精密五金模具设计作业标准-等高套筒使用
模具作业标准
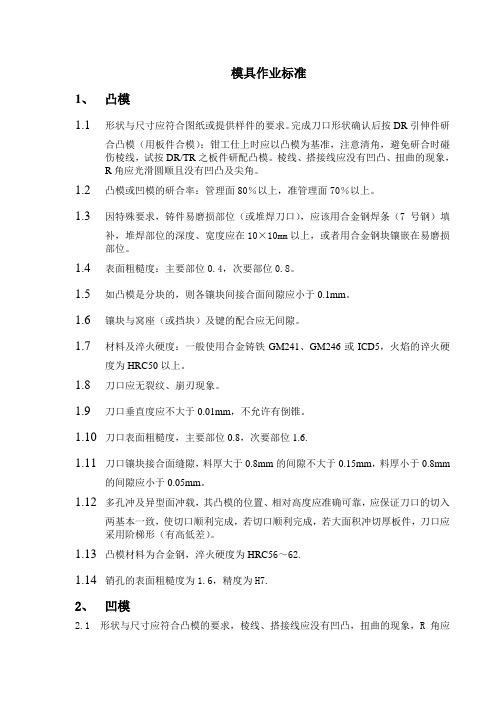
模具作业标准1、凸模1.1形状与尺寸应符合图纸或提供样件的要求。
完成刀口形状确认后按DR引伸件研合凸模(用板件合模):钳工仕上时应以凸模为基准,注意清角,避免研合时碰伤棱线,试按DR/TR之板件研配凸模。
棱线、搭接线应没有凹凸、扭曲的现象,R角应光滑圆顺且没有凹凸及尖角。
1.2凸模或凹模的研合率:管理面80%以上,准管理面70%以上。
1.3因特殊要求,铸件易磨损部位(或堆焊刀口),应该用合金钢焊条(7号钢)填补,堆焊部位的深度、宽度应在10×10mm以上,或者用合金钢块镶嵌在易磨损部位。
1.4表面粗糙度:主要部位0.4,次要部位0.8。
1.5如凸模是分块的,则各镶块间接合面间隙应小于0.1mm。
1.6镶块与窝座(或挡块)及键的配合应无间隙。
1.7材料及淬火硬度:一般使用合金铸铁GM241、GM246或ICD5,火焰的谇火硬度为HRC50以上。
1.8刀口应无裂纹、崩刃现象。
1.9刀口垂直度应不大于0.01mm,不允许有倒锥。
1.10刀口表面粗糙度,主要部位0.8,次要部位1.6.1.11刀口镶块接合面缝隙,料厚大于0.8mm的间隙不大于0.15mm,料厚小于0.8mm的间隙应小于0.05mm。
1.12多孔冲及异型面冲载,其凸模的位置、相对高度应准确可靠,应保证刀口的切入两基本一致,使切口顺利完成,若切口顺利完成,若大面积冲切厚板件,刀口应采用阶梯形(有高低差)。
1.13凸模材料为合金钢,淬火硬度为HRC56~62.1.14销孔的表面粗糙度为1.6,精度为H7.2、凹模2.1形状与尺寸应符合凸模的要求,棱线、搭接线应没有凹凸,扭曲的现象,R角应光滑圆顺且没有凹凸及尖角。
2.2工作部位表面粗糙度:主要部位低于0.8,次要部位1.6,凹模口圆角处粗糙度不低于0.4。
2.3因特殊要求,铸件易磨损部位(或堆焊刀口),应该用合金钢焊条填补,堆焊部位的深度、宽度应在10×10mm以上,或者用合金钢块镶嵌在易磨损部位。
五金模具规范要求

五金模具规范要求第一篇:五金模具规范要求五金冲压模具规范要求----德之佳为了规范和保证五金冲压模具品质、提高生产效率及结合我司实际情况,特制定本规范要求。
具体要求如下:结构及工艺要求:1.所有模具都必须有导柱、导套,特殊模具除外,但须和模具负责人沟通协定2.模具垫板、模座必须足够厚足够宽,防止模座(板)变形,16-25T模座(板)厚度≥25mm,30-40T模座(板)厚度≥30mm,60T及以上模座(板)厚度≥35mm;模柄要求使用标准模柄3.凹凸模及重要工作部件必须做真空热处理,冲裁硬度HRC58-60度,压型硬度HRC55-56度,不接受利用火焰枪直接做热处理4.推料、卸料机构必须灵活,无干涉现象5.所有活动部件应平稳灵活、无滞止干涉现象6.冲孔、落料的漏料孔必须保证通畅7.所有紧固件必须锁紧无松动,起限高作用的长螺丝需要有等高套或加用螺母锁死8.模具要求便于操作且安全,当模具需要有定位时必须要有定位外观要求:1.模具零部件不允许有裂纹,工作零部件表面不允许有划痕、机械损伤、锈蚀等表面缺陷2.凹凸模刃口及侧刃等必须锋利,不允许有蹦刃、缺刃和机械损伤3.凹凸模及工作面必须是光面,不接受没有处理的线割纹等不良表面4.模具外观面要求平整,不允许有锯齿纹等类似的粗糙面包装要求:1.必须在模具正面非工作区打上模具铭牌,铭牌内容:模具名称、出厂日期、供应商2.模具出厂前应清洗干净,所有工作件零件表面应涂覆防锈剂,不接受锈蚀的模具3.模具外观面清洗后需要涂覆油漆做防腐处理,不接受没有做涂覆处理的模具送样及送货要求:1.模具在送货前,必须先送样确认,每套产品必须送至少10PCS 样品,送样材料可以由我司提供2.模具负责人确认样品符合要求后再通知模具商送货3.送货时模具商必须派至少1人和我司维修工一起试模,模具负责人确认模具状况和加工出来的产品是否符合要求售后服务要求:1.所有冲压模具工作部件要求在10万次或6个月内免费维修,除工作部件外如模架部分等要求保修1年,我司人为原因除外2.模具维修时须遵循先报价且双方确认报价后再维修的原则注:1.出厂日期为最后确认模具的日期2.按照每月4周,每周冲压4000次计算,6个月计96000次3.如有一些特殊五金冲压模具不能符合本规范要求时,模具商须和模具负责人沟通协定4.本规范要求最终解释权利归本公司所有,且保留不断修改的权利5.本公司保留因供应商模具设计不当而造成损失要求赔偿的权利编制:杨芬洪审核:日期:版本:A/0第二篇:五金模具知识五金模具知识:模具基础知识 2009/9/28/10:02 来源:机械专家网[慧聪五金网]模具的基本构成(1)前模(母模)(定模),(2)后模(公模)(动模),(3)嵌件(镶件),(4)行位(滑块),(5)斜顶,(6)顶针,(7)浇口(入水口)2.模具制品形状对制品的影响壁厚,几何形状,会影响成形收缩率,脱模斜度大小。
五金模具标准件

五金模具标准件目录 (2)1、内导柱、导套 (3)2、外导柱、导套 (4)3、内六角螺丝 (8)4、固定销 (10)5、弹簧 (11)6、等高套筒 (14)7、顶料销 (15)8、止符螺丝 (18)9、两用销 (19)10、导正销 (21)11、圆冲子 (23)12、优力胶 (25)13、检测销 (25)第一节:内导柱、导套一、主要功能:内导柱主要用于模板间和上、下模间的导正。
内导套主要与内导柱相配合导正作用。
二、相关代号、规格及参数:1、代号:内导柱为“GP”,如GP20-80=>4 表示内导柱直径为∮20mm,长度为80mm,共4支。
内导套为肩型“GA”和直杆型“GB”,如GA20-25=>4 表示内导套内径为∮20mm,长度为25mm,共4支。
2、规格及参数:(见下图)三、选用原则:1、通常以直径较大的来优先设计,最主要还是根据模具的大小来选择直径的大小。
2、冲孔(或连续)模上模内导柱长度选取原则:一般情况下,开模时内导柱伸出打板面15~20MM,例图(a);当下模定位块(或导料块)等伸出模板面很高时,导柱伸出打板面的长度L=定位块(或导料块)伸出模板面的长度H+(5-7)MM(保证模具闭模过程中,内导柱先导正,定位块后进入打板)例图(b)(图a) (图b)四、排配原则:1、导柱一般排在模板的四个角落上,其孔边距板边最小处不低于12mm。
2、如果选用两柱,可排在斜对角,也可根据实际情况排。
3、在排配过程中要注意防呆,其防呆一般采用以左下角一孔向料带的平行方向偏移10MM以上来防呆。
4、内导套一般适用于精密模具上,产品形状或位置要求准确的情况下使用。
第二节:外导柱、导套一、主要功能:外导柱的功能主要是用于上、下模的导正,保证上、下模的相对位置。
外导套主要与外导柱相配合导正作用。
二、相关代号、规格及参数:1、代号:无附钢珠的外导柱、导套为“SGP组件”,如:SGP组件32-120=>4 表示外导柱直径为∮32mm,长度为120mm,无附钢珠的外导柱、导套共4支。
精密模具设计加工要求和标准

有推板结构的复位杆 的高度要取整数,不
能有小数点.
斜导柱沉头的深度可以深 斜0斜导H.100导柱Am..11S柱沉mmmC-沉头mmO0.--头标的1005..的准深11m55深;度mmm严,度mm可要格,,可以要要用来以深用用讲深,
斜导柱H能AH用SAC螺SOC丝O锁的要尽 可能用螺丝锁!
滑块座的这个位置 要导R5.0-R6.0;但 要根据实际工件的 大小来适当的加大
或减小
铲鸡的这个位置要 导R5.0-R6.0;但要 根据实际工件的 大小来适当的加大
或减小
避空 0.1mm
铲鸡的两个侧边 非定位的两边.单 边要避空0.1mm
滑块座滑出模 板的长度不可 以超出滑块座
自身的1/3
拉料杆顶针的 直径标准为
5.0mm
图为版本日 期章
图为年份 的日期章
图为月份 的日期章
8) 流道与进胶口 的位置有火花纹的
都需要抛光
6) 模仁的高度 要准确,公差要
求在+/-
0.01mm
7) 模仁的长度与宽 度要准确,公差要
求在-0.01mm
模仁
5) 模仁表面能 够磨尽量磨,不 能磨的尽量留
刀痕
4) 模仁底部上来 8mm要磨0.05mm的
避空(共ห้องสมุดไป่ตู้边)
1) 模仁的表面与模 板的表面要做防呆 的标志(防止模仁
顶针要比倒 扣底2.0mm
顶胶口的顶 针要做凹下 或凸出用来 固定流道,不 让流道自动
掉下.
10° 4mm-5mm
2.0mm
11) 所有大小 镶件都要做 好相应的字 码标示,并且 要按顺序来
做.
10) 所有的镶件, 镶针的沉头都
要做导角.
套筒的规范标准
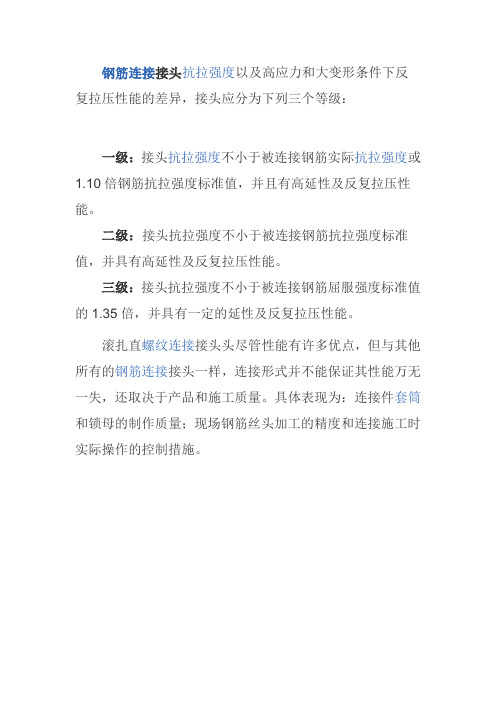
钢筋连接接头抗拉强度以及高应力和大变形条件下反复拉压性能的差异,接头应分为下列三个等级:
一级:接头抗拉强度不小于被连接钢筋实际抗拉强度或1.10倍钢筋抗拉强度标准值,并且有高延性及反复拉压性能。
二级:接头抗拉强度不小于被连接钢筋抗拉强度标准值,并具有高延性及反复拉压性能。
三级:接头抗拉强度不小于被连接钢筋屈服强度标准值的1.35倍,并具有一定的延性及反复拉压性能。
滚扎直螺纹连接接头头尽管性能有许多优点,但与其他所有的钢筋连接接头一样,连接形式并不能保证其性能万无一失,还取决于产品和施工质量。
具体表现为:连接件套筒和锁母的制作质量;现场钢筋丝头加工的精度和连接施工时实际操作的控制措施。
精密五金模具设计作业标准-尺寸标注作业标准

尺寸標注作業標准
1.五金零件代號文字和注解文字字高設定為
2.5MM(依圖框1:1,若圖框
比例放大,則字高也按比例放大)
2.文字顏色設定為Bylayer.
3.標注文字字體名稱:STYLE NAME:STANDARD
對應文字檔TXT.SHX : CHINESET.SHX
寬高比系數WIDTH FACTOR: 0.8
4.標註形式的選擇: 產品圖和工序圖的標注統一為二位小數
模板和模具零件圖的標注統一為三位小數
5.視圖一般採用1:1比例繪製,標註的尺寸值一般是計算機自動測量的值,不得用手改動編輯尺寸文字值.對於零件圖,要求標示清楚最大外形尺寸,及容易量測的尺寸,對於需要研磨的尺寸要標注清楚和合理。
6.標注尺寸大小的設定,依圖框1:1時,尺寸高度設定為0.18,箭頭大小為0.18,Use overall scale of 設定為:10,圖框放大時,僅將Use overall scale of 的設定按比例放大,其它不變。
套筒设计说明书
课程设计说明书----套筒班级:设计者:组员:设计时间:2011-12-8指导教师:前言机械加工工艺课程设计是我们对数控加工工艺这门课的充分利用。
通过这次的课程设计我们可以将我们所学的知识运用到实践中。
如在加工工艺过程设计中,对于加工路线的定制及加工余量,工序尺寸的确定,我们都得到了实践。
此外,在设计加工工序的过程中,对机床的选择,刀具的选择及切削知识等都有进一步的了解。
因此机械加工工艺课程设计实际上是我们对机械加工知识的综合运用。
在实际设计过程中,我们碰到了许多问题,解决问题的过程也是我们学习的过程。
通过这两周的学习我们了解了设计过程中,我们认识到自己的不足。
希望在这次实训中对自己未来的将从事的工作进一步适应的锻炼。
希望自己在设计中能锻炼自己的分析的能力,解决问题的能力,查资料的能力等。
由于本人能力有限,设计尚有许多不足之处,希望老师们给予指导。
目录一、零件图二、工件工艺分析三、零件制作工艺设计四、定位误差分析五、加工方法及加工路线六、确定加工参数七、小结八、参考资料一、零件图二、工件工艺分析:1.工件材料:20号钢削切、加工性良好。
2.零件组成表面:外圆表面(Φ38,Φ18),内表面(Φ12),两端面,内﹑外台阶面,内﹑外退刀槽,内﹑外倒角。
3.主要表面分析:Φ12内孔既是支承其它零件的支承面,亦是本零件的主要基本面;Φ18外圆及其台阶面亦用于支承其它零件。
4.主要技术条件:Φ18外圆与Φ12内孔的同轴度控制在0.02㎜范围内;台阶面与Φ12内孔的垂直度控制在0.025㎜范围内;Φ12内孔本身的尺寸公差为0.019㎜;粗糙度0.8;零件热处理硬度HRC50-55.三、零件制造工艺设计1.毛坯的选择:根据零件材料为20钢,生产类型为中批生产,零件直径尺寸差异较大,零件壁薄、刚度低、易变形,加工精度要求高,零件需经淬火处理等多方面因素,在棒料与模锻间做出选择:模锻件。
2.基准分析:主要定位基准应为Φ12内孔中心;加工内孔时的定位基准则为Φ18外圆中心。
等高套筒规格和参数表
等高套筒规格和参数表摘要:I.引言- 介绍等高套筒的定义和作用II.等高套筒的规格- 定义和分类- 我国常用的等高套筒规格III.等高套筒的参数- 关键参数及其作用- 我国常用的等高套筒参数IV.等高套筒的选择和使用- 如何选择合适的等高套筒- 等高套筒的使用方法V.总结- 概括等高套筒规格和参数的重要性- 对未来等高套筒发展的展望正文:I.引言等高套筒,作为一种常见的工具,广泛应用于各种工业领域。
它主要用于连接两个相同规格的螺纹元件,使连接的元件在同一高度上,以确保螺纹连接的稳定性和可靠性。
等高套筒规格和参数的正确选择,对保证连接质量和提高工作效率具有重要意义。
II.等高套筒的规格等高套筒的规格主要根据其内径、长度和螺纹规格来划分。
根据我国现有的标准和实际需求,常用的等高套筒规格主要有M10、M12、M16、M20、M24等几种。
此外,还有其他特殊规格的等高套筒,如加长型、减径型等,以满足不同场合的需求。
III.等高套筒的参数等高套筒的参数主要包括以下几个方面:1.材质:等高套筒的材质主要有碳钢、合金钢和不锈钢等,用户应根据实际需求选择合适的材质。
2.硬度:等高套筒的硬度直接影响其使用寿命和连接质量,通常硬度应在HRC40-50之间。
3.精度:等高套筒的精度包括尺寸精度和螺纹精度,用户应根据实际需求选择合适的精度等级。
IV.等高套筒的选择和使用1.选择合适的等高套筒规格:用户应根据需要连接的螺纹元件规格,选择合适的等高套筒规格。
2.选择合适的等高套筒参数:用户应根据实际需求,选择合适的材质、硬度和精度等级。
3.等高套筒的使用方法:在使用等高套筒时,应先将两个需要连接的螺纹元件分别插入等高套筒的内外螺纹槽中,然后用力旋转等高套筒,使螺纹元件紧密连接。
V.总结等高套筒规格和参数的正确选择,对保证连接质量和提高工作效率具有重要意义。
用户应根据实际需求,结合我国现有的标准和产品性能,选择合适的等高套筒规格和参数。
冲压模_等高套筒安装位置_解释说明以及概述
冲压模等高套筒安装位置解释说明以及概述1. 引言1.1 概述在冲压加工过程中,冲压模起着至关重要的作用。
它们被广泛应用于生产各种金属零件和产品,如汽车零部件、家电配件等。
而等高套筒安装位置则是冲压模中一个重要的组成部分,它对于冲压加工的质量和效率有着不可忽视的影响。
本文将对冲压模等高套筒安装位置进行详细解释说明,并阐述其在冲压加工中的重要性。
首先,我们将介绍冲压模的定义与作用以及其结构与组成。
然后,我们将重点关注等高套筒安装位置,包括其定义与原理、安装方法与注意事项以及实际应用案例分析。
最后,我们将探讨等高套筒安装位置的重要性,包括提高产品质量与效率、避免冲压过程中的问题与故障以及经济效益和可持续发展考虑。
通过本文的阐述和探讨,读者可以进一步了解冲压模等高套筒安装位置,并认识到其在冲压加工中不可替代的地位。
同时,本文也将为未来的研究方向提供展望和建议,以促进相关领域的发展与创新。
笔者希望通过本文的撰写,能够对读者有所启发,增加对冲压模等高套筒安装位置的了解和认识,并为相关领域的研究和实践提供一定的参考价值。
2. 冲压模2.1 定义与作用冲压模是一种用于金属加工的关键工具。
它是由金属材料制成,具有特定的形状和结构,用于将金属板材或其他金属材料通过冲击、挤压等方式进行变形加工。
冲压模广泛应用于汽车制造、家电制造、航空航天等行业中。
2.2 结构与组成冲压模通常由上模座、下模座、导柱、导套、上模和下模等部分组成。
上模座和下模座是支撑和固定冲压模的基础部件,导柱和导套起到引导和保证上下模对准的作用,上模和下模则根据加工要求的不同而拥有各自独特的形状和结构。
2.3 使用场景冲压模主要应用于批量生产中,特别适合进行大规模、高效率的金属加工。
它可以用于制造各种零部件,如汽车车身零部件、电器外壳等。
在汽车制造行业中,使用冲压技术可以实现快速、精确地形成复杂的汽车零部件,并提高产品的质量和稳定性。
冲压模也可以用于研究和验证新产品设计的可行性,以及进行小批量试制。
五金模具设计规范大全(一)
冲压模具设计标准目录编号內容版本发版日2007 AA01 图框填写作业标准 1.01.0 1.0 1.0 1.0 1.0 1.0 1.0 1.0 1.0 1.0 1.0 1.0 1.0 1.0 1.0 1.0 1.0 1.0 1.0 1.0 1.0 1.0 1.0 1.0 2007 2007 2007 2007 2007 2007 2007 2007 2007 2007 2007 2007 2007 2007 2007 2007 2007 2007 2007 2007 2007 2007 2007 2007AA02 模具图面图层作业标准AA03 尺寸标注作业标准AA04 展开图画法标准AA05 工程图画法标准AA06 产品展开计算标准AA07 结构图画法标准AA08 图示注解作业标准AA09 共用件注解标准AA10 设变图档作业标准AA11 模具图档作业规范AA12 公差及间隙标准AA13 五金零件加工要求AA14 板(零)件图画法作业规范AA15 中英文对照AA16 零部件作业规范(字模冲子)AA17 五金零件作业规范(弹簧)AA18 五金零件作业规范(顶料销)AA19 五金零件作业规范(导正销)AA20 五金零件作业规范(止付螺丝)AA21 零部件作业规范(圆冲子)AA22 零部件作业规范(异形冲子)AA23 零部件作业规范(切边冲子)AA24 零部件作业规范(折刀)AA25 零部件作业规范(滑块)2007 2007 2007 2007 2007 2007 2007 2007 2007 2007 2007 2007 2007 2007 2007 2007AA26 零部件 作业规范(压线冲子) AA27 零部件作业规范(压毛边冲子) AA28 零部件作业规范(压筋冲子) AA29 零部件作业规范(定位销,块) AA30 零部件作业规范(定位支承块) AA31 零部件作业规范(下模入子) AA32 加工组立工艺性 1.0 1.0 1.0 1.0 1.0 1.0 1.0 1.0 1.0 1.0 1.0 1.0 1.0 1.0 1.0 1.0AA33 小折模具结构(沙拉孔) AA34 小折模具结构(卷圆压平) AA35 模板备料作业规范(垫板夹板) AA36 模板备料作业规范 AA37 模座备料作业规范 AA38 滚轴成形公模退0.1mm 说明 AA39 铆合螺帽模具结构说明 AA40 带 N 折的成形模结构AA41 零部件作业规范(细小圆孔冲子) AA42 高凸成形方法标准件编码说明03第1页1 标准件编码规定0 3 □□—□……□—□□扩充编码 ○4 规格编码 小系列编码 大系列编码○ 2 3 ○ ○12标准件类编码表 序号 1 标准件名称 标准件分类码01 序号 标准件名称 标准件分类码21 螺丝 螺母 21 22 23 24 25 26 27浇口套(咀嘴) 2 3 02 03 04 05 06 07 08 09 10 11 12 13 14 15 16 17 18 19 20定位环 带钢球螺丝 顶出限位 22 23 24 25 26 27垫片 4 防松弹簧垫片冲针 5 支承柱 6 弹簧 锥度内6角螺塞垃圾钉7 顶针 8 内导柱(导套) 外导柱(导套)定位销 9 10 11 12 13 14 15 16 17 18 19 20顶料销 两用销 弹钉 ………………………引导销 检知销 等高套筒 华司 限位柱 下模圆形刀口 脱料圆形1 整套模具编码规定0 5 □□ □□□□□□-套数编码 ○ 4 5 ○ 月份编码 年份编码 ○ 3 ○ 等级编码 2 ○ 1大系列编码1.1列表说明○○2 ○3 ○4 ○5 1 代码说明 代码 06 说明 06年07年 08年代码 01 说明1月2月 3月 代码 01说明0102 0304 051级 2级 3级 4级 5级07 02 02 080303流水号05…… ………… …………9999年 12 12月 99(1)模具等级列表说明 代码 等级01 02 03 04 05 1级2级3级4级5级上盖板 无 S45C+M S45C+M S45C+M S45C+M S45C+铝合金 +M+TZ+YJ 上模座 无 S45C+M S45C+M S45C+M+TZ+JG上垫板 上夹板 S45C S45C 无 D2+H D2+H+W D2+H D2+H D2+H SKD11+H+S D2+H+W SKD11+CO+S D2+H+W SKD11+SC+S D2+H+W 背垫板 D2+H+W 脱料板无 D2+H+W SKD11+H+S SKD11+H+S D2+H+W SKD11+CO+S SKD11+CO+S D2+H+W SKD11+SC+S+PG SKD11+SC+S+PGD2+H+W 说 明下模板 S45C S45C 无 D2+H+W 下垫板D2+H+W 下模座 S45C+M+W SKD11+D2+W D2+SKD11+W SKD11+D2+W无S45C+M+WS45C+M+W+T2+JGS45C+M+W+TZ凹模入了 脱板入子 夹板入子 外导柱 无 SKH9+SKD11+S WC+SKH9+SKD11+S+PG WC+SKH9+SKD11+S+PG 无 SKD11+S SKD11+WC+S+PG SKD11+WC+SKH9+S+PG无 SKH9+SKD11+S WC+SKH9+SKD11+S+PG WC+SKD11+SKH9+S+PG无 钢珠导柱钢珠导柱 铜珠导柱 “一”字 导柱内导柱“一”字导柱 “一”字导柱钢珠导柱铜钛钨钢导柱(2)说明A 板件处理:H 热处理、深冷CO 、超冷SC 、调质T2、阳极YJ ;B 材质:WC 、SKH9、SKD11、D2、S45C ;C 加工方式:快走丝W 、慢走丝S 、光研PG 、内研磨JG 、铣床M 。