动刚度与静刚度
机械系统的静态与动态刚度分析
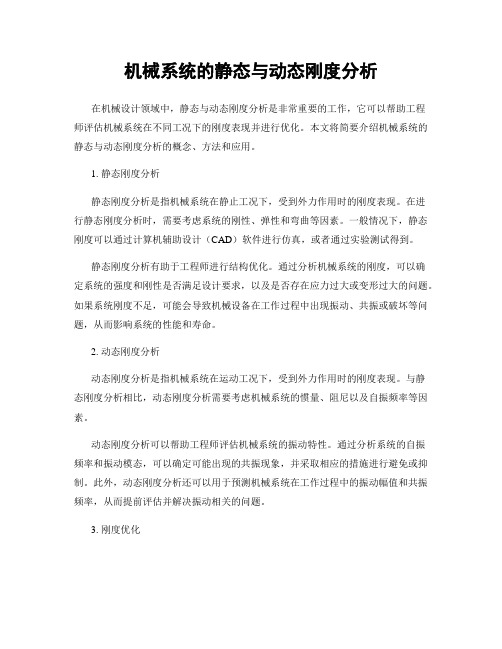
机械系统的静态与动态刚度分析在机械设计领域中,静态与动态刚度分析是非常重要的工作,它可以帮助工程师评估机械系统在不同工况下的刚度表现并进行优化。
本文将简要介绍机械系统的静态与动态刚度分析的概念、方法和应用。
1. 静态刚度分析静态刚度分析是指机械系统在静止工况下,受到外力作用时的刚度表现。
在进行静态刚度分析时,需要考虑系统的刚性、弹性和弯曲等因素。
一般情况下,静态刚度可以通过计算机辅助设计(CAD)软件进行仿真,或者通过实验测试得到。
静态刚度分析有助于工程师进行结构优化。
通过分析机械系统的刚度,可以确定系统的强度和刚性是否满足设计要求,以及是否存在应力过大或变形过大的问题。
如果系统刚度不足,可能会导致机械设备在工作过程中出现振动、共振或破坏等问题,从而影响系统的性能和寿命。
2. 动态刚度分析动态刚度分析是指机械系统在运动工况下,受到外力作用时的刚度表现。
与静态刚度分析相比,动态刚度分析需要考虑机械系统的惯量、阻尼以及自振频率等因素。
动态刚度分析可以帮助工程师评估机械系统的振动特性。
通过分析系统的自振频率和振动模态,可以确定可能出现的共振现象,并采取相应的措施进行避免或抑制。
此外,动态刚度分析还可以用于预测机械系统在工作过程中的振动幅值和共振频率,从而提前评估并解决振动相关的问题。
3. 刚度优化在机械系统设计中,静态与动态刚度分析可用于刚度优化。
刚度优化旨在提高机械系统的刚度,以满足设计要求并改善系统的性能。
优化方法一般包括结构改造、材料选择和加工工艺优化等。
在进行刚度优化时,需要权衡刚性和重量之间的关系。
增加结构刚度通常需要增加材料的厚度、强度或数量,从而增加系统的重量。
因此,刚度优化需要综合考虑机械系统的性能要求和重量限制,并进行合理的权衡。
4. 应用实例静态与动态刚度分析在实际应用中具有广泛的应用。
例如,汽车工程师可以使用刚度分析来评估汽车底盘的刚度表现,在遇到减震问题时进行改进。
此外,航空航天工程师可以使用刚度分析来评估飞机结构在起飞、飞行和降落等工况下的刚度表现,确保飞机的结构稳定性和安全性。
什么是动刚度
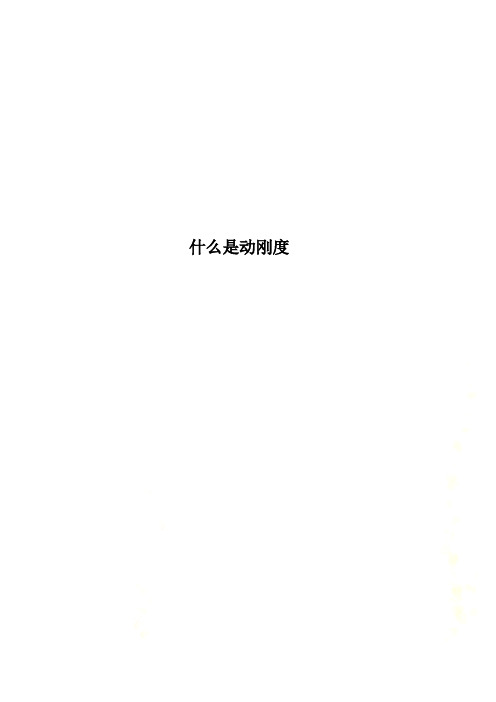
什么是动刚度同理,单自由度系统的动刚度曲线也有类似性质在低频段,动刚度接近静刚度,幅值是k,表明共振频率以下的频率段主要用占主导地位的刚度项来描述。
如果作用在系统的外力变化很慢,即外力变化的频率远小于结构的固有频率时,可以认为动刚度和静刚度基本相同。
在高频段,动刚度的幅值为ω2m,表明共振频率以上的频率段主要用占主导地位的质量项来描述,这是因为质量在高频振动中,产生很大的惯性阻力。
当外力的频率远大于结构的固有频率时,结构则不容易变形,即变形较小,此时结构的动刚度相对较大,也就是抵抗变形的能力强。
在共振频率处动刚度的幅值下降明显,其幅值为ωc,表明在共振频率处主要受阻尼控制。
而在共振频率处,我们知道,结构很容易被外界激励起来,结构的变形最大,因而结构抵抗变形的能力最小,也就是动刚度最小。
3. 多自由度动刚度单自由度系统是基础,但现实世界中的系统大多数都是多自由度系统,因此,我们测量出来的动刚度也是多自由度的动刚度。
下图为多自由度系统的同一位置的加速度频响函数(加速度导纳)和该点的动刚度曲线。
多自由度系统的驱动点FRF存在多个共振峰和反共振峰,在共振峰处,对结构施加很小的激励能量,结构就会产生非常大的振动(变形),因而在共振峰处,结构很容易被激励起来,结构的变形大,抵抗变形的能力弱,也就是动刚度小。
在反共振峰所对应的频率处进行激励,即使激励能量再大,结构也没有响应或者响应很微弱,也就是说在反共振峰所对应的频率处,结构很难被激励起来,结构的变形小,抵抗变形的能力强,因此,动刚度大。
从上图可以看出,频响函数共振峰对应的是动刚度曲线的极小值,也就是说频响函数幅值大的频率处,动刚度小。
在反共振峰处,动刚度大,二者刚好相反。
4. 原点动刚度原点动刚度IPI(Input Point Inertance,IPI):概念上类似原点(或称作驱动点)频响函数,指的是同一位置、同一方向上的激励力与位移之比,主要测量与车身接附点处的原点动刚度,比如车身与发动机悬置、副车架、悬架连接处、排气挂钩处等位置的局部动刚度,考虑的是在所关注的频率范围内该接附点局部区域的刚度水平,过低必须引起更大的噪声,因此,该性能指标对整车的NVH性能有较大的影响。
精密机床的静态与动态刚度分析
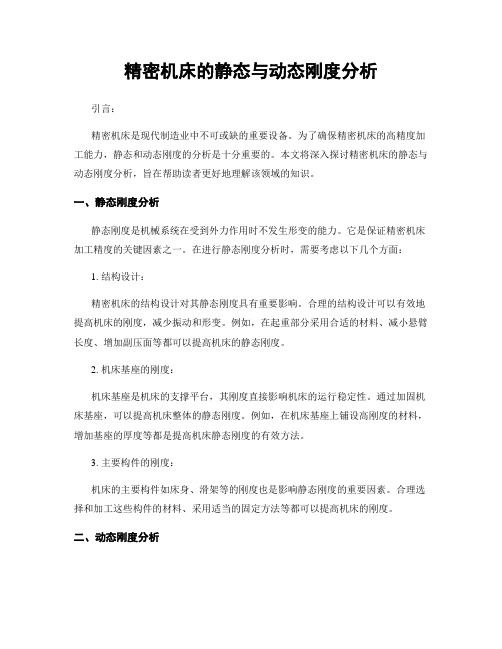
精密机床的静态与动态刚度分析引言:精密机床是现代制造业中不可或缺的重要设备。
为了确保精密机床的高精度加工能力,静态和动态刚度的分析是十分重要的。
本文将深入探讨精密机床的静态与动态刚度分析,旨在帮助读者更好地理解该领域的知识。
一、静态刚度分析静态刚度是机械系统在受到外力作用时不发生形变的能力。
它是保证精密机床加工精度的关键因素之一。
在进行静态刚度分析时,需要考虑以下几个方面:1. 结构设计:精密机床的结构设计对其静态刚度具有重要影响。
合理的结构设计可以有效地提高机床的刚度,减少振动和形变。
例如,在起重部分采用合适的材料、减小悬臂长度、增加副压面等都可以提高机床的静态刚度。
2. 机床基座的刚度:机床基座是机床的支撑平台,其刚度直接影响机床的运行稳定性。
通过加固机床基座,可以提高机床整体的静态刚度。
例如,在机床基座上铺设高刚度的材料,增加基座的厚度等都是提高机床静态刚度的有效方法。
3. 主要构件的刚度:机床的主要构件如床身、滑架等的刚度也是影响静态刚度的重要因素。
合理选择和加工这些构件的材料、采用适当的固定方法等都可以提高机床的刚度。
二、动态刚度分析动态刚度是机床在运动状态下的刚度特性,主要用于分析机床加工过程中的振动特性。
在进行动态刚度分析时,需要考虑以下几个方面:1. 特征频率分析:机床的结构和构件都有一定的频率响应。
找出机床的特征频率并进行分析,可以帮助识别和解决振动问题。
例如,采用频谱分析方法可以确定机床加工时的共振频率,从而避免加工过程中的振动影响。
2. 振动模态分析:振动模态分析是确定机床在特定频率下的振动模态形式和振动模态参数的方法。
通过分析机床的振动模态,可以了解机床振动的特点和影响机床刚度的因素。
例如,可以通过振型分析确定机床的关键模态,并进行针对性的刚度改进。
3. 结构阻尼分析:结构阻尼是机床动态刚度的重要组成部分。
合理的结构阻尼设计可以降低机床振动的幅度和频率,提高机床的动态刚度。
车辆减振橡胶动、静态刚度名词解释

减振橡胶动、静态刚度名词解释刚度又称弹簧常数。
弹簧常数是指弹簧发生单位长度或厚度应变时所需的力。
原来这个概念是来评价金属弹簧的。
用于橡胶时,是指橡胶松弛单位长度所需的力,即橡胶发生单位长度应变所需的力,单位N/mm。
刚度分为静态刚度(Ks)和动态刚度(Kd)。
以下分别进行介绍。
一、静态刚度Ks静态刚度的定义:指减振橡胶在一定的位移范围内,其所受压力(或拉伸力) 变化量与其位移变化量的比值。
静态刚度的测定必须在一定的位移范围内测定,不同的位移范围测定的静态刚度值是不同的,但有的厂家则要求整个位移范围测定的变化曲线.下面以压缩应变试验为例说明减振橡胶与金属弹簧的静态刚度的不同之处:图1 金属弹簧压缩载荷—位移曲线图将金属弹簧压缩到弹簧弹性极限内的一定范围的位移量后,再将压力缓慢匀速卸去,弹簧所受的载荷与位移量的关系如图1所示呈线性关系,在外力卸去后弹簧能够回复到初始位置.图2 减振橡胶压缩载荷—位移曲线图将减振橡胶压缩到一定范围的位移量后,再将压力缓慢匀速卸去,减振橡胶所受的载荷与位移量的关系如图2所示呈非线性关系,在外力卸去后减振橡胶不能够回复到初始位置,出现位移相对于载荷的滞后现象。
从上面的试验可以得出:橡胶的静态刚度是在一定的位移范围内,其所受载荷变化量与其位移变化量的比值,位移范围不同所得到的静态刚度值是不同的,即(F2-F1)/(X2-X1)≠(F3-F2)/(X3-X2) 。
而金属弹簧在任意位移范围内其所受载荷变化量与其位移变化量的比值是一定的,即(F2-F1)/(X2-X1)=(F3-F2)/(X3-X2).将金属弹簧和减振橡胶同时压缩到极限后,金属弹簧的压力会一直保持不变,而减振橡胶的压力会随着时间的推移出现压力松弛的现象,如图3所示,减振橡胶的这种压力松弛的特性使它具有比金属弹簧更好的消振作用。
图3 减振橡胶和金属弹簧压力时间曲线二、动态刚度Kd动态刚度的定义:指减振橡胶在一定的位移范围内, 一定的频率下, 其所受压力(或拉伸力)变化量与其位移变化量的比值.动态刚度的测定必须在一定的位移范围内,一定的频率下测定,不同的位移范围不同的频率下测定的动态刚度值是不同的. 减振橡胶不仅在静态特性上与金属弹簧不同而且在动特性上也与与金属弹簧存在很大的差异,下面以试验为例说明两者的不同之处:图4 减振胶与金属弹簧的振幅---振动时间关系图如图4所示,分别对减振橡胶与金属弹簧施加一个冲击力,来对比冲击后的振幅与振动时间的变化关系(不考虑系统以外力的影响),可以看出减振橡胶的振动很快消减并在很短时间振动停止,而金属弹簧的振动能持续很长时间,振幅的衰减速度很慢,因此减振橡胶与金属弹簧相比具有较大的阻尼,对振动的吸收性能好,能有效地防止振动的传播。
车身刚度小知识

车身刚度小知识车身刚度小知识车身刚度小知识看到许多人在比较polo的飞度的车身刚度,但仅限于口头争端,我来提供一些基础知识和数据吧先说说简单的概念吧,时间不多,周末要出门,就不详细写了。
车身刚度有两种,静态刚度和动态刚度。
车身静态刚度一般包括弯曲刚度和扭转刚度两种。
车身的弯曲刚度可由车身前后的变形量来衡量,车身扭转刚度可由前后窗和侧框的对象线变化量、车身锁位及车身扭转角等指标来衡量。
在转弯时,主要考察车身的侧倾刚度。
动态刚度用车身模态频率来衡量。
这个频率应该与载苛的激振频率相差较大才可以(共振的效应大家都知道吧?)发动机的怠速的激振频率是可以计算的。
例如,如果是四缸机,在怠速为n=750r/min时,怠速的激振频率为f=(750/60)*2 = 25hz如果是六缸机,在怠速为n=700r/min时,怠速的激振频率为f=(750/60)*3 = 35hz如果是八缸机,在怠速为n=600r/min时,怠速的激振频率为f=(750/60)*4 = 40hz而车轮的不平衡激振是在1-30hz之间。
车身的一阶固有激振频率一般在20-35hz之间。
下面开始提供数据:polo的车身静态刚度:扭转:19000nm/度其它:未知动态刚度:44hz飞度的查不到,但是saab-93的是epsilon构架的动态刚度是27hz,而且通用称其达到了多数豪华轿车的标准(看来通用在白车身制造方面不是很强的嘛,可惜了saab-93了)刚刚查到了中华,老中华的车身头部刚度37hz,新中华增加到46hz。
但我不明白为什么这个试验还可以仅做头部和尾部的?应该是整体车身一起做才对。
其它车辆的车身刚度欢迎大家补充。
p.s.网上查资料比较难,大多数都是在说比上一代提高了百分多之少,这样的宣传用语不可信之,因为,如果从10hz提高到13hz,就是提高了30%,而从30hz提高到40hz,也提高了30%,有可比性么?再p.s.现在的轿车都是承载式车身(连夏利都是),所以不用讨论车架了,有车架的车,刚度肯定高出许多.补充如下:自身频率是任何物体所固有的,对于车身来讲,拆掉一个翼子板也会改变。
减振橡胶动静刚度比研究

减振橡胶动静刚度比研究
减振橡胶动静刚度比是指在减振系统中橡胶材料在动态和静态
加载下的刚度比值。
这个比值可以帮助工程师评估橡胶材料在不同
工况下的性能表现。
首先,让我们从静态刚度和动态刚度的角度来看。
静态刚度是
指在静止状态下材料的刚度,而动态刚度则是在受到振动或动态加
载时材料的刚度。
减振橡胶通常在实际使用中会同时受到静态和动
态加载,因此了解动静刚度比可以帮助工程师更好地设计和选择减
振系统。
其次,动静刚度比还可以从材料的能量耗散特性来分析。
在动
态加载下,橡胶材料会因为内部分子摩擦和能量耗散而表现出不同
的刚度特性,而这种能量耗散对于减振系统的性能至关重要。
因此,研究动静刚度比可以帮助工程师评估橡胶材料的能量耗散特性,从
而更好地预测减振系统的性能。
此外,动静刚度比还可以从工程应用的角度进行研究。
不同的
工程应用对减振系统的要求不同,有些应用更注重静态刚度,而有
些则更注重动态刚度。
因此,了解动静刚度比可以帮助工程师根据
具体应用需求选择合适的橡胶材料,从而优化减振系统的性能。
综上所述,减振橡胶动静刚度比的研究涉及静态和动态刚度、能量耗散特性以及工程应用等多个方面,对于优化减振系统的设计和性能提升具有重要意义。
通过深入研究动静刚度比,工程师可以更好地理解和应用橡胶材料在减振系统中的性能,从而推动相关领域的发展和进步。
刚度浅谈
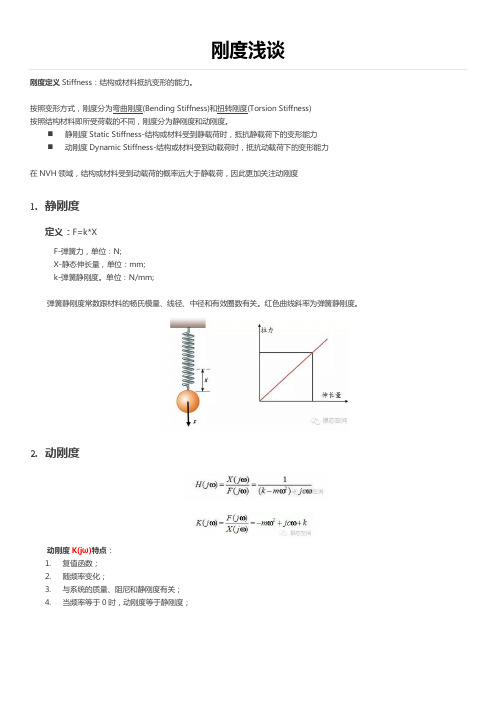
刚度浅谈刚度定义Stiffness:结构或材料抵抗变形的能力。
按照变形方式,刚度分为弯曲刚度(Bending Stiffness)和扭转刚度(Torsion Stiffness)按照结构材料即所受荷载的不同,刚度分为静刚度和动刚度。
⏹静刚度Static Stiffness-结构或材料受到静载荷时,抵抗静载荷下的变形能力⏹动刚度Dynamic Stiffness-结构或材料受到动载荷时,抵抗动载荷下的变形能力在NVH领域,结构或材料受到动载荷的概率远大于静载荷,因此更加关注动刚度1.静刚度定义:F=k*XF-弹簧力,单位:N;X-静态伸长量,单位:mm;k-弹簧静刚度。
单位:N/mm;弹簧静刚度常数跟材料的杨氏模量、线径、中径和有效圈数有关。
红色曲线斜率为弹簧静刚度。
2.动刚度动刚度K(jω)特点:1.复值函数;2.随频率变化;3.与系统的质量、阻尼和静刚度有关;4.当频率等于0时,动刚度等于静刚度;动刚度曲线特点:1.低频段-刚度控制区a)动刚度≈静刚度,幅值是k,在<共振频率时,刚度项占主导地位b)若作用在系统的外力变化很慢,即外力变化的频率远小于结构的固有频率时,可以认为动刚度≈静刚度2.高频段-质量控制区a)动刚度的幅值为ω2*m,在<共振频率时,质量项占主导地位(质量在高频振动中,产生很大的惯性阻力)b)当外力的频率>>结构固有频率时,结构则不容易变形,结构的动刚度相对较大3.共振频率处-阻尼控制区a)动刚度的幅值下降明显,其幅值为ω*c,在共振频率处主要受阻尼控制b)在共振频率处,结构的变形最大,动刚度最小3.多自由度动刚度单自由度系统是基础,但现实世界中的系统大多数都是多自由度系统。
下图为多自由度系统的同一位置的加速度频响函数(加速度导纳)和该点的动刚度曲线。
特点:1.多自由度系统的驱动点FRF存在多个共振峰和反共振峰,2.FRF峰谷值与动刚度谷峰值一一对应。
机械零件的强度与刚度分析

机械零件的强度与刚度分析在机械设计领域中,强度与刚度是非常重要的参数。
强度是指零件在受力下不发生破坏的能力,而刚度则是指零件在受力下不发生变形的能力。
在进行机械设计时,对于零件的强度与刚度的分析与评价,对于确保机械设备的可靠性和稳定性具有重要意义。
首先,我们来讨论机械零件的强度分析。
强度分析主要是通过计算零件所能承受的最大应力和应变,判断零件是否能够在受力过程中保持稳定不发生破坏。
这就需要对零件的材料性能、受力情况、工作环境等进行详细的分析。
在材料性能方面,不同材料具有不同的强度特性。
例如,金属材料一般具有较高的强度,可以承受较大的载荷,而塑料材料则强度较低,一般只适用于低强度要求的零件设计。
因此,在选择材料时,需要根据所设计零件的工作环境和承受的载荷来进行选择,以确保零件具有足够的强度。
受力情况是强度分析中的另一个关键因素。
不同零件在工作过程中所受的力的大小和方向不同,这就需要对零件在受力情况下的应力分布进行分析。
通过应力分布的计算,可以得到零件上各个点的应力值,并判断是否存在超过材料极限强度的情况。
如果存在超过极限强度的应力,就需要对零件进行重新设计或者采取加强措施。
此外,工作环境也对强度分析产生重要影响。
不同工作环境的温度、湿度、振动等因素都会对材料的强度产生影响。
例如,在高温环境下工作的零件需要考虑材料的高温强度和热膨胀系数,以保证在高温下零件仍能保持强度稳定。
接下来,我们来探讨机械零件的刚度分析。
刚度分析主要是通过计算零件的变形情况,判断零件在受力下是否会发生过大的变形。
刚度分析通常包括静态刚度和动态刚度两个方面。
静态刚度是指零件在定力状态下的刚度,主要用于判断零件在受力下是否会产生过大的变形。
静态刚度的计算一般采用材料力学和结构力学的原理,并结合有限元分析等数值计算方法进行。
通过计算得到的刚度参数可以用于优化设计,以保持零件在受力后的稳定性。
动态刚度是指零件在运动状态下的刚度,主要用于判断零件在运动过程中是否会产生过大的变形和共振现象。
- 1、下载文档前请自行甄别文档内容的完整性,平台不提供额外的编辑、内容补充、找答案等附加服务。
- 2、"仅部分预览"的文档,不可在线预览部分如存在完整性等问题,可反馈申请退款(可完整预览的文档不适用该条件!)。
- 3、如文档侵犯您的权益,请联系客服反馈,我们会尽快为您处理(人工客服工作时间:9:00-18:30)。
动刚度与静刚度静载荷下抵抗变形的能力称为静刚度,动载荷下抵抗变形的能力称为动刚度,即引起单位振幅所需要的动态力。
静刚度一般用结构的在静载荷作用下的变形多少来衡量,动刚度则是用结构振动的频率来衡量;如果动作用力变化很慢,即动作用力的频率远小于结构的固有频率时可以认为动刚度和静刚度基本相同。
否则,动作用力的频率远大于结构的固有频率时,结构变形比较小,动刚度则比较大。
但动作用力的频率与结构的固有频率相近时,有可能出现共振现象,此时动刚度最小,变形最大。
金属件的动刚度与静刚度基本一样,而橡胶件则基本上是不一样的,橡胶件的静刚度一般来说是非线性的,也就是在不同载荷下的静刚度值是不一样的;而金属件是线性的,也就是说基本上是各个载荷下静刚度值都是一样的;橡胶件的动刚度是随频率变化的,基本上是频率越高动刚度越大,在低频时变化较大,到高频是曲线趋于平坦,另外动刚度与振动的幅值也有关系,同一频率下,振动幅值越大,动刚度越小刚度刚度受外力作用的材料、构件或结构抵抗变形的能力。
材料的刚度由使其产生单位变形所需的外力值来量度。
各向同性材料的刚度取决于它的弹性模量E和剪切模量G(见胡克定律)。
结构的刚度除取决于组成材料的弹性模量外,还同其几何形状、边界条件等因素以及外力的作用形式有关。
分析材料和结构的刚度是工程设计中的一项重要工作。
对于一些须严格限制变形的结构(如机翼、高精度的装配件等),须通过刚度分析来控制变形。
许多结构(如建筑物、机械等也要通过控制刚度以防止发生振动、颤振或失稳。
另外,如弹簧秤、环式测力计等,须通过控制其刚度为某一合理值以确保其特定功能。
在结构力学的位移法分析中,为确定结构的变形和应力,通常也要分析其各部分的刚度。
刚度是指零件在载荷作用下抵抗弹性变形的能力。
零件的刚度(或称刚性)常用单位变形所需的力或力矩来表示,刚度的大小取决于零件的几何形状和材料种类(即材料的弹性模量)。
刚度要求对于某些弹性变形量超过一定数值后,会影响机器工作质量的零件尤为重要,如机床的主轴导轨、丝杠等。
工艺系统的刚度1.基本概念刚度的一般概念是指物体或系统抵抗变形的能力。
用加到物体的作用力与沿此作用力方向上产生的变形量的比值表示,即(10-5)式中——静刚度(N);——作用力(N/mm);——沿作用力方向的变形量(mm)。
越大,物体或系统抵抗变形能力越强,加工精度就越高。
切削加工过程中,在各种外力作用下,工艺系统各部分将在各个受力方向产生相应变形。
对于工艺系统受力变形,主要研究误差敏感方向上的变形量。
因此,工艺系统刚度定义为:作用于工件加工表面法线方向上的切削力与刀具在切削力作用下相对于工件在法线方向位移的比值,即(10-6)式中——工艺系统刚度(N/mm);作用于工件加工表面法线方向上的切削力(N);工艺系统总的变形量(mm)。
在上述工艺系统刚度定义中,力和变形是在静态下测定的,为工艺系统静刚度;变形量是由总切削力作用的综合结果,当引起Y方向位移超出引起的位移时(),总位移与方向相反,呈负值,此时刀架处于负刚度状态。
负刚度使刀尖扎入工件表面(扎刀),还会使工件产生振动,应尽量避免,如图10-12所示。
2.工艺系统刚度的计算工艺系统的总变形量应是各个组成环节在同一处的法向变形的叠加,即根据刚度定义,工艺系统各组成环节的刚度为,;;所以工艺系统刚度一般公式为(10-7)式中——工艺系统总的变形量(mm);——工艺系统刚度(N/mm);机床变形(mm);机床刚度(N/mm);夹具变形(mm);—一夹具刚度(N/mm);刀具变形(mm);刀具刚度(N/mm);工件变形(mm);一一工件刚度(N/mm)公式10-7表明,已知工艺系统各组成环节的刚度,即可求得工艺系统刚度。
对于工件和刀具,一般说来都是一些简单构件,可用材料力学公式近似计算,如车刀的刚度可以按悬臂梁计算,用三爪卡盘夹持工件,工件的刚度可以按悬臂梁计算,用顶尖加工细长轴,工件的刚度可以按简支梁计算等;对于机床和夹具,结构比较复杂,通常用实验法测定其刚度。
1、对于橡胶悬置来说,在10Hz后刚度变化就比较慢了,而且一般来说对于发动机动力总成来说刚体模态在6Hz~20Hz之间,对于一套发动机悬置,你都取6Hz,或都取10Hz,或者15Hz,20Hz,算出来的刚体模态频率差别很小,现在通常采用15Hz处的动刚度.但我建议取怠速时的点火激励频率处的动刚度来计算刚体模态,如果这样算得的刚体模态频率分布和振型解耦较好,,那么悬置匹配就比较好了(当然还有个传递率的问题),过了怠速,激振频率会增加很快,而发动机悬置的刚度相对来说增加很少,而导致的发动机刚体模态频率增加就更小了,所以只要取怠速时的点火激励匹配出来的悬置满足悬置设计的那些要求,那就肯定没问题了.2、我认为静刚度的考量衡量原因:1、支撑,及平衡,设计基本信息包括动力总成倾角、悬置取点、许用弹性中心的载荷、允许的位移量等。
2、限位,这个很容易理解的。
3、如果弹性单元是纯粹的弹性体,由于弹性体有自身动静比固定的特性,可以预先设计好静刚度,从而达到动刚度预先设计值;考虑动刚度的原因:原则上获取小的动刚度是有利于提高NVH性能的。
这个要素对于高频时的振动改善尤为重要,但是在低频时效果不很明显,当然,没有人愿意让车停在那里烧油玩。
正是由于弹性体有自身动静比固定的特性,这就有一个问题,支撑性能和低的动刚度是矛盾的两方面,不可一味的追求其一。
当然还要综合考虑疲劳强度、制造的工艺可行性、成本等方面的因素,才能设计出比较合理的悬置。
3、我的理解是,发动机悬置的刚度系数在解耦设计时应考虑为动刚度。
因为由于弹性支撑元件的阻尼存在,使得动载下的变形有迟滞现象出现,导致动刚度大于静刚度,比如橡胶隔振垫(天然橡胶的,一般动静比为1.3~1.6)。
如果是金属弹簧隔振器的话,因为没有迟滞现象,就不存在动刚度的说法,其动刚度等于静刚度。
4、我是做悬置结构的,工作6年。
我谈一下我的感觉,给您一些建议,也许有用。
1、强度及模态:我认为不要把乘用车设计成坦克,在这个话题上,有机会看一下日本的设计,会觉得我们浪费了很多中国的钢材。
说明一下我并不喜欢日本,但是喜欢他们的设计。
2、结构:时下国内流行铸造,很浪费。
然而聪明的冲压设计,是很重要的,车辆的成本会降低。
感叹:铝制件是好,但是资源消耗甚大;铸钢是好,但是铸造水平及铸造件的重量,当然还有某些蹩脚的CAE分析,更加重了设计的重量,又让油耗加大。
4、静刚度:首先想要的是合理的静刚度,准确的支撑对整个动力总成布置是至关重要的。
5、动刚度:避开频率噪点,如果您能够做到,越低越好,可以将不快遏制在怠速以下。
数次问题解决方向都是这样。
设想:假如发动机漂在水上,振动是无从传递的。
但是由于制造工艺及疲劳的限制,您往往不得不选择折中。
6、液压悬置:高频表现不错,但是我们国家总是在模仿,高速发展让我们忽略了追求根底。
很多情况是原理懂一些,但是总是理论指导不能与制造、测试结果合拍,不得不承认,我们有时候在自己糊弄自己,糊弄别人。
作为一个工程师,希望您能够静下心来,做一个实在一点的计算程序,别怕丢人,都知道连微软都在不停的改版本。
7、垫块、衬套式悬置我认为非常实用,很适合中国国情,千万不要妄在经济型车辆上使用液压悬置,会害死供应商,害死汽车厂家,无论如何,成本会增加1.5倍以上对于橡胶隔振器对于橡胶隔振器静刚度是当载荷缓慢地加载于隔振器,其变形速度控制在lcm/min左右,橡胶的变形量不超过它厚度的20%的情况下所测的受力与变形之比。
动刚度是隔振器在一定的频率(一般在5〜60Hz)和一定的振幅(一般不超过橡胶厚度的5%)的交变载荷下,也就是不超过lm/的变形速度下测得的受力与变形之比。
冲击刚度是当隔振器的变形速度为2〜6m/时测得的刚度。
动刚度一般是静刚度的1.3〜2.2倍,冲击刚度一般是动刚度的1.5〜2.0倍。
硫化压力对胶料性能的影响(2)使胶料流动,充满模腔;(3)提高附着力,改善硫化胶物理性能。
而国外在研究硫化压力时,已经不单单局限于我们上面的一些研究,已经通过调整硫化压力的大小来达到产品的一些特殊性能的要求,根据本人掌握的情况,国外橡胶厂家有如下一些对于硫化压力的共识。
(1)模压及移模注压的硫化方式,其模腔内的硫化压力为:10〜20Mpa。
(2)注压硫化方式其模腔内的硫化压力为:0〜150Mpa。
(3)随着硫化压力的增大,产品的收缩率和产品的静态刚度有交叉变化。
随着硫化压力的增大,其产品的静态刚度在逐渐增大,而随着硫化压力的增大,其胶料的收缩率在逐渐的减小。
在国内的减振橡胶行业内,对于调整产品的刚度,普遍采用的依然是增加或者降低产品所使用的胶料硬度,而在国外,已经普遍采用了提高或者降低产品硫化时的胶料硫化压力来调整产品的静态刚度。
随着胶料的硫化压力不断提高,产品胶料的收缩率会出现一个反常的现象,即当产品胶料的硫化压力达到83Mpa时,产品胶料的收缩率为0,若产品胶料的硫化压力继续不断上升,产品胶料的收缩率会出现负值,也就是说,在这种超高的产品胶料硫化压力下,产品硫化出来经停放后,其橡胶部分的尺寸比模具设计的尺寸还要大。
在模压和注压方式下,模腔内胶料的硫化压力随着时间的延长,其硫化压力总是先增高后减小,并最终处于平坦状态。
2.随着胶料硫化压力的提高,其胶料的300%定伸和拉伸强度均随之提高,其胶料的扯断伸长率、撕裂强度和压缩永久变形却随之下降。
3.在减震橡胶制品硫化过程中,注压硫化方式中模腔内胶料的压强比模压硫化方式的压强高一倍以上。
产品达到相同的静刚度所需的胶料硬度有较大差别。
随产品硫化时的硫化压力提高,产品在压缩永久变形性能方面有明显的提高。