纺纱原理与设备的后加工工序.
纺织工程中的纺纱工艺流程

纺织工程中的纺纱工艺流程一、纱线的定义和分类在纺织工程中,纱线是制成织物的基本原材料。
根据生产用途和规格不同,可以将纱线分为棉纱、毛纱、化纤纱和混纺纱等多种类型。
其中,棉纱是最为普遍的一种纱线。
二、棉纱的生产流程1. 筛选棉花棉纱的生产首先需要筛选棉花,这一步是确保生产质量的关键环节。
选购的棉花需要杂质较少,纤维细长饱满,色泽均匀,手感柔软。
2. 梳棉梳棉是纺织工程中的一个重要工艺,主要是使粗糙的棉纤维经过梳理之后,变得柔软光滑。
经过梳棉后,棉纤维变得整齐,方便后续的制作工序。
3. 纤维成条经过梳棉之后,棉纤维需要进行成条,这一步是为了使纤维在后续加工中能够顺畅地被拉伸。
成条的过程需要将梳理过的棉纤维进行整形,使其形成带状状的纱条。
4. 纱条拉伸纱条拉伸是棉纱生产中的重要环节,其目的是使成条的棉纤维变得更为细长、柔软,便于后续加工。
拉伸过程需要使用细钢丝将纱条挂在纺机上,慢慢地通过细钢丝拉动纱条,使之逐渐变细。
5. 纱锭纺纱纱锭纺纱是棉纱生产中的最后一步工序,也是将成品纺织面料所需的纱线制成的关键工艺。
纺纱工序通常采用纱锭纺法,通过对细长的棉纤维进行拉伸、捻合操作,使其形成一根长长的纱线。
三、棉纱的质量控制棉纱生产过程中需要严格控制产品的质量,确保其符合生产要求。
其中,棉纱质量的控制可以从以下几个方面进行考虑:1. 原料的选购:棉花成分、纤维长度、强度等都会影响制成的纱线的质量,因此在选购原料时需要严格把关。
2. 工艺的控制:每个生产环节都需要控制好温度、湿度等参数,严格遵守纺织工艺规范。
3. 质量检测:对于每批生产出来的棉纱都需要进行质量检测,确保其符合标准,避免产品质量问题对后续生产所带来的影响。
四、纱线的应用范围棉纱作为纺织品的基本原材料,广泛应用于制作各种面料、服装、家居用品等。
在日常生活中,我们可以看到很多纯棉面料的衣物、被套、床单等。
此外,棉纱还可用于制作纺织工业中的各种绳索和索具等。
纺纱原理及设备和后加工工序共41页

16、自己选择的路、跪着也要把它走 完。 17、一般情况下)不想三年以后的事, 只想现 在的事 。现在 有成就 ,以后 才能更 辉煌。
18、敢于向黑暗宣战的人,心里必须 充满光 明。 19、学习的关键--重复。
20、懦弱的人只会裹足不前,莽撞的 人只能 引为烧 身,只 有真正 勇敢的 人才能 所向披 靡。
41、学问是异常珍贵的东西,从任何源泉吸 收都不可耻。——阿卜·日·法拉兹
42、只有在人群中间,才能认识自 己。——德国
43、重复别人所说的话,只需要教育; 而要挑战别人所说的话,则需要头脑。—— 玛丽·佩蒂博恩·普尔
44、卓越的人一大优点是:在不利与艰 难的遭遇里百折不饶。——贝多芬
45、自己的饭量自己知道。——苏联
பைடு நூலகம்
纺纱学简要回顾。doc

第一章绪论1、纺纱基本原理(松解、集合、开松、梳理、牵伸、加捻、除杂、精梳、混和、卷绕)P1~2页及PPT教案。
2、纺纱工程包含的工序①初步加工工序:原棉的轧棉;原毛开洗烘及含草多时炭化;麻类纤维脱胶;绢纺中的精练以去除丝胶、油脂等。
②梳理前准备工序:棉纺即开清棉工程,制成棉卷(定量单位为克/米)或均匀的棉流。
使用机台为开清棉联合机。
毛纺即和毛。
使用机台即和毛机。
麻纺即精干麻→机械软麻→给湿加油→分磅堆仓→开松③梳理工序:棉纺盖板梳理机,制成生条(定量单位克/5米);毛、麻、绢纺用罗拉梳理机。
④精梳工序:对棉纺而言,是精梳前准备工序(制精梳小卷)+精梳机(制精梳棉条)的统称。
⑤并条(针梳)工序:制半熟条、熟条。
涉及并合原理、牵伸原理、混和原理(涤棉混纺纱采用棉条混和)。
⑥粗纱工序:制粗纱(定量单位为克/10米)。
⑦细纱工序:制细纱(定量单位为克/100米)。
⑧后加工工序:络筒、并纱、捻线、烧毛、上蜡、丝光等。
3、棉纺纺纱系统(普梳系统、精梳系统、废纺系统:与普梳系统相比,无并条工序)化纤与棉混纺系统(精梳系统:棉要经过精梳、涤要经过预并、然后三道混并普梳系统:棉不需精梳但要经过预并、涤要经过预并、然后三道混并)第二章纤维原料初加工与选配1、轧棉机分类、轧棉质量判断(三观察:外观变化、长度变化、皮辊棉黄根的多少及锯齿棉疵点的多少)。
2、棉包质量的标识方法(P9页。
类型代号、品级代号、长度代号、马克隆值代号)。
3、“三丝”定义,三丝含量分档(“无、低、中、高”四档)。
4、含糖棉的处理方法。
5、乳化洗毛原理及工艺流程。
(P12~13页)6、炭化原理。
7、麻纤维脱胶基本原理(微生物脱胶、化学脱胶)。
Chapter3 原料的选配与混合配棉定义:棉纺厂将几种唛头、地区或批号的原棉,按比例搭配使用的方法。
1.配棉目的或意义(能满足不同纱线的质量要求、能保持生产过程和成纱质量的相对稳定、多唛混纺,混和批量大,混和棉的性能差异也较单一品种间的原棉性能差异为小,因而采用混和棉纺纱既可增加投产批量,又能在较长时期内保持原棉性能的稳定,确保生产过程和成纱质量的相对稳定、能节约原棉和降低成本)3.原棉主要性能(长度、短绒、细度等)与成纱强力、条干间关系。
新大纺纱学讲义第9章 后加工

第九章后加工第一节概述用原棉和各种化纤作原料经多道工序纺成的细纱,还需要经过后加工工序,以满足对成纱各品种不同的要求。
后加工工序包括络筒、并纱、捻线、烧毛、摇纱、成包等加工过程。
根据需要可选用部分或全部加工工序。
一、后加工工序的任务1.改善产品的外观质量细纱机纺成的不同品种管纱中,仍含有一定的疵点、杂质、粗细节等,后加工工序可以清除较大的疵点、杂质、粗细节等。
为使股线光滑、圆润,有的捻线机上装有水槽还可进行湿捻加工。
有的高级股线还要经过烧毛除去表面毛羽,改善纱线光泽。
对纱线要求光滑的产品可进行上蜡处理。
2.改善产品的内在性能股线加工能改变纱线结构,从而改变其内在性能。
不同的单纱经一次或两次合股加捻,采用不同生产工艺过程,可达到改善纱线物理性能的目的,如强力、耐磨性、条干、光泽、手感等。
花式捻线还能使纱线结构、形式发生改变,形成环、圈、结、点、节以及不同颜色、不同粗细等具有特殊效果的异形纱线。
3.稳定产品结构状态经过不同的后加工工序,可以达到稳定纱线的捻回和均匀股线中单纱张力。
如纱线捻回不稳定,易引起“扭结”、“小辫子”、“纬缩”等疵点。
对捻回稳定性要求高或高捻的纱线,有时要经过湿热定型。
如股线中各根单纱张力不匀,会引起股线的“包芯”结构,导致股线强力、弹性和伸长率下降。
4.制成适当的卷装形式为了满足后道工序加工的需要,要将纱线制成不同的卷装形式。
卷装形式必须满足卷装容量大,易于高速退绕,且适合后续加工,便于贮存和运输。
二、后加工的工艺流程根据产品要求、用途不同,有不同的后加工工序。
1.单纱的工艺流程筒子包管纱→络筒摇纱→成包2.股纱的工艺流程管纱直接并纱并纱→线筒→摇纱→成包3.较高档股线的工艺流程管纱→络筒→并纱→捻线→线筒→烧毛→摇纱→成包根据需要,可进行一次烧毛或两次烧毛。
需定型时,一般在单纱络筒后或股线线筒后进行。
4.缆线的工艺流程所谓“缆线”是经过一次以上并捻的多股线。
第一次捻线工序称为初捻,第二次捻线工序称为复捻。
纺纱工程八个工序的总结

纺纱工程八个工序的总结要将纺织原料纺成符合一定性能要求的纱,除了以上述纺纱原理为基础外,还需要应用各种相应的技术手段,并经过一系列加工过程才能实现。
把纺织纤维制成纱线的过程称为纺纱工程,它由下列若干子工程或工序组成,而上述的纺纱原理就贯穿于这些工序之中。
1.初步加工工序纺织原料特别是天然纺织原料,因为自然环境、生产条件、收集方式和原料种类本身的特点,除可纺纤维外还含有多类杂质,而这些杂质必须在纺纱前加以去除,这个过程即为初步加工工程。
各种纺织原料初步加工工程随原料不同而异。
(1)从棉田中采摘下来的棉铃除了棉纤维外,还含有棉籽及其他杂质,在进行下道加工前必须用轧棉机排除棉籽,制成无籽的皮棉,故棉的初步加工称为轧棉。
轧棉在轧棉厂里完成,轧下来的皮棉(原棉)经检验打成紧包后,运输到棉纺厂进行后续加工。
(2)毛纺工厂使用的原料是从羊身上剪下来的羊毛(原毛)。
原毛含有油脂、汗液、粪尿以及草刺、沙土等杂质,必须在原毛初步加工(俗称开洗烘工程)中清除。
除杂时,首先将压得很紧的纤维进行开松,去除原毛中易于除去的杂质如砂土、羊粪等,然后用机械和化学相结合的方法去除羊毛中的油脂、羊汗及黏附的杂质。
有的羊毛如散毛含草杂较多时,还需经过炭化,即利用化学和机械方法除去净毛中所含的植物性杂质,所用的设备为开洗烘联合机和散毛炭化联合机,得到的半制品分别为洗净毛、炭净毛。
(3)从茎秆上剥下来的麻皮(又称原麻)中除含有纤维素外,还含有一些胶质和杂质,它们大多包围在纤维表面,使纤维粘在一起,为了确保纺纱过程的顺利和纱线质量,这些非纤维杂质必须在成纱前全部或部分除去,这部分初步加工在麻纺厂称为脱胶。
苎麻原麻经过脱胶后得到的半制品叫做精干麻。
(4)绢丝原料是养蚕、制丝和丝织业的疵茧和废丝,其中含有丝胶,油脂,泥沙污杂物和其他杂质。
这些杂质必须在纺纱前用化学、生物等方法去除,这种初步加工在绢纺中称为精练工程,制得较为洁净疏松的半制品叫做精干绵。
纺纱的原理

纺纱是将天然纤维或化学纤维通过机械或化学方法加工成纱线的过程。
纺纱原理主要是通过机械力或化学力将纤维材料拉伸、变形、交织,使其成为连续的纱线。
纺纱的原理可以简单概括为以下几个步骤:
1. 纤维材料的准备:将天然纤维或化学纤维进行处理,使其变得柔软、均匀、有弹性,以便后续处理。
2. 开清:将纤维材料切成小块,去除杂质和短纤维,使其更加均匀。
3. 加捻:将纤维材料通过加捻机进行加捻,使其形成一个长条状的纤维束,以便后续的拉伸和变形。
4. 拉伸:将纤维束通过拉伸机进行拉伸,使其长度增加,同时纤维的直径变细,从而提高纱线的强度和密度。
5. 并合:将拉伸后的纤维束通过并合机进行并合,使其形成一个更加均匀的纱线。
6. 梳理:将并合后的纱线通过梳理机进行梳理,使其纤维排列更加整齐,同时去除杂质和短纤维,使纱线更加纯净。
7. 纺纱:最后,将梳理后的纱线通过纺纱机进行纺纱,形成连续的纱线。
以上是纺纱的基本原理,不同的纤维材料和纱线类型可能需要不同的加工方法和设备,但总体原理是相似的。
纺纱工艺设计
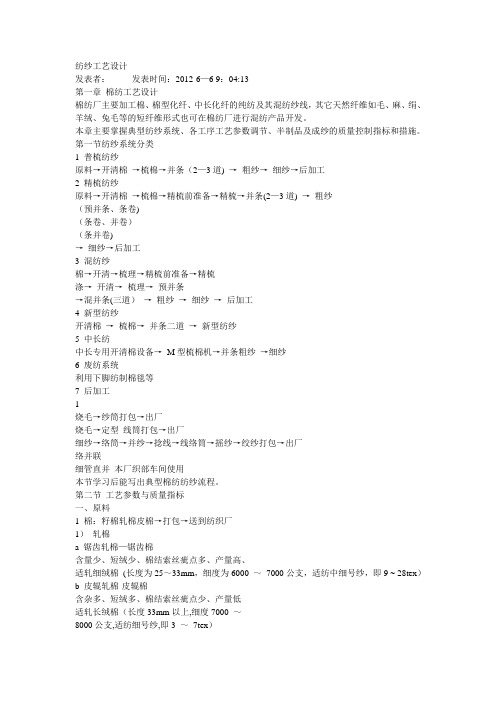
纺纱工艺设计发表者:发表时间:2012-6—6 9:04:13第一章棉纺工艺设计棉纺厂主要加工棉、棉型化纤、中长化纤的纯纺及其混纺纱线,其它天然纤维如毛、麻、绢、羊绒、兔毛等的短纤维形式也可在棉纺厂进行混纺产品开发。
本章主要掌握典型纺纱系统、各工序工艺参数调节、半制品及成纱的质量控制指标和措施。
第一节纺纱系统分类1 普梳纺纱原料→开清棉→梳棉→并条(2—3道) →粗纱→细纱→后加工2 精梳纺纱原料→开清棉→梳棉→精梳前准备→精梳→并条(2—3道) →粗纱(预并条、条卷)(条卷、并卷)(条并卷)→细纱→后加工3 混纺纱棉→开清→梳理→精梳前准备→精梳涤→开清→梳理→预并条→混并条(三道)→粗纱→细纱→后加工4 新型纺纱开清棉→梳棉→并条二道→新型纺纱5 中长纺中长专用开清棉设备→M型梳棉机→并条粗纱→细纱6 废纺系统利用下脚纺制棉毯等7 后加工1烧毛→纱筒打包→出厂烧毛→定型线筒打包→出厂细纱→络筒→并纱→捻线→线络筒→摇纱→绞纱打包→出厂络并联细管直并本厂织部车间使用本节学习后能写出典型棉纺纺纱流程。
第二节工艺参数与质量指标一、原料1 棉:籽棉轧棉皮棉→打包→送到纺织厂1)轧棉a 锯齿轧棉—锯齿棉含量少、短绒少、棉结索丝疵点多、产量高、适轧细绒棉(长度为25~33mm,细度为6000 ~7000公支,适纺中细号纱,即9 ~ 28tex)b 皮辊轧棉-皮辊棉含杂多、短绒多、棉结索丝疵点少、产量低适轧长绒棉(长度33mm以上,细度7000 ~8000公支,适纺细号纱,即3 ~7tex)2)打包规格:例国内包100*42*60cm 体积v=0.25m³密度300 ~ 360kg/m³G=75 ~90kg2、化纤1)品种粘胶莫代尔丽赛天丝2涤纶腈纶锦纶维纶丙纶)芳纶聚乳酸等2)型式长度(mm)细度(旦)棉型33—38 1。
2—1.5中长型51—76 2-3毛型76-102 3-5生产经验公式:L/D=1 L-英寸,D-旦3)分等及质量指标分等按内在质量和外观疵点分:内在质量:断裂强度、断裂伸长、细度偏差、长度偏差以及超长纤维、倍长纤维等. 外观疵点:粗丝、并丝、异状丝、油污纤维二、配棉简介1、不同种类纱线与原棉性状关系1)棉纱号数细号与中粗号的差别。
纺纱厂工艺流程

纺纱厂工艺流程
《纺纱厂工艺流程》
纺纱工艺流程是指将原料棉花、毛线或化纤纤维经过一系列的加工处理,最终变成纺纱产品的整个生产过程。
下面将介绍一下典型的纺纱厂工艺流程。
1. 纺前工序:这一阶段包括开松、梳理和精梳等工序。
开松是将原料纤维解开,梳理是将纤维进行整理和清理,而精梳则是通过一系列的络纱、成条和拉伸工序,排除杂质和短纤维,使纤维更加纯净和牢固。
2. 纺纱工序:在这一阶段,经过纺纱机的加工,将经过梳理的纤维进行纺成纱线。
纺纱机是一种设备,可以将纤维拉伸并形成细长的纱线,同时也可以通过捻合的方式增加纱线的强度和牢固性。
3. 纺后工序:包括加弹、浸纺、印染等工序。
加弹是指通过热处理或化学处理使纱线具有一定的弹性和柔软性,浸纺则是将纱线浸入染料中进行染色,而印染是在纱线上印上各种花纹和图案。
4. 最后是成品包装工序,将加工好的纱线进行包装,并进行质检和出厂。
纺纱工艺流程中,每一个环节都非常重要,只有各个环节都得到严格的执行和把关,最终才能生产出质量好、性能优越的纺
织品。
在工艺流程中,还需要充分运用科技手段和先进设备,以提高产量、节约能源,保护环境。
希望通过这篇文章,可以对纺纱的工艺流程有一定的了解。
- 1、下载文档前请自行甄别文档内容的完整性,平台不提供额外的编辑、内容补充、找答案等附加服务。
- 2、"仅部分预览"的文档,不可在线预览部分如存在完整性等问题,可反馈申请退款(可完整预览的文档不适用该条件!)。
- 3、如文档侵犯您的权益,请联系客服反馈,我们会尽快为您处理(人工客服工作时间:9:00-18:30)。
二、合股加捻后股线性质的变化
1.改善条干不匀 – 按并合原理,n根单纱并合后条干不匀率可降 低。 – 部分粗节或细节隐藏在芯腔里,外观不易察觉。
2.增加强力 – n根单纱并合后的强力一般达不到原来单纱强 力的n倍。因各股单纱伸长率不一致,伸长率 小的应力较集中。 – 股线的强力常超过单纱强力的总和,一般双股 线中的单纱平均强力是普通单纱强力1.2~1.5 倍,三股线的1.5~1.7倍。
二、对络筒工序的要求
• 不损伤纱线原有的物理机械性质 • 做成筒子容量要大,结构坚实,便于贮存 和运输 • 纱线的接头要小而坚固
三、络筒机的工艺过程
四、 络筒张力与张力装置 (一)络筒张力
1、张力大小对卷绕及质量的影响
• 张力过小 筒子容量小、卷绕不良 在退绕时易生脱圈与断头 • 张力过大纱线受到的拉伸过大纱线的强力、弹性下降。
纺纱原理与设备
第九章 后加工
本章知识要点:
1.掌握后加工工序的任务和工艺流程。 2.了解络筒工序的任务、要求、工艺过程。掌 握络筒机的结构和工艺。 3.了解并纱的任务、工艺过程。 4.掌握捻线的任务、工艺过程,股线股数、捻 向及捻系数的选择。 5.了解摇纱和成包的任务。
第一节 概述
纺部品种较多,成纱后要进一步加工
二、 后加工的工艺流程 1、单纱的工艺流程
2、股线的工艺流程
3、缆线的加工工艺流程 • 缆线:经过两次并捻的多股线,第一次捻 线工序称为初捻,第二次捻线工序称为复 捻。 • 工业用线如轮胎帘子布用线、多股缝纫线 等需要进行复捻。
第二节 络 筒
一、络筒工序的任务
• 接长纱线,以增加纱线的卷装容量,提高后续工 序的生产效率。 • 清除纱线上的疵点。杂质,改善纱线的品质和强 力。
• 纱筒插杆→单纱筒子→导纱钩→张力垫圈 装置→落针→导纱罗拉→槽筒→筒子。
三、并纱机的断头自停机构
1、作用:保证并合根数,当某一纱管用完 时,使筒子与槽筒脱开。 2、断头自停机构的数量:等于单纱的根数。
第四节 捻线
一、捻线的任务 • 单纱经过并合后得到的股线。 • 捻线实质,就是以改善纱线中纤维所受应 力的分布状态的方法来提高纱线的品质。
– 原料有棉及化纤; – 成品有单纱及各种股线; – 卷装形式有管纱、筒子纱、绞纱及大小包;
– 加工要求有的需要定型,有的高档和特殊要求的产品要烧毛。
• 细纱工序后的各种加工统称为后加工
一、后加工的任务
1.改善产品外观质量 – 清纱装置:清除纱线的疵点、杂质。 – 捻线机上装水槽进行湿捻加工:使股线表面光滑圆润。 – 有的高级股线经过烧毛,除去表面毛羽、纤维环以增进光泽,上 蜡表面光滑。 2.改变产品内在性能 – 不同品质的单纱经一次或两次合股加捻,配不同股数、 捻向、捻 系数。 – 提高条干均匀度和强力;增加弹性、耐磨、耐疲劳;改善光泽与 手感,使截面更圆整,或使结构松紧起变化。花式捻线能使结构 形态多样化,产生环、圈、结、点节等异样花式。
3、圆盘式张力装置 • 种类:按加压方式不同可分为垫圈加压式、重锤加压式和弹簧加压 式三种;以垫圈加压式为最多。 • 垫圈加压式张力装置的结构:上、下张力盘,轴芯,毛毡垫圈,张 力垫圈及控制圈组成。 • 加压原理:纱线从上下张力盘之间通过时,张力盘和轴芯对纱线产 生摩擦,使纱线产生张力。 • 张力垫圈重量的选择 考虑因素:筒子的外形、纱线的强力(纱线的 粗细)等。对不同特数的加压重量见下表:
•
纱特 隔距/mm 38 0.48-0.6 29 0.4-0.5 25 0.38-0.48 18 0.33-0.4 15.3 0.28-0.38
•
特点:调整方便、适用于高速;但不能清除细节疵点、清纱板处易积尘 屑、清除效率低、易刮毛纱线。
4、电子清纱器 • 种类:光电式和电容式两种。 • 光电式电子清纱器的工作原理:由检测装 置、转换与放大装置、鉴别系统、驱动装 置组成。 • 电容式电子清纱器工作原理:与光电式相 比,其检测装置不同。
3.稳定产品结构状态 – 主要稳定纱线捻回,改善股线强力、弹性、伸长等性能,减少捻 线机上的断头。 – 单纱捻回不稳定,易“扭结”或“纬缩”。 – 股线中各股纱张力均匀,可避免“包芯”结构, – 在并纱机上装张力装置控制张力,使股线张力均匀。 4.制成适当的卷装形式 – 将容量较小,不宜高速退绕的管纱,在络筒机(包括并纱机)上 改绕成容量大并适宜于高速退绕的筒子。 – 有的纱线需要染色或其它处理,可摇成松散绞纱。为便于长期贮 存或远距离运输,可以将绞纱打成紧密的大包。
六、卷绕装置
1、组成:槽筒、筒管。 2、卷绕方式:全动程螺旋式卷绕。 3、卷绕过程:
槽筒转动 • 筒管转动 纱线沿筒管周向卷绕 纱线沿螺旋沟槽轴向移动
第三节 并 纱
一、并纱的任务 • 将两根以上的单并合在一起; • 清除纱上的杂质与疵点; • 做成张力均匀一致的筒子。
二、 并纱机的工艺流程
特数 重量(克)
58-36 19-15
36-24 17-12
21-18 11.5-9
16-14 9.5-8.5
11.7以下 8-4
五、清纱器
1.作用:清除纱线表面的疵点,如粗节、杂物等。 2.清纱器 • 结构:前盖板、固定清纱板、活动清纱板、后盖板、紧压弹簧、螺丝等 组成。 • 清纱原理:疵点在通过清纱器的缝隙时除去。 • 清纱板隔:它是清纱器的一个重要参数,过大时则粗节和纱圈漏过,过 小时纱线易被刮毛,断头多;一般清纱隔距为纱线直径的1.5-2.5倍。 清纱隔距与纱线密度的关系见下表:
2、络筒张力的主要来源
• 纱线退绕时,由于气圈的作用所产生的张力 • 由于张力装置的作用所附加的张力 • 导纱机件对纱线的阻力
3、络筒张力控制
• 对于棉纱:络筒张力≤纱线强力×15%~20%
(二)张力装置 1.张力装置的作用:增加纱线张力,以使筒子卷绕 成形良好。 2.对张力装置的要求: • 产生的附加张力要均匀(对时间稳定) • 与纱线的接触表面在光滑,不产生乱毛纱线 • 结构简单,便于调节,以适应不同粗细的纱线 • 便于清洁