锻造成形工艺及其质量控制
金属材料加工中材料成型与控制工程

金属材料加工中材料成型与控制工程【摘要】本文主要探讨了金属材料加工中材料成型与控制工程的相关内容。
首先介绍了金属材料的选择与预处理,包括原材料的筛选和处理过程。
接着详细讨论了金属材料的成型工艺,包括铸造、锻造、拉伸等工艺技术。
然后介绍了金属材料控制工程技术,包括金属材料加工过程中的控制方法与技术。
并重点探讨了材料性能测试与质量控制,以保证产品的质量和稳定性。
最后讨论了金属材料加工中的环境保护措施,提出了可持续发展的相关建议。
总结了金属材料加工中材料成型与控制工程的重要性,并展望了未来发展趋势。
通过本文的研究,可以更好地了解金属材料加工中的关键技术和发展方向。
【关键词】金属材料、加工、成型、控制工程、选择、预处理、工艺、技术、性能测试、质量控制、环境保护、重要性、未来发展、展望。
1. 引言1.1 金属材料加工中材料成型与控制工程概述金属材料加工中材料成型与控制工程是金属加工领域的重要分支,旨在通过对金属材料的选择、加工工艺和控制技术的研究和应用,实现金属制品的成型和品质控制。
在这个过程中,材料成型工艺和控制工程技术起着至关重要的作用,能够影响金属制品的形状、尺寸和性能特征。
而材料性能测试与质量控制则是保证金属制品质量稳定的关键步骤,能够有效提高金属制品的使用价值和市场竞争力。
金属材料加工中的环境保护措施也是当前社会关注的焦点之一,通过采用环保材料和清洁生产工艺,减少生产对环境的污染,实现可持续发展。
金属材料加工中材料成型与控制工程的重要性不言而喻,其发展与应用将推动金属加工行业的技术进步和产业升级,为经济社会发展做出积极贡献。
未来,随着科学技术的不断进步和市场需求的不断变化,金属材料加工中材料成型与控制工程也将随之发展,不断探索新的成型工艺和控制技术,提高金属制品的质量和效率。
金属材料加工行业将迎来更广阔的发展空间,带动相关产业的快速发展,为实现绿色、智能和可持续的发展目标而努力。
2. 正文2.1 金属材料的选择与预处理金属材料的选择与预处理是金属材料加工中至关重要的一环。
2.3 锻造工艺解析

机械制造工艺基础——锻压工艺
5、平锻机上模锻:
• 平锻机的主要结构与曲柄压力机相同。只因 滑块是作水平运动,故称平锻机。
机械制造工艺基础——锻压工艺
5、平锻机上模锻:
•平锻机上模锻的特点: (1)有两个分模面,可以锻出其他模锻方 法无法锻出的锻件。 (2)生产率高,400-900件/小时。 (3)锻件尺寸精确,表面粗糙度低。 (4)材料利用率达85-95%。 (5)非回转体及中心不对称的锻件较难锻 造。平锻机造价高。 (6)适合于带头部的杆类和有孔零件的模 锻成型。
机械制造工艺基础——锻压工艺
补充: 典型零件模锻工艺过程: (1)零件图纸的分析
(2)选择分模面
(3)确定锻孔
(4)确定模锻工序
(5)绘制锻件图
(6) 锻模设计
机械制造工艺基础——锻压工艺
(1)零件图纸的分析
• 汽车后闸传动杆零件,上下端面、四个大孔、 20.3孔的端面和8孔需机械加工,其余均需模 锻锻出。
机械制造工艺基础——锻压工艺
1、模锻件图的绘制:
4)锻模圆角: •所有两表面交角处都应 有圆角。一般内圆角半 径(R)应大于其外圆半 径(r)。 5)留出冲孔连皮: •锻 件 上 直 径 小 于 25mm 的孔,一般不锻出,或 只压出球形凹穴。
机械制造工艺基础——锻压工艺
1、模锻件图的绘制:
• 大于25mm的通孔,也不能直接模锻出通孔, 而必须在孔内保留一层连皮。 • 冲孔连皮的厚度s与孔径d有关,当d =30~ 80mm时,s =4~8mm。
机械制造工艺基础——锻压工艺
3.摩擦压力机上模锻
④ 摩擦压力机承受偏心载荷能力差,通 常只适用于单膛锻模进行模锻。对于形 状复杂的锻件,需要在自由锻设备或其 它设备上制坯。 •应用: 适合于中小件的小批生产。如铆钉、 螺钉、螺母、气门、齿轮和三通阀体等。
锻造工艺及产品介绍
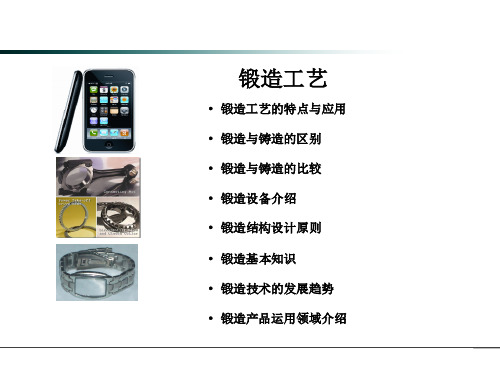
锻造成形的优势
1、 金属锻压件可以完成普通冲压件做不到的壁厚不一致产品,它可 以避免激光焊接、冲压铆合螺柱等工序的发生
锻造成形的优势
2、相对于金属压铸产品的锻造件表面质量好,且我们通常会选择塑性比较好的 铝合金材料来做锻压产品, 它可以进行表面的抛光、喷砂、拉丝、阳极等表面处 理工艺
锻造成形的优势
连续式超声波清洗机
单体式超声波清洗机
锻造件结构设计原则
锻造件形状设计主要考虑的因素:
1.工艺性:重点要考虑金属流动性,特征直角处采用圆角过渡,减少成型 工序和中间的退火次数,将锻造压力减到最小为标准; 2.材料利用率及减少切削成本:减少切削加工部位及余量,降低原料损耗; 3.品质:品质和精度容易控制和保证; 4.模具结构:模具结构根据产品特征排列成平衡方式,避免金属流动性造 成模具损坏和特征偏心。
3、增加产品的金属质感,还可以对电子辐射起到屏蔽作用,这些都是 塑料件无法具有的特点。
目前新开发的手机外壳的趋势就是往金属方向发展
锻造工艺介绍
下料
清洗
退火
沾油
成型
切边/ 冲孔
检验
包装
锻造工
成型一(热锻)
冲孔
清洗
分切
成型二
退火
锻造工艺介绍
下料:
C2680 -H铜棒 下料后
清洗后
锻造工艺介绍
退火:
退火产品
锻造工艺介绍
成形二:
500T-油压机
成型模
锻造工艺介绍
分切:
冲床
冲孔模
分切前
分切后
锻造工艺介绍
结论:
热压锻造工艺之所以能够在锻件精化上发挥作用,主要原因有: (1)锻造过程接近材料的真实塑性变形,锻造过程不考虑温降影响,将复杂问题简单化, 即将材料变形本构模型简单化,有利于锻件变形过程流动规律和组织性能演变的控制; (2)热压锻造可以减少变形死区的产生,从而减少机械加工余量,起到精化锻件的作用; (如图1) (3)热压锻造大幅度减小了机床吨位,提高模具寿命以较少的变形工步成形具有复杂形状 的锻件(如图2)
锻件工艺流程

锻件工艺流程
《锻件工艺流程》
锻件是一种传统的金属加工制造方法,通过将金属材料加热至一定温度后,在模具的作用下进行加工成特定形状的零部件。
锻件工艺流程包括原料准备、热处理、模具设计、锻造、修磨和表面处理等环节。
在原料准备阶段,首先需要对原材料进行选择和准备。
通常,锻件采用的材料主要包括钢、铝、铜和钛等金属材料。
不同的材料在后续的制造工艺流程中需要采用不同的热处理方法和模具设计。
热处理是锻件工艺中非常重要的一步。
通过热处理,可以改变金属的晶体结构和力学性能,优化原材料的可塑性和韧性,为后续的锻造提供更好的条件。
在模具设计环节,工程师需要根据最终产品的要求和工艺性能,设计出合适的模具结构。
模具的设计直接影响到锻件的成型质量和效率,因此需要进行充分的方案设计和评估。
锻造过程是锻件工艺流程中最核心的环节,通过对加热后的金属材料进行冲压、拉伸或挤压等加工方式,使其在模具的作用下成型为具有所需形状和尺寸的零部件。
在成型后,需要对锻件进行修磨,以去除表面的粗糙度和瑕疵,提高表面质量和尺寸精准度。
最后,通过表面处理方法(如喷
砂、镀层等)对锻件进行表面处理,提高其耐腐蚀性和美观度。
通过以上的工艺流程,锻件可以在保证质量的前提下,实现较高的生产效率和成本控制。
在现代制造业中,锻件工艺已经得到了广泛的应用,成为不可或缺的金属加工方法之一。
材料成型及控制技术

材料成型及控制技术材料成型及控制技术是现代制造业中非常重要的一部分,它涉及到材料加工的各个环节,包括材料的选择、成型工艺、控制技术等方面。
在制造业中,材料成型及控制技术的应用直接影响着产品的质量、成本和生产效率。
因此,深入了解材料成型及控制技术对于提高制造业的竞争力具有重要意义。
首先,材料成型技术是指将原材料经过一定的成型工艺,转化为具有一定形状和尺寸的制品的过程。
这个过程中,需要考虑原材料的性能、成型工艺的选择、成型设备的性能等因素。
常见的成型工艺包括锻造、压铸、注塑、挤压等,每种成型工艺都有其适用的材料和产品类型。
在材料成型过程中,需要充分考虑原材料的性能和成型工艺的匹配性,以确保最终产品的质量和性能。
其次,控制技术在材料成型过程中起着至关重要的作用。
控制技术包括对成型工艺参数、成型设备性能、原材料质量等方面的控制。
通过合理的控制技术,可以实现产品尺寸精度的控制、成型工艺的稳定性控制以及产品质量的可控性。
在现代制造业中,智能化控制技术的应用越来越广泛,通过传感器、控制系统等设备实现对成型过程的实时监控和调节,提高了生产效率和产品质量。
此外,材料成型及控制技术的发展也受到了材料科学的影响。
随着新材料的不断涌现,新的成型工艺和控制技术也在不断发展。
例如,复合材料的成型工艺和控制技术、3D打印技术等都是近年来备受关注的领域。
这些新技术的应用为制造业带来了新的发展机遇,同时也提出了新的挑战。
综上所述,材料成型及控制技术是现代制造业中不可或缺的一部分,它直接影响着产品的质量、成本和生产效率。
深入了解材料成型及控制技术,不仅有助于提高制造业的竞争力,也有助于推动制造业的技术创新和发展。
因此,我们应该不断学习和掌握最新的材料成型及控制技术,以适应制造业的发展需求,为推动制造业的高质量发展做出贡献。
铸造质量控制
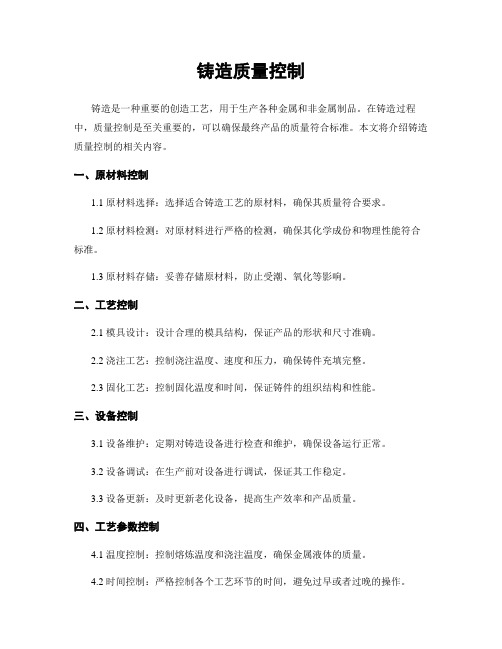
铸造质量控制铸造是一种重要的创造工艺,用于生产各种金属和非金属制品。
在铸造过程中,质量控制是至关重要的,可以确保最终产品的质量符合标准。
本文将介绍铸造质量控制的相关内容。
一、原材料控制1.1 原材料选择:选择适合铸造工艺的原材料,确保其质量符合要求。
1.2 原材料检测:对原材料进行严格的检测,确保其化学成份和物理性能符合标准。
1.3 原材料存储:妥善存储原材料,防止受潮、氧化等影响。
二、工艺控制2.1 模具设计:设计合理的模具结构,保证产品的形状和尺寸准确。
2.2 浇注工艺:控制浇注温度、速度和压力,确保铸件充填完整。
2.3 固化工艺:控制固化温度和时间,保证铸件的组织结构和性能。
三、设备控制3.1 设备维护:定期对铸造设备进行检查和维护,确保设备运行正常。
3.2 设备调试:在生产前对设备进行调试,保证其工作稳定。
3.3 设备更新:及时更新老化设备,提高生产效率和产品质量。
四、工艺参数控制4.1 温度控制:控制熔炼温度和浇注温度,确保金属液体的质量。
4.2 时间控制:严格控制各个工艺环节的时间,避免过早或者过晚的操作。
4.3 压力控制:根据产品要求控制浇注压力,确保铸件的密度和强度。
五、质量检验控制5.1 外观检验:对铸件的表面质量进行检查,包括气孔、裂纹等缺陷。
5.2 尺寸检验:测量铸件的尺寸和几何形状,确保符合设计要求。
5.3 化学成份检验:对铸件的化学成份进行分析,确保符合标准。
综上所述,铸造质量控制是确保铸件质量的关键环节,需要在原材料、工艺、设备、工艺参数和质量检验等方面进行全面控制。
惟独做好质量控制,才干生产出满足客户需求的优质铸件。
锻造的工艺过程
锻造的工艺过程简介锻造是一种常见的金属加工方法,通过将金属材料加热至一定温度后施加压力,使其发生塑性变形,以改变其形状和内部组织结构。
锻造广泛应用于航空航天、汽车、能源、机械制造等行业,是制造业中不可或缺的一部分。
本文将详细介绍锻造工艺过程。
热锻工艺过程加热在锻造过程中,首先需要将金属材料加热至一定温度,以提高其塑性和可锻性。
加热温度取决于金属材料的种类和锻件的形状复杂程度,一般可分为低温、中温和高温锻造。
加热可以使用电阻加热炉、气体加热炉等设备进行。
锻造1.预制坯料在加热到适当温度后,需要对金属材料进行预制坯料的加工,即将原始材料切割成适合锻造的形状和尺寸。
预制坯料的形状和尺寸要符合最终锻件的要求,以便于后续的锻造操作。
2.模具设计和制造在锻造之前,需要根据最终产品的形状和尺寸设计和制造相应的模具。
模具是锻造操作的关键,可以确定最终产品的形状和精度。
模具制造一般采用机械加工和热处理等工艺,确保模具具有足够的强度和耐磨性。
3.锻造操作锻造操作是将加热好的金属材料放入模具中,施加适当的压力进行变形的过程。
锻造过程中,压力可以通过液压机、锤击或压力机等工艺设备施加,以使金属材料发生塑性变形。
同时,根据需要进行多次锻造,以逐步改变金属材料的形状和组织结构。
4.热处理锻造后的金属材料通常需要进行热处理,以改善其力学性能和组织结构。
热处理可以包括退火、正火、淬火等工艺,通过控制加热和冷却过程,使金属材料获得理想的硬度和强度。
5.后续加工经过锻造和热处理后,锻件可能需要进行进一步的加工,包括切割、车削、铣削、钻孔等。
这些加工操作将锻件加工成最终产品,并满足其形状和精度要求。
冷锻工艺过程材料准备冷锻过程中使用的材料通常是冷硬性较高的金属,例如铝合金、不锈钢等。
在冷锻前,需要对材料进行预处理,如去除氧化层、清洁表面等,以保证冷锻过程的质量。
设备和工艺参数选择冷锻可以使用液压机、螺旋式冷锻机等设备进行。
在选择设备时,需要考虑材料的硬度、形状复杂度和生产效率等因素。
材料成型及其控制
材料成型及其控制材料成型是指将原材料通过一定的加工工艺,使其获得所需的形状和尺寸的过程。
在现代工业生产中,材料成型是非常重要的一步,它直接影响产品的质量和性能。
本文将探讨材料成型的基本原理、常见的成型方法以及成型过程的控制方法。
一、材料成型的基本原理材料成型的基本原理是利用力的作用使材料发生形变,从而获得所需的形状和尺寸。
常见的力包括挤压力、拉伸力、压力等。
材料在受力的作用下,会发生塑性变形或弹性变形,而成型过程中需要的是塑性变形。
因此,选择合适的材料以及施加适当的力是实现材料成型的基本要求。
二、常见的材料成型方法1. 压力成型:压力成型是指利用外部的压力将材料压缩和塑性变形,从而获得所需形状的方法。
常见的压力成型方法有压铸、冲压和锻造等。
压铸是利用高压将熔融金属注入模具中,经冷却凝固后获得零件的方法。
冲压是利用冲压模具将金属板材冲裁成所需形状的方法。
锻造是利用锻压机将金属材料加热至一定温度后施加一定的压力,使其塑性变形从而获得所需形状的方法。
2. 热成型:热成型是指在高温条件下将材料塑性变形,从而获得所需形状的方法。
常见的热成型方法有热挤压、热拉伸和热压缩等。
热挤压是将金属材料加热至一定温度后通过挤压机将其压制成所需形状的方法。
热拉伸是将塑料材料加热至一定温度后拉伸成所需形状的方法。
热压缩是将金属材料加热至一定温度后通过压力将其压制成所需形状的方法。
3. 注塑成型:注塑成型是将熔融的塑料材料注入模具中,经冷却凝固后获得所需形状的方法。
注塑成型广泛应用于塑料制品的生产,如塑料零件、塑料容器等。
三、材料成型过程的控制方法材料成型过程的控制是确保产品质量和生产效率的关键。
以下是几种常见的成型过程控制方法:1. 温度控制:在热成型过程中,控制材料和模具的温度是非常重要的。
适当的温度能够保证材料的塑性和流动性,从而获得所需形状。
通过控制加热温度和冷却速度,可以实现对材料成型过程的精确控制。
2. 压力控制:在压力成型过程中,控制施加的压力是关键。
金属锻造挤压成型技术
金属锻造挤压成型技术金属锻造挤压成型技术是一种常用的金属加工工艺,通过对金属材料施加压力,使其在模具中发生塑性变形,最终得到所需形状的金属零件。
这种技术广泛应用于汽车、航空航天、机械制造等领域,具有高效、精确、经济的特点。
一、挤压成型的基本原理金属锻造挤压成型是利用挤压机将金属材料加热至一定温度后,施加压力使其通过模具形成所需形状的工艺。
挤压成型的基本原理可概括为以下几个步骤:1. 加热:将金属材料加热至适宜的温度,一般为材料的再结晶温度以上,以提高材料的塑性。
2. 装料:将加热后的金属材料放入挤压机的料斗中,通过料斗和送料器将材料送入挤压机的工作腔。
3. 挤压:在加热的金属材料上施加一定的压力,使其通过模具的塑性变形,形成所需形状的工件。
4. 冷却:待金属材料通过模具完成挤压后,将其冷却至室温,使其保持所需形状。
二、金属锻造挤压成型的优势1. 节约材料:挤压成型可以有效利用金属材料,减少材料的浪费。
2. 提高产品质量:挤压成型可以使金属材料的晶粒细化,提高材料的强度和硬度。
3. 提高生产效率:挤压成型速度快,可大幅提高生产效率。
4. 适应性强:挤压成型适用于各种金属材料,包括铝、铜、钢等。
5. 成本低:挤压成型工艺简单,设备投资和生产成本相对较低。
三、金属锻造挤压成型的应用领域金属锻造挤压成型技术被广泛应用于各个领域,特别是在汽车、航空航天和机械制造等行业具有重要地位。
以下是几个典型的应用领域:1. 汽车制造:挤压成型可以用于制造汽车车身、车门、车架等零部件,具有优良的强度和刚性。
2. 航空航天:挤压成型可用于制造航空航天器的翼、舵面等零件,具有轻量化、高强度的特点。
3. 机械制造:挤压成型可用于制造各种机械零件,如齿轮、轴承座等,具有高精度和高强度。
四、金属锻造挤压成型技术的发展趋势随着科技的不断进步,金属锻造挤压成型技术也在不断发展。
未来,金属锻造挤压成型技术可能呈现以下几个趋势:1. 精密化:随着对产品精度要求的提高,金属锻造挤压成型技术将朝着更高的精密化方向发展。
环锻件生产工艺流程
环锻件生产工艺流程环锻件是利用材料在力的作用下产生塑性变形的特性,通过模具使其产生形状的变化,从而得到所需形状和尺寸的零部件。
环锻件广泛应用于航空航天、汽车、机械制造等领域,具有高强度、高硬度和耐磨性等优点。
下面将介绍环锻件的生产工艺流程。
一、锻前准备1.原料准备:选择符合要求的合金钢、不锈钢等金属材料,并按照配料比例进行加热处理,将其变为均匀的温度。
2.模具准备:根据零部件的设计图纸,选择合适的模具进行加工和调整,保证模具的质量和精度。
3.设备准备:检查环锻机器的各部件是否正常,对燃料、润滑油等进行加注,确保设备能够正常运转。
二、锻造工艺1.加热材料:将原料放入锻造炉中进行加热,使其达到一定的温度,以便于后续的锻造和成型。
2.成形锻造:将加热好的原料放入环锻机器中,通过压力使其产生塑性变形,逐步成型成为零部件的初步形状。
3.冷却处理:待成形的零部件冷却后,取出进行清理和修整,达到设计要求的尺寸和表面光洁度。
4.热处理:将锻造好的环锻件进行热处理,消除内部应力和提高其机械性能,增加硬度和耐磨性。
5.表面处理:对环锻件的表面进行喷砂、酸洗或其他处理,提高其表面质量和外观。
6.检测验收:对成品进行外观检查、尺寸测量、力学性能测试等,确保环锻件符合设计要求。
三、机加工工艺1.铣削加工:对环锻件的外形和尺寸进行铣削加工,确保其能够精确匹配其他零部件。
2.车削加工:对环锻件的孔径和轴向进行车削加工,提高其装配精度和密封性能。
3.钻孔加工:在环锻件上进行钻孔加工,以便于安装螺栓、销钉等连接零部件。
四、质量控制1.自检:生产操作人员对生产过程中的环锻件进行自检和互检,确保产品符合要求。
2.抽检:质检人员对成品进行定期抽检,对零部件的尺寸、外观和力学性能进行测试,发现问题及时处理。
3.追查:对有疑问的环锻件进行追溯,查找生产过程中的问题和原因,以及时调整和改进。
以上就是的详细介绍,通过科学的工艺流程和严格的质量控制,可以生产出高质量的环锻件,满足客户的需求。
- 1、下载文档前请自行甄别文档内容的完整性,平台不提供额外的编辑、内容补充、找答案等附加服务。
- 2、"仅部分预览"的文档,不可在线预览部分如存在完整性等问题,可反馈申请退款(可完整预览的文档不适用该条件!)。
- 3、如文档侵犯您的权益,请联系客服反馈,我们会尽快为您处理(人工客服工作时间:9:00-18:30)。
锻造成形工艺及其质量控制汽车前梁成形辊锻工艺日趋成熟,特别是近几年,前梁生产逐步采用整体辊锻模锻复合工艺,它是成形辊锻工艺基础上,引入模锻工艺,原理上汲取各自优点,但组成优于两者的新工艺,该工艺适用于各类轻、中、重型汽车前梁锻件的生产。
为少投入、高质量、大批量生产复杂类汽车零部件探索了一条新途径。
1、汽车前轴成形辊锻工艺汽车前轴(图2-1左右对称)成形辊锻工艺流程如下:图2-1 汽车前轴锻件图(1)下料采用G4032带锯条下料。
(2)加热采用KGPS250-1型中频感应炉加热。
(3)成形辊锻采用D42-1000辊锻机,进行制坯、预成形、终成形三道次辊锻或四道次。
(4)弯形局部整形采用6300T磨擦压力机整体弯形、整形。
(5)切边采用1600T摩擦压力整体切边。
(6)热校正采用1600T磨擦压力机整体热校正。
该工艺将圆钢通过制坯、预成形、终成形三道次辊锻制成带飞边直坯锻件,然后通过局部整形、切边、弯形、热校正完成锻件生产,从而达到工艺要求的几何尺寸。
2、下料是将原材料切割成所需尺寸的坯料。
3、锻造所用的原材料种类繁多,有各种钢号和非铁金属,有不同的截面形状,不同的尺寸规格,不同的化学成份的物理学性质等,所以下料方法是多种多样的。
4、辊锻工艺辊锻前轴一般利用圆钢作为初始材料,直径和长度都是设计出来的。
5、不同型号前轴所需圆钢尺寸不一样。
印度产品FA90 所需原钢尺寸为Φ150×7406、因辊锻工艺所需圆钢长度精确,端面平整,所以辊锻工艺采用锯床下料。
但存在生产率较低、锯口损耗较大等缺陷。
2.1.1加热在锻造生产中,金属坯料锻前一般均需加热,其目的是:提高金属塑性,降低变形抗力,使之易于流动成形并获得良好锻压组织。
因此,锻前加热是整个锻造过程中的一个重要环节,对提高锻造生产率,保证锻件质量及节约能源消耗等都有直接影响。
圆钢加热主要采用电加热。
电加热是通过把电能转变为热能来加热金属坯料。
其中有感应电加热,接触电加热,电阻炉加热和盐浴加热等。
辊锻工艺要求加热速度快,加热质量好,温度控制准确,金属烧损较少(一般小于0.5%),故一般采用感应加热。
并且感应加热还具有操作简单,工作稳定,便于和锻压设备组成生产线实现机械化一自动化,劳动条件好,对环无污染等优点。
感应加热的原理如图2-2在感应器通入变电流产生的交变磁切作用下,金属坯料内部产生交变涡流。
由于涡流发热机磁化发热(磁性转变点以下)便直接将金属坯料加热。
图2-2 感应电加热原理图1—感应器2—坯料坯料进行感应加热时,内部产生的流密度沿断面分布是不均匀的。
中心电流密度小,表层电流密度大,这种现象称为趋肤效应。
ρ(厘米)电流通过表层的厚度δ为电流透入深度可按下式计算:δ=5030fμ式中f—电流频率(赫芝)μ—相对导磁率,对各类钢而言,在7600C(居里点)以上时,μ=1;ρ——电阻率(欧姆·厘米2/厘米)。
由于趋肤效率效应,表层金属主要是因电流通过而被加热,心部金属则靠外层热量向内传导加热。
对于大直径的坯料,为了提高加热度,应选用较低电流频率,以增大电流透入深度。
而对小直径的坯料,由于截面尺寸较小,可采用较高电流效率,这样能够提高电效率。
在锻压生产中,主要用中频感应加热(f=500-10000赫芝)辊锻制坯皱形。
辊锻工艺采用的锻压设备称辊锻机;其结构与两辊式轧机相似,具有一对转速相同、转向相反的锻辊,其工作原理见图2-3。
辊锻辊模2固定在锻辊1上,电动机7径带5,齿轮副8和4减速后,再通过齿轮副3带动上下锻辊作等速反向的旋转。
通常,在辊锻机上还有磨擦离合器6和制动器9,以获得点动、单动、连动等多种操作规范。
弯形整形。
图2-3 辊锻机工作原理1—锻辊2—辊锻模3、4、8—齿轮副5——带6—磨擦离合器7—电动机9—制动器此工序是锻件终锻成形的关键工序,为使锻件弯形到位,充型饱,故需要较大吨位的设备,一般选用6300T磨擦压力机。
磨擦压力机具有锻锤和压力机的双重工作特性。
螺旋压力机在工作过程中带有一定的冲击作用,滑块行程不固定,这是锤类设备的工作特性;但它又是通过螺旋副传动能量的,在金属产生塑性变形的瞬间,滑块和工作台之间所受的力,由压力机封闭的框架承受,并形成一个封闭的力系,从而达到终锻要求。
弯形、整形采用复合模具,一边弯形、一边整形利用磨擦压力机可在一个型槽或两个型槽进行多次打击弯形的特点,从而完成先弯形后整形工序。
结构原理图见2-4。
切边、热效正工序一般都采作1600T的磨擦压力机,工作原理如同上工序。
图2-4 磨擦压力机工作原理2.1.2本工艺过程中存在的主要质量问题辊锻工艺制造汽车前轴有很多优势。
能大批量生产,且转产快,前轴金属沿纵向流向,强度高等,但也存在很多质量问题。
下料时存在的主要质量问题:料坯过长或短。
过长造成浪费;过短造成充型不满,甚至报废。
料坯有时会锯斜,也会造成充型不满,不同型号前轴的材质也可能不一样,如果材质混淆,热处理时会造成开裂。
加热时存在的质量问题:锻造的温度一般在800-1200摄氏度。
温度过低,不但坯料展不长,还易损坏设备。
温度过高,易造成过热或过烧。
辊锻制坯时存在问题:调试时废品多,正式生产时也易充型不满,甚至错模。
三道次料坯后也易造成过长或过短,甚至弯曲、缠辊。
废边过大或过小。
弯形、整形存在的质量问题:弯形不到位,有时压入废边,中心线未对正,错模,不易脱膜。
切边时存在质量问题:废边未切掉或切伤。
热校正存在质量问题:未校正,不易脱模。
2.1.3质量控制方法及改进措施产品质量是生产出来的,不是检验出来的。
所以想把产品质量控制好,还得从生产工序源头抓起。
对每工工序,都应有具体的质量管理办法。
1、钢材投料管理办法为了规范钢材投料程序,加强原材料质量控制,提高前轴等锻件内在质量,针对钢材投料环节的管理作如下规定:合格供方钢材:(1)合格供方内钢材应经质量部裣验员检验合格后方可投入使用。
(2)每季度抽取一种合格供方内钢材做金相、理化及台架试验,三年内覆盖所有钢材型号。
(3)困新产品开发需要的新牌号材料钢材或新增钢厂的材料,称为新进钢材。
属新进钢材从合格供方以外的厂家一次性购买临时采购时,必须严格履行会签、审批手续。
(4)试生产件从下料、辊锻、热处理到机加工都应做好标识,防止混料。
(5)试生产件应严格检测淬回火硬度,并进行100%磁粉探伤。
(6)试生产件机加工后抽取3件进行台架疲劳试验及金相组织分析,质量部根据最终检验结果出据报告,并对该批材料作出判定,若合格投入生产,不合格退货,责令供方整改并验证落实后重新送检/试产。
(7)合格供方内产品出现批量性质量问题后,暂停使用该供方产品;对方更改材料质西文及工艺后申请恢复供货时,按新进钢材对待,严格进行所有项目的检验和试验。
2、不同材质钢材色标规定钢材入库时所有圆钢均需由库管员用油漆逐支涂材质色标。
色标用“Ⅰ”表示,涂在圆钢端面上,色标不能覆盖原钢材的材质标签。
不同色标分别代表不同材质:红色=CrMo;天蓝色=40Cr;白色=50#;黄色=50#对于材质不清的圆钢由质检员分选。
3、锻造钢坯加热温度的控制(1)由于钢加热到5300C以上时会出现不同的火色,因此可对钢的加热温度采取目测火色,再与标准颜色图谱对照的方法来判定钢坯的加热温度。
(2)目测火色判定加热温度的方法温度越高,火色越浅且亮;温度越低,火色越深且暗目测钢坯的加热温度时要注意现场光线的强弱对火色的影响。
现场光线较强时,火色会相对而言偏暗;现场光线较弱时,火色会相对偏亮;刚开始使用色卡比较目测温度时,可用红外线测温仪进行校对,逐步掌握使用方法。
目测温度只是一种近似方法,对有经验的师傅来说,目测误差不大,一般可准确到±(20-50)0C2.1.4锻件的质量控制与规定1、锻件质量检测工作流程如图2-5所示。
操作者自检检验员巡检车间完工检查质检站专职检验员抽检合格?转序/入库不合格:填写“不合格品报告/处置单”报送质管部及技术部门检验记录不合格图2-5 质检工作流程图2、料坯锯切加工具体尺寸按《下料通知单》,防止因装夹和操作不当而产生不合格品。
3、坯料加工完毕,应按生产钢厂的规格型号分类码放在料架上,并在钢坯上作好生产钢厂代号标识、材质、规格型号及炉号代号,防止混用。
4、每次转产或更换新模具,车间应进行调试加工,经车间检验员检验合格后可指加工。
调试件检验不合格的,模(夹)具修整后应继续调试,直到产出合格产品。
5、操作者和车间检验员均应对首件毛坯实施检验。
每3小时抽检一次为4件,检验合格的,可继续生产;检验不合格的,不允许继续生产。
2.1.5前轴锻件完工检验指导书表2-1 完工检验指导书序号检验项目检验方法重要度备注1 不得有过烧、折叠、裂纹等缺陷目测[1]2 热处理硬度硬度计(布氏)[1]3 头部外径(大端)0-200㎜卡尺[2]头部外径(大端)0-200㎜卡尺[2]4 头部对钢板弹簧座中心扭曲度0-300㎜高度尺[2]5 两头部测理中心距卷尺2m [2]6 拳头轴心线内倾角0-320°角度尺[2]7 主肖孔中心至限位块0-200㎜卡尺[2]8 钢板弹簧座宽0-200㎜卡尺[2]9钢板弹簧座中心对前轴两端瓜头中心线的偏移0-200㎜卡尺0-300㎜高度尺[2]10 钢板弹簧座上凸缘厚度0-200㎜卡尺[2]11 钢板弹簧座下凸缘厚度0-200㎜卡尺[2]12 锻件在全长的错移量目测[2]13 残余飞边在头部0-200㎜卡尺[3]14 残余飞边在其它部位0-200㎜卡尺[3]15 去飞边时不得有台阶目测[2]16钢板弹簧座下边缘至瓜头上加工线距离,保证上、下加量均匀300㎜卡尺[2]17 工字部分宽度(上边缘)0-200㎜卡尺[2]工字部分宽度(下边缘)0-200㎜卡尺[2]18 限位凸台相对主销孔中心线的位置(用样板)样板[2]19局部充型不满,在热处理前允许焊补,焊补后必须打磨以消除焊补痕迹目测[1]说明:1、“[1]”为关键项目“[2]”为重要项目“[3]”为一般项目2、在填写检验记录表时,采用样板检查的项目合格打“√”,不合格打“×”。
目测项目合格打“√”,不合格打“×”。
上、下加工量数据合格打“√”,不合格打“×”。
其它项目以数据表达。
3、每批抽样样本量见抽样方法。
4、序3、序4根据产品要求进行检验。
2.1.6关键项控制要求锯料保证长度中频加热温度控制在800-1200030 。
辊锻初成形、打弯、终锻:保证无明显充型不满,无折叠刮伤,锻件表面平整圆滑。
切边:保证飞边高度小于1.5、整齐、无过切。
热校正:保证中心线偏移量不大于2,保证锻件压型尺寸公差。
2.1.7质量改进措施及具体质量目标在现代经营环境中,企业的竞争呈现出日益加剧的趋势,顾客的需要和期望也处在持续的变化之中。