Deform 6.1 开式模锻模拟实例
Deform使用简明步骤
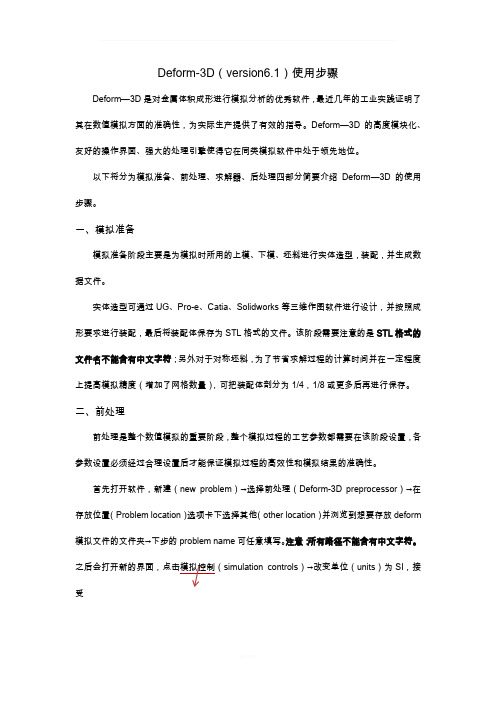
Deform-3D(version6.1)使用步骤Deform—3D是对金属体积成形进行模拟分析的优秀软件,最近几年的工业实践证明了其在数值模拟方面的准确性,为实际生产提供了有效的指导。
Deform—3D的高度模块化、友好的操作界面、强大的处理引擎使得它在同类模拟软件中处于领先地位。
以下将分为模拟准备、前处理、求解器、后处理四部分简要介绍Deform—3D的使用步骤。
一、模拟准备模拟准备阶段主要是为模拟时所用的上模、下模、坯料进行实体造型,装配,并生成数据文件。
实体造型可通过UG、Pro-e、Catia、Solidworks等三维作图软件进行设计,并按照成形要求进行装配,最后将装配体保存为STL格式的文件。
该阶段需要注意的是STL格式的文件名不能含有中文字符;另外对于对称坯料,为了节省求解过程的计算时间并在一定程度上提高模拟精度(增加了网格数量),可把装配体剖分为1/4,1/8或更多后再进行保存。
二、前处理前处理是整个数值模拟的重要阶段,整个模拟过程的工艺参数都需要在该阶段设置,各参数设置必须经过合理设置后才能保证模拟过程的高效性和模拟结果的准确性。
首先打开软件,新建(new problem)→选择前处理(Deform-3D preprocessor)→在存放位置(Problem location)选项卡下选择其他(other location)并浏览到想要存放deform 模拟文件的文件夹→下步的problem name可任意填写。
注意:所有路径不能含有中文字符。
simulation controls)→改变单位(units)为SI,接受弹出窗口默认值;选中模式(mode)选项卡下热传导(heat transfer)。
导入坯料、模具并设置参数:导入毛坯:1、general:通常采用刚塑性模型即毛坯定义为塑性(plastic),之后导入的模具定义为刚性(rigid);温度(temperature):根据成形要求设定坯料预热温度(温热成形时一定注意);材料(material):点击load选择毛坯材料,若材料库中没有对应的材料可选择牌号相近的。
deform模拟软件的实例操作与详细介绍

实验一:挤压变形过程数值模拟题目:工艺参数•锻造速度:5mm/s•摩擦系数:剪切摩擦,0.2材料:AL-5083要求•独立完成模拟过程分析,写出详细的分析报告•给出盘形件的等效应力、等效应变及流线分布图•给出载荷曲线答:(1)一、以UG软件作出锻件的三维实体图如图所示,算得其体积V=7086.4369mm3。
从而选择的毛坯为:Φ=25mm,H=15m进行锻造。
二、用CAD软件画出1/2的毛坯、上模、下模平面图,如下图所示:毛坯上模下模(2):建模过程:将单位定义为公制。
坯料的参数设计,首先定义坯料对坯料进行网格划分:(600个网格)定义材料为AL-5083:定义坯料的边界条件:上模的参数设计:上模定义为刚体下压速度为5mm/s:定义下模,刚体材料调整上模、坯料和下模的位置:定义摩擦系数为0.2:定义步长为0.0158mm/s:对模型进行检查、保存,然后进行计算:(3)后处理结果分析:锻件模拟结果如下,可以看到模腔填充完整,但产生少量飞边。
一、等效应力分析:从应力图可以看到红色区域内承受较大的应力。
二、等效应变:分析:从应变图可以看出在坯料的圆角附近区域,其应变值较大。
三、速度场矢量图:分析:从流线图可以看出,坯料向上下两凹腔和分型面出流动。
四、载荷——行程图:分析:从图中可以看出,开始时随着上模的下行载荷缓慢增加,当坯料圆柱外表面与上下模接触后,载荷随着上模的下行急剧增加,当坯料充满模腔时,载荷达到最大值。
五:流线图:分析:从图中可以看出在坯料中部流线变形很小,随着半径的增大流线越往外弓曲。
实验二:非等温问题数值模拟问题:用实验一的模型对坯料,上下模在锻后温度进行模拟。
其中坯料材料选择AlMgMn ,温度选择3000C ,模具材料选择D5-1U ,温度为1000C 。
(1)具体建模过程如实验一所示,主要区别是对模具的网格划分和坯料与模具、模具与环境、坯料与环境的热交换。
上下模网格划分都是200格,热交换定义如下图:坯料与模具热交换定义:对建立的模型进行检查、保存并计算:(2)后处理:模拟结果如下图所示:有图可以看出,锻件充型完好。
Deform实验报告模锻实验指导书

DEFORM-3D模锻成型仿真实验指导书2014年 4 月实验二DEFORM-3D模锻成型仿真实验1 实验目的与内容1.1 实验目的通过DEFORM软件平台实现模锻成型过程的仿真模拟实验。
了解材料在不同工艺条件下的变形流动情况,熟悉模锻成型工艺特点。
掌握模锻成型过程的应力应变场分布特点。
1.2 实验内容运用DEFORM模拟模锻成型过程,利用三维软件绘制一阶梯轴锻件,模拟其成形过程。
图1 锻件图(一)工艺条件上模:Φ200×50,刚性材料,初始温度200℃;下模:200×200×40。
工件:16钢,尺寸如表1所示。
表1 实验参数序号棒料尺寸,mm摩擦系数,滑动摩擦加热温度℃锤头运动速度,mm/s1 φ80*150 0 900 5002 φ80*150 0 1200 5003 φ80*150 0.2 900 5004 φ80*150 0.2 1200 500(二)实验要求(1)运用三维软件绘制各模具部件及工件的三维造型,以stl格式输出;(2)设计模拟控制参数;(3)DEFORM前处理与运算;(4)DEFORM后处理,观察变形过程,载荷曲线图;(5)提交分析报告。
2 实验过程•1)打开deform软件,新建一个文件,文件取名name.key;•2)打开前处理文件界面分别增加工具体,topdie和bottomdie(workpiece已经存在)。
•3)在各个工具体上相应导入几何体(就是前面所导出的stl文件。
•4检查上述几何体几何状况。
•5对坯料进行网格划分(有热传导情况模具也应划分网格)•6为坯料定义材料(有热交换的也需要对模具定义材料)•7定义工具体的速度(对轧制等给定坯料的初速度)•8定义边界条件,坯料性能(体积补偿)•9定义控制的单位和模拟类型,以及步长和运算停止条件。
•10自动靠模和边界接触的定义。
•11检查并生成分析所需db文件•12.进行模拟分析,完成或观察后处理结果。
运用Deform有限元分析优化锻造模具设计

软件介绍D eform 是一套基于有限元的工艺仿真系统,用于分析金属成形及其相关工艺的各种成形和热处理工艺。
通过在计算机上模拟整个加工过程,帮助工程师和设计人员设计工具和产品工艺过程,减少昂贵的现场实验成本。
提高模具的设计效率,降低生产的材料成本,缩短产品的研究开发周期。
案例分析以下就通过一个案例阐述在实际设计中如何运用D eform 有限元分析来优化锻造工艺及其锻造模具的设计。
图1产品是水龙头的一个重要零件,材质为铅黄铜(C uZn40Pb2),产品重量419克。
锻造工艺有两种方案:①开式模锻,如图2,②闭式挤压,如图3。
运用Deform 有限元分析优化锻造模具设计刘名水图1水龙头重要零件图2开式模锻图3闭式挤压!!!!!!!!!!!对两种方案分别运用DEFROM 进行模拟分析。
DEFROM 软件操作过程:因DEFROM -3D 本身建立几何模型功能较差,难以建立复杂几何模型,且模具设计是用P roe设计,所以就用P roe 建立几何模型。
上模,下模,以及锻造原材料(铜棒)。
用P roe 建好几何模型后,把上模,下模,原材料分别导成.stl 文件。
打开DEFROM -3D 中的DEFROM -F3模块,建立模拟文件,首先进行前处理。
导入之前建立的几何模型(.stl 文件),为了简化计算,不考虑热量在原材料与模具之间的传递,原材料进行网格划分,设定锻造参数:锻造温度700℃,模具温度150℃,摩擦系数0.3,上模移动速度400mm/sec ,上模移动距离等,原材料选择DE -FROM-3D 软件自带材料库里的DI N -CuZn40Pb2。
其中最重要的是注意原材料的网格划分,网格划分越粗,即网格数量越少,模拟计算就越不准确。
相反,网格划分越细,即网格数量越多,模拟计算就越准确,但计算量就越大。
需根据计算机硬件条件及分析需求,合理划分网格数。
前处理设定好,检测数据OK 后,生成待模拟计算数据。
然后进行模拟计算。
DEFORM6.1_3D 课件II
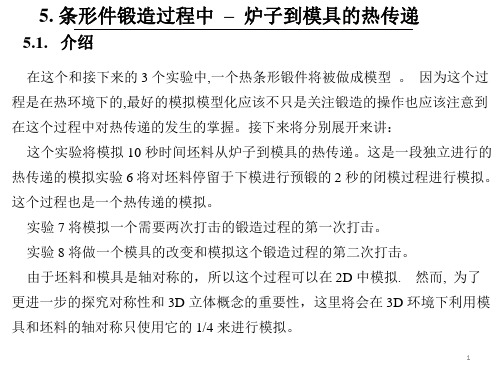
时 (Spike_TopDie2.STL ) 。你可以在一个新的项目输入它的几何形状然后使用
工具来测量一个几何小平面连接以模具为参考的半径。这个距离大约 0.0 8“,如 果坯料的单元格数值是他的一半那这个变化的半径可以很好的解决或是 0.04". 这 就是坯料最小单元格的价值所在,在完成测量以后删除 Top Die 2 。
7.1. 介绍
7.2. 打开先前的模拟文件
7.3. 设置模拟控制 7.4. 定位 Top Die(顶模)
7.5. 定义变形边界条件
7.5.1 Billet 7.5.2 Top Die
7.5.3 Bottom Die
7.6. 设置模具运动条件 7.7. 重设对象接触关系
7.8. 保存问题并运行模拟控制器
具和坯料的轴对称只使用它的 1/4 来进行模拟。
1
-
5. 条形件锻造过程中 – 炉子到模具的热传递
5.1. 介绍
2
-
相对网格化是一默认设置,在先前的实验中使用相对网格化。为了增加模 拟的准确性,对网格化的定义在模拟的各个时期得到了继承。 如果某部分的复杂
性增加,那么用来描述这部分的单元格数量将会相应的增加 。
绝对网格化。为了定义网格的 绝对设置,使用者在网格化时需要定义一个 单元格的最小尺寸。这个最小单元 格是通过测量模具上的与之相对应的区域的细
微特征和该部分的变形区域来决定的 。当这个项目有多次操作时,这种模具的最
小的特征在各个操作中显得尤为重要,因此锻件网格化的定义就不是第一位重要 的。在这个模拟中,变形区域最精确的特征是以上模为基础的半径在第二次打 击
7.9. 后处理
35
36
37
38
39
deform热锻模拟实例
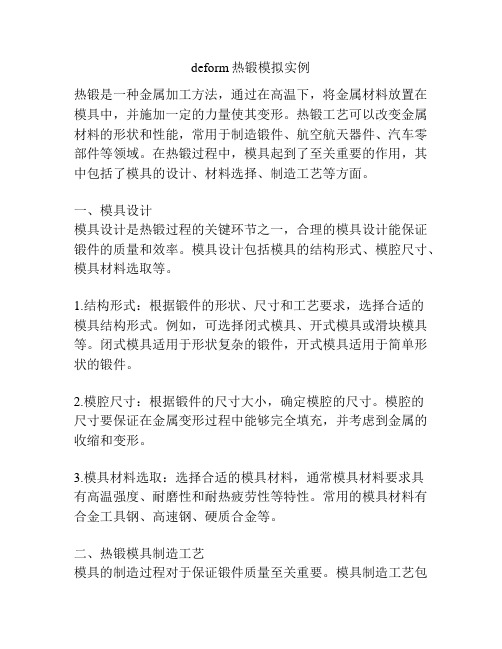
deform热锻模拟实例热锻是一种金属加工方法,通过在高温下,将金属材料放置在模具中,并施加一定的力量使其变形。
热锻工艺可以改变金属材料的形状和性能,常用于制造锻件、航空航天器件、汽车零部件等领域。
在热锻过程中,模具起到了至关重要的作用,其中包括了模具的设计、材料选择、制造工艺等方面。
一、模具设计模具设计是热锻过程的关键环节之一,合理的模具设计能保证锻件的质量和效率。
模具设计包括模具的结构形式、模腔尺寸、模具材料选取等。
1.结构形式:根据锻件的形状、尺寸和工艺要求,选择合适的模具结构形式。
例如,可选择闭式模具、开式模具或滑块模具等。
闭式模具适用于形状复杂的锻件,开式模具适用于简单形状的锻件。
2.模腔尺寸:根据锻件的尺寸大小,确定模腔的尺寸。
模腔的尺寸要保证在金属变形过程中能够完全填充,并考虑到金属的收缩和变形。
3.模具材料选取:选择合适的模具材料,通常模具材料要求具有高温强度、耐磨性和耐热疲劳性等特性。
常用的模具材料有合金工具钢、高速钢、硬质合金等。
二、热锻模具制造工艺模具的制造过程对于保证锻件质量至关重要。
模具制造工艺包括材料准备、加工、热处理和最终组装等步骤。
1.材料准备:根据模具设计,选择合适的模具材料,并进行材料的加工和热处理准备。
2.加工工艺:根据模具的形状和要求,选择合适的加工工艺。
常见的加工工艺包括数控加工、电火花加工、车削、磨削等。
3.热处理:模具的热处理是模具制造过程中必不可少的环节,通过热处理可以改变模具材料的组织结构和性能,提高其耐磨性、耐热疲劳性等。
常见的热处理方法有淬火、回火、正火等。
4.组装:将经过加工和热处理的模具组装起来,进行调试和检验。
确保模具的各零部件之间的配合精度和稳定性。
三、热锻模拟实例以某汽车零部件的热锻模具为例,进行模拟实例的介绍。
1.模具设计:根据锻件的形状和尺寸要求,设计闭式模具,确保模腔尺寸和形状合理。
2.材料选取:选择合金工具钢作为模具的材料,具有良好的耐磨性和耐热疲劳性。
DEFORM模拟锻压挤压实验报告
铜陵学院课程实验报告实验课程材料成型计算机模拟指导教师专业班级姓名学号2014年05月11日实验一 圆柱体压缩过程模拟1 实验目的与内容1.1 实验目的进一步熟悉AUTOCAD 或PRO/E 实体三维造型方法与技艺,掌握DEFORM 软件的前处理、后处理的操作方法与热能,学会运用DEFORM 软件分析压缩变形的变形力学问题。
1.2 实验内容运用DEFORM 模拟如图1所示的圆柱坯压缩过程。
(一)压缩条件与参数锤头与砧板:尺寸200×200×20mm ,材质DIN-D5-1U,COLD ,温度室温。
工件:材质DIN_CuZn40Pb2,尺寸如表1所示,温度700℃。
(二)实验要求(1)运用AUTOCAD 或PRO/e 绘制各模具部件及棒料的三维造型,以stl 格式输出;砧板工件锤头图1 圆柱体压缩过程模拟(2)设计模拟控制参数;(3)DEFORM前处理与运算(参考指导书);(4)DEFORM后处理,观察圆柱体压缩变形过程,载荷曲线图,通过轴对称剖分观察圆柱体内部应力、应变及损伤值分布状态;(5)比较实验 1与2、3与4、1与3和2与4的模拟结果,找出圆柱体变形后的形状差别,说明原因;(6)提交分析报告(纸质和电子版)、模拟数据文件、日志文件。
2 实验过程2.1工模具及工件的三维造型根据给定的几何尺寸,运用AUTOCAD或PRO/E分别绘制坯料、锤头和砧板的几何实体,文件名称分别为workpiece,topdie,bottomdie,输出STL格式。
2.2 压缩过程模拟2.2.1 前处理建立新问题:程序DEFORM6.1File New Problem Next在Problem Name栏中填写“Forging” Finish进入前前处理界面;单位制度选择:点击Simulation Conrol按钮Main按钮在Units栏中选中SI(国际标准单位制度)。
添加对象:点击+按钮添加对象,依次为“workpiece”、“topdie”、“bottomdie”。
基于Deform的汽车发动机连杆锻造模具改进
study on forming length in roll forming [J]. Journal of Materials Processing Technology , 2001 , 113(1~3) : 774~778.
模拟参数设的设定如表 1 所示。
表1
模拟参数设定
图 1 连杆锻件图 从图 1 可知该零件是属于沿轴线截面变化很大的长 轴类锻件,故其可按下式进行坯料尺寸的计算,原则上按 平 均 最 大 截 面 来 选 取 直 径 [1]。
F'=V'/l'
π 4
2
D坯=F'
姨 D坯=
4V' πl'
根椐上述原则进行坯料尺寸的确定, 所确定的坯料 尺寸如图 2 所示。
144 图 3 预锻应变
重庆电子工程职业学院学报
第 19 卷
由图可知经过预锻模预先分配材料后, 坯料在终锻 模中成形充分、饱满;成形填充较为理想。 4 试验对比分析及理论分析 4.1 试验结果对比分析
我们通过物理试验对上述分析结果进行了对比,从 实验结果中可以看到该连杆成形饱满,飞边分布合理。 但 在连杆大头至工字梁的过渡区间出现折叠缺陷 ,如图 10 所示。
针对工厂开发的某型号连杆,进行坯料尺寸的设计、 预锻和终锻工艺的设计。 连杆的锻件图如图 1 所示。
图 2 模锻坯料尺寸
确定上述模锻坯料尺寸为最终所确定的坯料尺寸,
是根椐最初所确定的坯料尺寸在多次模拟后, 进行局部
修改, 再根椐实际实验后对通过模拟所确定的坯料尺寸
deform模拟软件的实例操作与详细介绍
实验一:挤压变形过程数值模拟题目:工艺参数•锻造速度:5mm/s•摩擦系数:剪切摩擦,0.2材料:AL-5083要求•独立完成模拟过程分析,写出详细的分析报告•给出盘形件的等效应力、等效应变及流线分布图•给出载荷曲线答:(1)一、以UG软件作出锻件的三维实体图如图所示,算得其体积V=7086.4369mm3。
从而选择的毛坯为:Φ=25mm, H=15m进行锻造。
二、用CAD软件画出1/2的毛坯、上模、下模平面图,如下图所示:毛坯上模下模(2):建模过程:将单位定义为公制。
坯料的参数设计,首先定义坯料对坯料进行网格划分:(600个网格)定义材料为AL-5083:定义坯料的边界条件:上模的参数设计:上模定义为刚体下压速度为5mm/s:定义下模,刚体材料调整上模、坯料和下模的位置:定义摩擦系数为0.2:定义步长为0.0158mm/s:对模型进行检查、保存,然后进行计算:(3)后处理结果分析:锻件模拟结果如下,可以看到模腔填充完整,但产生少量飞边。
一、等效应力分析:从应力图可以看到红色区域内承受较大的应力。
二、等效应变:分析:从应变图可以看出在坯料的圆角附近区域,其应变值较大。
三、速度场矢量图:分析:从流线图可以看出,坯料向上下两凹腔和分型面出流动。
四、载荷——行程图:分析:从图中可以看出,开始时随着上模的下行载荷缓慢增加,当坯料圆柱外表面与上下模接触后,载荷随着上模的下行急剧增加,当坯料充满模腔时,载荷达到最大值。
五:流线图:分析:从图中可以看出在坯料中部流线变形很小,随着半径的增大流线越往外弓曲。
实验二:非等温问题数值模拟问题:用实验一的模型对坯料,上下模在锻后温度进行模拟。
其中坯料材料选择AlMgMn,温度选择3000C,模具材料选择D5-1U,温度为1000C。
(1)具体建模过程如实验一所示,主要区别是对模具的网格划分和坯料与模具、模具与环境、坯料与环境的热交换。
上下模网格划分都是200格,热交换定义如下图:坯料与模具热交换定义:对建立的模型进行检查、保存并计算:(2)后处理:模拟结果如下图所示:有图可以看出,锻件充型完好。
最新Deform_6.1_开式模锻模拟实例 2
一.DEFORM软件介绍DEFORM系列软件是由位于美国Ohio Clumbus的科学成形技术公司(Science Forming Technology Corporation)开发的。
该系列软件主要应用于金属塑性加工、热处理等工艺数值模拟、它的前身是美国Battelle实验室开发的ALPID软件。
在1991年成立的SFTC公司将其商业化,目前,Deform软件已经成为国际上流行的金属加工数值模拟软件之一。
其主要软件产品有:1. DEFORM-2D(二维)适用于各种常见的UNIX工作站平台(HP,SGI,SUN,DEC,IBM)和Windows-NT 微机平台。
可以分析平面应变和轴对称等二维模型。
它包含了最新的有限元分析技术,既适用于生产设计,又方便科学研究。
2. DEFORM-3D(三维)适用于各种常见的UNIX工作站平台(HP,SGI,SUN,DEC,IBM)和Windows-NT 微机平台。
可以分析复杂的三维材料流动模型。
用它来分析那些不能简化为二维模型的问题尤为理想。
3. DEFORM-PC(微机版)适用于运行Windows 95,98和NT的微机平台。
可以分析平面应变问题和轴对称问题。
适用于有限元技术刚起步的中小企业。
4. DEFORM-PC Pro(Pro版)适用于运行Windows 95,98和NT的微机平台。
比DEFORM-PC功能强大,它包含了DEFORM-2D的绝大部分功能。
5. DEFORM-HT(热处理)附加在DEFORM-2D和DEFORM-3D之上。
除了成形分析之外,DEFORM-HT还能分析热处理过程,包括:硬度、晶相组织分布、扭曲、残余应力、含碳量等。
二.模锻模拟2.1 创建一个新的题目正确安装DEFORM 6.1后运行程序DEFORM-3D,其界面如下图所示。
点击或从New Problem建立新的题目。
弹出如下窗口。
默认为Deform-3D preprocessor不用更改。
- 1、下载文档前请自行甄别文档内容的完整性,平台不提供额外的编辑、内容补充、找答案等附加服务。
- 2、"仅部分预览"的文档,不可在线预览部分如存在完整性等问题,可反馈申请退款(可完整预览的文档不适用该条件!)。
- 3、如文档侵犯您的权益,请联系客服反馈,我们会尽快为您处理(人工客服工作时间:9:00-18:30)。
一.DEFORM软件介绍DEFORM系列软件是由位于美国Ohio Clumbus的科学成形技术公司(Science Forming Technology Corporation)开发的。
该系列软件主要应用于金属塑性加工、热处理等工艺数值模拟、它的前身是美国Battelle实验室开发的ALPID软件。
在1991年成立的SFTC公司将其商业化,目前,Deform软件已经成为国际上流行的金属加工数值模拟软件之一。
其主要软件产品有:1. DEFORM-2D(二维)适用于各种常见的UNIX工作站平台(HP,SGI,SUN,DEC,IBM)和Windows-NT 微机平台。
可以分析平面应变和轴对称等二维模型。
它包含了最新的有限元分析技术,既适用于生产设计,又方便科学研究。
2. DEFORM-3D(三维)适用于各种常见的UNIX工作站平台(HP,SGI,SUN,DEC,IBM)和Windows-NT 微机平台。
可以分析复杂的三维材料流动模型。
用它来分析那些不能简化为二维模型的问题尤为理想。
3. DEFORM-PC(微机版)适用于运行Windows 95,98和NT的微机平台。
可以分析平面应变问题和轴对称问题。
适用于有限元技术刚起步的中小企业。
4. DEFORM-PC Pro(Pro版)适用于运行Windows 95,98和NT的微机平台。
比DEFORM-PC功能强大,它包含了DEFORM-2D的绝大部分功能。
5. DEFORM-HT(热处理)附加在DEFORM-2D和DEFORM-3D之上。
除了成形分析之外,DEFORM-HT还能分析热处理过程,包括:硬度、晶相组织分布、扭曲、残余应力、含碳量等。
二.模锻模拟2.1 创建一个新的题目正确安装DEFORM 6.1后运行程序DEFORM-3D,其界面如下图所示。
点击或从New Problem建立新的题目。
弹出如下窗口。
默认为Deform-3D preprocessor不用更改。
点击Next,选择Other location,选择预设的程序存储地址。
注意:路径不能包含中文!点击Next,输入Problem Name,如KSMD。
点击Finish,完成新题目的创建,自动进入前处理窗口,其创建的文件类型为key。
2.2 前处理2.2.1模拟控制参数设置前处理操作窗口如下图所示,由图形显示窗口、物体显示及选择窗口、物体参数输入窗口组成。
点击快捷按键,或Simulation Controls进入模拟控制参数设置窗口。
图形显示窗口物体显示及选择窗口物体参数输入Units选择框中选择UI国际制单位,弹出提示框时点OK,Reset all the values to new unit system defaults。
在Simulation Title中可设定标题如KSMD。
点击OK,完成模拟控制参数设置。
2.2.2导入毛坯几何文件Deform可导入的文件格式为stl。
可由UG等建模软件生成。
软件默认第一物体为workpiece即毛坯。
Geometry选项卡中点击Import Geo…导入预先生成的文件mapi.stl。
用修改。
在Mesh选项卡中,Number of Elements选项中输入网格数目。
网格数目根据毛坯尺寸和模拟精度要求设置,数目过多影响模拟计算速度,数目过少影响模拟效果。
此实例设定为5000。
点击生成网格。
2.2.4设置毛坯材料在General 选项卡中点击进入材料库。
由于材料库中没有我们要用的材料Pb,所以要自己建立Pb的材料数据库,这部分将在附录部分介绍。
选择User,在Material label选择框中显示出用户自己建立的材料,点取Pb,点击Load。
可在物体显示及选择窗口中看到毛坯材料属性为Pb 。
毛坯的参数设置完成。
2.2.4导入上模点击建立新几何体,其默认为Top Die即上模。
坯位置匹配。
若尺寸为匹配可通过工具栏中快捷键,进入Object Positioning,进行位置调整,此方法不推荐。
在General选项卡中可以看到上模默认属性为刚体Rigid,不做修改。
2.2.5设置上模运动参数在Movement选项卡中Constant Value输入上模运行速度,此实例采用5mm/sec。
在Direction选取上模运行方向,可通过观察图形显示窗口中的坐标系确定运行方向,此坐标系与UG建模时坐标系相一致。
2.2.4导入下模同上模导入一样,点击建立新几何体后,默认即为Bottom Die ,在Geometry 选项中点击Import Geo …,导入预先生成的bottom die.stl 。
此时,所以几何体均导入成功。
其整体效果如下图,可点击工具栏视图快捷键观察不同视图效果。
2.2.5设置物间联系虽然模具和毛坯已成功导入且位置相匹配,但是个物体之间是相互独立,没有任何联系的,需要通过设置摩擦和创建接触来使各物件之间发生联系。
点击工具栏快捷键,弹出Inter-Object对话框。
点击Edit…,进入参数设置,如下图。
Separation与Friction Type均采用默认,Constant点击下三角,选取Cold forming 0.12,设置完成。
点击Close 返回上层对话框,点击Apply to other relations ,将摩擦条件应用于所以物间关系。
在Contact BCC 选择区,点击Generate all ,生成物间接触。
此时,物间联系设置完成,点击OK 退出。
2.2.6设定模拟步长和步数点击快捷按键,或Simulation Controls 进入模拟控制参数设置窗口。
选择Step 选项卡,Solution Step Definition 选择With Die Displacement ,设定步长一般为变形体单元长度的1/3,比较容易收敛,节省时间。
变形体单元长度可通过Check Mesh 读出。
步数根据上模行程和步长来确定,起始步按默认-1,设置每两步保存一次,点击OK 完成设置。
此时所以参数设置已经完成,点击保存。
2.2.7生成数据库文件点击工具栏快捷键或Database打开数据库生成对话框。
12数据库文件的默认存储路径为之前创建项目的存储路径,点击Check,对话框中出现Database can be generated说明没有错误可生成文件,点击Generate生成数据库文件,点击Close退出对话框。
此时,前处理已经完成,点击退出,前处理窗口。
2.3开始模拟退出前处理窗口后返回到DEFORM 主窗口,点击运行快捷键或Simulator 中Run ,开始模拟。
通过Message 栏可观察每步的数据情况。
2.4后处理模拟完成以后,点击Post Processor 中DEFORM-3D Post 进入后处理窗口,由图形显示窗口,图形显示选择窗口,图形显示控制窗口组成。
通过动画播放按钮可观察模具运动和工件成形过程,通过改变视图可使显示更清楚。
右击图形显示选择区的物体名称Turn off 可隐藏物件,以便观察。
点击Single Object mode 或Multi Object mode 可设置显示模式。
图形显示窗口图形显示选择窗口图形显示控制窗口点击工具栏快捷键弹出Graph对话框,Plot objects选取Top Die,可选择不同单位N或tone,点击OK,生成载荷-行程曲线。
点击下拉框可查看各状况变量,点击More…或弹出对话框State Variables可选择更多的状况变量,显示方式Display中可选择各种显示方式,Line为显示等面图。
点击工具栏快捷键弹出Summary 对话框,可查看各步骤的数据,点击按钮可生成相应的曲线。
2.5录制变形过程点击工具栏快捷键,弹出动画制作窗口。
Setting选项卡中设置开始/结束延时和每步间隔时间,选择存储路径,点击Save自动生成变形动画。
三.附录3.1 DEFORM建立新材料数据库由于本实例毛坯采用Pb,而DEFORM原有材料库中并没有此材料,所以需要我们自己建立Pb的数据库。
因为通过新建材料数据来建立新材料是十分困难的,所以我们选择在现有材料的基础上通过更改其参数来得到我们所需的材料。
在前处理窗口中点击工具栏快捷键,弹出Material对话框。
首先我们载入一种原有材料,点击Load from lib,打开材料库。
选择Al,点击Load。
注意:Deform采用的是美国标号。
载入后,材料Al的参数便呈现出来。
需要我们修改的参数有杨氏模量、泊松比、线膨胀系数、热容、热传导率、放射率、扩散系数等,其中最重要的是对流动应力-应变曲线的修改。
点击上图所示俺就,然出流动应力-应变曲线。
其中包括不同温度和不同应变率下的流动应力值。
由于我们是在室温下进行模拟,所以删除其他温度。
参考下面曲线,可取不同应变率对应的应力和应变值,对流动应力-应变曲线进行修改。
注意:单位的换算。
数据修改完成后,即生产为现有数据的流动应力-应变曲线。
通过Plot Int.功能进行曲线绘制,可以根据已有数据绘制出其他应变率下的曲线,当然这是根据现有数据进行耦合得到的,与实际曲线有差距。
其余参数可以通过查询有关资料,进行修改。
参数修改完成之后,点击Save in lib.更改材料标签,点击OK,就可以将修改后的材料作为新材料存储到材料库中。
DEFORM6.1 开始模锻模拟——王伟下次使用时,Source选为User,就可以载入之前建立的新材料数据库。
21。