精密注塑成型PVT控制技术
塑料制品精密成型的几种方法
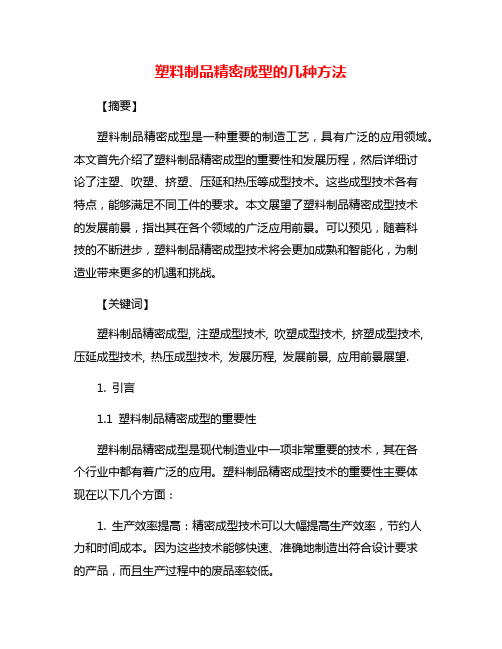
塑料制品精密成型的几种方法【摘要】塑料制品精密成型是一种重要的制造工艺,具有广泛的应用领域。
本文首先介绍了塑料制品精密成型的重要性和发展历程,然后详细讨论了注塑、吹塑、挤塑、压延和热压等成型技术。
这些成型技术各有特点,能够满足不同工件的要求。
本文展望了塑料制品精密成型技术的发展前景,指出其在各个领域的广泛应用前景。
可以预见,随着科技的不断进步,塑料制品精密成型技术将会更加成熟和智能化,为制造业带来更多的机遇和挑战。
【关键词】塑料制品精密成型, 注塑成型技术, 吹塑成型技术, 挤塑成型技术, 压延成型技术, 热压成型技术, 发展历程, 发展前景, 应用前景展望.1. 引言1.1 塑料制品精密成型的重要性塑料制品精密成型是现代制造业中一项非常重要的技术,其在各个行业中都有着广泛的应用。
塑料制品精密成型技术的重要性主要体现在以下几个方面:1. 生产效率提高:精密成型技术可以大幅提高生产效率,节约人力和时间成本。
因为这些技术能够快速、准确地制造出符合设计要求的产品,而且生产过程中的废品率较低。
2. 产品质量稳定:通过精密成型技术,可以确保所生产出的塑料制品具有高度的一致性和准确性,保证产品的质量稳定。
这对于一些对产品精度要求比较高的行业尤为重要。
3. 节约原材料:精密成型技术可以有效利用原材料,减少废料产生,降低生产成本。
这对于资源节约和环境保护都有着重要的意义。
4. 创新和发展:精密成型技术的不断发展也促进了塑料制品行业的创新和发展。
通过不断地改进和优化技术,可以开发出更多更高质量的塑料制品,满足市场的需求。
塑料制品精密成型技术的重要性不可忽视,它不仅提高了生产效率和产品质量,同时也促进了行业的创新和发展。
在未来,随着科技的不断进步,这项技术将会有着更加广阔的应用前景。
1.2 发展历程塑料制品精密成型技术的发展历程可以追溯到20世纪初,当时的塑料制品生产主要依靠传统的手工和半自动生产方式。
随着工业化的进程和科技的发展,塑料制品行业开始引入一些自动化设备和机械操作,提高了生产效率和产品质量。
什么叫做精密注塑成型

什么叫做精密注塑成型一、什么叫做精密注塑成型?精密注塑成型,从严格意义上来说,指的是通过注塑机设备生产出来的塑胶制品的尺寸精度,可以达到0.01mm以下,通常在0.01~0.001mm之间的一种注射成型生产方式。
“精密注射成型”这一概念,主要是区别于“常规注射成型”,随着高分子材料和微电子技术的高速发展,电子电路高度集成化,使得工业设备零件逐渐发展为高性能化、高精度化、轻量化、小型化和微型化。
这样,精密塑胶制件因为符合高精度要求,同时具备良好的机械、力学性能以及尺寸稳定性等优点,在机械、电子、仪器、通讯、汽车和航空仪表等行业领域里,取代了部分高精度的金属零件而得到了广泛应用。
由精密注塑成型的定义可知,精密塑胶件的尺寸公差范围是非常窄的。
而实际上,塑胶成型行业内公认,当塑胶制件的尺寸公差在0.1mm以下,或者说制件尺寸正负公差在0.1mm以下,都可称之为精密成型,制件的尺寸公差达到微米级的,可以称之为超精密级注塑成型。
相对精密注塑成型而言,普通注塑成型的制件的尺寸公差通常在0.1mm以上,制件的尺寸公差范围相对较宽,并且随着制件体积或重量的增加,制件的尺寸公差也会有所增加。
值得一提的是,由于材料本身的性质和加工手段不同,不能把塑料制件的精度与金属零件的精度等同起来。
塑料制品最高的精度等级是三级精度,即尺寸公差可达0.001mm以下,而金属零件尺寸可分为十四级,加工精度分有九级。
、精密注塑成型有哪些特点?(1)制件的尺寸精度高,公差范围小,即有高精度的尺寸界限精密塑胶制件的尺寸偏差会在0.03mm以内,有的甚至小到微米级,检测工具依赖于投影仪。
(2)制品重复精度高主要表现在制件重量偏差小,重量偏差通常在0.7%以下。
(3)模具的材料好,刚性足,型腔的尺寸精度、光洁度以及模板间的定位精度高(4)采用精密注射机设备(5)采用精密注射成型工艺精确控制模具温度、成型周期、制件重量、成型生产工艺。
(6)选择适应精密注射成型的材料PPS、PPA、LCP、PC、PMMA、PA、POM、PBT、加玻纤或碳纤的工程材料等。
如何进行精密注塑

如何进行精密注塑(时间:2006-12-30 10:10:31 共有834人次浏览)塑料电子零部件大都采用注射成型,由于这些塑料件本身具有较高的设计精度,使用特殊的工程塑料加工,对这些塑料件不能采用常规的注射成型,而必须采用精密注射成型工艺技术。
为了保证这些精密塑料件的性能、质量与可靠性及长期使用的稳定性,注射成型出质量较高、符合产品设计要求的塑料制品,必须对塑料材料、注塑设备与模具设计及注塑工艺以及注塑现场管理进行完善。
我们通常说的精密注塑成型是指注塑制品的外型精度应满足严格的尺寸公差、形位公差和表面粗糙度。
要进行精密注塑必须有许多相关的条件,而最本质的是塑料材料、注塑模具、注塑工艺和注塑设备这四项基本因素。
设计塑料制品时,应首先选定工程塑料材料,而能进行精密注塑的工程塑料又必须选用那些力学性能高、尺寸稳定、抗蠕变性能好、耐环境应力开裂的材料。
其次应根据所选择的塑料材料、成品尺寸精度、件重、质量要求以及预想的模具结构选用适用的注塑机。
在加工过程中,影响精密注塑制品的因素主要来自模具的温度、注塑工艺控制,以及生产现场的环境温度和湿度变化幅度及后天产品退火处理等方面。
就精密注塑而言,模具是用以取得符合质量要求的精密塑料制品的关键之一,精密注塑用的模具应切实符合制品尺寸、精度及形状的要求,模具材料应严格选取。
但即使模具的精度、尺寸一致,其模塑的塑料制品之实际尺寸也会因收缩量差异而不一致。
因此,有效地控制塑料制品的收缩率在精密注塑技术中就显得十分重要。
注塑模具设计得合理与否会直接影响塑料制品的收缩率,由于模具型腔尺寸是由塑料制品尺寸加上所估算的收缩率求得的,而收缩率则是由塑料生产厂家或工程塑料手册推荐的一个范围内的数值,它不仅与模具的浇口形式、浇口位置与分布有关,而且与工程塑料的结晶取向性(各向异性)、塑料制品的形状、尺寸、到浇口的距离及位置有关,同时和模具冷却分布系统紧密相关。
影响塑料收缩率的主要有热收缩、相变收缩、取向收缩、压缩收缩与弹性回复等因素,而这些影响因素与精密注塑制品的成型条件或操作条件有关。
基于注塑机的ABS树脂PVT特性在线测试

1
实验部分
1 1 原料及样品 1 1 1 原料 ABS 树脂, PA - 757K, 密度 1 05 g/ cm 3 , 镇江奇 美塑料有限公司生产。 1 1 2 样品 样品的形状呈碗状 , 碗沿端有一段圆筒直段 , 长 6 mm, 以方便进行加压测试。呈碗状的目的是为研 究样品形状对聚合物 PVT 特性的影响。样品形状 及相关尺寸参见图 1。 1 2 实验设备 聚合物 PVT 特性测试模具及数据采集系统, 自 行设计制造; 注塑 机, Allrounder 270S 500 - 60, 德国 Arburg 公司 ; 电子天平 , 50224, 余姚市 金诺天平仪 器有限公司。 采用聚合物 P VT 关系在线测试技术的测试设 备 , 主要由测试模具、 模温控制系统、 数据采集系统 3 部分组成, 测试模具的详细结构示意图和实物照 片可分别参见图 2 和图 3。 测试模具以模具型腔作为测试样品室, 通过改 变压力和温度条件来测试模腔体积的变化。测试样 品的浇口前端设置有浇口阀 , 在测试时关闭, 以保证 型腔中测试样品质量恒定。测试压力直接通过注塑
图3 Fig. 3
测试模具实物照片
Photograph of the testing mold
图 1 碗状样品 Fig . 1 Dimensions of the conically shaped sample
1 4 测试模式 聚合物 PVT 特性测试有等压和等温两种测试 模式。等压模式即压力恒定 , 改变温度, 温度可采用 加热升温或冷却降温的方式 , 测定比容同温度的变 化 ; 测定一 组曲线过后, 再将压力改变 为另一恒定 值 , 进行下一组曲线的测试。等温模式即采用温度 恒定, 改 变压力, 测定比容同压 力的变化。聚合物 PVT 特性测试模具可采用多种测试模式, 本文实验 采用的是等压模式升温 - 升压的测试模式。
注塑产品质量的控制
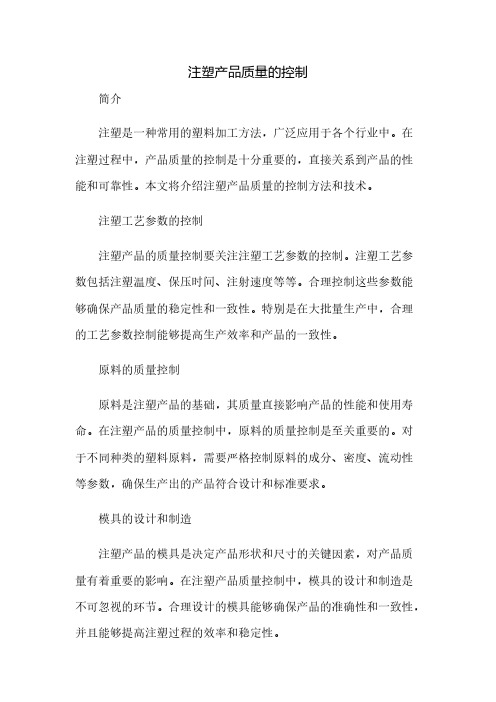
注塑产品质量的控制简介注塑是一种常用的塑料加工方法,广泛应用于各个行业中。
在注塑过程中,产品质量的控制是十分重要的,直接关系到产品的性能和可靠性。
本文将介绍注塑产品质量的控制方法和技术。
注塑工艺参数的控制注塑产品的质量控制要关注注塑工艺参数的控制。
注塑工艺参数包括注塑温度、保压时间、注射速度等等。
合理控制这些参数能够确保产品质量的稳定性和一致性。
特别是在大批量生产中,合理的工艺参数控制能够提高生产效率和产品的一致性。
原料的质量控制原料是注塑产品的基础,其质量直接影响产品的性能和使用寿命。
在注塑产品的质量控制中,原料的质量控制是至关重要的。
对于不同种类的塑料原料,需要严格控制原料的成分、密度、流动性等参数,确保生产出的产品符合设计和标准要求。
模具的设计和制造注塑产品的模具是决定产品形状和尺寸的关键因素,对产品质量有着重要的影响。
在注塑产品质量控制中,模具的设计和制造是不可忽视的环节。
合理设计的模具能够确保产品的准确性和一致性,并且能够提高注塑过程的效率和稳定性。
注塑设备的维护和保养注塑设备的维护和保养对于产品质量的控制也是至关重要的。
定期检查和保养设备能够保证设备的正常运行,提高生产效率和产品的稳定性。
特别是在大批量生产中,设备的故障可能会导致产品质量的下降和生产延误。
检测和检验在注塑产品的质量控制中,检测和检验是必不可少的环节。
通过对产品的尺寸、外观、性能等进行检测和检验,能够及时发现和解决问题,确保产品的质量稳定和一致性。
常用的检测方法包括尺寸测量、外观检查、物性测试等等。
注塑产品质量的控制是一个复杂的过程,需要从注塑工艺参数的控制、原料的质量控制、模具的设计和制造、设备的维护和保养等多个方面进行考虑。
通过合理控制这些环节,能够保证注塑产品的质量稳定和一致性,提高产品的性能和可靠性。
在实际生产中,应根据具体情况制定相应的质量控制方案,并不断优化和改进,以提高产品的竞争力和市场占有率。
注塑成型基础知识培训:温度控制,压力控制,成型周期

注塑成型基础知识培训:温度控制,压力控制,成型周期发表于 2012-5-24 13:18:18 |只看该作者注塑成型基础知识培训:温度控制,压力控制,成型周期注塑成型是一门工程技术,它所涉及的内容是将塑料转变为有用并能保持原有性能的制品。
注射成型的重要工艺条件是影响塑化流动和冷却的温度,压力和相应的各个作用时间。
一、温度控制1、料筒温度:注射模塑过程需要控制的温度有料筒温度,喷嘴温度和模具温度等。
前两程温度主要影响塑料的塑化和流动,而后一种温度主要是影响塑料的流动和冷却。
每一种塑料都具有不同的流动温度,同一种塑料,由于来源或牌号不同,其流动温度及分解温度是有差别的,这是由于平均分子量和分子量分布不同所致,塑料在不同类型的注射机内的塑化过程也是不同的,因而选择料筒温度也不相同。
2、喷嘴温度:喷嘴温度通常是略低于料筒最高温度的,这是为了防止熔料在直通式喷嘴可能发生的“流涎现象”。
喷嘴温度也不能过低,否则将会造成熔料的早凝而将喷嘴堵死,或者由于早凝料注入模腔而影响制品的性能3、模具温度:模具温度对制品的内在性能和表观质量影响很大。
模具温度的高低决定于塑料结晶性的有无、制品的尺寸与结构、性能要求,以及其它工艺条件(熔料温度、注射速度及注射压力、模塑周期等)。
二、压力控制:注塑过程中压力包括塑化压力和注射压力两种,并直接影响塑料的塑化和制品质量。
1、塑化压力:(背压)采用螺杆式注射机时,螺杆顶部熔料在螺杆转动后退时所受到的压力称为塑化压力,亦称背压。
这种压力的大小是可以通过液压系统中的溢流阀来调整的。
在注射中,塑化压力的大小是随螺杆的转速都不变,则增加塑化压力时即会提高熔体的温度,但会减小塑化的速度。
此外,增加塑化压力常能使熔体的温度均匀,色料的混合均匀和排出熔体中的气体。
一般操作中,塑化压力的决定应在保证制品质量优良的前提下越低越好,其具体数值是随所用的塑料的品种而异的,但通常很少超过20公斤/厘米2。
注塑成型技术

注塑成型技术注塑成型技术是一种常见的加工工艺,广泛应用于制造各种塑料制品。
它通过将熔化的塑料材料注入模具中,经过冷却和固化形成所需的产品。
本文将介绍注塑成型技术的工作原理、优势、应用领域以及未来发展方向等内容。
一、工作原理注塑成型技术主要由注射系统、模具系统、冷却系统、控制系统和辅助系统等组成。
首先,将塑料颗粒或粉末加热至熔化状态,然后通过注射系统将熔融的塑料注入到模具腔中。
随后,经过冷却和固化,将所需的产品从模具中取出。
在注塑成型过程中,需要注意控制以下因素:注塑压力、注塑速度、注射时间和冷却时间。
适当调节这些参数可以确保产品的质量和生产效率。
二、优势注塑成型技术具有许多优势,使其成为一种常用的塑料加工方法。
1. 生产效率高:注塑成型工艺可以实现连续生产,自动化程度高,生产效率较高。
2. 产品精度高:模具的设计和制造精度较高,可以生产出形状复杂、尺寸精确的产品。
3. 可塑性好:注塑成型工艺适用于各种不同类型的塑料材料,如聚丙烯、聚氯乙烯、聚苯乙烯等。
4. 成本低:由于注塑成型技术可以实现大规模连续生产,单个产品的生产成本相对较低。
5. 资源回收利用:废弃的塑料制品可以通过再次熔化和塑化再利用,降低了对资源的消耗。
三、应用领域注塑成型技术广泛应用于许多工业领域和日常生活中,以下是一些常见的应用领域:1. 电子电器:注塑成型技术可以用于生产各种电子设备外壳、插件、线束等。
2. 汽车工业:汽车零部件的生产通常采用注塑成型技术,如车灯、仪表盘、内饰件等。
3. 医疗器械:医用注射器、输液器和其他医疗器械都是通过注塑成型工艺制造的。
4. 家居用品:家具配件、塑料餐具、家用电器等都是使用注塑成型技术生产的。
5. 包装行业:塑料瓶、塑料桶、塑料盒等包装材料通常采用注塑成型工艺生产。
四、未来发展方向注塑成型技术在不断发展和创新的过程中,面临着一些挑战和机遇。
1. 环境友好型材料:随着环保意识的增强,未来的注塑成型技术可能会更加注重使用可降解和可回收的塑料材料。
PVT法工艺流程

PVT法工艺流程随着工业化的发展,各种工艺流程不断涌现,其中之一就是PVT法工艺流程。
PVT法(Pressure, Volume, Temperature法)是一种可用于制备高纯度材料的工艺流程,其基本原理是利用高压和高温对原料进行处理,以促使反应发生。
下面将详细介绍PVT法工艺流程的步骤和应用。
PVT法工艺流程分为以下几个步骤:原料准备、装载样品、施加压力、升温、冷却和卸载样品。
首先是原料准备。
在PVT法工艺流程中,选择适当的原料是非常重要的。
一般来说,原料应具有较高的纯度和良好的晶体结构。
常见的原料包括金属、合金、陶瓷和半导体等。
为了避免杂质的污染,原料应经过严格的清洁处理。
接下来是装载样品。
将经过清洁处理的原料放置在高温高压容器中,注意确保样品的均匀分布和紧密堆积。
样品的大小和形状可以根据不同的实验需求进行调整。
然后是施加压力。
在装载好样品后,需要施加一定的压力。
压力的大小可以根据具体实验设定,一般在几百兆帕至几千兆帕之间。
通过施加压力,可以使原料分子间距更加紧密,从而促进反应的进行。
接着是升温。
在施加了适当的压力后,需要将系统升温。
升温的速率和温度可以根据实验设计来调整。
在升温的过程中,原料会发生化学反应或结构相变。
这些反应或相变可以使原料更加纯净和有序。
然后是冷却。
在反应或相变完成后,需要将系统冷却至室温。
冷却的速率和温度也可以根据实验需求进行调整。
冷却过程中,原料会逐渐固化,并形成所需的结构和形貌。
最后是卸载样品。
在冷却完成后,可以打开高温高压容器,将样品取出。
取出样品后,可以对其进行表征和分析,以验证实验结果的准确性。
PVT法工艺流程在材料科学领域具有广泛的应用。
通过调控压力和温度等工艺条件,可以制备出具有良好晶体结构和高纯度的材料。
这些材料在微电子、光电、能源等领域具有重要的应用价值。
例如,在半导体器件制备中,PVT法可以制备出高质量的单晶硅材料;在光学器件制备中,PVT法可以制备出高透明度和低杂质的玻璃材料。
- 1、下载文档前请自行甄别文档内容的完整性,平台不提供额外的编辑、内容补充、找答案等附加服务。
- 2、"仅部分预览"的文档,不可在线预览部分如存在完整性等问题,可反馈申请退款(可完整预览的文档不适用该条件!)。
- 3、如文档侵犯您的权益,请联系客服反馈,我们会尽快为您处理(人工客服工作时间:9:00-18:30)。
精密注塑成型PVT控制技术新浪微博QQ空间人人网开心网更多
图1 聚合物典型PVT特性曲线
产效率。
综观当今注塑机市场,在保证制品质量的前提下,如何利用成熟的自动化设备,提高产品精度,降低废品、次品率及节约原材料、能源以降低成本,增强市场竞争,己引起国内外注塑机厂商的高度重视,为此采用先进的控制技术和管理手段已成为必然的趋势。
传统注塑机中的过程控制方法大多采用注射压力、保压压力、合模力、注射速度及注射量等参数作为控制量,称为机器变量。
这些变量由操作员根据经验和试模对注塑机预先输入控制参数,通常主要采用时间来控制每个阶段的开始和结束。
这些变量完全由注塑机本身决定,而与材料的特性关系不大。
参数控制作为控制系统的主要功能,需要对连续变化的过程参数,如温度、压力、位置和速度等进行精确的闭环控制。
由于注射过程主要参数都具有相当显著的非线性时变特性,而其动态特性又会随着工艺条件的更改而变化,所以这种对传统的固定参数进行控制的策略很难有效地保证不同操作条件下的控制性能。
随着对精密成型研究的深入,有人提出了采用物料的参数作为变量,例如熔体压力、熔体温度和熔体冷却速率等,这些变量称为工艺变量。
大量研究表明,工艺变量与传统的机器变量相比,具有更高的控制精度。
图2 注塑成型过程中型腔温度、压力曲线
聚合物材料从粒料(或粉料)经过塑化、填充、压缩、保压以及冷却定型成为制品,这是注塑成型的一般过程。
但是由于材料和模具的多样性,需要采用不同的工艺参数,如果参数选择不当,无论填充过多或是填充不足,都会影响最终制品的质量,甚至造成废品。
因此,确保每次成型的制品保持相同的尺寸、重量及收缩率,是注塑成型控制所要达到的目标。
PVT控制技术
聚合物的PVT特性,即压力(P)、比容(V)和温度(T)之间的相互关系,是聚合物材料的本质属性。
它们属于工艺参数,在聚合物的生产、加工以及应用等方面有着十分重
要的作用。
无论聚合物的状态如何,P、T和V这3个状态参数都会按照一定的规律变化,与加工手段和条件无关。
图1a和图1b分别显示了结晶型材料和无定形材料的典型PVT特性,从图中可以清楚地看出聚合物P、T和V之间的关系。
在注塑成型过程中,聚合物材料被加热成熔融态,并在很高的压力下注射到模具型腔中,经历了从高温、高压到迅速冷却和压力下降的过程,之后由熔融态转变为固态,同时聚合物材料的各种物性参数也经历了一连串剧烈的变化,这都和T、P和V有很大的关系。
特别是聚合物的V决定着最终成型制品的性能和质量:若最终成型制品的密度太小,会导致强度不够;若密度不均匀,则会产生内部残余应力,导致翘曲变形等。
质量重复精度是评价注塑机精度的一项重要指标。
研究表明,影响制品质量重复精度的因素很多,但本质所在是不同制品中V 的差异。
PVT 关系特性是高分子材料的固有物理特性。
高分子材料由原料经过加工成为产品的过程中,材料P-T-V参数虽持续变化,但三者之间始终遵循着PVT 特性规律。
3个变量一一对应,只要确定其中任意两个,就可以根据材料的PVT特性曲线求出第三个。
也就是说,注塑成型中无论采用何种过程控制方式都无法脱离对材料PVT 关系的依赖,并可在材料PVT 关系曲线中找到对应的加工路径。
不同控制方法得到的注塑制品的重复精度之所以存在差别,根本原因是所采用的控制方法对材料PVT 参数控制重复精度的差别。
图3 P-T过程控制方法的PVT曲线图
图2为聚合物注塑成型过程中模具型腔的温度和压力曲线示意图。
该图清楚地描绘出聚合物材料注塑成型的整个过程:聚合物在机筒中通过熔融塑化,达到设定的温度,模具闭合,注射座前进顶住浇口。
自熔体进入型腔后注塑成型可分为充填、压缩、保压和冷却4个阶段。
图中节点A-B-C为充填阶段,节点C-D为熔体压缩阶段,节点D-E为保压阶段,节点E-F-G为冷却阶段。
目前,有大量关于保压阶段最佳保压曲线的研究,但都只是基于对保压压力的研究,即保压过程采用时间控制的方式。
这种称为“P-t(时间)保压控制”的研究重点主要集中在保压曲线的形状和保压压力的取值方面。
采用该种传统的保压控制方法的后果是,随着模具温度的上升和环境的改变,制品的质量会出现波动。
如果温度变化过大,就会产生不合格品,降低生产效率,制品的质量重复精度也会受到影响。
基于材料的PVT特性,本文提出了一种基于熔体温度的保压过程的控制方法,即在保压过程中采用熔体温度作为控制信号,实现保压压力的切换,称为P-T控制。
P-T控制方法是在传统的P-t控制方法的基础上,直接监控熔体的P和T这两个工艺变量,再根据聚合物PVT特性对V进行更精确的控制。
这种方法与传统方法相比,大大拉近了控制和材料属性的关系。
令控制方法真正能够和材料属性结合,是聚合物PVT控制理论的重要组成部分,也是提高制品质量重复精度的一个有效方法。
图3所示为转压点相同,采用P-T控制的3条加工路径。
保压曲线的起始点和结束点的温度相同,而且过程各个控制节点的温度坐标也相同,在保压压力作用下,熔体压力也趋于相同,从而达到高精度的控制。
这种控制方法具有很多优点:利用工艺变量可以很好地实现转压和保压结束控制;对保压过程的各个节点进行分段控制,各控制段长度减小,保压曲线可以更加吻合,PVT特性的重复性提高,制品精度提高;采用变保压压力控制,还可以消除内应力,防止倒流。
要想提高制品的重复精度,就需要提高生产过程的重复精度,也就是提高制品从熔融注射到冷却成型经过的路径的重复性。
从PVT图上来看,就是要提高每一次注塑成型过程PVT特性的贴合程度。
如果注塑成型周期内物料的PVT特性始终相同,则最终的制品重量就会完全相同。
P-T控制方法可以很好地控制保压起点和终点的温度坐标(横坐标),在PVT 曲线图上表现为保压阶段的长度相同。
另外,中间点的控制又能使控制曲线更加贴合PVT 曲线,使保压过程按照所需的路径进行,使控制过程的重复性提高,从而提高了控制精度。
图4 不同控制方法的制品质量重复精度对比
验证试验
为了验证此控制方法的可行性和控制精度,我们对P-T控制和传统的P-t控制方法进行了对比试验。
控制装置主要由注塑机、模具、熔体温度传感器和PVT控制器模块组成,P-T 方法保压阶段的转换由型腔温度信号控制,P-t方法由时间控制,各保压段的压力值相同,保压总时间相同,其他阶段设置均相同。
图4是注塑机采用不同控制方法成型制品的质量重复精度的对比结果。
利用P-T控制方法得到的质量重复精度(0.0785%)比时间控制方式的(0.1843%)高出很多。
由此可见,将P-T控制方法应用于国产注塑成型装备,可显著提升国产装备产品等级,提升产品的市场竞争力,为企业创造更高价值。
结语
基于聚合物PVT关系的控制方法可以广泛用于普通注塑机中,并显著提高制品的质量重复精度,使普通注塑机达到精密注塑机的控制精度。
采用型腔温度控制比传统的时间控制具有更好的适应性和控制精度。
将此技术广泛应用于国产注塑机中,可以大幅度提高我国注塑机的精度水平。
该控制方法的提出,推动了我国精密成型技术的发展,并为在普通机型上生产精密制品奠定了基础。
将PVT控制系统广泛应用在注塑机中,作为与时间控制、位置控制类似的控制选择模块,实现PVT控制系统的大规模产业化,整体提升我国注塑成型领域技术水平,是在我国推广PVT控制技术的根本目标。