陶粒生产实用技术
免烧陶粒制作方法

免烧陶粒制作方法
免烧陶粒是一种环保、节能的新型建筑材料,它具有轻质、吸
水性好、保温隔热等优点,被广泛应用于建筑、园林、农业等领域。
下面将介绍一种简单的免烧陶粒制作方法,希望能对您有所帮助。
首先,准备原材料。
制作免烧陶粒所需的原材料主要包括粘土、煤灰、矿渣等。
这些原材料都可以在当地容易获取,成本较低,适
合大规模生产。
其次,将原材料进行混合。
将粘土、煤灰、矿渣按照一定的比
例进行混合,然后加入适量的水进行搅拌。
搅拌的过程中需要注意
控制水的用量,以免影响后续的成型工艺。
然后,进行成型。
将混合好的原料放入成型机中进行成型,成
型机可以根据需要选择合适的模具,将原料压制成规定的形状和尺寸。
成型完成后,将成型好的陶粒放置在通风处晾晒,待其自然风干。
接着,进行烧结。
将风干后的陶粒放入窑炉中进行烧结,烧结
的温度和时间需要根据具体的原料和成型工艺来确定。
烧结完成后,
取出陶粒进行冷却,待其完全冷却后即可使用。
最后,进行包装和储存。
将制作好的免烧陶粒进行包装,并做
好标识,以便于运输和使用。
同时,将包装好的免烧陶粒存放在干
燥通风的仓库中,避免潮湿和阳光直射,以确保产品质量。
通过以上简单的制作方法,我们可以得到优质的免烧陶粒产品,这种制作方法不仅操作简单,成本低廉,而且符合环保要求,具有
很高的实用价值。
希望本文所介绍的制作方法能够对您有所帮助,
也希望免烧陶粒能够在更多的领域得到应用,为环保事业做出贡献。
陶粒生产实用技术样本

陶粒生产技术1、烧胀陶粒与烧结陶粒的不同:烧结陶粒在焙烧过程中不发生较大的体积膨胀, 内部只有少量气孔, 而且有许多是联通或开放性的。
而烧胀陶粒会发生较大的体积膨胀, 内部有大量的气孔, 这些气孔多是密闭的, 互补连通的, 开放性气孔较少。
2、烧胀陶粒的主要性能特点由于是密闭微孔结构, 气孔率非常高, 一般要占陶粒总体积的48%-70%, 因此它除具有陶粒的共同特征外, 又具有了这种孔结构所赋予的都有特征。
①具有更加优异的保温性能, 热导率一般只有0.08-0.15w( m·k)②更低的堆积密度, 堆积密度大多为300-500kg/m3③优异的吸声隔声性能3、膨胀气体产生的基本原理膨胀的物质基础是气体, 这些气体是由一些原料成分在高温下发生反应而产生的, 而非外加的当前中国生产膨胀陶粒主要是利用如下四大类能够产生气体的成分: 碳酸盐类、硫化物类、氧化铁类、碳类。
最常见的碳酸盐为碳酸钙和碳酸镁, 最常见的硫化物为硫化铁、硫等, 最常见的氧化铁为Fe2O34、主要化学反应( 1) 碳酸钙的分解反应①碳酸钙的发起反应CaCO3→CaO+CO2↑( 850-900℃)②碳酸镁的发起反应MgCO3→MgO+CO2↑(400-500℃)( 2) 氧化铁的分解与还原反应2Fe2O3+C→4FeO+ CO2↑2Fe2O3+3C→4Fe+ 3CO2↑Fe2O3+C→2FeO+ CO↑Fe2O3+C→2Fe+ 3CO↑( 3) 硫化物的分解与氧化反应Fe2O3===FeS+S↑S+O2===SO24FeS2+11O2===2Fe2O3+8SO2↑( 4) 碳的化合反应C+O2→CO2↑2C+O2→2CO↑(缺氧条件下)5、在氧化气氛下, CO从600℃左右开始产生, 当温度超过1000℃时, CO溢出量增多, 由于CO是氧化铁与碳之间反应的产物, 它的出现不但消耗未燃尽的煤, 而且消耗氧化铁, 因此经600℃以上温度长时间预热, 膨胀会受到影响, 另外在膨胀温度范围内, 逸出的气体主要是CO, 说明CO是主要膨胀气体。
陶粒制备方法
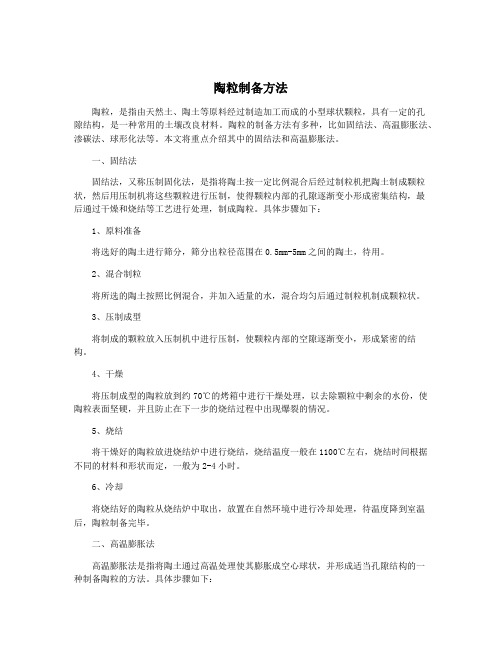
陶粒制备方法陶粒,是指由天然土、陶土等原料经过制造加工而成的小型球状颗粒,具有一定的孔隙结构,是一种常用的土壤改良材料。
陶粒的制备方法有多种,比如固结法、高温膨胀法、渗碳法、球形化法等。
本文将重点介绍其中的固结法和高温膨胀法。
一、固结法固结法,又称压制固化法,是指将陶土按一定比例混合后经过制粒机把陶土制成颗粒状,然后用压制机将这些颗粒进行压制,使得颗粒内部的孔隙逐渐变小形成密集结构,最后通过干燥和烧结等工艺进行处理,制成陶粒。
具体步骤如下:1、原料准备将选好的陶土进行筛分,筛分出粒径范围在0.5mm-5mm之间的陶土,待用。
2、混合制粒将所选的陶土按照比例混合,并加入适量的水,混合均匀后通过制粒机制成颗粒状。
3、压制成型将制成的颗粒放入压制机中进行压制,使颗粒内部的空隙逐渐变小,形成紧密的结构。
4、干燥将压制成型的陶粒放到约70℃的烤箱中进行干燥处理,以去除颗粒中剩余的水份,使陶粒表面坚硬,并且防止在下一步的烧结过程中出现爆裂的情况。
5、烧结将干燥好的陶粒放进烧结炉中进行烧结,烧结温度一般在1100℃左右,烧结时间根据不同的材料和形状而定,一般为2-4小时。
6、冷却将烧结好的陶粒从烧结炉中取出,放置在自然环境中进行冷却处理,待温度降到室温后,陶粒制备完毕。
二、高温膨胀法高温膨胀法是指将陶土通过高温处理使其膨胀成空心球状,并形成适当孔隙结构的一种制备陶粒的方法。
具体步骤如下:将所选的原料经过筛分,将粒径控制在1-5mm之间,在原料中加入化学添加剂,如氢氧化钠、碳酸氢钠等,调节陶土中的主要化学性质,使得烧后生成浮石的条件适宜。
2、高温处理将处理好的原料放入高温烧炉中进行高温处理,一般温度在1000℃以上。
在高温下,原料中的氢氧化钠或碳酸氢钠会分解放出大量气体,使得原料迅速膨胀成为球状,并形成适当的孔隙结构。
三、陶粒的应用陶粒是一种常用的土壤改良材料,主要应用于土壤改良、植物栽培、水利工程等领域。
它具有良好的透水性、透气性,能够增加土壤的孔隙度和通气性,促进植物生长。
可保煤矿陶粒制粒技术

关键 词 : 陶粒 [ 制粒机 1 J
陶粒 就 是 陶质 的 颗粒 , 是一 种 多功 能轻 质材 可作 为其 他 陶粒 厂家制 粒技 术 的参考 。
料, 其具有重量轻 、 强度高 、 物理及化学性能稳定 1 式制粒 机 制粒技 术原 理及 产 品特 性介 绍 辊
的特 点 , 广 泛 应 用 于 房 屋 建 筑 、 处 理 及 花 卉 被 水 辊 式 制 粒 机 制 粒 技 术 原 理 就 是 利 用 二 个 圆 无 土栽 培 等 领域 。 陶粒 的 表 面 是 一 层 坚 硬 的外 筒 对辊 相 向旋 转挤 压制 粒 , 图 1 示 : 如 所
粒 可制作 轻 集料 混凝 土 ;0 —5 0级 陶粒 经 过 双 30 0
轴 对辊 机 破 碎 、 圆筒 转 筛 筛分 后 可 做 花卉 无 土 栽 培 的 载 体 ;0 _ 8O级 陶 粒 经 过 双 轴 对 辊 机 破 6 0_ O 碎、 圆筒 转筛 筛 分后 即成 为 陶砂 , 陶砂 可 用 于 自
性 。辊 式 制粒 机 制粒 的粒 型 为 圆柱 型 , 焙 烧 窑 外 泄 、 经 产量 小 , 于满 足 实际生 产所 需 。 难 烧制 后 陶粒产 品形 状 为椭 圆型 。辊 式 制粒机 制 粒 1 . 式 制粒 机 设计 选 型 仍 选用 等 径 辊 筒 ,二 个 2辊 烧 制 的 陶粒 产 品从 3 0级 至 8 0级 不 等 _ 主要 辊 筒 上都 钻 孔 , 图 4所 示 。其 设 计 目的 是加 大 0 0 2 J , 如 应 用于建 筑领 域 。陶粒 产 品深加 工后 可应 用于 花 钻 孔数 目, 高制粒 效率 。但 因其 为等 径辊筒 , 提 辊
壳, 这层外壳呈 陶质或釉质【 陶粒 的内部结构特 1 J ,
陶粒生产工艺流程

陶粒生产工艺流程陶粒生产工艺流程是指将陶瓷原料进行加工、成型、烧结等多道工序,最终生产出陶粒产品的过程。
以下是常见的陶粒生产工艺流程。
1. 原料准备:选取优质的陶瓷原料,如粘土、瓷石、石英等,并进行研磨、筛分、调配等处理,使其具备良好的成型性能和烧结性能。
2. 成型:将准备好的陶瓷原料进行成型,常见的成型方式有挤压、制粒、湿法成型等。
挤压成型是最常用的成型方式,通过将陶瓷浆料注入模具中,经过挤压和脱水等工序,使其具备较高的强度和形状稳定性。
3. 干燥:成型后的陶粒需要进行干燥,以去除水分。
常见的干燥方式有自然干燥和烘干。
在自然干燥过程中,陶粒会放置在通风良好的环境下,水分逐渐蒸发。
而在烘干过程中,会采用专门的烘干设备,通过加热和通风等方式进行干燥。
4. 烧结:干燥后的陶粒需要进行烧结,以增加其强度和稳定性。
烧结过程中,陶粒被置于高温炉中,经过升温、保温和冷却等多个环节。
在升温过程中,温度逐渐升高,将原料化学反应进行到最终状态。
在保温过程中,陶粒在高温环境中保持一定时间,使其完全烧结。
最后,在冷却过程中,陶粒逐渐降温,凝固成坚固的陶粒。
5. 表面处理:烧结后的陶粒可以进行表面处理,以增加其光泽度和表面平整度。
常见的表面处理方式有抛光、喷涂、清洁等。
抛光会使用专门的抛光机械,对陶粒表面进行磨光处理。
喷涂会使用喷漆机械,将涂料均匀喷涂在陶粒表面,起到装饰和保护作用。
清洁则是对陶粒表面进行清洗,去除表面杂质和污垢。
6. 包装:完成表面处理后的陶粒可以进行包装,通常采用塑料袋、纸箱等包装材料。
包装后的陶粒可以进行储存、运输和销售。
以上就是常见的陶粒生产工艺流程。
在整个流程中,需要严格控制每个环节的工艺参数和质量要求,以确保陶粒产品的质量和性能。
同时,还需要配备相应的生产设备和工具,以提高生产效率和产品质量。
页岩制作陶粒生产工艺

页岩制作陶粒生产工艺页岩制作陶粒生产工艺引言1. 页岩制作陶粒是一种新兴的生产工艺,它利用页岩资源制造出高品质的陶粒产品。
本文将深入介绍页岩制作陶粒的工艺流程、技术优势及应用前景。
1. 页岩制作陶粒的工艺流程1. 原料准备- 选择质量优良的页岩矿石作为原料,并进行破碎、粉碎处理,以确保原料的均匀性和细度。
- 添加适量的助磨剂和粘结剂,以提高陶粒的强度和耐久性。
2. 过程控制- 通过控制烧结温度、烧结时间和气氛成分等参数,优化陶粒的烧结过程。
- 采用先进的自动化设备和智能监控系统,实时监测和调节工艺参数,以确保产品的质量稳定性。
3. 产品成型- 将调制好的原料放入模具中,通过挤压、压制和切割等工艺,使原料成型为具有一定规格和形状的陶粒。
- 进行后期处理,如烘干、烧结和表面处理等,以增强陶粒的物理和化学性能。
4. 品质检测- 对陶粒产品进行品质检测,包括外观检查、尺寸测量、强度测试和化学成分分析等,以确保产品符合相关标准和要求。
2. 页岩制作陶粒的技术优势1. 原料资源丰富:页岩是一种广泛存在于地壳中的矿石资源,全球范围内都具有较高的可开发利用价值。
2. 生产工艺环保:相比传统的陶粒生产工艺,页岩制作陶粒的烧结过程中不需要添加额外的燃料,减少了对环境的污染和能源消耗。
3. 产品优质稳定:通过优化工艺流程和控制生产参数,制作出的陶粒产品具有较高的物理和化学性能,如强度高、耐磨损等。
4. 市场应用广泛:页岩制作陶粒可应用于建筑材料、冶金材料、陶瓷制品等多个领域,满足不同行业对高品质陶粒的需求。
3. 页岩制作陶粒的应用前景1. 建筑材料领域:页岩制作的陶粒可用于生产轻质混凝土、隔热材料和保温材料等,提高建筑材料的质量和性能。
2. 冶金材料领域:页岩制作的陶粒可用于生产耐火砖、高温陶瓷和炉渣护盖等,应用于高温炉窑和冶金工艺中,提高材料的耐高温性能。
3. 陶瓷制品领域:页岩制作的陶粒可用于生产陶瓷板材、陶瓷管道和陶瓷砖等,提高产品的质量和外观效果。
陶粒造粒机造粒过程
陶粒造粒机造粒过程1. 引言陶粒是一种由陶瓷材料制成的颗粒状材料,具有轻质、多孔、耐高温等特点,被广泛应用于建筑、农业、环保等领域。
陶粒造粒机是一种专门用于将原料转化为陶粒的设备。
本文将详细介绍陶粒造粒机的造粒过程。
2. 陶粒造粒机的工作原理陶粒造粒机主要由进料系统、混合系统、造粒系统和出料系统组成。
其工作原理如下:1.进料系统:将原料通过输送带或其他方式输入到混合系统中。
2.混合系统:将不同种类的原料按照一定比例混合均匀,以确保最终产品的质量稳定。
3.造粒系统:混合好的原料进入到造粒系统中,在高速旋转的转鼓中受到离心力的作用,使其形成颗粒状。
4.出料系统:经过造粒后的颗粒通过出料口排出,并进行后续处理(如冷却、筛分等)。
3. 陶粒造粒过程的详细步骤陶粒造粒过程主要包括原料准备、混合、造粒和后处理等步骤。
下面将对每个步骤进行详细介绍:3.1 原料准备在陶粒造粒过程中,原料的选择和准备非常重要。
常用的原料包括陶瓷粉末、黏结剂和添加剂等。
这些原料需要经过筛分、研磨、干燥等处理,以确保其质量和适应造粒机的要求。
3.2 混合混合是将不同种类的原料按照一定比例混合均匀的过程。
通常采用混合机进行混合,通过搅拌、摩擦等作用,使各种原料充分融合,并形成均匀的混合物。
3.3 造粒在陶粒造粒机中,混合好的原料进入到造粒系统中进行造粒。
具体步骤如下:1.原料进入转鼓:通过进料系统,将混合好的原料输入到转鼓中。
2.转鼓旋转:转鼓在高速旋转的原料受到离心力的作用,向外壁靠拢。
3.粘结剂作用:在转鼓旋转的过程中,粘结剂会逐渐溶解,并将原料粘结在一起。
4.造粒形成:随着转鼓的旋转,原料逐渐形成颗粒状,大小均匀。
3.4 后处理造粒后的陶粒需要进行后处理,以提高其质量和适应特定需求。
常见的后处理步骤包括冷却、筛分和烘干等:1.冷却:将造粒后的陶粒通过冷却设备进行降温,以防止其过热变形或熔化。
2.筛分:通过筛网将陶粒按照不同大小进行筛分,以得到符合要求的颗粒尺寸范围。
粉煤灰制陶粒
粉煤灰制陶粒近年来,环保成为全球关注的热点话题。
在中国,由于工业化的快速推进,环境问题越来越突出。
其中,粉煤灰作为工业废弃物,其处理和利用一直备受关注。
近年来,粉煤灰制陶粒技术被广泛研究和应用,不仅可以解决粉煤灰的处理问题,还可以制造出高效环保的建材产品。
一、粉煤灰的来源和特点粉煤灰是燃烧煤炭时产生的废弃物,是一种细粉末状物质。
粉煤灰的主要成分是二氧化硅、氧化铝、氧化钙、氧化镁等,其物理化学性质稳定,不易分解和变质。
粉煤灰的颜色和质地因煤炭的种类、燃烧方式、煤炭的含量等因素而异。
二、粉煤灰制陶粒的工艺流程1. 粉煤灰的制备:将粉煤灰经过筛分、干燥、研磨等工艺处理,使其达到一定的粒度和质量要求。
2. 配料:将制备好的粉煤灰与粘土、长石、石英等原材料按一定比例混合,制成陶粒的原料。
3. 成型:将配好的原料放入成型机中,压制成不同形状和尺寸的陶粒。
4. 烧结:将成型好的陶粒放入窑炉中,进行高温烧结处理,使其达到硬度和强度的要求。
5. 包装:经过烧结后的陶粒进行包装,销售或运输到用户现场。
三、粉煤灰制陶粒的优势1. 环保:粉煤灰是工业废弃物,其处理和利用可以减少环境污染,降低对自然环境的破坏。
2. 节能:粉煤灰制陶粒的生产过程中,利用了废弃物资源,减少了对原材料的需求,节约了能源。
3. 高效:粉煤灰制陶粒的硬度和强度优于传统陶粒,可以更好地满足建筑和园艺等领域的需求。
4. 经济:粉煤灰制陶粒的生产成本低,产品价格相对较低,可以节约用户的经济成本。
四、粉煤灰制陶粒的应用领域1. 建筑:粉煤灰制陶粒可以用作建筑材料,如墙体隔热、吸声、保温等方面。
2. 园艺:粉煤灰制陶粒可以用作植物栽培的介质,如花卉、蔬菜、水果等。
3. 环境:粉煤灰制陶粒可以用作污水处理的填料、垃圾填埋场的覆盖层等。
4. 其他:粉煤灰制陶粒还可以用于电子、化工、冶金等领域。
五、粉煤灰制陶粒的发展前景随着环保和可持续发展理念的不断深入人心,粉煤灰制陶粒的应用将会越来越广泛。
陶粒的生产工艺
陶粒的生产工艺陶粒是一种轻质多孔的耐火材料,由于其独特的性能,在建筑、冶金、化工、农业等领域得到广泛应用。
陶粒的生产工艺主要包括原料配比、成型、烧结和制粒等环节。
下面将详细介绍陶粒的生产工艺。
首先是原料配比。
陶粒的原料主要包括膨胀高岭土、膨胀石英、膨胀蛭石等,它们具有较高的熔点和耐火性能。
原料配比的目的是确定各个成分的比例,以保证陶粒具有良好的物理性能和化学稳定性。
配料时需要将原料进行粉碎和筛选,以确保颗粒大小的均匀性,为后续成型提供良好的条件。
接下来是成型。
成型可以采用干压成型和湿法成型两种方式。
干压成型是将粉状原料加入模具中,通过压力使其变形成型。
湿法成型是将原料与适量的水混合,形成泥状物质后进行成型。
湿法成型的方法多样,包括滚筒成型、喷射成型、挤出成型等。
不同成型方法的选择取决于陶粒的用途和生产要求。
然后是烧结。
烧结是将成型后的陶粒在高温下进行加热,使其发生化学变化和物理结构的改变。
烧结温度和时间的选择对陶粒的性能有较大的影响。
一般情况下,烧结温度较高、时间较长,可以得到较高的烧结度和较好的力学性能。
烧结过程中还要控制气氛的氧化性,以避免陶粒表面的氧化。
最后是制粒。
制粒是为了提高陶粒的粒度分布和形状均匀性。
制粒一般采用颗粒机进行,将烧结后的陶粒进行粉碎、筛分和石英砂的混合,制成符合要求的颗粒。
制粒过程中需要控制破碎机的破碎度和破碎时间,以保证制得的陶粒质量。
以上就是陶粒的生产工艺,其中每个环节都需要精确控制和严格操作,以确保陶粒具有较好的物理性能和化学稳定性。
随着科学技术的发展,陶粒的生产工艺将会不断改进和完善,以适应不同的需求和应用领域的发展。
立窑陶粒生产工艺技术
立窑陶粒生产工艺技术
立窑陶粒是一种常用的建筑材料,广泛应用于墙体、地板和屋顶等建筑中。
它具有轻质、隔热、吸声和防火等优点,因此受到消费者的青睐。
下面将介绍立窑陶粒的生产工艺技术。
立窑陶粒的生产主要分为砂浆配料、窑烧煅烧和筛分干燥三个步骤。
首先,进行砂浆配料。
砂浆配料是立窑陶粒生产的重要环节,主要包括水泥、砂子和陶瓷粉等原料。
这些原料需要按照一定的比例混合,并加入适量的添加剂,如膨胀剂和黏结剂等。
混合后的砂浆配料需要放置一段时间,以确保原料充分融合。
其次,进行窑烧煅烧。
窑烧煅烧是立窑陶粒生产的核心环节,也是制造陶粒特性的重要步骤。
这一步需要将砂浆配料放入窑炉中,进行高温烧制。
在煅烧过程中,由于水泥膨胀剂的作用,砂浆配料中的水分逐渐蒸发,水泥产生化学反应,使砂浆配料膨胀。
同时,煅烧过程中的高温还会使陶瓷粉熔化,与水泥发生反应,从而形成坚固的立窑陶粒。
煅烧的温度和时间需要根据工艺要求进行控制,以确保产品质量。
最后,进行筛分干燥。
筛分干燥是立窑陶粒生产的最后一个环节,主要用于去除生产过程中可能产生的破碎或不合格的陶粒。
在筛分过程中,将陶粒按照不同的粒度进行分类,保证产品的均匀性和稳定性。
筛分完毕后,将陶粒放入干燥设备中,使其充分干燥。
综上所述,立窑陶粒的生产工艺技术主要包括砂浆配料、窑烧煅烧和筛分干燥。
这一工艺可以保证产品的均匀性和稳定性,同时还能满足消费者对于陶粒产品质量的要求。
未来,随着建筑行业的快速发展,立窑陶粒的应用将会得到进一步的扩大和深化。
- 1、下载文档前请自行甄别文档内容的完整性,平台不提供额外的编辑、内容补充、找答案等附加服务。
- 2、"仅部分预览"的文档,不可在线预览部分如存在完整性等问题,可反馈申请退款(可完整预览的文档不适用该条件!)。
- 3、如文档侵犯您的权益,请联系客服反馈,我们会尽快为您处理(人工客服工作时间:9:00-18:30)。
陶粒生产技术1、烧胀陶粒与烧结陶粒的不同:烧结陶粒在焙烧过程中不发生较大的体积膨胀,内部只有少量气孔,而且有许多是联通或开放性的。
而烧胀陶粒会发生较大的体积膨胀,内部有大量的气孔,这些气孔多是密闭的,互补连通的,开放性气孔较少。
2、烧胀陶粒的主要性能特点由于是密闭微孔结构,气孔率非常高,一般要占陶粒总体积的48%-70%,所以它除具有陶粒的共同特征外,又具有了这种孔结构所赋予的都有特征。
①具有更加优异的保温性能,热导率一般只有(m·k)②更低的堆积密度,堆积密度大多为300-500kg/m3③优异的吸声隔声性能3、膨胀气体产生的基本原理膨胀的物质基础是气体,这些气体是由一些原料成分在高温下发生反应而产生的,而非外加的目前我国生产膨胀陶粒主要是利用如下四大类可以产生气体的成分:碳酸盐类、硫化物类、氧化铁类、碳类。
最常用的碳酸盐为碳酸钙和碳酸镁,最常用的硫化物为硫化铁、硫等,最常用的氧化铁为Fe2O34、主要化学反应(1)碳酸钙的分解反应①碳酸钙的发起反应CaCO3→CaO+CO2↑(850-900℃)②碳酸镁的发起反应MgCO3→MgO+CO2↑(400-500℃)(2)氧化铁的分解与还原反应2Fe2O3+C→4FeO+ CO2↑2Fe2O3+3C→4Fe+ 3CO2↑Fe2O3+C→2FeO+ CO↑Fe2O3+C→2Fe+ 3CO↑(3)硫化物的分解与氧化反应Fe2O3===FeS+S↑S+O2===SO24FeS2+11O2===2Fe2O3+8SO2↑(4)碳的化合反应C+O2→CO2↑2C+O2→2CO↑(缺氧条件下)5、在氧化气氛下,CO从600℃左右开始产生,当温度超过1000℃时,CO溢出量增多,由于CO是氧化铁与碳之间反应的产物,它的出现不仅消耗未燃尽的煤,而且消耗氧化铁,所以经600℃以上温度长时间预热,膨胀会受到影响,另外在膨胀温度范围内,逸出的气体主要是CO,说明CO是主要膨胀气体。
6、膨胀原理陶粒的膨胀实际就是发泡,发泡物质在高温下释放气体,产生气体压力才能使陶粒坯体膨胀,但没有气体他就无法得以保存,所以还必须有能束缚住气体的溶体,通过加热产生的熔体包围并防止气体外溢,膨胀才能成功。
早期的动态平衡膨胀过程有利于坯体的膨胀使陶粒实现轻质化,,少量多余的溢出减压,为后期陶粒坯体的膨胀收缩创造了良好的条件。
后期的静态平衡膨胀过程可通过早期的气体释放减压和后期的降温增加来实现,致使陶粒表层开孔气孔减少或损失,同时内部气孔细化、封闭。
7、膨胀模式理论对生产陶粒的指导意义①发气量是陶粒膨胀的最基本因素,对它的正确把握至关重要。
膨胀模式理论可使我们在配方设计或工艺控制时,能够更为准确地把握陶粒坯体的发气量,是之既不会完全被液相始终抑制,达到要求的膨胀力,又能有一定的释放量,形成减压收缩,并且不造成大量气体的逸出,使液相对其的抑制难以进行。
这对于原料中发气成分的控制尤为重要。
②正确把握液相量及液相粘度如果液相量不足,他就无法包裹坯体产生的大量气体,如果液相量过大,就会使他的抑制作用过强,而使气体的膨胀力被过分地抑制。
液相的粘度也对气体的膨胀有极大的影响,粘度越大,对气体的控制力就越强。
③正确地把握不同膨胀端的技术特点8、气孔率对陶粒性能的影响大孔的直径大于1mm,小孔直径小于1mm,微孔直径小于a:陶粒密度陶粒的气孔率越大,他的堆积密度就越低,轻质性能就越优异。
当他的表观密度为500kg/m3左右时,其气孔率均在48%左右。
b:陶粒强度陶粒的强度随着气孔率的提高而降低。
气孔率为10%时,其强度会比无气孔时降低40%左右,气孔率在10%以下时,强度下降不太明显,当气孔率超过10%时,强度下降就十分明显。
c:陶粒吸水率陶粒的吸水率随气孔率的提高而提高。
气孔率越高,吸水率就越高,但这是一般情况。
在气孔细化、封闭、开口孔的连通孔均少或没有的情况下,高气孔率的陶粒也具有很低的吸水率。
9、气孔的尺寸、形状、均匀性对陶粒性能的影响气孔的尺寸越大,在密度相等时,逃离的强度就越差,保持陶粒的总孔隙率不变,气孔尺寸越小,强度就越高。
减小气孔的尺寸,可以提高陶粒的强度。
气孔的形状对强度和吸水率均具有重大的影响。
闭口型状的圆孔,会使陶粒强度高,而且吸水率低。
开口形状的气孔、连通形状的气孔都会使强度下降。
10、烧胀陶粒的孔间壁对陶粒性能的影响①陶粒强度孔间壁是陶粒内部结构的骨架,是承受压应力的主体。
孔间壁的厚度越大,孔间壁占陶粒体积的比例越大,孔间壁上的孔隙越小,陶粒的强度就越高。
孔间壁的物相成分对陶粒的强度影响也非常大。
孔间壁若以玻璃相为主,陶粒的强度就差,若以结晶体针状莫来石晶体网络为主,陶粒的强度就越好。
因为针状莫来石晶体呈网络状分布与玻璃相中,形成坚固的骨架结构,对玻璃相起到了支撑和加固作用,可提高陶粒的强度并提高其断裂强度。
②陶粒吸水率要烧制出优质的膨胀陶粒,就要满足(1)在保证不降低陶粒强度的情况下,尽量提高陶粒的气孔率,以降低陶粒的堆积密度,使其轻质的特性更加突出。
(2)在保证不降低套利的孔隙率的情况下,通过优化孔结构来实现高孔隙率下的理想强度和低吸水率。
这些油画孔结构的手段包括细化气孔,使气孔以封闭圆球孔为主,尽量减少或不形成连通孔和开口孔。
(3)优化陶粒孔结构的孔间壁,使之减少或不生成可以使气孔相连或开口的孔隙。
并使组成孔间壁的物相以针状莫来石晶体为主。
不能以莫来石为主的,也要尽量提高莫来石的数量,以使孔间壁形成坚固的骨架网络。
11、气体的释放主要是CO2、CO、SO2.在粘性状态的粘土内部形成了类似球形的孔洞,因而具有蜂窝状结构。
其原因主要有二:一方面是材料的粘度和材料在熔融过程中所发生的表面张力;另一方面时从这种材料的内部释放出一些气体,而产生膨胀的必要条件时在材料内部具有足够量的矿物成分和有机物。
这些矿物成分和有机物处于熔融温度时能够释放气体。
在一定温度下,出现一个熔融阶段,材料的粘度应足够大,足以把释放出的气体包裹起来。
为了达到以上条件,对材料的化学成分和矿物质成分及粒径应有所要求,必须选择那些具有分解和氧化的成分,一边释放出气体,形成适宜的膨胀,才能生产烧胀陶粒。
12、粉煤灰是生产烧胀陶粒的最理想原料,因为生产烧胀陶粒需要一定量的发气成分,而粉煤灰中的氧化铁具有分解和还原反应而释放二氧化碳的作用。
本身除含有大量二氧化硅和氧化铝外,还含有一部分助融成分如氧化镁。
氧化钠、氧化钾等,同时还含有氧化铁做发气成分。
所以在选择粉煤灰时,除要求他必须有足够含量的二氧化硅和氧化铝之外,还应用较高含量的氧化铁。
另外,粉煤灰的细度应小一些,越细越好,以增加成型性能和减少粉磨电耗。
13、对粉煤灰中二氧化硅和氧化铝、助熔剂氧化物、碳含量的具体要求如下。
(1)二氧化硅和氧化铝含量二氧化硅和氧化铝是粉煤灰中的主要成分,可以在高温下形成玻璃质熔体,赋予陶粒强度。
其中氧化铝应略高一些,他对烧胀陶粒的筒压强度影响更大一些,含量越高,陶粒筒压强度就越高,但烧结温度也随之提高。
适合少成陶粒的化学组成范围来看:二氧化硅53-79% 氧化铝12-26%,少数地方的粉煤灰可能达不到技术要求,可以另外在配方设计时加一些调节剂来补充,如果以粘土为粘结剂,可以补充硅铝含量。
(2)熔剂氧化物含量熔剂氧化物如氧化钾、氧化钠、氧化钙、氧化镁、氧化铁等在焙烧时起助熔作用,可以降低液相生成的温度,其含量的高低与烧成温度、烧成温度范围、回转窑的正常运转及成品率等,均有重要关系。
因此适宜的氧化物含量致关重要。
原料中的熔剂氧化物含量应为8%-12%,有些地方若达不到时,可以另外补加一些氧化钾或氧化钠即可,若是用粘土作粘结剂时,应注意其中的熔剂氧化物含量应与粉煤灰综合计算。
(3)碳含量碳在焙烧中的作用主要有三个:一是做燃料提供热能,产生燃烧;二是在燃烧过程中发生反应,生成一氧化碳气体,使陶粒产生膨胀;三是促进氧化铁的还原,产生气体,增加发气量,因而他又是氧化铁的发气促进剂。
适宜的碳含量应为5-10%,可根据产品的堆积密度要求及强度要求来调节含碳量。
14、尾矿制陶粒技术要求(1)尾矿成分技术要求二氧化硅50%-80%,氧化铝应为12%-26%氧化物包括氧化钠、氧化钾、氧化钙、氧化镁等总含量应为8%-12%,不足时可另加氧化钠、氧化钾补充。
(2)对尾矿砂粒度的要求尾矿的粒度越小越好,要求方孔筛筛余小于5%,所以最好选用细粉状的尾矿。
(3)对尾矿的其他技术要求尾矿的含水率应小于2%,含水量过大时,可采用自然晾晒或烘干的方式。
尾矿的草根树叶等杂志含量应小于1%,杂志太大时应增加除杂工艺。
15、陶粒按密度分为一般密度陶粒、超轻密度陶粒、特轻密度陶粒三类。
(1)一般密度陶粒一般密度陶粒是指密度大于500kg/m3的陶粒。
它的强度一般相对较高,多用于结构保温混凝土或高强混凝土。
(2)超轻密度陶粒轻密度陶粒一般是指300~500kg/m3的陶粒。
这种陶粒一般用于保温隔热混凝土及其制品,可用于混凝土面层料。
(3)特轻密度陶粒特轻密度陶粒是指小于300kg/m3的陶粒。
它的保温隔热性能非常优异,但强度较差。
一般用于生产特轻保温隔热混凝土及其制品。
16、页岩陶粒生产工艺页岩陶粒的生产过程一般分为五个阶段,生料制备、烘干、预热、焙烧以及冷却。
页岩原矿经颚式破碎机破碎,破碎后过筛,选择3mm~5mm粒径颗粒作为生料,然后将生料送入电炉预热,预热完毕立刻送入已经处于目标温度的电阴炉中焙烧,焙烧完毕后,室温冷却得到陶粒。
页岩生料的烘干、预热、焙烧、冷却时间及温度选择称之为陶粒的焙烧制度,研究陶粒焙烧制度是陶粒焙烧研究的主要内容。
陶粒制备过程中的各因素都会对陶粒的质量产生影响。
1、生料的制备:陶粒生产首先必须解决的是原材料加工和制粒工艺,其任务是将采集的原料,经破碎、筛分,配料、混合制成化学成分符合要求、质量均匀的含水物料,然后通过辊压、成球等方法制成不同粒径的生料。
生料的制备工艺很多,根据原料品种不同分为干法、塑化法、粉磨成球法和泥浆成球法。
2、烘干及预热:可以采用干法工艺,破碎筛分后,不用烘干即可进入预热阶段,预热阶段温度控制在400℃~600℃之间。
此预热阶段中,温度急剧变化会引起生料炸裂,而导致最终烧制的陶粒各项性能下降;其次是控制生料在焙烧阶段产生的气体量,因为在预热生料阶段,生料中的有机质和碳酸盐就已开始分解挥发产生气体,那么经过预热后,生料在焙烧阶段产生的气体量就会减少;再次就是为生料表层的软化做准备。
预热阶段控制的因素是预热温度和预热时间,这两个因素都会对最终的陶粒质量产生影响,若预热温度过高或者预热时间过长都会导致生料在预热阶段就已产生大量气体,导致生料在焙烧阶段因膨胀气体不足使陶粒膨胀不佳;但是预热不足,就会造成高温焙烧过程中生料的炸裂,所有这些都会影响到陶粒的最终性能。