸机压射机构中推动压射活塞的力。
这个力可以通过一个公式计算:
Fy=PgAD
(板书)
Fy:压射力(N)
Pg:液压系统的管路压力(Pa)
通过这个公式,我们可以知道,液体金属
充填铸型的线速度与压室直径的平方,冲头的
压射速度成正比,与内浇道的截面积成反比。
因此,我们可以通过什么方式调整充填速
度呢?
答:压室内经,压射冲头速度和内浇道截
面积
好了,我们现在介绍一下压铸速度的另一
个概念,充填速度
由于熔融金属是成液态的,所以,在此我
们借鉴了水力学原理,得到了压射比压与充填
教学难 点
教案内容 方法 过程
Ad=πd /4 d:压射冲头直径(m)
从上式中可以看出,压射比压与压铸机的压射力 成正比,与压射冲头的截面积成反比。
那么,我有个问题: 我们可以通过什么途径改变压射比压?
课堂问 答
答:通过改变压射力和压室内径实现。
压射比压在压铸工艺中是一个非常重要的参数,
然而,他并不是一个常数,而是随着压射阶段的变化
压铸工 学 艺及模 课 科具
压铸压力和压铸速度
班
级
题
人 数
授课时数
1课时
课型
新授 周次 第2周 课
授课时间
教
1.通过本节课的学习,使同学们知道压铸制造过程中的两
个重要参数:压铸压力和 压铸速度。
学
压铸工艺参数(时间)教案(精)
职业教育材料成型与控制技术专业教学资源库《铝合金铸件铸造技术》课程教案压力铸造—压铸工艺参数(时间)制作人:刘洋陕西工业职业技术学院压力铸造—压铸工艺参数(时间)一、充填时间金属液从开始进入模具型腔到充满型腔所需要的时间称为充填时间。
充填时间长短取决于压铸件的大小、复杂程度、内浇口截面积和内浇口速度等。
体积大、形状简单的压铸件,充填时间要长些,体积小、形状复杂的压铸件,充填时间短些。
当压铸件的体积确定后,充填时间与内浇口速度和内浇口截面积之乘积成反比。
即选用较大内浇口速度时,也能因内浇口截面积很小而仍需要较长的充填时间。
反之,当内浇口截面积较大时,即使用较小的内浇口速度,也能缩短充填时间。
因此,不能孤立地认为内浇口速度越大,其所需的充填时间越短。
在考虑内浇口截面积的大小对充填时间的影响时,还要与内浇口的厚度联系起来。
如内浇口截面积虽大,但很薄,由于压铸金属呈粘稠的”粥状”,粘度较大,通过薄的内浇口时受到很大阻力,则将使充填时间延长。
而且会使动能过多地损失,转变成热能,导致内浇口处局部过热,可能造成粘模。
压铸时,不论合金种类和铸件的复杂程度如何,一般充填时间都是很短的,中小型压铸件仅0.03~0.20s,或更短。
但充填时间对压铸件质量的影响是很明显的,充填时间长,慢速充填,金属液内卷入的气体少,但铸件表面粗糙度高。
充填时间短,快速填充,则情况相反。
二、增压建压时间增压建压时间是指从金属液充满型腔瞬间开始,到达预定增压压力所需时间,也就是增压阶段比压由压射比压上升到增压比压所需的时间。
从压铸工艺角度来说,这一时间越短越好。
但压铸机压射系统的增压装置所能提供的增压建压时间是有限度的,性能较好的机器最短建压时间也不少于0.01s。
增压建压时间取决于型腔中金属液的凝固时间。
凝固时间长的合金,增压建压时间可长些,但必须在内浇口凝固之前达到增压比压,因为合金一旦凝固,压力无法传递,即使增压也起不了压实作用。
因此压铸机增压装置上,增压建压时间的可调性十分重要。
- 1、下载文档前请自行甄别文档内容的完整性,平台不提供额外的编辑、内容补充、找答案等附加服务。
- 2、"仅部分预览"的文档,不可在线预览部分如存在完整性等问题,可反馈申请退款(可完整预览的文档不适用该条件!)。
- 3、如文档侵犯您的权益,请联系客服反馈,我们会尽快为您处理(人工客服工作时间:9:00-18:30)。
职业教育材料成型与控制技术专业
教学资源库
《铝合金铸件铸造技术》课程教案
压力铸造
—压铸工艺参数(速度)
制作人:刘洋
陕西工业职业技术学院
压力铸造—压铸工艺参数(速度)
一、压射速度
压射速度又称冲头速度,它是压室内的压射冲头推动金属液的移动速度,也就是压射冲头的速度。
压射过程中压射速度是变化的,它可分成低速和高速两个阶段,通过压铸机的速度调节阀可进行无级调速。
压射第一、第二阶段是低速压射,可防止金属液从加料口溅出,同时使压室内的空气有较充分的时间逸出,并使金属液堆积在内浇口前沿。
低速压射的速度根据浇到压室内金属液的多少而定,可按表1选择。
压射第三阶段是高速压射,以便金属液通过内浇口后迅速充满型腔,并出现压力峰,将压铸件压实,消除或减小缩孔、缩松。
表1 低速压射速度的选择
计算高速压射速度时,先由表2确定充填时间然后按下式计算:
u高=4V[l+(n-l)×0.1]/(πd2t)
式中u高—高速压射速度(m/s);
V—型腔容积,包括溢流槽部分及浇注系统部分(m3);
n—型腔数;
d—压射冲头直径(m);
t—填充时间(s)。
按式计算的高速压射速度是最小速度,一般压铸件可按计算数值提高
1.2倍,有较大镶件的压铸件或大模具压小铸件时,可提高至1.5~2倍。
二、充型速度
金属液通过内浇口处的线速度称为充型速度,又称内浇口速度。
它是压铸工艺的重要参数之一。
选用内浇口速度时,请注意如下几点: (1)铸件形状复杂或薄壁时,内浇口速度应高些;
(2)合金浇入温度低时,内浇口速度可高些;
(3)合金和模具材料导热性能好时,内浇口速度应高些;
(4)内浇口厚度较厚时,内浇口速度应高些。
计算高速压射速度时,按下式计算:
υ/V=πD2/4F
式中V—压射速度(m/s);
υ—充型线速度(m/s);
D—压室或冲头截面直径(m);
F—内浇口直径(m)。
一般压铸件可按计算数值提高1.2倍,有较大镶件的压铸件或大模具压小铸件时,可提高至1.5~2倍。