国内外高炉炼铁系统的能耗分析
国内外高炉炼铁技术的发展现状和趋势

国内外高炉炼铁技术的发展现状和趋势高炉炼铁技术是金属冶炼工业发展的基础,是保证金属铁质量和产量的关键技术,也是社会经济发展的重要依托。
近年来,随着金属冶炼工业的快速发展,国内外高炉炼铁技术的发展也取得了显著的成就,为保证金属铁质量、提高产量、提高经济效益发挥了重要作用。
首先,国内外高炉炼铁技术取得了重大突破,进一步提高了金属铁质量。
随着科学技术的进步,添加剂和冶炼工艺的改进,使高炉炼铁工艺取得重大进展,不仅能够有效提高铁素体组成,同时也能够改善铁水的流动性,有利于铁块的全面成型。
此外,利用新型炉料和改进的热处理技术,可以有效降低铁水的含氧量,提高铁液的液相容量,从而获得更高品质的铁。
其次,国内外高炉炼铁技术的发展,还大大提高了铁的产量。
传统的高炉炼铁工艺存在着大量的炉料损失,限制了铁的产量。
随着国内外高炉炼铁技术的发展,炉料损失大大减少,产量得到提高。
通过对炼铁工艺及其参数进行优化调整,获得合理的炉料计算和分配,进而有效提高铁的产量。
此外,结合智能技术、自动化技术和智能控制技术,还可以实现远程监控和智能化管理,可以使高炉炼铁效率更高,产量更大。
最后,国内外高炉炼铁技术的发展,对提高经济效益具有重要意义。
国内外高炉炼铁技术的发展,不仅缩短了铁的生产周期,提高了产量,而且可以减少能耗消耗和废气排放,降低了生产成本,有利于提高企业的竞争力,实现更高的经济效益。
此外,国内外高炉炼铁技术的发展还可以改善炼铁终端的工作环境,为炼铁行业的发展创造更加良好的条件。
以上是国内外高炉炼铁技术的发展现状和趋势的概述,未来的发展趋势可以简单地总结为以下几点:继续提高高炉炼铁质量和产量,推广智能技术,进一步优化炼铁工艺,合理设计炉料配比,提高炼铁效率,减少能耗和污染,改善炼铁环境,提高经济效益,实现绿色经济发展。
未来,相信国内外高炉炼铁技术将取得更好的发展,为我们社会的经济发展提供更多的依托。
国内外高炉炼铁系统的能耗分析
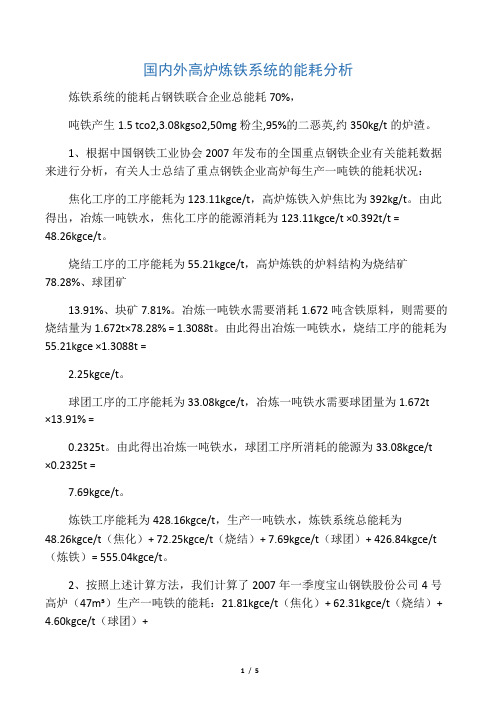
表12005年浦项制铁盒光阳厂炼铁有关能耗指标
项目工序能耗Kgce/t
烧结
66
57.4焦化
129.7
131.9炼铁
462.5
441.1入炉焦比Kgce/t炉料结构%
烧结比
76.4
70.9球团比
7.8
11.1块矿比
15.8
18.0xx
光阳494.7
492.1
表2全国重点钢铁企业能耗对比(单位Kgce/t)
高热值煤气回收利用率低是非高炉炼铁能耗高的“瓶颈”
2007年,我国重点钢铁企业的烧结、炼铁工序能耗与2006年相比进一步降低,炼铁生产部分工序能耗指标见表2。
2007年,全国重点钢铁企业高炉炼铁燃料比是529kg/t,浦项FINEX燃料比是740kg/t~750kg/t,澳大利亚Hismelt的煤耗在900kg/t(尚需1200℃风温和350kWh/t的电力)。这说明目前非高炉炼铁的能耗高于高炉冶炼生产工艺。
国内外高炉炼铁系统的能耗分析
炼铁系统的能耗占钢铁联合企业总能耗70%,
吨铁产生1.5 tco2,3.08kgso2,50mg粉尘,95%的二恶英,约350kg/t的炉渣。
1、根据中国钢铁工业协会2007年发布的全国重点钢铁企业有关能耗数据来进行分析,有关人士总结了重点钢铁企业高炉每生产一吨铁的能耗状况:
高炉冶炼节能分析

高炉冶炼节能分析摘要从高炉稳定顺行,提高喷煤比,搞好余热能的回收利用,减少煤气,氧气及高炉的鼓风放散率,开发高炉炉渣显热回收技术等几方面对武钢高炉冶炼节能进行了简要的论述。
关键词高炉冶炼节能降耗余热回收1 概述武钢高炉炼所消耗的能源约占全公司总能耗的40%~43%是公司最大的能耗大户,因此降低高炉能耗实质上是降低公司生产总能耗的主体部分,对于发展武钢这一特大型钢铁联合企业具有重要意义。
炼铁工序能耗组成中主要是燃料消耗,余下的是水、电、蒸汽、鼓风等动力消耗。
另外,消耗的辅助材料、备品备件在生产过程中都消耗了能耗,是载能体,属于社会能耗的范围。
燃料消耗占炼铁工序能耗的8 5 %左右,因而炼铁节能的重点是降低燃料消耗,提高高炉喷煤比,同时积极进行二次能源的回收利用,并对节约动力与辅助材料也要给足够的重视。
2 高炉稳定顺行是高炉冶炼节能的前提和基础高炉稳定顺行是高炉冶炼节能的前提和基础。
为确保高炉的稳定顺行,优良的原料、良好的外围条件以及先进的设备皆是提高高炉生产水平的物质基础。
而先进合理的操作制度和科学的生产组织与管理,则是高炉高产稳产的关键。
加强原燃料的管理。
改善原燃料质量,是提高精料水平的重要手段。
进一步推行槽下过筛,要求入炉矿料含粉率降低到 5%以下,炉料中小于5mm粉末减少l O%高炉产量可以提高8 %。
从而相应的降低了能耗;不断提高焦炭质量,降低并稳定焦炭水分,降低焦炭灰分,每降低焦炭灰分和提高矿石品位各1% ,高炉可降焦比约2% ,产量提高3%。
武钢对原有的操作制度进行不断地改进和提高,使高炉操作逐步适应了外部条件的变化,采甩合理的装料制度,控制合理气流分布,精心操作,高炉入炉焦比也正在一步步地降低,煤气利用率也得到了明显的改善。
煤气中的C O。
含量由1991年的16.3% 提高到1995年的18%,5年间提高了 1.7%,相当于降低焦比25kg/t左右,从而取得了较好的节能效果和较高的经济效益。
高炉炼铁的产能与运行效率分析

采用先进的控制技术,如自动控制系统、 专家系统等
加强设备维护和管理,减少设备故障和停 机时间
采用节能型工艺,如富氧炼铁、熔融还原 炼铁等
高炉炼铁的环保性能分析
环保性能评估指标
废气排放量:包括二氧化硫、氮氧化物、 颗粒物等
能源消耗量:包括煤炭、电力等
废水排放量:包括重金属、有机物等
环境影响评价:包括对周边环境的影响、 生态破坏程度等
能耗:能耗是衡量高炉炼铁运行效率 的另一个重要指标,包括燃料消耗、 电力消耗等。
设备利用率:设备利用率是指高炉炼 铁设备在运行时间占总运行时间的比 例,也是衡量运行效率的重要指标。
生产成本:生产成本包括原材料成 本、人工成本、设备折旧等,是衡 量高炉炼铁运行效率的综合指标。
影响运行效率的因素
原料质量:铁矿石、 焦炭等原料的质量 直接影响炼铁效率
备正常运行
产能优化案例
案例背景:某钢铁 公司高炉炼铁产能 不足,影响公司效 益
优化措施:采用先 进的生产工艺和技 术,提高设备利用 率
优化效果:产能提 高20%,成本降低 15%
启示:通过技术创 新和设备升级,可 以有效提高产能和 运行效率
高炉炼铁的运行效率分析
运行效率评估指标
产量:高炉炼铁的产量是衡量运行效 率的重要指标之一。
会影响产能
操作水平:工人的 操作技能和经验对
产能有重要影响
市场需求:市场需 求的变化也会影响
产能
提高产能的措施
优化原料配比:合理 选择铁矿石、焦炭等 原料,提高原料质量
采用先进的冶炼技术: 如富氧鼓风、喷煤等,
提高冶炼效率
改进炉型结构:采用 先进的高炉结构,提 高炉膛温度和热效率
加强设备维护和管理: 定期对高炉设备进行 检查和维护,确保设
炼铁系统能耗分析及节能

炼铁系统能耗分析及节能摘要:随着中国经济的快速增长以及工业化、城市化进程的加快,环境退化进一步加速,虽然我国采取了一系列措施加强环境保护。
但是,目前的环境保护在一定程度上还缺乏有效性和效率。
炼铁系统能耗和污染物排放占联合钢铁企业总量的70%以上,承担着钢铁工业节能减排的重任,在炼铁系统环节上应当积极创新和推广节能减排的新技术、新工艺,新设备、新的管理方法。
因此,我国在环保问题上还需要不断地完善管理体制和方法创新。
本文主要对炼铁系统能耗进行了一定的分析,并给出了相应的对策。
关键词:炼铁系统;能耗分析;节能;绿色城市引言钢铁行业在快速发展的同时,产能释放过快、铁矿石价格大幅上涨、钢材价格持续震荡、节能减排压力大等问题日益显现。
钢铁企业作为耗能大户,耗能量占全国耗能总量的12%左右。
据冶金部门统计,在产品生产成本中,主要的可控部分是能源消耗约占25-40%,能源价格上涨后更是如此。
国家已将节能减排定为国民经济发展的基本国策,国家环境保护部、工业和信息化部均已提出了对烧结工序的烟气脱硫的具体要求和时间表。
现在节能减排已经提上日程,志在实现高效、节能、环保、低碳生活。
1.背景概述1.1环境污染加剧的原因改革开放以来,我国由计划经济转人市场经济,以“解放生产力,发展生产力”为第一要务,各地传统工业相继崛起,采用高投人、高消费、高环境代价的工业发展模式开始。
尤其是东南沿海地区私人开办的工厂和各地集体集资的乡镇企业以“小、散、乱”为特点,技术水平落后,生产效率低下,为牟取最大收益不重视环境管理。
同时政府把重心放在了经济的高速发展上,针对环境保护问题没有强制性的管理制度和管理措施,环境管理处于失控和半失控状态。
环境持续恶化的趋势至今为止没有改变。
我国的经济发展正面临着历史上罕见的机遇,同时也经受着严峻的挑战。
1.2节能减排的意义随着全球变暖的严峻形势,环境治理已刻不容缓。
联合国环境规划署提出了“绿色经济”的口号,每年6月5日选择一个成员国举行“世界环境日”纪念活动,发表《环境现状的年度报告书》及表彰“全球500佳”,并根据当年的世界主要环境问题及环境热点,有针对性地制定每年的“世界环境日”主题。
高炉炼铁过程中的能源消耗与管理

高炉炼铁过程中的能源消耗与管理一、前言与背景高炉炼铁作为现代钢铁工业的基础,自19世纪末以来,一直是铁钢生产的主要方法。
高炉炼铁技术的出现和发展,对社会、经济和科技产生了深远影响。
它使得钢铁生产实现了规模化、低成本,极大地促进了工业革命和现代工业社会的形成。
同时,高炉炼铁过程也伴随着能源的消耗,据统计,能源消耗占到了高炉炼铁成本的很大一部分。
因此,研究和分析高炉炼铁过程中的能源消耗和管理,对于提高我国钢铁工业的能源利用效率,降低生产成本,提升竞争力具有重要意义。
二、高炉炼铁行业/领域的核心概念与分类高炉炼铁的概念高炉炼铁是一种利用焦炭和氧气反应产生的高温,将铁矿石还原成铁的过程。
其基本原理是在高温下,铁矿石中的氧化铁与一氧化碳反应,生成铁和二氧化碳。
高炉炼铁过程中,能源主要用于提供热能和动力能,其中热能主要用于维持高炉内的温度,动力能主要用于推动炉内物质的流动和完成各项机械作业。
高炉炼铁的分类高炉炼铁可以根据炉型、操作方式、燃料种类等不同标准进行分类。
按炉型可分为小型高炉、中型高炉和大型高炉;按操作方式可分为连续操作高炉和间歇操作高炉;按燃料种类可分为焦炭高炉和煤气高炉。
高炉炼铁的特征与应用领域高炉炼铁具有生产规模大、原料利用率高、产品品质好、能耗高等特征。
其应用领域广泛,几乎涵盖了所有钢铁生产领域。
高炉炼铁与其他领域的交叉与融合随着科技的发展,高炉炼铁技术与自动化、信息化、环保等领域日益交叉与融合。
例如,高炉炼铁过程的自动化控制,使得生产过程更加稳定,效率更高;信息化技术的应用,使得高炉炼铁过程的监测和控制更加精细;环保技术的应用,则有助于降低高炉炼铁过程中的污染排放。
三、关键技术或性能原理剖析高炉炼铁的关键技术高炉炼铁的关键技术主要包括燃料燃烧技术、还原反应技术、热量交换技术、原料处理技术等。
其中,燃料燃烧技术是高炉炼铁过程中能源消耗的主要部分,其效率的高低直接影响到高炉炼铁的能耗。
高炉炼铁的最新技术突破与创新成果近年来,高炉炼铁技术取得了许多重要突破和创新成果,如低焦比炼铁技术、高风温技术、煤气净化技术等。
炼铁工艺中的能源消耗与节能技术探索

炼铁工艺中的能源消耗与节能技术探索炼铁工艺是钢铁生产过程中至关重要的一环,同时也是一个高能耗行业。
随着能源资源的紧张和环境污染的加剧,如何减少炼铁工艺中的能源消耗并开展节能技术探索成为了当前的重要课题。
本文将围绕炼铁工艺的能源消耗分析和节能技术探索展开讨论。
一、炼铁工艺中的能源消耗分析在炼铁工艺中,能源消耗主要来自于两方面:一是燃料的消耗,二是电力的消耗。
燃料的消耗包括焦炭、煤炭、天然气等,而电力的消耗则主要用于激活炉料、通风、冷却以及一些辅助设备等方面。
1. 燃料消耗燃料在炼铁生产过程中主要用于冶炼过程中产生高温,以及提供还原、脱氧、燃烧等化学反应所需的热能。
传统的炼铁工艺,在高炉炼铁过程中主要使用焦炭作为还原剂,而焦炭的大量消耗不仅导致能源的浪费,还对环境造成了严重的污染。
因此,如何减少燃料的消耗,提高能源利用效率成为了迫切需求。
2. 电力消耗电力在炼铁工艺中主要用于提供动力和操作设备的供电,如驱动风机、循环水泵、输送带、起重机等。
随着炼铁工艺技术的发展,电力在工艺中的比重越来越大。
同时,炼铁工艺中一些辅助设备的能耗也逐渐增加。
因此,如何减少电力的消耗,实现节能减排成为了必然选择。
二、节能技术探索为了减少炼铁工艺中的能源消耗,许多节能技术不断被引入和应用。
下面将重点介绍一些有效的节能技术。
1. 高炉炼铁节能技术高炉炼铁是传统的炼铁工艺,其能源消耗较高。
为了提高高炉炼铁的能源利用效率,可以采取一系列节能技术措施,如提高燃烧温度、增加炉渣比例、改善燃料燃烧等。
此外,高炉炼铁还可以与其他冶金工艺相结合,进行能量互补,实现能源的综合利用。
2. 氧气炼铁技术氧气炼铁技术是近年来快速发展的一种新型炼铁工艺。
相比传统高炉炼铁,氧气炼铁工艺在能源消耗上具有明显的优势。
氧气炼铁可以减少焦炭的消耗量,增加反应温度,提高还原效果,从而在一定程度上实现了降低能源消耗、提高炼钢效率的目标。
3. 余热利用技术炼铁工艺中产生的大量余热往往未能得到合理利用,导致能源的浪费。
国内外吨钢综合能耗、可比能耗和工序能耗比较

内外吨钢综合能耗、可比能耗和工序能耗比较钢铁工业是国民经济重要的基础原材料工业,也是高耗能、高污染工业。
钢铁工业节约潜力巨大,为此,国外大型钢铁企业纷纷采取先进技术,开展节能降耗和综合利用,发展循环经济,不断优化工业的能耗指标和环保指标,以期达到能耗最少,环保最优。
与国外发达水平相比,我国钢铁工业差距明显。
2004年,我国大中型钢铁企业吨钢综合能耗为761千克标煤,比国际先进水平高81千克标煤;吨钢耗新水11. 15m3,比国际先进水平高 7. 3m:,;固体废物综合利用率乩比国际先进水平低个百分点。
在此,以我国大中型钢铁企业的相关指标与国外发达水平作对比,目的是寻找差距,迎头赶上。
下表列出了2003年我国重点企业主要工序能耗与国际先进水平(1999年)的比较,数据表明,我国转炉工序能耗与国外先进水平差值最大,炼铁工序差值最小。
2003年我国钢铁工业吨钢综合能耗为770kgce,吨钢可比能耗698kgce;2003年日本钢铁工业吨钢综合能耗为656kgce, 2000年国外主要产钢国家(英、日、法、徳)平均吨钢可比能耗为642kgce。
这两项指标分别比国外先进水平高出%和觥在国外,先进企业的高炉焦比已达到300kg/t以下,燃料比小于500kg/to我国重点钢铁企业的入炉焦比为426kg/t,部分其它企业为488kg/t,燃料比为560kg/t左右。
高炉工艺的能耗(标媒)比世界先进水平高出50〜 100kg/to同时,我国重点企业之间主要工序能耗的差距很大,指标先进的(如宝钢集团)已达到或超过国际先进水平, 而落后的能耗要高出先进值的1倍或数倍。
这说明,我国钢铁工业节能的潜力还是很大的。
新制订的《钢铁产业发展政策》明确提出,要建立循环型钢铁工厂,500万吨以上规模钢铁联合企业,要努力做到电力自供有余,实现外供。
2005年,全行业吨钢综合能耗降到吨标煤、吨钢可比能耗吨标煤、吨钢耗新水12吨以下;2010年分别降到吨标煤、吨标煤、8吨以下;2020年分别降到吨标煤、吨标煤、6吨以下。
- 1、下载文档前请自行甄别文档内容的完整性,平台不提供额外的编辑、内容补充、找答案等附加服务。
- 2、"仅部分预览"的文档,不可在线预览部分如存在完整性等问题,可反馈申请退款(可完整预览的文档不适用该条件!)。
- 3、如文档侵犯您的权益,请联系客服反馈,我们会尽快为您处理(人工客服工作时间:9:00-18:30)。
国内外高炉炼铁系统的能耗分析
炼铁系统的能耗占钢铁联合企业总能耗70%,
吨铁产生1.5 tco2, 3.08kgso2, 50mg粉尘, 95%的二恶英, 约350kg/t的炉渣。
1、根据中国钢铁工业协会2007年发布的全国重点钢铁企业有关能耗数据来进行分析,有关人士总结了重点钢铁企业高炉每生产一吨铁的能耗状况:
焦化工序的工序能耗为123.11kgce/t,高炉炼铁入炉焦比为392kg/t。
由此得出,冶炼一吨铁水,焦化工序的能源消耗为123.11kgce/t × 0.392t/t = 48.26kgce/t。
烧结工序的工序能耗为55.21kgce/t,高炉炼铁的炉料结构为烧结矿78.28%、球团矿13.91%、块矿7.81%。
冶炼一吨铁水需要消耗1.672吨含铁原料,则需要的烧结量为1.672t × 78.28% = 1.3088t。
由此得出冶炼一吨铁水,烧结工序的能耗为55.21kgce × 1.3088t = 2.25 kgce/t。
球团工序的工序能耗为33.08kgce/t,冶炼一吨铁水需要球团量为1.672t × 13.91% = 0.2325t。
由此得出冶炼一吨铁水,球团工序所消耗的能源为33.08kgce/t × 0.2325t =
7.69kgce/t。
炼铁工序能耗为428.16kgce/t,生产一吨铁水,炼铁系统总能耗为48.26kgce/t(焦化)+ 72.25kgce/t(烧结)+ 7.69kgce/t(球团)+ 426.84kgce/t(炼铁)= 555.04kgce/t。
2、按照上述计算方法,我们计算了2007年一季度宝山钢铁股份公司4号高炉(4747m³)生产一吨铁的能耗:21.81kgce/t(焦化)+ 62.31kgce/t(烧结)+ 4.60kgce/t(球团)+ 381.22kgce/t(炼铁)= 469.94kgce/t。
据了解,国外一些先进的钢铁企业采用高炉炼铁的能耗指标也在不断进步。
表1是2005年韩国浦项制铁和光阳厂焦化、烧结等有关能耗指标。
由表可得,2005年浦项制铁焦化工序能耗为129.7kgce/t × 0.4947t/t = 64.16kgce/t,光阳厂为131.9kgce/t × 0.4921t/t = 64.90kgce/t;韩国高炉炼铁矿耗在1.60t/t左右,浦项制铁烧结能耗为1.60 × 76.4% × 66kgce/t = 80.67kgce/t,光阳厂烧结能耗为1.60 × 70.9% ×57.4kgce/t = 65.11kgce/t;韩国球团矿全为进口,暂不记入能耗。
最终将各项指标汇总可得,浦项制铁炼铁系统能耗为64.16kgce/t + 80.67kgce/t + 426.5kgce/t = 607.33kgce/t,光阳厂炼铁系统能耗为64.90kgce/t + 65.11kgce/t + 441.1kgce/t = 571.11kgce/t。
2005年德国蒂
森钢铁公司的焦化工序能耗为75.1kgce/t,烧结工序能耗为58kgce/t,炼铁工序能耗为
426kgce/t,由此推算出其炼铁系统的能耗低于600kgce/t。
表1 2005年浦项制铁盒光阳厂炼铁有关能耗指标
表2 全国重点钢铁企业能耗对比(单位Kgce/t)
从表2可看出,我国重点钢铁企业炼铁系统能耗在降低,说明我国炼铁系统技术在不断进步,不断完善,有较强的生命力。
非高炉炼铁系统的能耗分析
目前,非高炉炼铁工序在一些工业发达国家已经应用了一段时期,其中,主要的非高炉炼铁系统在生产中的实际能耗情况如下:
南非COREX工艺——该系统生产需要约20%的焦炭(最低可达13%的焦炭),炉料中尚有约20%的球团,冶炼所消耗的燃料比约为1050kg/t左右,扣除部分煤气回收后其工序能耗为595kgce/t~609kgce/t。
韩国浦项FINEX工艺——浦项产能为150万吨/年的FINEX系统目前正处于调试阶段,相关数据尚未透露,现已运行4年的80万吨/年FINEX(日产达2300吨,燃料比在
740kg/t~750kg/t)设备进行分析。
浦项FINEX生产需要10%左右焦炭、块煤和喷吹煤粉,煤比为250kg/t~280kg/t。
FINEX的煤气可进行循环利用(脱出CO2后),可使煤比约降低100kg/t。
澳大利亚Hismelt工艺——2006年年底,澳大利亚Hismelt工艺在实际生产中的煤耗为900kg/t,尚需要有1200℃的高风温作保障,其电耗为350kWh/t。
而2006年我国重点钢铁企业吨铁电耗仅为67.67kWh/t,焦比为395 kg/t。
高热值煤气回收利用率低是非高炉炼铁能耗高的“瓶颈”
2007年,我国重点钢铁企业的烧结、炼铁工序能耗与2006年相比进一步降低,炼铁生产部分工序能耗指标见表2。
2007年,全国重点钢铁企业高炉炼铁燃料比是529kg/t,浦项FINEX燃料比是
740kg/t~750kg/t,澳大利亚Hismelt的煤耗在900kg/t(尚需1200℃风温和350kWh/t的电力)。
这说明目前非高炉炼铁的能耗高于高炉冶炼生产工艺。
从2006年开始我国电力折标准煤系数从0.404kgce/kWh调为0.1229kgce/kWh,是我国钢铁工业能耗值下降较多,与国外炼铁能耗水平的不可比性增加。
2007年,全国重点钢铁企业炼铁系统的能耗为555.03kgce/t。
2007年1季度宝山钢铁股份公司炼铁系统的能耗为469.94kgce/t。
2005年,韩国浦项和光阳炼铁公司炼铁系统的能耗为607.22kgce/t和622.11kgce/t。
通过高炉和非高炉炼铁能耗的对比可以看出,以目前的水平,宝钢的炼铁系统能耗低于非高炉炼铁工艺的能耗,韩国浦项制铁和光阳厂炼铁系统能耗略高于南非COREX的能耗,但低于FINEX和Hismelt的能耗。
非高炉炼铁工艺的能耗高主要问题是大量高热值煤气如合科学合理充分利用。
煤气去发电的能源利用率只有32%——42%,在能源利用率和成本核算上是不合适的,且增加较大投资和运行费。
我国一些企业拟采用煤造气,建设直接还原生产线。
煤造气在技术上是过关了,但是在能源利用率和成本核算上是不合适的。
富余煤气去发电的能源利用率只有32%——42%,在总能耗上是降不下来,成本上升,经济上要亏本。
经分析可得出,目前非高炉炼铁工艺的能耗高于高炉炼铁流程的主要原因有两个方面:一个是非高炉炼铁生产过程要产生大量的高热值煤气,这些热值煤气在回收利用方面还有待进一步加强;另一个是非高炉炼铁对于铁矿石的还原大多数是直接还原(吸热反应),而高炉炼铁大多数是间接还原(放热反应)。
所以,从能源利用效率来讲,高炉炼铁能耗暂时是优于非高炉炼铁的。
但是随着科学技术的不断完善,非高炉炼铁技术也会取得新的进展,得到不断的完善。
从长远出发,一旦非高炉炼铁在短流程优势得以充分发挥的同时,又在能耗降低方面取得突破性进展,其发展前景会更加广阔。
目前,我国大多数直接还原生产线的能耗和成本较高,经营困难,说明尚有较多要改进的地方。